Shelon – новое имя, новые планы
С располагающимся в Дедовичском районе Псковской области лесозаводом «Судома» журнал «ЛесПромИнформ» связывают давние и дружеские отношения. Разумеется, мы с благодарностью приняли любезное приглашение генерального директора предприятия Василия Калиниченко посетить промплощадку в связи с расширением и модернизацией производства. А приехав на завод, корреспонденты издания узнали и о том, что помимо всего прочего теперь компанию следует называть иначе…
Во времена СССР, когда лесной комплекс вносил весьма существенный вклад в ВВП нашей страны, работа в лесной отрасли была достаточно престижной, а лес и предприятия, его заготавливающие, принадлежали государству, существовало понятие «комплексный леспромхоз». Это понятие относилось к предприятиям, которые выполняли работы не только по заготовке, транспортировке и первичной обработке древесины, но занимались циклом работ по лесовосстановлению.
После распада СССР возникло разделение на негосударственные лесопромышленные предприятия, занимающиеся заготовкой, транспортировкой, и обработкой древесины, и государственные лесхозы, занимающиеся вопросами восстановления лесов, их охраны и защиты. В те годы возникло понятие «комплексное лесопромышленное предприятие» – то есть осуществляющее весь цикл работ по заготовке и переработке древесины.
С вступлением в силу действующего Лесного кодекса РФ, обязывающего лесопользователей выполнять лесовосстановительные работы на территории арендованных участков лесного фонда, в понятие «комплексное лесопромышленное предприятие» органично влилось и лесное хозяйство. То есть, сделав за 30 лет очередной оборот исторической спирали, уже на новом техническом и технологическом уровне, комплексные лесопромышленные предприятия вернулись, по сути, к комплексным леспромхозам.
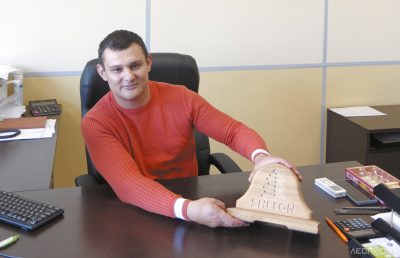
Отметим, что во многих лесных субъектах России у местного населения достаточно часто встречаются алармические настроения по отношению к лесному бизнесу: люди опасаются, что предприниматели спилят лес, и оставят местных жителей у «разбитого корыта» – с пустошью вместо лесов и разбитыми лесовозами дорогами.
Достаточно часто приходится объяснять, что никто больше лесопромышленника не заинтересован в эффективном лесовосстановлении и использовании заготовленной древесины и поддержании в рабочем состоянии транспортной инфраструктуры: это «черные» лесорубы могли «напилить и сбежать» со своими пилами и тракторами, а с деревообрабатывающим заводом разве убежишь?
Очень показательный пример эффективного комплексного и ответственного лесного бизнеса – лесопромышленный комплекс включающий лесозавод «Судома», «Дедовичскую Лесную Компанию» и лесной питомник «Экополис».
Совсем недавно предприятия комплекса по глубокой переработке древесины в пгт Дедовичи объедены под новым брендом – Shelon. Это название отражает близость реки Шелонь, которая берет свое начало в болотах недалеко от поселка и протекает через Псковскую область, впадая в озеро Ильмень (в Новгородской области).
Ключевое предприятие лесопромышленного комплекса Shelon – лесозавод «Судома» – является крупнейшим в России и Восточной Европе производителем термомодифицированных пиломатериалов, сертифицированным FSC. Он был введен в эксплуатацию в ноябре 2015 г.
У истоков лесопромышленного комплекса Shelon стоял холдинг GS Group, развивающий многочисленные бизнес-направления. В процессе диверсификации среди активов компании появился и лесной. Как пояснил генеральный директор лесозавода «Судома» Василий Калиниченко, интерес к возможностям внедрения и развития современных «зеленых» технологий отличал компанию изначально. Курс был взят на безотходное производство с получением востребованной, экспортно-ориентированной продукции и без нанесения вреда окружающей среде. Во многом планы уже удалось реализовать. Из пока не завершенных: создание инновационного биотопливного производства – выпуска биоэтанола из древесных отходов, который в России пока масштабно не производят (работа по этому проекту продолжается, идут лабораторные исследования).
За прошедшие 5 лет одно из основных направлений деятельности лесозавода – производство продукции из березы – получило серьезное развитие: в октябре 2021 г. начал работу новый производственный цех по изготовлению мебельного щита, черновой и чистовой мебельной заготовки.
Лесной вопрос стоит остро
Для обеспечения потребностей открывшегося лесозавода отдельное в сырье специально организована структура – «Дедовичская Лесная Компания» (ДЛК), которая получила значительную арендную базу, с годичной расчетной лесосекой в 300 тыс. м3. К сожалению, качество этой арендной базы оставляло желать много лучшего, по таксационным и почвенно-грунтовым условиям. Псковская область и юг Новгородской области не очень богаты хвойными лесами, доля которых в общем составе насаждений составляет около 30–35%. Кроме того, в 90-е годы ХХ века лесозаготовители повырубали самые качественные и доступные леса, что не могло не сказаться на снижении качества оставшихся. Поэтому в дальнейшем аренда была значительно сокращена, до 25 тыс. м3; причем выход пиловочных бревен из заготовленной в арендной базе древесины не очень большой. Во избежание дефицита древесного сырья в последние два года, лесозавод «Судома» взялся за реализацию приоритетного инвестиционного проекта в области освоения лесов. В рамках этого проекта была получена арендная база с годичной расчетной лесосекой в 186 тыс. м3, и построен цех по изготовлению мебельного щита, черновой и чистовой мебельной заготовки.
В настоящее время общий объем заготовки древесины составляет около 230 тыс. м3, с учетом ожидаемого с 01 января 2022 года внесения изменений в лесоустроительную документацию. Уровень освоения расчетной лесосеки в арендной базе составляет практически 100%.
В изначальном проекте технологической цепочки завода заложены возможности значительного увеличения производительности, без существенной модернизации существующей системы машин. И сейчас имеющиеся мощности завода могут работать с большей нагрузкой, чем нынешние 120 тыс. м3 в год.
Часть перерабатываемых пиловочных бревен (80–90 тыс. м3 в год) предприятие закупает, но, в свою очередь, часть заготовленной в собственной арендной базе древесины (хвойные и березовые балансы, техсырье, дрова, и т. д.) реализует сторонним организациям. При этом среднее плечо вывозки древесины составляет 100–150 км, а наработка за смену у автолесовоза может доходить до 700–800 км.
Одним из основных принципов работы предприятия является 100% -ная FSC-сертификация, что во многом связано с экспортной ориентированностью производства. Все ранее арендованные участки лесного фонда лесопромышленного комплекса Shelon имеют сертификат FSC, в настоящее время ведется работа по сертификации недавно полученных в аренду участков. Надо отметить, что с самого начала работы предприятие ориентировалось на передовые, ответственные формы организации труда и лесопользования, – в приоритете соблюдение требований российского законодательства, включая охрану труда и технику безопасности. Поэтому прохождение FSC-сертификации не представляет для компании сложностей.
Изначально основной объем лесосечных работ, выполняемых силами «Дедовичской Лесной Компании», производился с помощью машинных сортиментых комплексов производства компании Rottne. Небольшие объемы рубок ухода, выборочные рубки в труднодоступных местах выполняются механизированным способом вальщиками леса. Несмотря на значительную наработку машин Rottne за прошедшие годы, часть из них до сих пор успешно работает. Но для усиления и обновления машинного парка лесозаготовительного производства ДЛК заключила контракт на поставку еще трех сортиментых комплексов (харвестер + форвардер) с компанией Komatsu Forest.
Большая часть кадров лесопромышленного комплекса Shelon, а всего их около 500 чел., включая и операторов машинных комплексов в ДЛК, – местные жители.
Для решения проблемы транспортного освоения арендной базы, особенно обостряющейся в аномально теплые зимы и дождливые теплые периоды года,ДЛК использует собственную дорожно-строительную технику – бульдозеры, экскаваторы, и т. д. Благодаря наличию собственной арендной базы, полученной под реализацию приоритетного инвестпроекта, в настоящее время предприятие переходит к долгосрочному проектированию развития дорожной сети.
В ближайшие планы ДЛК также входит обновление парка лесовозной техники для первичной ступени транспортировки леса – от лесосеки до промежуточного склада у магистрали.
Непростые жизненные реалии
Безусловно, результаты реализации приоритетного инвестиционного проекта в области освоения лесов уже сейчас значительно повышают эффективность работы предприятия, а в дальнейшем планируется достижение еще более высоких показателей. Но сама работа над этим проектом была существенно осложнена пандемией COVID-19, и связанными с ней закрытием границ, а также падением курса рубля.
Закрытие границ привело к невозможности для специалистов проектной команды выехать на передовые деревообрабатывающие производства для ознакомления с опытом их работы, применяемыми технологиями и оборудованием, а также посетить заводы-производители оборудования, чтобы посмотреть и оценить его в работе. Поэтому пришлось покупать оборудование «заочно». Это крайне сложная задача, когда речь идет об инвестициях в сотни миллионов рублей.
Также стал проблематичным приезд в Россию специалистов компаний – производителей оборудования для его пусконаладки. Руководству предприятия пришлось предпринять значительные усилия, чтобы организовать их визит. Сложностей в части строительных работ добавила и морозная зима.
Но к настоящему времени все эти проблемы решены, оборудование доставлено, цех построен, работы по пусконаладке проведены. По-прежнему есть сложности с размещением приезжающих специалистов в гостиницах, поскольку для заселения требуется сертификат о прививке (либо о наличии антител) установленного в нашей стране образца, возникают и другие неудобства – и все это нужно предусмотреть.
Основное производство
С открытием нового цеха на биржу сырья завода стал приходить не только хвойный пиловочник, но и березовое сырье. Емкости биржи сырья (максимальная вместимость в зимний период – 25 тыс. м3) и мощностей погрузочно-разгрузочной техники для обслуживания увеличившегося грузооборота вполне хватает.
Разгрузка автолесовозов и укладка сортиментов на приемный стол автоматической сортировочной линии Hekotek выполняется при помощи полноповоротной транспортно-перевалочной машины Sennebogen или гидроманипуляторами самопогружающихся автолесовозов. В 2021 г. на сортировочной линии был установлен новый сканер Weinig Luxscan, более эффективно определяющий сложную кривизну сортиментов.
Из карманов-накопителей сортировочной линии при помощи многофункционального фронтального погрузчика Volvo или полноповоротной транспортно-перевалочной машины Sennebogen сортименты укладываются в плотные или пакетные штабели на складе. В теплый период года торцы сортиментов в штабелях покрываются известью с помощью пульверизаторов.
В настоящее время биржа сырья завода принимает сортименты трех древесных пород – ели, сосны, березы, но в планах предприятия расширить этот ассортимент, присовокупив также и сортименты из лиственницы, пробная партия которых была с успехом переработана на основном технологическом потоке – лесопильной линии EWD.
Кусковые отходы основного производства измельчаются и реализуются в качестве технологической щепы сторонним организациям (например, предприятию компании UPM). Опилки реализуются местным сельскохозяйственным предприятиям. Отходы окорки, частично (сосна, лиственница) реализуются в качестве мульчи, а частично (ель, береза) идут на сжигание в собственную котельную завода. Котел компании Polytechnik (мощностью 5 МВт) полностью работает на вторичном древесном сырье, образующемся на предприятии. Котельная, в том числе, дает тепловую энергию для работы 14 сушильных камер компании Katres, прошедших в 2020–21 гг. модернизацию.
Со временем лесной фонд не становится лучше, поэтому руководство предприятия рассматривает возможность приобретения оборудования для переработки тонкомера.
Помимо простых высушенных пиломатериалов завод производит термомодифицированные, импрегнированные, строганые и брашированные пиломатериалы, а также топливные брикеты.
В 2021 г. на заводе ожидается рекордный выпуск термодревесины – около 7 тыс. м3. Выпускаемые изделия из термомодифицированной древесины являются экологически чистым продуктом. При температуре от 170 до 210°С и переменном давлении в трех герметичных автоклавах французского производства происходит процесс пиролиза. Объем загрузки одного устройства – от 12 до 25 м3, технологический цикл длится 48 ч; в это время давление и температурные режимы меняются, в результате чего древесина высыхает до влажности 5–6%, без каких-либо химических добавок. Такая древесина становится практически водонепроницаемой. Она не подвержена гниению. Наконец, она безопасна – можно использовать для внутренней отделки в детских садах, школах и т. д. Большие объемы этой продукции реализуются в Европу, на Ближний Восток, в Индию и Китай. В Китае и других странах Азиатско-Тихоокеанского региона, где дождь может идти очень долго, термообработанная сосна особенно востребована благодаря своим качествам и является альтернативой лиственницы. В среднем, изделия из термомодифицированной древесины стоят на 40% больше, чем обычные сухие пиломатериалы. В июле 2020 г. начато производство термомодицированных террасной доски и планкена под брендом Groentec по заказу одного из российских ритейлеров.
Востребованы за рубежом и импрегнированные пиломатериалы, выпускаемые заводом в специальном автоклаве высокого давления производства компании MSL (Франция). Этот продукт менее экологичен, поэтому используется только для внешних отделочных работ, а вместе с тем достаточно дорог в производстве и доля его выпуска сегодня невелика.
Для производства погонажных изделий используются станки компании Weinig AG. Отходы цеха по производству погонажных изделий (как и нового цеха по изготовлению мебельного щита, черновой и чистовой мебельной заготовки) идут на единственное в регионе сертифицированное производство топливных брикетов. Для их производства, в рамках приоритетного инвестиционного проекта, создан отдельный цех, в котором установлены 2 брикетных пресса RUF500 и рубительная машина для измельчения кусковых отходов перед брикетированием. Кроме того, на участке установлена упаковочная машина для получаемых брикетов. Для реализации проекта понадобилось также модернизировать централизованную аспирационную систему Nestro, поставив дополнительные фильтры. Цех введен в эксплуатацию в первом квартале этого года. Инвестиции в проект составили 40 млн рублей.
Брикеты продаются преимущественно в зарубежную Европу. Также предприятие рассматривает варианты реализации брикетов в России, в настоящее время в процессе заключения договор на их поставку одному из крупных ритейлеров в сегменте DIY. В настоящее время предприятие отгружает 264 т брикетов в месяц.
Доставка древесного сырья на предприятие и отгрузка готовой продукции потребителям осуществляется с помощью автомобильного транспорта. Неподалеку есть железнодорожный тупик, но в его использовании пока нет необходимости. В марте 2020 г. на заводе запущено крупнейшее в России производство брашированного крашеного планкена в двух цветовых решениях из березы и хвойной древесины. А в июле заработала линия по выпуску мебельного шита и деталей.
Мебель для комфортной жизни
Производственные мощности цеха позволяют выпускать 700 м3 продукции в месяц. Выбор готовой продукции нового производства был совсем не случаен: прежде всего, он связан с небольшим количеством производителей аналогичной продукции, а также с меньшей волатильностью – отсутствием резких сезонных ценовых скачков на мебельный щит и мебельные заготовки, как в лесоматериалах для строительной отрасли. Рынок мебельных изделий и полуфабрикатов из березы намного более стабилен, что позволяет делать качественные прогнозы по развитию производства.
Инвестиции в создание нового цеха по изготовлению мебельного щита, черновой и чистовой мебельной заготовки были сделаны более чем солидные – около 677,5 млн руб. Площадь цеха – 3000 м2. Для его оснащения было закуплено оборудование и техника известных производителей: Weinig (Германия), Biesse и Bacci (Италия), Kundig (Швейцария), Combilift (Ирландия).
Производственная линия рассчитана на переработку 16 тыс. м3 обрезной березовой доски по входу и выпуск более 4 тыс. м3 мебельного щита и 4 тыс. м3 черновой и чистовой мебельной заготовки.
Директор по производству Александр Радзиховский рассказал: «Weinig был выбран как надежный партнер, знакомый нам по оснащению предыдущего участка. Проблем с этим оборудованием особых не было и нет, хорошая техническая поддержка. Удобно и то, что эта компания выпускает весь ассортимент необходимого нам на данном этапе оборудования – не нужно “собирать конструктор” из станков различных производителей. Кроме того, были опасения, что из-за пандемии коронавируса могут возникнуть сбои с поставками, а мы взяли на себя обязательства перед государством, не выполнить которые не могли – поэтому надежность партнера имела особую важность».
По условиям приоритетного инвестиционного проекта компания была обязана создать всего 18 новых рабочих мест, но, с учетом планируемого развитияновый цех при работе в три смены обеспечит работой около 100 человек. Планируется, что в две смены цех будет работать постоянно, а в третью смену будут работать те участки цеха, которые в общей технологической цепочке являются «узкими местами» по производительности.
Поскольку на заводе трудятся в основном местные жители, говорить о большом количестве подготовленных профессионалов, которых можно привлечь к работе, едва ли приходится. Готовых операторов станков в ЧПУ Псковская область предложить не может, поэтому проблему приходится решать самим. Из запланированных 100 человек персонала нанято немногим более половины, новых сотрудников обучают работе на высокоточном и производительном оборудовании прямо на предприятии. Этой ответственной работой занимаются директор по производству, главный технолог, начальники цехов и другие специалисты, подготовленные представителями компаний – производителей оборудования (как правило, это первая смена операторов, присутствующая при шеф-монтаже и пусконаладке).
«Мы стараемся выстраивать полноценную систему обучения и наставничества, – рассказывает Василий Калиниченко. – Постоянно проводим новые образовательные курсы. Планируем вводить разрядную сетку, будем стимулировать сотрудников, которые стремятся развиваться и двигаться вперед».
На производственных участках можно видеть немало представительниц слабого пола. Похожая картина характерна и для многих других деревообрабатывающих предприятий страны: самые кропотливые, требующие внимания и скрупулезности виды работы поручают именно женщинам. Современное оборудование помогает делать их труд не слишком тяжелым физически.
«Наши девушки молодцы, они быстро схватывают и отлично справляются со всеми поставленными задачами, – с гордостью говорит директор завода. – А еще они отличаются высокой ответственностью и наиболее активной жизненной позицией. Естественно, там, где работа потяжелей, ставим мужчин».
В настоящее время березовую доску получают на основной технологической линии предприятия – лесопильной линии EWD, в дальнейшем компания рассматривает возможность организации отдельной лесопильной линии для раскроя березовых бревен. Поступающая в цех обрезная доска при помощи многопильных станков раскраивается на ламели. Затем ламели подаются на линию оптимизации, оснащенную сканером CombiScan Evo LuxscanLine от компании Weinig, и торцовочными станками Weinig Dimter Opticut 450 Quantum.
После оптимизации пороков древесины и обрезки ламели разного размера сортируются. Отобранные в черновую мебельную заготовку ламели упаковываются для дальнейшей реализации сторонним организациям.
Оставшиеся ламели поступают на линию сращивания, также производства компании Weinig. На ней операторы укладывают ламели на стол подачи. Уложенные ламели склеиваются (используется клей Kleiberit 314) в заготовки, длиной до 2,5 м.
После сращивания ламелей выполняется еще одна строжка, для которой используются два строгально-калевочных станка Weinig Powermat 1500 с механизацией EM100. На этих же станках получают и чистовую мебельную заготовку, которая в дальнейшем упаковывается для реализации.
Срощенные ламели поступают в ТВЧ-пресс ProfiPress T 2500 HF (также производства компании Weinig), в котором из ламелей склеивается мебельный щит. Для склеивания используются современные импортные клеи от компании AkzoNobel, и ряда других производителей. В компании до сих пор проводятся тестирования различных композиций для поиска оптимального варианта.
Полученная щитовая заготовка поступает на раскроечный станок SelcoSK3 производства компании Biesse, где щит либо обрезают в размер, либо раскраивают на любые щитовые заготовки для дальнейшего производства или под конкретный заказ клиентов. После форматно-раскроечного станка щит поступает на шлифовальный станок Kundig, далее изделия подаются на упаковку в стандартный пакет или в термоусадочную пленку.
Внутрицеховые перемещения осуществляет многоходовой погрузчик Combilift. Индивидуальная аспирация на отдельных участках выполняется пылеулавливающими установками Consar.
Отметим, что технологический поток цеха по изготовлению мебельного щита, черновой и чистовой мебельной заготовки может перерабатывать не только березовые заготовки, но и заготовки хвойных пород, а также твердолиственных, например, дуба или ясеня.
В настоящее время предприятием закуплена пробная партия дубовых пиломатериалов (около 60 м3), выполнена их качественна сушка, которая заняла около 2 месяцев. Из данной партии планируется выпилить ламели, далее полностью произвести дубовый мебельный щит.
Руководство предприятия постоянно ведет поиск новых направлений работы по другим древесным породам, возможно, новым видам продукции, с еще большей добавленной стоимостью. В кабинете директора завода и в новом цехе уже можно видеть экспериментальные мебельные изделия – стулья, столы, скамьи, тумбочки, и т. д., произведенные на Bacci EvolutionJet – пятикоординатном обрабатывающем центре с ЧПУ и двумя рабочими головами. Этот многофункциональный и высокоточный станок не очень подходит для промышленного производства, зато отлично позволяет оттестировать технологию на отдельных изделиях любой сложности или малых сериях.
В цехе оставлены свободные площадки и продумана потенциальная возможность установки дополнительного оборудования. Василий Калиниченко поделился планами: «Выйдя с основной продукцией на рынок, проанализировав другие его потребности, мы можем разместить здесь шипорезный, присадочный или какие-то другие станки, или, например, паркетную линию. Площади предприятия позволяют и строительство еще одного, похожего по размерам цеха – например, для покрасочной линии – но это более отдаленные перспективы».
В течение следующего года планируется вывести линию на максимальную мощность, отточить все нюансы производства, поработать над качеством готового продукта и, условно говоря, закрепиться в профильном сегменте рынка.
«Мы пока не ставим перед собой задачи выйти к конечному потребителю с собственной готовой мебелью, разрабатывать какие-то свои дизайны – для этого в стране есть достаточно много крупных предприятий, но вот готовить для них компонентную базу нам вполне по силам, – считает директор “Судомы”. – Конструкционные элементы мебельных изделий любой сложности и высокого качества, из различных пород древесины… в общем, все, что мы можем делать из своего сырья без привлечения каких-то сторонних ресурсов, вот чем мы планируем заниматься в ближайшее время.
На сегодняшний день все, что мы выпускаем, продается моментально – с трудом успеваем за спросом. Портфель заказов расписан на текущий момент до конца года».
Способствует успеху предприятия и то, что оно работает в тесном сотрудничестве с районной и областной администрации. «Мы достигли полного взаимопонимания, – поясняет руководитель предприятия. –Совместными усилиями развиваем поселок Дедовичи». Экополис – город зеленых жителей
В динамично развивающийся комплекс предприятий под брендом Shelon, помимо лесозавода «Судома» и «Дедовичской Лесной Компании», также входит лесной питомник «Экополис», который занимается выращиванием посадочного материала с закрытой корневой системой для постоянно проводимого компанией лесовосстановления. Питомник был отмечен премией «Зеленый проект года – 2021», получил приз зрительских симпатий.
Производственная площадка «Экополиса» представляет собой современный, высокотехнологичный тепличный комплекс, в котором в две ротации в год выращивается посадочный материал с закрытой корневой системой. В тепличный комплекс входит 3 теплицы общей вместимостью до 2,5 млн сеянцев в одну ротацию, а также площадки закаливания. Первая ротация выращивания сеянцев в теплице длится с апреля по июнь, когда сеянцы из теплицы перемещаются на площадку закаливания. После чего в теплице сеется вторая ротация. На площадке закаливания сеянцам обеспечивается необходимый уход – полив и прополка сорняков.
В сезон основной работы, с апреля по октябрь, в питомнике работает 15–20 человек, в зимний период, когда технологический процесс выращивания останавливается, остается 5 сотрудников.
Семенной материал второго и третьего районов предприятие закупает у специализированных семеноводческих селекционных центров Новгородской, Ленинградской и Кировской области. В эти же субъекты реализуются выращенные сеянцы, а также в Костромскую, Смоленскую, Тверскую, Московскую, Вологодскую и другие области. Торф специального фракционного состава и плотности заказывается у поставщиков из Новгородской области.
Разброс цен на сертифицированный семенной материал достаточно значительный, и составляет в 2021 г. от 6 до 12 тыс. руб. за 1 кг семян высшего и первого сорта. Поступающие на предприятие семена за 2–3 дня перед посевом проходят необходимую подготовку. В отдельном помещении находится линия для посадки семян в кассеты. Сначала пустые кассеты, производства шведской компании BCC SideSlit вручную укладываются на линию подачи кассет, затем торфяная смесь в специальном барабане сепарируется и доводится до оптимальной плотности. Очищенный торф засыпается в кассеты, затем уплотняется, после чего в нем автоматом делается лунка, в которую через посадочные трубки попадают подготовленные семена (по 2 в каждую кассету). После чего кассеты устанавливаются на специальные поддоны и при помощи погрузчика Bobcat перемещаются в теплицу. Во время выращивания сеянцев в теплице вносятся азотные и калийные удобрения. Достигшие требуемых размеров на площадке закаливания сеянцы вручную вынимаются из кассет и упаковываются для отправки заказчикам.
В планах развития ООО «Экополис» – развитие направления по выращиванию декоративных растений для садово-паркового хозяйства и частных клиентов. Для этого предполагается закупка эксклюзивных семян.
***
В заключение хочется отметить, что Shelon, включая его головное предприятие – лесозавод «Судома», с уверенностью можно назвать инновационным, динамично развивающимся комплексным предприятием, выполняющим полный цикл эффективного ответственного лесопользования: заготовку древесины, получение из нее продукции с высокой добавленной стоимостью и лесовосстановление. Корреспонденты «ЛесПромИнформ» своими глазами убедились в том, что в сегодняшнем российском ЛПК это возможно: вести едва ли не эталонный бизнес, приносящий в страну валютную выручку, налоговые поступления в бюджеты различных уровней, обеспечивать высокотехнологичные рабочие места и оказывать существенную поддержку району своего расположения. Пожелаем лесопромышленному комплексу Shelon дальнейших успехов!
Текст Игорь Григорьев
Фото Максим Пирус