Ресурсы старые, результаты – новые
На заводе домостроения ООО «Содружество» в Алтайском крае подвели итоги проекта по оптимизации процесса производства домокомплектов из клееного бруса.
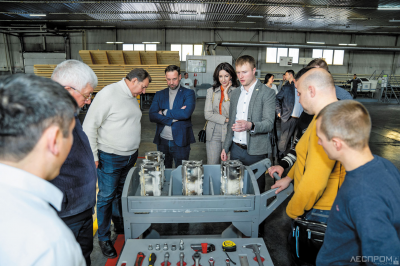
Девять месяцев напряженной работы дали свои плоды: удалось расширить ассортиментную линейку бруса, существенно сократить временные потери, внедрить систему 5С. Но главное, считают руководители, это изменение отношения сотрудников к организации производства и понимание ими своей роли в технологической цепочке, начиная с обустройства рабочего места и заканчивая рационализаторскими предложениями по оптимизации всех процессов. Сразу скажем, что борьба со скепсисом – одна из ключевых составляющих проекта. Зачем менять то, что работало много лет? Ответ на этот вопрос стал очевидным для всех в финале, и больше его никто не задает. И еще один важный момент: главное условие проекта – не прибегать к поиску новых ресурсов, а максимально задействовать имеющиеся.
Итак, обо всем по порядку.
Фиксируем проблемы
Проект по бережливому производству стартовал в феврале 2022 года при поддержке Регионального центра компетенций. Цели – сокращение длительности производственного процесса, увеличение выработки, снижение себестоимости продукции.
Завод расположен в селе Топчиха и работает уже 13 лет – с 2009 года. За это время произведено более 100 тыс. м3 клееного бруса, на зарезных центрах обработано примерно 90 тыс. м3 бруса под проект. Доля клееного бруса в выручке предприятия составляет 25%. Комплекты домов, бань, гостиничных и туристических комплексов, ресторанов были смонтированы во многих регионах России, а также за рубежом. В общей сложности больше 1500 объектов. Казалось бы, все процессы давно отлажены и хорошо понятны персоналу.
Но на первом же этапе проекта, когда сотрудники создавали карту потока ценностей текущего состояния, было выявлено 86 проблем. «Далее разработали план действий устранения недостатков – это 111 пунктов, из которых 93 были выполнены на этапе внедрения, 18 отклонены в процессе работы за ненадобностью. Важно, что любое действие фиксировалось документально – сроки, ключевые события, ответственные. Документ подписывался всеми задействованными лицами», – рассказывает заместитель директора по производству ООО «Содружество», руководитель проекта Андрей Касьяненко.
Ликвидируем пробелы
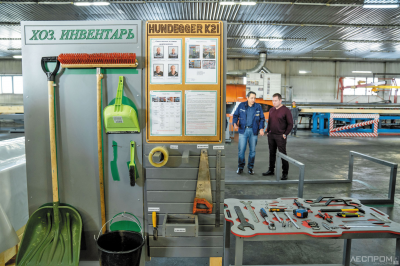
На участке оценки качества и сортировки пиломатериалов сотрудники выявили следующие проблемы: необходимость доработки процесса оценки качества, с тем чтобы исключить человеческий фактор и оценку пиломатериалов «по-своему»; высокую скорость работы линии, из-за которой сотрудники могли не успеть сделать качественную оценку; присутствие большого объема забракованного материала в цехе, мешающее передвижению техники; большой выход дров; простой линии сращивания из-за нехватки ламелей первого сорта. Что касается ламелей, то их выход по сортности также не укладывался в нужные параметры. Например, фактический выход ламелей первого сорта составлял 32% при потребности 40%, второго сорта – 64% при потребности 60%, третьего сорта – 4% при нулевой потребности (то есть, попросту говоря, они не нужны).
«Поэтому одной из первых наших задач стало изменение процессов сортировки, оценки качества и установка сортировочного стола, – отметил Андрей Касьяненко. – Обучили сотрудников на этом участке, внедрили стандарты сортировки, чтобы исключить человеческий фактор. Разделили участки сортировки и сращивания на отдельные, независимые друг от друга зоны. Изготовили и установили сортировочный стол для более удобной работы сотрудников, убрали ленточный транспортер. Удалось повысить процент выхода ламелей первого сорта и максимально снизить процент выхода дров».
Подчеркнем, что все усовершенствования сделали сами сотрудники, без привлечения сторонних подрядчиков. Экономия составила несколько миллионов рублей. Также были разработаны стандарты каждого рабочего места, уборки помещений, и это значительно облегчает работу персонала, в том числе новых сотрудников, которым не нужно несколько раз объяснять специфику деятельности.
Применяем инструменты
В рамках проекта была расширена ассортиментная линейка бруса. Это высокий брус сечений 210 Х 265 и 250 Х 265, а также брус сечений 80 Х 185 и 125 Х 185 для производства бюджетных бань, гаражей и летних домиков.
Внедрили SMED – инструмент бережливого производства, направленный на сокращение времени настройки или переналадки оборудования до минимально возможного. Оборудованы специальные столы для хранения инструмента, который теперь всегда под рукой.
«Самый красивый инструмент – это 5С, – отмечает Андрей Касьяненко, – соблюдение порядка, содержание в чистоте, стандартизация, совершенствование, сортировка». Внедрили зону карантина – это место, где размещают инструмент, назначение которого неясно или вызывает вопросы. «В целом рабочие места теперь организованы таким образом, что даже начинающий специалист сможет быстро разобраться в оборудовании, инструментах и так далее», – уточнил Андрей Андриянович. Изменились складские помещения: все детали, запасные части, расходные материалы находятся строго на своих местах.
Подводим итоги
Основными результатами реализации проекта стали уменьшение времени протекания процесса на 47%, сокращение незавершенного производства на 7,6%, увеличение выработки на 57%, снижение себестоимости 1 м3 на 7%.
Кроме того, удалось добиться дополнительных результатов: учет всех материалов и их остатков стал точнее, изменилась система оплаты труда, повысилась мотивация сотрудников, приобретено новое оборудование, сделан капитальный ремонт бытовых помещений и т. д.
Маленький, но важный нюанс. Ежедневные утренние планерки стали проводить возле оборудованного информационного центра. Обсуждаются текущие задачи, оценивается предыдущий день, озвучиваются планы на предстоящий. «Вроде бы, это мелочь, но на самом деле такой организационный момент задает тон всему дню. Каждый знает, чем нужно заниматься, чтобы сработать командой как можно лучше», – подытожил Андрей Андриянович.
Сотрудники, внесшие значительный вклад в реализацию проекта, получили от предприятия ценные призы: смарт-часы, ноутбуки, телевизоры, подарочные сертификаты и другие.
Оценки проделанной работы
Своим мнением о проекте поделились несколько специалистов.
«Мы завершаем уже шестой проект по бережливому производству. Благодаря ему мы перешли на новый уровень взаимопонимания не только между сотрудниками отдельно взятого предприятия, но и между предприятиями холдинга в целом», – сказал генеральный директор холдинга «Алтайлес» Иван Ключников.
«С чего мы начинали работу? Спрашивал у сотрудников, что им мешает быть эффективными. Кто-то говорил про качество, кто-то про запасные части. И тогда я отвечал: используйте то, что у вас есть, по максимуму. Проект закончился, но все мы понимаем, что процесс совершенствования должен быть непрерывным и бесконечным», – отметил эксперт Регионального центра компетенций Валерий Бессонов.
«В Алтайском крае в проекте принимают участие 72 предприятия, из них пять – это производственные предприятия холдинга "Алтайлес". Мы видим хорошие результаты, которых достигла команда завода домостроения благодаря устранению потерь. Особенно хочу отметить коллектив за преодоление скепсиса, который все еще есть по отношению к бережливому производству. Важно, что после завершения проекта это направление будет развиваться на предприятии самостоятельно», – подчеркнул заместитель министра экономического развития Алтайского края Сергей Кореннов.
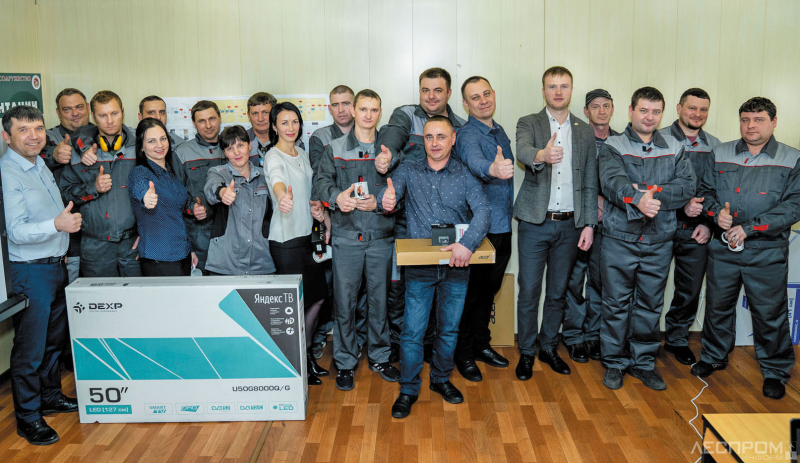
Текст Ольга Лисица