Методы повышения стойкости концевых твердосплавных фрез при обработке древесных плит
Плитные древесные материалы востребованы во многих областях современной деревообрабатывающей и мебельной промышленности. Особенно широко при изготовлении мебели используются древесно-стружечные плиты. HDF и MDF, характеризующиеся мелкодисперсной структурой, как правило, качественно фрезеруются алмазными фрезами, а вот древесно-стружечные плиты, особенно облицованные пленками, ввиду состава, структуры и строения относятся к труднообрабатываемым материалам. Зачастую при их обработке алмазный инструмент не демонстрирует стойкость режущих элементов фрез и сопровождается их повышенным износом, прежде всего в зонах клеевых швов плит и облицовочного материала.
Одним из основных видов режущего инструмента, применяемого для обработки заготовок, в том числе раскроя (нестинга) на заготовки и фрезерования кромок предварительно распиленных древесно-стружечных плит (ДСтП), являются концевые фрезы. Несмотря на широкое использование в промышленности, процесс фрезерования ДСтП концевыми фрезами по сей день недостаточно исследован и четких рекомендаций по выбору режимов резания нет либо они не вполне некорректны. Попробуем восполнить этот пробел.
ДСтП относят к труднообрабатываемым материалам по следующим основным причинам:
- присутствие коры, песка и глинозема в теле плит;
- присутствие твердой cмолы в структуре плиты и смолы в зоне отделочных материалов;
- наличие на поверхности плиты абразивных частиц (корунда) от шлифшкурки после калибрования плит;
- повышенная твердость отделочного материала из-за присутствия в нем абразивных частиц.
Основные факторы износа режущего инструмента
К факторам, влияющим на износ сверхтвердых инструментальных материалов (стеллитов, твердых сплавов, алмазов), относятся следующие:
- длина (путь) резания;
- твердость режущего материала;
- скорость резания;
- скорость подачи;
- углы резания режущего инструмента;
- качество сервисного обслуживания фрез;
- наличие качественной аспирации и конструкция пылеприемника на оборудовании.
В производственных условиях при обработке ДСтП концевой фрезерный инструмент снимает с поверхности заготовки припуск, размер которого составляет от 0,2 мм (для повышения качества поверхности под отделку и устранения сколов при ее обработке) до диаметра фрезы (в случае раскроя заготовки по методу нестинга).
Согласно многим исследованиям, при фрезеровании древесины и древесных плит качественные и энергетические показатели процесса в значительной степени зависят от средней толщины стружки aср, расчет которой при использовании концевого фрезерного инструмента имеет особенности.
При открытом фрезеровании заготовки в случае снятия припуска меньшего либо равного радиусу концевой фрезы, в зависимости от направления подачи по отношению к направлению вращения инструмента, осуществляется либо только встречное, либо только попутное фрезерование (рис. 1).
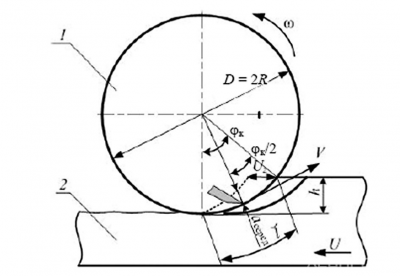
Средняя толщина стружки при фрезеровании насадной фрезой рассчитывается по формуле
где Uz – подача на зуб, мм; φк– угол контакта, град.
При раскрое концевым фрезерным инструментом φк = 180º и толщина стружки на середине дуги контакта, согласно формуле 1, aсеред = Uz – соответствует не сред- ней, а наибольшей толщине струж- ки на выходе фрезы из заготовки. Это обусловлено значительной величиной угла контакта при работе концевых фрез.
А процесс обработки кромки плиты со снятием припуска, размер которого больше радиуса или равен диаметру концевой фрезы, отличается последовательным осуществлением двух указанных типов фрезерования в процессе одного оборота инструмента.
В случае участия режущего элемента в движении последовательно на участках встречного фрезерования и фрагменте участка попутного или, наоборот, открытого фрезерования (снимаемый припуск меньше диаметра, рис. 2) длина дуги контакта, мм, может быть определена по формуле
где d – диаметр концевой фрезы, мм; φк – угол контакта, то есть центральный угол между нормальным к подаче радиусом резания и радиусом, проходящим через точку выхода лезвия зуба фрезы из обрабатываемого материала, град.
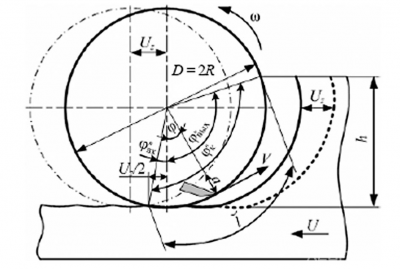
Средняя толщина стружки равна
h
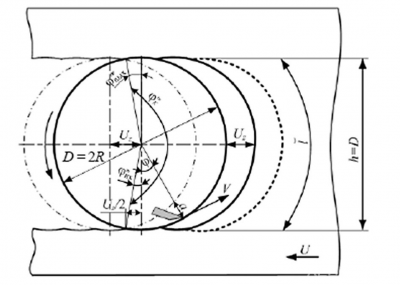
Расчет средней толщины стружки при нестинге ведется по формуле
ср 2∙R Из формулы 4 видно, что погрешность средней толщины стружки при операции раскроя материала концевыми фрезами, рассчитанной без учета угла выхода, в зависимости от диаметра концевой фрезы (12–28 мм) составляет от 0,5 до 5,5%.
В настоящее время большинство деревообрабатывающих станков с ЧПУ, как отечественного, так и импортного производства, изготавливаются без устройств, предназначенных для направления пыли и других измельченных отходов в системы аспирации, а паспорта старых станков не содержат аспирационных характеристик даже в тех случаях, когда пылеприемники установлены.
Схемы движения воздушных потоков в пылеприемниках различаются (рис. 4).
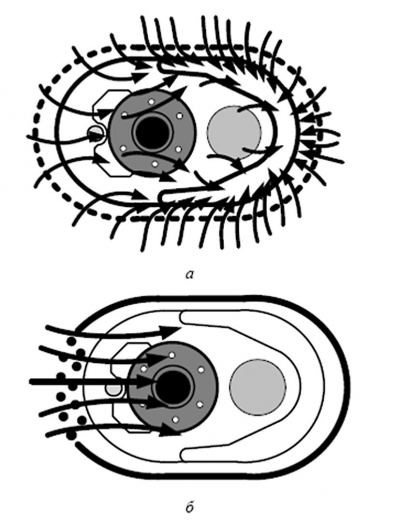
Щеточное, пленочное или иное не плотное основание пылеприемника резко увеличивает подсос воздуха из цеха и снижает эффективность удаления мягких отходов из зоны резания.
Варианты конструкций пылеприемников зависят от вида оборудования (рис. 5 и 6).
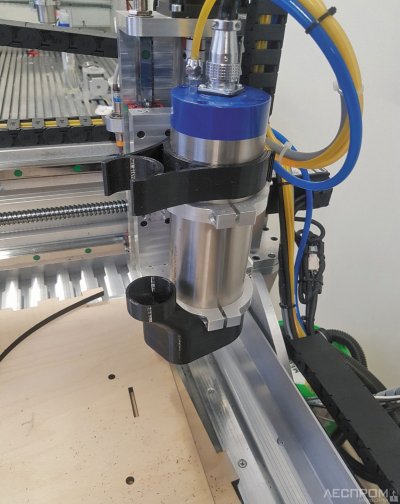
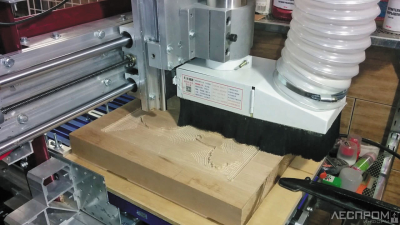
Таким образом…
В результате экспериментов установлено, что стойкость твердосплавных режущих элементов (зубьев) концевого фрезерного инструмента зависит от следующих характеристик:
- частоты вращения концевой фрезы или скорости резания (эта зависимость наиболее выражена при раскрое ДСтП);
- твердости материала, из которого выполнены зубья фрез; так, при уменьшении зернистости твердого сплава стойкость резцов повышается;
- скорости подачи и количества зубьев фрезы, а также их формы и расположения на корпусе фрезы, например, фрезы с прямыми лезвиями, в отличие от спиральных фрез, тупятся быстрее, что связано с ударными нагрузками;
- эффективности удаления отходов из зоны резания вследствие уменьшения вторичного измельчения стружки в зоне обработки;
- угловых параметров и качества заточки фрез: острые углы быстрее тупятся, чем тупые.
Увеличить стойкость зубьев можно с помощью осцилляции – постоянного перемещения фрезы попеременно вверх и вниз относительно заготовки, за счет участия во фрезеровании большего числа зубьев. Правда, такая операция возможна только при обгонке (обработке) заготовок по контуру.
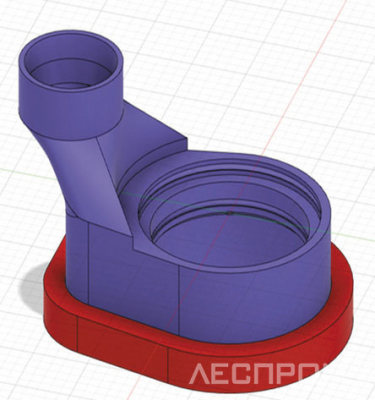
Текст Владимир Падерин