Ресурсосберегающая технология переработки макулатуры. Часть 10
Сгущение и диспергирование макулатурной массы
Продолжение. Начало в № № 3, 5−8 2006 г., № № 1, 3−5 2007 г.
В этой статье мы продолжаем тему диспергирования, начатую в прошлом номере журнала «ЛесПромИнформ». Цель диспергирования − создание условий, при которых частицы печатной краски, меловальных покрытий и липких загрязнений могут быть удалены при последующих операциях технологического процесса подготовки макулатурной массы.
В ходе диспергирования происходит разрушение частиц печатной краски и/или тонирующих веществ до размеров, невидимых невооруженным глазом; размягчение легкоплавких неволокнистых примесей и их равномерное распределение на волокнах в таком состоянии, при котором они не оказывают вредного влияния на процесс производства бумаги и картона.
Задачи диспергирования макулатурной массы:
- отделение от волокон частиц печатной краски и/или тонирующих веществ для последующего удаления при промывке и/или флотации;
- разрушение частиц проклеивающих веществ и меловальных покрытий;
- измельчение липких загрязнений до мелкодисперсного состояния и их распределение в массе;
- механическая обработка волокон − размол − для повышения прочности бумаги;
- термическая обработка волокон для повышения пухлости бумаги;
- смешивание отбеливающих реагентов с массой;
- стерилизация массы.
В таблице 1 приведены задачи диспергирования для различных видов бумаги, производимых из макулатурной массы.
При диспергировании макулатурной массы подвергается механическому воздействию в результате трения между размалывающими элементами диспергатора и между волокнами. Наличие большого зазора между элементами гарнитуры ротора и статора позволяет сохранить крупные посторонние примеси, такие как пленки, пластики, резина, металлические включения и другие, без измельчения. При этом частицы липких загрязнений под действием усилий сдвига подвергаются разрушению, что приводит к их тонкодисперсному распределению в массе.
Оптимальный эффект диспергирования макулатурной массы достигается при концентрации 22−30 %, что требует повышенного УРЭ. При диспергировании можно одновременно проводить смешивание макулатурной массы с отбеливающими реагентами, что значительно уменьшает эксплуатационные расходы и позволяет исключить смеситель из технологической схемы отбелки макулатурной массы.
Эффективность диспергирования зависит от концентрации и состава макулатурной массы, температуры обработки, типа гарнитуры и окружной скорости ротора диспергатора.
Перед диспергированием необходимо подвергнуть макулатурную массу тщательной очистке от тяжелых и легких примесей, а также сгущению до концентрации 25−35 % а. с. в.
В зависимости от состава и температуры плавления примесей макулатурной массы используют два способа диспергирования: «холодное» (при атмосферном давлении и температуре до 95 °С) и «горячее», или термодиспергирование (при давлении 0,3−0,5 МПа и температуре 130−150 °С).
При «холодном» диспергировании макулатурной массы частицы липких загрязнений с низкой температурой плавления размягчаются и диспергируются, осаждаясь на волокнах. При температуре механической обработки ниже 100 °С нет необходимости в дополнительном размоле макулатурной массы.
Термодиспергирование макулатурной массы применяется при содержании посторонних веществ с температурой плавления более 100°С. Равномерное распределение на волокнах частиц липких загрязнений придает макулатурной массе водостойкость и оптически гомогенный состав. Кроме того, данная обработка способствует стерилизации массы. Следует учитывать, что термодиспергирование макулатурной массы приводит к ослаблению межволоконных связей и снижению показателей механической прочности. Для восстановления прочности после термодиспергирования макулатурной массы необходимо подвергнуть дополнительному размолу.
Применение термодиспергирования макулатурной массы значительно повышает удельный расход пара. Кроме того, интенсивное трение между волокнами сопровождается некоторым повышением температуры массы в диспергаторе.
Повышение концентрации массы при постоянной производительности диспергатора приводит к увеличению УРЭ. По мере увеличения зазора между размалывающими элементами диспергатора снижается УРЭ.
УРЭ на диспергирование макулатурной массы зависит от вида волокнистых полуфабрикатов, входящих в состав макулатурного сырья. При повышенном содержании небеленой сульфатной целлюлозы УРЭ возрастает. При обработке полностью разволокненной макулатурной массы УРЭ снижается на 20−35 %.
Эффективность диспергирования липких загрязнений зависит от величины УРЭ, при увеличении которого размер всех частиц примесей уменьшается ниже предела видимости. Повышение концентрации макулатурной массы при диспергировании при постоянном значении УРЭ способствует измельчению частиц липких веществ. Эффективность диспергирования макулатурной массы также зависит от температуры, так как частицы липких веществ легче диспергируются при температуре размягчения.
Увеличение окружной скорости ротора более 50 м/с не оказывает дополнительного воздействия на диспергирование частиц липких загрязнений, а при более высокой скорости наблюдается повышенный износ и истирание деталей оборудования узла диспергирования. Увеличение УРЭ до 120 кВт•ч/т повышает эффективность диспергирования макулатурной массы. Для последующего удаления из макулатурной массы частиц печатной краски необходимо увеличить УРЭ до 150 кВт•ч/т.
Добавление пероксида водорода при диспергировании макулатурной массы способствует отделению частиц печатной краски и липких загрязнений при уменьшении их размеров. Для отделения обычной печатной краски от волокна преимущественно используется дисковый диспергатор, а при переработке макулатуры из бумаги с флексографической печатью − растирающий диспергатор.
Выбор системы диспергирования макулатурной массы зависит от состава макулатуры, температуры плавления содержащихся в ней примесей и требований к качеству конечного продукта. Термодиспергирование макулатурной массы целесообразно применять в технологических схемах переработки макулатуры только в отдельных случаях.
Диспергирование получило применение в процессе переработки макулатуры, поскольку обеспечивает отделение частиц печатной краски от волокна при сохранении высокого выхода макулатурной массы за счет отсутствия отходов. Существуют два варианта диспергирования:
- высокоскоростное диспергирование макулатурной массы в дисковом диспергаторе, создающем значительные усилия сдвига в тонком слое суспензии;
- низкоскоростное растирание макулатурной массы в растирающих диспергаторах, создающих в массе усилия сдвига умеренной величины в течение продолжительного времени.
Для диспергирования макулатурной массы используются диспергаторы двух типов: дисковые и растирающие. Диспергирование макулатурной массы в данных аппаратах отличается величиной усилий сдвига, создаваемых ротором, и значением окружной скорости ротора. Дисковый диспергатор имеет окружную скорость ротора 50−100 м/мин, растирающий диспергатор − 5−15 м/мин и менее. Расстояние между элементами гарнитуры ротора и статора в дисковых диспергаторах составляет 1 мм или менее, а в растирающих диспергаторах − 10 мм.
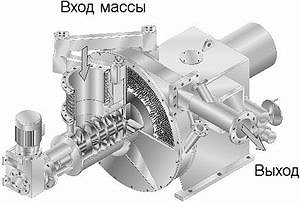
Рис. 1. Дисковый диспергатор
Дисковый диспергатор имеет размалывающую гарнитуру с пирамидальными зубьями или ножами. Под действием центробежной силы, создаваемой ротором, суспензия подается в зазор между гарнитурами ротора и статора в радиальном направлении. Эффект диспергирования макулатурной массы обеспечивается в результате трения между размалывающими элементами гарнитуры и за счет трения между волокнами и частицами примесей. На рисунке 1 представлена конструкция диспергатора, оснащенного гарнитурой с размалывающими элементами в виде зубьев. Эффект диспергирования зависит от величины УРЭ и концентрации массы.
Масса подается в дисковый диспергатор в зазор между дисками ротора и статора на зубчатые размалывающие элементы, которые располагаются на поверхности дисков в виде концентрических колец. Расстояние между размалывающими элементами не изменяется. При абразивном износе гарнитуры, который обнаруживается по снижению УРЭ и эффективности диспергирования, происходит увеличение зазора. Увеличение зазора между зубьями ротора и статора можно компенсировать повышением концентрации массы, поступающей в аппарат. Продолжительность диспергирования составляет 1−3 с. При «холодном» диспергировании масса свободно выходит из диспергатора и поступает в бассейн.
При термодиспергировании макулатурной массы нагревается насыщенным паром до температуры 130−150 °С при давлении 0,3−0,5 МПа в пропарочном питателе винтового типа. Теплообмен между конденсирующимся паром и макулатурной массы происходит при интенсивном перемешивании. В результате термической обработки массы с примесями, образующиеся летучие вещества испаряются, а остаток расплавленных примесей при механическом воздействии распределяется на волокнах.
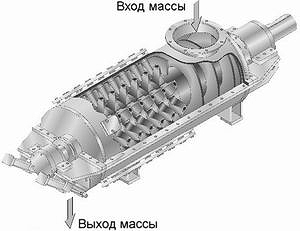
Рис. 2. Растирающий диспергатор с одним ротором
Растирающий диспергатор имеет горизонтальный цилиндрический корпус, внутри которого вращаются один или два ротора, оснащенных растирающими элементами в виде крылатки специальной формы. На внутренней поверхности корпуса аппарата дополнительно установлены элементы сопротивления движению потока массы. Усилия сдвига в растирающих диспергаторах возникают в результате интенсивного трения между волокнами при сопротивлении их движению в гарнитуре статора.
На рисунке 2 представлен растирающий диспергатор с одним ротором, имеющим ромбообразные крылатки. Статор диспергатора оснащен цилиндрическими элементами сопротивления. Регулирование УРЭ осуществляется за счет изменения окружной скорости ротора. Растирающий диспергатор может иметь два ротора. Крылатки ротора вращаются в разных направлениях и обеспечивают дополнительное сопротивление прохождению массы через аппарат.
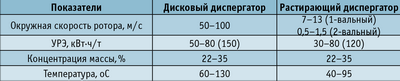
В таблице 2 представлены основные характеристики дисковых и растирающих диспергаторов. Оптимальный выбор типа диспергатора определяется условиями его эксплуатации и задачей диспергирования макулатурной массы.
Использование дискового диспергатора обеспечивает более эффективное уменьшение размеров частиц липких загрязнений, чем в растирающем диспергаторе, при этом образуются коллоидные частицы, устойчивые к агломерации. При диспергировании в растирающем диспергаторе сохраняются крупные частицы липких загрязнений, которые затем могут быть удалены при последующем сортировании макулатурной массы. Иногда для решения проблемы липких загрязнений и улучшения оптических свойств макулатурной массы вместо диспергирования применяют тонкое сортирование на сортировках с шириной щелей 0,15−0,25 мм.
В технологической схеме переработки вторичного волокнистого сырья диспергирование макулатурной массы, как правило, осуществляется перед флотацией или промывкой. При повышенных требованиях к качеству макулатурной массы диспергирование осуществляют в две ступени с использованием диспергаторов одного или различных типов.
При двухступенчатом диспергировании макулатурной массы на первой ступени обычно используют дисковый диспергатор, на второй ступени в конце технологической линии может быть установлен дисковый или растирающий диспергатор для обработки макулатурной массы перед второй ступенью флотации или промывки. При этом все примеси, в том числе оставшиеся на волокнах частицы печатной краски, измельчаются до незначительных размеров.
Применение дисковых диспергаторов, эксплуатируемых в режиме «холодного» диспергирования, позволяет несколько увеличить степень помола макулатурной массы, что приводит к повышению показателей её механической прочности. Растирающие диспергаторы работают при обычной температуре, и их применение практически не оказывает влияние на изменение степени помола макулатурной массы.
«Холодные» диспергаторы используются для окончательного разволокнения макулатурной массы после её сортирования и сгущения, а также перед сгущением отходов тонкого сортирования для снижения потери волокна.
Требования, предъявляемые к оборудованию узла диспергирования макулатурной массы, в значительной степени определяются не только свойствами используемого макулатурного сырья, но и требованиями к качеству макулатурной массы.
и размоле

Размол и диспергирование являются эффективными способами повышения качества макулатурной массы и улучшения безобрывности работы БДМ. Непрерывное совершенствование технологии переработки макулатуры приводит к их взаимозаменяемости (табл. 3).
Диспергирование макулатурной массы осуществляется при повышенном УРЭ и расходе пара, при размоле LC происходит измельчение волокон. Диспергирование способствует отделению частиц печатной краски и липких загрязнений от волокна. При размоле макулатурной массы частицы липких загрязнений образуют агломераты.
Сопротивление разрыву макулатурной массы повышается при использовании обеих операций. При переработке макулатуры из гофротары (ОСС) диспергирование макулатурной массы эффективнее для повышения прочности на разрыв и раздирание.
Включение в технологическую схему диспергирования макулатурной массы требует значительно больших капиталовложений, чем размол, но придает макулатурной массе свойства, которые не обеспечиваются размолом. Поэтому иногда предусматривают включение обеих операций в технологическую схему переработки макулатуры.
Узел диспергирования макулатурной массы включает диспергатор, винтовой пресс для сгущения массы, пропарочный питатель и винтовые питатели для транспортировки массы высокой концентрации. Перед диспергированием масса подвергается сгущению в винтовом (шнековом) или двухсеточном прессе. Повышение температуры массы производится с помощью подачи пара в пропарочный питатель винтового типа, что несколько снижает концентрацию массы за счет конденсации пара. Подача массы высокой концентрации в диспергатор осуществляется с помощью винтовых питателей.
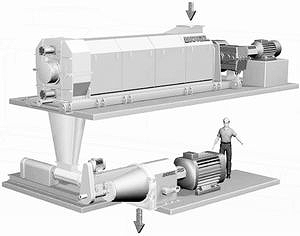
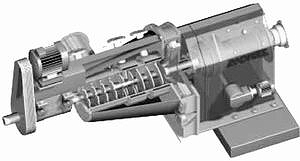
Рис. 3. Узел диспергирования фирмы Andritz
В узле диспергирования макулатурной массы фирмы Andritz подогрев и подача макулатурной массы в диспергатор объединены в одном компактном аппарате (рис. 3). По сравнению с традиционными системами узел диспергирования макулатурной массы фирмы Andritz занимает значительно меньшую площадь, а уменьшение количества оборудования приводит к снижению затрат на эксплуатацию и техническое обслуживание.
В зависимости от требований, предъявляемых к макулатурной массе, в узле диспергирования фирмы Andritz применяются дисковый диспергатор типа CompaDis™ или растирающий диспергатор типа TwinKneader™, выполняющие основную задачу по отделению частиц печатной краски и липких примесей от волокна.
Дисковый диспергатор типа CompaDis эксплуатируется при высокой скорости и пониженном УРЭ. Аппарат может использоваться при подготовке качественной макулатурной массы, применяемой в композиции писче-печатных видов бумаги. Узел диспергирования макулатурной массы, имеющий в своем составе данный аппарат, может эксплуатироваться при повышенном давлении. Производительность аппарата составляет от 50 до 1200 т/сут, УРЭ − 30−120 кВт•ч/т, температура диспергирования − 50−130°С, концентрация массы на выходе из аппарата − 5−30%.
Аппарат типа TwinKneader фирмы Andritz − растирающий диспергатор с двойным ротором для перемешивания макулатурной массы высокой концентрации. В нем также производится отделение от волокон частиц печатной краски и других загрязнений, которые затем удаляются из макулатурной массы на последующих ступенях технологической схемы. Производительность аппарата составляет от 100 до 400 т/сут, УРЭ − до 120 кВт•ч/т, температура диспергирования − 40−95 °С, концентрация массы на выходе из аппарата − 25−30 %.
Диспергаторы фирмы Andritz могут выполнять дополнительные функции в процессе переработки макулатуры: используются для смешивания отбеливающих реагентов с макулатурной массой перед заключительной ступенью переработки макулатуры − отбелке; повышают показатели механической прочности волокна и обеспечивают обеззараживание массы от микроорганизмов.
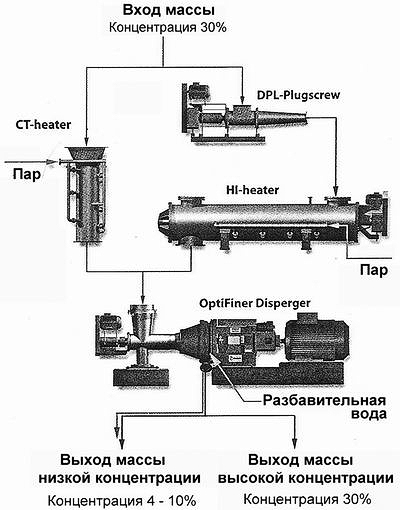
Рис. 4. Узел диспергирования типа OptiFiner Dispersion
Узел диспергирования макулатурной массы типа OptiFiner™ Dispersion фирмы Metso Paper оснащен коническим диспергатором типа OptiFiner Disperger (рис. 4). Данный узел может эксплуатироваться как в режиме холодного диспергирования, так и термодиспергирования. Диспергирование макулатурной массы с низким содержанием частиц печатной краски и липких загрязнений осуществляется при атмосферном давлении и температуре 80−90°С, при этом суспензия концентрацией 30% поступает в диспергатор после кратковременной обработки в течение 3−5 с в винтовом нагревателе типа CT-heater.
В случае термодиспергирования суспензия концентрацией 30% тщательно перемешивается в аппарате типа DPL-Plugscrew, который служит для предотвращения потери пара и давления в винтовом нагревателе типа HI-heater. Обработка макулатурной массы с высоким содержанием липких загрязнений в данном нагревателе производится в течение 20−30 с. Термодиспергирование макулатурной массы осуществляется при температуре 90−120°С и давлении до 100 кПа.
Узел диспергирования типа Creama фирмы Cellwood Machinery состоит из зон сгущения, подогрева и диспергирования. В зоне обезвоживания масса подвергается обезвоживанию в две ступени: в наклонном винтовом прессе − до концентрации 12%, в горизонтальном винтовом прессе − до 25−35 %. При сгущении происходит уменьшение содержания зольных элементов в макулатурной массе на 30−40 %.
Из зоны сгущения масса с помощью конусообразного винтового питателя (шнека) направляется в пропарочную камеру, которая представляет собой цилиндр, в полости которого вращается винт. Основная функция зоны подогрева массы − размягчить или расплавить различные включения, содержащиеся в макулатурной массе. Пар в камеру подается через специальные патрубки.
Пропарочная камера одновременно может быть использована для отбелки макулатурной массы, в этом случае отбеливающие реагенты (пероксид водорода, FAS и другие) подаются через патрубок, установленный до винтового питателя. Продолжительность обработки макулатурной массы в пропарочной камере при температуре 90−120°С составляет 2 мин. Сочетание воздействия повышенной температуры и химических реагентов при интенсивном перемешивании макулатурной массы позволяет производить отбелку без использования дополнительного оборудования. Расход пара составляет 400 кг/т.
В зону диспергирования масса поступает через загрузочный винтовой питатель. Дисковый диспергатор типа Creama оснащен гарнитурой из наборных сегментов с зубьями. Зазор между гарнитурами статора и ротора может составлять 0,05−0,5 мм. При диспергировании степень помола макулатурной массы повышается незначительно − на 2−3°ШР. В полость диспергатора может подаваться вода для разбавления массы до концентрации 3−12%, что позволяет сократить количество насосов и бассейнов. Расход энергии на диспергирование массы составляет 35 кВт•ч/т.
Производительность узла диспергирования Creama составляет от 15 до 800 т/сут при УРЭ 60−65 кВт/т. Использование данного узла диспергирования позволяет перерабатывать влагопрочные виды макулатурного сырья и исключить из технологической схемы размол макулатурной массы, так как при необходимости можно повысить степень помола массы на 10−12°ШР.
Сергей ПУЗЫРЕВ, профессор
Сергей Сергеевич Пузырев (19.09.1944−22.07.2007)
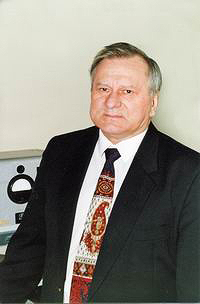
Ушел из жизни профессор Сергей Сергеевич Пузырев, наш постоянный автор и консультант. В журнале он выступал с циклом статей по целлюлозно-бумажному производству. Жизнь Сергея Сергеевича Пузырева оборвалась неожиданно, остались нереализованными многие совместные проекты − по выпуску изданий, разработок тем, поездок за границу. В этом номере мы посмертно публикуем его статью из цикла «Ресурсосберегающая технология переработки макулатуры».
22 июля 2007 года прервался жизненный путь профессора С. С. Пузырева. Многие любили его, и многие ненавидели. Непростой характер, острый язык, способность мыслить масштабно, мечтать неограниченно, смотреть на вещи и явления глубоко, проницательно и с юмором − вот основные качества личности профессора С. С. Пузырева.
Потомственный «бумажник», он прошел путь от студента и аспиранта до заведующего кафедрой целлюлозно-бумажного производства Ленинградской лесотехнической академии. Вся жизнь профессора С. С. Пузырева была посвящена совершенствованию технологии производства волокнистых полуфабрикатов и бумаги. Основное внимание он уделял развитию производства механической древесной массы, чему посвятил 3 монографии. На консультацию к нему приезжали многие производственники, аспиранты и магистры.
В общей сложности профессор С. С. Пузырев подготовил более 150 инженеров, 22 магистра и 4 кандидата технических наук. В списке его научных работ 4 монографии и более 300 публикаций, в том числе и подготовленных к публикации в настоящее время.
Основной труд последних лет − монография «Переработка вторичного волокнистого сырья», подготовленная в соавторстве с доцентом О. П. Ковалевой и руководителями ЦНИИБ Е. Т. Тюриным и В. А. Волковым, − является долгожданным пособием для переработчиков макулатуры и специалистов по производству картонно-бумажной продукции из вторичного сырья.
В книге широко представлены основные положения современной технологии переработки макулатурного сырья, основанные на достижениях ведущих фирм − производителей технологического оборудования. Профессор С. С. Пузырев тесно сотрудничал с представителями фирм Voith Paper (Германия), Metso Paper (Финляндия), Andritz (Австрия), PAPCEL (Чехия) и многими другими.
Внедрение нового высокоэффективного и ресурсосберегающего оборудования на предприятиях целлюлозно-бумажной промышленности с целью повышения качества отечественной продукции являлось чрезвычайной заботой этого человека. С большой любовью и трепетом профессор С. С. Пузырев передавал свои знания подрастающему поколению, воспитал и взрастил многих талантливых специалистов, преданных целлюлозно-бумажному производству.
Вечная память и благодарность учеников, коллег и партнеров одному из последних могикан эпохи «развитого» социализма, посвятившему свою жизнь подготовке специалистов и развитию технологии целлюлозно-бумажного производства.
С горечью утраты, друзья и коллеги
Статьи из цикла «Ресурсосберегающая технология переработки макулатуры»:
Ресурсосберегающая технология переработки макулатуры. Часть 13
Ресурсосберегающая технология переработки макулатуры. Часть 12.2
Ресурсосберегающая технология переработки макулатуры. Часть 12.1
Ресурсосберегающая технология переработки макулатуры. Часть 11
Ресурсосберегающая технология переработки макулатуры. Часть 9
Ресурсосберегающая технология переработки макулатуры. Часть 8
Ресурсосберегающая технология переработки макулатуры. Часть 7
Ресурсосберегающая технология переработки макулатуры. Часть 6
Ресурсосберегающая технология переработки макулатуры. Часть 5
Ресурсосберегающая технология переработки макулатуры. Часть 4
Ресурсосберегающая технология переработки макулатуры. Часть 3
Ресурсосберегающая технология переработки макулатуры. Часть 2
Ресурсосберегающая технология переработки макулатуры. Часть 1