Ресурсосберегающая технология переработки макулатуры. Часть 8
Удаление печатной краски
Продолжение. Начало в № № 3, 5−8 2006 г., № № 1,3 2007 г.
Идея «безбумажного офиса» уже сейчас кажется очередным растаявшим миражом времен Интернет-бума. Перспективы выглядели многообещающими: традиционная почта, ползущая к нам черепашьим шагом, вот-вот отомрет, а вместе с ней уйдет в небытие и сама бумага – продукт дорогой и неэкологичный в изготовлении. Случилось обратное: с развитием Интернета к тем грудам бумаги, которые уже громоздились в офисах, прибавились новые. Кроме обычной переписки, внутренней и внешней, сотрудники офисов имеют обыкновение складывать у себя на столах распечатанные на принтере листки электронной почты. Страницы, которые они просматривают в Интернете, для удобства обычно тоже распечатываются. Что делать дальше со всей этой бумагой? Как показывает опыт, основная часть бумаг, с которыми имеет дело сотрудник любого офиса, – документы одноразового использования, которые просятся в мусорную корзину немедленно после прочтения. Бюрократическая шелуха, бумажный сор – все эти циркуляры, меморандумы, рекомендации и предписания, немедленно после получения превращающиеся в туалетную бумагу, – требуют обязательного выкидывания, а то и уничтожения в специальной машине, именуемой шреддером. Однако некоторые люди неспособны оценить важность той или иной бумаги в иерархии корпоративных ценностей. У подобных людей бумажные горы на столах растут лавинообразно. Каждую вновь поступившую бумажку такой сотрудник автоматически кладет сверху, на громоздящуюся кипу, за которой порой не видно его самого. Он просто не верит, что успеет внимательно прочесть каждый документ, и оставляет все на случай, если там вдруг окажется что-то важное. Горы высятся, по-настоящему нужные бумаги теряются, срочные и бессмысленные путаются между собой. Но бумажные горы не могут расти бесконечно, так как они ограничены размером офиса. Все равно таким информационным плюшкиным приходится иногда делать чистку и полностью разбирать свои «волокнистые горы». И тут на помощь приходят технологии переработки макулатуры и, в частности, технологии удаления печатной краски. Именно они способны превратить весь этот бело-черный мусор в девственно чистую поверхность, в «табула раса», которую можно вновь замарать лазерным напылением всевозможных оттенков или краской черно-белого струйника, если дела в вашей фирме обстоят не так хорошо. Именно таким образом Вы замкнете цепочку, которая именуется «Круговорот чистой бумаги в производстве».
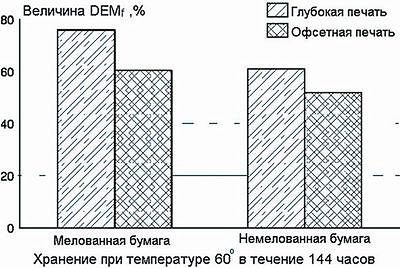
Рис. 1. Эффективность удаления печатной краски из макулатурной массы в зависимости от марки макулатуры и вида печатной краски
В макулатурном сырье могут содержаться частицы печатной краски, которые не удаляются из макулатурной массы при очистке, сортировании, диспергировании и других технологических операциях. Удаление из волокнистой суспензии частиц печатной краски, предварительно отделенных от волокон при диспергировании, а также последующее обесцвечивание или отбелка макулатурной массы (ММ) занимают важное место в технологии переработки макулатуры при получении высококачественного полуфабриката, применяемого при производстве писче-печатных и санитарно-бытовых видов бумаги. Совокупность данных операций – диспергирования, удаления печатной краски и отбелки – в отечественной литературе называется облагораживанием макулатурной массы.
Удаление печатной краски из макулатурной массы – облагораживание (deinking) – с целью улучшения оптических свойств полуфабриката производится методом флотации или промывки.
Макулатурная масса, из которой удалена печатная краска, называется облагороженной (DIP – deinked pulp) и, как правило, после отбелки используется для изготовления писче-печатных и санитарно-бытовых видов бумаги (tissue), а также покровных слоев (top liners) картона типа тест-лайнера (white lined chipboard).
Удаление печатной краски обычно осуществляется при переработке смеси газетной и журнальной макулатуры с содержанием механической древесной массы (МДМ), а также из офисной макулатуры без содержания механической древесной массы. В этом случае использование макулатуры низших марок, таких как упаковочные виды бумаги и картона, нежелательно, поскольку при этом значительно понижается белизна макулатурной массы.
Флотация представляет собой технологическую операцию по очистке волокнистой суспензии, основанную на способности гидрофобных частиц примесей прикрепляться к пузырькам воздуха и перемещаться вместе с ними к поверхности суспензии.
В бумажной промышленности применяют 2 типа флотации. Для удаления частиц печатной краски из волокнистой суспензии используется селективная флотация – облагораживание (deinking flotation). Микрофлотация, или флотация производственной воды с помощью растворенного воздуха (dissolved air flotation – DAF), используется с целью её очистки, улавливания волокна и удаления примесей, способных к флотации.
Для эффективного удаления частиц печатной краски в технологических схемах переработки макулатуры наряду с флотацией используют промывку макулатурной массы.
Промывка макулатурной массы – технологическая операция по удалению из суспензии определенных фракций твердых веществ – частиц примесей размером менее 30 мкм.
Удаление частиц печатной краски методом флотации, по сравнению с промывкой, является более сложной технологической операцией, требующей предварительной механической обработки макулатурной массы и применения специальных химических реагентов.
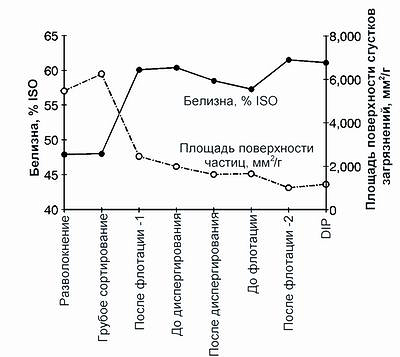
Рис. 2. Изменение белизны макулатурной массы и площади поверхности сгустков загрязнений при удалении печатной краски
С целью повышения эффективности облагораживания производится механическая и химическая подготовка макулатурной массы для отделения гидрофобных частиц от волокон.
Для отделения прочно закрепленных частиц печатной краски от волокна осуществляется диспергирование и/или растирание макулатурной массы. Диспергирование макулатурной массы используется для переработки макулатуры с частицами краски для офсетной или глубокой печати, а растирание более эффективно для обработки макулатурной массы из офисной макулатуры с частицами краски лазерных принтеров.
Механизм отделения частиц печатной краски от волокон включает: набухание волокон при увлажнении макулатуры, механическое воздействие на волокна, ослабление химических связей. Набухание волокон приводит к образованию трещин в пленке печатной краски и её разрушению. Механическая обработка макулатурной массы способствует отделению частиц печатной краски за счет трения между волокнами и воздействия на них гарнитуры диспергатора.
Следует учитывать, что при диспергировании/растирании несколько снижается белизна макулатурной массы вследствие адсорбции на волокнах измельченных частиц печатной краски.
Определяющими факторами облагораживания макулатурной массы являются эффективность отделения частиц печатной краски от волокон и скорость осаждения их на волокна. Чем меньше усилие сдвига при разволокнении макулатуры, тем медленнее происходит измельчение частиц печатной краски и их повторное осаждение на волокна, поскольку мелкие частицы адсорбируются более интенсивно. Задача разволокнения макулатуры заключается в ограничении степени измельчения посторонних примесей, в том числе частиц печатной краски.
Степень измельчения частиц печатной краски при разволокнении газетной макулатуры уменьшается при снижении величины рН до нейтрального значения. Поэтому вместо гидроксида натрия, силиката натрия и EDTA возможно применение сульфита натрия при разволокнении макулатуры в нейтральной среде.
Интенсивное диспергирование и размол макулатурной массы также приводит к повторному осаждению частиц печатной краски на волокна, поэтому более целесообразно использовать растирание волокнистой суспензии для измельчения частиц печатной краски до размеров, оптимальных для эффективного удаления методом флотации или промывки.
Поскольку удаление частиц тонирующих веществ размером 70−400 мкм затруднено, необходимо производить химическую обработку макулатурного сырья при разволокнении и растирании для измельчения частиц тонирующих веществ и флотацию макулатурной массы.
Крупные частицы тонирующих веществ можно отделить от волокнистой суспензии в гидроциклонах, при этом используются специальные химические реагенты, способствующие образованию агломератов частиц печатной краски.
Эффективность удаления печатной краски из макулатурной массы зависит от вида печатной краски и способа её сушки, наличия меловального покрытия, марки макулатуры и продолжительности её хранения.
Энзимы – липаза, эстераза, пектиназа, гемицеллюлозы, целлюлаза – наиболее эффективны для удаления органических красителей – тонирующих веществ. Они способствуют измельчению частиц печатной краски и препятствуют их повторному осаждению на волокнах.
Преимуществом использования энзимов является возможность исключения из технологической схемы переработки макулатуры операций сгущения и диспергирования, а также повторной флотации (постфлотации) и промывки макулатурной массы, что снижает УРЭ и затраты на оборудование для переработки макулатуры. Применение энзимов позволяет уменьшить расход отбеливающих реагентов и, следовательно, затраты на очистку производственной воды. Макулатурная масса, обработанная энзимами, обладает пониженным водоудержанием, что позволяет увеличить скорость БДМ.
Использование энзимов сдерживается их высокой стоимостью. Промышленное внедрение обработки макулатурной массы энзимами требует разработки вариантов их состава в зависимости от конкретных условий предприятия, использования новых технологий ферментации и очистки, а также увеличения общего объема их производства.
Состав макулатурного сырья определяет белизну волокнистого полуфабриката. Повышение белизны макулатурной массы из мелованной и немелованной макулатуры без содержания механической древесной массы после флотации составляет 17−22 %, из макулатуры с содержанием механической древесной массы – 8%. Это объясняется взаимодействием между лигнином и компонентами печатной краски и, как следствие, более интенсивным прикреплением частиц печатной краски к волокнам механической древесной массы. При обработке макулатурной массы с содержанием механической древесной массы образуется большое количество частиц печатной краски диаметром менее 30 мкм, что приводит к значительному снижению эффективности флотации.
При увеличении продолжительности хранения печатной продукции эффективность удаления из нее печатной краски может снижаться. Кроме фактора времени, на процесс старения бумаги и печатной краски могут оказывать влияние такие факторы окружающей среды, как температура, влажность и ультрафиолетовое излучение.
Белизна макулатурной массы с офсетной печатной краской снижается при увеличении продолжительности хранения макулатуры, что особенно характерно для макулатурной массы с низким содержанием наполнителя. Продолжительность хранения макулатурного сырья незначительно влияет на эффективность облагораживания макулатурной массы из газетной бумаги с высокой печатью.
Наличие меловального покрытия оказывает влияние на эффективность удаления частиц печатной краски из макулатурной массы, полученной после длительного хранения макулатуры. Частицы офсетной краски и краски для глубокой печати легко отделяются от волокон мелованной бумаги после продолжительного хранения. Хранение немелованной журнальной бумаги обусловливает снижение эффективности удаления частиц офсетной краски и незначительно влияет на эффективность удаления краски для глубокой печати.
Общий выход макулатурной массы после удаления печатной краски зависит от количества ступеней флотации и промывки. Твердые вещества, удаляемые при флотации, такие как частицы печатной краски, наполнителей, меловальных покрытий и липких загрязнений, мелкие волокна, присутствуют в пене – флотошламе. При промывке для расчета выхода макулатурной массы следует учитывать содержание твердых веществ в фильтрате.
На выход макулатурной массы оказывают влияние величина рН, расход воздуха и продолжительность флотации. В зависимости от состава макулатуры выход макулатурной массы после флотации составляет 85−90 %.
Степень разбавления и сгущения определяет выход макулатурной массы после промывки. При использовании промывки макулатурной массы с содержанием механической древесной массы выход волокнистого полуфабриката составляет 75−85 %.
На основании расчета количества отходов облагораживания и содержания зольных элементов в макулатурной массе определяется селективность удаления частиц печатной краски по отношению к удалению волокон.
Эффективность удаления печатной краски определяется по повышению белизны и чистоты макулатурной массы. Для оценки эффективности удаления печатной краски используют коэффициент эффективности удаления печатной краски – DEMf (deinkability factor). Данный показатель рассчитан из соотношения значений белизны облагороженной макулатурной массы, полученной из макулатуры без печати (unprinted deinked pulp – US), белизны макулатурной массы, полученной из запечатанной макулатуры без удаления печатной краски (printed undeinked pulp – BS), и белизны DIP:
DEMf = 100 (%)
Величина DEMf может составлять от 0 до 100%. Например, величина DEMf для ММ, полученной из немелованной макулатуры с офсетной печатью, равна 52%, с глубокой печатью – 60%; а для макулатурной массы, полученной из мелованной макулатуры, – 60 и 78 % соответственно. Значение 100 % соответствует полному удалению печатной краски из макулатурной массы. Следует учитывать, что данный показатель недостаточно полно характеризует оптические свойства DIP из макулатуры с цветной печатью.
Другим способом оценки эффективности облагораживания является определение значения остаточной концентрации печатной краски – ERIC (effective residual ink concentration). Данный способ предполагает измерение коэффициента отражения поверхности образца макулатурной массы в ИК-спектре при длине волны 950 нм, при этом свет поглощает только черная печатная краска.
Для оценки оптических свойств DIP используют коэффициент спектрального отражения R457, который определяют с помощью спектрофотометра. Данный показатель получают при сравнении интенсивности света, отраженного от образца бумаги при определенной величине угла луча света, и интенсивности света, который отражается от эталона белизны.
В целлюлозно-бумажной промышленности применяют 2 метода определения белизны, основанные на измерении коэффициента отражения образца бумаги или волокнистого полуфабриката при длине волны света 457 нм: стандартный метод TAPPI, широко используемый в Северной Америке, и метод ISO, используемый в Европе. Различие между этими методами заключается в геометрических параметрах падающего луча света. В методе TAPPI его величина равна 45°. Метод ISO предполагает диффузное освещение образца бумаги, то есть использование нескольких источников света. При измерении в обоих случаях используют угол отражения, равный 0°.
При использовании DIP для производства писче-печатных видов бумаги необходимо учитывать её колориметрические характеристики. Например, наличие в макулатурной массе синих пигментов, которые имеют интенсивное отражение при длине волны 440−480 нм, может исказить истинное значение коэффициента отражения. При измерении белизны по ISO необходимо контролировать долю ультрафиолетового излучения источника света, так как наличие оптических отбеливателей в DIP может оказывать влияние на значение коэффициента отражения.
Для оценки качества DIP используют систему анализа изображений, которая позволяет определить оптическую гетерогенность волокнистого полуфабриката. Сгустки загрязнений, присутствующие в DIP, контрастируют при сравнении с белым фоном и обнаруживаются с помощью сканера. Результаты исследований свидетельствуют о том, что после разволокнения макулатуры более 90% сгустков загрязнений в макулатурной массе имеют размер менее 50 мкм.
На рисунке 2 приведены данные по изменению белизны макулатурной массы и площади поверхности сгустков загрязнений на различных ступенях технологической схемы переработки макулатуры. По мере уменьшения площади поверхности сгустков загрязнений возрастает белизна макулатурной массы. Наибольшее повышение белизны макулатурной массы и соответственно уменьшение площади поверхности сгустков загрязнений происходит при флотации.
Поскольку при измельчении частиц печатной краски увеличивается количество сгустков загрязнений, после диспергирования наблюдается некоторое снижение белизны макулатурной массы. Однако согласно данным, представленным на рисунке 2, площадь поверхности сгустков загрязнений после диспергирования уменьшается, что объясняется тем, что частицы загрязнений не могли быть зарегистрированы прибором вследствие их незначительных размеров. Площадь поверхности сгустков загрязнений обычно выражают в мм2 на 1 м2 поверхности образца бумаги или на 1 г а. с. массы.
Как правило, наличие сгустков загрязнений имеет меньшее влияние на белизну волокнистого полуфабриката, но увеличивает оптическую гетерогенность макулатурной массы и полученной из нее бумаги.
В состав печатной краски входят связующие и красящие вещества, а также различные добавки. Связующие вещества – носители и связующие реагенты – формируют пленку печатной краски, прочно закрепляя пигменты на поверхности бумаги при сушке. Носители (растворители) растворяют твердые связующие реагенты и удерживают печатную краску в жидком состоянии. После нанесения печатной краски носители испаряются или абсорбируются на поверхности бумаги с образованием пленки. В качестве носителей применяются спирты, эфиры, гликоли и их производные, ацетон, углеводороды и вода.
Основой связующих реагентов природного происхождения являются канифоль, асфальт, битумы и синтетические связующие реагенты, которые представляют собой продукты полимеризации. Для печатных красок на основе воды используют акриловые дисперсии, акриловые или малеиновые смолы.
Способ сушки печатной краски оказывает решающее влияние на выбор связующего реагента и носителя, а также на эффективность облагораживания макулатурной массы. Способы сушки печатной краски подразделяются на физический – абсорбция на поверхности полотна или испарение растворителя – и химический – окисление или сушка под действием излучения энергии. При химических способах сушки связующий реагент подвергается окислению или полимеризации. Сушка краски под действием излучения энергии – ультрафиолетовое излучение или пучок электронов – происходит в течение долей секунды. Полимеризованные компоненты краски нерастворимы в большинстве растворителей, и их удаление из макулатурной массы затруднено.
Для эффективного облагораживания макулатурной массы связующие вещества печатной краски должны иметь ковалентную связь, слабые поперечные связи и низкую растворимость в щелочи. Разволокнение макулатуры может осуществляться в присутствии различных химических реагентов: гидроксида натрия, пероксида водорода, а также анионных и неионогенных ПАВ. Следует учитывать, что связующие вещества могут вступать в реакцию с данными химическими реагентами, что также оказывает влияние на эффективность облагораживания макулатурной массы.
Пигменты – плохо растворимые неорганические или органические вещества. Красители – растворимые органические вещества, редко используемые в печатных красках. Пигменты и красители определяют такие характеристики печатной продукции, как светостойкость, влагостойкость и устойчивость к воздействию щелочей, кислот и растворителей. Тонирующие пигменты или красители используются для придания краске определенного тона.
Размер частиц печатной краски является определяющим фактором для облагораживания макулатурной массы. После разволокнения макулатуры частицы флексографской печатной краски имеют меньшие размеры, чем частицы краски для высокой, офсетной и глубокой печати.
Следует учитывать, что размеры частиц печатной краски в значительной степени зависят от величины рН на различных ступенях технологического процесса переработки макулатуры. Эффективность облагораживания макулатурной массы в щелочной среде зависит от свойств пигментов: удаление гидрофобных пигментов происходит легче, чем гидрофильных.
Для улучшения свойств печатной краски, таких как сухость, блеск и устойчивость к внешним воздействиям, в её состав вносят различные добавки: осушающие реагенты, масла, воск, пластификаторы, смазки и диспергирующие вещества. Осушающий реагент является необходимым компонентом печатной краски и служит катализатором полимеризации связующих веществ. Выбор используемых добавок настолько разнообразен, что в настоящее время отсутствует конкретная информация о влиянии добавок на эффективность удаления печатной краски из макулатурной массы.
При разволокнении макулатуры печатная краска для струйной печати распределяется в суспензии в виде частиц малых размеров, которые трудно удаляются при флотации и могут вновь прикрепляться к волокну. При промывке эффективность удаления этих частиц улучшается незначительно. Использование восстановительных отбеливающих реагентов способствует разрушению хромофорных групп азокрасителей.
С. С. ПУЗЫРЕВ, проф., О. П. КОВАЛЕВА, доцент
Статьи из цикла «Ресурсосберегающая технология переработки макулатуры»:
Ресурсосберегающая технология переработки макулатуры. Часть 13
Ресурсосберегающая технология переработки макулатуры. Часть 12.2
Ресурсосберегающая технология переработки макулатуры. Часть 12.1
Ресурсосберегающая технология переработки макулатуры. Часть 11
Ресурсосберегающая технология переработки макулатуры. Часть 10
Ресурсосберегающая технология переработки макулатуры. Часть 9
Ресурсосберегающая технология переработки макулатуры. Часть 7
Ресурсосберегающая технология переработки макулатуры. Часть 6
Ресурсосберегающая технология переработки макулатуры. Часть 5
Ресурсосберегающая технология переработки макулатуры. Часть 4
Ресурсосберегающая технология переработки макулатуры. Часть 3
Ресурсосберегающая технология переработки макулатуры. Часть 2
Ресурсосберегающая технология переработки макулатуры. Часть 1