Сверлильно-присадочные станки
Устройство и оптимальный выбор
Современное производство мебели немыслимо без сверлильно-присадочных станков. Точное и быстрое сверление целых групп отверстий − основное условие безошибочной серийной сборки мебельных заготовок.
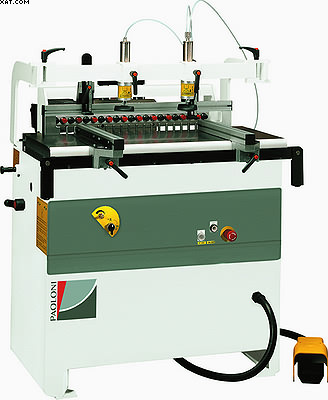
21-шпиндельный сверлильно-присадочный станок Paoloni F121
Актуальность использования сверлильно-присадочных станков в современном мебельном производстве обусловлена несколькими факторами. Во-первых, станки данного типа имеют высокую производительность за счет одновременного использования от двух до нескольких десятков единиц инструмента − сверл, зенковок, цековок и т.д. Во-вторых, все они четко ориентированы друг относительно друга, что дает неоспоримую точность сверления отверстий. В-третьих, практически все сверлильно-присадочные станки имеют удобную и понятную систему управления, что сокращает время на их освоение и переналадку.
Отверстия, получаемые с помощью сверлильно-присадочных станков, необходимы для установки мебельной фурнитуры − петель, опор, ручек и т. п., элементов крепления − шурупов, винтов, штифтов и т. д. Очевидно, что от качества и точности расположения таких отверстий зависит, как будут собираться тот или иной шкаф, стол или гардероб, какой у них будет внешний вид. Большая часть отверстий в мебельных заготовках участвует в размерных цепях, и смещение хотя бы одного из них на величину, превышающую позиционный допуск, может вызвать появление ступеньки, искажение геометрии готового изделия или вообще сделать его сборку невыполнимой. На практике допуски на мебельные размеры задаются по 11−13 квалитету в соответствии с ГОСТ 6449.1−82. Так, для размера 32 мм отклонения должны быть в пределах +0,19 мм (13 квалитет), для 320 мм − соответственно +0,28 мм (12 квалитет), а для 640 мм, например, +0,4 мм. Там, где изготовление и сборка мебели осуществляются в разных местах и в разное время, вопрос ее собираемости и вовсе приобретает ключевое значение − мебельные комплекты могут вернуть на завод-изготовитель как бракованные из-за невозможности их сборки.
В основе работы сверлильно-присадочных станков положен принцип агрегатирования, когда в операции участвуют сразу множество инструментов осевого типа − сверл различного диаметра, цековок, зенковок. Все они устанавливаются в специальный агрегат, называемый многошпиндельной сверлильной головкой. Однако соответствующее использование данных агрегатов с учетом требований технологического процесса заставляет задуматься о правильности выбора сверлильно-присадочного станка, и только знание его особенностей и устройства позволяют достигнуть требуемого высокого результата.
Типы сверлильно-присадочных станков
Для сравнения предлагается описание устройства сверлильно-присадочных станков трех основных типов. Открывают ряд станки позиционного типа с одной многошпиндельной головкой (рис. 2). Обрабатываемая деталь, а это чаще всего плита (ДСтП, MDF и др.), устанавливается на рабочий стол (поз. 3, рис. 2) с помощью позиционной линейки с упорами (поз. 5, рис. 2) и пневматических прижимов (поз. 4, рис. 2). Это позволяет четко ориентировать заготовку относительно инструмента и надежно фиксировать ее во время обработки. После фиксации стартует рабочий цикл: многошпиндельная головка (поз. 2, рис. 3) вместе с инструментом подается к кромке детали (поз. 1, рис. 2), выставленной по упору (поз. 3, рис. 3). Скорость подачи 5−10 м/мин не оказывает особого влияния на производительность, так как глубина отверстий − в среднем 20−40 мм. Дойдя до конечной точки, многошпиндельная головка возвращается в исходное положение. Оператор, используя пульт управления, отключает прижим, снимает деталь с отверстиями и устанавливает новую.
Универсальность станку придает поворотный механизм, который позволяет в процессе наладки наклонять многошпиндельную головку на 90°. Это позволяет обрабатывать детали со скошенными кромками, а также сверлить отверстия в пласти (рис. 4). Для этого на рабочем столе (поз. 2, рис. 4) предусмотрены специальные пазы, позволяющие проходить инструменту снизу вверх. Принцип сверления пласти такой же, как и при обработке кромки. Такие сверлильно-присадочные станки имеют небольшие габариты и хорошо зарекомендовали себя на небольших предприятиях, с ограниченными сериями разнообразных заготовок.
Следующая модификация − это сверлильно-присадочные станки с несколькими многошпиндельными головками. Они имеют оптимальный набор исполнительных устройств. Наиболее типичная компоновка такого оборудования представлена на рис. 5. Для обработки кромки используется одна горизонтальная головка (поз. 1, рис. 5), а для сверления отверстий в пласти 2−3 вертикальные (поз. 2, рис. 5). Все они, вместе с механизмами подачи и позиционирования, размещаются в специальной станине (поз. 5, рис. 5). Станина оснащена опорными планками (поз. 3, рис. 5) с позиционными упорами, которые служат для определенной ориентации детали относительно групп инструментов. Плита устанавливается на планки (поз. 3, рис. 5) по упорам и надежно фиксируется пневматическими прижимами (поз. 4, рис. 5). Затем все многошпиндельные головки одновременно совершают рабочий цикл, подавая вращающийся инструмент (поз. 2, рис. 6) к детали (поз. 1, рис. 6).
Станки, оснащенные несколькими многошпиндельными головками, относятся к более дорогому ценовому сегменту, что дает возможность разработчикам использовать в конструкции полезные опции − средства адаптивного контроля, электронные датчики положения, приводы с регулируемой частотой и скоростью, что позволяет повысить качество обработки, оптимизировать режимы сверления и снизить риск поломки оборудования.
Главные отличия данного вида сверлильно-присадочных станков от универсальных моделей с одной головкой:
1. Головки позиционируются автоматически, за счет централизованной электронной системы управления, что сокращает время на переналадку и повышает точность настройки.
2. Деталь одновременно обрабатывается как со стороны кромки, так и со стороны пласти несколькими головками, что повышает производительность и точность обработки. Не требуется перестройки станка и повторной обработки партии сложных деталей с их неизбежной переустановкой.
3. Вертикальные многошпиндельные головки (поз. 2, рис. 5), помимо описанных движений, могут поворачиваться относительно оси главного привода. Это расширяет диапазон применимости станков с такими головками: линии, на которых располагаются отверстия, могут быть не только параллельными, но и под углом в плане.
4. Опорные планки (поз. 3, рис. 5) могут оснащаться механизмом загрузки-выгрузки заготовок, что исключает ручную установку детали перед обработкой и ее снятие тем же способом. Сверлильно-присадочные станки с автоматизированной подачей считаются станками позиционно-проходного типа и могут встраиваться в поточные технологические линии.
Современные мебельные производства оснащаются технологическими модулями проходного типа для сверления множества отверстий в заготовках из древесины без ее остановки. Такой модуль способен обрабатывать деталь в процессе ее движения на конвейере. Это дает дополнительный выигрыш во времени и полностью исключает ручной труд во время рабочего цикла.
Но какими бы ни были сверлильно-присадочные станки, многошпиндельная сверлильная головка остается для них главным и характерным агрегатом.
Многошпиндельная сверлильная головка
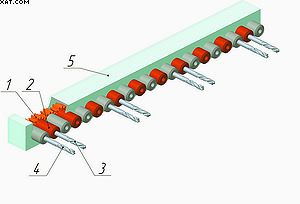
Рис. 1. Многошпиндельная сверлильная головка.
1 – шестерня; 2 – шпиндель;
3 – сверло с «левым» направлением вращения;
4 – сверло с «правым» направлением вращения;
5 – корпус
Многошпиндельная сверлильная головка (рис. 1) состоит из ряда шпинделей (поз. 2, рис. 1). Расстояние между шпинделями строго одинаковое − 32 мм. Этого параметра придерживается подавляющее большинство производителей сверлильно-присадочных станков. Неслучайно в мебельных конструкциях позиционные размеры отверстий кратны 32 мм. Исключение составляют специальные головки, предназначенные, например, для сверления отверстий под петлю на фасаде, где расстояние между ними задает изготовитель фурнитуры.
Вращение в шпиндельной головке от электропривода к каждому шпинделю передается посредством шестерен (поз. 1, рис. 1), расположенных внутри корпуса (поз. 5, рис. 1) головки, мощностью 1−1,5 кВт. Головка может комплектоваться и двумя двигателями, в зависимости от числа шпинделей. Такая кинематическая схема предопределяет разнонаправленное вращение смежных шпинделей − одни вращаются в правую, другие − в левую сторону. Как следствие, в качестве инструмента используются, например, сверла с «левым» (поз. 3, рис. 1) и «правым» (поз. 4, рис. 1) направлением вращения. Для удобства соответствующие шпиндели маркируются метками разного цвета.
Частота вращения шпинделей поддерживается на уровне 2800 об/мин для нормальной работы сверл. Наиболее распространенное число шпинделей в многошпиндельных головках − 21 и 27, но может доходить и до 39 и более. В таких агрегатах расстояние между осями крайних шпинделей соответственно 640, 832 или 1216 мм. Каждый шпиндель устроен таким образом, что может быстро зажать хвостовик инструмента. В целях унификации шпиндели в многошпиндельных головках рассчитаны на диаметр хвостовика 5 или 10 мм.
Многошпиндельная головка присоединяется к станку через устройство подачи, состоящее из коротких направляющих и пневмопривода подачи. Величина подачи − рабочий ход многошпиндельной сверлильной головки вдоль оси инструмента − настраивается с помощью упоров или электронных датчиков положения и может быть в пределах 40−90 мм. Эта величина предопределяет максимальную глубину получаемых отверстий.
Эффективность использования многошпиндельной головки во многом зависит от особенности устройства станка, метода позиционирования заготовки и подготовительных мероприятий, необходимых для настройки оборудования на обработку конкретной партии деталей.
Область применения и качество работы сверлильно-присадочных станков
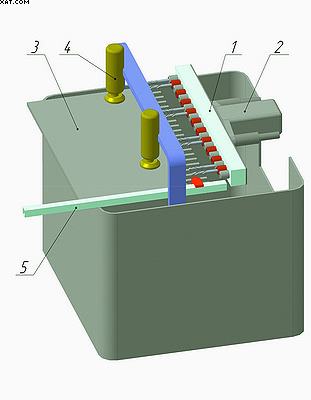
Рис. 2. Сверлильно- присадочный станок позиционного
типа (упрощенная схема).
1 – многошпиндельная сверлильная головка;
2 – привод; 3 – рабочий стол;
4 – пневматические прижимы;
5 – позиционная линейка с упором.
Для сверления деталей в серийном мебельном производстве используют группы различных сверлильно-присадочных станков. Наравне с оборудованием, оснащенным несколькими многошпиндельными головками (рис. 5), могут применяться универсальные, с одной головкой. Дело в том, что на практике часто бывает целесообразно организовать несколько сверлильных участков, чтобы сократить объем перемещаемых полуфабрикатов в пределах деревообрабатывающего цеха. Кроме того, около каждого сверлильно-присадочного станка организуется зона накопления заготовок и деталей, прошедших обработку. В массовом производстве перегрузка таких зон за счет поступлений с нескольких участков опасна заторами, что требует соответствующего перераспределения деталей по нескольким зонам. Наличие нескольких сверлильно-присадочных станков также выгодно тем, что в случае поломки или длительной настройки одного другой может принять технологический поток на себя и тем самым исключить простой производства. Комплектация производства сверлильно-присадочными станками зависит также от уровня его автоматизации в целом. Там, где организован централизованный единый канал управления всем технологическим процессом, эффективно использовать станки с несколькими многошпиндельными головками и электронным управлением. В этом случае, помимо экономии времени на подготовку к операции, пользователь снижает риск ошибки, так как вся информация поступает в станок транзитом, без потерь и искажений.
Выбор сверлильно-присадочных станков по характеру позиционирования заготовки всецело зависит от объемов производства. Для малых и средних серий вполне оправдывают себя станки позиционного типа. Время, затрачиваемое на установку и снятие заготовки после сверления, вполне укладывается в общий производственный регламент такого масштаба.
Для среднесерийного мебельного цеха, как правило, выбирается оборудование позиционно-проходного типа. Там требуется сверление больших серий деталей. Переход от позиционных к позиционно-проходным станкам позволит сократить время цикла на 30−50%, так как загрузка и разгрузка в данном виде оборудования производится механизированным способом. При соответствующей стыковке к основным транспортным потокам перед пользователем открывается перспектива сократить долю ручного труда не только на участке сверления, но и в рамках всего производства. Такой эффект особенно ощутим при выпуске мебели эконом-класса, где борьба за снижение себестоимости приобретает особенное значение.
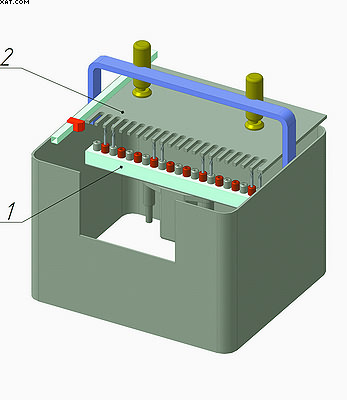
Рис. 4. Настройка станка для сверления пласти.
1 – многошпиндельная сверлильная головка в вертикальном
положении; 2 – рабочий стол
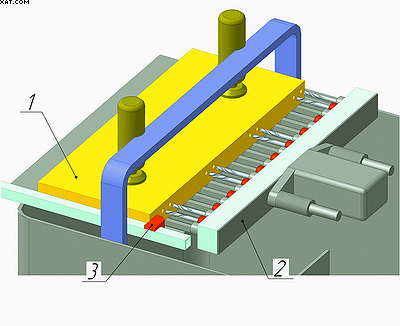
Рис. 3. Сверление отверстий в торце заготовки.
1 – заготовка; 2 – многошпиндельная сверлильная головка; 3 – упор
Различные сверлильно-присадочные станки имеют общие методики оценки качества их работы. Это объясняется тем, что в основе каждого из них используются многошпиндельные сверлильные головки, схожие по своему устройству. Вот только некоторые виды проверки работоспособности сверлильно-присадочных станков.
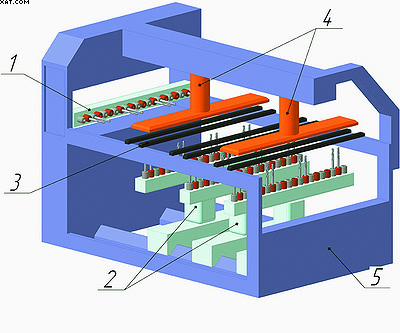
Рис. 5. Сверлильно-присадочный станок с различными
многошпиндельными головками (упрощенная схема).
1 – горизонтальная многошпиндельная сверлильная головка;
2 – вертикальные сверлильные головки;
3 – опорные планки; 4 – пневматические прижимы; 5 – станина
Диаметр получаемых отверстий. Сверло относится к категории наиболее точных видов инструментов. При переточке двух ее режущих кромок диаметр сохраняет свое изначальное значение. Свои коррективы вносит привод сверла − шпиндель и механизм его вращения. В шпинделе имеются опоры, зажимные штанги, которые способствуют радиальному биению сверла. Для проверки необходимо замерить диаметр сверла и получаемого в древесине отверстия − разница в показаниях косвенно характеризует величину такого биения. Допустимую разницу, а диаметр отверстия всегда будет больше размера сверла, определяют технические требования к мебельной заготовки. В одних случаях это сквозные отверстия для шурупов, где отклонения в 0,2−0,7 мм не оказывают существенного влияния на дальнейшую сборку, в других − глухие отверстия для штифтов, и такое положение дел может свести их функцию на нет.
Нельзя не учитывать влияние значительного радиального биения на качество получаемой грани отверстия при входе и выходе из нее инструмента. Сколы и отрывы декоративного слоя на MDF или ДСтП в этом месте ухудшают внешний вид изделия. Но этот дефект может быть вызван и неудовлетворительным состоянием режущих кромок самого сверла. Устранить биение можно путем ремонта или замены шпинделей или их отдельных частей в многошпиндельных сверлильных головках.
Другой, не менее важный критерий оценки качества работы сверлильно-присадочных станков − это определение межцентрового расстояния между получаемыми отверстиями. Кратное 32 мм для большинства моделей, оно имеет свой допуск. Фактическое отклонение этого размера должно быть в пределах допуска. Чем более жесткий допуск, тем точнее станок и, соответственно, позиционирование сверлимых на нем отверстий. Отклонение межцентрового расстояния всецело зависит от исполнения многошпиндельной сверлильной головки. Существенный разброс межцентрового расстояния свидетельствует о низком качестве данной головки и необходимости ее замены. Детали, получаемые с ее использованием, могут не собраться в готовое изделие из-за несовпадения соосных отверстий.
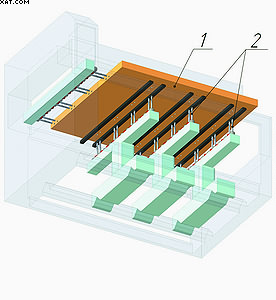
Рис. 6. Сверление отверстий на станке с
несколькими многошпиндельными головками.
1 – заготовка; 2 – сверла
В универсальных сверлильно-присадочных станках многошпиндельная головка имеет возможность наклоняться относительно заготовки. Если неправильно отрегулированы упоры крайних положений, то сверло входит в кромку или пласть детали не под прямым углом. В некоторых случаях это также может затруднить последующую сборку. Для контроля данного параметра существует несколько способов. Один из них − вставка в отверстие металлического стержня такого же диаметра, который будет материализовать ось этого отверстия. С помощью угольника и набора щупов измеряется угол между стержнем и базовой поверхностью или его отклонение от прямого угла. Для коррекции необходим доступ к упорам (если они регулируются). В иных случаях необходима более серьезная коррекция положения многошпиндельной сверлильной головки относительно заготовки. При комплексной диагностике сверлильно-присадочного станка нелишним будет сверить глубину получаемых отверстий и ее настроечные параметры. На абсолютное значение глубины может оказывать влияние первоначальная настройка станка − положение упоров, сверла в шпинделе. Отклонение глубины одного и того же отверстия в масштабах партии деталей свидетельствует о зазорах и износе механизма подачи многошпиндельной головки. Отклонения в 1−2 мм могут и не оказывать негативного влияния на сборку деталей, но быть тревожным симптомом нарушений в работе станка. Последующий износ коротких направляющих или ослабившийся болт могут привести к более серьезным последствиям: отклонениям расстояний между группами отверстий от разных головок, элипсообразным сечениям отверстий и так далее. В этом случае как минимум требуется внеплановый и тщательный технический осмотр станка.
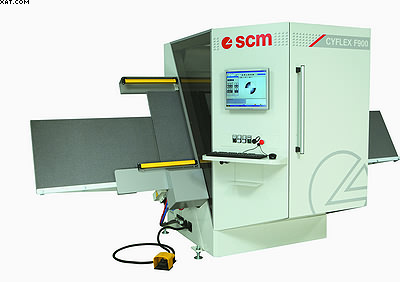
Гибкий автоматический сверлильно-присадочный станок SCM Cyflex
F900 PRO
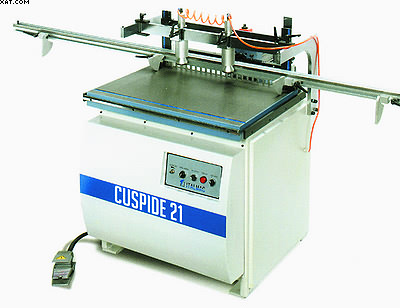
21-шпиндельный сверлильный-присадочный станок Cuspide-21
от Italmac
Для сверлильно-присадочных станков важно, чтобы рабочие циклы осуществлялись плавно, без рывков и скачков. Это исключает как дефекты на самих деталях, так и преждевременную выработку ресурса оборудования. Для этого разработчики внедряют в систему подачи многошпиндельных головок, а это, как правило, пневмоцилиндры, различные демпферы или электронные датчики с нелинейной функцией управления. В этих случаях головка плавно набирает скорость и также плавно тормозит во время рабочего цикла. Кроме того, такая система управления позволяет устанавливать оптимальную скорость подачи инструмента в заготовку и максимальную на обратном ходе.
О нарушениях в работе сверлильно-присадочных станков могут свидетельствовать повышенный шум при их работе, грохот, вибрации, смещение заготовки и прочее. В этих случаях оптимальным вариантом является вмешательство аккредитованного представителя завода-изготовителя станка, имеющего соответствующую квалификацию для проведения диагностики или ремонта станка.
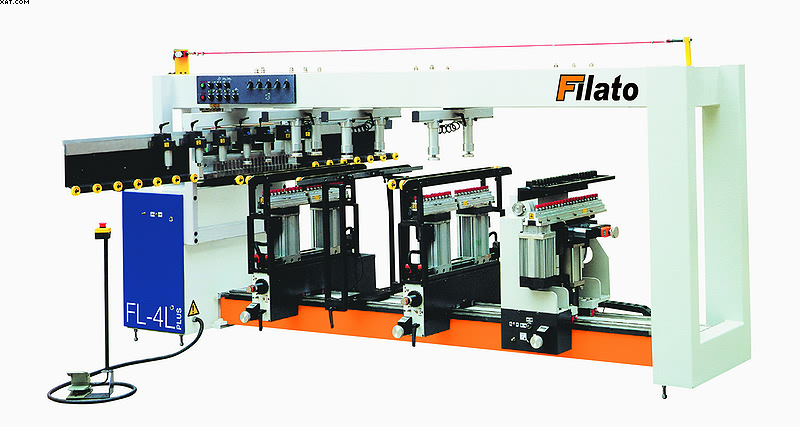
Сверлильно-присадочный станок проходного типа Filato FL-4L
Во всех случаях требуется неукоснительное соблюдение правил безопасности при проведении тестирования и ремонтных работ. Роль сверлильно-присадочных станков в современном деревообрабатывающем производстве трудно переоценить.
Безусловно, существует альтернатива в виде ручного электроинструмента, используемого вместе с накладными шаблонами. Но преимущества, которые дает внедрение даже одношпиндельного агрегата, − точность, производительность, универсальность, предопределяют выбор в пользу комплектной сверлильной установки. Неслучайно на долю сверлильно-присадочных станков приходится значительная часть единиц оборудования современного мебельного производства.
Андрей Морозов,
компания «МедиаТехнологии»
по заказу журнала «ЛесПромИнформ»