«Лесобалт» − радиальный распил в промышленных масштабах
Почти в центре Европы, в г. Калининграде, вот уже несколько лет успешно работает уникальное предприятие, хорошо известное европейским производителям окон. «Лесобалт» − молодая и динамичная компания, которая обладает впечатляющим производственным потенциалом. Первая очередь этого современного и в большой степени уникального − как с точки зрения технологии, так и методов деревообработки − лесоперерабатывающего комбината была запущена 3 августа 2005 года.
Оборудование, которое эксплуатируется в цехах и на участках «Лесобалта», это оборудование премиум-класса. Здесь работает техника таких известных фирм, как EWD, Holtec, Kallfass, Vecoplan, Weinig, Muehlboeck Vanicek, Polytechnik и др.
Продукция и сырье, сбыт и сертификация «Лесобалта»
Основная продукция предприятия − многослойный оконный брус, при изготовлении которого используются ламели только радиального распила и который в настоящее время производится компанией в объеме 1400 м в месяц в одну смену. Кроме бруса калининградский комбинат производит также клееный щит, профилированный погонаж, террасную доску, мелкореечный клееный брус, стеновой брус, экзотическую хагару (строганая доска из склеенного мелкореечного бруса) и другие продукты глубокой переработки древесины. Для производства используется древесина, поставляемая из сибирских и северных регионов России, которая особенно ценится в европейских странах − это ангарская сосна и сибирская лиственница.
Основные потребители продукции «Лесобалта» − это европейские страны: Чехия, Италия, Германия, Австрия, Швейцария, Бельгия, Норвегия, Швеция. Часть продукции уходит в Японию, там пользуется спросом хагара, которая применяется в строительстве как более стабильный материал, чем обычная доска. В этом году «Лесобалт» получил сертификат Лесного попечительского совета FSC и начинает выходить на рынки Франции и Великобритании. Для работы на этих рынках такой сертификат обязателен. Однако не менее важным является сертификат Немецкого института оконных технологий ift-Rosenheim, Бавария, который ООО «Лесобалт» получило в 2009 году, кстати, первым в России.
Сертифицировать продукцию предприятие может, только если будет соблюдена вся технологическая цепочка изготовления оконного бруса, начиная с распиловки и заканчивая складом, причем на каждом этапе производства необходимо контролировать качество продукции.
«У нас есть собственная лаборатория, − рассказывает Андрей Шафигулин, генеральный директор предприятия, − сертифицированная этим же институтом. Из каждой партии товара для исследований берутся образцы, результаты всех исследований документально фиксируются. Кроме того, специалисты института из Розенхайма проводят регулярную инспекцию предприятия. Два раза в год они приезжают на производство, оценивают технологический процесс и выдают нам рекомендации. В первом полугодии этого года у нас были незначительные замечания, а во втором полугодии нам поставили оценку отлично. Нельзя сказать, что работа по подготовке к сертифицированию и проведение инспекций требует больших затрат, скорее, это хлопотно, потому что в основном это работа с персоналом, которая требует много времени и сил. Мы относимся к такой работе ответственно, потому что не хотим подводить партнеров и должны быть уверены в качестве».
Решение о сертификации предприятия немецкий институт принимает на основании результатов надзора специалистов над системой управления качеством на производстве, а также после успешного прохождения тестов образцов готовой продукции в головном институте ift-Rosenheim. Фактически этот институт выступает гарантом качества продукции, а полученный сертификат удостоверяет, что продукция предприятия соответствует требованиям европейской директивы «Деревянные слоистые профили для оконных рам. − Требования и контроль» HO.10 (QM 309:2002).
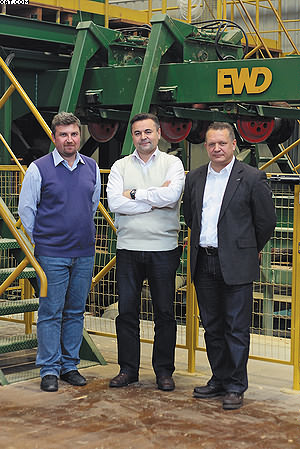
Слева направо: Андрей Бoрис (начальник цеха
распиловки ООО «Лесобалт»), Андрей Шафигулин
(генеральный директор ООО «Лесобалт»), Фридрих
Крамер (менеджер компании EWD по сбыту в России
и СНГ)
Деревообрабатывающее производство компании «Лесобалт» имеет выгодное географическое расположение: благодаря близости к рынкам сбыта вся продукция отгружается потребителям автотранспортом. Кроме того, находясь почти в центре Европы, проще вести переговоры с покупателями, немаловажно и то, что здесь, в Калининграде, есть возможность привлечь к работе квалифицированный персонал. Сегодня на предприятии работает 257 человек, коллектив молодой (средний возраст не превышает 40 лет), сплоченный и профессиональный. Трудовой процесс организован на основе лучших решений и опыта советских производств, а также с применением современных технологий, позволяющих автоматизировать многие процессы. По опыту работы советских заводов здесь, например, организованы отдел технического контроля и единая диспетчерская служба, которая позволяет постоянно, круглосуточно контролировать все транспортные процессы, логистику движения материалов и транспорта. Все диспетчеры производства и водители снабжены мобильными радиостанциями. Здесь много внимания уделяется социальной поддержке и поощрению сотрудников, благодаря чему на предприятии создана уникальная трудовая атмосфера, что подтверждают и специалисты иностранных компаний, которые проводят сервисное обслуживание оборудования. Сегодня часть персонала, работающего на предприятии, − это те люди, которые участвовали в монтаже и запуске завода. Многие из них продолжают работу уже на более высоких должностях, чем в начале своей карьеры в «Лесобалте».
Первое требование к операторам станков, которое учитывалось при приеме людей на работу, − высшее образование. Такой подход оправдал себя еще при наладке линий: персонал молодого российского предприятия понимал, что именно он делал, заинтересованно относился к техническим вопросам и на равных общался с иностранными специалистами, которые также проявляли уважительное отношение к операторскому и инженерному составу, так как видели высокий уровень их подготовки.
Производство «Лесобалта»
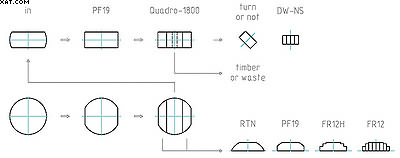
Рис. 1. Схема распиловки
Предприятие размещено в промышленной зоне Калининграда, на берегу реки Преголя, на площади 12 га. Вблизи находится территория перспективного развития, где есть возможность организации причала. Освоение территории «Лесобалт» начал в 2003 году. Почти год потребовался строителям, чтобы провести значительную по объемам работу по выравниванию площадки и подготовки ее к строительству. Тогда было принято оригинальное решение замостить всю площадку тротуарной плиткой, для производства которой на территории предприятия даже был запущен временный цех. Такое покрытие исправно служит уже не первый год даже в местах проезда тяжелой техники, вес которой доходит до 20 т. К тому же при необходимости плитка может быть легко разобрана для ремонта или переноса сетей или для быстрого и простого восстановления при проседании грунта. В 2004 году на площадке был начат монтаж линии сортировки и лесопильного цеха, а в 2005-м − монтаж деревообрабатывающего цеха, силовой подстанции и сушильных камер. В том же году здесь было распилено первое бревно.
Линия сортировки лесоматериалов в «Лесобалте»
Все сырье доставляется на площадку железнодорожным транспортом и, как говорится, «с колес» подается на сортировку круглого леса. На складе лесоматериалов хранится только отсортированный лес в объеме, который обычно не превышает месячный запас. Благодаря широкой географии поставщиков сырья сезонных проблем с поставками нет, однако для страховки от таких неприятностей предприятие запасает сырье в распиленном виде. То есть перед летним периодом интенсифицируется распиловка зимнего леса, по каждому из долгосрочных контрактов компании составляются соответствующие схемы пиления, осуществляется распиловка и сушка пиломатериалов требуемых длин и сечения до транспортной влажности, которые размещаются на складе временного хранения. Таким образом, решается проблема сезонности поставок и долговременного хранения сырья.
Линия сортировки лесоматериалов Holtec оборудована 28 сортировочными «карманами», предназначенными для трех- и четырехметровых сортиментов. Шестиметровые лесоматериалы раскряжевываются пополам при помощи встроенной в сортировочную линию шины с цепной пилой. Сырье доставляется на предприятие уже сортированным по длине, поэтому на линии сортировка осуществляется только по диаметрам (с шагом через 1 см) и по качеству. Сортименты с металлическими включениями, излишней кривизной или сбежистостью отсортировываются автоматически, а качественные показатели пиловочника определяются оператором визуально. В состав линии входит металлоискатель, который улавливает даже незначительные металлические включения в бревнах, лесоматериалы с такими включениями отсортировываются отдельно. Все транспортные операции с круглым лесом на площадке осуществляются двумя машинами − фронтальным погрузчиком Volvo L180E и грейферным погрузчиком Sennebogen.
Подача на лесопильную линию «Лесобалта»

Разворот бревен перед подачей в лесопильный цех

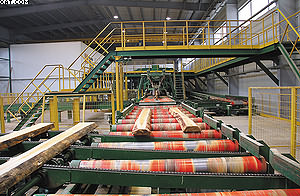

Редуцирующий ленточнопильный станок Quadro
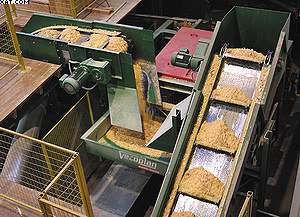
Система удаления отходов
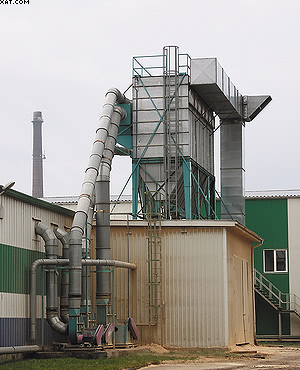
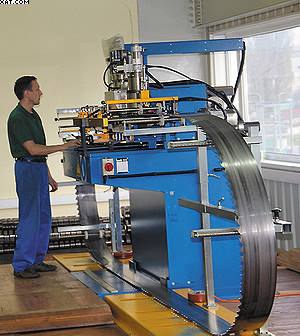
Автоматический вальцовочный станок для ленточных
пил
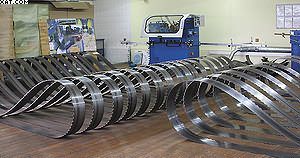
Ленточные пилы ALBER TERMEX. Ширина полотна –
200 мм, шаг зуба 50 –мм
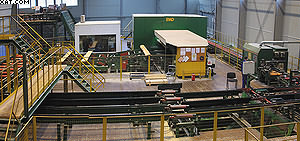
Фрезерно-круглопильная линия распиловки
полулафетов
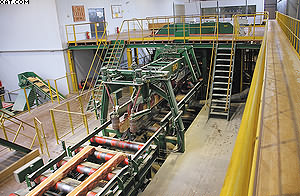
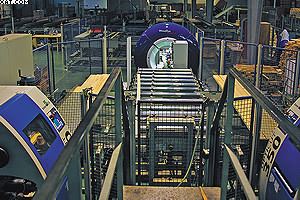
В центре сканер пороков, по бокам торцовочные
установки

Сортировка заготовок перед сращиванием
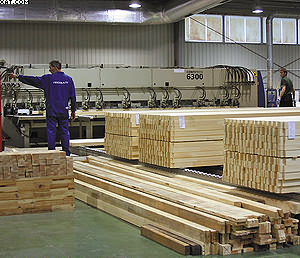
На линии прессования
Сортировка лесоматериалов происходит без раскомлевки, но на линии подачи в лесопильный цех установлен сканер, который определяет длину, диаметр и вершину сортимента. Далее установлено поворотное устройство, которое разворачивает бревно вершиной вперед. Такая подача обусловлена необходимостью точного ориентирования сортимента для увеличения коэффициента выхода пиломатериала. Окорочный станок Valon Kone VK-820 установлен в лесопильном цехе, поэтому пиловочник подается в распиловку без коры и грязи, что очень важно для обеспечения долговечности и качества работы инструмента.
Технология радиального распила в «Лесобалте»
Уникальность используемой технологии и производства в компании «Лесобалт» состоит в непривычно высоких скоростях и объемах пиления радиальной доски. Действительно, обычно радиальные пиломатериалы получают на одиночных пильных агрегатах с многократным возвратом сортимента, что и определяет низкую производительность производства. А вот на линии, работающей в «Лесобалте», обработка идет на скоростях от 22 до 100 м/мин с одним возвратом. Максимальная производительность, которой удалось достигнуть здесь за 12-часовую смену, составила 760 м лесоматериалов.
Все оборудование, установленное в цехе радиального распила, включая подачу в цех, сортировку досок, удаление отходов и вспомогательное оборудование, рассчитано и скомплектовано компанией EWD, выступившей в этом проекте в качестве генерального подрядчика. Лесопильный цех был спроектирован для поточной распиловки радиальных пиломатериалов из крупномерных бревен. Некоторые технические и технологические решения линии распиловки были разработаны впервые, специально для компании «Лесобалт», и впоследствии были запатентованы как в Европе, так и в России. В этом проекте были объединены три технологии пиления: фрезерно-профилирующая, ленточнопильная и круглопильная. Синтез этих технологий позволил эффективно использовать достоинства каждой из них и осуществить проект организации качественного, экономного и при этом высокоскоростного пильного производства с получением радиальных пиломатериалов.
В качестве головного станка в линии лесопиления на «Лесобалте» используется жесткая связка механизма центрирования и подачи ERB-ZE, фрезерно-брусующего агрегата PF19 и редуцирующего четырехпильного ленточнопильного станка Quadro-EBT1800. Это универсальная, гибко программируемая линия, позволяющая решать многие задачи. Здесь можно использовать одну, две, три или четыре ленточных пилы, можно применять радиальный или классический тангентальный распил. Система управления станком многофакторная, включает в себя управление положением и натяжением пил, скоростью подачи и вращением шкивов в зависимости от нагрузки и требуемой подачи на зуб. Центрирование и распиловка пиловочника осуществляется здесь автоматически, оператору необходимо только базировать сортимент, учитывая его овальность и кривизну и контролировать процесс распиловки. Пиловочник должен быть сориентирован кривизной вниз, но с некоторым разворотом, чтобы обеспечить беспрепятственное прохождение и оптимальную форму выпиливаемых лафетов. Качество базирования во многом зависит от мастерства оператора. Кстати, чтобы подготовить специалиста хорошего уровня для работы на этой машине, требуется несколько месяцев. Конечно, самостоятельно пилить он начинает уже через месяц после начала обучения, но для того, чтобы человек, что называется, слился с машиной, требуется не менее полугода.
База для жесткой фиксации бревна создается фрезами с приводом в 110 кВт, которые перерабатывают горбыльную часть сортимента в технологическую щепу. Скорость вращения фрез регулируется автоматически, в зависимости от скорости подачи, чем обеспечивается постоянство геометрических размеров щепы. В ленточнопильном агрегате (мощность привода каждой пилы − 90 кВт) происходит отделение двух подгорбыльных брусьев (полулафетов) от центральной части бревна (центрального лафета). Полученные полулафеты автоматически транспортируются на фрезерно-круглопильную линию для дальнейшей обработки, а центральный лафет по транспортерам системы обвода возвращается на накопительный стол перед головным станком.
По заполнении накопительного стола подача круглого леса прекращается, а в распиловку направляются лафеты, выпиленные из центральной части ствола. Фрезерные агрегаты снимают горбыльную часть лафета и задают базу для его дальнейшего центрирования. Далее ленточнопильный агрегат раскраивает лафет на радиальные и сердцевинный брусья. Распиленный материал поступает на поперечный транспортер, где второй оператор управляет механизированной системой сортировки брусьев. Радиальные брусья из боковых частей лафета автоматически позиционируются и подаются на двухвальный круглопильный станок A.COSTA.Righi Falcone (2х75 кВт), где распиливаются на радиальные доски. Радиальные доски направляются на линию «сырой» сортировки, а брус из центральной части лафета поступает на первый этаж лесопильного цеха, где может быть распилен на многопильном станке на тангентальные пиломатериалы или удален из цеха как готовый продукт.
Полулафеты, полученные после первого распила на Quadro-EBT1800, подаются на фрезерно-круглопильную линию широкой пластью вниз. Оператор этой линии контролирует положение лафета и при необходимости может перевернуть его на 180° при помощи механизированных захватов. Полулафет должен обязательно находиться в положении обзолом вверх, поскольку фрезерование нижней (широкой) пласти здесь не происходит. Перед подачей на фрезерование осуществляется сканирование полулафета для измерения величины обзола. Система автоматического позиционирования RTN выравнивает лафет и подает его на фрезерование таким образом, чтобы получить максимальный выход пиломатериалов. Фрезерно-круглопильная линия состоит из трех соосных агрегатов, обрабатывающих полулафеты на скорости до 100 м/мин. Первым в линии установлен фрезерно-брусующий агрегат PF19, который снимает часть бокового обзола по всей длине полулафета, образуя тем самым базу для его жесткой фиксации при последующей обработке. Следующий агрегат − FR12H снимает остаток обзола верхней части полулафета и одновременно профилирует верхний контур будущих пиломатериалов. Этот станок оснащен мощным приводом (200 кВт) и системой позиционирования фрез. Третий станок в этой связке − тяжелый двухвальный многопил с жестким поставом и мощным приводом (2х200 кВт). Здесь профилированный полулафет распиливается на радиальные ламели.
Описанное сочетание профилирующей фрезы и многопильного станка для обработки полулафетов и получения радиальных пиломатериалов было разработано впервые. Соответствующий патент РФ был заявлен в 2004 году и в 2009-м получен фирмой EWD. Преимущество этой технологии получения радиальных пиломатериалов заключается в высоких скоростях и объемах обработки, простоте и надежности исполнения, в легком управлении и обслуживании. Все оборудование линии размещено в шумоизолирующем корпусе, оснащенном системой аспирации. Весь процесс контролирует один человек. Схемы распила составляются автоматически, то есть в систему расчета вводятся размеры пиломатериалов, которые надо получить, и программа, разработанная специалистами ALFHA GmbH & Co. KG, выдает несколько схем распила для каждого диаметра пиловочника. Выбранная схема автоматически направляется в операторскую, распечатывается и передается в заточной цех, где согласно выбранным схемам составляются фрезерные и пильные поставы.
Система удаления отходов поставлена фирмой Vecoplan. Скребковые транспортеры и вибролотки захватывают получающиеся в процессе пиления древесные отходы непосредственно под каждым агрегатом и подают их на просеивающее сито. Мощная установка просеивания, состоящая из вибрационного сита типа VSS 60/2 и звездочного грохота, отделяет опилки от щепы. Специальные скребковые транспортеры подают обе выработанные фракции в соответствующие накопители за пределами цеха. На первом этаже лесопильного цеха установлена также барабанная рубительная машина типа VTH 55/20/3 с мощностью привода 55 кВт, которая измельчает входной материал в однородную щепу и также подает их на установку просеивания. Кроме механической системы удаления отходов в цехе работает система аспирации Nestro, которая отбирает запыленный воздух из укрытия профилирующей линии и кожухов ленточнопильных агрегатов. Этот воздух очищается в рукавных фильтрах и возвращается в цех, а собранная пыль поступает в котельную на сжигание.
Неотъемлемая часть лесопильного цеха − заточная мастерская, расположена на втором уровне, вблизи ленточнопильного станка. Здесь установлены станки для подготовки дисковых и ленточных пил, ножей, фрез, позволяющие производить полный цикл обработки инструмента. Почти все оборудование заточного цеха поставлено компанией Iseli. Специалисты этой швейцарской фирмы подобрали оборудование и провели обучение персонала на калининградском предприятии, осуществляют гарантийное и сервисное обслуживание. Для качественной подготовки ленточных пил в заточном цехе установлен вальцовочный станок Iseli RZ1, позволяющий в автоматическом режиме выравнивать пильные ленты и обеспечивать в них требуемые напряжения. Ручная вальцовка используется только для местного ремонта ленты после сварки. В «Лесобалте» используют стеллитированные пилы Alber Termex (Германия), рекомендованные фирмой EWD. Хороший инструмент, надежное заточное оборудование и его правильная эксплуатации позволяют с большим успехом использовать ленточные пилы и на больших скоростях обработки. Достаточно сказать, что в «Лесобалте» ленточные пилы меняются только 2 раза в смену, то есть каждая пила работает до 6 часов без замены. При этом затраты на инструмент в себестоимости продукции составляют не более 1,5–2%, а весь имеющийся в цехе режущий инструмент обслуживают только два заточника.
Обслуживание оборудования в «Лесобалте»
Технический регламент производства в «Лесобалте» предусматривает регулярное плановое обслуживание оборудования. Для планово-профилактического ремонта в лесопильном цехе запланированы три смены ежемесячно. В это время, как правило, проводится очистка оборудования и проверка технического состояния узлов и систем в соответствии с индивидуальным планом обслуживания для каждой машины. Смазка подшипников почти не требуется, так как все ответственные узлы пильных агрегатов оборудованы системой центральной смазки. Регулярные профилактические работы позволяют обеспечить бесперебойную работу оборудования в течение смены. Однако если случаются какие-либо сбои или возникают технологические вопросы, всегда можно связаться со специалистами генерального поставщика − фирмы EWD. Руководство компании «Лесобалт» отмечает, что фирма EWD всегда очень чутко и быстро реагирует на подобные запросы.
Для оперативного решения технических вопросов системы управления станками посредством модемного соединения подключаются к сервисному центру EWD.
Система удаленного доступа позволяет сделать анализ состояния машины, увидеть, какие узлы перегружены в момент работы, и найти причину сбоя.
Однако если какое-то время назад при запуске оборудования и обучении персонала такая связь требовалась постоянно, то теперь, по мере накопления опыта, к ней прибегают все реже. Эксплуатация и обслуживание такой лесопильной линии требуют хорошей подготовки инструмента и высокой квалификация операторов. Здесь обязателен тщательный подбор и обучение персонала, высокий уровень технического оснащения и культуры производства.
«Сырая» сортировка в «Лесобалте»
После линии радиального распила в здании лесопильного цеха установлена линия сортировки и штабелирования сырой доски. Это автоматическая линия Kallfass с 15 вертикальными «карманами», позволяющая сортировать доски по размерам и проводить подсортировку по трем критериям качества − сорта А, В и С.
Всего на линии работает три человека (два оператора-сортировщика и один оператор пакетоформирующей машины).
Сортировка пиломатериалов по длине, ширине и толщине происходит автоматически, а подсортировку по качеству осуществляет оператор, перемещая доску, двигающуюся по поперечному транспортеру, до определенного упора. Отмеченная таким образом доска попадает в назначенный сортировочный «карман». «Карманы» смонтированы под углом 30° для смягчения удара при соскальзывании доски в «карман». По его заполнению сортировочный «карман» разгружается на нижний транспортер, и доски направляются на участок пакетирования, предварительно пройдя торцовку.
Торцовка осуществляется автоматически на одну длину − 3 или 4 м. Именно такая длина пиломатериалов требуется в деревообрабатывающем цехе, впрочем, если доска выпускается на экспорт, то торцовка выполняется на необходимую длину по спецификации.
Отторцованные пиломатериалы поступают на пакетоформирующую машину, а отходы отторцовки подаются на измельчение в барабанную рубительную машину. Сформированные сушильные пакеты вилочным погрузчиком Hubtex (Германия) перевозятся в буферный склад перед сушильными камерами.
Сушильно-котельный комплекс «Лесобалта»
Сушильный комплекс предприятия состоит из 24 камер (4 блока по 6 камер) фирмы Muehlboeck Vanicek. В каждую камеру может быть загружено до 130 м пиломатериалов. Программное обеспечение системы управления процессом сушки содержит более 200 вариантов для различных условий, начиная от стандартных и заканчивая технологическими условиями для обработки экзотических пород древесины.
Конечно же, есть программы и для лиственницы, которую здесь успешно сушат в больших объемах. Лиственница − это сложный материал, с которым надо учиться работать, она сохнет дольше, чем сосна и очень капризна, то есть если проявить невнимательность к технологическим режимам, то это сразу же скажется на качестве сушки, могут появиться коробление, торцевые трещины или другие дефекты.
Тепло для сушильных камер и отопления производственных помещений вырабатывается в котельной, которая расположена в отдельном здании, стоящем вблизи лесопильного цеха. В котельной работают три водогрейных котла с подвижными колосниковыми решетками Polytechnik тепловой мощностью 6 мВт каждый. Загрузка котлов осуществляется в автоматическом режиме со стокерных полов, куда топливо подается ковшовым погрузчиком.
Топливом для котельной является неизмельченная кора, накопление которой происходит в бетонном отсеке у лесопильного цеха. Там же размещены отсеки временного хранения щепы и опилок.
Количества поступающей на сжигание коры вполне достаточно для покрытия потребности в тепловой энергии всего предприятия, поэтому щепа и опилки являются товарным продуктом и реализуются на внутреннем рынке в качестве топлива.
Деревообрабатывающий цех «Лесобалта»
Распиловка леса на предприятии осуществляется в основном для переработки на собственном деревообрабатывающем производстве, поэтому сортировка сухих пиломатериалов не предусмотрена. После сушки пакеты пиломатериалов автопогрузчиком доставляются сразу в буферный склад деревообрабатывающего цеха. Здесь пакеты выдерживаются 2–3 дня для выравнивания температуры и равномерного распределения влажности. Для создания требуемых микроклиматических параметров воздуха в буферном складе «Лесобалта», так же как и в деревообрабатывающем цехе, установлена система вентиляции и кондиционирования, поддерживающая определенную температуру и влажность.
Генеральным поставщиком оборудования для деревообрабатывающего цеха стала компания Weinig. Специалистами этой фирмы была разработана технология производства, произведены расчеты и подобрано соответствующее оборудование компаний Dimter и GreСon Weinig.
Согласно заданию на проектирование в цехе площадью 11 500 м установлено несколько самостоятельных производственных линий для оптимизации пиломатериалов, сращивания заготовок по длине, производства клееного бруса и клееного щита, погонажных изделий. Оборудование, установленное в цехе, обладает высоким уровнем автоматизации, а перемещение материалов в значительной степени механизировано.
С буферного склада пиломатериалы подаются на участок оптимизации, где происходит предварительная острожка доски и вырезание дефектных зон. На участке установлены две одинаковые линии обработки с системой автоматической загрузки. Пакеты пиломатериалов разбираются системой разборки штабеля, которая поштучно выдает доски на устройство измерения влажности Brookhuis. Слишком влажные пиломатериалы выносятся из потока, штабелируются и направляются на досушку. Кондиционные пиломатериалы проходят острожку на четырехстороннем станке Hydromat 22B. Скорость обработки здесь достигает 120 м/мин, поэтому применяется околостаночная механизация. После острожки пиломатериалы поступают на автоматический оптический сканер WoodEye, который в зависимости от заданных параметров обработки и пороков древесины размечает ламель и передает данные на торцовочную установку. Один такой сканер заменяет работу 5–6 человек и позволяет добиться высоких скоростей обработки при отсутствии ошибок. Дефектные места, вырезанные на торцовочной установке OptiCut 350, сбрасываются на транспортер и поступают в дробилку. Готовые заготовки без сучков и прочих пороков, нарезанные на определенную длину, так называемые мерные длины, а также короткие заготовки, (коротье), поступают на продольные транспортеры, распределяющие их в зависимости от размера и сорта по соответствующим накопительным столам. Линия работает на огромной скорости, кажется, что станки выстреливают заготовки.
Подготовленные таким образом заготовки собираются на десяти сортировочных столах и направляются на участок сращивания. Сращивание заготовок для изготовления оконного бруса происходит на вертикальный минишип на двух участках сращивания GreСon. Укладывание заготовок осуществляется вручную с дополнительным контролем качества, остальные операции выполняются автоматически. Максимальная длина сращенной ламели 6,3 м, а при необходимости сращенная на мини-шип заготовка распиливается на заготовки требуемой длины на торцовочном станке, установленном на выходе из линии сращивания. Ламели, предназначенные для производства мебельного щита, сращиваются по длине на горизонтальный или вертикальный мини-шип на тех же участках. Сложенные в пакет сращенные по длине ламели погрузчиком транспортируются на складские буферные зоны, где как минимум сутки выдерживаются для стабилизации клеевых соединений. Этапы оптимизации и сращивания ламели по длине являются важнейшими в технологическом процессе с точки зрения полезного выхода материалов. При этом существует прямая зависимость между качеством пиломатериалов и процентом полезного выхода.
Склеивание многослойного оконного бруса происходит на двух линиях Dimter: ContiPress 4500, с длиной прессования 4,5 м, на которой клеится брус состоящий из двух наружных цельных ламелей и средних сращенных, т.н. мерные длины, и ContiPress 6300, с длиной прессования 6,3 м на которой производится брус из трех или более сращенных ламелей. Каждая линия имеет возможность разделения потоков по двум качествам − наружные ламели и внутренние ламели. Автоматическая система загрузки осуществляет попеременную подачу заготовок из штабелей с наружными и внутренними ламелями в строгальный станок Hydromat H23 (Hydromat 22B для пресса 6300). После строгания заготовки поступают на станцию клеенанесения, где клей наносится на каждую вторую и последующие ламели. На первую ламель клей не наносится, так как требуется получить не сплошной щит, а отдельный многослойный брус. Ламели с нанесенным на них клеем собираются в пакеты и подаются в проходной пресс. В прессе происходит отверждение клеевых швов под действием температуры и давления.
На выходе из пресса брус разделяется по бесклеевому соединению, укладывается в штабель и транспортируется на буферный склад. После выдержки производятся чистовая обрезка торцов склеенного бруса и его четырехсторонняя острожка на строгальном станке Hydromat H23C. Готовый брус направляется в автоматический штабелеукладчик и далее − на линию упаковки пакетов Fischer sfv 1100H-S, где выполняется упаковка и маркировка штабеля.
Мебельный щит производится на линии прессования ProfiPress PP 5500. Для его изготовления используются сращенные по длине или цельные ламели. Ламели из штабеля укладываются в загрузочное устройство линии и подаются в строгальный станок Unimat Super 4, где они прострагиваются с четырех сторон. После чего ламели проходят станцию клеенанесения и передаются на участок сборки. Собранный щит автоматически загружается в пресс ProfiPress PP 5500, где под действием токов высокой частоты происходит отверждение клеевых швов.
После прессования все щиты сортируются, штабелируются и передаются на линию торцовки PZS 5500 и шлифования Profiline SVR 313. Готовые мебельные щиты упаковывается в термоусадочную или обычную упаковочную пленку и отправляются на склад.
Погонажные изделия изготавливаются на линии профилирования на базе станка Unimat 23 EL с пильным шпинделем. Кроме профилирования здесь возможен также раскрой заготовок на несколько ламелей по ширине. Станок оборудован системами механизации загрузки и выгрузки, предназначен для выполнения работ по профилированию изделий различной сложности при высокой производительности. После профилирования погонажные изделия торцуются в заданный размер на станке OptiCut S75, пакетируются, упаковываются и транспортируются на склад готовой продукции, откуда отгружаются покупателю автотранспортом.
Все отходы, образующиеся в процессе деревообработки, собираются системами аспирации и улавливаются в фильтрах JHM-Moldow. Системой пневмотранспорта собранные отходы подаются в циклон, расположенный непосредственно у котельной. Из циклона смесь отходов поступает в систему из двух реверсивных, герметичных конвейеров типа Redler и поступает в накопительные бункера.
Реструктуризация производства и развитие «Лесобалта»
Руководством компании «Лесобалт» разработана четкая и перспективная схема развития предприятия на несколько лет вперед.
В связи с высокой потребностью рынка оконного бруса в Европе уже сейчас необходимо значительное увеличение производительности предприятия. Деревообрабатывающий цех в Калининграде имеет необходимый запас мощности, и он будет развиваться. Но для его снабжения сырьем требуется реструктуризация производства.
Дело в том, что за последние годы сильно выросли тарифы на железнодорожные перевозки и к тому же ощущается дефицит подвижного состава. В этих условиях доставка круглого леса из сибирских регионов страны весьма ощутимо отражается на себестоимости продукции, поэтому в компании принято решение перенести склад леса и лесопильное производство ближе к месту заготовки сырья, а на калининградское предприятие доставлять полуфабрикат − сухую доску транспортной влажности. Для реализации этих целей «Лесобалт» приобрел производственную площадку в г. Братск Иркутской области. Эта площадка идеально подходит для организации современного лесопильного производства требуемой мощности. Сегодня на производстве в Братске уже работают две лесопильные линии − линия обработки тонкомера HewSaw R200 и ленточная линия распиловки крупномерных сортиментов EWD. В 2012–2013 годах планируется перенос лесопильной линии EWD, производящей пиломатериал радиального распила из Калининграда в Братск. Причем мощность линии радиального распила после переезда может быть увеличена почти в два раза путем установки в систему возврата лафета обычного многопильного станка.
Таким образом, производственные мощности позволят «Лесобалту» закупать у заготовителя не только экспортный пиловочник, как это обычно происходит в Сибирском регионе, но и другие лесоматериалы без предварительной сортировки, в том числе и тонкомерное сырье.
Согласно стратегическим планам развития холдинга, новое предприятие будет обеспечивать радиальными пиломатериалами деревообрабатывающий комплекс в Калининграде, мощность которого увеличится вдвое, а также производить тангентальные пиломатериалы для новых рынков.
Подготовил Виталий ТИКАЧЕВ
Комментарии
Фирма EWD как генеральный поставщик проектировала всю технологическую цепочку оборудования «Лесобалта» − от подачи на распиловку до сортировки доски, а также системы удаления отходов и аспирации. Достоинство фирмы EWD заключается в том, что она производит оборудование для всех основных технологий лесопиления − профилирующей, фрезерно-круглопильной, ленточнопильной, кромкообрезной и рамной. В зависимости от требований заказчика EWD может найти оптимальное технологическое решение производства и подобрать требуемую технику. Индивидуально для каждого клиента мы изучаем сырье и готовую продукцию, комбинируем технологии, осуществляем проектирование и оснащение производства, проводим обучение персонала и запускаем производство.
Линия, установленная в Калининграде на «Лесобалте», обладает высокими техническими и конкурентными преимуществами и обеспечивает:
- высокий полезный выход;
- технологическую гибкость;
- хорошее качество обработки поверхности, которое позволяет минимизировать отходы при деревообработке;
- минимум обслуживающего персонала − всего три оператора и два заточника.
Надежность линии обеспечивается применением проверенных технологических решений и лучших комплектующих. Компания EWD осуществляет поддержку работающих лесопильных линий и снабжение запасными частями. В каждую поставку EWD включает так называемый ЗИП, в состав которого входят все основные изнашиваемые запчасти и расходные материалы (подшипники, ремни, ремонтные устройства), которые могут потребовать срочной замены. Для снижения сроков поставки запчастей на территории России планируется открытие Красноярского сервисного центра.
За последние годы между EWD и «Лесобалтом» сложилась конструктивная рабочая атмосфера, позволяющая успешно оказывать оперативную техническую поддержку, развивать новые схемы раскроя, а также производить последовательную модернизацию оборудования для повышения производительности.
В связи с запланированным Компанией «Лесобалт» в 2012-2013 годах переносом лесопильной линии EWD из Калининграда на новую площадку компании в г. Братск, компания EWD совместно с предприятием «Лесобалт» дооснастит линию круглопильным станком второго ряда, что позволит не только повысить производительность линии до 40%, но также дополнительно поднять коэффициент полезного выхода.
Зная высокий уровень организации и профессионализма кадров предприятия «Лесобалт», руководство компании EWD уверено в успешном результате реструктуризации производства калининградского предприятия с переносом лесопильной линии в Иркутскую область и со своей стороны окажет «Лесобалту» полноценную и профессиональную поддержку.