«АРДИС»: на новой ступени
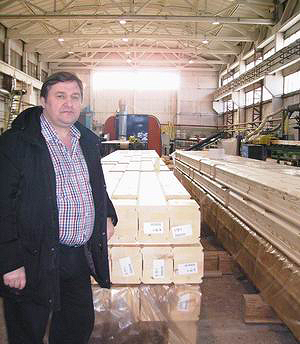
Руководитель ОП ОО «АРДИС» Игорь Черединов:
«Мы выпускаем востребованную продукцию»
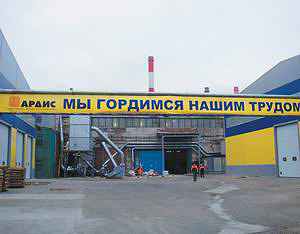
Общий вид производственной площадки завода
«АРДИС»
На растяжке, которая висит между корпусами этого предприятия, написано: «Мы гордимся своим трудом!» Это не пережиток советских времен. В этом лозунге выражение общего настроя коллектива, у которого есть все основания для того, чтобы гордиться своей компанией - одной из лучших на российском рынке деревянного домостроения.
Новое Ступино - первый в России малоэтажный город-спутник, сочетающий в себе комфортабельное доступное жилье, индустриальный парк с рабочими местами, торговую и деловую инфраструктуру, социальные объекты и рекреационные зоны. Планируется, что общая площадь города составит 12 км2, предполагаемое количество жителей - 55 тыс. человек. Город-спутник расположен в 70 км от Москвы, в Ступинском районе.
В 40 минутах езды на автомобиле находится международный аэропорт Домодедово. Рядом с городом проходят скоростная безсветофорная федеральная автотрасса М4 «Дон» и железная дорога Павелецкого направления.
«Вестфалия» - современный коттеджный поселок европейского типа с традиционной немецкой архитектурой. Поселок расположен всего в 40 минутах езды от Москвы по Симферопольскому шоссе (федеральная трасса М2 «Крым») - скоростной автомагистрали без населенных пунктов, светофоров и перекрестков. Добротные комфортабельные немецкие дома из немецких материалов изготавливаются и возводятся в строгом соответствии с немецкой технологией.
ООО «АРДИС», по российским меркам, компания довольно молодая - в январе этого года минуло всего восемь лет с момента ее регистрации. Но сегодня она заслуженно входит в число трех крупнейших производителей клееного бруса и является одной из ведущих российских компаний на рынке деревянного домостроения. Ее название «АРДИС» расшифровывается как «архитектура, дизайн, строительство» и красноречиво говорит об основных направлениях деятельности предприятия. В его активе многие десятки быстровозводимых домов из клееного профилированного бруса и каркасно-панельных домов, тщательно спроектированных специалистами архитектурно-проектного бюро (которое находится в головном офисе, расположенном в одном из центральных районов Москвы) и изготовленных из высококачественных материалов на современном заводе в подмосковном городе Ступино. Эти энергоэффективные и экологичные дома, которые собираются прямо на строительной площадке из элементов домокомплекта по принципу детского конструктора «Лего», монтируются на фундаменте в течение двух-трех недель, почти не требуют окончательной отделки и предназначены для круглогодичного проживания семьи в условиях, соответствующих европейским понятиям о комфорте.
В красивых, надежных и удобных деревянных коттеджах, построенных в российской столице и Подмосковье, а также в самых разных регионах страны, живут сегодня тысячи людей. Работая с частными застройщиками и участвуя в реализации государственных программ обеспечения населения доступным малоэтажным жильем, «АРДИС» добился заслуженного признания как клиентов, так и специалистов домостроительной отрасли. Всего через два года после начала работы, в 2007 году, компания стала лауреатом Всероссийской лесопромышленной премии в номинации «Самая динамично развивающаяся компания в секторе деревянного домостроения».
А по итогам прошедшей в ноябре прошлого года в Москве выставки «Красивые деревянные дома» стенд «АРДИСа» был признан лучшим. Продукция завода соответствует международным стандартам качества ISO 9001:2000, а производственные принципы компании аналогичны системе менеджмента качества Total Qality Management (TQM).
Предприятие работает под девизом: «Высокое качество за разумную цену», и все больше заказчиков прибегают к его услугам. Сейчас «АРДИС» участвует в реализации таких масштабных проектов, как экогород Новое Ступино, застройщиком которого является крупный игрок на рынке столичной недвижимости - компания MR Group, и коттеджный поселок «Вестфалия» в Подмосковье.
Современный подход к организации производства
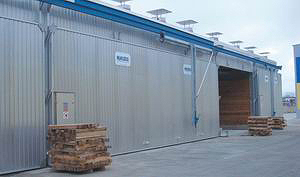
В составе сушильного комплекса завода девять камер
периодического действия Muehlboeck Vanicek
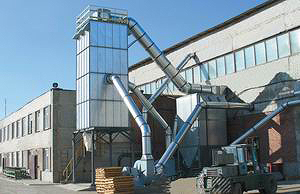
На заводе установлена аспирационная система
компании «Консар»
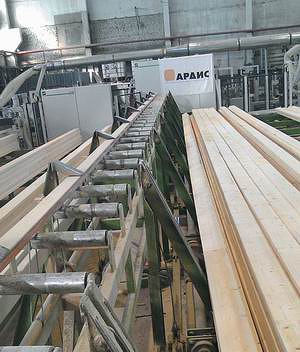
На заводе «АРДИС» производят высококачественный
клееный брус длиной 20 м
В успехе компании «АРДИС» много слагаемых. Среди них и следование тенденциям рынка деревянного домостроения, и внимательное отношение к запросам клиентов, и создание отвечающих духу времени проектов комфортного жилья - модельный ряд типовых проектов домов постоянно пополняется новинками, и в то же время архитекторы компании могут выполнить индивидуальный заказ. Конструкции и дизайн зданий прорабатываются до мельчайших деталей, продумывается все, вплоть до мест нарезания венцовых чашек для соединения бруса, отверстий для прокладки коммуникаций и для нагелей и т. п. Но все же определяющим фактором является уровень организации и оснащенности основного производства, а также степень квалификации персонала, от которой зависит качество конечного продукта - домокомплектов. Поэтому мы подробно расскажем о заводе компании, который расположен в г. Ступино (88 км к югу от Москвы по федеральной трассе М4 «Дон»).
Общая площадь территории предприятия сейчас составляет около 1,5 га. Основные структурные звенья: участок приемки и подготовки сырья; сушильный комплекс; цех по производству клееного профилированного бруса и домокомплектов для коттеджей из этого материала (площадь примерно 3200 м2); цех по производству каркасно-панельных домов (площадь примерно 3300 м2); склад готовой продукции; котельная; административный корпус. «Финансирование проекта велось за счет привлечения денежных средств частным инвестором, который является владельцем предприятия, - рассказывает руководитель ОП ООО «АРДИС» Игорь Черединов. - Здание для брусового цеха на территории завода уже было построено, инженеры и технологи «АРДИСа» подбирали и приобретали для этого производства лучшее в своем классе оборудование у немецких и финских машиностроителей и совместно с инженерами этих компаний «вписывали» его в имевшиеся площади. Корпуса каркасно-панельного производства и расстановку техники на этих площадях проектировали специалисты немецкой компании Weinmann - поставщики оборудования». У предприятия мощный производственный потенциал. В машинном парке завода «АРДИС» оборудование лучших европейских производителей: Weinig Group, Rex Maschinenfabrik GmbH, GreCon Greten GmbH & Ко KG), Weinmann Holzbausystemtechnik GmbH (входит в HOMAG Group AG), Hundegger Maschinenbau GmbH (все - Германия), Muehlboeck Vanicek (Австрия), Makron Engineering (Финляндия), AkzoNobel (Голландия), ЗАО «Консар» (Россия) и др. Имеющихся мощностей достаточно для изготовления в год 200 комплектов деревянных домов площадью 250 м2 каждый.
«Сегодня мы производим в месяц 1300-1400 м3 клееного бруса, который используется для изготовления элементов и конструкций как домов из бруса (по скандинавской технологии), так и каркасно-панельных домов (по немецкой технологии). В месяц мы изготавливаем 10-15 каркасно-панельных домов (средняя площадь одного - 120 м2). Для того чтобы обеспечить такие объемы производства, нам требуется в месяц более 2000 м3 высушенной древесины, и с этой задачей отлично справляется наш сушильный комплекс, - говорит Игорь Анатольевич, показывая на выстроившиеся в ряд сушильные камеры периодического типа известной австрийской фирмы Muehlboeck Vanicek. - В комплекс входят пять камер объемом разовой загрузки 55 м3 каждая, две камеры по 65 м3 и две по 135 м3, итого 670 м3 разовой загрузки».
Древесное сырье - обрезной пиломатериал (в основном сосновые и еловые доски) - автомобильным транспортом доставляется в «АРДИС» из Архангельской, Вологодской, Иркутской, Брянской и Ярославской областей. Основные поставщики - ООО «Древоделец» (г. Чуна, Иркутская обл.), ООО «Кострома-Инвест» (г. Ярославль), ООО «ДОЦ» (г. Брянск). Получатель сырья предъявляет к поставляемым пиломатериалам строгие требования в соответствии с ГОСТом 8486-86 и разработанными сотрудниками ОП ООО «АРДИС» техническими условиями, в которых четко прописаны все нормативы: по сучкам, трещинам, гнили, грибковым поражениям, червоточинам, смоляным кармашкам, обзолу и т. д. «Надо сказать, что наши поставщики дорожат партнерскими отношениями с "АРДИСом" и стараются придерживаться наших требований», - отмечает руководитель предприятия.
Доставленные пиломатериалы тщательно сортируются по породам и качеству, часть сырья складируется на площадке временного хранения - для создания межсезонного запаса, часть укладывается в сушильные пакеты, которые с помощью автопогрузчиков загружаются в сушильные камеры. Древесину сушат в мягком режиме в течение 10-12 дней, всеми параметрами процесса управляет компьютер. В результате достигается оптимальная - равномерная технологическая влажность пиломатериалов (8-10%), что обеспечивает полную сохранность древесных волокон и исключает риск усадки, растрескивания и деформации заготовок, из которых и будет изготавливаться клееный брус. У бруса, который производится на заводе в Ступино, помимо множества достоинств, присущих этому виду строительного материала, есть несколько особенностей.
Производство клееного бруса
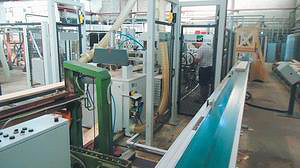
Линия сращивания на мини-шип производства компании
GreCon обеспечивает клееному брусу и отличную
прочность и эстетическую привлекательность
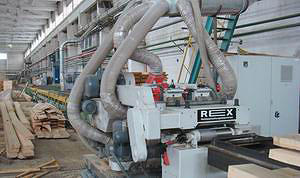
Строгальные станки компании Rex используются для
первичной и чистовой строжки материалов
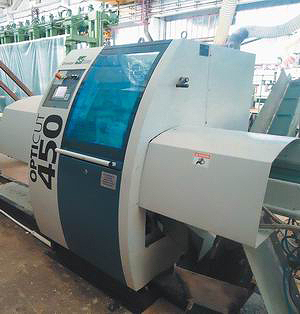
На станке-оптимизаторе Opti-Cut (Weinig) из досок
вырезаются и удаляются участки с дефектами
Деревянные дома от компании «АРДИС» отличают добротность, надежность, их высокие теплозащитные свойства обеспечивают в жилье оптимальный микроклимат, а фитонциды, выделяемые древесиной хвойных пород, которая используется для изготовления клееного бруса, оказывают благотворное действие на здоровье людей. Кроме того, такое жилье не нуждается в дополнительной отделке. Клееный брус используется и для создания домокоплектов коттеджей (финская технология), и для производства каркасно-панельных домов (немецкая технология). Кроме того, при строительстве домов из клееного бруса можно использовать панели перекрытия, кровельные и внутренние стены, выполненные по каркасно-панельной технологии, благодаря чему снижается стоимость квадратного метра здания. Итак, профилированный клееный брус - основной конструктивный материал для домов, которые проектирует, изготавливает в заводских условиях и монтирует компания «АРДИС». Поэтому есть смысл подробно рассказать о технологии изготовления этого материала на подмосковном предприятии.
На заводе «АРДИС» производят клееный брус длиной 20 (двадцать!) м, что обеспечивает дополнительные возможности при проектировании домов и позволяет значительно уменьшить объемы отходов деревообработки. Есть и еще одна особенность, но о ней чуть позже. Высушенные до технологической влажности пиломатериалы подвергают первичной строжке на четырехстороннем строгальном станке Rex (производитель - компания Rex Maschinenfabrik GmbH, Германия). Затем их выдерживают в течение суток, после чего доски поступают на линию оптимизации. Операторы внимательно просматривают движущиеся мимо них по транспортеру доски и флуоресцентным маркером отмечают дефекты и пороки, а также сортируют пиломатериалы по качеству.
Доски с обнаруженными дефектами отправляются на станок-оптимизатор Opti-Cut 450 (производитель - Weinig Group, Германия), на котором вырезаются и удаляются участки с дефектами. Подготовленные заготовки движутся по транспортеру к оператору, он еще раз проверяет качество досок и, перед тем как отправить на линии сращивания, сортирует, базирует и распределяет по двум потокам - для изготовления лицевых и внутренних ламелей бруса. По транспортеру заготовки доставляются на линии сращивания на мини-шип GreCon (производитель - компания GreCon Greten GmbH & Ко KG, Германия). На этом автоматизированном оборудовании, которое было изготовлено под заказ и поставлено на завод в 2012 году, ламели сращиваются на мини-шип (мебельный шип) с использованием двухкомпонентного клея международного концерна AkzoNobel.
станок Rex Homs-760 (A-DA-VA), производитель –
компания Rex Maschinenfabrik GmbH, Германия
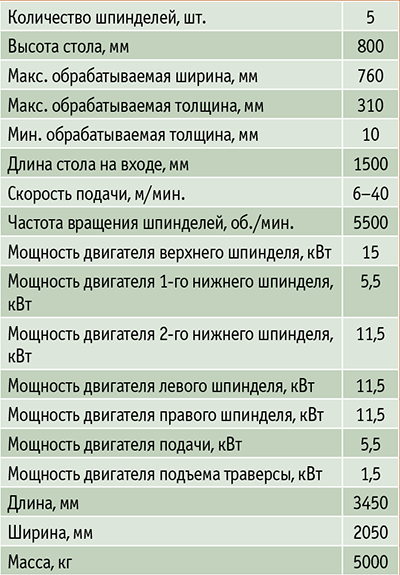
Таблица 2. Станок Opti-Cut 450 Quantum Dimter,
производитель – Weinig Group, Германия
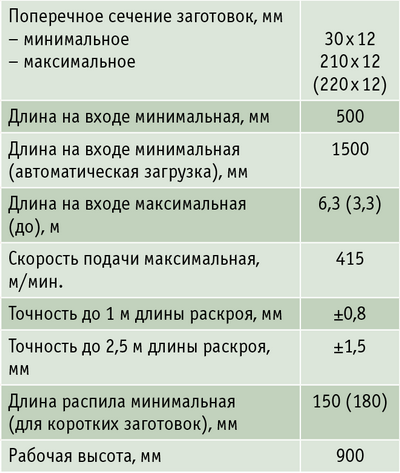
«При сращивании лицевых ламелей особое внимание уделяется тому, чтобы соседние сращиваемые участки максимально совпадали по текстуре и цвету древесины. В результате на выходе получаются ламели 20-метровой длины с почти незаметным глазу и не ощутимым на ощупь соединением с закрытым краевым стыком», - подчеркивает Игорь Черединов. Такое соединение выгодно отличает продукцию «АРДИСа» и обеспечивает готовому продукту - клееному брусу - дополнительные плюсы как по прочности, так и по эстетике. После накопления определенного количества ламели в полуавтоматическом режиме поступают на двухсторонний строгальный станок Rex для чистовой строжки с двух сторон. Затем из 20-метровых ламелей формируются заготовки для производства стенового бруса или балок, оператор настраивает клеенаносящую машину на автоматический режим и приступает к работе. На строганую поверхность раздельно наносятся клей и отвердитель, после чего ламель сбрасывается на накопительный стол. На этом столе формируются полные пакеты для загрузки пресса (по 10 шт. в каждом), которые отправляются на накопительный конвейер перед прессом. Далее сформированный пакет подается в пресс. На этом конвейере пакеты находятся более двух часов, что позволяет клею в соединениях ламелей полностью полимеризоваться. Затем - в зависимости от заказа (от этого зависит сечение бруса) - оператор подает в клеенаносящую машину концерна AkzoNobel требуемое количество лицевых и внутренних ламелей. Оборудование, которым оснащен завод, позволяет производить клееный брус сечением до 280 мм.
«Для изготовления нашего клееного бруса мы используем двухкомпонентный меламино-карбамидный клей международного концерна AkzoNobel - мирового лидера в производстве клеевых материалов для деревообрабатывающей промышленности, - говорит руководитель «АРДИСа». - Этот клей гарантирует качественное и весьма прочное соединение, кроме того, он экологически безопасен и не нарушает способность древесины "дышать". А это одна из важных характеристик домов из клееного бруса. Кстати, на нашем производстве используется одна из самых последних моделей клееналивной установки этой голландской фирмы. Мы очень довольны этой "умной" машиной, которая отмеряет для каждой ламели - в зависимости от ее места в "слоеном пироге", каким является клееный брус, - требуемое количество клеевого состава с учетом периода открытой выдержки. Оптимальный расход (300 г на квадратный метр поверхности) обеспечивает существенную экономию клея без риска потери качества готовой продукции». В год «АРДИСу» требуется почти 60 т клея.
После заполнения формирующего стола ламели поступают в пресс российского производства, который изготовлен под заказ и поставлен на завод в 2009 году. Продолжительность склейки партии бруса составляет от одного до полутора часов. После окончания цикла склейки брус вынимается из пресса и подается на автоматический станок Makron (производитель - компания Makron Engineering, Финляндия), на котором выполняется профилирование материала в зависимости от типа деревянного дома.
Дома по финской технологии
Дома, построенные по финской технологии, имеют множество неоспоримых достоинств, прошли проверку временем и давно доказали свою востребованность потребителями. Для производства домокомплектов коттеджей из клееного бруса на заводе «АРДИС» брус строгается на станке Makron, а затем по транспортерам отправляется на высокоточный обрабатывающий центр с ЧПУ Logmatic (производитель - Makron Engineering).
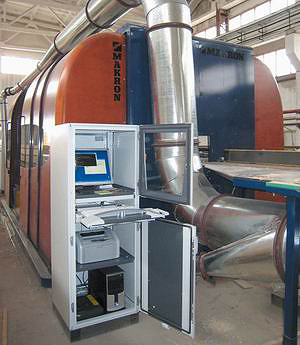
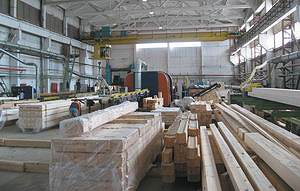
Общий вид производства клееного бруса. На переднем
плане – упакованные в пленку элементы очередного
домокомплекта по «финской» технологии
Таблица 3. Технические характеристики ОЦ
Logmatic (производитель – Makron Engineering,
Финляндия)
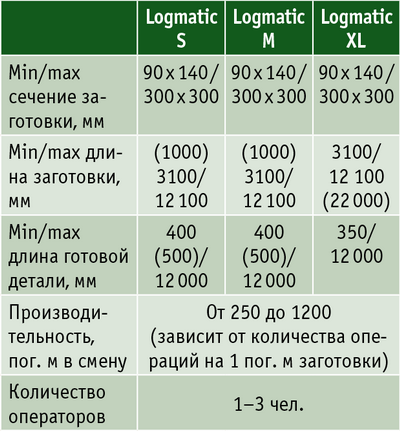
Поступивший к обрабатывающему центру брус оценивается оператором на наличие видимых дефектов, вращая брус с помощью специального устройства. Выявленные дефекты отмечаются оператором и автоматически выторцовываются с оптимизацией раскроя. Эта операция позволяет гарантировать высокое качество поверхности стены дома без трудоемкого и недолговечного ремонта.
В соответствии с конкретным заказом и индивидуальным проектом дома (который в виде машинных кодов передается на завод из архитектурно-проектного бюро московского офиса «АРДИСа») на этом мультиинструментальном деревообрабатывающем комплексе изготавливаются уникальные конструктивные элементы будущего дома, а также зарезаются все «чашки» венцовых соединений, выбираются и просверливаются все необходимые отверстия под нагели и шпильки, фрезеруются пазы под скрытую электропроводку и другие коммуникации, а также под «обсаду» дверных и оконных блоков и для Т-образного соединения стен без перерубов. Стыковочные узлы дома, построенного из клееного бруса с финским классическим профилем, не промерзают, в них не попадает влага, не заводится грибок.
Кроме того, ОЦ Makron выполняется маркировка каждой детали в соответствии с рабочими чертежами проекта, что обеспечивает быструю и безошибочную сборку дома на объекте. Перед упаковкой выполняется окончательный контроль качества и количества деталей. Оператор считывает сканером штрих-код с этикеток деталей, отвечающих всем требуемым параметрам, а система управления формирует упаковочную спецификацию на проверенные детали. Если в пачке выявляется дефектная деталь, то ее штрих-код не сканируется, и она попадает не в упаковочный лист, а в лист производства. Эта система защищает клиентов компании от недопоставленных вовремя деталей и простоев строителей во время сборки домов.
Стропильные части крыши и перекрытий дома изготавливаются на автоматизированном обрабатывающем центре Hundegger (производитель - Hundegger Maschinenbau GmbH, Германия). Готовые детали и элементы домокомплекта складываются в пакеты на прокладки, упаковываются в пленку и отправляются на склад готовой продукции, откуда в соответствии с графиком отгружаются по адресам заказчиков.
На строительной площадке рабочие в короткий срок (не более месяца) на заранее подготовленном ленточно-свайном фундаменте собирают дом из пронумерованных элементов по чертежам. Использование межвенцового утеплителя обеспечивает дополнительную защиту от продувания и промерзания в местах стыка брусьев, что исключает риск возникновения «мостиков холода», а также способствует дополнительному теплосбережению в доме. Внутренние и внешние стены дома из клееного бруса гладкие и не требуют дополнительной отделки, что позволяет экономить на внутренней отделке.
Дома по немецкой технологии
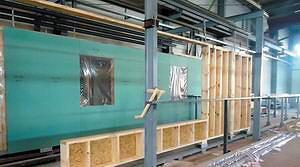
Так выглядят панели будущих домов по немецкой
технологии
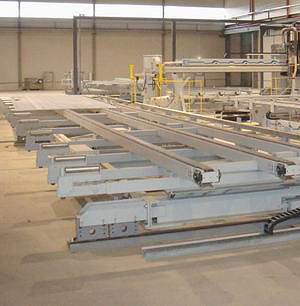
Завод укомплектован автоматизированной линией по
производству стен и перекрытий для каркасно-
панельных домов Weinmann
Дома по каркасно-панельной технологии, которые производит и строит ООО «АРДИС», создаются и возводятся с использованием немецкой технологии строительства. В соответствии с этой технологией стеновые панели и другие элементы домов изготавливаются на самом современном автоматизированном оборудовании лучших германских машиностроителей. Полные домокомплекты в виде готовых панелей наружных и внутренних стен, перекрытий и крыш изготавливаются на заводе. Проектирование домов и все операции по предварительному раскрою и обработке пило- и плитных материалов: разрезание по размерам, фрезерование соединительных пазов, сверление отверстий, маркировка и нанесение монтажных линий - ведутся в строгом соответствии с требованиями технологии по компьютерной программе компании SEMA (Германия).
В качестве каркаса для домокомплекта этих зданий используется клееный многогребневый (шпунтованный) брус. Такой профиль - «гребенкой» - формируется на 20-метровых заготовках на многофункциональном автоматизированном обрабатывающем центре Makron.
«Мы связываем с развитием каркасно-панельного домостроения в России будущее нашего предприятия, - говорит Игорь Черединов. - По эксплуатационным характеристикам и уровню комфорта дома, возводимые по немецкой технологии, как нельзя лучше подходят для климатических условий многих регионов нашей страны. Например, толщина панельных стен домов, которые изготавливаем мы, - от 235 до 275 мм, по тепловым характеристикам они отвечают условиям строительства в районах Крайнего Севера. Поэтому мы уверены, что такие дома с каждым годом будут все больше востребованы на рынке. Производственные мощности и потенциал нашего завода дают основания с оптимизмом смотреть в будущее: заказчиков у нас будет много».
На первом этапе технологического процесса на автоматизированном станке Hundegger (производитель - компания Hundegger Maschinenbau GmbH, Германия) в соответствии с параметрами индивидуального проекта дома выполняется раскрой пиломатериалов и изготовление отдельных деталей будущего домокомплекта. На каждый элемент с помощью принтера наносится маркировка, которая соответствует нумерации, указанной в рабочих чертежах. Затем заготовки - в зависимости от назначения - направляются на автоматизированную линию по производству стен и перекрытий, которая спроектирована и поставлена на подмосковное предприятие одним из ведущих производителей оборудования для производства каркасно-панельных домов - немецкой компанией Weinmann Holzbausystemtechnik GmbH (входит в HOMAG Group AG).
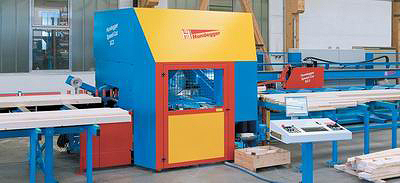
Раскрой пиломатериалов и изготовление отдельных деталей
домокомплекта по немецкой технологии ведется на автоматизированном
станке Hundegger
Каркас зашивается с двух сторон плитными материалами, пустоты между плитами заполняются минеральными теплоизоляционными уплотнителями (это современные экологичные материалы Isover или Knauf, качество которых подтверждено международными сертификатами). Второй слой утеплителя укладывается на фасады внешних стен (что позволяет избежать риска появления точки росы в стеновых панелях, а также повышает теплоизоляционные характеристики дома). Затем устанавливаются направляющие для прокладки кабеля электропроводки, выполняется внутренняя и наружная отделка элементов облицовочными материалами (черновая и чистовая штукатурка, для внутренних стен - зашивка гипсокартоном), изготавливаются проемы под окна и двери, наносятся монтажные линии для упрощения сборки на стройплощадке. По желанию заказчика на заводе можно установить оконные блоки со стеклопакетами и дверные блоки, которые производятся на заводе.
Hundegger Speed-Cut SC-3
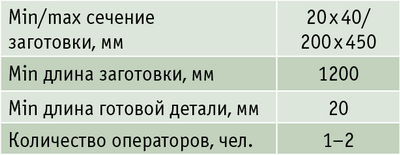
На стройплощадку готовые панели дома доставляются на низкорамных платформах. «Обычно бригада рабочих такой дом (средняя площадь 160 м2) собирает по монтажным чертежам за несколько дней, - говорит менеджер по контролю качества строительства компании «АРДИС» Дмитрий Киртаев. - Качество монтажа всегда высокое, и у заказчиков почти не бывает замечаний, а если и бывают, мы их внимательно рассматриваем и стараемся удовлетворить все просьбы клиентов».
«Словом, каркасно-панельный дом, тщательно спроектированный нашими архитекторами и изготовленный на нашем заводе по немецкой технологии, - это добротное и комфортное жилье для семьи, которое можно приобрести по приемлемой цене», - заключает руководитель ОП ООО «АРДИС». Ну что ж, эти слова еще раз подчеркивают приверженность предприятия девизу «Высокое качество - по разумной цене».
Инфраструктура, оптимизация процессов
Конечно, рассказ о предприятии был бы неполным без представления вспомогательных служб и трудового коллектива завода.
В производственных помещениях установлена система аспирации производства компании «Консар» (г. Саров, Нижегородская обл.), которая является деловым партнером «АРДИСа» с 2005 года. Система не только удаляет опилки от станков и очищает воздух от пыли, но и возвращает теплый воздух в цеха, что способствует тепло- и энергосбережению. Система спроектирована и установлена так, что ее отдельные звенья работают именно на тех участках, на которых в настоящий момент ведется деревообработка, то есть остальные звенья системы не работают вхолостую. Опилки по трубопроводам поступают в накопительный бункер, который находится у корпуса котельной.
Кусковые отходы производства перерабатываются на рубительной машине в технологическую щепу. Опилки и щепа используются в качестве топлива для сжигания в двух котлах малой мощности - по 0,8 МВт и в котле мощностью 4 МВт производства Ковровского завода, которые вырабатывают тепло для обеспечения нужд производства (сушильный комплекс) и отопления административных и производственных помещений. Котлы малой мощности используются в летнее время, а мощный котел задействуется в холодный период года.
«Сейчас мы работаем над тем, чтобы рационально использовать часть образующихся крупных кусковых отходов, например обрезков ламелей, из которых собираемся изготавливать клееный брус для каркасно-панельных домокомплектов, - делится планами развития предприятия его директор. - Кроме того, в ближайшее время мы намерены увеличить производственную площадку завода за счет присоединения соседней территории. Это позволит еще больше расширить наши возможности и более эффективно использовать имеющееся в нашем распоряжении современное оборудование. Сейчас линия Weinmann вписана в помещение цеха таким образом, что оборудование разделено на две части и детали домокомплектов приходится как бы поворачивать на 180 градусов и пускать в обработку на станках, установленных параллельно. С расширением территории мы сможем достроить здание каркасно-панельного цеха и организовать сквозную (прямую) линию по производству домокомплектов для домов по немецкой технологии».
По словам руководителя предприятия, сегодня на заводе «АРДИС» работают 95 человек, большинство из них живут в г. Ступино, расположенном неподалеку г. Кашира, а также в близлежащих поселках.
Операторы основного оборудования в период его установки и запуска на заводе прошли обучение у иностранных специалистов. Кроме того, Игорь Черединов, который возглавил предприятие в конце осени прошлого года, внес в организацию производственных процессов несколько существенных изменений.
Во-первых, было сокращено количество типоразмеров пиломатериалов и готового бруса, что позволило стандартизировать производство и упорядочить процессы. Предприятие перешло на работу в две смены по 12 часов, что позволяет добиться оптимального рабочего ритма и избежать накладок при пересменках. На каждом рабочем месте есть сжатая, изложенная доступным языком инструкция по обслуживанию оборудования. Сотрудники, занятые на самых ответственных участках, обязаны раз в год проходить аттестацию.
В результате производительность за смену выросла с 450 до 1000 м3 при сохранении уровня оплаты труда. Кстати, сегодня средняя заработная плата на предприятии достигает 25 тыс. руб. в месяц. Сотрудники обеспечены полным социальным пакетом, горячим питанием (готовые обеды) за счет предприятия, тем, кто живет в собственных домах в пригородах
Ступино, бесплатно отпускаются дрова для отопления, а также другие отходы основного производства для использования в дачном строительстве.
Благодаря высокому качеству продукции, изготовленной на современном оборудовании лучших европейских машиностроителей по самым эффективным технологиям, а также разумной стоимости домокомплектов дома «АРДИС» становятся все более и более востребованными на рынке деревянного домостроения. И поэтому подмосковное предприятие по праву входит в тройку крупнейших производителей деревянных домов в Российской Федерации.
Александр РЕЧИЦКИЙ
Фото автора