Изготовление ламелей для КДК
В предыдущей публикации мы разобрали вопросы принципиального проектирования цеха, общей производительности и мощности прессового оборудования. В этой рассмотрим необходимость и возможности выбора строгального оборудования, линии сращивания и оптимизатора.
Главный вопрос, который требует ответа при комплектации производства клееных деревянных конструкций: насколько необходима линия сращивания? Абсолютно необходима, если вы предполагаете изготавливать конструкции длиной более 6 м, но если они будут меньшей длины, можно обойтись и без этого оборудования. В стандартах четко прописаны ограничения по порокам древесины в КДК, поэтому при отсутствии линии сращивания потребуется очень строгий подход к качеству поставляемых на производство пиломатериалов: приемка по шаблону, тщательная сортировка, выбраковка. При наличии линии сращивания можно использовать пиломатериалы более низкой сортности. Многолетний анализ работы разных производств показал, что наличие или отсутствие линии сращивания не влияет на себестоимость готовой продукции при условии выпуска продукции, соответствующей ГОСТам.
Все линии сращивания на производствах КДК можно подразделить на две группы: конечные и бесконечные. В состав конечных входят шипорезный и клеенаносящий узел, после которого подготовленные заготовки длиной 6 м с нарезанным шипом и нанесенным на него клеем попадают на стол прессования, где выполняется подпрессовка шиповых соединений с торца всей заготовки, затем выравнивание высоты по всей длине приложением давления во всю длину по пласти. Прессование ведется в течение 10-20 сек., затем заготовка сбрасывается в буфер, где выдерживается перед дальнейшей обработкой.
Бесконечные линии сращивания до столов прессования выстроены так же. Однако на бесконечной линии подпрессовка каждого последующего сегмента заготовки выполняется по отдельности, затем следует протяжка заготовки и добавление следующего сегмента. Таким образом получается заготовка необходимой длины, которая выставляется в зависимости от длины пресса на производстве, но принципиально длина может быть изменена в любой момент, что очень удобно при обработке большого количества заготовок заданной длины.
Для изготовления КДК бесконечные линии сращивания предпочтительнее. Многие небольшие предприятия на стадии запуска производства делают выбор в пользу конечных линий, однако через несколько лет именно эти линии становятся причиной, тормозящей рост производительности, наращивание мощностей прессового оборудования и переход на освоение выпуска заготовок длиной более 6 м. Сегодня существенной разницы в цене на бесконечные и 6-метровые линии уже нет, поскольку в России ряд предприятий наладили выпуск вполне работоспособных моделей бесконечных линий сращивания.
Шип и клей
В соответствии с существующими российскими нормами, размер шипа КДК должен быть не менее 18 мм (по европейским нормам, 15 мм), шиповое соединение должно выдерживать нагрузку 27 МПа. Ориентация шипа - горизонтальная или вертикальная - не определена. Чаще всего используется вертикальный шип, при таком соединении на пласти можно увидеть зубцы шипа. Казалось бы, горизонтальный шип смотрится интереснее - на шиповом соединении по пласти он почти не заметен. Дело в том, что при одном и том же сечении заготовки вертикального шипового соединения по площади больше горизонтального, поэтому выше качество склейки и больше шансов, что готовое изделие пройдет норматив по нагрузке шипового соединения.
Три основных типа шипорезов: отдельно стоящие, парные паркетные и парные проходного типа.
Отдельно стоящие. Шипы на подобных агрегатах зарезаются вручную на одной заготовке либо на пакете. Это оборудование используется только с конечными малопроизводительными линиями и только на небольших производствах. У него нет ресурса для увеличения производительности, оно серьезно зависит от так называемого человеческого фактора.
Парные пакетные. Устанавливаются в линию последовательно. Пакет заготовок набирается до определенного количества, затем нарезается шип на одной стороне заготовок и они подаются на следующий узел, где шипы нарезаются на второй стороне заготовок. У такого оборудования есть ресурс для повышения производительности. Оно используется в основном на линиях бесконечного сращивания, но встречается и на 6-метровых. Основной минус этого оборудования: необходима точная регулировка соосности фрез на разнесенных в стороны шипорезах, что требует длительной настройки и точной установки.
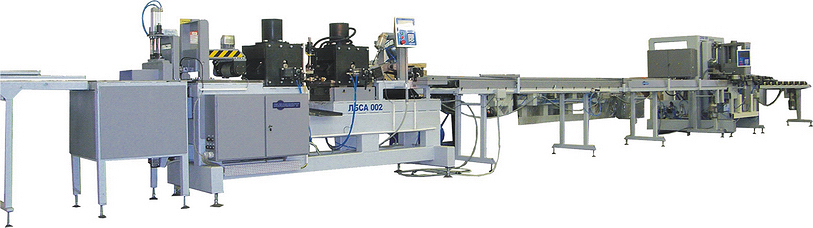
Автоматическая линия беспрерывного сращивания ЛБСА 002 («Бакаут»)
Парные проходного типа. Шип нарезается одновременно на двух подающихся последовательно заготовках на одном узле, где закреплены сразу две фрезы, за один такт прохода шипорезного узла. Это наиболее производительная система, позволяющая добиться высокой точности обработки. Такие агрегаты используются на линиях бесконечного сращивания.
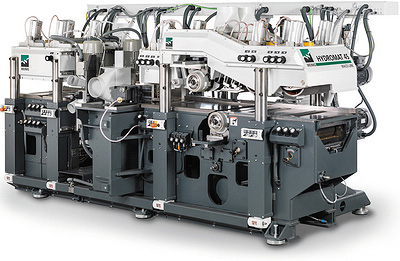
Линия сращивания PowerJoint15 в комбинации с торцовочным станком
OptiCut450 XL (Weinig)
При этом практика показывает, что от степени автоматизации шипореза производительность линии прессования почти не зависит. В настоящее время для техники большинства производителей характерна скорость прохода заготовки в линии сращивания около 30-40 м/мин. (следует учесть, что этот показатель вторичен и не оказывает прямого влияния на производительность линии). Гораздо большее влияние на производительность линии сращивания оказывает количество тактов в минуту самого пресса, поскольку именно этот агрегат обеспечивает реальную скорость линии сращивания в целом, и нет никакого резона в увеличении скорости подачи заготовок, если пресс не успевает отрабатывать их все. При наличии одного 6-метрового пресса вполне достаточно двух тактов в минуту, при наличии большего количества прессов следует рассматривать варианты, когда выполняется не менее четырех тактов в минуту. Дальнейшее наращивание производительности зависит уже от степени автоматизации всей линии (в частности, от автоподачи заготовок на всех этапах обработки и скорости этого процесса). Производства, которые вооружены прессами длиной не менее 24 м, целесообразно оснащать двумя линиями сращивания. При заказе оборудования следует также обращать внимание на заявленную производительность и уточнять у поставщика, на заготовки какой длины рассчитана эта производительность. Как ни печально, большинство мировых производителей завышают реальную производительность линий сращивания на 30-50%.
Виды узлов клеенанесения: отдельно стоящие, роликовые, дюзовые.
Отдельно стоящие. Это клеенаносящие ролики из фторопласта, вращающиеся над ванной с клеем. Подача ручная. Используются исключительно на небольших производствах.
Роликовые. Похожи по принципу действия на отдельно стоящие, но смонтированы непосредственно на шипорезах и работают параллельно с фрезами. Клей наносится сразу после нарезки шипа. Устанавливаются на пакетные шипорезные узлы. Клеенанесение нерегулируемое.
Дюзовые. Монтируются непосредственно на шипорезном узле, обычно на узлах проходного типа, реже встречаются на пакетных шипорезах. Клей наносится на шип под высоким давлением сразу после нарезки шипа. Возможна тонкая регулировка точности клеенанесения. Высокопроизводительные линии комплектуются исключительно дюзовыми узлами клеенанесения.
Уловки производителей оборудования
При заказе линии сращивания для производства КДК необходимо помнить, что российскими и европейскими нормами для шипового соединения не допускаются ПВА-клеи. Однако, по умолчанию, все линии сращивания комплектуются узлами клеенанесения именно под ПВА. Также, по умолчанию, устанавливаются 12-миллиметровые фрезы. Это одна из самых распространенных ошибок при заказе этого вида оборудования, и впоследствии приходится вкладывать существенные средства в доработку названных узлов. Необходимо заказывать узлы для раздельного нанесения меламинформальдегидных клеевых материалов, согласно российским нормативам. В соответствии с европейскими нормативами возможны еще два варианта: узел смешивания для эмульсии полимерного изоцианата или для однокомпонентного полиуретана. Следует четко понимать: если вы планируете выпускать не только клееные конструкции для малоэтажного домостроения, но и несущие конструкции, последние два варианта вам не подойдут ни при каких условиях. Остается только один: раздельное клеенанесение под меламин- или резорцинформальдегидные клеевые системы. Принципиально эти клеевые материалы можно наносить и в смеси, но на практике смесь почти нигде не используется, поскольку требует частой промывки узлов клеенанесения.
В пакетных линиях узел клеенанесения уже приспособлен для раздельного нанесения клеевых материалов. Если пакетная линия оборудована одним шипорезным узлом, то на ней можно будет использовать только ПВА. Вывод: подобные линии для производства КДК неприемлемы.
Дюзовый узел клеенанесения следует заказывать на стадии согласования договора поставки. Наиболее распространен и часто предлагается производителями узел для однокомпонентных полиуретанов. Переделать такой агрегат под раздельное нанесение невозможно, потребуется его существенная доработка либо замена.
Клеевые материалы и нюансы клеенанесения мы рассмотрим в отдельной публикации.
Оптимизатор
При выборе оптимизатора необходимо руководствоваться габаритами возможной заготовки и производительностью остального оборудования, чтобы его технические возможности могли соответствовать возможностям линии сращивания. Сегодня все чаще на операции оптимизации используют электронные системы отслеживания пороков древесины, скрытых пороков, сортировки заготовок по влажности. Эти системы, конечно, довольно дороги, но существенно повышают производительность этого участка. Правда, зачастую подобные электронные компоненты на предприятиях на задействованы, поскольку либо не нужна высокая скорость работы оптимизатора, либо качество пиломатериала таково, что эти системы невозможно использовать. Для обеспечения скоростной работы линии сращивания гораздо большее значение имеют приводные рольганги и поворотные столы, и на них экономить не стоит.
Очень важно при заказе линий сращивания прописывать в договоре поставки монтаж оборудования силами производителя (по крайней мере шеф-монтаж), выполнять монтаж собственными силами можно лишь при глубокой уверенности в профессионализме своих сотрудников. Почему это так важно? Дело в том, что линии сращивания большой протяженности и многие ее элементы большой длины. Точность их установки позволит уменьшить процент будущих потерь при обработке сращенных заготовок (наиболее распространенный дефект сращивания - «ступенька», которую впоследствии необходимо сострогать в ноль). Самые распространенные причины возникновения «ступеньки»: пиломатериал низкого качества и неравномерной геометрии; отсутствие соосности фрез шипореза; неверно выставленные уровни приемоподающих рольгангов, пресса и шипорезов. В случае монтажа линии силами поставщика решение названных проблем ляжет на его плечи. Также нужно знать: монтаж и регулировка линии сращивания бесконечного типа с автоматическими системами подачи продолжается в среднем полгода, иногда дольше. Для того чтобы поставить оборудование для линии, много времени не требуется. А вот регулировки, причем как у импортных, так и у российских поставщиков, занимают очень много времени.
Как сделать заготовку необходимой длины, мы разобрали. Теперь перейдем к рассмотрению процесса строгания.
Четырехсторонники
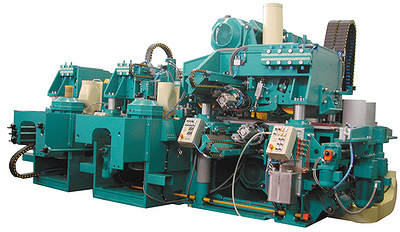
Тяжелый универсальный строгальный станок Ledinek Superles
Нехитрый расчет показывает, что для производства 500 м3 КДК требуется четырехсторонний станок со скоростью строгания 12 м/мин. С такой скоростью работают все современные модели подобного оборудования. Для небольшого предприятия с одним прессом достаточно приобрести любой современный четырехсторонник, главное, чтобы он мог обработать заготовку необходимого сечения и требуемой длины. Но всегда есть нюансы, которые следует учитывать.
При производстве КДК принципиально важна геометрия строжки. Стандартами жестко определены как геометрические размеры готовых изделий, так и прочность клеевых соединений, которые напрямую зависят от толщины клеевого шва. Для большинства клеевых систем максимально допустимая толщина клеевого шва - 0,3 мм. Это означает, что разнотолщинность ламели после финишной строжки должна быть не более 0,15 мм в любой паре точек на длине ламели. Такая малая величина допустимой разнотолщинности определяет довольно жесткие требования к используемым четырехсторонникам.
Общие требования к четырехстороннему станку для финишной строжки: максимально тяжелая станина, строгальные барабаны с дополнительными гидроопорами, двигатели мощностью от 6 кВт (лучше 15 кВт), рабочая скорость от 12 м/мин. (максимальная всегда выше примерно на 30%), не менее пяти шпинделей. Пятый шпиндель необходим для подравнивания геометрии строжки. Если линии сращивания нет, достаточно одного 5-шпиндельного четырехсторонника. Если на предприятии планируется использование линии сращивания, потребуются минимум два четырехсторонника - один для вскрытия дефектов перед оптимизацией, а второй - после линии сращивания, перед прессованием. В принципе, перед линией сращивание возможно использование даже рейсмуса тяжелого класса, но, во-первых, это оправдано только при наличии линий сращивания проходного типа, а во-вторых, требует очень точной нивелировки приемо-подающих рольгангов, а тут уже впору усомниться в рентабельности такой затеи. Производственники до сих пор спорят - где именно ставить более мощный четырехсторонний станок: до или после линии сращивания.
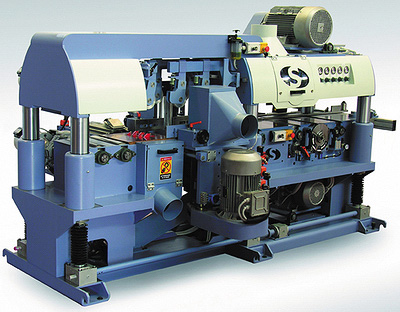
Двухсторонний строгальный станок Spanevello Universal 300
Лично мне больше импонирует следующая схема: перед оптимизатором устанавливается 5-шпиндельный четырехсторонник с мощностью приводов от 6 кВт (лучше 9 кВт). На этом станке с заготовки снимается максимальный слой древесины - 1-1,5 мм с каждой стороны. После линии сращивания ставится 5-6-шпиндельный четырехсторонник, задача которого - снятие дефектов сращивания (ступеньки, винта), дополнительные шпиндели требуются для выведения чистой геометрии в соответствии со стандартами. Общий съем - по 0,3-0,7 мм на сторону. Такая схема позволяет использовать менее мощные приводы на станках и, как следствие, существенно экономить при закупке оборудования, однако требует серьезного внимания к регулировке линии сращивания, поскольку в противном случае уровень отходов будет очень высоким, что недопустимо.
Вторая схема такова: перед оптимизатором ставится 4-шпиндельный четырехсторонник, задача которого - исключительно вскрытие дефектов. Съем пиломатериала - около 0,5 мм с каждой стороны. При такой величине съема нет необходимости в высокой мощности приводов, на этот этап технологической цепочки можно поставить буквально любой станок любого производителя. После линии сращивания ставится 6-7-шпиндельный станок с мощностью приводов от 9 кВт (оптимальный вариант - 15) тяжелого класса, который обеспечивает как съем всех дефектов пиления и сращивания, так и выравнивание геометрии заготовки. Конечно, подобные станки требуют серьезных финансовых вложений. Однако у этой схемы есть один недостаток. При большом финишном съеме на ламели могут проявиться скрытые дефекты, что потребует дополнительной сортировки готовой заготовки бруса. С другой стороны, эта схема позволяет в значительной степени сгладить возможные дефекты линии сращивания.
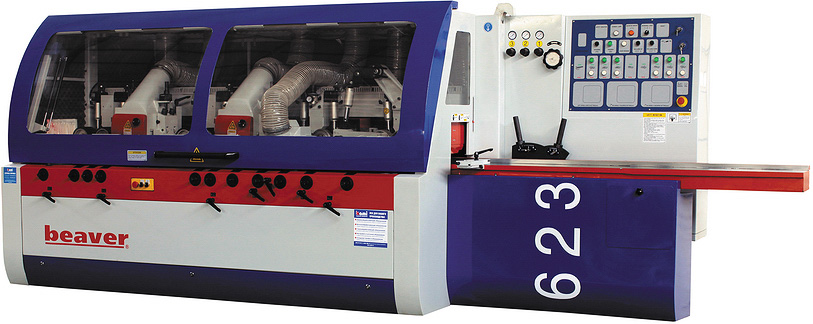
Четырехсторонний станок Beaver-623 («KAMИ»)
Пары подобных станков хватит для обеспечения участка прессования с 12-метровым прессом. При большем количестве прессов потребуется либо увеличивать парк строгального оборудования, либо рассматривать варианты установки высокоскоростных строгальных станков тяжелого класса. В таком случае необходимо рассматривать варианты станков со скоростью строгания от 80 м/мин., что связано со скоростью сборки пакета ламелей в пресс и корректной работой клеенаносящего оборудования.
Очень важный момент при проектировании линий строжки - установка подающих и приемных рольгангов. Они, во-первых, должны быть обязательно, иначе при строгании гарантированы выхваты и волны, во-вторых, рольганги должны быть установлены четко по уровню относительно станин четырехсторонников, в том числе должны быть нивелированы завалы. Без тщательной нивелировки все затраты на станочный парк пойдут прахом - при завале одного из рольгангов в сторону винт на строжке будет обязательно. Впоследствии при строгании заготовки любой разбитый подшипник ролика или замятие на рольганге будут приводить к появлению выхватов или непростроганных мест.
Также следует особое внимание обратить на гидроопоры строгальных барабанов. Сечение у заготовок для КДК довольно велико, поэтому даже на новых станках при строгании почти сразу образуется трапеция, а чуть позже и волна - коренные подшипники приходят в негодность очень быстро. Все станки должны быть обеспечены строгальными барабанами на замену, заточку ножей необходимо делать каждую смену. Если в результате всех циклов обработки на доске остались непростроги - эту ламель клеить нельзя, потребуется ее перестрожка в более тонкую заготовку.
Склейка досок возможна в течение не более 24 часов с момента строгания. Это обусловлено свойствами древесины, с течением времени закрываются вскрытые при строгании поры и адгезия клеевых материалов существенно снижается, что может спровоцировать брак готовой продукции. Отсюда следует правило: чем быстрее после строжки будет сделана склейка, тем лучше. Основное правило, по которому следует комплектовать строгальное оборудование и сопутствующую автоматику, - это выравнивание всех скоростей обработки на всех участках; при этом лучше ориентироваться на реальные скорости обработки, которые обычно, в силу очень многих причин (в том числе пресловутого человеческого фактора), на 30% ниже максимальных, заявленных производителями характеристик. Также рекомендую всегда закладывать до 20% производственных мощностей на необходимое увеличение производительности.
Михаил ТАРАСЕНКО,
www.pro-kleim.ucoz.ru
Клееные конструкции в деревянном домостроении
Клеи в производстве ДКК
Производство клееных деревянных конструкций. Инженерные системы
Производство клееных деревянных конструкций. Детали домокомплекта