Производство КДК
Детали домокомплекта
Мы рассмотрели нюансы технологии склейки заготовки будущего бруса или несущих конструкций. Переходим к завершающему этапу обработки - профилированию и нарезке деталей будущего домокомплекта.
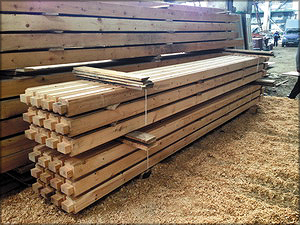
Заготовки, склеенные с использованием ММФ клеевых систем и конструкционных полиуретановых клеев, рекомендуется обрабатывать сразу после прессования. При применении ТВЧ-прессов - после стабилизации, то есть снижения температуры заготовок до уровня температуры окружающей среды. Связано это с природой названных выше клеевых систем и быстрым приобретением прочности клеевых соединений. Буквально через несколько часов после склейки заготовки уже можно отправлять на строительную площадку, клеевые швы набирают прочность и из-за этого при обработке деталей быстро тупятся ножи. Не выручает даже сталь марки HSS. Ножей хватает до переточки на обработку 120-150 пог. м заготовок. А вот в случае обработки деталей сразу после прессования переточка требуется примерно после обработки 1500-2000 пог. м заготовок.
Заготовки, произведенные с использованием ЭПИ клеевых систем, требуется выдерживать до обработки в течение от двух до 24 часов, в зависимости от конкретной клеевой системы - до необходимого набора прочности клеевых швов. Применять готовые изделия по назначению можно через три - семь суток после склейки. Заготовки, изготовленные с использованием ЭПИ клеевых систем, обрабатывать гораздо легче, режущий инструмент можно эксплуатировать в течение длительного периода без переточек. Обрабатывать сразу после склейки, без выдержки не рекомендуется - возможно повреждение клеевых соединений.
В зависимости от выбранной на производстве клеевой системы выполняется расстановка обрабатывающего оборудования - либо профилирующий станок ставится сразу после зоны склейки, либо там размещается буфер выдержки склеенных заготовок. В таком случае профилирующий станок может устанавливаться даже в отдельном помещении.
Что необходимо знать для правильного выбора профилирующего оборудования?
Есть несколько важных моментов. Один из них - сечение заготовки. В основном, производители изготавливают клееный стеновой брус сечением до 200х240 мм, а несущие конструкции сечением до 200х350 мм. Профилирование заготовок выполняется преимущественно вертикальными шпинделями, поэтому размеры створа станка должны быть не менее, чем 370х220 мм. Перед выбором профилирующего станка, следует также обратить внимание на то, что в последнее время все более востребована продукция элитного уровня - стеновой брус крупных сечений и фахверковые конструкции, при производстве которых не обойтись без деталей сечением до 270х320 мм - для стеновых элементов и сечением до 330х650 - для несущих конструкций.
Таким образом, перед приобретением профилирующего станка необходимо четко определить, исходя из потребностей ваших целевых заказчиков, заготовки с каким сечением будут обрабатываться на этом оборудовании. Ведь разница в стоимости четырехсторонних станков для профилирования деталей с максимальным сечением и станков для обработки заготовок с небольшим сечением, весьма существенна.
В силу того, что профилируемых заготовок как минимум в четыре раза меньше, чем обрабатываемых ламелей, скорость подачи в профилирующем станке может быть существенно ниже, чем в калибрующих четырехсторонниках. При этом не обязательно соблюдать высокоточную геометрию заготовки, однако следует обратить внимание на ее вес, поскольку он в четыре-пять раз превышает вес ламели, что оказывает существенные физические нагрузки как на опоры строгальных барабанов, так и на станок в целом. Выбор обычно останавливают на станках с невысокой производительностью, на которых можно обрабатывать заготовки с большим сечением. По причине невысокой скорости подачи на таком оборудовании не требуются приводы повышенной мощности, зачастую хватает и 6 кВт, но лучше все-таки ориентироваться на 9 кВт, чтобы избежать перегрева двигателей при непрерывной работе, при этом следует выбирать максимально тяжелую станину, что обеспечит высокое качество обработки.
Особое внимание следует уделить тому, чтобы станок находился максимально близко к аспирационной установке. При обработке заготовок на профилирующем оборудовании происходит максимальный съем пиломатериала - соответственно, образуется большой объем отходов - стружки, опилок, пыли, и поэтому чем ближе станок будет к циклону, тем ниже будет нагрузка на систему аспирации в целом. Требуется применять фрезы только с твердосплавными ножами, поскольку клеевые швы обладают гораздо большей механической прочностью, чем древесина. Заточку ножей надо выполнять через каждые 1500-2000 пог. м, не реже одного раза в смену.
Чашкорез или обрабатывающий центр
Сегодня на рынке представлен широкий выбор чашкозарезных станков и обрабатывающих центров. К сожалению, поставщики оборудования грешат тем, что в рекламных целях искажают характеристики этого оборудования, естественно, преувеличивая их возможности. Обычно мощность станка декларируется исходя из зарезок прямых чашек минимальных размеров на заготовке максимальных размеров. Поэтому цифру, отражающую производительность чашкорезов в рекламных буклетах, можно смело делить на два.
От чего зависит выбор станка? Исключительно от вашего видения перспектив предприятия. Если речь идет о выпуске простых домокомплектов с прямыми чашками, достаточно чашкозарезного станка небольшой производительности. Косые чашки, к примеру, на эркерах зарезают вручную. Однако если в вашем альбоме проектов есть проекты домов, при изготовлении элементов которых требуется зарезка чашек сложной формы или проекты домов, которые строятся из клееного бруса с использованием соединений типа «ласточкин хвост», следует обратить внимание на обрабатывающие центры. Как несложно догадаться, цена таких ОЦ выше цены обычных чашкозарезных станков в разы. Также необходимо предусмотреть заранее, будете ли вы проектировать и изготавливать домокомплекты со скрытыми коммуникациями - дооснащение чашкорезов фрезерами стоит недорого, но существенно снижает их производительность. Следует также учитывать, что в подавляющем большинстве моделей чашкозарезных станков позиционирование заготовок выполняется вручную оператором, что также влияет на производительность оборудования.
Обрабатывающие центры используются в случае, если требуется зарезка чашек сложной геометрии, фрезеровка пазов под скрытые коммуникации и обработка фахверковых конструкций в автоматическом режиме. Производительность обрабатывающих центров значительно выше, чем у простых чашкозарезных станков, в первую очередь - за счет автоматизации позиционирования заготовок и автоматической смены фрез. Конструкцией обрабатывающих центров предусмотрено много дополнительных опций, которые определяют их универсальность. Следует учитывать, что узлы и агрегаты для обработки крупноформатных заготовок шириной 650, 900 и даже до 1200 мм являются опцией и не входят в стандартную комплектацию обрабатывающих центров. Также некоторые производители предлагают в качестве опций оснащение ОЦ пятиосевой фрезой, и горизонтальной пилой, автоматической сменой фрез. То есть при использовании ОЦ со стандартной конфигурацией невозможно выпускать фахверковые конструкции произвольных форм, поэтому характеристики оборудования следует уточнять до момента его покупки.
Размещение в цехах чашкорезов и обрабатывающих центров может быть произвольным, там, где удобно производственникам. Зачастую это оборудование находится в разных помещениях, поскольку на скорость их работы другие станки никак не влияют. Важно знать, что для установки обрабатывающих центров, за редким исключением, требуются устройство основательного фундамента с приямком, что делает последующий перенос станка на другое место почти невозможным. Также требуется обеспечить максимально близкое расположение оборудования к циклону, либо установку отдельной прямой магистрали системы аспирации.
Хранение и транспортировка готовых изделий
Максимально доступно и развернуто правила транспортировки и хранения изложены в ГОСТ 20850-2014, раздел 9.
На период транспортирования и хранения на строительной площадке конструкции упаковывают на предприятии-изготовителе в полимерную пленку. Не допускается использование прозрачной пленки в качестве транспортной упаковки. Для уменьшения нагрева конструкций под воздействием солнечных лучей следует использовать двухцветную пленку: белой стороной наружу, черной стороной внутрь пакета конструкций. По согласованию с заказчиком, в случаях, когда конструкции предназначены для эксплуатации на открытом воздухе и защищены атмосферостойкими покрытиями, допускается поставка их без транспортной упаковки.
При погрузке, транспортировании, разгрузке и хранении элементов домокомплектов должна быть обеспечена их защита от механических повреждений, загрязнений, атмосферных осадков и прямого попадания солнечных лучей. Складирование и хранение элементов будущих строений на предприятии-изготовителе должны осуществляться на специально отведенном участке с обеспечением отвода грунтовых, талых и ливневых вод.
При длительном хранении заводская упаковка должна быть открыта снизу, что обеспечит проветривание конструкций и элементов и стекание воды, случайно попавшей внутрь упаковки через поврежденную пленку. Во избежание «парникового эффекта» хранение конструкций и элементов в герметичной паронепроницаемой упаковке, исключающей постоянное их проветривание и подсушивание, не допускается.
При складировании и хранении элементов домокомплектов на открытой площадке на срок более месяца должны быть предусмотрены меры по устройству временных укрытий в виде навесов, инвентарных щитов и т. п., исключающих попадание на деревянные конструкции атмосферных осадков и прямых солнечных лучей. При этом конструкции и элементы домокомплектов должны быть полностью освобождены от заводской упаковки. Изделия при хранении в штабелях или транспортных пакетах должны быть размещены на прокладках с толщиной не менее 30 мм. Высота прокладок не менее чем на 20 мм должна превышать высоту выступающих частей элементов и толщину стропов. Прокладки по высоте рядов располагают строго по вертикали. Количество прокладок и расстояние между ними должны исключить риск провисания и деформации конструкций и их элементов. При хранении в складских помещениях под нижний ряд штабеля или под нижний транспортный пакет должны быть уложены опоры высотой не менее 100 мм и не менее 500 мм - при хранении под навесом или на открытой площадке. Укладка конструкций и элементов непосредственно на грунт, а также хождение по ним не допускаются.
Обязательно нужно обрабатывать торцы готовых деталей специальными герметиками. Как ни хорошо и полно написаны правила хранения готовых изделий - они часто нарушаются как самими производителями, так и заказчиками на стройплощадках. Поэтому, во избежание растрескивания деталей по торцам, и как следствие - предъявления претензий со стороны заказчиков - настоятельно рекомендую производить эту несложную и недорогую операцию сразу после разбрусовки деталей, до их упаковки.
Поговорим о сушке
Я сделал этот технологический процесс темой отдельной главы потому, что считаю его наиболее сложным из всего вышеописанного. И дело здесь не в выборе оборудования - предложений разного уровня не просто много, а такое огромное количество, которое позволит удовлетворить абсолютно любые запросы. Речь скорее о моем личном понимании сушки: она требует наличия на заводе квалифицированного специалиста, действительно глубоко понимающего и чувствующего этот процесс.
Практика работы деревообрабатывающих предприятий свидетельствует о том, что первопричиной бракованной продукции является именно неправильная сушка древесного сырья. Попробуем разобрать причины.
Большинство предприятий не прибегают к атмосферной сушке пиломатериалов, несмотря на то, что она регламентирована ГОСТом. И понять производителей можно - большинство оборотных средств вкладывается как раз в пиломатериалы, поэтому все стараются максимально сократить срок изготовления готовых изделий. Про атмосферную сушку стараются даже не вспоминать. Поэтому не происходит стабилизации напряжений внутри древесины, как результат - в процессе сушки ламели деформируются.
Разбег по влажности древесины одной партии загрузки. Месторасположение пакета пиломатериалов одной партии в той или иной части сушильной камеры оказывает прямое влияние на степень просушки и пропаривания ламелей. В итоге в дальнейшую обработку поступает партия досок, разница влажности которых достигает 10%, что еще больше усугубляется в зимний период, когда в сушилки отправляют доски, раскроенные из мороженых бревен. Автоматика сушильных камер в таком случае в прямом смысле «сходит с ума», и датчики влажности показывают неверные значения уровня влажности древесины, поскольку количество датчиков ограничено и не отражает реальную картину происходящего в камере. В итоге в цех обработки попадает пиломатериал с превышенным уровнем влажности, что в конечном счете влияет на качество склеивания.
Смола
Смола, выделяемая хвойными породами, препятствует адгезии клеев. Поэтому от смолы в пиломатериале необходимо избавиться. В ходе процесса сушки, смола, находящаяся в древесине, может кристаллизоваться. Однако это происходит при температуре 72 ºC (в некоторых источниках указывается другая цифра - 80 ºC). Сушка сырого пиломатериала в таких жестких температурных условиях неизбежно приведет к тому, что доски «поведет». Обычно сушка выполняется при температуре 62-65 ºC, при которой не происходит процесс кристаллизации смолы. К тому же, на большинстве современных сушильных комплексов процесс сушки автоматизирован, и за соблюдением его параметров строго следит компьютер, в «память» которого заложена программа. Чуткие датчики передают информацию о состоянии древесного сырья на управляющий компьютер, и в режимы сушки автоматически вносятся необходимые коррективы.
Для того, чтобы обеспечить кристаллизацию смолы в хвойной древесине, необходимо вручную корректировать программы сушки и изменять температурный режим на разных этапах сушки пиломатериалов. Жесткую температурную обработку лучше всего выполнять на предпоследнем этапе, когда влажность пиломатериала в сушилке приближается к 14-16% и он более-менее стабилизирован «мягким» режимом, а на последнем этапе следует снова вернуться к «мягкому» режиму. Длительность высокотемпературной обработки должна быть не менее суток. Общая же продолжительность процесса сушки пиломатериала - 10-12 дней (автор считает этот срок оптимальным для нормального сушильного процесса, когда производитель старается максимально сохранить геометрию ламелей и выровнять влажность в рамках одной партии пиломатериала). Можно, конечно, уложиться и в шесть - семь дней, но при условии обязательной предварительной атмосферной сушки пиломатериала.
После выгрузки пиломатериалов из сушилки он в течение суток должен стабилизироваться, и только после этого его можно использовать для дальнейшей обработки.
Хотелось бы обратить внимание потенциальных производителей КДК на практику аутсорсинга. То есть, на покупку сухого пиломатериала требуемой влажности и геометрических размеров. Нет, конечно, собственные сушилки также нужны, по крайней мере, в том количестве, которое обеспечит 20% необходимого для работы сухого пиломатериала (то есть, для подстраховки). Выгоды очевидны.
Дело в том, что крупные деревоперерабатывающие заводы, в составе которых имеются мощные сушильные комплексы из десятков камер, могут без труда удовлетворить высокий спрос на сухие пиломатериалы, более того - на этих предприятиях можно осуществлять в автоматическом режиме предварительную сортировку пиломатериала по влажности. Вступив в партнерские отношения с таким предприятием, вы будете получать высушенные до требуемой влажности заготовки необходимых геометрических размеров, которые останется только откалибровать, причем, с минимальным припуском. Дополнительным преимуществом после вступления в силу ГОСТа 20850-2014 станет наличие на подобных производствах предварительной сортировки пиломатериала по классам прочности. Конечно, такое сырье стоит гораздо дороже, чем пиломатериал естественной влажности. Но стоит посчитать - во сколько обойдется собственный сушильный комплекс, его обслуживание и содержание, во что обходится производственный процесс? Практика показывает, что содержание собственного полноценного сушильного комплекса и его постоянная эксплуатация - это один из самых затратных пунктов в производственной программе. Известны примеры того, как несколько довольно крупных предприятий пришли к решению покупать сухой пиломатериал, и в результате себестоимость их готовой продукции снизилась.
От автора - вместо заключения
Итак, мы завершаем цикл публикаций об основных этапах производства КДК.
В западной Европе давно уже существует специализация предприятий, работающих в сфере деревянного домостроения. Это, в частности:
• перерабатывающие комбинаты: производят доски заданных размеров и требуемой влажности; как правило, находятся в сырьевых регионах.
- производственные компании: изготавливают полуфабрикаты - клееный брус, мебельный щит, погонажные изделия. Могут быть расположены как в сырьевых регионах, так и в регионах конечных потребителей.
- домостроительные компании: пользуясь обрабатывающими центрами, изготавливают детали домокомплектов и другие готовые изделия, к примеру - окна, двери; организуются максимально близко к конечному потребителю продукции.
Иногда такие компании объединяются в холдинги. Каждое структурное подразделение холдинга отвечает за свой участок технологической цепочки и получает свою часть прибыли за счет оптимизации расходов и увеличения производительности.
В нашей стране другой подход: производственники стремятся взять на себя весь цикл - от раскроя кругляка до изготовления домокомплектов и возведения строений на земельном участке заказчика. Владелец компании пытается сконцентрировать контроль процесса изготовления изделий в своих руках, однако при этом теряется контроль эффективности производственных участков, что ведет к снижению выхода готовой продукции и росту объема отходов.
Мое мнение: нашим деревообработчикам надо привыкать к узкой специализации - это эффективный способ контролировать производство и получать максимальную прибыль.
Деревообработка вообще бизнес сложный, в нашей стране - особенно. Я глубоко уважаю людей, которые занимаются производством, и прежде всего потому, что для них это - образ жизни. Если вы не готовы в прямом смысле ЖИТЬ своим предприятием, не стоит даже пытаться входить в этот бизнес. Деревообработка не та сфера, где можно заработать на инвестициях, для этого существуют гораздо более прибыльные проекты.
Одна из самых распространенных ошибок инвесторов: дескать, «вот бревно, оно стоит 2000 руб., а вот клееный брус - уже за 25 000 руб. Нужно только станки купить, запустить - и деньги польются рекой». А это совсем не так. Инвестиции в деревообработке окупаются 10-20 лет, а не два-три года, как ошибочно полагают такие бизнесмены! Только если вы готовы прожить вместе со своими инвестициями в этом бизнесе весь этот срок, вы сможете получить удовольствие от результатов проделанной работы.
Такова уж специфика нашего бизнеса... И, если прочитав весь цикл материалов по производству КДК, вы не разочаровались в его перспективах, а только окрепли в желании производить клееные деревянные конструкции, приветствую вас в братстве деревообработчиков.
Михаил ТАРАСЕНКО,
Pro-kleim.ucoz.ru
Клееные конструкции в деревянном домостроении
Изготовление ламелей для КДК
Клеи в производстве ДКК
Производство клееных деревянных конструкций. Инженерные системы