Новые технические решения для повышения эффективности лесозаготовительного производства. Часть 4
Устройства для снижения потерь древесины при окорке
в окорочных барабанах
Часть 1. Способ определения степени затупления ножей рубительных машин для линии производства технологической щепы
Часть 2. Повышение эффективности облагораживания низкокачественной древесины для подготовки к производству технологической щепы
Часть 3. Повышение эффективности групповой механической окорки лесоматериалов в окорочных барабанах
Часть 5. Использование сканеров для повышения эффективности чистой окорки лесоматериалов
Качество получаемой в древесно-подготовительных цехах технологической щепы напрямую зависит от наличия в ней коры. Определение качества осуществляется по методике, описанной в ГОСТ 15815-83 и основанной на периодическом отборе проб щепы и проведении их анализа на лабораторном анализаторе. Отбор коры в пробе щепы выполнятся вручную, причем если кора не отделена от щепки, ее также отделяют вручную.
Метод заключается в том, что через равные промежутки времени отбирают пробы щепы после сортирования (кондиционную фракцию). Пробу щепы методом квартования доводят до навески примерно 2,5 кг. Навеску сортируют на лабораторном анализаторе щепы (АЛГ-1М) с ситами, диаметр круглых отверстий которых 30, 20, 10, 5 мм, и поддоном.
Щепу на ситах после сортирования в течение одной минуты взвешивают по фракциям и определяют процентное соотношение каждой фракции в навеске. Для объективной оценки качества щепы таких определений (проб) должно быть не менее шести в течение смены. В ГОСТ 15815-83 приведена таблица качественных показателей технологической щепы для различных марок: Ц-1, Ц-2, Ц-3. Фрагмент этой таблицы см. ниже.
технологической щепы по ГОСТ
15815-83 (фракционный состав
щепы)
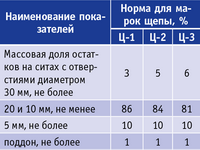
Более сложная задача - определение количества отходов древесины при рубке, дезинтегрировании и сортировании щепы, методика определения количества отходов описана в Инструкции по нормированию расхода на производство целлюлозы и древесной массы (утверждена Минлесбумпромом, НИИПиНом при Госплане СССР от 01 02.1984 г.).
По этой методике пробы щепы должны быть взяты как до сортирования, так и после него. Количество проб должно быть не менее 120 на каждой стадии. Путем сравнения фракционного состава щепы до и после сортирования определяют количество отходов древесины (отсева) при сортировании.
Такая работа может быть выполнена в течение нескольких смен (суток), так как в течение одной смены один лаборант может отобрать и проанализировать не более 30 навесок щепы. Далее по полученным результатам анализа щепы до и после сортирования определяется количество отходов по содержанию мелкой фракции щепы (отсева) по формуле:
А = Е - Е΄, (1)
где А - количество отходов сортирования щепы, %; Е - количество мелкой фракции в щепе до сортирования, %;
Е΄ - количество мелкой фракции в щепе после сортирования, %.
На основании анализа проб щепы делают вывод о ее качестве и дают команду оператору регулировать процесс окорки путем изменения подачи теплоносителя (или увлажнителя) в окорочную установку, изменения скорости вращения окорочной установки или положения шандора.
Такой подход к регулированию процесса окорки очень инертен и часто приводит к большому расходу древесины в брак (перекору), что связано с тем, что продолжительность нахождения бревен в окорочном барабане напрямую влияет на величину потерь древесины, возникающих во время выполнения этой операции.
Часто технологи для получения щепы только высшего качества ставят окорочный барабан в режим, рассчитанный на самые худшие условия окорки (малая влажность, отрицательная температура окариваемых бревен), что существенно увеличивает время нахождения бревен в барабане, уменьшает производительность барабана и снижает энергоэффективность окорки.
Если условия окорки меняются в лучшую сторону (повышается влажность и температура окариваемой древесины), то время, необходимое для окорки, существенно уменьшается. При отсутствии оперативного контроля и без уменьшения продолжительности нахождения бревен в барабане возникает перекор, от бревен в большом количестве начинает отделяться древесина и удаляться вместе с отходами окорки из окорочного барабана через специальные прорези на выносной транспортер, находящийся под окорочным барабаном. В справочной литературе указывается, что при окорке в барабанах потери древесины составляют от 1,5 до 8%, а в ряде источников встречается и 12%. Очевидно, что при весьма значительных объемах производства технологической щепы (десятки миллионов кубометров) потери из-за несоблюдения оптимальных режимов работы окорочных барабанов могут составлять 100 тыс. м3 на 1 млн м3 окоренной древесины!
Для устранения указанных недостатков сотрудниками ЛИФ СПБГЛТУ модернизирован узел групповой механической окорки лесоматериалов. В состав линии (рис. 1) входят последовательно установленные и технологически связанные узел подачи неокоренных лесоматериалов, окорочный барабан с загрузочным отверстием и выгрузочным отверстием, оборудованным приводным шандором, узел выгрузки окоренных лесоматериалов, а также узел приема и транспортировки отходов окорки. Особенность линии в том, что с целью обеспечения оперативного регулирования процесса окорки узел приема и транспортировки отходов окорки снабжается измельчителем, например, корорубкой, и дозирующим устройством, обеспечивающим выход равномерного слоя измельченных отходов на транспортер с плоской лентой, над которой расположен узел сканирования с блоками информации и программирования, причем последний связан с приводами шандора, барабана и узла подачи неокоренных лесоматериалов.
Исследования процесса окорки лесоматериалов (балансов) в барабанах непрерывного действия показали, что в зависимости от породы древесины и состояния поверхности ее коры, для обеспечения высокого качества окорки требуется пребывание древесины в барабане в течение определенного времени. Это время можно регулировать скоростью вращения барабана и величиной открытия выпускного отверстия барабана, размеры которого задает положение шандора. Кроме того, качество окорки можно регулировать за счет увеличения или уменьшения подачи теплоносителя в окорочный барабан.
В зависимости от качества окорки изменяется величина потерь древесины. Так как и кора, и отходы древесины удаляются из-под барабана одним и тем же транспортером отходов, по соотношению их объемов в отходах окорки можно определять количество отходов древесины.
Авторами отмечено, что изменение соотношения объемов коры и древесины в отходах окорки влияет на изменение цвета общей массы отходов, особенно после измельчения, например, в корорубке, когда масса приобретает однородность по фракционному составу. Это связано с тем, что при окорке в барабанах от бревен откалывается кора и куски древесины, куски небольшого диаметра также могут обламываться и попадать в отходы, изменяя цветовую гамму отходов окорки.
Измельчив все отходы окорки (кору, отщепы древесины и кусковые отходы), можно не только улучшить условия их утилизации, но и оценить цветовую гамму (рис. 2), по которой можно определить количество древесины в отходах окорки, и на этом основании принимать решение об оперативном регулировании показателей режима окорки.
На практике неоптимальный режим работы окорочного барабана может привести к недоокорке балансов. Тогда цветовая гамма измельченных отходов будет соответствовать требованию минимального содержания древесины в отходах окорки для снижения потерь древесины, а качество окорки не будет соответствовать нормативам.
Для устранения этого недостатка разработано еще одно техническое решение. Линия изготовления технологической щепы, в состав которой входят последовательно установленные и технологически связанные узел подачи неокоренных лесоматериалов, окорочный барабан с приводами системы подачи теплоносителя в окорочный барабан и шандора, рубительная машина и сортировочная установка для щепы, снабжается смонтированным после сортировочной установки автоматическим узлом непрерывной оценки качества кондиционной щепы по показателю содержания в ней коры. Этот узел выполнен в виде наклонного прозрачного склиза, над которым и под которым установлены сканерные устройства узла сканирования, содержащего блок обработки информации и программного управления процессом окорки лесоматериалов, причем последний связан с приводами системы подачи теплоносителя в окорочный барабан и шандора.
Предлагаемая линия изготовления технологической щепы работает следующим образом: неокоренные лесоматериалы, рассортированные по породам, через тарельчатый питатель и ленточный транспортер поштучно подают на гидроколун, которым раскалывают на четыре или шесть частей так, чтобы максимальная ширина сечения расколотого полена соответствовала размерам загрузочного патрона рубительной машины. Лесоматериалы без внутренней гнили, диаметр которых соответствует диаметру загрузочного патрона рубительной машины, раскалыванию не подлежат.
Лесоматериалы и колотые поленья транспортером, расположенным под гидроколуном, подают через загрузочную воронку в окорочный барабан. Окоренные лесоматериалы и колотые поленья поступают из окорочного барабана на транспортер и, пройдя через металлоискатель, направляются в рубительную машину для изготовления технологической щепы. Плохо окоренные лесоматериалы поступают в лоток и на транспортер для возврата на доокорку в окорочный барабан.
Из рубительной машины щепу через циклон подают на верхнее сито плоской сортировочной установки. Кондиционная щепа из сортировочной установки шнеком подается в наклонный прозрачный склиз автоматического узла непрерывной оценки качества кондиционной щепы по показателю содержания в ней коры и распределяется в виде щети. При этом вся щепа щети непрерывно перемещается по наклонному прозрачному склизу и просматривается сверху и снизу через этот склиз сканерными устройствами узла сканирования. Информация о количестве коры в кондиционной щепе передается в блок обработки информации и оперативного программного управления процессом окорки, откуда на основе расчета необходимых действий оперативного управления регулированием процесса окорки управляющее воздействие направляется на приводы системы подачи теплоносителя в окорочный барабан и шандора.
Отсортированная кондиционная щепа через шлюзовой питатель поступает в пневмопровод пневмотранспортной установки и доставляется на склад готовой продукции. Крупные щепки и мелочь, выделенные на сортировочной установке, а также отходы из-под окорочного барабана выносятся из цеха ленточным транспортером.
Таким образом, полезная модель позволяет повысить эффективность линии изготовления технологической щепы за счет обеспечения непрерывной автоматизированной оценки качества изготавливаемой кондиционной щепы и оперативного управления процессом окорки лесоматериалов, повышения производительности линии, снижения энергоемкости процесса и потерь древесины.
Игорь ГРИГОРЬЕВ, д-р техн. наук,
Борис ЛОКШТАНОВ, канд. техн. наук,
Ольга КУНИЦКАЯ, канд. техн. наук,
Антон ГУЛЬКО, аспирант,
кафедра технологии лесозаготовительных производств СПбГЛТУ