Лесосибирский ЛДК № 1: бренд, известный во всем мире
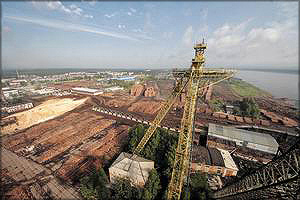
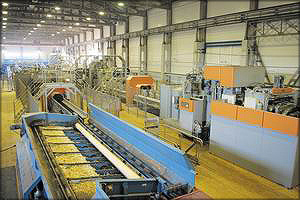
Лесопильный цех
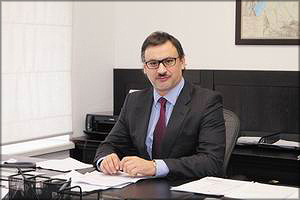
Семен Млодик: «На Ближнем Востоке сейчас
наблюдается существенный прирост населения, и закрывать потребности региона в жилье приходится в основном за счет деревянного домостроения. Наш комбинат поставляет большие партии продукции, отвечающей самым высоким стандартам качества, для удовлетворения растущих потребностей рынков этих регионов»
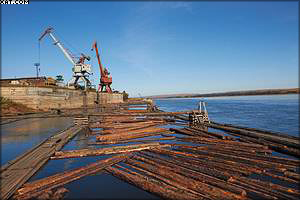
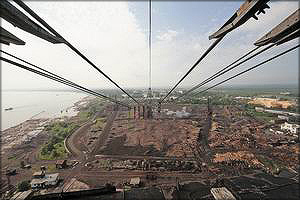
На комбинате еще 50 лет назад было установлено четыре радиальных крана, сейчас работают два. Высота каждого – 70 метров. На одном из них чуть выше кабины оператора поселилась парочка сапсанов
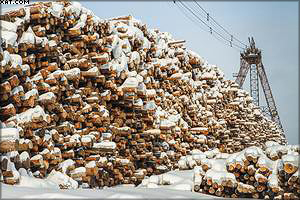
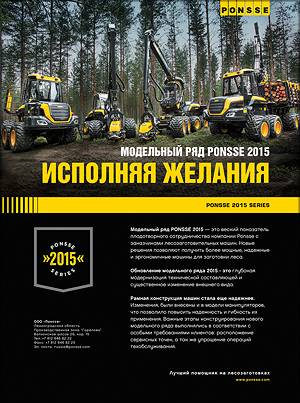
Ponsse. Лесозаготовительная техника
ОАО «Лесосибирский ЛДК № 1» - крупнейший в России комплекс по переработке древесины. В его составе несколько лесозаготовительных предприятий, новое современное лесопильное производство, цех сушки и пакетирования пиломатериалов, цех по выпуску и отделке ДВП, мебельное производство, а также комплекс котельных, которые обеспечивают потребности не только предприятия, но и части города.
Предприятие, которое до середины августа 1978 года называлось «Новомаклаковский ЛДК № 1», впервые заявило о себе на мировом рынке пиломатериалов в 1969 году. Сегодня у ОАО «Лесосибирский ЛДК № 1» в деловом мире репутация надежного партнера. И 99% выпускаемых комбинатом пиломатериалов поставляется на экспорт. Основными рынками сбыта являются: Великобритания, Бельгия, Дания, Германия, Франция, Греция, Италия, Кипр, Испания, Египет, Сирия, Ливан, Турция и ряд других стран. Работа на ЛДК построена таким образом, что при необходимости в течение двух недель логистическая цепочка может быть перестроена для отправки продукции на новые рынки в любую часть света.
Возглавляет комбинат Семен Млодик, руководитель с большим управленческим опытом. Семен Геннадьевич получил его за 12 лет работы на руководящих постах на предприятиях отечественного машиностроения, таких как Чебоксарский завод промышленных тракторов, Челябинский тракторный завод, принадлежащая РЖД машиностроительная группа «Ремпутьмаш».
Богатая история комбината отмечена множеством свершений и интересных событий. Но, по мнению генерального директора, одним из главных событий в истории ЛДК-1 можно считать присоединение к нему лесозаготовительной базы. И сегодня более 50% леса заготавливается на этой базе. Для ЛДК наличие собственной лесозаготовки - важнейший фактор стратегии развития.
То, что комбинат в своей сбытовой политике ориентируется на зарубежный, а не на внутренний рынок, зависит от нескольких факторов. Прежде всего, это географическое положение ЛДК № 1, которое позволяет комбинату эффективно работать как с европейским, так и с азиатским рынками сбыта и поставлять своим клиентам пиломатериалы высокого качества. В России почти вокруг всех крупных городов, кроме Москвы, расположены предприятия деревообрабатывающей промышленности, которые удовлетворяют свои потребности в сырье, прежде всего за счет низкосортной древесины. У леса, произрастающего в европейской части России, физико-механические свойства древесины не такие высокие, как у древесины, заготавливаемой в сибирских лесах. Качество сибирской древесины отвечает требованиям зарубежного рынка. Именно поэтому 99% продукции комбината с момента основания отправлялось на экспорт: сначала только в Великобританию, а потом и на рынки Северной Африки и Ближнего Востока.
Продукция предприятия соответствует ГОСТ 26002-83 («Пиломатериалы хвойных пород северной сортировки, поставляемые на экспорт. Технические условия») и ГОСТ 8486-86 («Пиломатериалы хвойных пород. Технические условия»).
С 1995 года комбинат ведет собственную лесозаготовку в лесозаготовительных филиалах ЛЛДК № 1, расположенных на берегах Ангары и Енисея. Общая площадь арендуемых лесных территорий - 894 922 га. Лесозаготовка осуществляется с использованием современных лесозаготовительных комплексов John Deere, Ponsse. Предприятие давно и успешно сотрудничает с ведущими мировыми производителями лесной техники. В 2007-2008 годах John Deere поставил на ЛДК-1 четыре ВПМ 853J, четыре процессора 2054, пять скиддеров и два форвардера 1010D, в 2013 году - две ВПМ 903К, а в 2014-м - ВПМ 953 К, самую крупную из ВПМ, которые выпускает John Deere. На комбинате отмечают, что вся техника John Deere отличается высокой надежностью, долговечностью и удобством обслуживания, а конструкция предусматривает легкий доступ ко всем основным компонентам машин. Отлично зарекомендовали себя и лесные машины Ponsse (лесозаготовители комбината эксплуатируют одну машину Buffalo и две - Buffalo King).
Ежегодно собственные лесозаготовительные филиалы и поставщики комбината поставляют на переработку около 1 млн м3 древесины. Как отметил Семен Млодик, в ближайших планах ЛЛДК увеличить собственную лесозаготовку в полтора раза.
После заготовки в леспромхозах бревна свозят к Ангаре и Енисею, где из них формируются плоты, состоящие из шести-семи секций. Объем одного такого плота - от 7 до 11 тыс. м3. Далее буксиром плоты тянут по воде до места выгрузки на территории предприятия. Буксировкой занимаются Енисейская сплавная контора и собственный флот комбината. У территории комбината плоты встречают суда и катера, которыми плоты прижимают к берегу, расформировывают, распускают и подают в гавань. Собственных судов у предприятия восемь, два из них занимаются сбором обвязки и крепежа плотов, остальные встречают и распускают плоты и обеспечивают охрану плотов, которые стоят на рейде в ожидании выгрузки. Протяженность этой гавани около 800 м. Гавань поделена на четыре дворика, два из которых ведут на линии сортировки бревен № 1 и № 2.
Об организации процессов на складе сырья, где занимаются приемкой и выгрузкой круглых лесоматериалов из воды, рассказал контрольный мастер Сергей Трухин. Лес подается в наплавные сооружения и по дворикам поступает к кранам. Краны КПП-16-30 выгружают бревна на линии сортировки № 1 и № 2 и на челночную линию, тележками которой бревна подаются к радиальному крану РКК-1, которым укладываются в штабеля. В самом ближнем к берегу дворике лес выгружается из воды лесопогрузчиком Terex Fuchs MHL350 в лесовозы (при этом каждое бревно учитывается и маркируется) и подается под портальные краны, где укладывается в штабеля для запаса на зиму. На протяжении судоходного периода плоты подходят почти ежедневно, и на складе пиловочного сырья комбината формируется значительный запас бревен, который требуется для того, чтобы обеспечить полную загрузку перерабатывающих мощностей предприятия на период до следующего сезона сплава. Для укладки в штабеля также используются два радиальных крана грузоподъемностью 20 т, технические возможности которых позволяют обрабатывать и укладывать бревна в штабеля в радиусе не менее 300 м.
Общая мощность комбината по сырью –
1,5 млн м3.
70% общего объема сырья составляет ангарская сосна,
18% – лиственница, 12% – ель и пихта.
Лесопиление
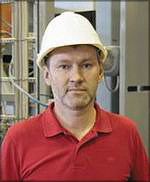
Модернизация производственных мощностей - важнейший этап на пути устойчивого развития предприятия - призвана обеспечить наиболее эффективное использование сырья, увеличить полезный выход продукции, а также вывести комбинат на новые рынки сбыта. Ввод в эксплуатацию нового лесопильного оборудования позволит вовлечь в переработку дополнительно 500 тыс. м3 сырья.
О действующем комплексе рассказал и. о. начальника лесопильного комплекса Александр Пантюхов. В цехе установлены две лесопильные линии: HewSaw SL250 3.3 с оптимизацией раскроя, на которой распиливают бревна диаметром от 10 до 42 см в вершине и до 55 см в комле, а также линия HewSaw R200 A.1, на которой можно пилить бревна диаметром от 10 до 22 см в вершине.
Линия сортировки бревен Hekotek с 32 карманами установлена в 2011 году. Подача осуществляется фронтальным погрузчиком Volvo L 180G. Сканер фирмы Hekotek измеряет диаметр вершины и комля, а также длину бревна. На линии установлены рабочий стол с поштучной выдачей бревен (производитель Hekotek), металлоискатель (производитель Metaldet), сканер для измерения геометрических параметров бревен «Вектор-3D» (производитель «Автоматика-Вектор», Архангельск), сортировочный конвейер с карманами (производитель Hekotek). Скорость конвейера - до 150 м/мин.
Именно на этом этапе решается задача оптимизации раскроя. Если диаметр бревна превышает заданные параметры, оно автоматически отправляется в карман брака. Если диаметр бревна соответствует параметрам, то оно поступает в окорочный цех. Перед раскроем на HewSaw R200 A.1 выполняется окорка бревен на станке Valon Kone 5000HD-Combi-2R, оснащенном двумя окорочными роторами с пневматическим прижимом ножей, выполняется окорка бревен с максимальным диаметром 44 см в комле. Бревна с максимальным диаметром 56 см в комле для распиловки на HewSaw SL-250 3.3 окариваются на станке Valon Kone 8000HD-Combi-2R, оснащенном двумя окорочными роторами с пневматическим прижимом ножей.
После окорки бревно сканируется и подается на измерительный конвейер ЕК1 универсальной лесопильной линии HewSaw SL250 3.3. и проходит через 3D-сканер Prologic. На этом этапе определяются основные параметры бревна, ориентации положения и выбор постава и режима криволинейного пиления. Роторное устройство LogIn-2R ориентирует бревно в оптимальное положение и подает во фрезерно-брусующий станок. Полученный четырехсторонний брус сканируется сканером True Shape, в котором рассчитывается оптимизация постава для получения максимального полезного выхода. Затем брус еще раз измеряется и поступает в блок пиления, где от него отделяются либо две, либо четыре боковые доски (в зависимости от диаметра), после чего брус разворачивается и отправляется в блок делительного пиления, где раскраивается на центральные доски. Благодаря тому, что линия оснащена автоматизированной системой Prologic и подвижными пилами, смена постава занимает несколько секунд. Разделение боковых досок происходит на трехэтажном разделительном транспортере ЕК3. В процессе пиления получаются пиломатериалы высокого качества с точными размерами, а также высококачественная технологическая щепа.
Каждая лесопильная линия оснащена собственной системой конвейеров для отходов. Ввиду особенностей конструкции линий все отходы (опилки, щепа) с линии попадают на один конвейер и только затем сепарируются на виброситах Bruks.
Уникальная лесопильная линия HewSaw SL250 3.3 с оптимизацией представляет собой сложный программно-аппаратный комплекс, перед которым стоит задача обеспечения скоростного и точного пиления с высоким коэффициентом полезного выхода пиломатериалов. До ЛЛДК № 1 компания Veisto установила в мире всего пять таких комплексов, и в силу сложности и инновационности процесс пусконаладки линии занял немало времени. Выход продукции на линии HewSaw SL250 3.3 с оптимизацией раскроя на 10% выше, чем на HewSaw R200 A.1.
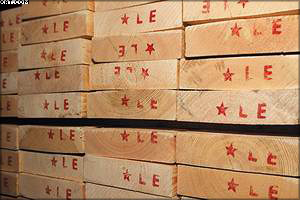
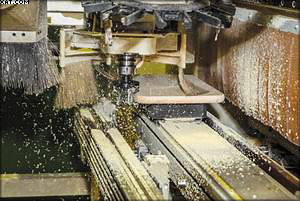
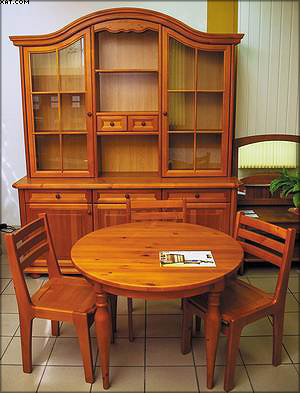
Линия HewSaw A.1.2 - это надежное и компактное решение на базе одного станка, который оснащен 3D-сканером Prologic и осуществляет точную ориентацию бревна перед подачей по осевой линии с помощью LogIN-2R. Функция криволинейного пиления позволяет обеспечить максимальный полезный выход пиломатериалов. Кроме того, на линии установлен многопильный станок NS200, в котором выполняется раскрой бруса с повышенным выходом пиломатериала.
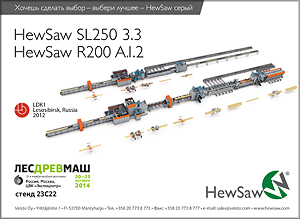
HewSaw. Оборудование для лесопиления
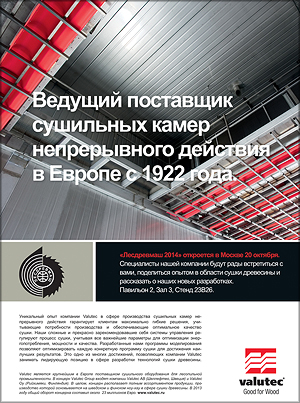
Valutec. Сушильные камеры для древесины
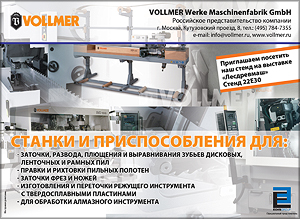
Vollmer. Заточное оборудование
Процессы пиления на линиях HewSaw R200 A.1 и HewSaw SL250 3.3 схожи. После окорки сырье поступает на накопительный стол, проходит через измеритель и подается на распил, после чего сортируется по сечению. Различия между этими линиями следующие: на линии HewSaw R200 A.1 бревна раскраивают пилами с жестким поставом, а на линии HewSaw SL250 3.3 - с оптимизацией боковой доски, и в зависимости от диаметра выпиливается либо две, либо четыре боковые доски.
Максимальная производительность пиления, достигнутая на линии HewSaw R200 A.1, - 1003 м3 в смену при раскрое сосновых бревен диаметром 20 см. На линии HewSaw SL250 3.3 пока достигнута производительность 1226 м3 в смену. Пилы меняются в пересменку или в обеденный перерыв, когда заточники и помощник оператора проверяют состояние режущего инструмента.
В заточном цехе стоит оборудование с ЧПУ фирмы Vollmer. Заточники были обучены в Германии. Операторы лесопильного цеха проходили обучение в Финляндии. Электронику техники обслуживает инженер IT и электронщики, которые помогают в настройке программного обеспечения линии сортировки и линии пиления. В лесопильном цехе в смену трудится 28 человек. Сейчас цех работает в трехсменном режиме. Лесопильным оборудованием в смену управляют десять человек: оператор и его помощники, на сортировке шесть операторов и шесть укладчиц рейки, а также контролер, который наклеивает паспорта на выпускаемые пакеты. Цех оборудован системами дымоудаления, притока воздуха и вытяжкой. Летом 2014 года введен в эксплуатацию участок антисептирования пиломатериалов.
Доски поступают на линии сортировки сырых пиломатериалов Heinola - для боковых и центральных досок, поступающих с обеих линий пиления. Датчики определяют их сечение, и далее доски рассортировываются по карманам: 30 карманов для центральных досок и 35 карманов - для боковых. Из сортировочного кармана партия пиломатериалов подается транспортером прямо на штабелеформирующую установку. Скорость укладки слоев достигает 160 реек в минуту.
Комбинат производит только сухие экспортные пиломатериалы. Сушильный комплекс комбината состоит из 31 сушильной камеры. Тринадцать из них - это туннели Valmet, отработавшие на ЛДК не один десяток лет и успешно модернизированные компанией Valutec. Объем разовой загрузки каждой такой камеры 280 м3. В рамках модернизации старый туннель был поделен на две сушильные зоны, в каждую из которых установлен дополнительный комплект калориферов и вентиляторов. Кроме того, смонтирована транспортная система для автоматического перемещения штабелей. Таким образом, общая производительность туннельных сушилок Valmet сейчас достигает 300 тыс. м3 неторцованных пиломатериалов в год. В результате модернизации камер для тонких досок произошло значительное увеличение выхода продукции. Срок сушки, например, для сосновых досок сократился с четырех до двух с половиной суток. Остальные 18 камер произведены фирмой Nardi, объем разовой загрузки каждой камеры - 200 м3.
В рамках модернизации Лесосибирского ЛДК № 1 на линию сортировки сухих пиломатериалов Almab, где сортируется более 60% всех пиломатериалов, выпускаемых комбинатом, в 2011 году была поставлена система автоматического определения качества доски BoardMaster FS4-140 от компании FinScan. Эта система сканирует каждую доску с четырех сторон и, быстро и эффективно обрабатывая полученные изображения, проводит анализ качества доски. Также по просьбе комбината в программное обеспечение системы BoardMaster было добавлено определение таких пороков пиломатериала, как кофейная темнина, светлая и темная синева. В 2012 году на линии было установлено программное обеспечение B-Sort (разработка компании «Автоматика-Вектор»).
Линия Almab оборудована 54 сортировочными карманами, при наполнении которых происходит пакетирование в плотные пакеты, упаковка и увязка. Далее готовые пакеты поступают на склад готовой продукции. Пакетирование пиломатериалов также осуществляется на двух финских линиях Plan-cell, имеющих по 36 сортировочных кармана каждая.
Что же дал новый лесоцех предприятию? По мнению Семена Млодика, его строительство - это насущная необходимость. Продолжать активную эксплуатацию имеющегося на комбинате старого лесопильного цеха нельзя. В стране закрылся последний завод, производивший пильные рамы. То есть те, кто сейчас еще работает на этих рамах, не смогут обслуживать эти комплексы через пару лет ввиду отсутствия комплектующих. С точки зрения качества отечественные пильные рамы отличаются от современных импортных фрезерно-брусующих линий по классу шероховатости. Пиломатериалы, полученные на фрезерно-брусующей линии, можно использовать без строгания. И лет через пять эти требования по шероховатости будут стандартом. Еще один плюс новой техники - автоматизация процессов и уменьшение объемов ручного труда.
Плитное производство
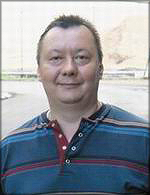
Отходы лесопильного производства (щепа) перерабатываются в цехе производства древесно-волокнистых плит. Об особенностях технологического процесса выпуска ДВП рассказал старший механик Сергей Бодров.
ЛДК № 1 производит экологичные плиты без использования химических связующих, по технологии влажного прессования.
Все начинается с участка подачи щепы. Щепа поступает сюда из нового лесопильного цеха и складируется гуртом. С помощью транспортера она подается в цех, где стоят восемь бункеров емкостью 500 м3 каждый. Цех по производству плит работает без выходных, в три смены, по скользящему графику. Останавливают цех ДВП только на новогодние каникулы и во время капитального ремонта (десять дней в году). Проектировался цех в 1973 году, тогда же был оснащен оборудованием польского производства, работает оно до сих пор, замены коснулись отдельных узлов. В цехе работает система очистки оборотной воды. В год комбинат выпускает 25 млн м2 плит.
Плиты раскраиваются на двух форматно-обрезных станках: на одном в соответствии с стандартами ГОСТа, а на втором - в соответствии с индивидуальными потребностями заказчика. Когда на плитном рынке предложение превышает спрос, цех за счет выпуска нестандартной продукции под индивидуальные потребности не останавливает производство. Склад рассчитан на 3-4-дневный запас продукции. Плиты в основном поставляются в Казахстан и Узбекистан, некоторое количество поставляется в Новосибирск, Омск.
Капитальный ремонт и инспекцию прессов осуществляет компания «Союзлесмонтаж» из Вологды.
Производство мебели
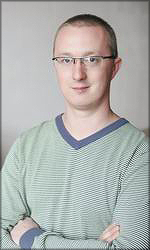
На ЛДК работает также мебельный цех. Об этом рассказал конструктор цеха мебельного производства Александр Крюков. Мебельное производство работает с марта 1993 года. В основном здесь изготавливают кухонные гарнитуры, спальни, шкафы, комоды, зеркала, столы, стулья. Для деревянного домостроения производятся двери, строганный погонаж, террасная доска, блок-хаус, вагонка, доска пола. Разработка проекта фабрики, подбор и монтаж оборудования, создание первых моделей мебели осуществлялись совместно с известным итальянским производителем мебели в Европе Чезаре Лачеделли. Изначально в этом цехе планировалось производство мебели из ангарской сосны. Первые годы после пуска цеха здесь изготавливались итальянские модели мебели, дизайн которых был передан на ЛДК итальянской стороной в приложение к контракту на строительство завода, что позволило пустить цех сразу и изготавливать качественную мебель. В цехе было установлено оборудование в основном производства компании SCM Group: многопильный станок M-3, сверлильный станок TOP35, фрезерные станки T-130 и Т-130N, рейсмусовый станок S520, форматная пила SI16WAW. Сейчас в цехе стоят два обрабатывающих центра с ЧПУ: SCM NUM750 и Morbidelli Author 430. На этом оборудовании можно обрабатывать плоские заготовки. В перспективе планируется приобрести современный пятиосевой обрабатывающий центр.
Как отметил Александр Крюков, на рынке мебели довольно высокая конкуренция, поэтому для гарантированного сбыта продукции планируется перейти на производство мебели под заказ и по предоплате и не держать запасы на складе. Уже сейчас мебель выпускается мелкими сериями - по 10-15 шт. одной позиции.
Покупатели продукции комбината уверены не только в качестве, но и в гарантированной доставке заказов - с 2008 года комбинат отгружает продукцию контейнерными поездами, а с октября 2013 года запустил новую технологию отправки отправительскими маршрутами. В каждой партии, отправляемой строго в соответствии с расписанием, 71 груженый полувагон. Такая партия следует одним маршрутом без переформирования на промежуточных станциях. Введению новшества предшествовала длительная совместная работа отдела комбината и ОАО «РЖД».
Руководство Лесосибирского ЛДК № 1 разработало планы развития на среднесрочную и долгосрочную перспективу, которые были обнародованы на праздновании 45-летия комбината. Была предоставлена кредитная линия на семь лет от Сбербанка. Цель - получить максимум добавленной стоимости при минимуме издержек и потерь качества. Намерены здесь освоить и так называемую потоковую модель производства. Также в планах модернизация котельных, которые полностью обслуживают производство, а также снабжают тепловой энергией город. В настоящее время 40% топлива, на котором работают котельные, это уголь. В ближайшей перспективе планируется снизить долю угля до 10%. В плане развития на 2014 год строительство пеллетного производства. В рамках программы модернизации технологии пиления на ЛЛДК № 1 увеличивается объем производства, что влечет за собой и увеличение объемов отходов лесопиления, в частности опилок, которые требуют утилизации. Руководством комбината была выбрана технология производства пеллет, это позволит получать дополнительную прибыль от реализации нового продукта. В настоящее время завершается процедура выбора поставщика и ведется доработка проектной части будущего пеллетного производства. Также руководство предприятия думает о возможности производства CLT-панелей.
Как отметил Семен Млодик, для производства продукции Лесосибирский ЛДК № 1 использует прекрасное сырье - ангарскую сосну с высокими физико-механическими свойствами, и было бы неразумно портить его химическими добавками. Предприятие планирует расширять спектр производимой продукции, заниматься всеми видами переработки древесины, которые не приводят к химической модификации исходных материалов, и сохранить тем самым статус производителя экологичной продукции.
Подготовил Михаил ДМИТРИЕВ
Фотографии: Лесосибирский ЛДК № 1 и Андрей Забелин
История Лесосибирского ЛДК № 1
30 декабря 1968 года - на предприятии распилено первое бревно.
1969 год - выполнены первые поставки пиломатериалов на зарубежный рынок.
1973 год - состоялся пуск завода древесно-волокнистых плит, что позволило перейти к комплексному использованию отходов лесопиления. Завод ДВП нуждался в больших объемах тепловой энергии, и в том же году была пущена тепловая станция.
1975 год - поселки, в которых жили работники лесопромышленного комплекса, объединились в г. Лесосибирск.
1976 год - иностранным покупателям был отгружен миллионный кубометр пиломатериалов.
14 августа 1978 года - Новомаклаковский ЛДК № 1 стал называться Лесосибирским ЛДК № 1, комбинат получил официальный статус градообразующего предприятия.
1993 год - пущено мебельное производство, на котором изготавливают большой ассортимент экологически чистой мебели из массива ангарской сосны.
1995 год - Лесосибирский ЛДК № 1 начал заготавливать пиловочник собственными силами.
1997 год - комбинат награжден дипломами Министерства экономики РФ и Союза лесопромышленников и лесоэкспортеров России.
2005 год - ЛЛДК № 1 получил сертификат Лесного попечительского совета (FSC).
2006 год - годовой объем производства пиломатериалов превысил 500 тыс. м3.
2007 год - началась активная модернизация технологий, монтаж нового сушильного комплекса Nardi и штабелеформирующей установки Almab.
2011 год - реализован первый этап модернизации, введена в эксплуатацию новая линия сортировки, обработки и упаковки пиломатериала Almab, линия сортировки пиловочного сырья Hekotek.
2012 год - началось строительство лесопильного комплекса с участием ведущих мировых поставщиков оборудования: Veisto, Hekotek, Heinola.
2013 год - пущен новый лесопильный комплекс проектной мощностью 1,5 млн м3 по сырью.
2014 год - ЛЛДК № 1 стал лауреатом премии «Гуд Вуд» (лесного попечительского совета FSC России) и получил диплом победителя в номинации «Экологически ответственный производитель».
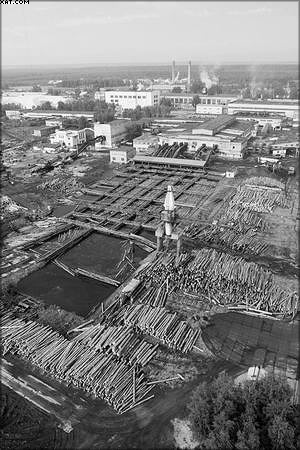
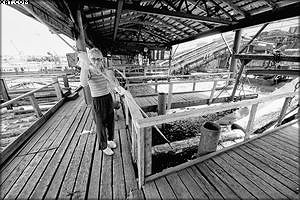
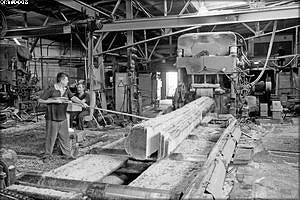
В советское время на комбинате применялась ручная сортировка пиломатериалов – почти весь год доски пилились и навалом под открытым небом складировались до лета, когда на предприятие привозили учителей, милиционеров и прочих бюджетников не только из Лесосибирска, но и Красноярска. Их руками и осуществлялась сортировка досок. Сейчас в старом лесопильном цехе на рамах распиливаются только слишком толстые или кривые бревна, его загрузка минимальна.