Оборудование современных предприятий по производству клееных деревянных конструкций. Часть 3
В предыдущих публикациях были рассмотрены виды деревянных клееных конструкций (ДКК), технологии сушки и предварительной сортировки пиломатериалов, раскроя заготовок и сращивания их в ламели при изготовлении ДКК.
Рассмотрим дальнейшие этапы производства ДКК, технологии и оборудование, используемое для этих операций.
Строжка слоев многослойных элементов деревянных конструкций
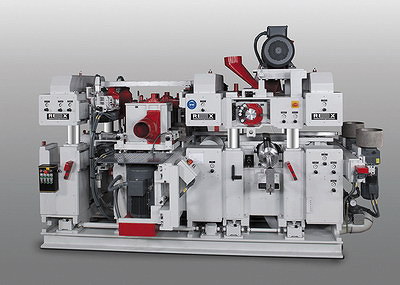
а)
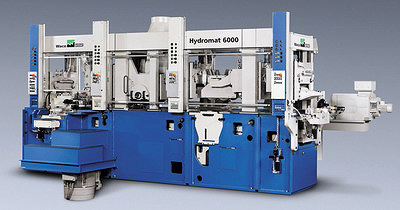
б)
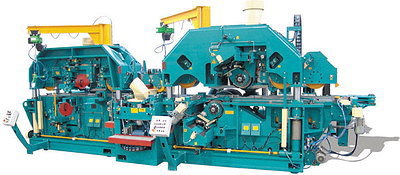
в)
Рис. 1. Строгальные станки тяжелого класса для обработки слоев и KVH: а – REX Bigmaster, б – Weinig Hydromat 6000, в – Ledinek Stratoplan
Для заготовок конструкционных брусьев KVH строжка после сращивания является одной из последних операций в технологической цепочке, дальше следует только операция упаковки. Строжка слоев двух-, трех и многослойных элементов предшествует их склеиванию в брусья. На крупных специализированных предприятиях на этой операции задействован строгальный станок, на котором можно обрабатывать заготовки довольно большого сечения - до 160 х 300 мм и в то же время работать на скорости подачи 60-80 и даже 100-120 м/мин. На крупных производствах слоистых элементов на этой операции задействуют станки, рассчитанные на меньшее сечение заготовок (обычно не более 80 х 300 мм), но работающие на скорости подачи 350-450 м/мин.
Для получения качественной строганой поверхности станки, работающие на такой скорости, обязательно оснащаются устройствами прифуговки ножей на валу - джойнтерами. Довольно распространена ситуация, когда на одном производстве (обычно среднего масштаба) выпускаются как KVH, так и слоистые элементы. В этом случае строгальный станок должен быть и высокоскоростным, чтобы эффективно строгать слои, и усиленным, чтобы качественно обрабатывать брусья; к тому же подобное оборудование должно быстро перенастраиваться. Достижение этих целей обеспечивает современная система ЧПУ и специальное устройство для снятия четвертой фаски.
Если для высокоскоростной строжки слоев оптимальным решением являются строгальные станки стредне-тяжелого класса, например станки серий Powermat 2500 или Hydromat 3500 и 5000 фирмы Weinig, то для строгания больших объемов брусьев KVH такое оборудование не подходит. Для решения этой задачи используются станки тяжелого класса с мощной станиной с вертикальными опорами. Подобные станки выпускают компании G. Schwarzbeck (под маркой Rex), Ledinek, Kälin, а с недавних пор и Weinig. В индустрии клееных конструкций станки тяжелого класса традиционно используются на всех строгальных операциях, в том числе и при строжке слоев.
Примерами станков, которые могут вести обработку самых больших заготовок KVH на большой скорости, являются станки серий Rex Bigmaster и Supermaster, Hydromat 6000, Kälin Industry, Ledinek Europlan и Superles 300/400. Станки Ledinek Superplan и Stratoplan могут применяться для высокоскоростной строжки в случаях, когда толщина заготовок не превышает 125 мм.
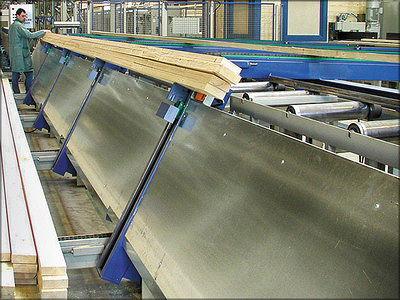
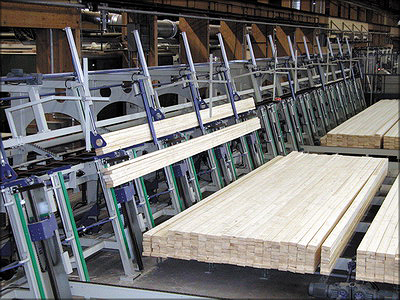
Рис. 2. Разборщики пачек фирмы Minda: полуавтоматический (сверху) и автоматический (снизу)
На небольших предприятиях, объемом производства 5-10 тыс. м3 в год, при односменном режиме строгальный станок зачастую используется еще и для финишной обработки двух-, трех- и многослойных элементов для домостроения, причем не только для строжки, но и для профилирования. В этом случае требуется станок еще более тяжелого класса, обрабатывающий заготовки сечением до 310 х 450 (630) мм, тогда как скорость обработки может быть снижена по сравнению с оборудованием, используемым на крупных предприятиях. Подобное решение требует определенной системы механизации, обеспечивающей доставку клееных элементов после их склеивания и выдержки к строгальному станку и подачу в обработку попеременно со слоями и балками KVH. Плюсами этого варианта являются снижение стоимости производственной линии, как правило, компактное размещение ее элементов, а также возможность выстраивать нестандартные технологические цепочки: например, клееные брусья могут склеиваться по толщине для наращивания высоты сечения элемента (что весьма актуально для производства стеновых брусьев).
Заготовки могут поступать на строгальную линию поштучно с конвейера-этажерки (это современное и поддающееся автоматизации решение), а также в пачках и пакетах. Для разборки пачек применяются полуавтоматические наклонно-опрокидывающие механизмы, в которых слой заготовок соскальзывает на рольганг строгальной линии, или автоматические системы, в которых нижняя доска вытаскивается из пачки в поперечном направлении. Для разборки пакетов используются механизмы, в которых верхний слой заготовок автоматически сталкивается в поперечном направлении захватами или упорами.
Простроганные слои поступают на буферный поперечный конвейер. Наличие перед клеенаносителем такого конвейера, который может вмещать запас слоев заготовок на одну загрузку пресса, гарантирует, что при незапланированной остановке строгального станка в запасе всегда будет необходимое число простроганных слоев для завершения формирования пакета для склеивания. Это особенно актуально, когда применяются клеи с малым временем отверждения и малым временем закрытой выдержки.
Как известно, между строганием и склеиванием слоев перерыв должен быть не больше 12 часов (в случае со склеиванием лиственницы еще меньше), иначе склеиваемые поверхности «стареют» и покрываются пылью, что ухудшает адгезию.
Склеивание прямолинейных элементов деревянных конструкций
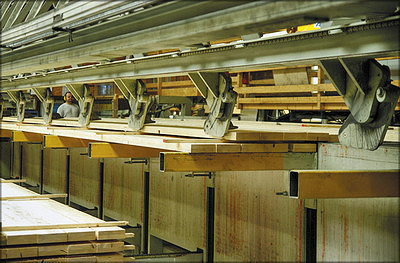
Рис. 3. Разборщик пакетов фирмы HIT
К прямолинейным относят элементы как постоянного, так и переменного сечения, такие как балки, ригели и стойки рам. Традиционно для склеивания подобных элементов используются гидравлические прессы с боковой загрузкой. Прессование осуществляется вертикальными гидроцилиндрами с большим ходом поршня. Такие установки для производства элементов ДКК легко определить по длинным штокам, возвышающимся над прессом. Большой ход поршня позволяет прессовать как большие, так и маленькие пакеты. А при наличии независимого хода каждого цилиндра можно склеивать элементы переменного сечения.
Высота прессуемого пакета обычно в пределах 1800 мм (в последние годы она все чаще ограничивается 1400 мм в целях повышения гибкости процесса), ширина - 280-310 мм, что позволяет прессовать два узких пакета в ряд; встречаются и экземпляры с шириной пакета до 400 мм.
Прессы оснащают механизмами для автоматического набора пакета. При оснащении системой сброса заготовки в заданной точке возможен полностью автоматический набор пакета для склеивания элементов переменного сечения.
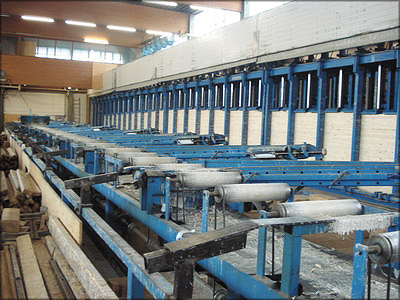
Рис. 4. Склеивание балки с переменной высотой сечения на заводе Stephan Holzbau
Для удаления пакета из пресса чаще всего применяют приводные ролики, смонтированные на откидной раме или установленные под ней, - при опускании рамы в крайнюю нижнюю точку пакет оказывается на роликах, по которым перемещается в продольном направлении. Другим возможным решением этой операции является установка внизу, под откидной рамой и рольгангом, поперечного цепного конвейера, с помощью которого пакет удаляется с участка.
Самое простое решение, которое обычно применяют при склеивании элементов большепролетных конструкций длиной 18-30 м, - удаление готового элемента краном-балкой.
Использование современных клеевых систем при работе на паре прессов длиной 12 м, установленных по обеим сторонам от рольганга и оснащенных автоматами формирования пакетов, позволяют достичь производительности до 20 тыс. м3 продукции в год.
Однако совсем недавно, каких-нибудь 20 лет назад, на рынке были только фенолрезорциновые (ФРФ) и мочевиномеламиновые (ММФ) клеевые системы, при использовании которых цикл склеивания длился 8-12 часов, что позволяло на прессах с боковой загрузкой достигать объемов производства всего несколько тысяч кубометров в год.
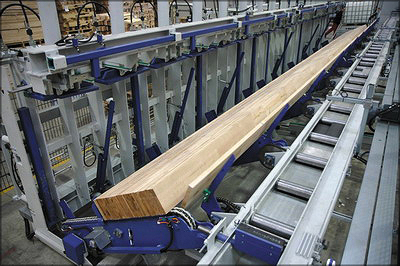
Рис. 5. Пресс Minda с системой автоматического набора пакетов
Поэтому в конструкциях разработанных несколько десятилетий назад линий повышенной мощности появились отдельный механизм для набора пакетов (так называемый «патерностер»), батарея гидравлических прессов, загружаемых с торца, и поперечная тележка для доставки пакетов и погрузки их в прессы. Эта же тележка использовалась и для приемки склеенных изделий. Следующим шагом стало создание кожуха вокруг прессов и поддержание внутри этой герметичной камеры повышенной температуры (до 100 °С) и определенной влажности воздуха, чтобы избежать пересушивания торцов заготовок. В результате продолжительность цикла удалось сократить до 3-5 ч, что позволило достичь производительности 30-40 тыс. м3 продукции в год.
Другим методом интенсификации производственного процесса стало склеивание в поле токов высокой частоты (т. в. ч.), в результате чего клей отвердевает за несколько минут. Особенно широко прессы т. в. ч. применялись в США и Скандинавских странах, но в последнее время они стали популярны и в Центральной Европе. Например, новое производство в австрийском г. Имст, принадлежащее компании Pfeifer, оснащено двумя прессами т. в. ч. фирмы Kallesøe, благодаря чему проектная мощность завода составляет 200 тыс. м3 клееных элементов в год. Такой же показатель - 200 тыс. м3 - уже достигнут на заводе Nordlam в немецком Магдебурге, где установлены два вертикальных пресса т. в. ч. шведской фирмы Ersson Engineering. В России пресс т. в. ч. Kallesøe эксплуатируется на Сокольском ДОКе, проектная мощность производственной линии - более 100 тыс. м3 в год.
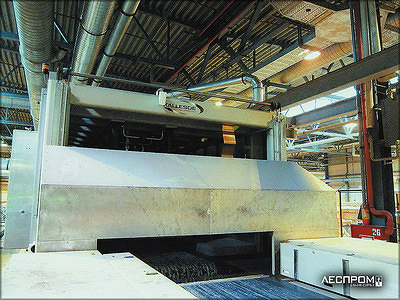
Рис. 6. Пресс т.в.ч. Kallesøe на Сокольском ДОКе. Пакет в прессе склеивается в горизонтальном положении
Среди европейских изготовителей прессов т. в. ч. можно также отметить австрийские компании Technik Management и Höfer Presstechnik. В CША подобное оборудование изготавливает компания USNR, являющаяся правопреемником всех крупных американских разработчиков подобных прессов за последние полвека, а также компания K. Ogden.
Прессы т. в. ч. выпускаются тактовые и непрерывного действия, горизонтальные и вертикальные. Обычно пакет склеивается не целиком, а участками, при постепенном продвижении между электродами.
Однако с разработкой новых клеевых систем появилась возможность достичь высокой производительности без какого-либо нагрева. Так, внедрение технологии раздельного нанесения клея и отвердителя привело к распространению меламиновых клеев (МФ), при использовании которых время склеивания составляло три часа или даже меньше. Затем появились полимер-изоцианатные клеи (ЭПИ), которые в настоящее время широко применяются для изготовления брусьев для японского рынка и стеновых брусьев. В то же время получили распространение однокомпонентные полиизоцианатные клеи (1К-ПУР), отверждаемые влагой воздуха. ПУР клей подается из герметичного контейнера и после нанесения при контакте с воздухом вспенивается и становится вязким, приобретает отличные тиксотропные свойства, то есть способность удерживаться на вертикальных и наклонных поверхностях, что позволяет сократить расход клея и таким образом отчасти компенсировать высокую стоимость однокомпонентных полиизоцианатных систем. Но самое главное: период прессования может быть сколь угодно коротким, его ограничивает лишь сборочное время (об этой проблеме ниже). Другой важной особенностью ПУР клеев является прекрасная адгезия к любым материалам, что, с одной стороны, позволяет страховаться от непроклеев в местах расположения сучков и на плохо простроганных поверхностях, а с другой - создает проблемы при эксплуатации оборудования, которое загрязняется каплями клея.
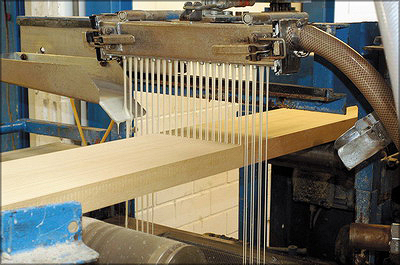
а)
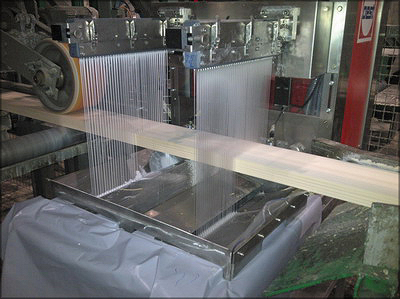
б)
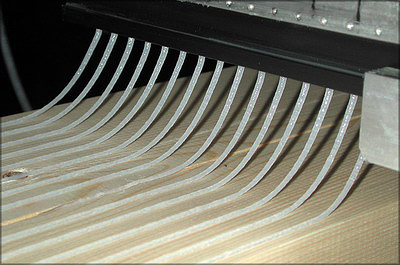
в)
Рис. 7. Нанесение клея: а – нанесение клеевой смеси, б – раздельное нанесение клея и отвердителя, в – нанесение однокомпонентного полиизоцианатного клея
Ведущим изготовителем клеенаносящих машин всех типов является германская компания Oest. Машины для нанесения смесей и раздельного нанесения компонентов оснащаются системами рециркуляции, то есть не попавший на древесину клеевой материал возвращается в наносящую головку. Автоматика машины считает заготовки и выдает команду, на какие слои наносить клей, а на какие не надо. В состав комплекса для нанесения смеси входит также агрегат дозирования и смешивания компонентов клеевой смеси.
Появление клеев с коротким временем прессования позволило отказаться от прессов-камер. Так, на германском предприятии Hüttemann Wismar имеются патерностер, батарея из восьми прессов, тележка для загрузки и выгрузки пакетов. Применяется клеевая система на основе МФ-смолы. Помимо прессов с торцовой загрузкой, на предприятии есть длинный пресс с боковой загрузкой. По данным компании, производственная мощность предприятия составляет 150 тыс. м3/год клееной продукции.
Однако полностью реализовать потенциал современных клеевых систем мешало ограничение скорости набора пакета и подачи в пресс. Дело в том, что чем быстрее клей твердеет, тем меньше времени отводится на то, чтобы загрузить слои в пресс. Так называемое сборочное время обычно составляет примерно 40% от времени прессования. Это означает, что для сокращения времени прессования до 30 мин. должна быть возможность менее чем за 12 мин. набрать пакет, загрузить в пресс, приложить давление сбоку (выровнять пакет) и сверху.
Одним из решений этой проблемы стали передвижные прессовые установки, которые сегодня предлагают компании Minda, HIT (прессы lignoPRESS) и Springer (прессы Newton). В этих установках нет промежуточного звена - тележки, развозящей пакеты по прессам и принимающей их после склеивания. Батарея прессов (обычно она состоит из двух одинарных или сдвоенных прессов) представляет собой единый комплекс, установленный на платформе, передвигающейся по рельсам. Пресс, подлежащий разгрузке и загрузке, устанавливается торцом напротив пакетоукладчика. Противоположный торец пресса при этом оказывается напротив механизма приемки склеенного пакета. Разгрузка пресса и его загрузка следующим пакетом осуществляются одновременно. В результате стало возможным применение клеевых систем со сборочным временем 10-20 мин.
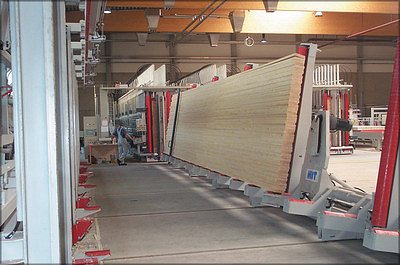
Подобное оборудование, например, установлено в построенном в 2012 году втором цехе завода Nordlam, с пуском которого производственная мощность предприятия выросла с 200 тыс. до 260 тыс. м3 клееной продукции в год. Установка lignoPRESS состоит из двух прессов длиной 16 м, высота пакета - 1300 мм. Слои к пакетоукладчику подаются двухъярусной системой конвейеров, что позволяет при необходимости набирать сечение элемента из заготовок двух конструкционных сортов. Разделение заготовок на сорта происходит после поперечного раскроя, в дальнейшем они обрабатываются раздельно, хранятся на разных этажах накопителя, подаются одним из двух конвейеров к участку прессования, проходя при этом через клееналивные машины (разработанные и изготовленные компанией HIT).
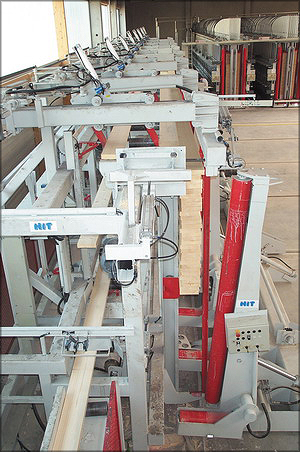
Рис. 8. Набор пакета на патерностере и загрузка в пресс на заводе Hüttemann Wismar. Изготовитель оборудования – компания HIT, Германия
Весь процесс автоматизирован. Небольшая высота прессов обеспечивает оптимальную технологическую гибкость. В целом весь технологический процесс от раскроя пиломатериалов до склеивания в прессе выстроен таким образом, что клееные элементы могут изготавливаться штучно.
Как HIT, так и Minda заявляют, что при использовании их прессов можно добиться значительной экономии материала, поскольку мощные боковые прижимы выравнивают пакет, а это позволяет состругивать небольшой слой древесины. Аналогичная конструкция, обеспечивающая большое боковое давление, и у пресса Springer. Да и вертикальное давление достигается чрезвычайно мощное - до 2 МПа (по технологии изготовления ДКК обычно требуется не больше 1 МПа). Поставляются прессы с высотой пакета до 1800 мм. Однако на практике есть тенденция к использованию прессов с высотой пакета до 1300 мм, который набирается быстрее, чем в прессах с высотой пакетов 1700-1800 мм, а также «быстрых» клеевых систем. Ширина склеиваемого пакета обычно в пределах 320 мм, на заказ изготавливаются и прессы с широким проемом, в которых можно склеивать два пакета в ряд.
Другое решение предложила словенская компания Ledinek: четырехсекционный роторный пресс Rotopress. Пакет формируется в горизонтальном положении и подается в пресс снизу, зажимается, после чего пресс совершает поворот на 90° и следующая секция освобождается от склеенного пакета и загружается новым. Высота склеиваемого пакета достигает 1300 мм, ширина - 300 мм.
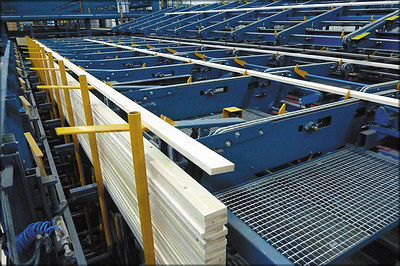
Рис. 9. Подача слоев разных сортов к пакетоукладчику на заводе Nordlam
У этого пресса нет боковых прижимов, выравнивающих пакет, как в вертикальных прессах. При большой высоте пакета устанавливаются дополнительные прижимные балки, препятствующие выпучиванию. Выравнивание пакета выполняется с помощью механизма подъема при загрузке снизу. Вряд ли такая система по степени выравнивания пакета может сравниться с боковыми прижимами рассмотренных выше прессов, что является определенным недостатком пресса Ledinek. В числе достоинств - простота и компактность конструкции. Возможно, поэтому австрийская фирма Weinberger-Holz остановила выбор именно на этом прессе при создании своего производства клееных элементов. На четырехсекционном роторном прессе длиной 18 м можно выпускать 60 тыс. м3 продукции в год.
Таким образом, для склеивания прямолинейных элементов в наши дни предлагается широкий спектр оборудования, включающий прессы с боковой загрузкой для небольших предприятий, прессы с торцовой загрузкой для заводов средней мощности и прессы т. в. ч. для заводов большой мощности (100-200 тыс. м3 в год).
Склеивание криволинейных элементов деревянных конструкций
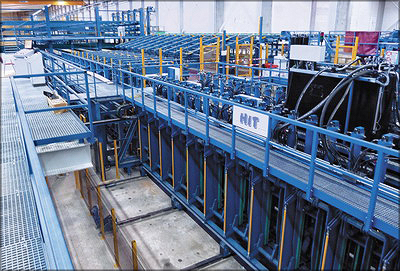
Рис. 10. Передвижная прессовая установка lignoPRESS в составе комплекса оборудования, изготовленного фирмой HIT для завода Nordlam. На заднем плане виден многоярусный склад для выдержки и накопления слоев после сращивания
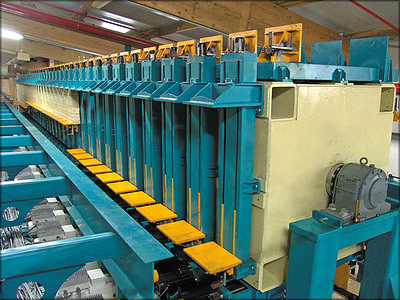
Рис. 11. Пресс Ledinek Rotopress
Оборудование, которое используется для склеивания криволинейных элементов, позволяет прессовать и прямолинейные элементы переменного и постоянного сечения. И многие специализированные предприятия, выпускающие элементы большепролетных клееных конструкций, обходятся только этим видом прессового оборудования.
Наиболее популярным решением здесь были и остаются горизонтальные винтовые прессы. В наши дни подобное оборудование оснащают системами для полуавтоматической расстановки стоек в соответствии с формой получаемого изделия, порталами для выравнивания слоев и передвижными консольными кранами для тяжелых гайковертов. Подобные сложные прессовые установки в настоящее время выпускают две фирмы: немецкая Minda и словенская Ledinek. А прессы простой конструкции изготавливают множество фирм в Европе и в России.
Операции формирования пакета и прессования на современных предприятиях разнесены. Установка формирования пакета представляет собой рольганг, на котором автоматически перемещается упор, определяющий, в каком месте будет сброшен каждый слой; с механизмом снятия доски с рольганга и укладки в пакет и цепного механизма опускания пакета на упорах. Сформированный пакет переносят краном в пресс. Подобное решение позволяет осуществлять автоматизированный процесс формирования пакета параллельно с запрессовкой предыдущих пакетов в прессе, то есть эффективность использования головного оборудования участка повышается.
У прессов и околопрессового оборудования Minda и Ledinek схожая конструкция. Горизонтальные стальные балки основания, в которых закреплены стойки, установлены неподвижно (образуют так называемый силовой пол или поле), но сами стойки могут поворачиваться и перемещаться. Положение и угол поворота каждой стойки задаются CAD-программой, и в соответствии с этими данными специальное устройство автоматически расставляет стойки и регулирует их поворот. После выставления всех стоек, задействованных в склеивании изделия, пресс готов к использованию.
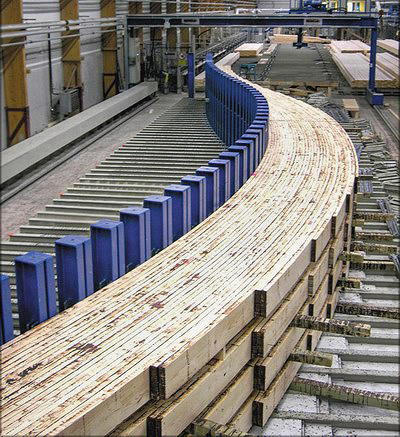
б)
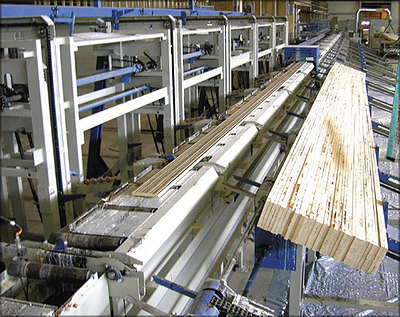
а)
Рис. 12. Комплекс оборудования фирмы Minda для прессования криволинейных элементов: а – установка формирования пакета, б – пресс с полученными клееными элементами, на заднем плане – портал с устройством выравнивания пакета
Пакеты запрессовываются парами, между которыми прокладываются металлические стержни с отверстиями - тяги. Один конец каждой тяги защемлен в стойке, а на другой надевают и максимально близко к пакету закрепляют тяжелый башмак. Для затягивания гаек, которые расположены на тыльной стороне пресса, за стойками, применяется тяжелый гайковерт, подвешенный на легком консольном кране, перемещающемся по рельсам. Затягивание гаек на тягах выполняется от центра к краю пакета. Для повышения производительности вдоль пресса от центра к краям могут двигаться два консольных крана. Перед запрессовкой конкретного участка пакета его выравнивают, продавливая слои и устраняя выступы. Для этого Minda предлагает специальное устройство, установленное на подвижном портале.
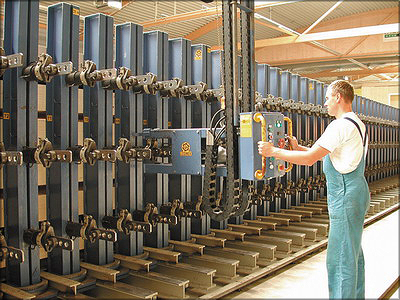
б)
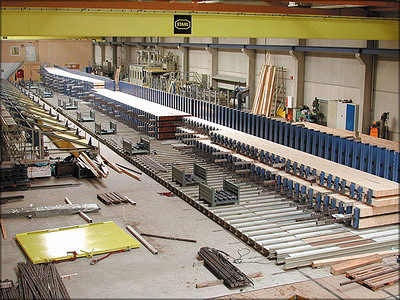
а)
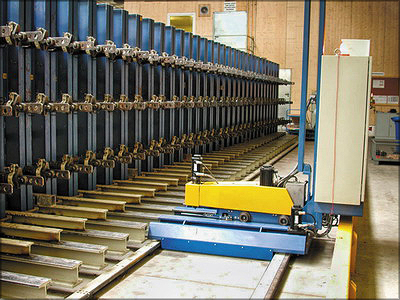
г)
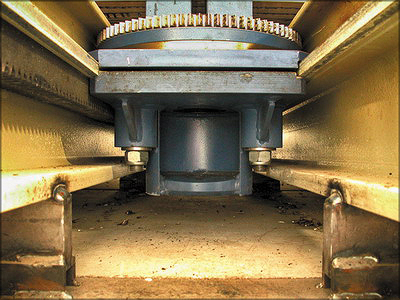
в)
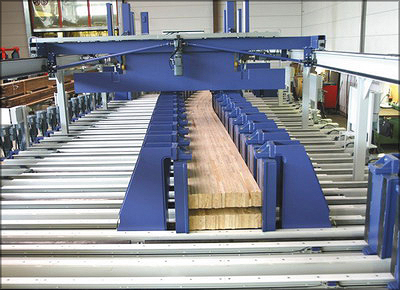
Рис. 14. Автоматический пресс Minda для криволинейных элементов
После завершения запрессовки двух пакетов в этом же прессе запрессовывают следующую пару. В итоге в прессе можно одновременно склеивать до шести пакетов, разумеется, при условии, что размеры партии элементов позволяют это сделать. На протяжении цикла склеивания гайки неоднократно подтягивают для сохранения необходимого давления.
Как можно видеть на рис. 13, в одном длинном прессе может быть выделено несколько зон прессования пакетов разной конфигурации. Чем длиннее пресс, тем более гибкий в технологическом плане производственный участок.
Другим решением для склеивания криволинейных элементов являются горизонтальные гидравлические и электромеханические прессы. Здесь конкуренция также развернулась между компаниями Minda и Ledinek. Достоинством этого типа оборудования является возможность полной автоматизации процесса, включая настройку на форму элемента, выравнивание слоев, приложение давления и поддержание его постоянным в течение всего цикла прессования. Загрузка пакетов в пресс может осуществляться краном, но есть также и вариант компоновки с установкой пресса вблизи установки формирования пакета, позволяющий транспортировать набранный пакет сразу в пресс.
Несмотря на все сильные стороны подобных прессовых установок, они пока не нашли широкого применения, возможно, по причине дороговизны.
Склеивание деревянных панелей
Можно выделить два основных направления в производстве массивных панелей: изготовление панелей малого формата с последующим сращиванием их на нужную длину и изготовление крупноформатных панелей.
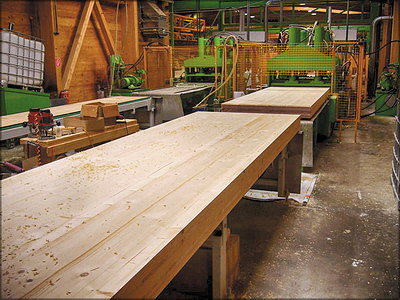
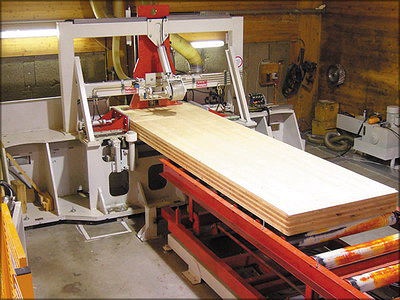
Рис. 15. Шипорезный станок и прессы HIT для сращивания панелей на заводе Binderholz
Примерами производств, работающих по первой из названных технологий, являются завод панелей CLT фирмы Binderholz (Австрия) и завод панелей Lignotrend (Германия). На предприятии Binderholz в прессе получают плиты форматом до 1250 х 3500 мм, а затем сращивают их на горизонтальный зубчатый шип на необходимую длину (до 24 м). Для сращивания подобных панелей фирмой HIT была специально разработана и изготовлена установка, состоящая из фрезерно-калибровочного станка (для обработки боковых сторон панелей), шипорезного станка, двух прессов и цепно-пильного торцовочного станка. После выдержки полученные панели строгают на тяжелом строгальном станке Ledinek. Такое предприятие при работе в двухсменном режиме производит до 50 тыс. м3 панелей в год.
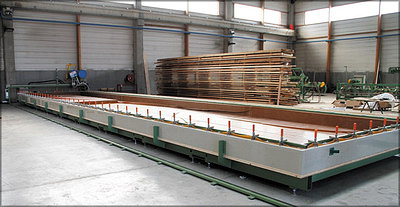
а)
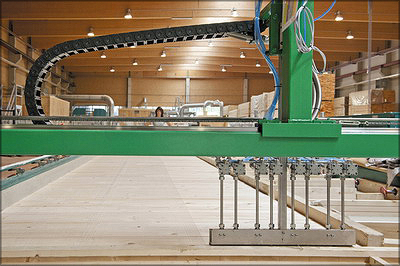
б)
Рис. 16. Вакуумный пресс Woodtec Fankhauser: а – общий вид, б – нанесение клея
Аналогичным образом осуществляется изготовление панелей на заводе Lignotrend. Нарезание зубчатых шипов на панелях выполняется установкой фирмы Fill.
Но более широко распространены технологии изготовления крупноформатных панелей из длинных слоев. Сегодня такой подход преобладает в производстве панелей CLT. В рамках этого подхода также можно выделить разные технологии: склеивание в вакуумном прессе, в холодном гидравлическом или пневматическом прессе, в прессе т. в. ч.
Некоторые специалисты с удивлением воспринимают информацию о том, что несущие панели можно получать в вакуумном прессе: вакуум по определению не может создать давление выше 0,1 МПа, а ведь для склеивания древесины по пласти требуется выше. Но так ли это? Теоретически, если бы заготовки были идеально плоскими, одинаковыми по толщине и гладкими, а клей был бы нанесен абсолютно равномерно, никакого давления для склеивания вообще не требовалось бы. Однако в реальности всегда есть небольшие отклонения формы деталей, например, из-за покоробленности древесины, а также дефекты поверхности. Давление необходимо, чтобы продавить весь «пирог» пакета, заставить заготовки плотно прилегать друг к другу, а клей - равномерно распределиться и попасть в поры древесины. Но тогда получается, что требуемое давление зависит от качества подготовки пиломатериалов и податливости древесины. Для повышения податливости на заготовках делают глубокие продольные пропилы - на 1/3-1/2 их толщины. Многое зависит от применяемого клея: если меламиновый и фенолрезорциновый клеи для равномерного распределения требуют большого давления прессования, то полиизоцианатный клей (1К-ПУР), заполняющий пустоты и имеющий прекрасную адгезию к любым поверхностям, позволяет добиваться отличных результатов при давлении всего 0,01-0,1 МПа.
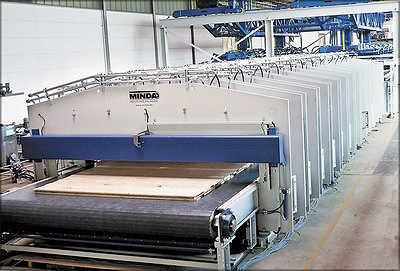
а)
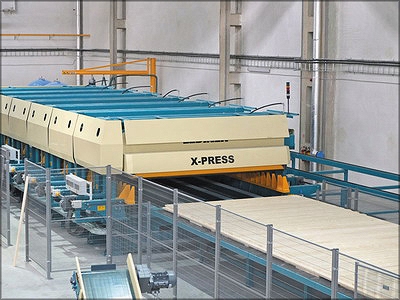
б)
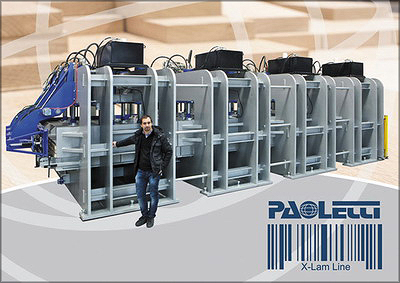
в)
Рис. 17. Холодные прессы для панелей CLT: а – пресс Minda, б – Ledinek X-press, в – пресс Paoletti
Вакуумные прессы для панелей CLT изобрела швейцарская фирма woodtec Fankhauser. Пресс изготавливается в соответствии с индивидуальными требованиями заказчика. Ширина получаемой панели обычно не превышает 3,5 м, длина кратна 2,25 м (то есть величине модуля пресса), как правило, 16-18 м, а толщина - до 300 мм. Пакет для склеивания формируется непосредственно в прессе, заготовки укладываются вручную перекрестными слоями. После укладки каждого слоя наносится клей, обычно полиизоцианатный, для чего над прессом перемещается портал с клеенаносящим оборудованием. Ширина головки клеенаносителя - не более 625 мм, поэтому нанесение клея осуществляется за несколько проходов портала. После набора пакеты по всей длине пресса с боковых сторон зажимаются пневмоцилиндрами - для плотного прилегания заготовок к кромкам, герметично накрываются специальным материалом, затем включается вакуумный насос. Обычно на заполнение и подготовку пресса уходит 30-70 мин., что означает, что на склеивание потребуется 1,5-3,5 ч.
После загрузки одного пресса рабочие могут перейти на другой. Так, на предприятии Hasslacher Norica Timber в г. Шталл до реконструкции эксплуатировались три вакуумных пресса с общим клеевым порталом. Когда рабочие заканчивали загрузку третьего пресса, первый был готов к разгрузке.
Технология woodtec - прекрасный вариант для стартапа. Капитальные затраты невелики: несколько прессов с порталом обойдутся в несколько сотен тысяч евро. В прессе можно изготавливать пустотелые панели, заполняемые изоляцией или тяжелыми засыпками по типу панелей Lignatur или Lignatrend, и даже «сэндвич»-панели из плит OSB и изоляционного материала. То есть пресс woodtec Fankhauser - это универсальное оборудование, в отличие от других прессов для производства CLT. Массивные панели, получаемые способом woodtec, отвечают тем же требованиям нормативов, что и продукт, производимый в гидравлических прессах.
По данным изготовителя - компании woodtec Fankhauser, на текущий момент поставлено 29 прессов. Среди покупателей фирмы из Канады, Новой Зеландии, Швейцарии, Чехии, Испании и Эстонии.
К настоящему времени у компании woodtec Fankhauser уже появился первый конкурент: итальянская компания Sarmax предлагает аналог швейцарского пресса.
Главным недостатком вакуумных прессов является невозможность механизации процесса укладки слоев: рабочие вручную укладывают заготовки, передвигаясь в прессе или вдоль пресса в согнутом состоянии. Интенсивный технологический процесс в таких условиях вряд ли возможен. Вероятно, именно поэтому завод Stall компании Hasslacher Norica Timber, закрепившись на рынке с панелями CLT, в 2012 году приобрел линию на базе пресса т. в. ч., что позволило достичь производственной мощности 30 тыс. м3 панелей CLT в год.
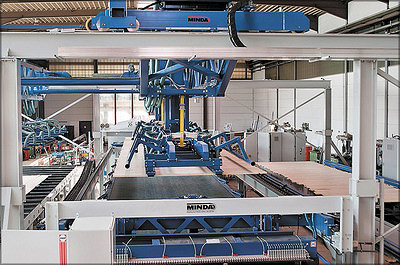
Рис. 18. Система автоматического формирования пакета Minda, в состав которой входят два укладчика с вакуумными захватами – для продольных и поперечных слоев, и портал с широкой клеенаносящей головкой Oest (на переднем плане). Пакет формируется на среднем конвейере
Холодные гидравлические прессы для склеивания панелей CLT предлагают германские компании Bürkle, Minda, HIT, Leiße & Söhne, австрийская компания Fill, итальянские Paoletti и Sormec 2000. Ledinek производит пресс X-Press, приложение верхнего давления в котором осуществляется через пневмокамеры, поэтому этот пресс можно назвать пневмомеханическим. Все изготовители предлагают комплектацию пресса боковыми прижимами не только с продольной стороны, но и с торцов (эти прижимы опускаются после заполнения пресса), что необходимо для получения стеновых панелей без зазоров между досками. Fill изготавливает пресс с поперечной загрузкой, что позволяет сократить производственные площади, но в этом случае приходится изготавливать пресс с поднимающимися боковыми прижимами по продольным сторонам, чтобы обеспечить свободный проход пакета. Еще более радикальное решение для экономии места предлагает Leiße & Söhne: в линии, выпускаемой этой компанией, не пакет подается в пресс, а пресс перемещается от одной платформы к другой. Пока прессуется пакет на одной платформе, на другой набирается следующий пакет.
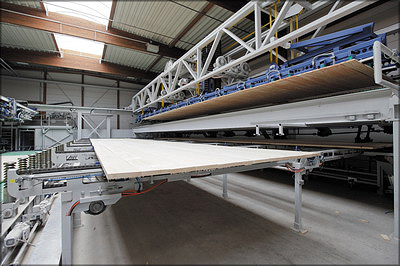
б)
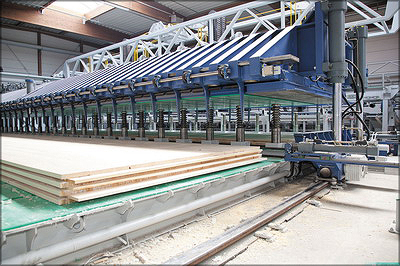
а)
Рис. 19. Линия прессования Leiße & Söhne: а – передвижной холодный пресс, на левой платформе – готовая панель, на правой – набранный пакет, пресс опускается в рабочее положение; б – установка набора пакета с двумя уровнями конвейеров для поступления продольных и поперечных слоев
Пресс Sormec 2000 рассчитан на склеивание панелей шириной до 3000 мм, прессы Paoletti и Fill - до 3200 мм, другие перечисленные выше прессы - до 3600 мм. В длину пресс набирается из модулей, поэтому изготовители предлагают установки длиной до 18 м. Панель в прессе склеивается целиком, поэтому длина пресса определяет максимальную длину панелей. Толщина склеиваемых пакетов обычно 70-400 мм, что позволяет склеивать по несколько панелей в пакете, а во избежание склеивания пакетов прокладывать между ними пленку.
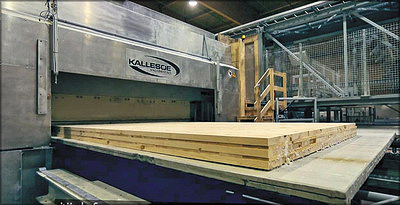
Рис. 20. Панель CLT на выходе из пресса т. в. ч. Kallesøe
Максимальное давление прессования обычно 0,6-1,1 МПа, но компания HIT предлагает прессы, в которых давление достигает 2 МПа. Здесь следует оговориться, что при обработке под избыточным давлением можно повредить древесину, поэтому для обработки изделий из европейских хвойных пород рекомендуется давление 0,4-0,6 МПа.
Самые простые линии на базе холодных прессов состоят из пресса, подающего и приемного конвейеров и клеенаносителя. Пока в прессе склеивается один пакет, на подающем конвейере рабочими вручную набирается другой. Иногда для экономии средств и пространства используют один конвейер в качестве и приемного, и подающего. Клеенаноситель обычно представляет собой передвижной портал с емкостью и системой нанесения клея, подобный тому, который применяется в системах с вакуумными прессами. В состав компактной линии, поставленной фирмой Ledinek одному из колледжей в Финляндии, входит стационарный портал, и пакет несколько раз должен пройти под ним (и зайти при этом в пресс), чтобы клей был нанесен на всю поверхность слоя. Причем пресс при этом не работает.
Использование подобных решений, конечно, позволяет экономить капитал, что важно при создании производства, особенно в условиях формирующегося рынка. Однако нельзя не отметить, что по отдаче на вложенный капитал участок, оснащенный подобным оборудованием, намного уступает участку на базе вакуумных прессов. Не в полной мере оказывается задействованным также дорогостоящее оборудование для подготовки слоев, в частности линия сращивания, что еще больше увеличивает инвестиционную составляющую себестоимости (если производство создается на заемные средства, которые необходимо возвращать). В результате конечный продукт при такой организации участка прессования может оказаться чрезмерно дорогим в изготовлении. Кроме того, рабочим приходится вручную раскладывать длинные заготовки.
Именно поэтому гидравлические прессы, как правило, дополняют автоматическими системами формирования пакета, что позволяет сократить и время прессования. С такими системами предприятия достигают производственной мощности 25 тыс. м3 в год при односменном режиме.
Хотелось бы особо отметить вариант организации участка прессования, реализованный компанией Leiße & Söhne на заводе группы Derix в г. Нидеркрюхтене. Как уже было сказано, особенность конструкции оборудования, которое используется на этом предприятии, заключается в том, что верхняя плита пресса регулярно перемещается от одной нижней плиты к другой, при этом на первой плите остается склеенная панель или панели, а на второй лежит набранный пакет. Верхняя плита опускается на пакет, при этом стойки нижней плиты входят в отверстия верхней и закручиваются, в результате чего создается давление по всей рабочей поверхности плит, прикладывается боковое давление вдоль пакета или по его торцам. Во время прессования вакуумный укладчик формирует следующий пакет на освободившейся от склеенных изделий плите, причем если это дальняя плита, то укладчик свободно перемещается над прессом. Слои поступают в зону подбора укладчиком по двухуровневой системе конвейеров: поперечные - сверху, продольные - снизу. Клеенаноситель установлен на конструкции, перемещающейся по тем же крановым путям, что и укладчик. Основное достоинство этого оборудования в том, что сформированный пакет никуда не перемещается и нет риска смещения заготовок в нем, а это открывает возможности для изготовления в прессе не только плит CLT, но и пустотелых панелей вроде Lignatur или Lignatrend.
А если компания хочет, чтобы объем выпуска ДКК был выше 25 тыс. м3 в год? Поскольку процесс формирования пакета обычно в три-четыре раза быстрее склеивания, логично установить на предприятии несколько прессов, которые обслуживаются одной системой укладки.
Впрочем, можно просто выбрать пресс т. в. ч. от фирмы Kallesøe. Конструкция пресса для склеивания массивных панелей отличается от конструкции пресса для многослойных элементов расположением электродов и системой подачи, но принцип действия прессов одинаковый: в поле токов высокой частоты склеивание обычными клеями на основе смол ММФ и ФРФ можно выполнять за считаные минуты, что позволяет организовать непрерывный процесс формирования пакетов и их склеивания. Прессование пакета обычно осуществляется участками, а длина самого пресса может быть небольшой. Наращивание длины пресса позволяет увеличить производительность.
В прессе Kallesøe склеиваются элементы Lignatur - как панели, так и балки коробчатого сечения. Для предотвращения смещения заготовок пакет стягивают пластиковыми лентами.
Поставленная заводу Hasslacher Norica Timber линия CLT на базе пресса Kallesøe оснащена механизацией Springer с оригинальной системой набора пакета, позволяющей создавать при укладке оконные и дверные проемы, формировать оптимальный контур панелей, что дает возможность избежать потерь материала при последующем изготовлении элементов. Такое решение требует применения весьма сложной автоматики, ведь в зону формирования пакета в этом случае поступает большое число заготовок разной длины, и все они должны быть поданы в нужном порядке. Однако достигаемая при этом экономия материалов перевешивает любые затраты на такую систему.
Во всех описанных выше случаях в составе технологического процесса нет операции склеивания заготовок поперечных слоев перед их подачей в зону набора пакета. Однако на заводах компании Stora Enso, крупнейшего в мире производителя CLT (140 тыс. м3 в год), эта операция является частью технологического процесса. Предварительное склеивание по кромкам позволяет исключить даже малейшие зазоры между заготовками, благодаря чему стена, изготовленная из таких панелей, выглядит монолитной. Склеивание осуществляется в прессе Dimter (Weinig Group), откуда материал выходит в виде непрерывной широкой ленты, от которой пилой отрезается плита требуемой длины, а остаток становится началом следующей плиты.
Некоторые специалисты, впрочем, считают, что избежать появления щелей на лицевой поверхности в принципе невозможно: они рано или поздно появятся из-за взаимно перпендикулярных направлений усушки в слоях материала. А значит, и склеивать по кромкам заготовки поперечного слоя нет смысла. Вместо этого применяют другие решения: специальный профиль на кромках этих заготовок (слой получается как бы набранным в шпунт и гребень, заготовки в слое самовыравниваются), мощные торцовые прижимы в прессе, а также дополнительные наружные поперечные слои (такая комбинация позволяет снизить напряжения в лицевом слое и избежать появления щелей при эксплуатации).
Тем не менее группа Weinig предлагает свою технологию производства панелей CLT, основанную именно на предварительном соединении по кромкам в поперечных и продольных слоях. Как и технология Springer, эта технология предполагает создание проемов и уступов еще при формировании слоя за счет особого расположения заготовок требуемой длины, что позволяет избежать вырезов в готовых элементах.
Технология склеивания элементов Kielsteg предполагает их получение с использованием полученных сращиванием длинных слоев из досок и плит OSB на прессах особой конструкции и с помощью автоматической системы укладки заготовок в пресс.
Артем ЛУКИЧЕВ