Напольные покрытия из древесины
К числу напольных покрытий, для изготовления которых в той или иной степени используется древесина, относят паркет и ламинат. Паркет вошел в моду с XVII века и с тех пор свидетельствует о хорошем вкусе и статусе владельца жилья с уложенными паркетными полами. Сегодня на рынке натуральных деревянных напольных покрытий представлен штучный (наборный) паркет, массивная доска пола и паркетная доска. Ламинат (ламинированное напольное покрытие) - развитие идеи паркетной доски, многослойная конструкция, для производства которой используются HDF, MDF, пластмасса и особые сорта бумаги, с рисунком или без, и пропитанные смолой.
Производство паркета. Технология, оборудование, инструментЧто такое штучный паркет?
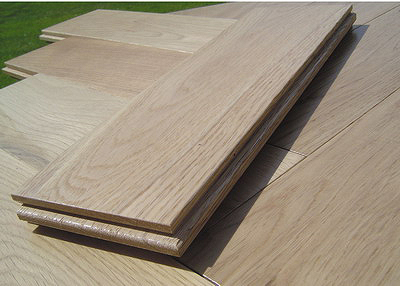
Рис. 1. Шиповое соединение штучного паркета
Штучный паркет выпускается многими российскими предприятиями, технология его производства у нас в стране весьма хорошо отработана. У штучного паркета довольно простой профиль шипового соединения (см. рис. 1).
Штучный паркет для клеевой или гвоздевой укладки значительно доступнее по цене, чем паркетные доски и ламинат с замковыми соединениями, однако паркет, для укладки которого использовался клей, повторному использованию после демонтажа не подлежит. Для нас особенно интересны два вида напольных покрытий: многослойная паркетная доска и ламинат на основе плит HDF и MDF. Вызван этот интерес применением новых материалов (плит, клеев и ЛКМ), вовлечением в производство, например, паркетной доски, значительных объемов низкосортной древесины, новых плитных материалов, бурным ростом выпуска этой продукции как в мире, так и в России, а также постоянным совершенствованием технологий и оборудования.
Что такое паркетная доска?
Паркетная доска - современное трехслойное напольное покрытие из древесины, слои которой склеены перпендикулярно. Каждый слой изготовлен из древесины разных пород и решает свою задачу.
Верхний (лицевой) слой трехслойной конструкции изготавливают из шпона ценных пород древесины, в основном дуба, ясеня и ореха, реже - из экзотических пород. Толщина слоя, как правило, не менее 0,5 мм (более тонкий слой недопустим, иначе при производстве доски и ее отделке может произойти разрыв лицевого покрытия - шпона) и не более 2 мм.
Средний слой паркетной доски состоит из сосновых или еловых реек толщиной около 8 мм, обработанных специальным образом для снятия внутренних напряжений в древесине. Иногда, чтобы паркетной доске придать стабильность в случае изменения температуры и влажности, средний слой изготавливают из HDF-плиты, фанеры из хвойных пород или ламелей из хвойной или лиственной древесины, которые при склейке укладывают перпендикулярно декоративному слою. На этом же слое вырезают замковые соединения. Нижний слой паркетной конструкции однороден, изготавливается из шпона древесины хвойных пород толщиной обычно около 1,5 мм или трехслойной фанеры; основная задача слоя - препятствовать выгибанию паркетной доски в процессе производства, укладки и эксплуатации.
Толщина паркетной доски варьирует от 7 до 22 мм, ширина - от 13 до 20 см, а длина - от 2 до 2,5 м. Главные достоинства паркетной доски: экологичность, привлекательный внешний вид, влагоустойчивость, прочность и долговечность.
Верхний слой паркета для повышения износостойкости покрывают маслом, паркетным лаком или воском, как правило, в процессе производства.
Что такое ламинат?
Ламинат - это одно из самых лучших искусственных напольных покрытий. Популярным ламинат стал за счет привлекательного внешнего вида, высокой долговечности, прочности и практичности.
Особенность ламината в том, что его внешняя поверхность имитирует структуру и цвет разных пород. Верхний слой ламината различается по классам износостойкости, среди которых есть повышенные: 32, 33 и 34.
Доска ламината представляет собой многослойную конструкцию. Основа - древесноволокнистая плита HDF, которая обеспечивает необходимую прочность и жесткость доске. На нее наклеен слой специальной бумаги с предварительно нанесенным рисунком, имитирующим текстуру древесины. Поверх бумаги с рисунком на ламинат наносится защитный слой из акриловой или меламиновой смолы, из-за чего этот материал и получил название «ламинат». Этот слой отвечает за такие свойства ламината, как абразивная устойчивость (сопротивление истиранию), невосприимчивость к пятнам, воздействию солнечных лучей, химикатов, к механическим повреждениям. Невысокая стоимость ламината обеспечивает его широкую доступность для потребителей.
В отличие от паркетной доски, ламинат - полностью искусственный материал. Он изначально разрабатывался для имитации паркета, причем планировалось значительно улучшить его технические и эксплуатационные характеристики по сравнению с характеристиками деревянных напольных покрытий. Поэтому первые образцы ламината были значительно дороже паркетной доски. Но благодаря развитию технологий удалось удешевить производство и приступить к выпуску недорогого ламината 21-го класса (см. ГОСТ 32304-2013), который внес свою лепту в формирование мнения россиян о низких эксплуатационных характеристиках ламината.
Сегодня российский рынок минимум на 70% заполнен российской и китайской продукцией, представляющей собой дешевую ламинированную плиту MDF. Покрытие подобного качества вряд ли годится для устройства добротного пола, хотя нередко довольно дорогое: во многих строительных гипермаркетах продается ламинат якобы 33-го класса износостойкости, толщина которого всего 7 мм. Это подделка - выпуск ламината с такими характеристиками противоречит всем европейским санитарным и строительным нормам. Дело в том, что компания, не входящая в ассоциацию европейских производителей напольных ламинированных покрытий, может указать на упаковке своей продукции любой класс, какой вздумается, и не несет за это никакой ответственности.
Замковые соединения паркетных напольных покрытий
При сборке полов из паркетной доски, как и из ламината, в отличие от штучного паркета используются специально разработанные замковые соединения сборно-разборного типа.
Первый опыт замены соединения напольного покрытия по принципу «шип - паз» замком типа сlick относится к 2002 году. Инновация инженеров немецкой компании Parador в то время не получила должного отклика и развития. Это и понятно, ведь на первых этапах изделие было довольно дорогостоящим. Однако вместе с совершенствованием технологии паркетная доска с замком пошла в серию, профили замковых соединений были запатентованы несколькими фирмами, и сейчас это один из наиболее востребованных продуктов на рынке напольных покрытий.
В настоящее время все паркетные покрытия на основе замковых систем снабжены на торцах специальными стыковочными пазами и гребнями. Механизмы соединений разнообразны, но все они по варианту фиксации подразделяются на замки типа lock и сборно-разборные типа click.
Замковая система типа lock
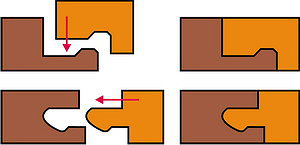
Рис. 2. Замковая система типа lock на напольном
паркетном покрытии
Доски, оснащенные защелками типа lock, считаются экономичным вариантом. Простота конструкции и надежность стыковки обеспечили напольным покрытиям с этой замковой системой популярность у потребителей. Этот вариант соединения также называют забивным, исходя из особенностей сборки пола.
Суть замка-защелки заключается в следующем: на одной доске покрытия имеется паз, а на другой - шип, который оснащен специальным гребнем, обеспечивающим его прочную фиксацию внутри паза после сборки. Соединение, которое выполняют забиванием шипов в пазы с помощью деревянной или резиновой киянки и без использования клея, получается неразрывным. Подобное соединение считается весьма прочным, минимально подверженным образованию щелей и очень удобным в монтаже. Работают эти замки следующим образом: шип планки вставляют под углом 45° в паз предыдущей планки и, подавая вниз и вперед, слегка нажимают или подбивают киянкой. Защелкивание замка сопровождается характерным звуком. Для монтажа не требуется физических усилий или использования специальных инструментов, что, несомненно, большой плюс. Стоимость напольных покрытий с lock-защелками невысокая, но для их монтажа необходимо абсолютно ровное основание.
При нагрузках замковая система не испытывает трения, а находится под воздействием силы сжатия, что дополнительно повышает прочность соединения.
Система типа click
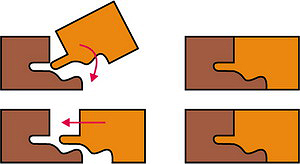
Рис. 3. Замковая система типа сlick на напольном
паркетном покрытии
Замки системы типа click - более совершенные соединения по сравнению с lock-замками. Уложить и разобрать напольное покрытие, снабженное замками типа click, легко и быстро может любой человек, не обладающий профессиональными навыками.
Чтобы разобрать покрытие в одном помещении и настелить пол в другом, потребуется значительно меньше времени, чем при разборке напольного покрытия с замковым соединением типа lock. Кстати, разборку/сборку полов, снабженных системой click, можно выполнять по нескольку раз в течение эксплуатационного срока напольного покрытия. Элементы замков click, в отличие от lock-систем, не ломаются при демонтаже. Допустимый перепад высоты при укладке покрытия с замком click - до 3 мм на 1 пог. метр.
Пол из паркетной доски с качественными замками типа click, по сути, монолитный, конечно, если он правильно уложен, с учетом оптимального направления панелей.
Система типа uniclick
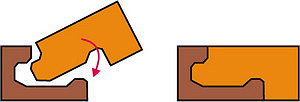
Рис. 4. Универсальная замковая система типа uniclick на
напольном паркетном покрытии
Разработанный недавно универсальный замок типа uniclick запирается поворотом - как click, или забиванием - как lock. Им снабжают все четыре кромки паркетных досок и ламината, как торцевые, так и длинные.
А использование похожего по профилю на uniclick замка unicliсk multifit, разработанного фирмой Quick-Step, позволяет выполнять защелкивание тремя способами: сверху, под углом или в горизонтальной плоскости, - что существенно облегчает и ускоряет укладку, особенно в неудобных и труднодоступных местах.
Достоинства замковых соединений:
- обеспечивают простоту укладки, в отличие от соединений типа «шип - паз», особенно клеевых, к тому же для монтажа не требуется клей и не надо ждать, когда он высохнет;
- обеспечивают малозаметное и надежное соединение досок напольного покрытия;
- скорость укладки материала возрастает в несколько раз по сравнению с технологией монтажа покрытия «шип - паз»;
- покрытие можно эксплуатировать сразу же после монтажа;
- после соединения доски образуют цельную пружинящую, довольно устойчивую плоскость, которая не скрипит при ходьбе по ней;
- при необходимости готовый пол из напольных паркетных покрытий с замковым соединением можно разобрать и заново уложить в другом помещении; для демонтажа надо просто поднять доску со стороны, противоположной замку.
Производство паркетной доски
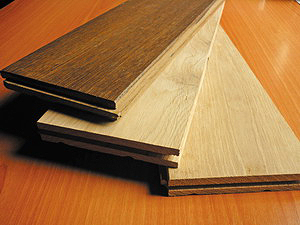
Рис. 5. Паркетная доска
В структуру предприятия по производству паркетной доски могут входить следующие подразделения: склад сырья и материалов; лесопильный цех; сушильный цех; участок первичной механической обработки древесины; участок обработки строганного и лущеного шпона; участок термообработки и браширования (по необходимости); прессовый участок; участок повторной механической обработки; отделочный участок; участок сортировки и упаковки готовой продукции; склад готовой продукции.
В России не так много производств с полным циклом обработки паркетной доски. Чаще всего они используют готовый сухой пиломатериал, что негативно влияет на качество продукции из-за некачественной сушки, неправильной транспортировки и хранения сухих пиломатериалов. Поэтому необходимо включить в состав технологических подразделений производства сушильный участок, чтобы жестко контролировать процесс сушки пиломатериалов. При работе с древесиной твердолиственных пород и лиственницы для получения сухих пиломатериалов гарантированного качества целесообразно использовать сушилки, оснащенные установками увлажнения древесины паром.
Если у предприятия есть собственный участок лесопиления, следует учесть, что при раскрое древесины как твердолиственных, так и хвойных пород следует отдавать предпочтение лесопильному оборудованию для индивидуального раскроя пиловочного сырья (т. е. однопильному), обеспечивающему минимальную толщину пропила и возможность размерно-качественной сортировки сырых пиломатериалов. Раскрой брусьев можно выполнять как на многопильных круглопильных станках с использованием тонких ступенчатых пил, так и на тарных лесопильных рамах или их аналогах.
На участке первичной механической сортировки следует предусмотреть установку качественного технологического оборудования для продольного и поперечного раскроя пиловочного сырья с вырезкой дефектов строения древесины, линий по продольному и поперечному сращиванию некондиционной древесины для ее более полного вовлечения в производство. В случае изготовления всех трех слоев паркетной доски из древесины нужно предусмотреть оборудование для раскроя срощенных заготовок и щитов на заготовки под лицевые, внутренние и наружный слои паркетной доски.
На участке обработки шпона необходимо установить оборудование требуемой производительности по починке строганного шпона, по продольному и поперечному раскрою кнолей, оборудовать участок сортировки, сшивания нитью или склеиванию заготовок из шпона в рубашки для лицевой поверхности паркетной доски. При использовании лущеного шпона для оборотной стороны паркетной доски также нужно предусмотреть участок для его раскроя и сортировки.
Древесина лицевых слоев паркетной доски может быть подвергнута термообработке и брашированию. Термообработка - это нагрев древесины по специальной технологии до температуры выше 195 °С без доступа воздуха, в результате чего она приобретает насыщенный темный цвет, и доска становится стабильной. Благодаря этой операции почти незаметны оставляемые на темном полу царапины, а паркетная доска мало подвержена усушке и разбуханию (впитыванию влаги) и ее можно использовать в т. ч. и при устройстве «теплых полов».
В естественных условиях годовые кольца, образованные в стволе дерева весной, обладают меньшей плотностью, чем те, что образовались осенью и зимой. Поэтому со временем эти мягкие волокна разрушаются. Технология браширования (т. н. искусственного состаривания) предполагает удаление мягких волокон при помощи специальных станков с металлическими щетками, благодаря чему древесина становится рельефной, с подчеркнутой текстурой годовых колец. На брашированной доске почти незаметны вмятины, царапины и трещины, а объемный рисунок придает особый шарм напольному покрытию.
На прессовом участке необходимо предусмотреть технологическое оборудование для качественного склеивания слоев в трехслойную заготовку будущей паркетной доски, тепловой или ТВЧ-сушки клеевых швов - в зависимости от применяемого клея (смолы) и требуемой производительности участка.
После прессового участка заготовки паркетной доски поступают на участок повторной механической обработки, где форматируются и на них с четырех сторон нарезаются замковые профили, затем доски сортируют и упаковывают на участке сортировки и упаковки, откуда отправляют на склад готовой продукции. Оборудование для нарезки на таких паркетных досках должно быть оснащено фрезерными и пильными узлами (шпинделями) с антискольными функциями.
Упрощенно технология производства паркетной доски такова: к среднему слою из плиты HDF приклеивают декоративный и стабилизирующий слои из древесины или шпона, препятствующие выгибанию паркетной доски.
Производство ламината
Российские предприятия, производящие, как правило, ламинат в больших объемах (чтобы снизить себестоимость выпускаемой продукции), в основном входят в состав заводов, на которых изготавливаются плитные материалы, или максимально приближены к ним территориально для снижения издержек по сырью.
Для производства ламината, в зависимости от объемов производства, необходимы следующие подразделения: склад сырья и материалов; участок раскроя плитных материалов; участок раскроя бумажной продукции (для лицевой и оборотной стороны); прессовый участок; участок механической обработки, участок сортировки и упаковки готовой продукции; склад готовой продукции. Участок нанесения финишного покрытия отсутствует, т. к. приклеивание финишного слоя может быть совмещено со склеиванием слоев ламината на прессовом участке.
Что выгоднее производить: паркетную доску или ламинат?
Понятно, что наиболее благоприятный вариант, когда рядом с предприятием есть доступное по объемам, качеству и стоимости сырье, ведь львиную долю в себестоимости продукции составляет именно оно. Кроме того, при принятии решения о строительстве завода по выпуску напольных покрытий надо иметь в виду и объемы рынков паркетной доски, произведенной из массива древесины, трехслойного профиля, а также ламината. Ведь производство паркетной доски, например, требует дополнительных капиталовложений, больших площадей (в частности, для изготовления паркета из переклеенной древесины необходимо оборудование для раскроя сырья, сушки заготовок, отделки продукции). При выпуске небольших объемов продукции экономически целесообразнее работать с массивной и переклеенной древесиной, чем с ламинатом.
Ламинат - это искусственное напольное покрытие, в состав которого в лучшем случае входит плита HDF, а чаще всего - полимерные материалы и смолы, которые при нагревании помещения выделяют опасные для здоровья эфиры. Древесина - натуральный продукт, который выделяет в атмосферу фитонциды (особенно древесина хвойных пород) - биологически активные вещества, убивающие или подавляющие рост и развитие бактерий, грибков и простейших микроорганизмов.
Конечно, разница в цене качественной паркетной доски и ламината весьма ощутима. Отечественные производители паркетной доски стараются находить разумный компромисс цен на паркетную доску и ламинат. Цены на паркетную доску российского производства немногим выше цен на качественный импортный ламинат.
Качество импортной и отечественной массивной доски, по сути, одинаковое, т. к. в России производство осуществляется на импортном оборудовании, которое используется на всех этапах технологической цепочки. Для того чтобы составить серьезную конкуренцию зарубежным производителям ламината, на российских предприятиях должно быть создано крупное производство качественной плиты HDF.
Чаще всего отечественный производитель использует местное сырье, которое достается ему по более низкой цене, чем древесина экзотических пород, поэтому цена паркетной доски отечественного производства сопоставима с ценой хорошего импортного ламината. Самый популярный и традиционный материал для изготовления напольных покрытий - древесина дуба. Используются и древесина бука, ореха, ясеня, березы, а также таких экзотов, как мербау, ятоба, венге.
Виды и сорта паркетной доски
Виды паркетной доски: однополосная, двухполосная, трехполосная, четырехполосная, многополосная.
Сортность паркетной доски - это установленный уровень качества верхнего декоративного слоя напольного покрытия по таким показателям, как способ распила; наличие, размер и число сучков; наличие и площадь заболони; цветовая гамма; наклон волокон. Рассмотрим в общих чертах самые распространенные сорта паркетной доски и их характеристики.
В настоящее время на российском рынке в зависимости от сортности верхнего слоя представлена паркетная доска следующих сортов: «Радиал-селект», «Селект (стандарт)», «Натур», «Рустик» («Кантри»), «Ротубус» («Эконом»).
«Радиал-селект» - высший сорт, получивший название из-за особой - максимально ровной текстуры, без ярко выраженных сердцевидных лучей, которая обеспечивается в результате радиального распила пиломатериала. Для его производства используется древесина, в которой не допускаются сучки, заболонь, механические повреждения и другие пороки древесины. Характеристики паркета этого сорта близки к параметрам категории А по ГОСТ 862.1-85.
Паркет сорта «Радиал-селект» используют чаще всего при геометрическом способе укладки щитового паркета, получается равномерный и незамысловатый однотонный рисунок. «Селект (стандарт)» - это высший сорт паркета, изготовленного из древесины смешанного распила (радиального и тангенциального). Ему присущи выраженный натуральный рисунок текстуры древесины и небольшие перепады тональности. Для его производства используется древесина, в которой не допускаются сучки, заболонь, механические повреждения и другие пороки. Характеристики сорта близки к параметрам категории А по ГОСТ 862.1-85.
«Натур» - это сорт паркета, для изготовления которого используют доски как радиального, так и тангенциального распила. Для него характерны ярко выраженный натуральный рисунок текстуры древесины и хорошо заметные перепады по тонам. Для его производства используется древесина, в которой допускается наличие мелких сучков (около 2 мм), сердцевидных лучей, прожилок и заболони, доля которых определяется заводом-производителем.
«Рустик» («Кантри») - сорт паркета, для изготовления которого используют доски как радиального, так и тангенциального распила. Ему присущи ярко выраженный натуральный рисунок текстуры древесины и хорошо заметные перепады по тонам. Для его производства используется древесина, в которой допускается наличие больших сучков, сердцевидных лучей, наклона волокон, прожилок, заболони и мелких механических повреждений, доля которых определяется заводом-изготовителем. Характеристики этого сорта паркета близки к параметрам категории Б по ГОСТ 862.1-85.
«Эконом» («Ротубус») - сорт паркета, для изготовления которого используют доски как радиального, так и тангенциального распила в любом соотношении, без отбора по распилу и тону древесины. Для производства подходит древесина, в которой допускается наличие сучков, сердцевидных лучей, прожилок, заболони, трещин, наклона волокон и любых механических повреждений, доля которых определяется заводом-изготовителем.
Виды защитных покрытий паркетной доски
Один из основных плюсов паркетной доски - износостойкий защитный слой. На заводе доски покрывают специальным лаком, маслом или воском. У каждого из этих покрытий есть свои достоинства и недостатки.
Достоинства и недостатки лакового покрытия:
- лаковое покрытие в 1,5-3 раза более износостойкое, чем масляное, при условии правильной эксплуатации паркета. Масляное покрытие надо реставрировать каждые 2-5 лет, лаковое (например, выполненное с использованием лака кислотного отверждения) прослужит без обновления 6-10 лет; лаковое покрытие можно снять - отциклевать поверхность досок и обработать их маслом;
- стоимость лакированной паркетной доски зачастую ниже стоимости доски с масляным покрытием;
- паркетную доску, покрытую лаком, в случае появления царапин надо шлифовать; если пол уложен плавающим способом и не приклеен к основанию, то реставрировать имеет смысл только однополосную доску. Дело в том, что пол, уложенный плавающим способом, под шлифовальной машиной будет чуть-чуть прогибаться на замках, и шлифовка окажется неравномерной. На однополосной доске небольшие искривления пола малозаметны. Трехполосные доски слишком дорого и проблематично циклевать и реставрировать, разумнее заменить новыми;
- лаковое покрытие при частых контактах с водой разрушается, а при усушке паркетной доски - трескается.
Достоинства паркетной доски с масляным защитным покрытием:
- паркетная доска «под маслом» смотрится более натурально;
- доска с масляным покрытием на ощупь приятнее, чем лакированная;
- паркетный пол с масляным защитным слоем можно реставрировать локально - обновляя масляное покрытие на поврежденной доске;
- паркетная доска с масляным покрытием значительно лучше, чем лакированная, переносит перепады температуры и влажности;
- паркетная доска с масляным покрытием больше пригодна для устройства и эксплуатации «теплых полов», чем доска, покрытая лаком;
- доска с масляным покрытием, в отличие от лакированной, лучше «дышит».
Но есть и минус: паркетная доска, покрытая масляным защитным слоем, идеальна для жилых помещений, но по ней нельзя ходить в уличной обуви, т. к. вымыть впитавшуюся в покрытие грязь не удастся.
Владимир ПАДЕРИН