Ligna 2019: отрасль в развитии
Прошедшая выставка была интересна не только своими новинками, но и тем, насколько по-разному производители оборудования видят направления развития своих компаний и ЛПК в целом. Слияния и укрупнения компаний, изменение рынков продаж и даже профилей деятельности, наравне с новинками техники и технологии с полным правом могут быть выделены в качестве основных трендов прошедшего мероприятия.
В дни выставки мы попросили ведущих специалистов нескольких компаний-экспонентов не только рассказать о внедряемых ими изменениях в станкостроении и применяемых IT-технологиях, но и поделиться мыслями о том, как компаниям удается соответствовать изменяющимся рыночным требованиям на протяжении всего периода работы, чем вызваны процессы объединения производителей, или же, наоборот, выход на рынок под собственным брендом, а также попробовать предсказать изменение тенденции в разных регионах мира.
Специалисты Altendorf Group охарактеризовали Ligna 2019 как «мировой смотр премьер компании». Повод для такого заявления есть уже потому, что именно там две именитые машиностроительные фирмы – эксперт форматно-раскроечного оборудования Altendorf и производитель кромкооблицовочных станков Hebrock впервые выступили в составе одной группы.
Сильные бренды Altendorf Group должны дать дополнительный импульс росту ее репутации в мире. После приобретения инвестором Avedon компании Altendorf в 2017 году команда менеджеров во главе с новым генеральным директором группы Андреасом Тингваллем разработала концепцию развития группы в ближайшем будущем как поставщика широкого ассортимента высококачественного оборудования для обработки плит деревообрабатывающим и мебельным предприятиям. Помимо традиционной для Altendorf линейки планируется выпускать еще две категории станков с ЧПУ. Первым шагом на этом пути стало вхождение в апреле 2018 года в состав группы компании Hebrock из Восточной Вестфалии, вторым – создание в начале 2019 года американского подразделения (Altendorf Group America) в Мурсвилле, штат Северная Каролина.
Демонстрацией слияния компаний на выставке стала интеграция станков Altendorf и Hebrock, выполненных в одном дизайне, известном отраслевому сообществу по удостоенному многих премий знаменитому пильному станку с подвижной кареткой Altendorf F45. Изменения коснулись не только облика кромкооблицовочных станков Hebrock, но и блока управления: появился контроль уровня клеевого состава в клеевой ванне, сканер штрих-кодов, светодиодная подсветка рабочей зоны станка и т. д.
Миссия и первоочередная цель объединения машиностроительных фирм – безукоризненное обеспечение современных плитных производств новейшими технологиями.
Средствами достижения этой цели руководство группы считает дальнейшее углубление цифровизации, удаленное сервисное обслуживание, прямую связь производителя и пользователя машин. Дистанционный сервис обеспечивает незамедлительную техподдержку в режиме 24/7 всех станков, выпущенных Altendorf с середины 2015 года: при помощи специализированного ПО сервисная служба может получить прямой доступ к компьютеру станка на предприятии клиента и проверить систему управления, устранить проблему и изменить настройки. Дороже всего предприятию обходятся простои оборудования, и удаленный сервис поможет их сократить. Диапазон услуг в онлайн-режиме будет существенно расширен (пакеты финансовых решений, онлайн-тренинги, сервис по индивидуальному запросу и др.), а пользователи получат возможность обратной связи, их отклики и мнения станут основой для разработки продуктов, которые действительно нужны для повышения эффективности работы. Глобальный проект «Платформа пользователя» был запущен в мае 2019 года.
Важный аспект работы деревообрабатывающего завода – безопасность. Предотвращение несчастных случаев стало приоритетом Altendorf Group. На выставке компания презентует систему предотвращения аварий, разработчики которой учли все недостатки прежних систем безопасности. С помощью современной 3D-камеры контролируется ситуация в рабочей зоне, не допускаются ни травмы, ни ложные срабатывания.
Холдинг ARA Technology Group может предложить игрокам рынка комплексные поставки оборудования для организации лесопильного предприятия: от линий сортировки и раскроя круглых лесоматериалов до участков строгания и упаковки пиломатериалов, за исключением оборудования для гидротермической обработки. В 2018 году общий оборот холдинга составил более 40 млн евро.
За последние несколько лет ARA Technology Group укрепила позиции за счет присоединения компаний Hedlunds и Milltech, что позволило существенно расширить ассортимент выпускаемого оборудования. В группу входят компании разного уровня, поэтому она может предложить клиентам полный спектр оборудования для строительства лесопильного завода мощностью от 100 до 600 тыс. м3 круглых лесоматериалов в год, а также спроектировать и поставить многопоточные лесопильные линии высокой производительности.
Отличительной особенностью лесопильных линий AriVislanda является возможность раскроя круглых лесоматериалов диаметром от 100 до 700 мм на одних и тех же станках, без необходимости строительства дополнительных цехов для переработки толстомерной древесины. При проектировании оборудования больше внимания уделяется эффективной переработке сортиментов, а не достижению рекордных скоростей подачи сырья. Лесопильное оборудование оснащается системами криволинейного пиления, а также современными устройствами, позволяющими обеспечить оптимизацию распиловки по критерию наибольшего объемного выхода.
Несмотря на то что в России многие предприятия оснащены оборудованием ARA Technology Group, бóльшая его часть была приобретена не напрямую у компаний холдинга, а на вторичном рынке. В последние годы число заказов от российских компаний увеличивается. Одни хотят модернизировать производства, в том числе расширить возможности заводов, дооснастив их оборудованием для строгания и крашения пиломатериалов, а другие ведут переговоры, планируя организовать новые предприятия с использованием оборудования холдинга.
В настоящее время руководство группы компаний рассматривает Россию как перспективно развивающийся рынок. Требования к оборудованию, его производительности, эффективности использования сырья и культуре производства на российском рынке почти такие же, как в Финляндии или Швеции, что позволяет ожидать повышения спроса на современные высокоавтоматизированные заводы, на производстве которых специализируется группа компаний.
Директоp компании С. Gunnarssons Verkstads AB Йорген Гуннарссон: «Представляя продукцию компании, мы постарались сфокусировать внимание посетителей на характерном для нашего оборудования эффективном сочетании надежности и высокой скорости работы линий сортировки сырых и сухих пиломатериалов. На стенде мы продемонстрировали сортировочные линии, отличающиеся высоким инновационным уровнем и одновременно не слишком сложные в эксплуатации, что значительно сокращает расходы на их обслуживание. Фактически, речь идет о совершенно новом поколении оборудования, в котором идеальная синхронизация всех компонентов высокоскоростных систем сортировки пиломатериалов имеет первостепенное значение, и при этом весь процесс отличает высокая динамичность, работа линий более плавная, а главное – более эффективная. Важно, чтобы система работала без сбоев, время подготовки к работе было минимальным.
География наших поставок очень широка, за годы работы мы поставляли высокоскоростные линии сортировки пиломатериалов (до 200+ упоров/мин) для лесопильных предприятий в Северную Европу, а также отдельные виды оборудования далеко за ее пределы, например, в Новую Зеландию. Бесспорно, шведская компания C. Gunnarssons Verkstads AB заинтересована и в российском рынке, и среди наших клиентов уже есть лесопильные предприятия из России.
Мы располагаем оборудованием, которое подходит как для крупных, так и малых лесопильных предприятий, и всегда можем адаптировать наши технологии под индивидуальные потребности заказчика. Компанию C. Gunnarssons Verkstads AB отличает семейная культура, которая способствует стабильному развитию и сохранению хороших взаимоотношений с партнерами и клиентами».
Eberl Trocknungsanlagen GmbH, баварский производитель сушильных установок, представил новую технологию предварительной пропарки древесины в отдельной камере, предотвращающую изменение цвета древесины при вакуумной сушке.
Компания Eberl Trocknungsanlagen GmbH была основана в 1998 году как изготовитель вакуумных камер, предназначенных для сушки древесины твердолиственных пород и хвойных лесоматериалов большого сечения. Компания ориентируется на малые и средние предприятия, перерабатывающие древесину разных пород. Вся продукция производится в Баварии.
За 21 год работы реализовано более 550 единиц оборудования в 27 стран мира. Больше всего поставок осуществлено в Германию, Польшу, Австрию, Италию, Колумбию и Новую Зеландию. В Россию за это время была поставлена всего одна сушильная камера, однако российский, белорусский и украинский рынки представляются руководству компании весьма перспективными, поскольку в этих странах активно вовлекается в промышленное производство лиственная древесина.
Eberl Trocknungsanlagen GmbH производит сушильные камеры с полезным объемом загрузки до 100 м3. Но не обязательно заполнять всю камеру, поэтому можно избежать простоев при накоплении минимальной партии, а также сушить только тот объем древесины, который необходим по производственной программе предприятия.
Поскольку в вакуумных камерах при уменьшении давления понижается температура кипения воды, возможна быстрая и щадящая сушка за счет ускоренного и равномерного испарения влаги из древесины, кроме того, эластичность древесины повышается и обеспечивается низкое энергопотребление (для циркуляции воздуха и испарения воды).
Особенностью вакуумных сушильных камер является также одновременная загрузка древесины разных пород, продолжительность сушки которых примерно одинаковая. Так, например, вместе можно сушить заготовки из дуба и ясеня толщиной 50 мм: приблизительно за 10 дней содержание влаги в них снизится с 40 до 10%.
Помимо вакуумных, компания производит установки для конвективной сушки разных пород древесины. Компактные теплоизолированные контейнеры подходят для размещения таких сушильных камер. На заводе камеры оснащаются высококачественными системами вентиляции, нагрева, увлажнения, а также приборами для измерения влажности среды и древесины. «Система управления, специальное программное обеспечение и наш большой опыт производства сушильного оборудования позволяют сделать из контейнера недорогую сушильную камеру для древесины, характеристики которой мы согласовываем с покупателями», – говорит Александр Шмаглиенко, официальный представитель компании Eberl Trocknungsanlagen GmbH.
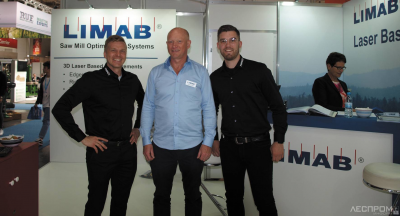
Компания Finnos, имеющая большой опыт производства рентгеновских сканеров для оценки строения и внутренней структуры круглых лесоматериалов, в 2016 году поглотила компанию Bintec, основанную в 1988 году и установившую один из первых в мире рентгеновских сканеров для бревен в 2002 году, и, аккумулировав накопленные знания, продолжает активно развивать собственные технологии. До конца 2019 года количество пущенных на предприятиях лесопромышленного комплекса систем неразрушающего контроля с использованием рентгеновского анализа достигнет 50 единиц, что, по словам представителей компании, упрочит ее позиции в качестве лидера рынка.
Рост стоимости сырья и усиление конкуренции на международных рынках требуют от лесопильных заводов постоянного инвестирования в развитие технологий, позволяющих повышать объемный и качественный выход пилопродукции. По данным компании, в 2018 году в Финляндии больше половины сортиментов перед раскроем оценивается с помощью рентгеновских сканеров Finnos. Такой подход позволяет сортировать пиловочник не только по поставам, но и по качественным характеристикам, требования к которым обусловлены контрактами на готовую продукцию. Поскольку критерии оценки качества круглых лесоматериалов различаются в зависимости от вида и назначения пиломатериалов, менеджмент Finnos решил отказаться от выпуска стандартных сканеров и адаптировать продукцию в зависимости от специфики производства. До выхода компании на рынок под собственным брендом были проведены объемные маркетинговые исследования, включая анкетирование и более 100 личных встреч на нескольких лесопильных заводах. Все системы сканирования были разработаны и изготовлены в соответствии с полученными результатами. Такой подход поспособствовал удовлетворению всех потребностей лесопильных предприятий по оценке круглых лесоматериалов. Современная система использует несколько измерительных технологий с потенциалом для развития.
Рентгеновские сканеры устанавливаются на линии сортировки круглых лесоматериалов и оценивают размеры, форму и внутреннее строение бревен. «Ни одному лесопильному предприятию не удается перерабатывать бревна только высших сортов. Заводы выпускают пилопродукцию разного назначения, и на этапе сортировки устанавливается, какая продукция может быть получена из каждого бревна с максимальной экономической эффективностью. Именно на стадии приемки и сортировки сырья необходимо определять назначение сортиментов, с тем чтобы увеличить выход спецификационной продукции. Мы стремимся подбирать технические решения со сроком окупаемости инвестиций от двух до шести месяцев, как в случае сканеров производства Finnos, установленных на финских предприятиях, – говорит генеральный директор Finnos Йере Хейккинен. – Рыночный спрос на рентгеновские сканеры в настоящее время превышает возможности завода. Очередь на поставку оборудования сейчас больше четырех месяцев. Пуск в Таиланде дополнительного завода к 2020 году позволит удвоить объемы производства и довести выпуск до 40 сканеров в год».
Для того чтобы эффективно использовать полученные на этапе сортировки круглых лесоматериалов данные и в дальнейшем идентифицировать пиловочные бревна в лесопильном цехе, необходимо установить сканер на линии подачи пиловочника в распиловку. На этом участке нужно также использовать рентгеновский сканер, поскольку лазерное сканирование формы сортиментов обеспечивает точность идентификации только 80%. На линии входа в лесопильный цех устанавливается модифицированная версия сканера, задачей которой является оценка формы и основных пороков бревен, это позволяет соотнести бревно с его полной цифровой копией, полученной на линии сортировки по диаметру. По результатам оценки в программном комплексе определяется необходимый угол доворота бревна вокруг своей оси механизмами базирования перед головным лесопильным станком для достижения наибольшего спецификационного выхода продукции.
Оценка круглых лесоматериалов диаметром до 500 мм может проводиться на скорости подачи до 240 м/ мин, которая соответствует производительности современных крупных предприятий. При необходимости скорость подачи увеличивается. Самый большой действующий сканер компании может оценить круглые лесоматериалы диаметром до 700 мм. Сканеры Finnos эффективно работают не только на крупных предприятиях, но и на малых и средних лесопильных заводах, выпускающих от 35 тыс. м3 пиломатериалов в год.
«В ближайших планах компании – выход на российский рынок. Результаты работы в Скандинавии показывают, что запрос на сканеры растет с каждым годом и пользователи уже хорошо представляют, что они хотят получить от установки X-Ray-оборудования, – рассказывает руководитель направления бизнеса в России и странах СНГ Владислав Закатов. – Несмотря на то что в России рентгеновские сканеры пока воспринимают иначе, чем в европейских странах, мы готовы к долгой и ответственной работе с лесопильными предприятиями. В ближайших планах Finnos – организация деловой поездки для руководителей российских заводов по промышленным предприятиям Финляндии уже осенью 2019 года, во время которой они смогут посмотреть X-Ray-оборудование в работе и поговорить со специалистами предприятий, уже эксплуатирующих его. Первые российские лесопильные предприятия, которые будут использовать X-Ray в производстве, получат серьезное конкурентное преимущество на рынке. Представители российских лесопильных компаний заинтересованы в приобретении рентгеновских сканеров и других технических решений Finnos и активно интересовались техническими характеристиками оборудования во время выставки. Finnos рассчитывает, что Россию ждет революция в лесопильной отрасли, которая уже произошла в Финляндии».
Компания Heinola разрабатывает комплексные решения для оснащения лесопильных предприятий и предлагает клиентам полный спектр оборудования. В линейке продукции компании несколько видов лесопильных линий, сушильные камеры и туннели, линии сортировки пиломатериалов разной производительности, а также рубительные машины. Heinola ориентирована на предоставление готовых решений для разных производственных участков, оснащенных необходимой автоматикой, что позволяет клиентам получать готовый лесопильный участок из одних рук.
Новые разработки и технические решения внедряются по мере их появления в текущих проектах. Новинка этого года – триммер для пиломатериалов, повышающий производительность их сортировки, – уже успешно используется на финских лесозаводах.
Одна из особенностей работы Heinola с клиентами – постоянная постпродажная поддержка и помощь в модернизации оборудования в соответствии с изменениями в сырьевом обеспечении на предприятии заказчика, а также консультирование по внедрению новшеств, позволяющих повысить экономическую эффективность установленного оборудования.
Оборудование компании поставляется в Финляндию, Швецию, страны Южной Америки, Японию, Англию, прибалтийские страны и Россию. Российский рынок в настоящее время потребляет уже 30% мощности станкостроительного предприятия. Наиболее значимыми за последние два года проектами стали поставка в Республику Удмуртия полностью профилирующей лесопильной линии мощностью около 500 тыс. м3 бревен в год для компании ООО «ТПК “Восток-Ресурс”», пуск лесопильной линии мощностью около 200 тыс. м3 бревен в год по заказу ООО «НЛК “Содружество”» в Новгородской области, поставка ООО «Устьянский ЛПК» линии быстрой сортировки сухих пиломатериалов и двух блоков из четырех сушильных туннелей каждый, а также поставка двух туннелей на завод «Вельский лес». Срок изготовления новой лесопильной или сортировочной линии от 8 до 12 месяцев, в зависимости от ситуации с заказами.
При производстве оборудования для российского рынка Heinola активно сотрудничает с компанией «Автоматика-Вектор». Разрабатываемые совместно системы автоматизации не только адаптируются под требования каждого клиента, но и позволяют управлять линией на русском языке. Подобная практика распространена и в других странах, где системы управления создаются с привлечением местных компаний.
Опираясь на опыт выставки 2017 года, компания Holtec снова приехала на Ligna с двумя стендами: один был посвящен технологиям лесопиления, другой – производству древесных плит. Представителей компании в этот раз было больше, и они старались предложить гостям как можно больше новых идей, продуктов и услуг. В рамках темы Industry 4.0 был представлен широкий ассортимент решений по удаленному контролю и обслуживанию техники, включая системы виртуальной реальности, компьютерное моделирование, онлайн-каталоги запчастей.
«Новые рынки, меняющиеся условия окружающей среды, стремление клиентов экономить время и средства – вот условия, в которых бизнес существует сегодня, – сказал генеральный директор Holtec GmbH & Co. KG Александр Гебеле. – Мы готовы к этим вызовам и постоянно повышающимся требованиям в деревообрабатывающей промышленности, мы помогаем клиентам эффективнее эксплуатировать оборудование и обеспечивать контроль всех систем. Так, с помощью дистанционного обслуживания RemotePlus4.0 мы налаживаем коммуникацию нашего сервисного инженера с техническим специалистом на заводе клиента. Техник, “вооруженный” очками дополненной реальности, передающими данные, изображения и аудиосигналы, в режиме реального времени осматривает узлы машины и консультируется с удаленным сервисным центром».
Еще одна важная тема из будущего и для будущего – это удаленный мониторинг работы всего завода. Речь идет об отслеживании состояния и эффективности работы всей цепочки оборудования с детальной визуализацией процессов. Совместно с Siemens специалисты компании Holtec разработали приложение HOLtrack4.0, которое позволяет из любой точки мира в режиме реального времени передавать, записывать и анализировать машинные данные. Модульное устройство дает возможность выстраивать систему в разных комбинациях – согласно потребностям клиента.
Цифровой симулятор Simtec – инструмент моделирования производства, благодаря которому можно составить все цепочки оборудования, выбрать оптимальную комплектацию для достижения необходимых параметров, прежде чем воплощать ее в жизнь и делать инвестиции. Решения Holtec 4.0 интегрированы с виртуальным магазином, так что клиент может не только контролировать работу своего завода со смартфона или планшета, но и оперативно дооснащать производство.
Попробовать все инструменты в работе можно было на стенде компании в специальной зоне DigiCube.
Еще одна важная проблема лесопильных технологий, которую акцентировала Holtec, – это дальнейшее развитие системы транспортировки бревен без цепей и смазки chainless, которую компания впервые представила более 10 лет назад, установив новые стандарты оптимизации и снижения износа и эксплуатационных расходов. Продемонстрированные новейшие разработки в этой технологии позволяют не только сохранить оборудование, но и существенно повысить скорость его работы.
Оборудование Holtec работает по всему миру. Есть в портфеле заказов компании и проекты в России, один из недавних – новое производство MDF на Павловском ДОКе в Алтайском крае.
Директор московского представительства словенской компании Ledinek Engineering d.o.o. Ольга Осинова: «За последние годы компании Ledinek удалось получить признание на рынке в качестве эксперта по производству оборудования для массивной клееной древесины, а также стать поставщиком оборудования, предлагающим комплексные решения под ключ. Наряду с представленными на выставке машинами – это прежде всего установка для сращивания на мини-шип Kontizink и пресс для соединения ламелей в шип, фрезерный станок Rotoles для калибрования ламелей, высокопроизводительная торцовочная установка X-Cut и пресс для склеивания массивных стеновых панелей X-Press, – компания поставляет также механизмы, необходимые для обеспечения производственного процесса. В настоящее время именно возможность предложить комплексные решения позволяет нам оставаться лидерами в производстве оборудования для CLT. Компания работает сейчас над десятым по счету проектом завода CLT, в этот раз он будет реализован в России на площадке Сокольского ДОКа (входит в состав холдинга “Сегежа Групп”), пуск производства планируется на конец 2020 года. Это будет первая линия по производству панелей CLT в России, причем самая передовая в мире – в ней будут воплощены все самые современные разработки инженеров нашей компании».
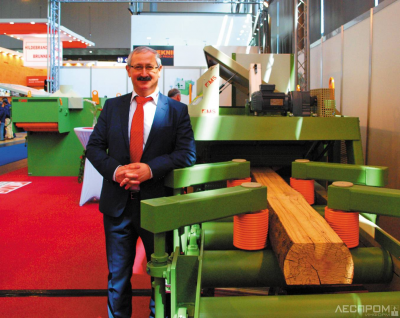
Семейная компания MS Maschinenbau из небольшого немецкого городка Фишбек хорошо известна за пределами Германии как производитель круглопильного лесопильного оборудования для малых и средних предприятий. Более 85% продукции компания экспортирует. Оборудование MS Maschinenbau работает уже в 46 странах.
До 2009 года значительная часть оборудования поставлялась на российский рынок. Многие лесопильные линии, выполненные на базе брусовального станка UBS, работают по всей стране – от Ленинградской области до Комсомольска-на-Амуре. Но после экономического кризиса ситуация изменилась: спрос в России на лесопильные линии для малых и средних предприятий снизился, хотя последние несколько лет ситуация стала улучшаться.
В ответ на изменения экономической ситуации в мире MS Maschinenbau значительно расширила направления экспортных продаж. В настоящее время компания поставляет оборудование в Российскую Федерацию, Республику Беларусь, на Украину, в Польшу, Румынию, Венгрию, Италию, Португалию, страны Балтии, а также на активно развивающиеся рынки Южной Америки – в Парагвай, Перу, Венесуэлу, Чили, Коста-Рику. Активно осваивается африканский рынок. Уже вторая лесопильная линия MS Maschinenbau пущена в эксплуатацию в Зимбабве.
Высокая скорость освоения новых рынков, где создаются малые и средние лесопильные предприятия, обусловлена не только надежностью и производительностью оборудования с брендом «Сделано в Германии», но и простотой технического обслуживания станков. Использование в конструкции стандартизированных элементов позволяет быстро обеспечить в любой стране техническое обслуживание оборудования. Обучение персонала базовым навыкам эксплуатации проводится на стадии монтажа станков сотрудниками MS Maschinenbau.
На выставке Ligna 2019 компания представила свои проверенные двухвальные круглопильные станки для распиловки бревен DBS и брусьев HNS-2. По мнению руководителя продаж Александра Рабаева, «в сегменте малых и средних предприятий видна активная тенденция внедрения технологий двухвального раскроя круглых лесоматериалов. Двухвальная конструкция, несмотря на более высокую стоимость, за счет применения пильных дисков меньшего диаметра позволяет уменьшить до 25% толщину распила. И при годовом объеме распиловки 20 тыс. м3 это обеспечит увеличение полезного выхода до 600 м3 в сравнении с работой одновальной конструкции. Кроме того, двухвальная конструкция позволяет сократить потребление электроэнергии, а обслуживание пильных дисков меньшего диаметра не столь затратно».
Головные лесопильные станки, в зависимости от диаметра перерабатываемых круглых лесоматериалов, оснащаются двигателями разной мощности, что обеспечивает раскрой сырья диаметром до 560 мм. При преимущественной распиловке тонкомерной древесины для экономии электроэнергии могут быть установлены верхние двигатели меньшей мощности, поскольку на них обычно приходится менее 40% общей нагрузки.
Еще одним направлением развития компании стало совершенствование конструкции кромкообрезных станков, которые оснащаются двумя или тремя подвижными пилами для рационального раскроя пиломатериалов и увеличения объемного выхода пилопродукции. Для повышения эффективности работы обрезного участка в компании разработаны собственные системы автоматизации и механизации.
Представители MS Maschinenbau отмечают, что за последние несколько лет предпочтения потребителей значительно изменились: «Заказчики стали подходить к выбору лесопильного оборудования более расчетливо и готовы увеличить инвестиции для повышения объемного выхода. Все больше предприятий хотят иметь возможность раскроя короткомерного сырья длиной от одного метра. Это связано с удорожанием
сырья. В распиловку вовлекается балансовая древесина, а также бревна с большим сбегом или кривизной, которые еще несколько лет назад просто выбраковывались. Сегодня небольшие компании не могут себе этого позволить, и такие сортименты раскряжевывают и пускают в распиловку».
Компания Renholmen нацелена на выпуск скоростных и высокоточных систем для сортировки пиломатериалов, ее инженеры достигли гарантированной производительности линий 240 досок в минуту, что позволяет использовать их на самых современных лесопильных предприятиях.
В лесопромышленном комплексе Скандинавии, на который преимущественно ориентируется менеджмент Renholmen, много крупных заводов, заимающихся не только распиловкой, но и строганием пиломатериалов. Кроме того, многопоточные лесопильные предприятия все больше используют короткомерную древесину длиной от 2,7 м, применяя для всех пиломатериалов одну сортировочную линию. Многие заводы специализируются на выпуске калиброванных пиломатериалов, что предполагает необходимость оснащения участка сортировки строгальными станками.
Так, недавно Renholmen получила крупный заказ на изготовление линии сортировки сухих пиломатериалов с интегрированной системой строгания стоимостью около 20 млн евро. Для того чтобы строганые пиломатериалы не повредились при составлении штабелей для отгрузки, все карманы (а их в линии 16) сделаны горизонтальными. Полную автоматизацию такой линии, помимо конструкторов и программистов компании, обеспечивают инженеры Siemens, которые по заказам Renholmen разрабатывают индивидуальные электронные системы.
Увеличение производственной мощности линий сортировки пиломатериалов требует совершенствования узлов подачи и торцовки сортиментов, которые также должны работать с высокой производительностью. Инженеры компании разработали новый штабелер с тремя парами вил, позволяющий укладывать в пакет до 19 слоев пиломатериалов в минуту. Также разработаны специальные штабелеры, позволяющие складывать сушильные пакеты нестандартных размеров для размещения на железнодорожных вагонетках, которые используются при сушке пиломатериалов в туннельных камерах.
Несмотря на то что оборудование компании весьма дорогостоящее ввиду полной автоматизации и постоянного внедрения новых технических решений, завод загружен заказами до 2021 года. На выставке Renholmen представила несколько новинок как оборудования, так и программного обеспечения. Посетители стенда могли ознакомиться с техническими характеристиками нового электрического триммера и автоматической системы упаковки пиломатериалов в защитную пленку.
Программное обеспечение сильно изменилось. Управление сортировкой пиломатериалов теперь осуществляется с помощью новой централизованной цифровой системы комплексного управления частотными преобразователями, сервоприводами и поворотными устройствами линии, интегрированной с новой системой автоматизации, разработанной совместно с компанией Siemens.
По словам официального представителя ARA Technology Group AB в РФ Андрея Школяренко, компания Renholmen рассматривает Россию как потенциально интересный рынок, но единой стратегии продвижения в стране пока не выработано. Это прежде всего связано с тем, что российским потребителям всегда представляли скоростные и полностью автоматизированные линии компании только для крупных лесопильных предприятий, тем самым существенно ограничивая возможный рынок сбыта, а вследствие их высокой стоимости потребители предпочитали ввозить бывшие в употреблении линии Renholmen, выпущенные 20–30 лет назад.
Ориентируясь на шведский опыт, линии сортировки пиломатериалов Renholmen устанавливаются на заводах, выпускающих не менее 50 тыс. м3 пиломатериалов в год. В российских условиях, учитывая отсутствие участков по строганию и дальнейшей глубокой переработке пиломатериалов, следует говорить о рентабельности оборудования при производительности 100 и более тыс. м3 пиломатериалов ежегодно. В настоящее время компанией принято решение о создании новой линейки оборудования для средних лесопильных предприятий по меньшей стоимости. При этом на этапе проектирования закладывается возможность их быстрой и простой модернизации с ростом производительности лесопильного участка.
Рассказывает начальник отдела сбыта по Восточной Европе Serra Maschinenbau GmbH Вячеслав Филатов: «На Ligna 2019 я ношу фирменную куртку с надписью “Wintersteiger team” и традиционную красную бейсболку Serra – это тонкий намек на весьма серьезные обстоятельства. И наша главная премьера в этом году: Serra впервые выступает на главной отраслевой выставке в Ганновере как часть группы компаний Wintersteiger. Хотя слияние произошло еще в январе, официальное объявление состоялось в марте, а многим своим клиентам мы сообщили новость только здесь. На самом деле наши компании успешно взаимодействуют очень давно, около 20 лет. В частности, на мощностях Wintersteiger производятся пилы для нашего оборудования, а также разрабатывается инструмент для специальных заказов (особые формы зубьев, углы резания). Наконец, бизнес-сотрудничество переросло в объединение, которое, на мой взгляд, дает нам много плюсов. Во-первых, мы стали составной частью крупного машиностроительного концерна, получив доступ к его ресурсам. Во-вторых, имея за спиной такую внушительную поддержку, Serra сможет еще полнее реализовать свой потенциал по производству лесопильных линий. Руководство Wintersteiger по достоинству оценивает наши достижения, а 2018 год стал для Serra особенно успешным, и будет всемерно помогать развитию этого направления. Для нас все отчетливее проявляется тренд превалирования стационарного лесопиления над мобильным: в последнее время мы продаем до 70%–75% стационарных станков. Теперь совместно сможем из одних рук предложить клиентам полный комплект оборудования для переработки древесины. Уверен, производители паркета по всему миру обрадуются новому союзу, ведь с помощью Serra можно будет получить из круглого леса заготовку, которую в дальнейшем превратит в готовую продукцию оборудование Wintersteiger.
Мы рады, что стали членами большой семьи Wintersteiger, сохранив свое имя и “родной” красный цвет, давно заслужившие отличную репутацию на рынке.
Что касается машин, представленных в экспозиции Serra, то в этот раз мы решили сделать акцент не на новейших разработках, а на усовершенствовании наиболее популярных моделей. Если говорить о новинках, здесь мы показываем компьютерные системы и ПО, обеспечивающие гораздо более быстрое и четкое позиционирование. Даже от маленьких улучшений сегодня можно получить большой экономический эффект при эксплуатации промышленного оборудования.
На выставке мы представлены двумя стендами (а с учетом Wintersteiger – четырьмя!): на открытой площадке в работе демонстрируется мобильное оборудование (в том числе Alpina KE90, одна из самых продаваемых моделей фирмы, и другой бестселлер – ME110 – в комбинации с высокопродуктивным многопильным станком CS600), а в павильоне выставлено стационарное оборудование – многоголовочный делительный ленточнопильный станок МК402, обновленные XE135 и XE160 из серии “Африка” и др.
Думаю, что слияние Wintersteiger и Serra в скором времени даст результаты, которые мы с удовольствием продемонстрируем на следующей выставке Ligna. Сотрудники обеих компаний нацелены на позитивные изменения. Приходите – и вы увидите много новинок с неизменным качеством Serra!»
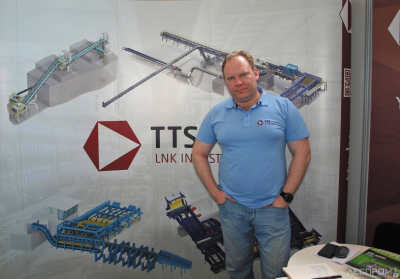
Латвийская компания TTS входит в холдинг LNK Group, который занимается инжинирингом, производством и строительством, а также развитием проектов в сфере недвижимости. В 2007 году в холдинге решили запустить производство систем механизации для деревообрабатывающих и целлюлозно-бумажных предприятий.
Предприятие уже имело опыт контрактного производства для известных западных компаний. Оборудование изготавливалось по чертежам заказчика и выпускалось под его же брендом. Так, например, завод TTS долгое время выпускал продукцию по заказу компаний Raute, Dieffenbacher и Andritz.
После экономического кризиса 2009 года, когда у основных заказчиков снизились объемы продаж, TTS стала выпускать продукцию под маркой компании. По мнению менеджмента, бренд делает компанию более устойчивой, поскольку повышает ее узнаваемость на внутреннем и внешнем рынке. В сфере деревообработки предприятие занимается производством линий сортировки круглого леса, комплексных линий окорки и раскряжевки для фанерных и лесопильных производств, линий подачи сырья в цех, а также вспомогательного оборудования для станков и нестандартных машин и механизмов. Освоено и производство систем удаления кородревесных отходов.
Большое внимание в компании уделяется разработке наиболее востребованных автоматизированных систем и линий, работающих без участия человека. Это обусловлено не только кадровым дефицитом, но и стремлением снизить себестоимость производства в долгосрочной перспективе, увеличивая стартовые инвестиции, но возмещая их за счет гарантии стабильности и надежности выполнения технологических операций.
В ТТС значительно усилено подразделение, отвечающее за монтажные и пусконаладочные работы: несколько профессиональных бригад выполняют весь спектр монтажных работ, запуск оборудования и обучение персонала заказчика.
В Санкт-Петербурге открыто российское представительство компании, обеспечивающее оперативное сервисное обслуживание оборудования и снабжение запасными частями клиентов в Российской Федерации.
Сотрудники предприятия последние два года отмечают снижение спроса на оборудование в России, по их мнению, вызванное увеличением внутреннего предложения, а также реализацией в РФ программ по импортозамещению. Если до 2015 года компания почти полностью ориентировалась на российский рынок и тесно сотрудничала с такими известными производителями как «Свеза» и «Илим Тимбер», то в 2016–2019 годах поставки снизились до минимума, хотя TTS постоянно участвует в тендерах на профильных предприятиях.
Компания переориентировалась на европейских потребителей, активно поставляет оборудование на внутренний рынок Латвии и прибалтийских стран, стремительно развивающийся последние годы. «Число деревообрабатывающих заводов в Латвии увеличивается, объем лесосырьевой базы позволяет создать много предприятий. Мы планируем расширение производства, чтобы удовлетворить растущий спрос. На заводе внедряется робототехника, что позволяет повысить качество продукции и производительность. Заводской портфель заказов сформирован на 1,5 года вперед, и сегодня одной из основных задач компании является сокращение сроков ожидания для заказчиков», – говорят в компании.
Турецкая компания Üstünkarli представила оборудование, предназначенное для работы с высококачественной лиственной древесиной элитного сегмента. Проект заказал клиент из Германии, производственная линия будет установлена на границе Франции и Германии. Линию составляют следующие элементы:
1. Наклонная гидравлическая каретка для бревен, оснащенная 2D-сканером и управляемая с помощью специального ПО для оптимизации. 2. Фрезерный блок (кантер) с управлением скоростью.
3. Наклонная гидравлическая вертикальная пилорама с управлением скоростью.
4. Автоматическая кромкообрезная линия с фрезерным блоком.
Для всех операций на линии обрезки (включая обработку отходов) требуется только один оператор.
В системе управления предлагаются два рабочих режима: программный дает возможность оптимизировать распиливание досок по ширине, заранее запрограммировав необходимый размер, а режим качества позволяет распознавать и распределять сырье по качеству с помощью лазера – дефекты маркируются и удаляются. «Выставка произвела самое благоприятно
е впечатление и оправдала наши ожидания, – поделились специалисты Üstünkarli. – Есть интересные контакты, есть сделки, которые заключили прямо там, уже запланированы новые деловые встречи с потенциальными заказчиками, знакомство с которыми состоялось на Ligna».
Для компании Vollmer выставка Ligna является не менее значимым мероприятием, чем выставка GrindTec – международный форум по шлифовальному оборудованию. Традиционно компания занимает очень большой стенд, на котором представители деревообрабатывающих предприятий могут увидеть весь спектр оборудования для подготовки дереворежущего инструмента, за исключением станков для правки ленточных пил, от изготовления которых пришлось отказаться несколько лет назад из-за падения спроса.
Из последних новинок на выставку Vollmer привезла оборудование для производства инструмента из цельного твердого сплава, а также усовершенствованную технологию обработки алмазных фрез: использование нового генератора и специально разработанного программного обеспечения позволило увеличить скорость обработки без снижения качества режущей кромки инструмента.
Исследования и конструкторские разработки компании относятся к сфере информационных технологий, поскольку без их развития дальнейшее качественное улучшение подготовки инструмента к работе представить довольно сложно. В этом году закончено внедрение технологий «Индустрии 4.0». Станки оснащаются программными продуктами, собирающими информацию об их работе для оптимизации производственных операций и выявления причин простоев. Консолидация информации с разных предприятий позволяет определить среднюю скорость выполнения каждой операции, а при отклонении от полученных значений выявить ошибки или, наоборот, получить информацию о способах повышения производительности, внедренных в отрасли.
Специалисты Vollmer отмечают рост числа посетителей из России, Белоруссии, Украины и Молдавии, которые хотят не только узнать о возможностях оборудования, но и получить консультации по правильной подготовке дереворежущего инструмента. Уровень квалификации специалистов крупных российских предприятий постоянно повышается, и много вопросов у них вызывают новинки заточного и напайного оборудования, которые, несмотря на высокую стоимость, довольно быстро окупаются за счет продления срока службы и повышения стойкости режущего инструмента. Выставка предоставляет возможность общения с конструкторами и проектировщиками оборудования, то есть получения необходимой обратной связи.
На российском рынке компания Vollmer представлена уже более 100 лет. Первые станки были завезены в Россию в 1917 году. Основные поставки оборудования были осуществлены в 80–90-е годы прошлого века. Специалисты компании отмечают, что в последние несколько лет предпочтения клиентов из России сильно изменились. Если до 2010 года, ввиду относительно высокой стоимости оборудования, обусловленной качеством исполнения, большинство клиентов были заинтересованы в приобретении самых простых модификаций, без дополнительных опций, то сейчас зафиксирован тренд инвестирования в самые передовые технологии. Все чаще предприятия отказываются от самостоятельного технического обслуживания, поскольку при этом велик риск ошибок, снижения качества работы станка, а неквалифицированный ремонт может привести к длительным простоям оборудования, которые перекрывают экономию на вызове сервисного инженера. Кроме того, некоторые предприятия стали приглашать специалистов компании не столько для проведения сервисного осмотра, сколько для того, чтобы наметить направления модернизации заточного участка. Наиболее распространен отказ от применения СОЖ в пользу масляного охлаждения, которое позволяет не только увеличить рабочий ресурс оборудования, но и избежать перегрева инструмента во время обработки.
В 2014 году технология производства станков претерпела серьезные изменения. Vollmer отказалась от гидравлических узлов, и все оборудование с тех пор оснащается ЧПУ. Станки изготавливаются на новой унифицированной базе, поэтому снизилась их стоимость. Разработана новая линейка недорогих станков, которые выпускаются на дочернем предприятии компании в Китае.
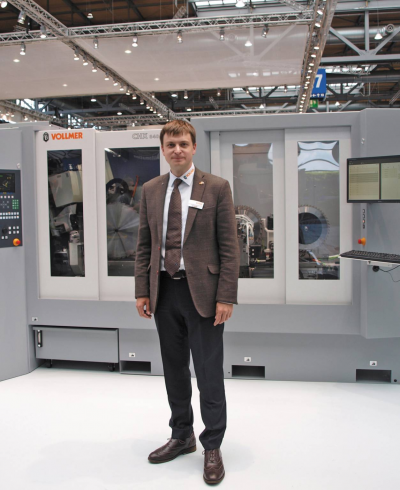
Одной из основных проблем деревообрабатывающих предприятий России является недостаточная квалификация работников, считает специалист компании Vollmer Андрей Федоров: «Несмотря на то что работать на станке Vollmer не слишком сложно – операторы должны просто следовать разработанным алгоритмам – многие просто не хотят воспринимать новую информацию. При отсутствии у работников профильного образования и специальных знаний о резании древесины, объяснять им, какие должны быть углы заточки, а также проводить общее обучение – задача поставщиков режущего инструмента, однако эти функции нам часто приходится брать на себя, хотя это совсем не наш профиль. Приходится рассказывать, какие угловые параметры должны быть у инструмента для распиловки той или иной породы древесины, хотя в нашей компетенции только решение вопросов, как их добиться на станке с максимальной скоростью и эффективностью. Качеством и стойкостью инструмента должны заниматься его поставщики».
Фирма Wema Probst (Wolfgang Hofmann GmbH) является известным специалистом по производству станков и оборудования для эффективной переработки тонкомерного лесоматериала (Ø от 4 до 40 см и длиной от 1 до 14 (16) м). Все оборудование конструируется и производится исключительно в Германии – в г. Фрайгерихт, в 54 км от Франкфурта-на-Майне.
В Ганновере Wema Probst представила станок для оцилиндровки лесоматерила тип RHM160 I-H и окорoчный станок тип WPSS 200, а также станки для последующей обработки отфрезерованного или окоренного материала, изготовления элементов «садовой архитектуры», столбов электропередач, деталей рубленых домов, пиломатериалов и бруса.
Специалисты компании были рады приветствовать на своем стенде уже хорошо знакомых, а также новых гостей из различных стран мира (Канада, Мексика, Колумбия, Бразилия, Португалия, Южная Африка, Испания и др.), а также из Белоруссии и самых разных регионов России – от Урала и Коми до Сибири и Дальнего Востока.
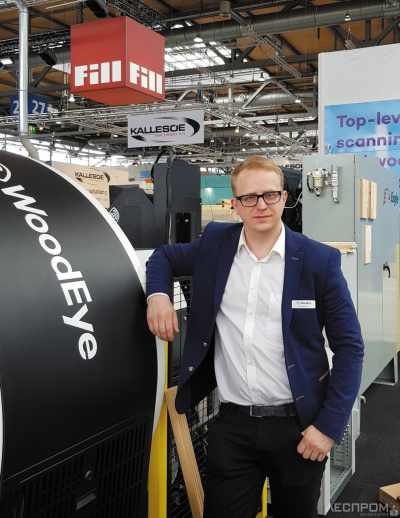
Компания WoodEye представила апробированные автоматизированные решения для линий сортировки ламелей, выполненные по технологии «Индустрия 3.0» и обеспечивающие сканирование и оценку качества пиломатериалов с высокой скоростью. Линии пакетирования на базе оборудования WoodEye позволяют оценивать до шести досок в секунду.
Еще одной новинкой выставки стала разработанная инженерами компании новая торцовочная пила Talon Cross Cut, оснащенная безредукторными серводвигателями с сегментированной системой привода, обеспечивающая возможность быстрого ускорения, точного раскроя и замедления инструмента.
Наибольшее количество поставок оборудования WoodEye приходится на европейские рынки. «Российский рынок еще не в полной мере оправился от последствий экономического кризиса 2014 года. Интерес к оборудованию из России есть, но пока в сегменте деревообрабатывающего производства у большинства компаний нет возможности инвестировать в развитие производства. В нынешних экономических условиях уверенно себя чувствуют только лесопильные предприятия, которые платят заработную плату в национальной валюте и приобретают сырье за рубли, а продукцию реализуют на экспортных рынках, получая выручку в долларах или евро. Вместе с тем крупные лесопильные компании в России по ряду причин не готовы перейти на глубокую переработку древесины. Кого-то останавливает негативный опыт прошлых лет, кто-то не хочет открывать новые предприятия, поскольку при высокой рентабельности лесопиления не испытывает потребности в диверсификации производства», – считает региональный менеджер по продажам в Восточной Европе Эрик Лильенгрен.
Тем не менее за последние два года подписано несколько контрактов, по которым сейчас осуществляются поставки оборудования. По мнению менеджмента компании, значительный интерес представляет развитие мебельных и паркетных производств в южной и центральной России, откуда в последнее время выросло количество запросов на современное сканирующее оборудование.
Еще одна причина, сдерживающая поставки современного автоматизированного оборудования на российский рынок, – это плохое кадровое обеспечение деревообрабатывающих предприятий. Необходимо повышать общий уровень образования населения. Для полного раскрытия потенциала современных высокопроизводительных сканирующих линий, работники должны не только обладать знаниями в области древесиноведения, но и иметь высокую инженерную подготовку, хорошо знать математику и иностранные языки. Специалисты высокого уровня в России есть, но их не так много, а кроме того, высококвалифицированные кадры сложно привлечь к работе на деревообрабатывающих предприятиях, которые обычно расположены в отдаленных поселках.
Компания обучает персонал предприятий клиентов при промышленном внедрении на них современных технологий, но, по мнению Эрика Лильенгрена, для качественных изменений в отрасли необходимы комплексные усилия, как профильных вузов, так и станкостроительных компаний и отраслевых ассоциаций. Подготовку кадров следует проводить не в форме локального обучения операторов силами одной компании на каждом участке производства, а путем разработки и внедрения комплексной программы обучения работе с современным оборудованием в профильных вузах. В России сегодня эти стандарты есть на бумаге, но они не реализуются.
По многолетней традиции компания Zaffaroni из города Турате (провинция Комо, Италия) демонстрирует на выставке свои лучшие разработки в области поперечного многопильного раскроя.
Последней новинкой производителя стал многопильный станок для поперечного раскроя с верхним шпинделем серии MSR-TR. Как и в предыдущей, хорошо известной и успешной серии MSR, в станках новой серии применяется шпиндель держателя инструмента с возможностью поперечного раскроя деталей до 1900 мм.
Новая серия MSR-TR соответствует всем требованиям поперечного распила при промышленных объемах обработки элементов разной формы из разных материалов, уже облицованных декоративной пленкой. Приводные подрезные устройства обеспечивают оптимальный распил без образования сколов при удалении инструмента, особенно при распиле деталей сложной формы с самыми трудными для обработки покрытиями.
В развитие темы инноваций представители компании также сообщили о продолжающемся обновлении серии обрабатывающих центров STM. Недавно серия обогатилась сверлильным устройством модели 5f2 с автономными вертикальным и горизонтальным шпинделями для сверления в том числе сквозных отверстий при производстве деталей подвесной и корпусной мебели.