Гремячинский ДОК отметил первый юбилей
Настроение по-прежнему оранжевое
Время летит быстро. Нашему доброму знакомству с Евгением Бакуновым, возглавляющим Гремячинский ДОК, уже три года. Во время состоявшегося в центральном московском офисе компании интервью у нас как-то сама собой возникла тема «оранжевого настроения», которая получила неожиданное, а вместе с тем и закономерное продолжение.
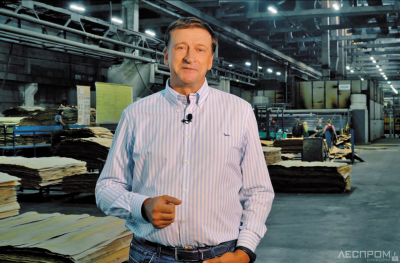
«У нас много новостей, – значилось в приглашении, пришедшем по электронной почте от Евгения Бакунова. – Инвестпроект официально завершили. Развиваемся: закупаем лесозаготовительные комплексы, расширяем производство и т. д. Начинаю проект по редизайну завода в рамках “оранжевого настроения”. Для изменения облика производства пригласили пермских дизайнеров. Сейчас проект обсуждаем. Приглашаю в гости!»
А когда выяснилось, что в 2018 году предприятие отмечает свой первый, 10-летний юбилей, удержаться от того, чтобы полететь в Пермь и посмотреть, чем живет завод сегодня, стало попросту невозможно.
Деревообрабатывающий комбинат расположен в г. Гремячинске, это почти 200 км по автодорогам от столицы Пермского края. Маршрут пролегает по живописнейшим ландшафтам, ближе к цели моего путешествия становящимся все более гористыми – не только своими лесами, пещерами и водопадами, но и горнолыжными курортами известны эти места. Вслед за колонной лесовозов подъезжаем к воротам с табличкой «Гремячинский ДОК», где меня уже встречают руководители комбината.
Шаг за шагом
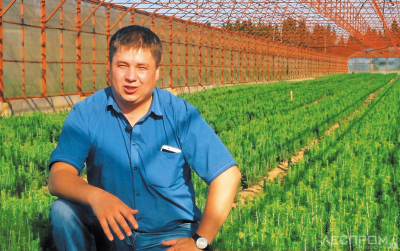
Надо сказать, оранжевых заводских корпусов я не увидел, и, видимо, уловив немой вопрос, учредитель компании объяснил: «Я вовсе не передумал придать комбинату радостный апельсиновый цвет. Как раз сейчас команда дизайнеров работает над концепцией редизайна. А до той поры мы по мере сил украшаем и улучшаем то место, где работаем и живем».
Короткой экскурсии по производству хватило, чтобы понять: так оно и есть. И в том смысле, что процесс преобразования еще только начинается, и в том, что начинается он весьма активно. Причем в первую очередь подумали не о зданиях и машинах – о людях: отремонтированы комната приема пищи, комната мастеров в основном цехе, помещения для отдыха иногородних рабочих (более 300 м2), душевые, комнаты отдыха водителей и санузел в гараже, организованы места отдыха и курения. Комнаты отдыха стали первыми ласточками в стиле «оранжевого настроения». Светлые, с яркими стенами и плакатами-мотиваторами на них, празднично-новенькой мебелью и электротехникой, позволяющей приготовить чай или небольшой перекус.
«Разрабатывая единый дизайн, общий стиль завода, начинаем со средств наглядной агитации и оформления бытовых комнат. – говорит Евгений Бакунов. – постепенно распространим этот опыт на другие помещения».
«Мы последовательно занимаемся улучшениями, которые, может, и незаметны постороннему глазу, но очень и очень важны, – подчеркивает руководитель производственного подразделения Азат Тимергалеев. – Заменили светильники в административно-бытовом корпусе и основном цехе на светодиодные – всего более 300 штук. Результат того стоил: освещение теперь отличное! Заменены входные двери, ворота в цехе, более 150 м2 окон. Проведен ремонт крыши: капитальный – на 4000 м2 и текущий – на 13 000 м2».
В рамках реновации были отремонтированы и полностью укомплектованы оборудованием и инструментом слесарные мастерские. Установлена современная вытяжная система. И опять-таки видно, что не забыли об эстетике, делалось все с умом и любовью: слесарка не просто оснащена, она удобна и красива.
Реновация имущественного комплекса комбината потребовала более 23 млн руб. инвестиций только за последний год.
«Дайте срок и средства, – смеется Евгений Бакунов, – и скоро завод будет не узнать. Внедряем элементы бережливого производства. Уверен, в этом поможет и коллектив: мы организовали регулярные собрания по развитию предприятия и специальную доску предложений, на которой любой работник может высказать свое мнение о проблемах и возможностях их решения, предложить те или иные улучшения. Из 37 предложений, поступивших за последнее время, 11 уже внедрены. Причем касаются они порой очень серьезных и важных вещей. Например, результатом подобной рационализации стала недавняя установка и пуск в эксплуатацию транспортера-накопителя к форматному станку для фанеры. Это позволило снизить количество перемещений плиты в технологическом процессе, а также моторесурс автопогрузчиков.
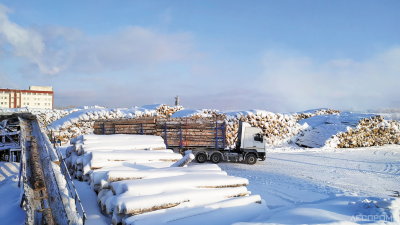
Кроме того, мы создали "уголок качества". Толчком для этого послужила фраза, услышанная на учебе для руководителей: "Мы делаем все, чтобы добиться качества, но занимаемся качеством сверху вниз". То есть производственным браком озабочены прежде всего те, кто управляет процессом, а без непосредственного участия работников это не приведет к нужным результатам. И мы решили устроить такое место, где все работники смогут посмотреть свои ошибки и недочеты, понять, как и почему появляется брак. Все возможные дефекты – рядом с рабочим местом. Причем мы отмечаем по всем видам брака, сколько мы теряем на каждом участке – и в штуках, и в деньгах. На самом деле, это еще один элемент японской философии непрерывного совершенствования процессов производства кайдзен, которую мы внедряем на заводе. Все должно быть предельно наглядно: что-то плохо – люди должны это видеть, добились успехов – опять же, пусть "страна знает своих героев".
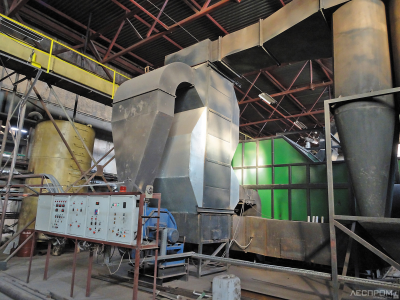
Продолжаем стандартизацию внутризаводских регламентов. За 10 лет работы у нас их накопилось сорок или пятьдесят, сейчас оптимизируем и модернизируем эту систему. Разработали положение конкурса "Лучший по профессии"».
Успех любого деревообрабатывающего производства начинается с качественного сырьевого обеспечения. Рассказывает Азат Тимергалеев: «Породный состав на арендуемых нами участках с соотношением примерно 40/60 хвойных и лиственных. Аренда раскидана очень сильно: с севера на юг 250 км, с запада на восток – 80 км. Участки в пяти разных лесничествах: Лысьвенском, Кизеловском, Горнозаводском, Кишертском и Чусовском. Максимальное плечо доставки сырья около 150 км. Березу используем для собственных нужд. Очень не хватает рынка сбыта мягколиственных пород. Надеемся, что на пермском рынке появится такой потребитель. Нужен баланс потребления древесины. Пока перекос в сторону хвойных пород.
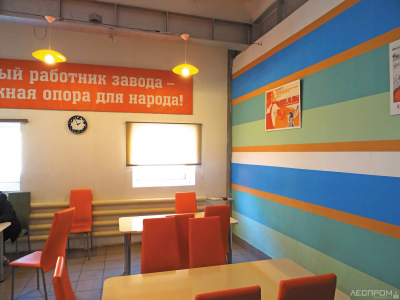
В 2018 году взяли в лизинг три новых лесозаготовительных комплекса Komatsu: харвестер 911XS + форвардер модели 975. Komatsu был выбран поставщиком, потому что предложил самые лучшие условия: машины дали, скажем так, на пробу с выгодной арендной платой – уровня лизинговых платежей. И в случае положительного решения о покупке эта арендная плата зачитывается в общую стоимость. Подходит нам это сотрудничество и в плане сервиса: в Перми у компании есть полноценный сервисный центр, в Сыктывкаре – учебный центр. Кроме того, дилеры компании показали себя очень профессионально. Для вывозки древесины приобрели четыре лесовоза-вездехода "КамАЗ", планируем купить еще шесть. Приобрели и трактор для строительства дорог. Все это позволит нам лучше осваивать имеющуюся расчетную лесосеку. Собственной заготовкой мы покрываем до 60% потребностей предприятия в сырье.
Для контроля и учета лесного фонда активно применяются геоинформационные системы. Использование геоинформационных спутниковых технологий позволяет оптимизировать и значительно повысить эффективность работы в лесу: подбирать участки лесного фонда в эксплуатационных лесах, оперативно контролировать работу подрядчиков, отслеживать и предотвращать незаконные рубки на арендных участках, обнаруживать возгорания в пожароопасный период и планировать совместные действия по их устранению».
Лесной питомник
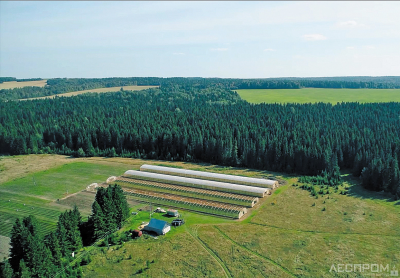
Разумеется, не может быть заготовки леса без его последующего восстановления. Этот вопрос, подобно многим другим, на Гремячинском ДОКе решили самостоятельно и исчерпывающе: для обеспечения саженцами своих и сторонних нужд в 2012 году с нуля построили лесной питомник в деревне Аитково в Лысьвенском районе Пермского края.
«23 августа получили указание от руководства – и уже 27 августа начали строительство, – улыбаясь, вспоминает Азат Тимергалеев. – По-другому у нас и не бывает».
Площадь питомника – 15 га. Площадь парников – 4800 м2. Численность работников – 16 человек (на период посева и выкапывания приходится привлекать жителей близлежащей деревни, и персонал временно увеличивается до 35 человек).
В 2018 году выращено около 2 млн сеянцев сибирской ели (примерно 20% общего объема по Пермскому краю), из них половина пойдет на собственные нужды лесовосстановления, другая – на продажу, для покрытия дефицита лесосеменного фонда в крае. На сегодня это оптимальный объем производства, хотя потенциал питомника составляет 4 млн сеянцев в год, а в дальнейшем возможно увеличение мощностей до 6 млн сеянцев в год (55% общего объема по региону), что позволит полностью обеспечить Пермский край собственным районированным посадочным материалом с хорошей приживаемостью. Площадь посева в 2018 году составила 1,24 га.
«Половину тех семян, которые мы высеиваем, собираем сами с собственного лесфонда, – рассказывает Азат Тимергалеев. – Их сушат, шелушат, сертифицируют, в апреле высеивают в закрытый питомник. Он укрывается пленкой, прогревается. В течение лета сеянцы постепенно адаптируются к окружающей среде, к сентябрю утепление уже не требуется, зимой растения уходят под снег. Высаженные в парнике семена ели за полгода дают прирост, сравнимый с двухлетними саженцами, растущими в открытом грунте. За год вырастают до 5–6 см. Плюсовые семена дают за два года сеянец высотой до 15–20 см».
Аитково – крепкое, развитое поселение с 300-летней историей и почти 1600 жителями, многие из которых не только становятся сезонными сотрудниками питомника, но и вахтовым методом работают на комбинате. А Гремячинский ДОК традиционно участвует в проведении там ряда общественных мероприятий, таких как Сабантуй и День гуся (это, замечу, официальные праздники 59-го региона). Начиная с 2015 года ежегодный «День посадки ели» в мае собирает в Аитково наряду с сотрудниками Гремячинского ДОКа и жителями села представителей Министерств края, руководителей районов, жителей окрестных поселений.
Производство
Официальный слоган Гремячинского ДОКа звучит так: «Настоящие решения для будущего!» А это неизбежно подразумевает постоянное, безостановочное развитие.
Общий объем инвестиций в модернизацию производства в 2018 году превысил 250 млн руб. Помимо приобретения лесозаготовительных комплексов, были установлены и запущены в эксплуатацию конвейер сортировки латофлекса, подъемные столы на вальцах для сушилки, восстановлены два фрезерных станка, приобретены и запущены в рамках программы импортозамещения два многопильных станка российского производства, приобретены две упаковочные степпинг-машины на участок производства латофлекса, запущена новая система аспирации.
Запланирована автоматизация прессов для изготовления фанеры (их два: 16- и 15-пролетный, украинского производства) для снижения влияния пресловутого человеческого фактора.
Пять латофлексных 8-пролетных прессов итальянского производства были приобретены новыми при первоначальном оснащении завода и показали себя отлично: за все прошедшие годы на одном из прессов поменяли одну-единственную пресс-прокладку, в остальном они проработали до первого юбилея завода без серьезных ремонтов и модернизаций. И все же учредитель предприятия задумывается о том, чтобы нынешние пять заменить на два 15-пролетных с более широкими плитами – более производительные. Так и место в цеху можно будет использовать оптимально, и продукцию выпускать эффективнее, и рабочие руки высвободить – а их, чего уж греха таить, не хватает.
Кардинально снижен уровень простоев. Производительность труда на производстве за год увеличена на 8,5%. Всего один пример с участка сортировки фанеры: если раньше четыре работника за смену сортировали 40 м3, то сейчас двое – 30 м3. В 2018 году на сортировке фанеры пустили в эксплуатацию три конвейера. Раньше погрузчиком доставляли фанеру на сортировку, сортировали и снова увозили с участка. При стандартной производительности машина должна была подъезжать каждые три минуты. Теперь такая необходимость отпала – три транспортера на электроприводе решают эту задачу.
Внедрена новая система оптимизации раскроя латофлекса, только благодаря этому экономия материала составит более 30 м3 в месяц. Продолжаются плановые ремонтные работы на рубительной машине и ребросклейках (их в цеху две: высокопроизводительная «японка» Hashimoto и тайваньская «Чинтай», которая в среднесрочной перспективе может уступить место еще одной Hashimoto). 90% всех работ выполнены своими силами.
Экономить более 2,5 млн руб. в год позволяет использование новой рецептуры клея. «Смолы растут в цене опережающими темпами, только за минувший год удорожание превысило 20%, – рассказывает глава компании. – А ведь наше годичное потребление составляет около 6 млн кг, так что задача экономии клеев, оптимизация их состава и качества стоит необычайно остро. Не менее важно и улучшение экологических показателей смол, снижение эмиссии в окружающую среду. В новой рецептуре уменьшено содержание формальдегида. Мы применяем клеевые составы компании "Метадинея", адаптацию рецептуры проводили совместно наши и их технологи».
Использование котлов, работающих на отходах своего производства, и оборудования для производства биотоплива позволило на 100% решить проблему утилизации древесных отходов.
В 2018 году вложили около 3,5–4 млн руб. в обновление котлов, работающих на отходах деревообработки (производитель – «Ковровские котлы»). Поменяли все футуровки и колосники.
«В рамках реализации стратегии импортозамещения стали потихоньку переходить от импортных насосов к отечественным, Валдайского насосного завода. Каждый вчетверо дешевле зарубежного аналога, при этом вполне сопоставим по характеристикам, разве что размером чуть побольше», – говорит Азат Тимергалеев.
Еще про импортозамещение: из шести работающих фрезерных станков на четырех штатные двигатели заменены на российские 3-киловаттные, что позволило снизить цену на каждый из них с 4 тыс. евро до 70 тыс. руб. По мере выработки ресурса будет произведена замена остальных двигателей.
Обновлен автопарк предприятия: приобретены машины «Газель», «Нива», «КамАЗ» с гидроманипулятором, автопогрузчик. Самое новое пополнение транспортной службы – фронтальный погрузчик «Амкодор»: многофункциональная машина за счет смены навесного оборудования может и лес разгружать, и щепу возить, и дороги чистить.
На территории комбината построены две новые АЗС (дизель и бензин). Прежде машины ездили на заправку, а теперь можно залить топливо здесь, что позволяет экономить 750–800 тыс. руб. в год только на амортизации техники. Есть план по созданию газовой АЗС.
Огромная работа была проделана коммерческой службой по стандартизации упаковки фанеры и ЛФ. Внедрена система штрих-кодирования продукции.
Небольшая, но очень интересная новация: на основных технологических участках появилась кнопка вызова погрузчика. После ее нажатия машина должна прийти в течение шести минут, а у водителя погрузчика есть специальные часы, реагирующие на посланный «заказчиком» сигнал.
Продукция
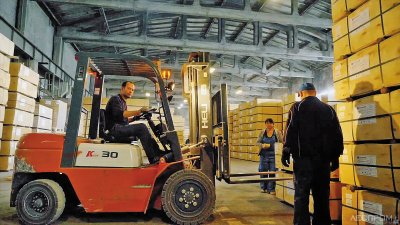
Потребители продукции Гремячинского ДОКа – компании не только из России, но и из стран Европы, Азии и США. География и объемы зарубежных поставок существенно выросли за последние годы: экспорт поднялся с 25 до 40% выпуска, а в будущем его долю планируется увеличить до 60%.
«Однако мы тонко регулируем этот процесс, – поясняет Евгений Бакунов. – Вне зависимости от конъюнктуры нужно поддерживать и внутренний рынок, чтобы нас и дома не забывали.
Все более значимым потребителем нашей фанеры становятся США. Там очень жесткие стандарты по требованиям к фанере – мы долго отрабатывали режимы и рецептуры, чтобы получить то самое "честное" качество, которое требуется на этом рынке. В США популярен "квадрат", и если в Европе фанеру используют для производства мебели, то за океаном она активно применяется в строительстве.
Остающийся после лущения "карандаш" идет на производство древесного угля, который с удовольствием приобретают европейские страны, в основном Германия и страны Балтии, на подъезде к заводу обращает на себя внимание высокая "башня" установки для углежжения. Сейчас там производится около 180 т в месяц, проектная мощность до 500 т. Спрос на этот продукт велик, маржинальность высокая, и руководство завода считает направление древесного угля очень перспективным».
Продукция вывозится с завода автомобильным транспортом. В месяц предприятие отгружает более 100 еврофур готовой продукции.
Контейнеры с экспортной фанерой для Египта и США доставляются в порты Санкт-Петербурга и Новороссийска, далее отправляются покупателям морем.
«Осваиваем новую продукцию, – делится Евгений Бакунов настоящим секретом фирмы (поэтому о нем пока то, что можно сказать). – Затеяли один эксперимент – так еще никто не делал. Выпустили готовую продукцию, показали фотографии зарубежным партнерам, они заинтересовались».
Путь к юбилею
Оставив за спиной шум работающих станков, мы собрались за кофе, чтобы обсудить итоги работы предприятия в 2018 году.
«Досрочно рассчитались со всеми кредитами, – не скрывает радости Евгений Бакунов. – А это значит, что появляется больше возможностей для развития».
В 2018 году по сравнению с 2017 годом комбинат выпустил фанеры на 16%, больше, а латофлекса – на 26%.
«2018 год стал для нас знаковым: мы вышли на второе место по производству фанеры в Пермском крае, по латофлексу – на второе место в России! По годовому плану на 2019 год намечено увеличение выпуска продукции еще на 10–11% в сравнении с уровнем 2018 года», – рассказывает Азат Тимергалеев.
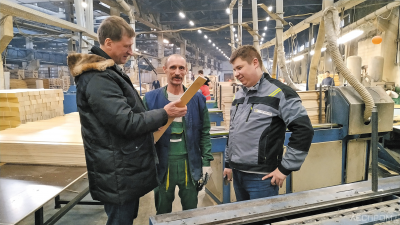
«А если все, что намечено на текущий год, удастся выполнить, рассчитываем еще на 15–20% роста, – добавляет Евгений Бакунов. – В бизнес-план заложено 67 млн руб. инвестиций на развитие. Причем рост 6% по латофлексу может быть достигнут без каких бы то ни было дополнительных затрат, только за счет внутренних резервов по повышению эффективности работы».
Празднование 10-летия комбината для работников организовали 19 декабря прямо в цеху, для этого оформили его, в стиле техно-арт, как сказал Евгений Бакунов: «Поставили сцену, пригласили профессиональных артистов – гостей развлекал "Сиреневым туманом" Владимир Маркин».
Праздник по приглашению администрации завода посетили депутат Госдумы Алексей Бурнашов, представители министерств Пермского края, председатель Гремячинской городской думы Юрий Менде и другие.
Гости угощались горячим чаем с разными вкусностями. Традиционно праздник завершился красочным фейерверком, и его, по сообщениям местного ТВ, было видно в радиусе 20 километров.
Персонал
Количество работников основного производства за последний год выросло с 430 до 490 человек (по штатному расписанию, на комбинате числится 502 сотрудника). Еще 83 человека трудятся на лесозаготовке.
На предприятии работают не только гремячинцы, но и жители других мест – Лысьвенского района, городов Чусовой и Горнозаводск. «Проблема с кадрами большая, – сетует Евгений Бакунов. – А ведь зарплаты у нас выше, чем в городе. Средняя зарплата с 2017 года выросла на 27%. На комбинате это около 23 тысяч, причем оплата у нас сдельная, и если ты стараешься, будешь получать и 30, и 35 тысяч».
На регулярных встречах руководства с персоналом обсуждаются и фиксируются насущные проблемы, поощряются передовики. Жизнь сотрудников стараются сделать интересной – совместные празднования памятных дат, поздравления, подарки, различные конкурсы и коллективные выезды. Только за первые месяцы 2019 года руководство Гремячинского ДОКа организовало для 40 сотрудников и членов их семей поездку на горнолыжный курорт «Такман» (г. Чусовой), поход в цирк (130 человек), на спектакль в театр г. Лысьва, в Кунгурскую пещеру.
Силами Гремячинского ДОКа была устроена детская площадка в городском парке – ее открывал губернатор, и теперь это чуть ли не самое популярное место в Гремячинске, где любят отдыхать и стар и млад.
«На производстве самое главное – вовлечь людей, заинтересовать. Сколько раз приходилось слышать: "Это невозможно..." – а потом начинали делать и все получалось! Нужно только преодолеть два стереотипа: "Мы так никогда не делали" и "Мы всегда делали только так". И дело наладится!» – уверяет Евгений Бакунов.
Инфосреда
Реалии нового времени подсказывают необходимость более активного продвижения в сети Интернет, в том числе при помощи социальных сетей (число участников группы Гремячинского ДОКа «ВКонтакте» увеличилось за год с 400 до 720 человек).
Руководитель предприятия поясняет: «Мы ставим себе отдельной задачей разработку PR-программы о заводе, масштабное и постоянное информирование о нашей деятельности и целях. Еще два года назад мы и не думали о таких вещах, а сейчас развиваем группы "ВКонтакте" и Facebook, размещаем новости объявления, устраиваем опросы и голосования. Цели развития информационной среды – это продвижение, реклама, непосредственное общение».
Для того чтобы лучше понимать, чего же ждут от руководства завода работники, стали проводить интернет-опросы. По первым итогам выяснили: требуется ремонт помещений, обеспечение инструментом и инвентарем, обучение, общественная жизнь и многое другое.
Виртуальная открытость комбината и его администрации подкрепляются доступностью для общественности в повседневной жизни, ведь всегда находятся местные жители, недовольные работой градообразующего предприятия, не очень хорошо понимающие, чем и как оно занимается. Для них проводят экскурсии по предприятию. Привозят на ДОК и детей, молодежь. «Только за последний год больше ста ребят провели по цехам, чтобы они лучше представляли, как же выглядит завод изнутри, чем живет и для чего развивается, где работают их родители и, возможно, спустя годы станут работать они. Мы открыты для горожан и не просто разрешаем такие визиты, а сами приглашаем. Даже предоставляем автобус, для того чтобы люди могли приехать и уехать», – рассказывает Азат Тимергалеев.
Планы на будущее
«У любого бизнеса, серьезного предприятия должна быть не просто цель, а миссия. Без миссии и стратегия плохо выстраивается, – считает председатель совета директоров Гремячинского ДОКа Евгений Бакунов. – Наша миссия: "Мы выпускаем нужную продукцию на предприятии, которым гордимся!"».
В ближайшие два года намечены серьезные вложения в автоматизацию лущильных и сушильных линий, участка прессования. Планируется организация специализированной компании для перевозки древесного сырья и строительства дорог. В среднесрочной перспективе – строительство завода для переработки древесины хвойных пород.
«Обсуждаем с компанией Komatsu возможность установки у нас симулятора для подготовки операторов. Вообще, думаем совместно с Уральским лесотехническим университетом устроить на заводе обучающий центр для работников лесной промышленности. Мы готовы обеспечить базу для практики студентов вуза – возможно, кто-то из них станет работать у нас. Руководство региона поддерживает эту идею и обещает помощь.
Знаете, я даже не ставлю перед собой каких-то практических целей, с выгодой, – улыбается Евгений Бакунов. – Больше всего хочется живой активной деятельности молодых энергичных людей, чтобы тут витал дух науки, просвещения, развития! Я не строю иллюзий, будто мы так решим проблему кадров, мой подход скорее эмоциональный. Но это и не наивность "нью-васюковцев", а корысть более высокого уровня – на перспективу: вместо того чтобы трястись над парой заезжих спецов, создать в своем коллективе, в своем городе такую привлекательную атмосферу, чтобы люди хотели здесь жить и работать. Интерес, вовлеченность порой не менее важны, чем материальные блага».
P. S. И все же не будем забывать об оранжевом настроении, которое некогда стало отправной точкой для этой поездки. Совсем скоро торцевую стену здания заводоуправления должен украсить большой яркий рисунок: руководство предприятия приняло решение провести в городе конкурс художников граффити, победитель которого в буквальном смысле оставит свой след на Гремячинском ДОКе...
Текст Максим Пирус
Фото Максим Пирус, «Гремячинский ДОК»
ЛесПромИнформ №1 (123), 2017 г. Гремячинский ДОК. Оранжевое настроение
Справка
Гремячинский ДОК – предприятие полного цикла, от выращивания посадочного материала и лесозаготовки до глубокой переработки древесины. Укомплектовано современным технологическим оборудованием фирм Fezer Industrias Mecanica, Hashimoto Denki, Vichiatto Chang Tai, «Волев», «Гейзер», Mitsubishi и пр., позволяющим выпускать продукцию, которая соответствует самым высоким международным стандартам качества.
Строительство комбината началось в ноябре 2007 года на площадке бывшего механического завода: была произведена модернизация основного производственного корпуса и возведены новые здания, построены бассейны для гидротермической обработки сырья.
В 2008 году в цеха поступило оборудование из Японии, Швеции, Италии, Словении, Бразилии, России, и 19 декабря производство пустили в эксплуатацию, чтобы уже через полтора месяца отгрузить первую партию продукции в Западную Европу. В конце 2009 года комбинат вошел в федеральный Перечень приоритетных инвестиционных проектов в области освоения лесов. Завод выпускает березовую фанеру марки ФК, соответствующей ГОСТ 3916.1–96, – высококачественный конструкционный материал для мебельного производства и строительства. В год перерабатывается 45 железнодорожных составов фанерного кряжа. Фанера реализуется в России и 11 странах мира. Гнутоклееные изделия (латофлекс) с классом эмиссии Е0 продаются в России и девяти странах Европы. Для переработки отходов налажено производство древесного угля и топливных брикетов RUF. Продукция завода имеет сертификаты FSC, CARB2, Ростест, Made in Russia.
ЛесПромИнформ №1 (123), 2017 г. Гремячинский ДОК. Оранжевое настроение