Облицовывание поверхностей. Часть 2
В предыдущем номере журнала рассказывалось об облицовывании, о том, что такое фанера, шпон, фанера клееная, какие технологические операции выполняются при облицовывании и чем отличается ламинирование от каширования. Следует заметить, что речь шла о терминах «ламинирование» и «каширование», применяемых именно в мебельной промышленности. В других отраслях, например в полиграфии, они имеют совершенно другое значение. Сегодня мы продолжим разговор о кашировании.
Технология каширования
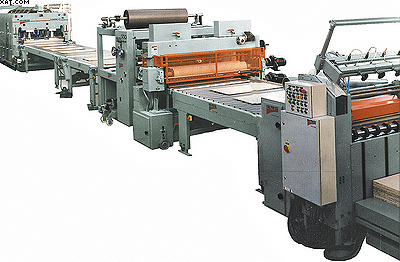
Линия облицовывания пластей щитовых заготовок по способу «Квикстеп»:
1 – станок вальцовый клеенаносящий;
2 – рольганг с игольчатыми роликами;
3 – станок облицовочный;
4 – транспортер ленточный ускорительный;
5 – пресс однопролетный короткотактный
Называть кашированием любой вид облицовывания поверхностей пластмассовыми пленками или другими листовыми синтетическими материалами — неверно. Основным определяющим признаком этого процесса является накатывание облицовочного материала на облицовываемую поверхность в вальцах. Вальцами называется устройство, состоящее из двух приводных вращающихся навстречу друг другу валов довольно большого диаметра с параллельными осями, предназначенное для создания давления на поверхность обрабатываемого материала, пропускаемого между ними. В общем случае при кашировании могут выполняться следующие операции: очистка пластей и кромок заготовок от пыли, предварительный подогрев облицовываемой поверхности (подложки), нанесение клея на пласть плит или заготовок, удаление из него влаги, нанесение отвердителя на слой клея («мокрый по мокрому») или на оборотную сторону облицовочного материала, накатывание рулонного облицовочного материала на облицовываемую поверхность (непосредственно из рулона), разрезание его непрерывного полотна в разрывах между облицовываемыми полноформатными плитами или заготовками, прикатывание облицовочного материала и окончательное отверждение клея.
Все эти операции проводятся одновременно и симметрично для обеих облицовываемых пластей. Одностороннее облицовывание выполняется чрезвычайно редко, поскольку, как правило, приводит к продольному, а иногда и к попутному короблению деталей.
В зависимости от выполняемых операций технологические процессы каширования в отечественной терминологии условно подразделяют на холодное, теплое и горячее каширование (иначе термокаширование).
Холодное каширование
В первом случае используются модифицированные клеи на основе поливинилацетатной дисперсии (ПВАД). На поверхность облицовываемого материала наносится слой клея, и после короткой выдержки на него накатывается облицовочный материал. Затем, после разрезания верхнего и нижнего полотен облицовочного материала по разрывам между заготовками и прикатывания в вальцах, облицованные детали укладываются в стопу для выдержки до полного отверждения клеевого слоя. При этом используется простое пригружение стопы сверху, иногда её помещают в холодный пакетный пресс. Длительность выдержки — около суток.
Первая линия каширования была разработана в конце 1960-х годов немецкой фирмой Adolf Friz, которая сегодня под именем Friz входит в группу фирм Homag.
Эта линия включала в себя двухсторонний щеточный станок, вальцовый клеенаносящий станок, дисковый рольганг и облицовочный станок. В конструкцию этого станка входили устройства для установки рулонов пленки (сверху и снизу), система размоточных валов для подачи полотна пленки к вальцам, вальцы для накатывания пленки на подложку, суппорт сопровождения с автоматическим отрезным ножом, а также ещё одни вальцы — прикатывающие, обеспечивающие окончательное прижатие облицовочного материала к облицовываемой заготовке, прежде всего к её ребрам, где обычно наблюдается отслоение материала после воздействия отрезного ножа.
На подобных линиях и сегодня производится облицовывание пластей заготовок пленками на основе бумаг или пластмассовыми — обычно на основе ПВХ.
Рабочая скорость подачи таких линий практически не зависит от материала подложки и вида используемой облицовки и составляет 20 м/мин и более.
Недостаток такой технологии в том, что вода, содержащаяся в дисперсионном клее, при его отверждении не может просочиться через облицовочный материал и впитывается в подложку, распределяясь внутри плитыосновы и увеличивая её влажность. При этом отдельные частицы мелкоструктурного лицевого слоя древесно-стружечных плит разбухают довольно равномерно, что не оказывает заметного влияния на вид облицованной поверхности. Но разбухание стружек в срединном слое ДСП часто приводит к проявлению на облицованной поверхности дефектов в виде характерного звездчатого рисунка.
Теплое каширование
Для устранения описанного выше дефекта в начале 70-х годов прошлого века была разработана технология каширования, позволившая сократить объем воды в клеевом слое путем её частичного испарения за счет воздействия тепла, аккумулированного на поверхности подложки.
Для этого линия, в состав которой входят те же агрегаты, что и в линию для холодного каширования, дополнительно оснащается камерой нагрева — обычно с использованием инфракрасных ламп, работающих в среднем диапазоне излучения (длина волны 2,5−50 мкм). Нагрев поверхностей осуществляется симметрично, одновременно с обеих сторон заготовки.
Аккумулированное тепло не проникает вглубь облицовываемой плиты, а остается в тонком слое на её поверхности, что способствует быстрому испарению влаги из клея, нанесенного после нагрева, повышению его вязкости и ускорению последующего схватывания.
После теплого каширования детали также укладываются в стопу, которая либо нагружается сверху, либо помещается в пакетный пресс. Но время выдержки под давлением существенно сокращается: в ряде случаев уже через часполтора детали могут быть направлены на дальнейшую обработку.
Скорость подачи у линий теплого каширования такая же, как и у линий холодного, — 20 м/мин и более.
Автоматические линии, оснащенные камерой подогрева пластей перед нанесением клея, выпускаются практически всеми изготовителями оборудования для каширования в Германии, Италии, Испании, на Тайване и в США.
Горячее каширование
Линии горячего каширования отличаются тем, что отверждение клея происходит в результате его непосредственного нагрева через облицовочный материал.
При этой технологии могут использоваться клей-расплав, клеи на основе ПВАД или модифицированные одно- и двухкомпонентные карбамидные клеи, стоимость которых значительно ниже, чем стоимость клееврасплавов или клеев на основе ПВАД.
Линии облицовывания, в которых используются клеи-расплавы, относительно просты: в них не нужен станок для нанесения клея, а облицованная деталь после охлаждения клеевого слоя может сразу же обрабатываться. Но стоимость облицовочного материала с нанесенным на него клеем слишком высока, а термостойкость облицованной поверхности оказывается недостаточной. Поэтому такие линии широкого распространения не получили.
Первая линия горячего каширования в виде комбинации линии холодного каширования и короткотактного однопролетного пресса (о них речь пойдет ниже), объединенных промежуточными ленточными транспортерами, была предложена немецкой компанией GreCon в начале 1970 х. Эта линия, а потом и сам способ получили название «Квикстеп» (Quickstep). Как пояснялось в рекламных статьях фирмы, такое название возникло потому, что «разработанный способ такой же быстрый и элегантный, как одноименный танец». Сначала предполагалось, что на линии будет производиться облицовывание пластей пленками на основе бумаг с заранее нанесенным на их оборотную сторону слоем клея-расплава. Затем комплект агрегатов линии был дополнен вальцовым станком для нанесения обычных клеев. И тогда оказалось, что, сочетая в себе два способа обработки — в вальцах и обогреваемом прессе, линия способна обеспечить облицовывание заготовок из различных плит не только рулонными, но и листовыми материалами.
И уже в конце 70-х годов прошлого века такие линии производились практически всеми крупными изготовителями прессового оборудования (Wemhöner, Bürkle, Friz, Italpresse, Omma, Simiimpianti и др.)
Недостаток линий типа «Квикстеп» в том, что они относятся к циклопроходному оборудованию, то есть совмещают проходную и позиционную обработку. В результате при скорости подачи облицовочного участка (линии холодного каширования) 12 м/мин полный цикл пресса должен составлять не более 12 с. В противном случае подача линии каширования должна будет периодически останавливаться, что снизит качество накатывания облицовки и может привести к обрывам рулонного материала. Вместе с тем при столь коротком цикле пресса на выдержку заготовок под давлением остается всего около 8 с, а этого времени явно недостаточно для полного отверждения карбамидных клеев даже при отверждении под нагревом.
Это обстоятельство обусловило значительное снижение производительности линии типа «Квикстеп» по сравнению с линиями проходного типа — до 6−8 м/мин.
Горячее каширование с вальцовым прессом
Чтобы повысить производительность линий каширования с использованием карбамидных клеев, в конце 1970-х были сделаны попытки осуществить прикатывание облицовочного материала обогреваемыми валами.
Так, первой линией горячего каширования (нем. Heisskaschieranlage) стала установка, совместно разработанная немецкими фирмами Bison и Bürkle, образец которой был продемонстрирован на выставке «Деревообработка-78» в Москве. Она была закуплена для Ленинградской мебельной фабрики № 1, но для её промышленной эксплуатации необходимо было использование специальных клеев, и линия так и не заработала.
Доработанные промышленные образцы таких линий были закуплены для облицовывания полноформатных древесно-стружечных плит для предприятий в Одинцово, Волгодонске, Красноярске и др. Но в них уже применялся технологический процесс облицовывания с нанесением клея «мокрый по мокрому».
При этом в линии использовались два вальцовых клеенаносящих станка, первый из которых наносил на предварительно нагретые пласти плиты клей с добавлением отвердителя, а второй — клей с ускорителем.
Затем плиты поступали на облицовочный станок с тремя вальцами, оснащенными обогреваемыми валами. Первые вальцы осуществляли накатывание облицовочного материала, вторые — тиснением имитировали на поверхности структуру древесины, а третьи прикатывали облицовочный материал, после чего достигалась прочность приклеивания, достаточная для раскроя плиты на заготовки. Раскрой производился сразу, на этой же линии.
В вальцовом прессе происходит лишь линейный контакт прессующего вала с поверхностью заготовки. При этом нагрев клеевого слоя до температуры отверждения через толстый облицовочный материал затруднен, из-за чего при горячем кашировании стараются применять пленки с малой массой — на основе тонких бумаг. Наилучшие результаты достигаются при использовании так называемой японской бумаги — разновидности пергамента, тонкой и мягкой полупрозрачной клееной бумаги без наполнителя, имеющей высокие показатели механической прочности, жиро- и маслопроницаемости и массой 30−40 г/м2 . Она изготавливается в Японии из древесины таких местных пород, как мицумата, гампи, кувака, а также из коры тутового дерева. Но сквозь тонкие пленки на облицованных поверхностях часто проступает структура подложки. Чтобы понизить вероятность появления этого дефекта, немецкая фирма Hymmen в начале 1980 х использовала для предварительного нагрева и выравнивания подложки интересное и эффективное решение — термопрокат. При этом в результате одновременного прокатывания валами (180−200°С) обеих пластей обеспечивается не только их нагрев, но и выглаживание за счет припаивания волокон (ворса) древесины к облицовываемому материалу.
Линии горячего каширования этой фирмы при использовании пленок на основе «японской бумаги» работают при скорости подачи 50 м/мин. Hymmen сегодня является единственным изготовителем оборудования проходного типа для ламинирования пластей, созданного на базе ленточного пресса и используемого, в частности, для облицовывания заготовок паркета. Но об этом в следующем номере журнала.
Сергей НИКИТИН,
компания «Медиатехнологии»,
по заказу журнала «ЛесПромИнформ»