Облицовывание поверхностей. Часть 3
Продолжаем начатую в 5 и 6 номерах журнала серию публикаций, посвященных технологиям облицовывания поверхностей материалов, используемых в мебельном производстве. В предлагаемой вашему вниманию статье речь снова пойдет о ламинировании.
Иллюстрации и таблицы см. в PDF-версии статьи
Термин «ламинаты» в терминологии отечественных мебельщиков сегодня употребляется не только в связи с технологиями производства древесно-
стружечных (ДВП) или древесно-волокнистых плит (ДСП), облицованных термореактивными пленками, но и с многослойными бумажно-слоистыми пластиками и паркетной доской на основе древесно-волокнистых плит сухого способа производства с облицовкой из таких пленок.
Ламинирование в ленточном прессе
Современные бумажно-слоистые пластики за рубежом, а теперь и у нас часто обозначаются аббревиатурой CPL, которая расшифровывается как continuous pressure laminates, что в переводе с английского означает ламинаты (слоистые пластики) непрерывного способа производства.
Для их изготовления используются пленки на основе бумаги, заранее пропитанной термореактивными смолами, реакция полимеризации которых остановлена на промежуточной стадии. Как правило, это меламиноформальдегидные смолы, представляющие собой водные растворы олигомерных продуктов конденсации меламина с формальдегидом, с введенными в них модифицирующими веществами.
Под непрерывным понимается такой способ ламинирования, когда окончательное отверждение смол с одновременным склеиванием рулонных полотен в несколько слоев происходит во время их движения под воздействием высокой температуры и давления.
При этом способе используется двухсторонний ленточный пресс, конструкция которого впервые была разработана немецкой фирмой Held («Хельд») в самом начале 70-х годов прошлого века.
Изначально установка, созданная на основе этого станка, предназначалась для изготовления многослойного кромочного пластика и имела рабочую ширину 600 мм.
Этот пластик состоял из подслоя на основе пропитанной фоновой бумаги, пергаментного промежуточного слоя и лицевого слоя из пленки на основе текстурной бумаги.
В немецком языке такой трехслойный кромочный пластик стал называться Melaminkante — меламиновая кромка.
В 1990-х неквалифицированный перевод с немецкого привел к появлению у нас кальки «кромка-меламин», которая неверна, поскольку кромку плиты облицовывают кромочным пластиком, а не кромкой.
Установка, о которой идет речь (рис. 1), включала в себя устройства для размотки пленки; двухленточный пресс проходного типа для создания высокой температуры и давления, необходимых для обеспечения склеивания и одновременного отверждения смолы; станок для шерохования оборотной стороны полученного пластика и станок для его продольной разрезки на полосы необходимой ширины с устройством, предназначенным для их намотки в рулоны.
Замкнутые ленты, используемые в прессе, — уникальные изделия, изготовленные из гибких полос устойчивой к образованию наклепа высококачественной хромистой стали, имеющих сварной стыковой шов, разделанный до полного совпадения с их поверхностью и не оставляющий следов на облицованной поверхности. В зависимости от исполнения рабочей поверхности этих лент поверхность получаемого пластика может быть структурированной, матированной или глянцевой.
Во времена СССР были закуплены всего три такие установки — для Электрогорского мебельного комбината и для завода по выпуску ДСП в г. Подрезково Московской области.
В 1978 году патент на этот пресс и способ производства ламинатов был продан немецкой фирме Hymmen, которая доработала конструкцию станка, сделав возможным применение этого оборудования, например, при производстве гетинакса с верхним слоем из медной фольги, используемого для изготовления печатных плат.
Другая область применения такого пресса — производство ламинированного паркета. С этой целью он оснащается устройствами для размотки рулонных пленок и рольгангом для автоматической подачи заготовок из MDF или ХДФ, а на выходе — приемным рольгангом с механизмом для разделения полученного непрерывного полотна в разрывах между заготовками, аналогичным устанавливаемому в линиях каширования.
Различие между установками состоит лишь в том, что одно размоточное устройство находится снизу — для пленки, служащей противотягом, а два других расположены сверху — для декоративной пленки, имитирующей текстурный рисунок древесины или какой-то другой материал, и прозрачной покровной пленки, часто называемой у нас оверлеем.
Термин «оверлей» (англ. overlay) образован от сочетания слов over (верх) и layer (пласт, слой). Пленка используется для получения поверхностей облицованных плит, которые должны быть особенно устойчивы к истиранию и царапанию, и наносится поверх декоративной бумажно-смоляной пленки. Её изготавливают из светостойкой бумаги на основе альфа-целлюлозы, не содержащей наполнителей и пигментов, которая после пропитки становится прозрачной.
Масса этой бумаги до пропитки составляет 18−40 г/м2. Для изготовления подслойных пленок используется бумага массой 80−150 г/м2.
Ленточный пресс из-за трения прижима и ленты не может обеспечить высокое давление, необходимое для полного выдавливания пропиточной смолы из бумажной пленки при ламинировании.
Это несколько снижает прочность готового пластика или прочность наружного слоя ламинированного паркета по сравнению с прочностью продукта, который получается при плоском прессовании.
Поэтому у пластиков, имеющих обозначение CPL, износостойкость меньше, чем у пластиков HPL, изготовленных с использованием плоских прессов. Английская аббревиатура HPL расшифровывается как high pressure laminates — в переводе ламинаты (слоистые пластики) высокого давления.
Плоские прессы
Под прессом понимается машина для обработки давлением, которая рабочими частями оказывает статическое (но не ударное!) воздействие на заготовку или материал.
Прессы, создававшие рабочее давление посредством винта, вращаемого вручную, появились в XV–XVI веках и использовались в различных ремеслах, не связанных с обработкой металла или древесины (маслоделии, виноградарстве, переплетном и печатном деле). В конце XVII — начале XVIII века винтовые прессы начали применяться для обработки металлов давлением, в частности для чеканки монет и медалей. Гидравлические прессы были созданы в начале XIX века и получили распространение со второй его половины в кузнечно-штамповочном производстве, а в деревообработке начали широко применяться только в 1950-х годах.
До того времени все процессы фанерования выполнялись вручную, и действовавшим тогда артелям и небольшим фабрикам было вполне достаточно производительности винтовых прессов. Кроме того, использовавшиеся в середине прошлого века альбуминовые и казеиновые клеи нельзя было наносить механическим способом.
Толчок активному внедрению прессов в деревообработке дало освоение производства древесно-стружечных плит в промышленных масштабах, начавшееся в 50-е годы прошлого столетия.
Благодаря освоению этой технологии все отрасли деревообработки перешли к промышленному производству, а облицовывание пластей стало обязательным. Но для отверждения использовавшихся в то время синтетических клеев требовалась длительная выдержка в прессе, а это влекло за собой необходимость постоянно увеличивать количество прессов на каждом предприятии, повышать капитальные затраты и создавать дефицит производственных площадей.
Поэтому сначала для производства древесно-стружечных плит и их облицовывания стали применяться изобретенные тогда же, в 1950-е, многопролетные прессы, в которых плоские прессующие плиты располагались одна над другой, создавая одновременно несколько рабочих проемов.
Многопролетный пресс
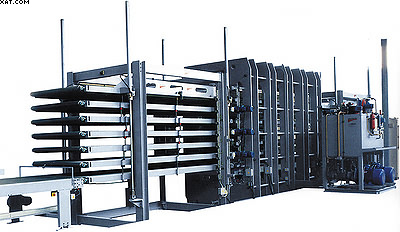
Рис. 2. Многопролетный пресс с загрузочными этажерками
В конструкцию такого пресса (рис. 2) входят: рама, состоящая из вертикальных колонн, объединенных сверху горизонтальными поперечными связями, называемыми архитравами; плиты, движущиеся вертикально вдоль этих колонн по направляющим; механизм смыкания плит и создания рабочего давления с помощью гидроцилиндров; гидростанция, обеспечивающая нагнетание рабочей жидкости (масла) в эти гидроцилиндры; система нагрева и циркуляции теплоносителя в системе обогрева плит.
Важнейшими агрегатами многопролетного пресса являются загрузочные этажерки, располагающиеся со стороны зоны загрузки и выгрузки. Они представляют собой вертикальные конструкции, по которым перемещаются горизонтальные рамы, осуществляющие прием набранных прессуемых пакетов и их подъем на уровень каждой из плит пресса. Горизонтальные рамы принимают на себя заготовки после окончания цикла прессования и опускают их вниз, на уровень разгрузки.
Без использования загрузочных этажерок, обеспечивающих одновременную загрузку всех пролетов пресса, первый помещенный в него пакет оставался бы лежать на горячей плите до окончания загрузки всех остальных и отверждение клея в нем завершилось бы ещё до смыкания и подачи рабочего давления.
При работе многопролетного пресса пакеты, набранные на индивидуальных металлических поддонах, по одному поступают на подъемные рамы загрузочной этажерки и поднимаются вместе с ними вверх. Каждая рама располагается на уровне загрузки соответствующего этажа пресса. Когда закончится заданное время выдержки пакетов, загруженных в пресс ранее, он раскрывается, его плиты опускаются вниз и каждая достигает своего уровня. Затем из пресса на горизонтальные рамы приемной загрузочной этажерки одновременно выталкиваются все спрессованные заготовки, а их место занимают новые. После этого сразу же включается гидравлический механизм, обеспечивающий смыкание плит и создание рабочего давления в прессе.
Одновременно опускаются все рамы загрузочной этажерки и происходит их очередная загрузка, начиная с верхней, а рамы приемной этажерки по одной опускаются вниз и с них удаляются поддоны с прессованными деталями. По окончании разгрузки все рамы снова поднимаются и останавливаются каждая на своем уровне — для приема следующих плит после раскрытия пресса.
Подобные прессы использовались для сушки лущеной фанеры (так называемые дыхательные прессы), в производстве древесно-стружечных плит (для прессования стружечного ковра), для склеивания и облицовывания полотен дверей щитовой конструкции, а также для облицовывания заготовок щитовых деталей мебели.
Число рабочих проемов многопролетных прессов в зависимости от их назначения и требуемой производительности составляет от 2 до 40. Впрочем, если необходимо, их может быть и больше. При этом важно, чтобы время набора всех пакетов для полной загрузки такого пресса приблизительно соответствовало времени технологической выдержки заготовок в нем. При передержке возможны перегрев клеевого слоя и его деструкция, снижающая прочность склеивания, или неполная загрузка пресса.
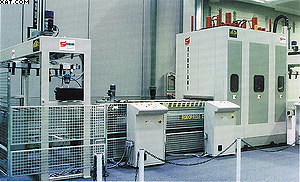
Рис. 3. Многопролетный пресс с последовательной
загрузкой прессуемых пакетов без использования
этажерок
Существенные недостатки многопролетных прессов с загрузочными этажерками — сложности, возникающие в процессе их эксплуатации, обслуживания и ремонта, и необходимость использования поддонов, которые требуют отдельного обслуживания, поскольку от постоянного циклического воздействия давления приобретают наклеп и коробятся, загрязняются и нуждаются в регулярной очистке.
Кроме того, из-за довольно длительного рабочего цикла таких прессов при их использовании должны применяться клеи с длительным периодом открытой выдержки, что в некоторых случаях невозможно, так как приводит к их впитыванию в подложку с разбуханием подложки.
Недостатком прессов такой конструкции считается и сложность обеспечения строгой параллельности всех плит и равномерности давления на все прессуемые пакеты, в особенности при смещении внутри пролета хотя бы одного из них или при наличии заготовок разной толщины в одном пролете.
Для устранения некоторых недостатков подобной техники в мире создан по крайней мере один многопролетный пресс, загружаемый без использования этажерок.
Пресс мод. LAS 230 EVOLUZIONE итальянской фирмы Sergiani (рис. 3) оснащен запатентованной этой фирмой системой последовательной загрузки и разгрузки его пролетов поддонами с прессуемыми пакетами снизу, в то время как остальные его этажи находятся под постоянным рабочим давлением. Он работает в автоматическом режиме и имеет постоянный уровень загрузки и выгрузки.
Возросшие к концу 1960-х годов требования к подобномй оборудованию в части увеличения его производительности, а также достижения в области химии привели к разработке быстроотверждаемых клеев и возврату к использованию однопролетных прессов, но не механических или винтовых гидравлических, а гидравлических, имеющих особо короткий цикл смыкания и размыкания плит, оснащенных системой ленточной загрузки.
Но о них мы расскажем в следующем номере журнала.
Сергей НИКИТИН, компания «Медиатехнологии», по заказу журнала «ЛесПромИнформ»