Облицовывание поверхностей. Часть 4
Принято считать, что первый в мире гидравлический пресс был создан известным в свое время, но почти забытым теперь английским изобретателем Йозефом Брамой (Josef Bramah) еще в 1795 году. Но широкое распространение гидропрессы получили только в конце XIX века, в ходе промышленной революции. А в деревообработке и мебельном производстве это произошло лишь в послевоенные 1940-е годы, когда было освоено промышленное производство древесно-стружечных плит.
Иллюстрации и таблицы см. в PDF-версии статьи
До той поры облицовывание древесных поверхностей производилось натуральным шпоном с применением животных (столярных) клеев и вручную, с помощью притирочного молотка или с использованием хомутовых струбцин и винтовых прессов.
Производительность и клей
После перехода к промышленному производству мебели и столярностроительных изделий производительность этого простейшего оборудования оказалась явно недостаточной, и технологи наконец обратили внимание на гидравлические прессы, которые к тому времени уже давно использовались в производстве клееной фанеры, называвшейся тогда также диктом или фанеройпереклейкой.
Одновременно стали применяться и синтетические клеи – сначала на основе карбамидных (мочевинных и мочевино¬формальдегидных) смол. Они были дешевле животных клеев, могли наноситься на склеиваемые поверхности в холодном состоянии и оказались более удобными при склеивании в прессах.
У первых смоляных клеев был довольно большой период желатинизации, но для их отверждения требовалась длительная выдержка под давлением в холодном прессе. Чтобы увеличить производительность, стали использовать многопролетные прессы, которые позволяли в ожидании отверждения в них клея получать сразу несколько облицованных заготовок. А поскольку ждать приходилось долго, то можно было заняться набором нужного количества пакетов для следующей загрузки пресса. Кроме того, можно было неспешно разгружать и загружать пресс без опасения, что клей начнет желатинизироваться.
Ситуация радикально изменилась с появлением клеев горячего отверждения и началом использования многопролетных обогреваемых прессов.
Сроки выдержки прессуемых пакетов сократились по сравнению с прежней технологией в десять раз, но все равно за это время необходимо было набрать все пакеты для полной загрузки пресса. К тому же стало невозможным загружать эти пакеты в пресс по одному: в том, который загружался в пресс первым, клей начинал отвердевать еще до того, как загружался последний пакет, и происходило смыкание плит. Это и стало причиной оснащения многопролетных прессов загрузочными этажерками, которые обеспечивали одновременное помещение в них всех прессуемых пакетов и создавали равные условия для их прессования.
Однопролетные прессы на новый лад
Успехи в области химии привели в середине 1960-х годов к разработке быстроотверждаемых клеев, отличавшихся не только коротким периодом отверждения, но и сокращенным временем открытой выдержки. А это сделало применение загрузочных этажерок невозможным – в процессе их наполнения клей начинал желатинизироваться.
До того момента в промышленности уже применялись обогреваемые однопролетные гидравлические прессы, которые использовались преимущественно на мелких предприятиях с небольшими объемами производства и загрузка которых производилась вручную. Прессуемый пакет задвигался в них на металлическом поддоне толщиной до 3 мм. Металл поддона прогревался довольно быстро, и разница в скорости прогрева верхнего и нижнего клеевых слоев не оказывала существенного влияния на качество облицовывания при использовании обычных карбамидных клеев.
Наносить клей нужно было за очень короткое время – пока он не начал отверждаться. А применение быстроотверждаемых клеев потребовало выполнять эту операцию еще быстрее, причем с высокой степенью равномерности.
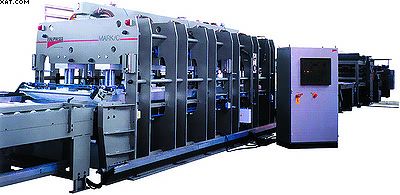
Рис. 1. Линия облицовывания пластей на базе однопролетного
пресса с загрузочной кареткой
Для этого сначала были разработаны вальцовые клеенаносящие станки с дозирующими роликами, обеспечивающие точное регулирование расхода клея, а затем и полуавтоматические линии облицовывания пластей щитовых заготовок на базе однопролетного пресса с механизированной загрузкой (рис. 1).
Подобные линии первых моделей имели в своем составе автоматический загрузчик облицовываемых заготовок, щеточный станок для очистки их поверхностей от пыли, вальцовый клеенаносящий станок, два подстопных места для облицовок, каретку для загрузки пресса, собственно сам пресс и приемный ленточный конвейер. На каретке также располагался ленточный конвейер, на котором производился набор прессуемых пакетов.
При работе линии загрузчик по сигналу оператора по одной подавал заготовки из стопы в линию. После этого они проходили через щеточный станок, где с них удалялась пыль, затем поступали на клеенаносящий станок, в котором на обе пласти с заданным расходом наносился клей. За станком располагался рольганг с дисковыми роликами, который предупреждал нарушение клеевого слоя на нижней пласти заготовки. Два оператора, находившиеся по обе стороны линии, брали с подстопного места и укладывали на ленточный конвейер каретки нижнюю облицовку, помещали на нее заготовку с клеем, а затем укладывали верхнюю облицовку. После этого оператор нажатием педали включал конвейер, который продвигался вперед и освобождал место для сборки следующего пакета. При заполнении всей рабочей поверхности этого конвейера пресс раскрывался и каретка с подготовленными для прессования пакетами входила в его пролет. Одновременно своим передним краем каретка выталкивала загруженные в пресс ранее облицованные детали на приемный конвейер, скорость которого была синхронизирована с ее движением. После этого каретка начинала обратное движение. Одновременно включался конвейер каретки, и находившиеся на нем пакеты переходили на нижнюю плиту пресса. Когда каретка полностью освобождала пролет, пресс смыкался и начиналось прессование. Затем весь цикл повторялся. Принцип работы описанной выше линии был взят за основу при конструировании отечественной линии облицовывания пластей МФП1.
Но недостатком такой системы загрузки пресса оказалось то, что при падении пакетов с конвейера каретки на плиту пресса происходил сдвиг облицовки, а из¬за попадания на плиту отколовшихся от пакетов древесных частиц на поверхности готовой детали после прессования появлялись вмятины.
Прессы с ленточной загрузкой
Стремление к дальнейшему увеличению производительности линий облицовывания пластей за счет совершенствования процесса и экономии времени, затрачиваемого на возврат загрузочной каретки, работа конструкторов, направленная на устранение недостатков существовавших линий такого типа, привели к созданию однопролетных прессов с механизмом ленточной загрузки.
Рабочим органом такого механизма является конвейер с лентой из полиэтилентерефталатной (лавсановой) пленки толщиной 0,4−0,6 мм.
Такая пленка устойчива к длительному воздействию температуры до 250°С, к химическому воздействию смол и клеев на их основе и не обладает адгезией к ним.
Конвейер с такой лентой состоит из двух частей: одна находится между плитами пресса, на его нижней плите, а другая под этой плитой. В ходе каждого цикла загрузки они меняются местами, что позволяет охлаждать нижнюю часть ленты, которая становится холостой.
Линия с этим прессом имеет такой же состав, как линия, оснащенная загрузочной кареткой. Отличие состоит в том, что формирование прессуемых пакетов ведется на стационарном ленточном конвейере. При его заполнении и окончании времени выдержки заготовок в прессе пресс раскрывается, после чего одновременно включаются все три ленточных конвейера линии: формирующий, ленточный конвейер пресса и приемный, расположенный за ним. Облицованные детали выходят из пресса и поступают на ленту приемного конвейера, а их место в прессе занимают сформированные пакеты. Далее пресс смыкается, в нем создается рабочее давление, и после соответствующей выдержки заготовок процесс повторяется.
Линии с прессами, оснащенными ленточными механизмами загрузки мод. АКДА 4138 и АКД 4140, выпускались отечественной промышленностью до начала 1990-х.
Что такое короткотактный пресс
Прессы, используемые в таких линиях, называются короткотактными, иногда быстроходными. Это общее наименование всех горячих (обогреваемых) однопролетных прессов, оснащенных системой автоматической загрузки и выгрузки, обеспечивающих минимально возможный технически цикл (такт) прессования при облицовывании пластей щитовых деталей.
Время цикла в них складывается из временных отрезков, необходимых для размыкания плит; загрузки пакетов прессуемых деталей, заранее уложенных на ленточный транспортер; смыкания плит и достижения в прессе заданного усилия (рабочего давления); выдержки деталей под давлением; снятия давления; размыкания плит и выгрузки облицованных деталей. Причем загрузка и выгрузка деталей производятся одновременно.
Общая продолжительность цикла в основном определяется временем выдержки прессуемых пакетов под давлением, которое задается технологией облицовывания и зависит от материала подложки, облицовочного материала и вида используемого клея. Наименьшее время цикла у современных короткотактных прессов составляет 12 с (без учета времени выдержки под давлением). Такие прессы используются преимущественно для облицовывания пластей щитовых деталей тонкими облицовочными материалами с применением быстроотверждающихся клеев.
Быстрая загрузка и достижение прессом необходимого усилия предотвращают схватывание клея до достижения заданного рабочего давления прессования – в первую очередь на той стороне прессуемого пакета, которая лежит на нагретой нижней плите пресса.
Короткотактные прессы используются также в составе цикловопроходных линий каширования, работающих по методу «квикстеп». В этом случае накатывание облицовочного материала на пласти деталей осуществляется непрерывно, в проходном режиме, а прессование – циклически.
Поэтому скорость подачи облицовочного станка в таких линиях каширования во многом зависит от длины плит короткотактного пресса и на практике не может превышать 7−8 м/мин.
Но вот парадокс: высокая производительность линий облицовывания (даже тех, в которых набор пакетов производится вручную) сегодня для подавляющего большинства мебельных предприятий просто не нужна! Даже по самым грубым подсчетам, одна такая линия в год обеспечивает двухстороннее облицовывание пластей всех (!) деталей для 10 тыс. мебельных стенок, каждая из которых состоит из четырех секций (или примерно для 40 стенок в смену).
Однопролетный пресс
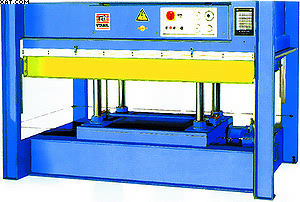
Рис. 2. Простой однопролетный пресс
Именно по этой причине наши производители не стремятся оснащать свои производства линиями облицовывания, а ограничиваются приобретением однопролетных обогреваемых прессов с ручной загрузкой, как правило, рассчитанных на обработку плит 3500 х 1300 мм (рис. 2).
Но и здесь существуют определенные тонкости. Первая из них – выбор системы нагрева. На предприятиях, где есть собственная котельная, стараются приобрести пресс с паровым или водяным нагревом плит. Но он создает температуру не выше 90°С. Нагрев до 140°С обеспечивает термомасляная установка, но используемый в ней теплоноситель (термомасло) весьма дорог, и при его потере, например вследствие нарушения герметичности системы циркуляции, расходы на восстановление будут достаточно велики.
Электронагрев связан с большими затратами электроэнергии. А ее стоимость постоянно растет… Поэтому, прежде чем сделать выбор, стоит все взвесить, оценить и просчитать разные варианты.
При необходимости увеличения производительности такой пресс, имеющий довольно большой пролет, как правило, может оснащаться дополнительными греющими плитами, что дает возможность превратить его в многопролетный с ручной загрузкой. И если такая перспектива просматривается, то при покупке следует сообщить о ней производителю, чтобы изготавливаемое оборудование было подготовлено к возможной модернизации.
К сожалению, некоторые производственники, приобретая однопролетный пресс и выбирая машину с низкой стоимостью, почему-то не обращают внимания на наличие в ней механизма синхронизации смыкания плит, который оказывается весьма полезным при облицовывании деталей большого размера.
Для тех предприятий, которые производят изделия по заказу, совсем не лишним будет устройство для отключения плунжеров, не участвующих в создании рабочего давления на заготовку, – оно дает возможность облицовывать даже одну деталь, расположенную на плите несимметрично, что предотвращает изгиб плит, устранение которого невозможно.
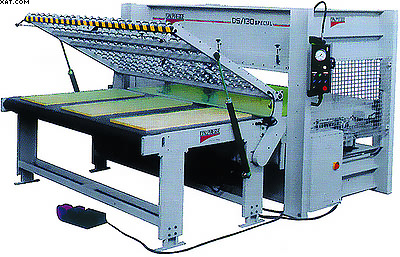
Рис. 3. Однопролетный пресс с системой ленточной загрузки
Советуем также осведомиться у изготовителя пресса, есть ли в нем устройство для отключения давления при перекосе плит из¬за попадания между ними инородного предмета. Повторимся: изгиб плиты обходится слишком дорого.
Вообще при выборе оборудования не нужно отказываться от разного рода дополнительных устройств и приспособлений.
В современных условиях, при достаточно высокой производительности предприятия, приобретая даже самый простой пресс, обязательно следует позаботиться о его оснащении системой ленточной загрузки (рис. 3).
Ее эксплуатация как минимум позволит рабочим избежать ожогов рук при ручной загрузке пресса. Помните: искривленный поддон не способствует качественному облицовыванию. А это часто выясняется только при шлифовании, когда деталь, облицованную дорогим шпоном, приходится отправлять в брак.
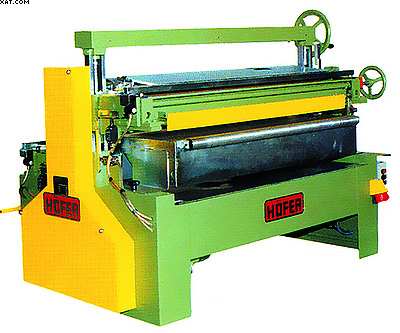
Рис. 4. Станок четырехвальцовый клеенаносящий
Особое внимание надо уделять правильному нанесению клея и его оптимальному расходу. Если клей наносится валиком, то можно ожидать, что на шпоне появятся пробития клея или «чижи» – места, где шпон не приклеился к основе. Поэтому желательно иметь на предприятии вальцовый клеенаносящий станок. Но и здесь есть тонкость: при облицовывании тонкими материалами, например шпоном толщиной от 0,4 мм или пленками на основе бумаг массой от 60 г/м2, этот станок должен быть оснащен дозирующими роликами (рис. 4). В противном случае точно регулировать расход клея будет невозможно. А такой контроль особенно важен при облицовывании двух сторон заготовки разными материалами. Например, пластиком и лущеным шпоном в качестве противотяга.
Клеенаносящий станок с дозирующими роликами (четырехвальцовый) нужен и при использовании реконструированного шпона типа «файнлайн» и его аналогов, когда пробитие клея – обычное дело.
Процесс облицовывания технологически довольно прост. Но сегодня для многих предприятий, переходящих к выпуску дорогой мебели и других изделий, облицованных натуральным шпоном, эта технология облицовывания довольно нова.
Главное, производственник не должен забывать, что для обеспечения высокого качества облицовывания и необходимой производительности большое значение имеет не только правильный выбор оборудования, но и строгое соблюдение всех заданных режимов, определяемых материалом заготовки, облицовок и применяемыми клеями.
Сергей НИКИТИН,
компания «Медиатехнологии»,
по заказу журнала «ЛесПромИнформ»