Многопильные станки. Часть 2
Равнение на максимальный результат
Подача заготовок в многопильном станке должна быть точной и непрерывной − таков девиз разработчиков данного вида оборудования. Действительно, выбор в пользу того или иного варианта системы подачи, ее настройка предопределяют надежность и производительность станка, качество и геометрию получаемого пиломатериала.
Многопильные станки оснащаются системами подачи гусеничного или вальцового типа, каждая из которых имеет свои особенности. Гусеничную подачу еще называют цепной или конвейерной.
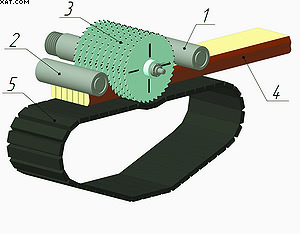
Рис. 1. Гусеничная система подачи:
1 – прижимной ролик на входе заготовки;
2 – прижимной ролик на выходе заготовки;
3 – пильный блок;
4 – заготовка;
5 – гусеничный транспортер
В основе гусеничной системы подачи (рис. 1) − секционный транспортер (поз. 5). Секции транспортера соединены шарнирами, оснащены выступами для надежной фиксации заготовки с одной стороны и пазами для линейных направляющих и звездочек − с другой. В некоторых моделях многопильных станков в качестве такого транспортера используется многорядная специальная цепь.
Верхняя ветвь гусеничного транспортера − рабочая; на этом участке установлены дополнительные направляющие для стабилизации движения в поперечном направлении. Поступательное движение транспортера осуществляется за счет вращения звездочек приводом подачи. Нижняя ветвь предназначена для обратного движения секций транспортера.
Под пильным блоком (поз. 3) секции транспортера могут двигаться по траектории в виде выемки, что необходимо для выхода инструмента из заготовки.
Для того чтобы полубрус (поз. 4) не смещался относительно секций гусеничного транспортера (поз. 5), его прижимают ролики (поз. 1 и 2) перед пильным блоком (поз. 3) и за ним. Для организации эффективного процесса пиления используются дополнительные прижимные планки с прорезями для пил, компенсаторы колебаний транспортерных ветвей, механизмы подъема-опускания роликов (поз. 1 и 2) с дифференцированным усилием прижима и т. п.
Гусеничная система подачи имеет ряд преимуществ. Прежде всего это точное направление подачи: заготовка (поз. 4) располагается на множестве выступов транспортера. Если транспортер не имеет поперечного люфта, то брус проходит зону пиления по идеальной прямолинейной траектории. При должном взаимном расположении инструмента и транспортера получается пиломатериал с превосходной геометрической формой. Кроме того, на многопильном станке с такой системой подачи можно распиливать короткие заготовки − длиной 250−300 мм, точность подачи не зависит от их размера.
До недавнего времени станки данного типа имели ограничения по скорости подачи, а также отличались высоким уровнем шума. Но с появлением новых антифрикционных материалов для направляющих верхней ветви транспортера, втулок шарниров, динамических смазок верхний скоростной порог значительно повысился − до 80−120 м/мин, а вибрации снизились до приемлемого уровня. Благодаря надежной фиксации заготовки на транспортере движение бруса имеет непрерывный характер, без скачков и остановок, что также предопределяет высокое качество готовой продукции. Система подачи данного типа допускает некоторое отклонение от параллельности верхней и нижней пласти полубруса без ущерба для точности перемещения. Такой лояльностью к форме поперечного сечения заготовки не обладает ни один подающий механизм.
Пильный блок в многопильных станках с гусеничной системой подачи, как правило, один и располагается над транспортером. Вращение пил осуществляется навстречу подаче. Особая задача − сбор и утилизация опилок, так как они не должны засорять подвижные части транспортера (поз. 5). Выступы на его секциях неизбежно оставляют след на кромке пиломатериала в виде периодических углублений, что характерно для всех видов многопильных станков. Уменьшить размер углублений можно путем подбора оптимального усилия прижима роликов (поз. 1 и 2), а также за счет дальнейшей обработки доски − строгания, пиления и т. п.
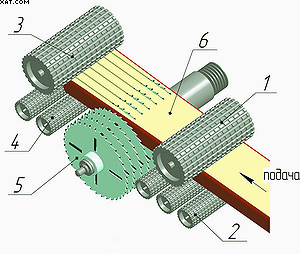
Рис. 2. Вальцовая система подачи:
1 – верхний подающий вал;
2 – нижние подающие вальцы;
3 – верхний приемный вал;
4 – нижние приемные вальцы;
5 – пильный блок;
6 – заготовка
Вальцовая система подачи (рис. 2) состоит из специальных роликов − вальцов (поз. 1−4), которые взаимодействуют с заготовкой (поз. 6) и заставляют ее двигаться в определенном направлении.
Нижние вальцы (поз. 2 и 4) имеют определенное, неизменное положение осей и образуют опорную плоскость для заготовки (поз. 6). Верхние вальцы могут подниматься и опускаться, чтобы прижимать заготовку различной высоты. Следует отметить, что диапазон регулирования верхних вальцов (поз. 1 и 3) строго соответствует высоте пропила пильного блока (поз. 5). Минимальная толщина заготовки определяется исходя из условия стабильной работы механизма подачи. Для исключения проскальзывания поверхность вальцов имеет ребристую форму, каждый вал (поз. 1−4), как правило, приводной, чтобы движение передавалось по максимально возможной площади контакта древесины и подающих механизмов. Эта задача решается с помощью зубчатых и цепных передач.
Вальцовая система подачи изначально проектировалась как высокоскоростная. Некоторые модели с такой механизированной подачей способны поддерживать скорость потока до 180 м/мин. Действительно, ограничений для угловой скорости вращения вальцов нет, кроме регламента собственно процесса резания. Очевидно, что при прочих равных условиях фактическая подача заготовки высотой 50 мм будет больше, чем у образца размером 200 или 250 мм. Максимальная скорость подачи, указываемая в паспорте станка, нередко соответствует режиму тестирования оборудования, без реальной заготовки. Вальцы по сравнению с транспортером имеют более высокую износостойкость и, как следствие, долговечность. Однако в случае изменений условий резания или состояния заготовки часты случаи самопроизвольной остановки бруса и, соответственно, проскальзывания вальцов.
Чтобы исключить подобные инциденты, в многопильных станках с вальцовой системой подачи особое внимание уделяется механизму прижима верхних подающего (поз. 1) и приемного (поз. 3) ролика.
В одних моделях прижим осуществляется гидро- или пневмоцилиндром с определенным усилием, которое, с одной стороны, гарантирует равномерную подачу, а с другой − минимальную деформацию кромки получаемого пиломатериала от выступов на поверхности вальцов. В других прижимающее усилие возникает от пружин или от собственной массы вальцов (поз. 1 и 3). Так или иначе, станку требуется предустановка на определенный диапазон высоты заготовки, а также корректировка настроечных параметров в зависимости от породы древесины, состояния инструмента (режущие кромки, наличие СОЖ и т. п.) и заготовки (мерзлый лес, смолистость и т. д.).
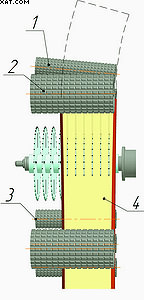
Рис. 3. Нарушения работы
системы подачи:
1 – нижний приемный вал
с перекосом;
2 – верхний приемный вал;
3 – нижний подающий вал;
4 – заготовка
Помимо оптимального прижима, вальцовая система подачи должна иметь безупречное расположение вальцов относительно друг друга и относительно пильного вала. Так, если один из валов (поз. 1 рис. 3) будет иметь перекос своей оси относительно других валов (поз. 2 и 3), то заготовка (поз. 4), скорее всего, будет двигаться по криволинейной траектории. Как следствие, могут быть изогнутыми получаемые доски, с дефектными пластями от касания с инструментом, соответственно, стоит ожидать снижения доли выхода готового материала: крайние доски будут иметь форму клина. Не многие модели многопильных станков имеют возможность корректировки положения вальцов или пильного вала. В любом случае такой ремонт должен осуществляться специалистами, аккредитованными заводом-изготовителем, так как требуется, помимо прочего, специальный контрольно-измерительный инструмент.
От пользователя требуется неукоснительное выполнение требований установки и эксплуатации многопильного станка, в частности выставление его в строго горизонтальное положение.
Нестабильная геометрия готового пиломатериала наблюдается и в случае раскроя короткомерных заготовок из-за снижения площади контакта, а также в моделях с минимальным количеством вальцов. Минимальная длина заготовки для вальцовых подающих систем определяется исходя из расстояния между нижними подающими (поз. 2 рис. 2) и приемными (поз. 4) вальцами и обычно равна 1,2−1,6 м. Если нарушить это условие, то заготовка попросту упадет на дно станка. На практике неплохие результаты показала схема, изображенная на рис. 2. Для первичной ориентации заготовки используются три нижних вальца (поз. 2), а для выхода − два (поз. 4).
Вальцовая система подачи чувствительна к заготовкам неправильной геометрической формы. Непараллельность верхней и нижней пласти полубруса (поз. 6) приводит к тому, что верхние прижимные вальцы (поз. 1 и 3) контактируют не с пластью, а с его краем, что провоцирует несимметричные усилия, направленные на поперечное смещение заготовки. Возникает дефект, аналогичный представленному на рис. 3. Для предотвращения подобной ситуации необходимо тщательно подходить к выбору станка первого ряда, на котором формируется полубрус.
Вальцовая система подачи менее зависима от выхода стружки − опоры вальцов надежно защищены уплотнениями, однако ребра вальцов быстро засоряются смолой, попадающей на них вместе с древесиной, и требуют регулярной очистки.
Подающий механизм позволяет работать при любом расположении пильного вала, а также при использовании двухвального пильного блока. Как правило, одновальные многопильные станки имеют пильный вал, расположенный ниже заготовки, с направлением вращения ей навстречу.
В характеристике многопильного станка указывается максимальная ширина заготовки, она может быть от 350 до 1100 мм. Она больше расстояния между крайними пилами и ограничена размерами проема для заготовки. Это необходимо, чтобы формировались две крайние обзольные доски. Иногда проем значительно превышает длину пильного вала, что позволяет распиливать широкий полубрус в два захода.
В качестве привода как гусеничной, так и вальцовой системы подачи могут использоваться электродвигатели с редуктором, а также гидродвигатели с прямой передачей. Гидродвигатель более компактный, в ситуации, когда осуществляется повторный пуск системы подачи, с загруженной заготовкой, он более предпочтителен, так как имеет высокий пусковой момент.
Но гидропривод требует и более тщательного ухода: при низком качестве рабочей жидкости, ее несоответствии климатическим условиям нередки случаи снижения скорости вращения гидродвигателя, что снижает производительность или приводит к полной остановке многопильного станка.
Важное свойство привода − регулировка скорости подачи. У гидравлических систем эта функция реализуется за счет регулируемых дросселей. Для электропривода с редуктором характерно ступенчатое переключение (а это создает определенные неудобства в работе) либо вариатор.
С появлением частотных преобразователей скорость электродвигателей может устанавливаться плавно, но некоторые модели чувствительны к низким температурам эксплуатации и требуют поддержания рабочей температуры в блоках управления таких приводов. Потребляемая мощность механизированной системы подачи зависит от режимов резания, количества пил и размеров заготовки. В большинстве моделей она на порядок ниже мощности привода главного движения и не превышает 3 кВт.
В соответствии с требованиями ГОСТ 12.2.026.0-93 «Оборудование деревообрабатывающее. Требования безопасности к конструкции» многопильные станки должны оснащаться как минимум двумя завесами из подвижных предохранительных упоров.
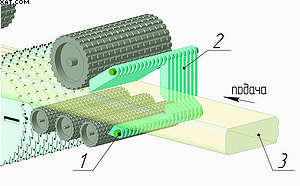
Рис. 4. Завесы из предохранительных упоров:
1 – нижний ряд упоров;
2 – верхняя завеса из подвижных предохранительных
упоров;
3 – заготовка
Одна такая завеса для примера показана на рис. 4 (поз. 2). Угол заклинивания упоров должен составлять 55−65. Упоры нужны для того, чтобы не допустить самопроизвольное движение заготовки в направлении, противоположном вектору подачи.
Для многопильных станков с механизированной подачей гусеничного типа обязателен нижний ряд предохранительных упоров (поз. 1 рис. 4). Упоры имеют механизм их подъема для тех случаев, когда необходимо вытащить заготовку из станка при ее заклинивании, например. При этом рычаг должен иметь датчик, который должен блокировать пуск всех приводов на время внештатного положения предохранительных упоров.
В станке также должна быть электроблокировка, препятствующая запуску системы подачи, если не включен привод главного движения, а также ряд других устройств − ограждений, защитных устройств и т. д., которые повышают уровень безопасности работы на многопильном станке.
Техническое обслуживание многопильных станков
Механизированные подачи многопильных станков, как и прочие механизмы, требуют периодического осмотра и обслуживания. В фокусе внимания должны находиться все трущиеся элементы: шарниры секций транспортеров, опоры вальцов, рычагов, открытые зубчатые и цепные передачи и т. д. В инструкции по эксплуатации многопильных станков изготовитель обычно указывает регламент консистентной смазки, замены жидкой смазки в редукторах или коробках передач, ориентировочные периоды работы ремней, цепей и других устройств. В соответствии с этим регламентом и нормами безопасной работы производится обслуживание деревообрабатывающего оборудования данного типа, и в частности механизированной подачи. Очистка механизмов от пыли, стружки, смолы и грязи производится не реже одного раза в смену или по мере необходимости, так как стружка наиболее часто становится причиной блокировки механизмов или их неправильной работы. Кроме того, засоренность винтовых пар может увеличить нагрузку на рукоятки или штурвалы, что также недопустимо и является нарушением требований безопасности.
Адаптация многопильного станка
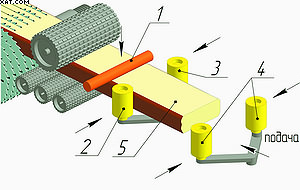
Рис. 5. Околостаночное оборудование:
1 – датчик высоты заготовки;
2, 3, 4 – ролики центрирующего устройства;
5 – заготовка на подающем рольганге
Многопильный станок эффективно работает как модуль технологической линии. Для адаптации станка в линию следует учитывать ряд факторов. Во-первых, для высокопроизводительных производств наиболее сложным является организация так называемой рабочей среды вокруг станка. Процесс, где брус массой 300−400 кг движется со скоростью 20−30 м/мин и выше, практически исключает любые ручные манипуляции из-за угрозы травматизма. Для этих целей используется околостаночное оборудование: подающие и приемные рольганги, ленточные транспортеры, кантователи, центрирующие механизмы (поз. 2, 3, 4 рис. 5), разного рода датчики и другие устройства. Многопильные станки, оснащенные полуавтоматической системой настройки на высоту заготовки, где верхние ролики (поз. 1 и 2 рис. 1) или вальцы (поз. 1 и 3 рис. 2) до входа бруса в станок устанавливаются в определенное положение по вертикали, должны получать данные об этом размере заготовки. Для этой цели перед станком устанавливается датчик высоты, вариант такого датчика представлен на рис. 5: ролик (поз. 1), соединенный с пневмоприжимом и электронной линейкой опускается на брус до момента касания, после чего данные передаются в систему управления станочной механизированной подачи.
Центрирующий механизм сдвигает брус так, чтобы его условная средняя плоскость совпала со средней плоскостью пильного блока многопильного станка. В этом случае достигается оптимальный раскрой заготовки, а также исключается вероятность ее заклинивания вследствие контакта с корпусом станка. Центрирование осуществляется по следующему циклу. Как только брус полностью входит в рабочую зону механизма, срабатывает датчик и две пары роликов сводятся к центру (поз. 2, 3, 4 рис. 5). За счет специальной механизации ролики (поз. 2 и 3) двигаются синхронно и всегда симметричны относительно средней плоскости пильного узла. Таким образом, ролики будут смещать брус (поз. 5) в поперечном направлении до тех пор, пока он не займет «центральное» положение, после чего разойдутся и займут исходное положение. Пара роликов (поз. 2 и 3) центрирует переднюю часть бруса, вторая пара (поз. 4) − заднюю, чтобы заготовка заняла положение, максимально близкое к среднему: двухкантный брус, как правило, имеет весьма неровную обзольную часть поверхности.
Для организации поточного производства следует предусмотреть место на участке перед многопильным станком на случай нештатной остановки или заклинивания заготовки в станке.
В этом случае потребуется, помимо экстренного торможения всего потока, возврат бруса и, возможно, его выемка. Конструкция приемного рольганга должна учитывать, что получаемый пиломатериал неустойчив, так как опирается на транспортер кромкой и крайние доски могут опрокидываться, создавая затор. Для безостановочной работы линии необходимо, чтобы механизированная система подачи оснащалась датчиками обратной связи: в этом случае риск нарушения рабочих циклов снижается, а оператор имеет возможность тестирования многопильного станка и профилактики нештатных ситуаций.
Там, где скорость потока невелика, механизация может быть менее сложной. Для ориентации заготовки перед подачей в многопильный станок также используются лазерные указатели, имитирующие плоскость крайней пилы, − в этом случае оператор вручную перемещает заготовку на подающем рольганге до требуемого положения. Если заготовка представляет собой трех- или четырехкантный брус, можно использовать направляющую линейку, вдоль которой будет подаваться заготовка. Такая линейка может быть в конструкции многопильного станка.
Во всех случаях требуется оборудование специальных рабочих мест для операторов и обслуживающего персонала деревообрабатывающих установок в соответствии с требованиями нормативных документов, регламентирующих безопасные условия труда.
В частности, в свободном доступе должна быть кнопка аварийного отключения станка или смежных с ним механизмов, вся техника должна быть снабжена защитными ограждениями и экранами, исключающими производственные травмы.
В лесопилении многие модели многопильных станков промышленного класса могут перерабатывать объединенный поток от двух станков первого ряда.
Однако следует иметь в виду, что более предпочтительной является схема, когда имеется не менее двух многопильных станков и в случае вынужденной остановки одного из них транспортная система оперативно переключает поток. Скорость подачи многопильного станка должна соответствовать не только режимам резания, но и скорости потока. Только в этом случае оборудование данного типа будет эффективным звеном всей технологической схемы современного производства.
Андрей МОРОЗОВ,
компания «МедиаТехнологии»,
по заказу журнала «ЛесПромИнформ»
Многопильные станки: равнение на максимальный результат. Часть 1