Клеевые материалы для мембранно-вакуумного прессования. Часть 2
Двухкомпонентные клеи
В предыдущем номере журнала мы начали рассказ о технологии 3D-облицовывания элементов мебели, в которой большую роль играют современные клеевые материалы. В частности, были рассмотрены несколько марок однокомпонентных клеев, используемых при трехмерном облицовывании, которые выпускаются известными производителями и компаниями − новичками рынка клеев.
В предлагаемой вниманию читателей публикации мы расскажем о двухкомпонентных клеевых материалах на основе водной дисперсии полиуретана для трехмерного облицовывания, а также о методах оценки теплостойкости клеевого соединения.
Общие рекомендации производителей
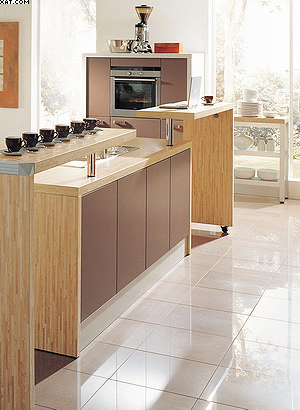
Работая с двухкомпонентными клеями, необходимо соблюдать следующие правила. При подготовке смеси следует тщательно перемешать клей с отвердителем в течение двух-трех минут. Как правило, упаковки двухкомпонентных клеевых систем производители выпускают в комплекте с дозаторами, что обеспечивает добавление в клей точного количества отвердителя. Клей перемешивают вручную или при помощи механизма. Затем смесь отфильтровывают в нагнетательный бачок через четыре слоя марли или фильтр с ячейками диаметром 300 мкм. Фильтровать смесь необходимо для достижения однородности клеевого состава. В нефильтрованном клее могут оставаться неразмешанные частицы, которые при использовании такой смеси непременно забьют сопла клеенаносящего оборудования.
Для нанесения клея на облицовываемую поверхность используют распылительные пистолеты. Правильный выбор размера сопла пистолета имеет решающее значение для работы с клеями низкой вязкости (до 1000−1200 мПа•с) и почти не имеет особого значения при использовании клея с вязкостью около 2000 мПа•с и выше. Давление воздуха на пистолет должно составлять 2,0−2,5 бар, давление на нагнетательный бачок − 4,5−5,0 бар.
В основном мебельные фасады изготавливают фрезерованными. Рисунок, вырезанный фрезой обрабатывающего центра, необходимо тщательно отшлифовать при помощи шлифовальной губки с зернистостью 100−120. После шлифования деталь очищают от пыли. Помещение, предназначенное для нанесения клея на детали, должно быть оборудовано распылительной кабиной с гидрозавесой или сухим фильтром. Качество облицовываемой поверхности будет выше, если помещение для клеенанесения изолировать от основного цеха, что минимизирует попадание пыли на деталь.
Кромка облицовываемой детали отличается большей впитываемостью, чем пласть, поэтому готовую смесь (основа + отвердитель) сначала наносят на кромку в два слоя, без промежуточной сушки. После этого клей наносится на фрезерованный рисунок детали. И здесь также есть свои особенности: сначала клей наносят на две долевые части рисунка, разворачивают деталь на 90° и наносят клей на две поперечные части. Операцию выполняют дважды.
Затем клей наносится на пласть детали. Детали с нанесенным клеем помещаются на стеллажи для подсыхания. Продолжительность сушки − от получаса до восьми часов. Детали после нанесения клея шлифовать нельзя.
В положенный срок стеллажи с деталями подаются на участок прессования. Детали укладываются на рабочий стол пресса, на подложку, затем с размоточного устройства подается пленочный материал. Запрессовка деталей производится в соответствии с технологическим режимом предприятия. При прессовании необходимо контролировать температуру прогрева облицовочного материала и температуру активации клея. От того, насколько точно подобран режим прессования, зависят качество склеивания и теплостойкость клеевого соединения. При недостаточном прогреве происходит побеление облицовочного материала на кромках фрезерованного рисунка и кромках щита. Неверно подобранный режим прессования не позволяет реактивировать клей в достаточной мере.
После прессования детали обрезают по периметру и укладывают на стеллажи для остывания в течение 2−5 мин. Затем обрезают свесы пленки, детали очищают от остатков клея и укладывают на подстопное место для отгрузки на склад готовой продукции или в мебельный цех.
2К-системы для 3D-технологии
материалов для мембранно-вакуумного прессования
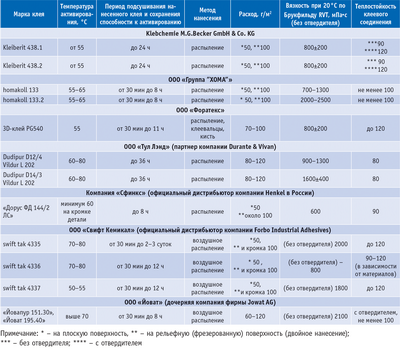
Итак, какие же марки двухкомпонентных клеев для 3D-облицовывания производят и предлагают на российском рынке, каких рекомендаций производителей и поставщиков клеев при работе с 2К-системами следует придерживаться потребителям?
В ассортименте компании «Группа „ХОМА“» есть двухкомпонентные клеи homakoll 103 и homakoll 103.1. Для облицовывания древесных плит при пониженной температуре специалисты компании разработали клей homakoll 133. Также компания поставляет для мебельных предприятий клей homakoll 133.2, характеризующийся повышенной вязкостью. В качестве отвердителя рекомендуется использовать homakoll 915. Его введение в вышеназванные клеевые материалы в соотношении 5 весовых частей (в. ч.) на 100 в. ч. клея повышает теплостойкость клеевого соединения (у клеев homakoll 103, homakoll 133 и их модификаций − не менее 100 °С) и его устойчивость к воздействию влаги, жиров и масел. Низкая температура активирования клеевого слоя (от 55−60 °С) позволяет рекомендовать клеи homakoll 133 и homakoll 133.2 для облицовывания изделий тонкими и глянцевыми пленками ПВХ.
Компания «Сфинкс» выступает официальным дистрибьютором компании Henkel в России и предлагает российским потребителям использовать клеи марок «Дорус ФД 144/1 ЛС» и «Дорус ФД 144/2 ЛС», которые применяются с отвердителем «Дорус Р397». Жизнеспособность готовой смеси − 4−6 ч в зависимости от температуры воздуха в рабочем помещении. Для достижения оптимального качества склеивания рабочая температура клея и обрабатываемых деталей должна быть минимум +16 °С.
Более низкие температуры ведут к повышению вязкости клея. Клеевая смесь наносится с помощью специального пистолета-распылителя (диаметр сопла − 1−1,5 мм). Давление в системе подачи клея не должно превышать 2 бар. Специалисты компании советуют использовать ручные распылительные пистолеты с низким давлением и диаметром сопла 1,2−2,2 мм − в зависимости от вязкости применяемого клея. Давление в распылителе должно составлять 3−5 бар. Целесообразно применять специальные распылительные или сушильные камеры.
При распылении первого клеевого слоя рекомендуется наносить минимальное количество клея. Второй слой клея должен быть виден невооруженным глазом. При облицовывании обрабатываемые детали помещаются на так называемую подложку высотой 12−16 мм. Стороны подложки по всему периметру должны быть меньше сторон детали на 3 мм (исключение − PIN-система). Готовые детали достигают максимальной термостойкости спустя три дня. Тест на термоустойчивость готовых деталей должен проводиться через семь дней после операции облицовывания.
При использовании двухкомпонентных клеев торговой марки Kleiberit (компания Klebchemie) к основе Kleiberit 438.1 и 438.2 добавляют изоцианатный отвердитель Kleiberit 807.0 в соотношении 5 в. ч. отвердителя на 100 в. ч. основы. Жизнеспособность смеси − 8 ч. Ее можно продлить, добавив в оставшийся клей примерно 5% отвердителя от массы клея, то есть приготовленную смесь можно использовать повторно. Прочность клеевого шва достигает максимального значения через 1−3 суток (24−72 ч). Как отмечает технический директор компании Klebchemie M. G. Becker GmbH & Co. KG в России и СНГ Ханну Саллинен, «качество облицованных деталей определяют в том числе и условия их хранения. Поэтому готовые изделия должны храниться на деревянных поддонах в крытых помещениях при температуре не ниже +2 °С и относительной влажности от 45 до 70%. Размер поддонов для хранения должен соответствовать размеру упаковки − чтобы не было свесов и прогибов. На одной палете должны находиться упаковки приблизительно одинакового размера, причем высота палеты не должна превышать 1,6 м».
ООО «Форатекс» для облицовывания плитных древесных материалов пленкой ПВХ предлагает жидкий 3D-клей PG540 для мембранно-вакуумного прессования. Он подходит для приклеивания тонкой ПВХ-пленки. Рекомендован для пистолета диаметром 2,0 мм. PG540 можно использовать как самостоятельный клеевой материал, так и с отвердителем (в пропорции 3−5 мас. частей отвердителя на 100 мас. частей клея).
ООО «Тул Лэнд» (партнер компании Durante & Vivan, Италия) предлагает отечественному потребителю двухкомпонентные клеи марок Dudipur D 12/4 (отвердитель Vildur L 202) и Dudipur D 14/3 (отвердитель Vildur L 202). Введение 3−5 мас. частей отвердителя Vildur L202 в 100 мас. частей основы обеспечивает теплостойкость готового клеевого соединения до 80 °С. «Если уменьшить количество отвердителя, то оно увеличивает время реактивации, но уменьшает теплостойкость конечной продукции», − отмечает специалист компании «Тул Лэнд» Павел Шульга.
Компания Forbo Industrial Adhesives (сокращенно − Forbo Adhesives) выпускает несколько видов двухкомпонентных клеев для мембранно-вакуумного прессования; на российском рынке представлены три марки. Клей swift tak 4335 − высококачественный продукт, используемый при запрессовке высокоглянцевых пленок. Его рекомендуется использовать при облицовывании деталей в тех случаях, когда требуется высокая тепло- и влагостойкость конечного изделия. Клей отличается высокой смачивающей способностью и при нанесении равномерно растекается по обрабатываемой поверхности. Клей swift tak 4336, характеризующийся малой вязкостью, − универсальный продукт, применяемый при изготовлении кухонных фасадов, арок, дверей и дверных декоративных элементов. Для его нанесения рекомендуется использовать форсунки диаметром от 1,2 до 1,5 мм, что обеспечивает равномерность нанесения и после облицовывания древесной плиты снижает риск появления эффектов «шагрени» или «апельсиновой корки».
Клей swift tak 4337 характеризуется низкой температурой реактивации (50−55 °C). Его применяют при облицовывании деталей высокоглянцевыми пленками. Среди плюсов этого клея его способность даже при избыточном нанесении равномерно распределяться по поверхности детали. При использовании swift tak 4337 для облицовывания древесных плит отечественного производства тонкими пленками поверхность детали выглядит ровной и гладкой.
Введение в основу отвердителя swift hardener 4547 или swift hardener 4547 blue повышает теплостойкость готового изделия. При использовании смеси 100 в. ч. клея swift tak 4335 и 5 в. ч. swift hardener 4547 достигается теплостойкость конечного изделия, близкая к 120 °C (оценка теплостойкости проведена по методике компании Forbo Adhesives). Жизнеспособность смеси − около 8 ч, она зависит от температуры помещения, в котором происходит операция отделки. При температуре выше 30 °C смесь следует израсходовать в течение четырех часов.
Из двухкомпонентных клеевых систем компании Jowat AG на российском рынке представлен клей «Йовапур 151.30», который можно применять как отдельно, так и с добавлением 5 в. ч. отвердителя «Йоват 195.40» на 100 в. ч. основы. По словам менеджера ООО «Йоват» (дочерней компании фирмы Jowat AG) Игоря Гресько, «качество деталей (их термо- и влагостойкость) сильно зависит от равномерного смешивания клея и отвердителя, поэтому при введении отвердителя рекомендуется использовать механические мешалки с соответствующими насадками и тщательно перемешивать смесь не менее десяти минут, не допуская возникновения пены. Термостойкость определяется по методике фирмы Jowat. Испытания проводятся после выдержки деталей в течение семи дней при нормальных климатических условиях».
Оцениваем качество клеевого соединения
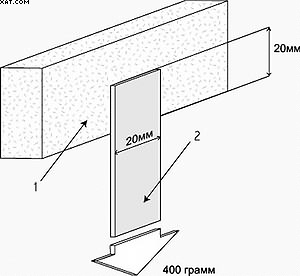
Образец для испытания клеевого соединения на
теплостойкость:
1 – жесткая подложка; 2 – мягкая подложка
Главный показатель качества продукции, полученной в результате использования 3D-технологии, − это теплостойкость. Чаще всего ее характеризуют температурой, при превышении которой происходит существенное снижение качества клеевого соединения. Методик определения теплостойкости множество.
Зарубежные компании-производители оценивают теплостойкость готовой продукции в соответствии с европейскими или немецкими стандартами. Технический директор компании Klebchemie в России и СНГ Ханну Саллинен говорит: «Единых стандартов оценки теплостойкости облицованной по 3D-технологии древесной плиты не существует. Но большинство компаний проводят тест по следующей методике. В термошкаф помещают образцы облицованной древесной плиты и при температуре 50 °С выдерживают один час. Затем образец вынимают и визуально оценивают, есть ли отслоение облицовочного материала от основы. Если на облицованной поверхности нет изменений, то деталь повторно помещают в термошкаф и выдерживают один час при температуре 60 °С. Эксперимент продолжают до обнаружения отслоения».
Александр Балашов (компания Forbo Adhesives Russia) поясняет: «Как правило, методики оценки теплостойкости разрабатывают компании − производители клеевых материалов, а также производители облицовочных материалов, прессового оборудования и готовых кухонь. Методика оценки теплостойкости клеев компании Forbo − это выдерживание образцов один час при температуре 50 °C в термошкафу. После этого образец исследуется визуально на наличие изменений − коробление пленки (складки, сдвиги, наплывы). Если коробление есть, то тест закончен. Если изменений нет, то температуру выдержки повышают на 10 °C и выдерживают образец один час, а затем вновь производят визуальный контроль, и так до тех пор, пока не появятся изменения».
Г-н Балашов рассказал также и о других методиках, которые могут использовать компании при оценке теплостойкости клеевого соединения.
Методика FIRA (Furniture Industry Research Association, Великобритания, − общество, занимающееся стандартизацией и независимой аттестацией мебельных комплектующих) такова. Образцы выдерживают в течение трех дней при температуре 40/50/60/70 °C и т. д. Если на их облицованной поверхности появляются изменения, то тест останавливают и фиксируют температуру, при которой наблюдалось это изменение.
Методика EMF (Vereinigung europдischer Mцbelfrontenhersteller − Объединение европейских производителей мебельных фасадов, Германия) сходна с методикой Forbo. Образец также выдерживают в течение часа в шкафу, а затем проводят визуальный контроль на наличие коробления. Допускается образование морщин пленки в пределах до 1 мм. Если сморщивание превышает это значение, то тест останавливают и фиксируют температуру.
По методике AMK (Arbeitskreis Moderne Kьche − объединение «Современные кухни», Германия) заготовку выдерживают в шкафу один час при 50 °C, далее один час при 60 °C, далее один час при 70 °C, затем один час при 75 °C, потом три часа при 75 °C, затем (по желанию) один час при 80 °C. Сморщивание пленки на канте принимается допустимым, если сдвиг не превышает 0,15 мм. Если пленка отслаивается или сдвиг превышает 0,15 мм, то тест останавливают и фиксируют температуру.
Сходны с вышеописанными методики Catas (Италия) и CTBA (Франция). В Австралии общество по использованию 3D-технологии называется ATLA, но данных по его методикам у российских поставщиков и производителей клеевых материалов пока нет. По словам г-на Балашова, «такие объединения, как EMF и AMK, сейчас работают над созданием общей методики контроля теплостойкости, однако этот документ будет носить лишь рекомендательный характер. Какие-либо нормативы вводить не планируется».
Еще об одной методике измерения теплостойкости клеевого шва рассказала продукт-менеджер ООО «Группа „ХОМА“» Екатерина Краснова. К образцу для испытаний, представляющему собой полоску облицовочного материала, приклеенную к основанию, подвешивают груз, создающий усилие сдвига в клеевом соединении, равное 0,1 кг/см2.
Образец закрепляют в держателе и нагревают инфракрасной лампой с облицованной стороны при одновременной фиксации температуры клеевого соединения. Температуру, при превышении которой разрушается клеевое соединение, принимают за показатель теплостойкости (Standard FHIS 141 WTZ Holz Dresden, Standard FHIS 145 WTZ Dresden). Метод можно применить и при испытаниях образца в сушильном шкафу, последовательно выдерживая образец в течение часа при разных температурах.
Есть и другой качественный способ оценки теплостойкости образцов, вырезанных прямо из готовой облицованной плиты или изделия. Такие образцы выдерживают при определенной температуре в течение часа, после чего анализируют качество клеевого соединения. Если оно не изменилось, то клеевое соединение можно считать стойким при данной температуре.
Расскажем подробно о том, как проводится это испытание. Отбор проб выполняют по ГОСТ 9980.2. В качестве оборудования для испытаний используют сушильный шкаф с регулировкой температуры с точностью ±2 °С; жесткую подложку прямоугольной формы произвольного размера, вырезанную из древесно-стружечной плиты (ДСП) толщиной 8−10 мм, которая применяется в мебельном производстве и отвечает требованиям, указанным в соответствующей нормативно-технической документации; мягкую подложку − полоску шириной 20±0,75 мм и длиной не менее 50 мм, вырезанную из пленки ПВХ, предназначенной для облицовывания мебельных фасадов методом мембранного прессования и отвечающую требованиям, указанным в нормативно-технической документации на нее; металлическую или деревянную подставку произвольной конструкции для размещения и закрепления образца; груз с устройством для его закрепления на свободном конце гибкой подложки (общей массой 400 г).
Для приготовления склеек полоска из пленки ПВХ приклеивается внахлестку к плоскости жесткой подложки, перпендикулярно одной из ее длинных сторон (см. рис.). Длина нахлестки должна быть 20 мм.
Образец закрепляют на подставке таким образом, чтобы плоскость склеивания и свободный конец пленки были направлены вертикально вниз.
К свободному концу пленки подвешивают груз и помещают подставку с образцом в сушильный шкаф, предварительно разогретый до выбранной температуры. Образец выдерживают при этой температуре в течение одного часа. Затем повышают температуру на 5 °С и выдерживают образец при этой температуре один час и т. д. Температуру продолжают повышать до тех пор, пока не разрушится клеевое соединение. После этого фиксируют максимальную температуру, предшествующую той, при которой произошло разрушение клеевого соединения.
В качестве показателя теплостойкости готового клеевого соединения принимают среднее арифметическое, выведенное по результатам трех измерений.
Наряду с методами лабораторного инструментального контроля, предполагающими применение специального оборудования, используются упрощенные методы, которые обычно применяют на производстве либо в лаборатории с привлечением простейшего лабораторного оборудования. Например, для быстрого анализа качества приклеивания жестких облицовочных материалов с помощью обыкновенной стамески облицовочный материал отделяют от основы и визуально оценивают этот участок плиты. При качественном склеивании разрушение происходит по материалу основы или облицовки. Такую оценку производят не раньше чем через сутки после склеивания.
Подводя итог, отметим, что клеи для 3D-облицовывания на основе водной дисперсии полиуретана пользуются большим спросом на отечественном рынке. Они экологически безопасны, обеспечивают высокую прочность клеевого соединения, стойкость клеевого слоя к пластификаторам (что важно при облицовывании мебели пленками ПВХ), повышают устойчивость пленок ПВХ к обесцвечиванию при действии ультрафиолета. При работе с клеевыми составами для технологий 3D-облицовывания существуют нюансы, которые необходимо учитывать. Один из критериев выбора этих клеев − теплостойкость клеевого соединения, которая определяет качество готовой продукции.
Следует также помнить, что клей − это лишь одна из составляющих технологического процесса, от которой, конечно, зависит качество конечной продукции, но получить высококачественное изделие можно только при строгом соблюдении всех основных требований 3D-технологии.
Екатерина МАТЮШЕНКОВА
Автор выражает благодарность продукт-менеджеру ООО «Группа „ХОМА“» Екатерине Красновой и
менеджеру и техническому консультанту компании Forbo Industrial Adhesives Russia Александру Балашову
за помощь в подготовке материала
Литература:
- Huber R. 3D Thermoform-lamination: High-gloss solution from Bürkle/Interior surfaces conference proceedings. − 2007. − P. 117−122.
- Шилз Дж. Клеящие материалы: справочник / пер. с англ. Ю. А. Гаращенко и др.; под ред. В. П. Батизата. − М.: Машиностроение. − 1980. − 360 с.
Менеджер по продажам и технический консультант компании Forbo Industrial Adhesives Russia
Александр Балашов:
− Несмотря на сравнительную популярность однокомпонентных (1K) полиуретановых дисперсий для мембранно-вакуумного прессования, многие ведущие производители кухонных фасадов и других элементов мебели предпочитают для облицовывания по 3D-технологии двухкомпонентные (2К) системы. Причину выбора этих систем каждый производитель мебели объясняет по-своему. Можно выделить следующие достоинства 2К-систем: по сравнению с 1К-системами они более стабильны во времени − меньше подвержены увеличению вязкости и снижению клеящей способности. Изменение свойств 2К-системы при длительном хранении на складе потребителя мало-вероятно, тогда как свойства 1К-системы, в состав которой введен отвердитель, к концу срока годности могут измениться. Несмотря на новые разработки с целью удешевления клеевых продуктов, при производстве 1К-систем используется более дорогое сырье, чем при изготовлении 2К-клеев. Кроме того, сама технология изготовления 1К-системы более затратна для производителей. Двухкомпонентный клей, как правило, дешевле, чем равноценная ему по характеристикам 1К-система. Для крупных потребителей, которым ежемесячно требуются тонны клея, разница в стоимости таких материалов имеет большое значение.
Даже если при работе с 2К-системами произойдет сбой из-за человеческого фактора (например, рабочие могут забыть добавить в состав клеевой смеси второй компонент − отвердитель), накопленный успешный опыт работы с двухкомпонентными системами позволит выправить положение. При приготовлении клеевого состава особо внимательным надо быть при добавке отвердителя к основе, а также следить за способностью 2К-системы к реактивации. При добавлении отвердителя к основе всегда стоит учитывать, что составляющие имеют, во-первых, разную вязкость, а во-вторых, разную структуру. Поэтому отвердитель следует добавлять постепенно, частями, непрерывно перемешивая состав для достижения максимальной гомогенизации 2К-системы.