ЛПК «АРКАИМ»: есть чем гордиться!
Проект лесоперерабатывающего комбината «Аркаим» (ЛПК «Аркаим»), расположенного в поселке Октябрьский Ванинского района Хабаровского края, стартовал в 2007 году и сразу вошел в число приоритетных инвестиционных проектов лесопромышленного комплекса региона. Его цель – производство продукции глубокой переработки древесины, основанное на комплексном использовании древесного сырья с применением современных безотходных технологий.
На более чем 100 га территории комбината работают лесопильное производство и производство ДСП, в 2011 году введены в эксплуатацию производство строганых пиломатериалов и пеллетное производство. В фазе пусконаладки находится третья очередь комбината – производство клееной балки и клееного щита из массивной древесины. Когда предприятие выйдет на полную мощность, объем переработки круглого леса составит 1,2 млн м3 в год. При этом вся древесина будет переработана в продукцию с высокой добавленной стоимостью, качество которой гарантировано использованием современных технологий обработки древесины, эксплуатацией оборудования ведущих европейских производителей и высоким уровнем организации труда. Серьезные конкурентные преимущества предприятия – доступность сырья, наличие морского порта и близость к азиатским рынкам. Потребителями продукции комбината уже стали фирмы из Японии, Китая, Кореи и Европы.
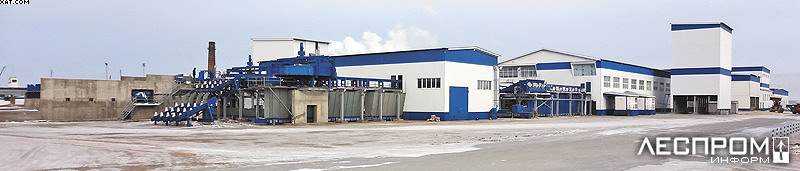
Общий вид лесопильного цеха ЛПК «Аркаим»
История проекта ЛПК «Аркаим»
ЛПК «Аркаим» расположен на территории бывшего Коппинского лесоперерабатывающего комбината, который еще в 1998 году объявил себя банкротом. К 2006 году большинство зданий на площадке было разрушено, а оборудование подлежало утилизации. Сегодня о прошлом комбината напоминает только кирпичная дымовая труба прежней котельной, которую строители оставили как своеобразный памятник советской эпохе. С начала проекта в оборудование и строительство было инвестировано $0,5 млрд. Кроме основных производственных зданий, на площадке построены: бытовой комплекс, гостиница, столовая, пожарная часть, электроцех, склад материалов, столярный цех, гараж и станция техобслуживания грузовой техники. Для обеспечения предприятия электроэнергией была реконструирована подстанция «Ванино», а также построены подстанция «Лесозавод» и десятикилометровая ЛЭП мощностью 110 кВт.
Идея реализации этого крупного инвестиционного проекта принадлежит учредителю и собственнику предприятия Александру Лепихову. В соответствии с разработанной им стратегией развития СП «Аркаим», начинавшее свою деятельность еще в 1993 году, было превращено в крупный промышленный холдинг, осуществляющий работы на всех этапах реализации проекта без привлечения посредников. Доход от заготовки, вывозки и продажи древесины на первом этапе стал основным источником средств для погашения кредитов и пополнения оборотных средств. Для закупки и обслуживания лесозаготовительной и строительной техники был создан собственный дилерский и сервисный центр. Для возведения ЛПК «Аркаим» были выкуплены активы Хабаровского завода металлоконструкций и создана строительная фирма, для выполнения перевозок приобретены железнодорожные платформы, а потом и морские суда. Таким образом, была создана инфраструктура, обеспечивающая эффективность работы компании и возможность ее развития.
Для реализации проекта потребовались поставки качественного деревообрабатывающего оборудования европейских производителей, – для планирования и координации поставок оборудования, его монтажа и выхода на проектную производительность «Аркаимом» была выбрана немецкая инжиниринговая компания Kornak GmbH, у руководителя которой, опытного инженера Эдуарда Кюстера, большой опыт строительства крупных деревообрабатывающих предприятий в России. Специалистами инжиниринговой компании были сформированы технические требования к технологическим линиям, выбраны изготовители оборудования, предложившие оптимальное сочетание качества и цены, а также приемлемые сроки изготовления, и подготовлены контракты на поставку оборудования.
В обязанности инжиниринговой компании вошли также контроль сборки и монтажа оборудования, осуществление взаимодействия поставщиков с представителями строительных и монтажных организаций. Это позволило реализовать проект последовательно и без простоев – после завершения одного этапа сразу шел другой.
Финансирование проекта началось в 2007 году, а через 21 месяц объект первой очереди строительства – лесопильный завод – был сдан в эксплуатацию. Осенью 2009 года лесопиление уже вышло на проектную мощность, такие сроки для России можно назвать рекордными. Проектирование последующих этапов велось одновременно со строительством. С одной стороны, это позволило сократить сроки реализации проекта, а с другой – дало возможность проектному менеджменту оперативно реагировать на решения, принимаемые в ходе строительства. Для запуска завода требовалась экспертиза проектной документации, выполненной по российским нормам, в Хабаровске не нашлось компании, способной подготовить такую документацию, поэтому в службе заказчика был создан проектный отдел, который выполнил адаптацию проекта.
Строительство комбината было реализовано в три этапа. На первом этапе было смонтировано оборудование и запущены первая очередь лесопильного производства и завод ДСП. В финансировании проекта принимали участие Сбербанк и финансовая группа ВТБ. Второй этап строительства – завод строганых пиломатериалов, вторая очередь лесопильного производства и пеллетное производство – был реализован при поддержке банка «Возрождение». Третий этап – заводы по выпуску клееной балки и клееного бруса – при поддержке Внешэкономбанка.
На площадке деревообрабатывающего комбината расположены шесть самостоятельных производств, на которых осуществляется полный цикл переработки древесины. Учитывая масштабы производств, каждое из них можно назвать отдельным заводом. Все заводы объединены общими инженерными сетями, дорогами, обслуживаются от единой тепловой сети и являются частями одной технологической цепочки. Лесопильный завод, с которого началось строительство комбината, стал поставщиком сырья для завода ДСП и пеллетного завода, также он снабжает котельную комбината древесным топливом – отходами деревообработки, образующимися при окорке и распиловке круглого леса. Основная часть продукции лесопильного производства направляется на глубокую переработку – на завод строганых пиломатериалов, клееной строительной балки и клееного щита. Отходы этих производств также являются сырьем для пеллетного производства. В то же время технологические линии всех шести производств построены таким образом, чтобы уменьшить их зависимость друг от друга и повысить гибкость производства как по сырью, так и по готовой продукции. Пеллетное производство может работать как на влажных отходах лесопиления, так и на сухих отходах деревообработки или на круглом сырье, а заводы глубокой переработки могут выпускать продукцию как для европейского рынка, так и для рынков Японии, Южной Кореи, Китая. Такой подход позволяет быстро реагировать на изменения в рыночной ситуации и эффективно управлять распределением ресурсов, к тому же облегчает финансовый учет. Например, по финансовой модели лесопильный завод продает пиломатериалы строгальному заводу, а строгальный завод продает свои отходы на пеллетный завод.

Обслуживание транспорта на ЛПК «Аркаим»
Лесопиление ЛПК «Аркаим»

Лесопильный цех
В лесах Хабаровского края преобладают хвойные породы – лиственница, ель, пихта, представляющие ценное сырье для глубокой переработки. Лесосеки «Аркаима» находятся в Комсомольском, Нанайском, Ванинском и Советско-Гаванском районах. Заготовка леса ведется в основном в гористой местности, до 15% древесины приходится забирать из труднодоступных мест, поэтому иногда применяется трелевка древесины канатными установками. Доставка пиловочника на комбинат осуществляется в основном автотранспортом, а плечо доставки составляет около 150–200 км. У «Аркаима» мощное лесозаготовительное подразделение, укомплектованное современной техникой, которое обеспечивает бесперебойные поставки сырья, что позволяет работать без промежуточных или сезонных складов сырья. На «Аркаиме» используется пиловочник диаметром от 10 до 45 см (средний диаметр 19 см), древесина (в основном это лиственница) очень плотная и смолистая, что потребовало применения оборудования в тяжелом исполнении и специально подготовленного инструмента.
Первая очередь лесопильного цеха, введенная в эксплуатацию в 2009 году, включает в себя линию сортировки круглых лесоматериалов, фрезерно-профилирующую лесопильную линию, линию сортировки сырых пиломатериалов, линию пересортировки сухих пиломатериалов и линию автоматического возврата сушильных прокладок. Причем возврат прокладок был предусмотрен таким образом, чтобы можно было установить в дальнейшем вторую линию сортировки сырых пиломатериалов. Производительность первой очереди по проекту – 400 тыс. м3 лесоматериалов в год. Но за счет повышения эффективности эксплуатации – снижения времени запланированных остановок и увеличения общего времени работы – предприятие смогло выйти на производительность 500 тыс. м3.
Весь пиловочник, поступающий на площадку, сортируется по размерно-качественным параметрам, что позволяет оптимально использовать возможности линий лесопиления и сортировки пиломатериалов. Оборудование для сортировки пиловочника (производитель – компания Holtec) изготовлено в тяжелом исполнении с учетом суровых климатических условий, в которых оно эксплуатируется. Линия оборудована 56 сортировочными карманами и рассчитана на скорость сортировки 100 м/мин. Пост управления, помещение под электрооборудование, гидравлику и систему измерения изготовлены в Германии в виде модулей, что позволило сократить сроки монтажа и минимизировать возможные ошибки. Все модули оснащены системой кондиционирования и отопления.
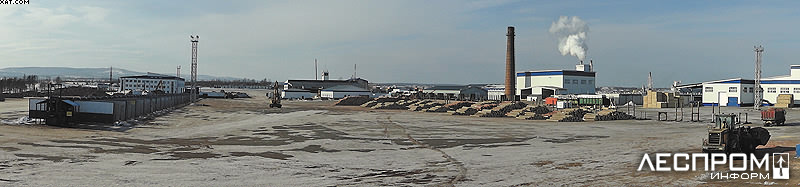
Линия сортировки бревен на ЛПК «Аркаим»
Отсортированный пиловочник подается погрузчиком на накопительный стол линии окорки и подачи Holtec. Сортименты разобщаются, разворачиваются на поворотном устройстве и подаются вершиной вперед в окорочный станок Valon Kone VK550-Combi-3R. Станок оснащен двумя окорочными роторами типа 620, а также оцилиндровочным ротором для оцилиндровки комлевой части бревна. Оцилиндровка комля облегчает дальнейшую обработку бревен в лесопильной линии. Окорочный станок оснащен гидравлическим механизмом прижима ножей. Для облегчения ремонта ножи снабжены сменными режущими пластинами. Максимальная скорость VK550-Combi-3R с роторами типа 620 с гидравлическим прижимом ножей составляет около 100–120 м/мин. На поперечном транспортере после окорки накапливается некоторое количество окоренных сортиментов, так называемый буферный запас, гарантирующий ритмичную подачу сортиментов к лесопильной линии даже при кратковременной остановке оборудования для окорки.
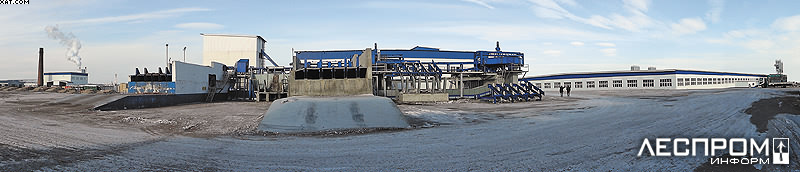
Загрузка бревен в цех
В лесопильном цехе установлена высокопроизводительная фрезернопрофилирующая линия EWD. Линия построена из нескольких агрегатов, которые последовательно выполняют фрезерование и распиловку сортимента на обрезные доски. В зависимости от диаметра на линии можно получать до 8 боковых досок на одном бревне. Распиловка ведется на скорости до 150 м/мин в летний период и до 120 м/мин зимой. В холодное время года на обработку поступает в основном замороженная древесина, т. е. более плотная, чем «летняя», что требует больших затрат энергии на резание. Линия функционирует полностью в автоматическом режиме, оператор только контролирует работу механизмов. На линии одновременно работают два оператора – ввиду высокой информационной нагрузки они меняются местами каждые два часа, один из них постоянно находится за пультом, в шумоизолированной операторской, а другой – в цехе, где контролирует работу оборудования. Для предприятия с такой производительностью, как «Аркаим», очень важен устойчивый ритм работы, а простой оборачивается значительными финансовыми потерями, поэтому одна из главных задач обслуживающего персонала – предупреждение возникновения нештатных ситуаций с помощью постоянного контроля и проведения обслуживания по регламенту.
Весной 2012 года в лесопильном цехе введена в производство лесопильная линия второй очереди. Это также фрезерно-профилирующая агрегатная линия EWD. Вторая лесопильная линия ориентирована на распиловку тонкомера и рассчитана на переработку пиловочника диаметром от 12 до 28 см, хотя при необходимости может быть загружена сырьем с диаметром до 35 см в вершине. Набор агрегатов на линии обработки тонкомера следующий: фрезерно-брусующий станок, устройство поворота бревна, фрезерно-брусующий станок, комбинированный профилирующий и делительный агрегат, затем опять поворотное устройство и агрегат для профилирования боковых досок. Далее профилированный брус направляется в многопильный станок. Отличие этой линии от первой состоит в том, что на ней может быть выпилено не более четырех боковых досок (на первой линии – до восьми боковых досок), а в конструкции последнего многопильного агрегата предусмотрена возможность оперативного изменения постава, что выгодно при распиловке небольших партий пиломатериалов. Скорость подачи на этой линии – до 100 м/мин.
Монтаж второй лесопильной линии потребовал установки дополнительной линии подачи и окорки сырья, которая по набору агрегатов соответствует линии первой очереди, но выполнена в зеркальном исполнении. Расчетная мощность второй лесопильной линии – до 500 тыс. м3 круглого леса в год. Таким образом, планируется, что после выхода на проектную мощность второй очереди лесопиления завод будет обрабатывать до 1,2 млн. м3 лесоматериалов в год. Производство работает в двухсменном режиме, с удлиненными (до 10 ч) сменами. Четыре часа в сутки отводятся на профилактику в соответствии с картами обслуживания и на плановую замену инструмента. Кроме ежедневной профилактики, на лесопильных линиях проводятся еженедельные, ежеквартальные и ежегодные регламентные работы.
Лесопильные линии установлены параллельно в двухпролетном цехе. Между линиями размещены бытовые и технические помещения. Такая компоновка весьма удобна, поскольку позволяет уменьшить длину коммуникаций.
Заточной участок в лесопильном цехе оснащен полным комплектом автоматических станков, в основном это станки Vollmer. При комплектовании заточного участка оборудованием была поставлена задача минимизировать влияние т. н. «человеческого фактора» на обслуживание инструмента и максимально экономить ресурс режущего инструмента. Поэтому здесь используется профессиональное оборудование для автоматической заточки круглых пил, их правки и напайки твердосплавных зубьев на полотна дисковых пил индукционным способом. Основные станки оснащены масляной системой охлаждения, включая автоматическую станцию регенерации масла, что гарантирует длительную и надежную эксплуатацию оборудования. Такие станки применяются в том числе в сервисных центрах и на заводах – изготовителях инструмента. Заточное оборудование подготовлено с учетом того, что предприятие работает с лиственницей: например, для отмывания пил от смоляных отложений используется специальная ультразвуковая машина.
На участке обработки отходов, который расположен в пристроенном к лесопильному цеху помещении, используется оборудование компании Vecoplan, рассчитанное на переработку до 900 насыпных кубов в час. Отходы распиловки – щепа и опилки – собираются скребковыми транспортерами, установленными на «первом этаже» лесопильного цеха, и направляются на участок сортировки щепы. Здесь находятся три вибросита, которые разделяют отходы на три фракции: кондиционную технологическую щепу, опилки и крупные кусковые отходы. Кусковые отходы измельчаются барабанной рубительной машиной, щепа от которой снова подается на сортировку, а кондиционная щепа и опилки с отсевом поступают в накопительные бункеры. На пеллетное производство и производство ДСП отходы лесопиления сейчас подаются автотранспортом. Изначально рассматривался вариант установки табуляторов для транспортирования отходов, однако из-за значительной стоимости их установку решили пока отложить.
Сортировка пиломатериалов ЛПК «Аркаим»
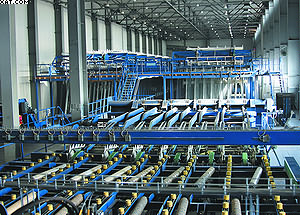
Участок сортировки сырых пиломатериалов на
ЛПК «Аркаим»
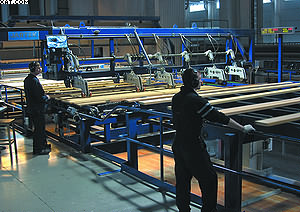
Сканирование пиломатериалов на линии сортировки
Jartek на ЛПК «Аркаим»
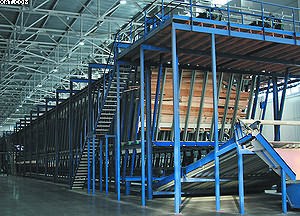
Линия сортировки сухих пиломатериалов на ЛПК
«Аркаим»
После распиловки пиломатериалы подаются на участок сортировки. Здесь установлены две линии сырой сортировки производства финской компании Jartek, в каждой из которых 40 сортировочных карманов. Максимальная расчетная производительность каждой лесопильной линии – 180 досок в минуту, средняя производительность в течение одной смены составляет 150 шт./мин.
На «Аркаиме» доски, выпиленные из центральной части бревна, наиболее толстые и боковые доски (как правило, тонкие) транспортируются от лесопильных агрегатов раздельно и подаются на разные линии сортировки. Такой подход позволяет увеличить скорость сортировки и облегчает настройку линии, поскольку все механизмы могут быть настроены на определенный диапазон толщины досок.
Линии сортировки, как и лесопильные потоки, работают в полностью автоматическом режиме. Каждая доска сканируется последовательно со всех сторон для определения пороков древесины и назначения сорта, причем сорт назначается по пласти с худшим качеством. Установленная на этих линиях система сканирования FinScan в числе прочих пороков определяет и червоточину.
После определения сорта и геометрических размеров пиломатериалы раскладываются по сортировочным карманам, каждый из которых оборудован устройством минимизации высоты падения материала. Из сортировочных карманов пиломатериалы партиями подаются на линию штабелирования, где происходит автоматическое формирование сушильных штабелей.
В этом же цехе установлена линия пересортировки сухих пиломатериалов на 50 карманов (производитель – компания Jartek). Штабели высушенных пиломатериалов доставляются сюда от сушильных камер автопогрузчиками. Линия сухой сортировки также полностью автоматизирована – сушильные штабели разбираются на доски, которые так же, как и на линиях сырой сортировки, проходят автоматическое сканирование. После прохождения датчиков определения пороков и геометрических размеров в соответствии с заданной программой выполняется поперечный раскрой пиломатериалов. Управляющая программа может выдавать команды оборудованию для оптимизации раскроя как по объемному выходу, так и по ценовому критерию.
Высокой эффективности производства способствует и использование оборудования для автоматического возврата сушильных прокладок, установленное в сортировочном цехе. Линия, состоящая из системы транспортеров и штабелеров, собирает прокладки, освобождающиеся при разборке штабелей высушенных пиломатериалов, и возвращает их к месту формирования новых сушильных штабелей. Поскольку площадь, занятая сортировочным оборудованием, весьма внушительная – более 3 тыс. м2, то для уборки мусора под всеми сортировочными линиями установлены скребковые транспортеры.
Сушильно-котельный комплекс ЛПК «Аркаим»

Сушильные камеры Muehlboeck Vanicek на ЛПК «Аркаим»
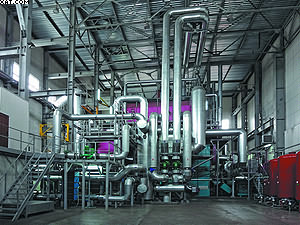
Котельное оборудование Polytechnik на ЛПК «Аркаим»
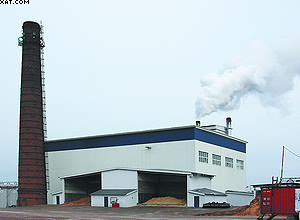
Котельная с независимыми топливными складами на ЛПК «Аркаим»
Площадь сушильного комплекса «Аркаима» – почти 5 га. Здесь размещены 46 камер периодического типа Mühlböck Vanicek общим объемом 9560 м3 (объем каждой камеры – 208 м3 при расчетной толщине доски 40 мм). Выбор типа камер обусловлен спецификой предприятия: в сушку поступают доски разного сечения, партиями разного объема, предназначенные для сушки до разной влажности. Кроме того, здесь сушится большое количество древесины лиственницы, которая, как известно, сушится почти в два раза дольше, чем других хвойных лесоматериалов – сосны и ели – и подвержена растрескиванию и короблению. В этих условиях предпочтительно использовать камеры периодического действия, поскольку они легче поддаются регулированию и более гибкие при настройке режима сушки.
Тепло для сушильных камер, а также для нужд систем отопления и вентиляции вырабатывается в котельной, расположенной рядом с сушильным комплексом. В здании котельной установлены два 10-мегаваттных котла австрийской компании Polytechnik, предназначенные для сжигания влажного древесного топлива. Каждый котел запитан от своего склада топлива, это делает котлы независимыми друг от друга и позволяет более гибко подходить к настройке режима сжигания.
Конструкция топок котлов дает возможность использовать в качестве топлива только кору, однако при сжигании коры лиственницы в топке образуются крупные куски шлака, поэтому желательно добавлять в такое топливо небольшое количество опилок или щепы.
В холодное время года около 25% мощностей котельной расходуется на отопление и вентиляцию зданий. В летний период для обеспечения работы сушильных камер достаточно тепловой мощности одного котла, поэтому котлы по очереди останавливают на профилактику. На обслуживание котла уходит несколько дней – сначала котел остывает, потом требуется от трех до пяти дней для его чистки, после чего необходимо вывести котел на рабочую температуру. Нормальным считается увеличение температуры на 30 градусов в час, таким образом, для достижения температуры 600 °С нужно 20 ч. Эта температура выдерживается 8 ч, чтобы мощная каменная кладка внутри котла (футеровка) равномерно прогрелась, не испытывая экстремальных нагрузок от теплового расширения.
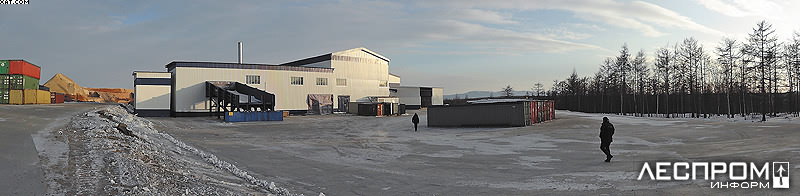
Промплощадка ЛПК «Аркаим»
Пеллетное производство ЛПК «Аркаим»
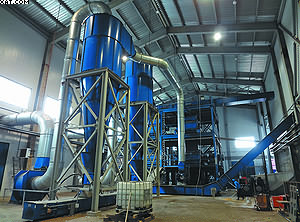
Участок измельчения сырья пеллетного производства на ЛПК «Аркаим»
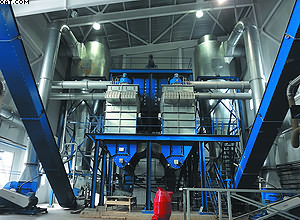
Выгрузка измельченного сырья для производства пеллет из дробилок осуществляется шнековыми конвейерами и пневмотранспортной системой. ЛПК «Аркаим»
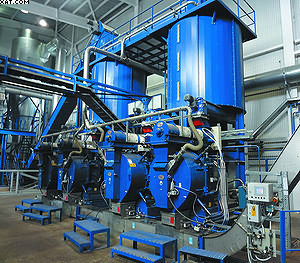
Линия гранулирования на ЛПК «Аркаим». Производительность – 20 тонн пеллет в час
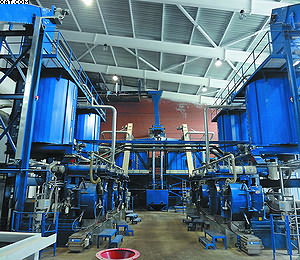
Участок гранулирования на ЛПК «Аркаим». На заднем плане – охладители гранул
В начале этого года на «Аркаиме» запущен завод по производству пеллет. Проектная мощность завода – 240 тыс. т готовой продукции в год. Все технологические линии на комбинате укомплектованы оборудованием исходя из условия максимальной гибкости производства. Не стал исключением и пеллетный завод – по требованию заказчика была обеспечена максимальная гибкость производства в отношении сырья. В технологической цепочке предусмотрены три независимые линии подачи сырья: для круглого леса, для влажной измельченной древесины (отходов лесопиления) и для сухой древесины (отходов деревообработки). Таким образом, на пеллетирование могут быть поданы не только измельченные отходы производства, но и низкосортная древесина, непригодная для лесопиления.
У пеллет, произведенных из окоренных лесоматериалов, небольшая зольность, они востребованы на рынке, поэтому в линию подачи круглого леса, установленную на предприятии компанией Holtec, включен окорочный станок барабанного типа, который, в отличие от роторных станков, эффективен при окорке сильно искривленных или коротких материалов.
Щепа из низкосортной древесины или щепа из лесопильного цеха и опилки подаются на участок измельчения сырья. Причем щепа и опилки подаются разными транспортерами – это необходимо для оптимизации сушки. На транспортер, доставляющий материалы на участок измельчения, щепа и опилки подаются в определенном соотношении, что позволяет регулировать качество смеси. На участке измельчения установлены две высокопроизводительные молотковые мельницы ZEG, тип USZ 08-1250/2700. В них сырье измельчается до фракции 15 мм и перемешивается. Разгрузка мельниц выполняется шнековыми транспортерами на конвейер, доставляющий подготовленное сырье в сушильный барабан. Аспирационная система участка измельчения изготовлена компанией Scheuch. Задача этой мощной системы механизации – приготовить однородную смесь с постоянными влажностными и размерными параметрами, чтобы участок сушки работал в одном режиме, с максимальной производительностью, поскольку в этом процессе нет ничего сложнее, чем перенастройка барабанной сушилки.
Сушка предварительно измельченного сырья выполняется в сушильном барабане, в потоке горячих топочных газов, вырабатываемых теплогенератором. По сути, теплогенератор – это полноценная котельная мощностью 25 МВт, в которой присутствует теплообменник (водонагреватель) мощностью 3 МВт для передачи остаточного тепла в общую теплосеть ЛПК. Топливом для теплогенератора является влажная измельченная древесина, в том числе и кора. Оборудование участка сушки поставлено компанией Buttner.
Измельченное и высушенное до влажности около 9% сырье поступает в цех пеллетирования. Генеральный поставщик оборудования цеха – австрийская фирма Knoblinger. В цехе расположены две линии окончательного измельчения, гранулирования и охлаждения, скомпонованные зеркально, производительность каждой – 20 т пеллет в час. На каждой линии установлены четыре пресса-гранулятора американской компании CPM (California Pellet Mill Co.) мощностью 5 т в час каждый. В прессах CPM используются приводные вертикальные кольцевые матрицы и парные ролики, свободно вращающиеся вокруг своей оси, у прессов прямой зубчатый привод, они просты в эксплуатации и ценятся за надежность. Грануляторы CPM широко распространены, они изготавливаются в том числе европейским подразделением компании CPM Europe и собираются на заводе в Амстердаме, поэтому трудностей с их сервисным обслуживанием не возникает.
Готовые пеллеты складируются навалом в складах, пристроенных к пеллетному цеху, объем которых достаточен для накопления судовой партии. По желанию заказчика, пеллеты могут быть упакованы в биг-бэги или пластиковые пакеты. Высокая производительность пеллетного завода и близость предприятия к морскому порту позволили «Аркаиму» заключить контракты на поставку пеллет на крупнейшие энергостанции Японии.
Строганные пиломатериалы ЛПК «Аркаим»
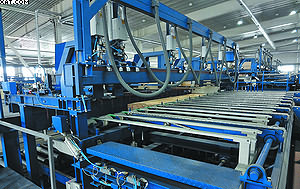
Линия сортировки строганных пиломатериалов на ЛПК «Аркаим»

Линия штабелирования строганных пиломатериалов на ЛПК «Аркаим»
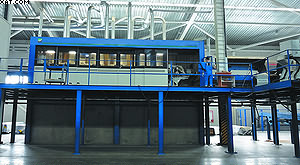
Четырехсторонний строгальный станок Weinig Powermat 2500 на ЛПК «Аркаим»
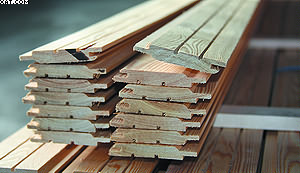
Строганные пиломатериалы
В цехе строганых пиломатериалов установлены две производственные линии – строгания пиломатериалов и оптимизации низкосортных пиломатериалов с последующим сращиванием их по длине. Пиломатериалы высокого качества сразу поступают на линию профилирования, а пиломатериалы 4–5 сортов направляются на линию оптимизации, где после удаления дефектов их сорт повышается до 2–3-го.
Производительность линии оптимизации – до 70 тыс. м3 срощенных пиломатериалов заданного качества. Сюда подается сырье влажностью 10±2%. Разброс влажности пиломатериалов не должен превышать 2%, поэтому все сырье проходит через устройство контроля влажности, которое отбраковывает слишком влажный или слишком сухой материал. После чего пиломатериалы калибрируются с четырех сторон на станке Weinig Hydromat 2000, для вскрытия дефектов и придания требуемых геометрических размеров. Подготовленные таким образом ламели проходят через сканер Microtec Goldeneye 501, который определяет пороки, недопустимые в продукции, и дает команду двум высокопроизводительным торцовочным установкам Weinig OptiCut 450 Quantum вырезать дефекты. Удаленные дефектные участки утилизируются, а качественные ламели сортируются и направляются на линию сращивания по длине компании NKT. Ламели сортируются не только по качеству, но и по оттенку – изготовленный таким способом материал имеет равномерный тон и заданное качество.
Линия строгания, установленная в строгальном цехе, предназначена для изготовления практически любых типов погонажных изделий, но ориентирована в основном на производство террасной доски из лиственницы. Мощность линии – 180 тыс. м3 готовой продукции в год при двухсменном режиме работы. Все пиломатериалы перед профилированием проходят контроль влажности. Кондиционные пиломатериалы при необходимости торцуются на заданную длину, автоматически переворачиваются кривизной вверх и подаются в четырехсторонний строгальный станок Weinig Powermat 2500, оснащенный десятью шпинделями (максимальная скорость подачи – 250 м/мин). Это третий станок данной модели, произведенный компанией Weinig. Два первых станка были поставлены в Германию и Австрию и хорошо себя зарекомендовали. Модель считается очень удачной среди высокопроизводительных станков.

Общий вид цеха строганных пиломатериалов на ЛПК «Аркаим»
Строганые пиломатериалы сортируются на три класса (сорта) по качеству и брак – в соответствии с требованиями европейских покупателей. Качество погонажа определяется сканером Microtec Goldeneye 701 в автоматическом режиме. Сканер определяет наличие и размер сучков, смоляных кармашков, трещин и других пороков древесины на всех сторонах изделия и назначает сорт в соответствии с заданными параметрами качества. Отсортированный материал системой транспортеров распределяется на три автоматические линии штабелирования и упаковки. Готовые изделия складываются в полноразмерные пакеты или пачки (мини-пакеты) по 9–12 шт., которые упаковываются в полиэтиленовую пленку. В смену в цехе работает всего 20 человек, включая управляющий и обслуживающий персонал (на оптимизации работает пять человек, а на линии профилирования – девять). Мощные системы механизации, необходимые при высоких скоростях обработки, позволяют уменьшить влияние человеческого фактора, что в конечном итоге гарантирует постоянное качество продукции.
Клееные конструкции ЛПК «Аркаим»
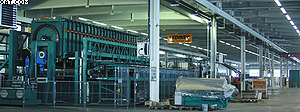
Пресс Ledinek для производства клееных балок на ЛПК «Аркаим»
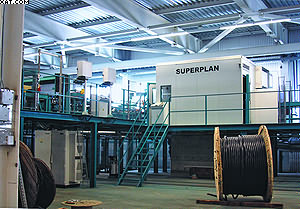
Строгальный станок Ledinek Superplan на ЛПК «Аркаим»
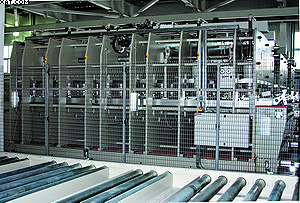
Пресс Italpress для производства клееного щита
На ЛПК «Аркаим» в фазе пусконаладки и выхода на проектные мощности находятся еще два цеха – по производству строительной клееной балки и клееного щита из массивной древесины. Цехи укомплектованы новейшим высокопроизводительным оборудованием. Например, на производстве клееного бруса система определения качества пиломатериалов оснащена несколькими установками, в том числе и рентгеновским сканером, что позволит с высокой степенью достоверности сортировать пиломатериалы по прочности. В цехе расположены линия сортировки пиломатериалов по качеству и прочности и две линии изготовления клееной балки – для европейского и японского рынка. Это разные продукты, поэтому для них построены самостоятельные линии. Отличие состоит в размерах сечения, в требованиях к прочностным характеристикам продукции и длине продукта. Для европейского рынка будут производить балку, в том числе криволинейную, длиной до 36 м, в то время как для японского рынка будут выпускать короткие балки длиной до 12 м. Оборудование, установленное в цехе, позволит изготавливать до 100 тыс. м3 клееных балок в год. Выпуск продукции начался в апреле этого года.
Через 2–3 месяца планируется запустить цех по производству клееного щита из массивной древесины, его проектная мощность составляет 70 тыс. м3 в год. В цехе будут изготавливать как однослойный, так и многослойный клееный щит. Здесь так же, как и в цехе строгания, будет производиться вырезание дефектов древесины, сращивание пиломатериалов по длине и их автоматическая сортировка. Установленное в цехе оборудование позволяет автоматически подбирать ламели по качеству и тону древесины, благодаря чему упрощается выпуск щитов с определенным качеством поверхности для каждой стороны. Планируется выпуск клееных деревянных щитов длиной до 6 м и шириной до 1,5 м, которые могут использоваться как в мебельной промышленности, так и в строительстве.
Оборудование для цеха строительной балки поставлено компаниями Ledinek, NKT и Microtec, в цехе клееного щита установлены строгальные станки компании Weinig, торцовочные станки и механизация датской фирмы System TM, прессы для однослойных щитов Torwegge, для многослойных – Italpress, линии сращивания компании NKT, аспирационные системы Scheuch.
Вместо заключения
Организация производства на «Аркаиме» очень жесткая – каждый знает, за какой участок он отвечает. Все работы запланированы и регламентированы, для их выполнения установлены определенные сроки. Регламентированы даже уборочные работы, причем их график согласовывается с технологами таким образом, чтобы не мешать производственному процессу. Для полноценного отдыха на предприятии созданы замечательные бытовые условия. На территории комбината работает столовая с разнообразным и недорогим меню. Для иностранных рабочих (монтажников, наладчиков оборудования), а также для гостей предприятия построена гостиница. Бытовые и офисные помещения отделаны качественными материалами и оборудованы необходимой бытовой техникой.
Работает служба развозки сотрудников. Сотрудники переодеваются в рабочую одежду в специальных гардеробных, устроенных на манер медицинских санпропускников. Между гардеробами установлены душевые кабины. Для стирки рабочей одежды оборудовано специальное помещение, в котором установлены промышленные стиральные машины.
«Аркаим» – не только успешный инвестиционный проект, комбинат выполняет важную социальную функцию. На заготовке, транспортировке и переработке древесины занято 1800 человек. Благодаря комбинату, который имеет статус градообразующего предприятия, в Ванинском районе развивается инфраструктура, возрождены лесопиление и деревообработка.
Уникальность «Аркаима» состоит в том, что этот крупный проект, стартовавший с нуля и получивший развитие в период кризиса, когда многие предприятия закрывались, показал свою эффективность – запланированные этапы строительства и развития реализуются в короткие сроки.
Проект стал успешным прежде всего благодаря грамотным организационным решениям, основанным на комплексном использовании ресурсов, применению современных технологий и новейшего оборудования, а также высокому уровню организации труда. Можно гордиться тем, что на Дальнем Востоке России построен, работает и развивается один из самых современных в мире деревообрабатывающих комбинатов, поставляющих конкурентную продукцию не только в Азию, но и в Европу.
Виталий ТИКАЧЕВ
Справка
ООО СП «Аркаим» было образовано в 1993 году. Компания начинала свою деятельность с заготовки леса, и сегодня это направление остается одним из основных в ее работе. Заготовленная древесина перерабатывается на лесоперерабатывающем комбинате компании, расположенном на берегу Татарского пролива, рядом с морским торговым портом Ванино. Значительная часть грузов перевозится собственным флотом компании, состоящим из четырех сухогрузов водоизмещением от 6 до 10 тыс. т.
Древний Аркаим
Аркаим – укрепленное поселение эпохи средней бронзы рубежа III–II тысячелетий до н. э., получившее свое название от горы, возвышающейся над местностью, и случайно обнаруженное в 1987 году на юге Челябинской области. Раскопки позволили реконструировать архитектуру и быт горожан, но многие факты до сих пор остаются загадкой. С Аркаимом связано много легенд, возможно, этот археологический памятник является самым таинственным на территории России. Город имеет кольцевую структуру и четко сориентирован по звездам. Часто его называют не городом, а сооружением, которое было сначала задумано, потом вычерчено с мельчайшими деталями и только затем построено.
Город был построен и жил по законам астрологии, законам космоса. Большая часть жизни людей протекала за пределами оборонительных сооружений, в долине. Горожане жили в гармонии с природой, занимались выпасом скота, заготовкой древесины для строительства и отопления, добычей руды. Имущественного и социального расслоения не было, все люди были равны. Не случайно Аркаим часто сравнивают с самой знаменитой и прекрасной утопией европейского Средневековья – Городом Солнца, придуманным Томмазо Кампанеллой. Работающая на Дальнем Востоке компания «Аркаим» взяла свое название в честь этой прекрасной легенды, а образ Города Солнца получил отражение в ее логотипе.
ЛесПромИнформ №2 (108), 2015 г. Что ожидает «Аркаим»?
ЛесПромИнформ №8 (82), 2011 г. «Аркаим» наращивает мощности
Автор: Виталий ТИКАЧЕВ