«АКБ-11» - Ладожский завод клееных деревянных конструкций
Принято считать, что в лесопромышленном комплексе эффективно работать могут только крупные предприятия, поскольку они конкурентоспособны на внутреннем и мировом рынке за счет больших объемов производства, обеспечивающих низкую себестоимость продукции. Вместе с тем в сегменте деревянного домостроения есть множество малых предприятий, эффективно сотрудничающих с девелоперскими компаниями и крупными производствами и предлагающих на рынке дома по индивидуальным проектам с использованием современных технологий проектирования, изготовления домокомплектов и строительства.
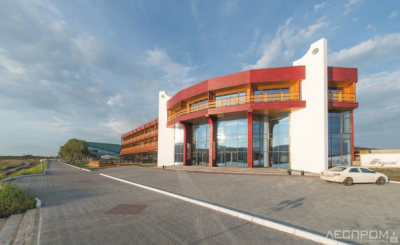
Одной из таких компаний является архитектурно-конструкторское бюро «АКБ-11», основанное в 2008 году на базе завода по изготовлению клееного бруса «Древпродукт» в г. Стерлитамаке (Республика Башкортостан). Первое время компания занималась только разработкой проектно-сметной документации, проектированием сооружений из клееного бруса, а также подготовкой исполнительных файлов для станков Hundegger.
В 2009 году специалисты архитектурного бюро начали проектировать жилые здания из древесины, а также освоили технологию изготовления фахверковых домов. За три года работы было спроектировано по индивидуальным проектам более 70 домов, которые были построены в разных регионах России.
В 2011 году в связи с реконструкцией завода «Древпродукт» компания «АКБ-11» была переведена в г. Тверь, где стала сотрудничать с заводом «Интер-Древ». Накопившийся опыт позволил расширить номенклатуру проектируемых зданий, и заказчикам предлагалась разработка проектов ресторанов и баз отдыха, а также услуги шефмонтажа. В 2012 году, после обучения в Швеции, специалисты «АКБ-11» по технологии возведения многоэтажных деревянных домов спроектировали и изготовили на заводе «Интер-Древ» трехэтажную гостиницу из клееного бруса для базы отдыха «Диостан» в Башкирии. На XV Международной выставке деревянного домостроения HolzHaus этот проект был удостоен диплома за лучшие конструктивные и проектно-архитектурные решения 2012 года.
В 2014 году «АКБ-11» переехало в Санкт-Петербург, стало самостоятельным предприятием и параллельно с разработкой проектов сооружений для сторонних заводов наладило собственное производство комплектов элементов деревянных зданий и сооружений. В апреле 2015 года «АКБ-11» и ООО ПК «Глобус» взяли в аренду в пос. Юшково Ленинградской области Ладожский завод клееных деревянных конструкций, частично реконструировали и ввели в эксплуатацию. В 2016 году вместе с компанией BG Holztechnik было создано объединение Home-R.
Производственные мощности
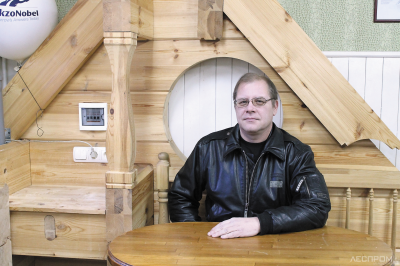
Ладожский завод клееных деревянных конструкций (ЛЗ КДК) был построен компанией «Стройкомплект-Волхов» в 2005 году в Волховском районе Ленинградской области. Выбор места для строительства – в 122 км от Санкт-Петербурга – был обусловлен возможностью приобретения земли в собственность в нескольких сотнях метров от федеральной трассы, что обеспечивало существенные преимущества логистики при поставке клееного бруса и домокомплектов как в Ленинградскую область, так и в соседние регионы. Общая площадь завода составляет 22 350 м2, на территории расположены четыре производственных цеха, административное здание, котельная, две электрические подстанции, три сушильные камеры и склады (общей площадью около 5000 м2). Мощности машинного парка позволяют производить до 5500 м3 клееного бруса в год.
На полную мощность завод вышел в 2011 году, но в 2015-м на рынке деревянного домостроения начался спад, вследствие которого производство типового клееного бруса стало нерентабельным. Предприятие, выпускающее небольшие объемы клееного бруса, не в силах конкурировать с крупными заводами Ленинградской и Вологодской областей – цены на их продукцию ниже себестоимости бруса, изготавливаемого на ЛЗ КДК.
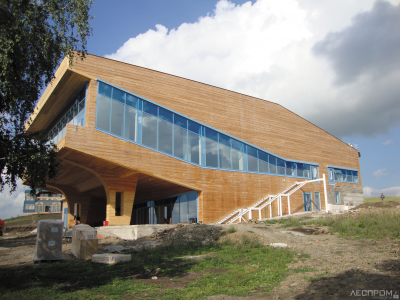
«В 2015 году на заводе сложилась уникальная ситуация: у нас не было задолженностей по кредитам, предприятие находилось в работоспособном состоянии, но не могло выпускать продукцию, поскольку даже при полной загрузке оборудования и его эксплуатации на полной мощности производить клееный брус означало работать в убыток, – вспоминает генеральный директор компании „АКБ-11“ Андрей Стаценко. – С другой стороны, перепрофилировать производственную площадку под другой вид деятельности тоже было затруднительно. В непосредственной близости от завода была построена транспортная развязка для федеральной трассы, что затруднило въезд транспорта на предприятие и выезд с его территории».
Для обеспечения рентабельности производства в сложившихся рыночных условиях компания «АКБ- 11» внедрила на заводе технологию производства фахверковых конструкций, изготавливаемых по индивидуальным проектам. Кроме того, было налажено производство из клееного бруса нестандартных деталей и сборочных элементов сложного профиля или большого сечения, которые экономически нецелесообразно изготавливать в условиях поточного производства.
На заводе выпускают элементы каркасно-ригельных сооружений. В деревянный несущий каркас из клееного бруса в виде колонн и горизонтальных балок встраиваются ненесущие панели, а также оконные и дверные блоки.
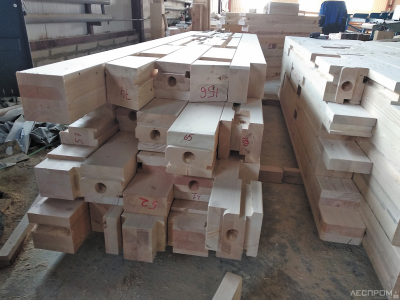
Технология строительства фахверковых сооружений позволяет использовать для заполнения каркаса разные материалы – по выбору заказчика, что открывает широкий простор для архитектурных решений. Для строительства домов по этой технологии требуется небольшой объем древесины, из которой изготавливаются детали несущего каркаса: для здания площадью 150 м2 необходимо всего 15–17 м3 клееного бруса.
Создание во внутренних стенах домов из клееного бруса коммуникационных каналов для прокладки труб канализации или электрических кабелей, фрезерование пазов для крепления стеклопакетов, изготовление различных балочных шиповых и пазовых соединений отличает высокая сложность.
Эти операции могут быть выполнены только на оборудовании типа Hundegger, и из-за низкой скорости фрезерования при создании сложных профилей на них затрачивается очень много машинного времени. Обработка некоторых деталей объемом всего 0,3 м3 может занимать 1,5–2,5 часа. На предприятиях, ориентированных на большие объемы производства продукции, подобное недопустимо.
На заводе выпускаются клееные балки и колонны шириной до 300 и высотой до 420 мм, длиной до 15 м; конструктивные элементы фахверковых домов; широкий ассортимент погонажных изделий, декоративных изделий в виде закругленных арок и ненесущих ферм. Очень много подобной продукции изготавливается по договорам подряда от других заводов, на которых невозможно производить элементы большого сечения.
Сырьевое обеспечение

Сырьем для изготовления клееных деревянных конструкций служат пиломатериалы сечением 50×100 мм из хвойной древесины естественной влажности 0–4 сорта по ГОСТ 8486-86 «Пиломатериалы хвойных пород. Технические условия». Пиломатериалы, поставляемые на завод автомобильным транспортом, разгружаются и перемещаются по территории предприятия вилочным погрузчиком. Доски и брусья закупаются у местных лесозаготовительных компаний, преимущественно из Республики Карелия. Закупка сухих пиломатериалов у расположенных рядом лесопильных компаний, таких как «Майер-Мелнхоф Хольц Ефимовский» или «Свирь Тимбер», невозможна, поскольку небольшие деревообрабатывающие производства не готовы покупать партии объемом от 500 м3 – минимального объема заказа у крупных предприятий. Вместе с тем растет число предложений от малых лесопильных заводов. Рентабельность лесопиления повышается, лесозаготовительные компании создают на своих предприятиях лесопильные участки и стараются по возможности распиливать бревна, а не продавать древесину в виде круглых лесоматериалов.
Несмотря на то что закупаемые пиломатериалы вырабатываются по большей части на недорогих позиционных ленточно-пильных станках, качество их поверхности вполне хорошее, а встречающаяся иногда разнотолщинность в диапазоне допуска. Приемка пилопродукции проводится геометрическим способом, а качество древесины оценивается визуально. В соответствии с техническими условиями на заводе не допускаются гниль пиломатериалов, синева, обзол и поражение дереворазрушающими насекомыми. Объем разовой закупки пиломатериалов составляет 120 м3, что соответствует объему разовой загрузки сушильной камеры.
Сушка пиломатериалов
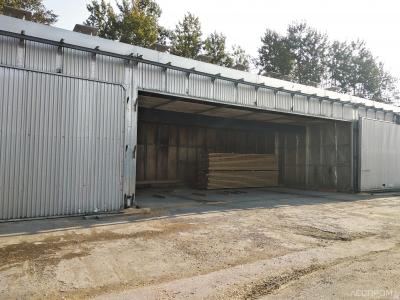
Летом рядовые штабели пиломатериалов со шпациями размещают на специально подготовленных подстопных местах на проветриваемой площадке для атмосферной сушки. В остальное время пиломатериалы укладывают в сушильные пакеты и подвергают камерной сушке.
На предприятии установлены три конвективные сушильные камеры Nardi с объемом разовой загрузки до 120 м3 пиломатериалов каждая. Продолжительность сушки сортиментов сечением 50×150 мм до влажности 12% составляет от 8 до 10 дней. Гидротермическая обработка осуществляется при температуре 50–60°С, что позволяет почти полностью исключить коробление. Режимы сушки составлены таким образом, чтобы минимизировать необходимость искусственного увлажнения.
После окончания сушки и кондиционирования пиломатериалы погрузчиком перевозят в цех механической обработки. Тепловая энергия для участка сушки вырабатывается в котельной, где установлены два котла производства компании «СпецМонтаж» (г. Тверь), в которых сжигаются опилки и стружки – отходы основного производства. Совокупная мощность тепловых агрегатов 2 МВт.
Склеивание древесины
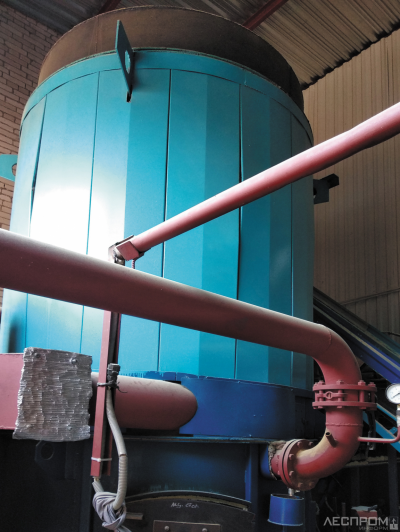
Сухие пиломатериалы поступают в цех предварительного калибрования, где обрабатываются с четырех сторон на строгальном четырехстороннем продольно-фрезерном станке С25-5А (производитель – Боровичский завод деревообрабатывающих станков), что позволяет вскрыть поверхность древесины и выявить пороки и трещины. Дефектные участки оператор отмечает люминесцентным мелком. Затем сортименты на продольном транспортере подаются на линию оптимизации, где местоположение меток считывается датчиком «Бакаут оптима 7» и в автоматическом режиме осуществляется поперечный раскрой заготовок.
Готовые заготовки перемещают в цех, где установлена линия сращивания пиломатериалов на вертикальный шип «ЛБСА 001–200» (производитель – «ТД «Бакаут»), на которой выполняется нарезка шипов, нанесение клея, прессование заготовок и торцовка склеенных плетей на заданную длину.
После технологической выдержки, необходимой для отверждения клея, склеенные заготовки с помощью кран-балки перемещаются к калибровально-рейсмусовому станку Kupfermühle, на котором ламели калибруются по толщине.
На следующем этапе на пласти ламелей наносится связующее. Для склеивания древесины используется ММФ-клеевая система 1249/2579 производства компании AkzoNobel. Клей и отвердитель наносятся раздельно с помощью клеенаносящей машины Ribbon Spreader 8230 Combo.
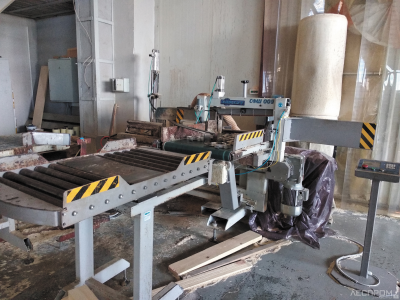
Склеивание выполняется на двух вертикальных гидравлических прессах Giga15. Возможности прессового оборудования позволяют изготавливать клееный брус длиной до 15 метров.
При толщине ламелей 42 мм давление прессования 0,9 МПа, а расход клея на 1 м3 – около 29 кг. Продолжительность прессования – до 1,5 ч, в зависимости от соотношения клея и отвердителя. При изготовлении бруса шириной 300 мм на этом же прессе после предварительного строгания может выполняться склеивание двух брусьев по ширине.
После склеивания брусья выдерживаются не менее 24 ч для отверждения связующего, затем погрузчиком их перевозят в следующий цех, где из них изготавливают строительные детали.
Механическая обработка древесины
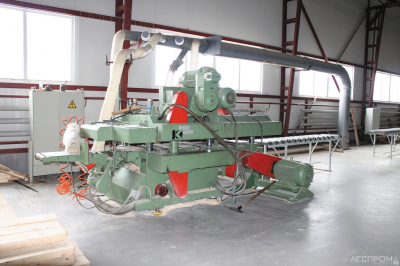
В зависимости от назначения деталей клееный брус обрабатывается на двух параллельно установленных линиях.
Если конечной продукцией является обычный стеновой брус, доля которого в общем объеме производства не превышает 15%, то его обработка осуществляется следующим образом. Сначала выполняется профильное фрезерование на четырехстороннем шестишпиндельном строгальном станке Reignmac RMM 633, предназначенном для фрезерования бруса высотой до 230 мм и шириной до 330 мм, позволяющее сформировать необходимое сечение бруса с тепловым замком. Затем заготовки подаются в автоматический станок Auer Biglog 260A производства компании Auertech, на котором изготавливаются элементы стандартных угловых соединений.
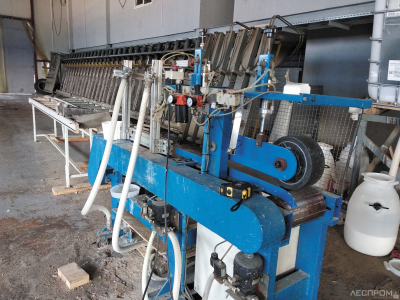
При производстве основной продукции, которой являются элементы фахверковых зданий и колонны сложного профиля, выпускаемые как для компоновки домокомплектов по собственным проектам предприятия, так и на заказ для других предприятий, заготовки обрабатываются по иной технологии. На станке Reignmac RMM 633 выполняется только их калибрование, а пазы и соединительные элементы сложной формы, отверстия для устройства встроенных инженерных коммуникаций вырезаются на автоматическом программируемом деревообрабатывающем центре Hundegger K2.
Вне зависимости от используемой технологии все изготовленные детали проверяются специалистами ОТК, маркируются, упаковываются в пленку и перемещаются на склад готовой продукции.
Программное обеспечение
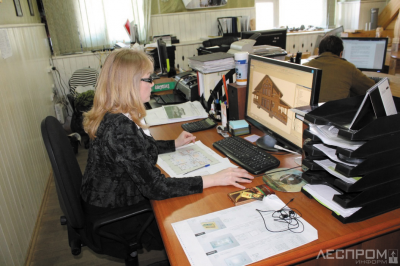
Изготовление деталей для фахверковых сооружений невозможно без создания полной конструкторской документации и разработки программ для обработки деталей на деревообрабатывающем центре Hundegger K2. Строительство домов по указанной технологии предполагает необходимость обеспечения жесткости каркаса, достигаемой за счет обработки соединительных элементов сложной формы с высокой точностью, что исключает риск появления отклонений в осях собранных конструкций. Кроме того, во всех элементах несущего каркаса должны быть сделаны пазы для установки стеклопакетов или заполнения стеновых элементов плитными материалами. По заверению представителей компании, выпилить эти пазы бензопилой на сборочной площадке нельзя. Их необходимо делать в заводских условиях, а при написании исполнительных программ для станка «Hundegger K2» – учитывать максимально возможный съем древесины инструмента за один проход и формировать глубокие профили за несколько проходов.
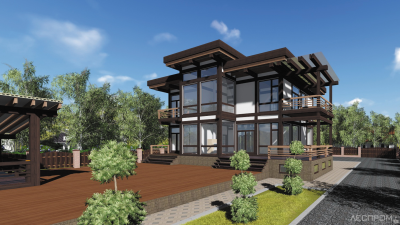
Проектирование дома начинается с разработки архитектурной части (включая расстановку мебели), выполняемой с помощью программного комплекса ArchiCAD. Следующий шаг – визуализация проекта в программах SketchUp или Lumion, возможности которых позволяют получать изображение будущего дома в формате 3D и вносить в проект элементы анимации, позволяющие оценить, как будут выглядеть дом и прилегающая территория при разных погодных условиях и в разное время суток. После согласования с заказчиком создается полный пакет проектной документации, в которой основное внимание уделяется созданию конструктивных решений и расчету нагрузок на конструкции. Эта часть проекта выполняется в программе CadWork, оптимально соответствующей требованиям при работе со станками типа Hundegger K2, поскольку возможности программы позволяют автоматически формировать исполнительные файлы для обработки заготовок на станке. Объекты, создаваемые с помощью CadWork, рассчитываются программными алгоритмами как твердые тела, и при проектировании отверстий, соединительных элементов и других операций, где требуется удаление древесины, достигается высокая точность обработки заготовок в полном соответствии с параметрами, заданными программным обеспечением. Это ключевое отличие CadWork от подобных программ.
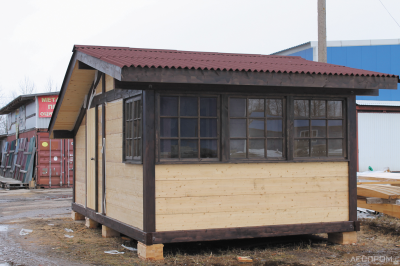
Программные расчеты при определении порядка изготовления деталей из бруса позволяют достичь минимальных (1–2%) потерь древесины в результате торцевания бруса. Для того чтобы обеспечить расчетный показатель выхода готовых деталей при обработке бруса на станке на уровне 98%, необходимо провести дополнительную оптимизацию порядка раскроя в программном комплексе станка. Так, например, при фрезеровании шипового соединения сложной формы следует учитывать, что фреза, завершая обработку, может на 1–2 см выйти за пределы детали, повредив таким образом следующий за ним элемент, который подается в станок на обработку. Подобные ситуации инженерам надо просчитывать и вносить в порядок обработки заготовок изменения, размещая подобные детали в торцах бруса, чтобы избежать повреждения соседних деталей. При составлении карты обработки бруса следует проверить возможность закрепления деталей небольших размеров перед обработкой. Очень маленькие детали, которые не могут быть закреплены в станке по отдельности, необходимо вырабатывать из центральной части бруса.
В стандартных библиотеках программных продуктов нет файлов с информацией об обработке множества сложных узлов и деталей, поэтому программы для деревообрабатывающего центра приходится дополнять специалистам на местах.
Производительность
Производственная мощность завода зависит от сложности заказов. При изготовлении колонн для фахверковых зданий с пазами для крепления плитных материалов производительность составляет 150–200 м3 в месяц, при изготовлении сложных строительных элементов с полостями для прокладки инженерных коммуникаций – около 100 м3.
Поскольку циклы обработки деталей на станке Hundegger K2 длительные, участок работает в двухсменном режиме, в то время как основные подразделения завода успевают полностью загрузить его заготовками за одну смену. Установка второго обрабатывающего центра в настоящее время экономически нецелесообразна, поскольку и при указанном объеме производства мощности загружены только на 80% вследствие общего спада на рынке деревянного домостроения по сравнению с 2007 и 2015 годами.
Кадровое обеспечение
У станочников Ладожского завода клееных деревянных конструкций не было базовых знаний в области обработки древесины, рабочие – местные жители – обучались тонкостям работы с древесиной на заводе. Большинство специалистов трудятся здесь с основания завода и за это время накопили значительный опыт, позволяющий быстро переключаться на освоение новых видов продукции при изменении ассортимента продукции.
География поставок
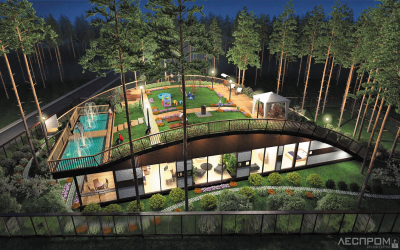
Несмотря на высокую сложность обработки клееного бруса для строительства фахверкового дома стоимость 1 м3 бруса с отверстиями для инженерных коммуникаций около 35 тыс. руб. Это вполне конкурентоспособная цена с учетом небольшого числа несущих элементов из цельной древесины в домах такой конструкции.
С 2008 года специалисты компании «АКБ-11» спроектировали и построили более 200 деревянных сооружений в Московской, Ленинградской, Новгородской, Тверской, Ульяновской, Самарской областях, а также в республиках Башкортостан и Молдова.
Клиентами Ладожского завода клееных деревянных конструкций являются не только частные заказчики, но и строительные подрядные организации, у которых нет собственных производственных мощностей, но которые позиционируют себя на рынке как компании – производители домокомплектов. Такие подрядчики делают на заводе заказ на изготовление либо полного домокомплекта, либо сложных элементов, которые им не могут поставить крупные заводы, выпускающие стандартизованную продукцию. Доля подобных заказов в общем объеме производства достигает 70%, остальное – заказы на индивидуальные фахверковые дома для частных потребителей.
Перспективы фахверковой технологии
Фахверковая технология в России мало распространена, поскольку обычный потребитель, по сути, не знает ее особенностей и часто не может отличить ее от каркасной или каркасно-панельной.
«Отраслевые вузы не занимаются популяризацией разных технологий индивидуального домостроения. На отраслевых семинарах и конференциях по деревянному домостроению также почти не уделяют внимания критическому анализу особенностей строительства и эксплуатации индивидуальных зданий, изготовленных по разным технологиям. В центре обсуждения обычно состояние рынков сырья и продукции, тенденции общего роста отрасли и вопросы актуализации нормативных документов, что, безусловно, интересно производителям, но не покупателю. Развитие фахверковой технологии деревянного домостроения сдерживается также тем, что не все строительные подрядные организации имеют опыт возведения подобных зданий, – считает Андрей Стаценко. – А в совокупности с желанием заказчиков сэкономить на шефмонтаже, отсутствие этого опыта приводит к ошибкам при сборке конструкций на строительных площадках. Срок сборки двухэтажного дома сложной конструкции площадью 200 м2 опытной бригадой 10–20 дней, но при привлечении неквалифицированных рабочих он иногда увеличивается до нескольких месяцев, а конечный результат может оказаться неудовлетворительным».
Специалистам завода часто приходится выезжать на строительные площадки, обучать строителей чтению чертежей, исправлять их ошибки и, по сути, осуществлять шефмонтажные работы, которые должны заказываться изначально, но от которых заказчики часто отказываются из желания сэкономить.
Направления развития
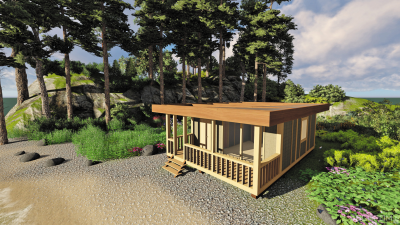
Совместно с девелоперской компанией Hill Park компания «АКБ- 11» разработала архитектурные и конструкторские решения энергоэффективных экспериментальных домов с мини-парком на крыше. У домов, которые изготавливаются по фахверковой технологии, большая площадь остекления, что обеспечивает им оригинальный дизайн. Первые дома по подобной технологии уже построены в ДНП «Памир» в Ленинградской области. По мнению руководства «АКБ-11», эти дома будут востребованы потребителями, а возможности станочного парка завода позволяют быстро организовать их производство и увеличить объемы выпуска деревянных домов заводского изготовления.
В феврале 2019 года специалисты компании «АКБ-11» разработали проект и приступили к производству фахверковых домов в виде модуль-блоков заводского изготовления, использование которых позволит сократить сроки сооружения зданий на строительной площадке. Подобные модульные дома могут быть использованы в качестве первой быстровозводимой постройки при освоении земельного участка.
Александр Тамби