«Талион Терра». Производство шпонового бруса LVL
Ultralam − супердерево из Торжка
В апреле нынешнего года в Тверской области начал производственную деятельность новый завод по выпуску шпоновых балок (бруса) LVL. Его продукция предназначена главным образом для строительного рынка. Это второй завод по производству LVL-бруса в нашей стране, но проект компании «Талион Терра» стал во многом инновационным и даже уникальным для России.
Организовать производство LVL-бруса руководство компании решило в городе Торжок Тверской области, расположенном в 237 км от Москвы и в 473 км от Санкт-Петербурга, рядом с федеральной трассой М10.
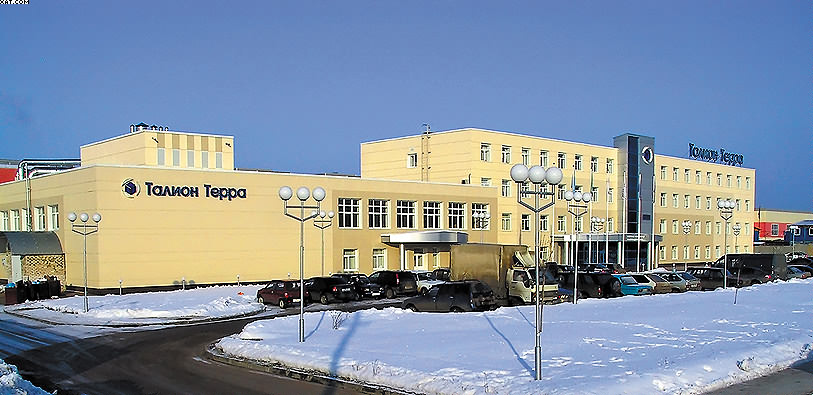
Завод LVL «Талион Терра»
Выбор места для «Талион Терра»
Именно выгодное с точки зрения логистики расположение города и стало определяющим при выборе места строительства завода. Инициатива создания производства шпоновых балок принадлежит Александру Ебралидзе и Якову Барскому, акционерам петербургского ОАО «Талион» и совладельцам ООО «Талион Терра». Финансирование проекта было организовано Сбербанком России. Объем инвестиций составил 170 млн евро.
Был куплен недостроенный завод железобетонных конструкций в промышленной зоне города и территория 24 га. Начало реализации проекта положено в ноябре 2005 года. За проектирование завода взялась компания «Рапс» из Санкт-Петербурга.
На первом этапе была установлена линия по производству топливных гранул производственной мощностью 60 тыс. т в год. В августе 2007 года началось строительство завода шпоновых балок. Проектная мощность линии LVL-бруса − 140 тыс. м3 готовой продукции в год. При этом производительность пресса такова, что позволяет выпускать до 300 тыс. м3 LVL в. год.
Строительство завода «Талион Терра» и приток инвестиций буквально вдохнули жизнь в маленький провинциальный Торжок. И это заметно не только по изменениям во внешнем виде города, появлению новых магазинов и гостиниц, но и по тому, как выросли там цены на аренду жилья.
Возведение нового деревообрабатывающего производства позволило создать 370 новых рабочих мест и, без сомнения, сделает Торжок крупным центром деревообработки в России. Планируется, что объемы лесозаготовки в Тверской области в ближайшее время вырастут с текущих 3 млн до 7 млн м3 круглого леса в год.
Сырьевое обеспечение «Талион Терра»
Для такого крупного производства, как «Талион Терра», одной из важнейших задач является непрерывное обеспечение предприятия древесным сырьем. Решает эту задачу специально созданное предприятие − ООО «ЛесоСырьевоеОбеспечение» («ЛСО»), которое занимается как самостоятельной лесозаготовкой, так и торгово-закупочными операциями с круглым лесом. Для работы на проектной мощности заводу «Талион Терра» требуется до 360 тыс. м3 леса в год. В производстве используются хвойные породы древесины: ель и сосна. Сейчас в аренде «ЛСО» находятся 263 тыс. м3 расчетной лесосеки. Заготовка ведется в семи районах Тверской области сортиментным способом. Лесные угодья проходят сертификацию по системе FSC (Forest Stewardship Council). В 2009 году планируется увеличить аренду лесных угодий до 1 млн м3.
Технологии на «Талион Терра»
В среднем на производство 1 м³ LVL-бруса расходуется 2,5 м³ древесины. На площадке «Талион Терра» организована биржа сырья, которая позволяет единовременно складировать до 40 тыс. м3 леса. Территория биржи полностью забетонирована. Сырье поставляется на завод в сортиментах одной длины − 5,5 м. Транспортные развязки организованы с учетом того, что 70% древесного сырья будут доставляться на площадку железнодорожным транспортом и ещё 30% − сортиментовозами. Разгрузкой и всеми манипуляциями с круглым лесом на самой бирже занимаются колесные погрузчики. Приемка сырья осуществляется на установленной тут же линии обмера и сортировки бревен производства Hekotek (Эстония).
С биржи сырья бревна первым делом подают на окорку. Хорошо известная в нашей стране финская компания Valon Kone Oy поставила для этих целей мощный однороторный окорочный станок VK 820.
Станки Valon Kone не боятся эксплуатации при низкой температуре, поэтому линию окорки было решено не прятать в стены цеха, а установить под навесом.
За окоркой в технологической цепочке идет гидротермическая обработка древесины (ГТО). Основная функция гидротермической обработки древесины − прогрев древесины, с тем чтобы сделать её более мягкой и гибкой перед лущением. Интересно, что в проекте «Талион Терра» окаривать бревна решено было до гидротермической обработки древесины. Ведь если эту операцию выполнять сразу после гидротермической обработки древесины, то в коре, поступающей дальше в котельную, будет содержаться очень много влаги. Прежде чем отходы можно будет сжечь, эту влагу нужно каким-то образом удалить. Мокрое топливо − это всегда потери тепла и снижение КПД теплогенерирующей установки. Кроме того, по всему тракту перемещения мокрой коры обычно образуются потеки и, как следствие, грязь. Да и загрязнение бассейнов гидротермической обработкой древесины также происходит быстрее, когда в них находятся неокоренные бревна.
Но этим новшества на участке подготовки древесины не ограничиваются. На заводе впервые в России эксплуатируются бассейны гидротермической обработки древесины проходного типа, спроектированные канадской компанией Vitech Engineering Inc. Всего бассейнов пять − четыре рабочих и один резервный, для проведения технического обслуживания. Бассейны рассчитаны на обработку бревен одной длины − 5,5 м. Длина каждого бассейна − около 40 м. Бревна поступают в бассейн из входных накопителей (рис. 1). Благодаря специальному захватному механизму, имеющему четыре трелевочные цепи особой конструкции (рассчитаны на особо тяжелые условия эксплуатации и ударные нагрузки), бревна затягиваются в бассейн, погружаются в воду и постепенно продвигаются к выходу из бассейна. Прижимные траверсы, по которым перемещаются цепи, удерживают все бревна в воде, не давая им всплывать. Конструкция прижимных траверсов позволяет использовать бассейны на всю глубину, увеличивая тем самым их пропускную способность. Температура воды в бассейнах устанавливается в диапазоне 40–80°С − в зависимости от температуры окружающей среды и ряда других факторов. Нагрев воды в бассейнах осуществляется с помощью термомасляных радиаторов, встроенных в боковые стенки каждой бетонной чаши. Для того чтобы вода в бассейне нагревалась равномерно и не застаивалась, предусмотрена специальная система циркуляции жидкости.
Технический директор Vitech Engineering Витольд Вацински говорит: «Чистить такой бассейн нужно не чаще одного-двух раз в год. Во время эксплуатации нужно лишь следить за уровнем pH воды. Для его выравнивания можно использовать каустическую соду. Что касается системы нагрева, то использование термомаслянных радиаторов − проверенный, хорошо себя зарекомендовавший метод. Выполнены они из нержавеющей стали и защищены от механических повреждений специальными решетками. Вероятность протечки термомасла в бассейн практически сведена к нулю».
Бассейны открытого типа, лишь зоны выгрузки находятся в стенах цеха. Для сокращения потерь тепла из-за парения в зимнее время зеркало воды в бассейнах закрыто досками. Такое решение позволило сократить строительные объемы и удешевить строительство.
Бревна в бассейне выдерживаются 24–36 часов и по наклонным бревнотаскам выгружаются на цепной транспортер, который дальше поштучно подает их на слешер − маятниковую циркулярную пилу с тремя пильными блоками (рис. 2). Кстати, система разгрузки бассейнов на «Талион Терра» была предметом инженерной дискуссии. В Канаде обычно применяют наклонные бревнотаски (по-английски jack-ladders) − по одной на бассейн. Европейские поставщики оборудования часто рекомендуют другой подход к решению проблемы − использование крана с грейферным захватом. При этом один кран может обслуживать сразу три-четыре бассейна. Основным недостатком бревнотасок является угроза возникновения заторов и блокировка транспортера бревнами, соскальзывающими с захватов при подъеме. Вот как объяснил выбранное техническое решение директор по запуску проекта «Талион Терра» Брюс Грэмлинг: «Мы отдали предпочтение бревнотаскам в первую очередь потому, что они обеспечивают большую надежность работы линии. Если кран сломается, то вся входная группа, вся линия подготовки древесины будет остановлена до починки подъемного механизма. Кроме того, мы работаем с довольно длинными бревнами с хорошей геометрией, поэтому вероятность возникновения заторов на бревнотасках минимальна».
После гидротермической обработки бревна на слешере торцуют и распиливают на чураки длиной 2,65 м, которые затем поступают на линию лущения шпона.
Получение шпона на «Талион Терра»
Поставщиком линии лущения была выбрана канадская компания COE Manufacturing (на рис. 3 изображено центрирующе-загрузочное устройство лущильного станка). Кстати сказать, это, пожалуй, первый случай, когда известная финская компания RAUTE Oy проиграла канадцам тендер в России. Причем по техническим параметрам оборудования. Для работы завода на проектной мощности необходимо, чтобы лущильный станок распускал на шпон 8–10 чураков в минуту. Как показали гарантийные испытания, один канадский станок способен, «не напрягаясь», лущить до 18 чураков в минуту. Таким образом, у «Талион Терра» есть ещё и потенциал для увеличения производительности, и возможность обеспечить оптимальную производительность, используя более тонкое сырье. По требованию завода компания COE специально изготовила свое оборудование в метрической системе мер, а систему управления оснастила элементной базой Siemens. Напомним, что в Северной Америке все оборудование изготавливается в дюймовой системе мер, а для систем управления стандартно используются компоненты производства компании Allan Bradley.
Но вернемся к технологии. Из чураков получают ленту шпона толщиной 3,2 мм, её рубят на листы нужной длины, сортируют по влажности и тут же укладывают в стопы. Сортировку шпона по влажности обязательно необходимо проводить перед сушкой шпона, так как влажность заболонной и сердцевинной частей древесины после гидротермической обработки значительно разнится. Специальный механизм опорных роликов на станке СОЕ позволяет лущить чураки практически до диаметра карандаша (90 мм).
Карандаши и шпон-рванина отводятся по конвейеру и после измельчения используются как сырье для производства пеллет. Как и любое современное производство, завод «Талион Терра» задумывался и проектировался как безотходное производство, когда в дело идет вся древесина. Так называемые черные отходы − те, что образуются в процессе окорки древесины, а также отходы, которые собираются аспирационной системой завода, сжигаются в котельной. В котельной три котла суммарной тепловой мощностью 39 МВт. Один котел работает только на древесных отходах, у второго имеется дополнительная горелка для сжигания древесной пыли, а третий котел работает исключительно на природном газе. Котельную станцию для завода поставила немецкая компания Maxxtec AG.
Сушка шпона на «Талион Терра»
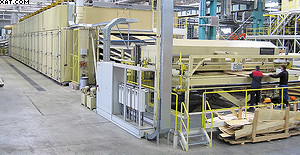
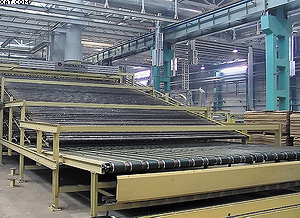
Рис. 5. Линия сушки шпона производства Grenzebach
BSH GmbH
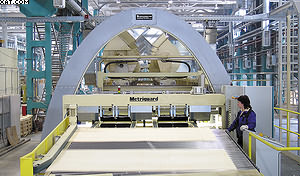
Рис. 6. Визуальный контроль и сортировка шпона по
плотности на оборудовании компании Metriguard Inc.
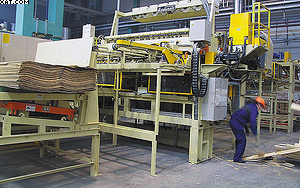
Рис. 7. Станок для ребросклеивания шпона производства
Hashimoto Denki
Для сушки шпона используется 6-уровневая роликовая сушилка немецкого производства Grenzebach BSH GmbH (рис. 5). Сушка шпона происходит при температуре 160–200 °С пока уровень влажности материала не достигнет 5%. После сушки шпон по транспортерам поступает на линию сортировки и стопоукладки. Каждый лист шпона проходит мимо оператора линии и подвергается визуальному контролю: оператор отделяет лучшие, бессучковые листы шпона (так называемую рубашку), которые пойдут в дальнейшем на наружный слой LVL-бруса, от тех, что выглядят похуже и будут служить в качестве срединного слоя. Влажность измеряется контактным способом на устройстве для измерения влажности Elliott Bay Industries производства США. Если она выше нормы, шпон отсортировывается и отправляется на досушку.
В производстве LVL прочность шпона является очень важным фактором, поэтому на линии сортировки сухой шпон сортируют ещё и по плотности.
Сортировка происходит на оборудовании американской компании Metriguard Inc. (рис. 6) при помощи ультразвуковых датчиков.
Благодаря такой тщательной сортировке шпон с разными физико-механическими параметрами будет затем равномерно распределен в массе готового изделия, что в результате позволит получить материал со стабильными одинаковыми характеристиками.
Высушенный, отсортированный и классифицированный шпон укладывается в стопы и погрузчиком подается в цех производства LVL-бруса.
При сушке, а также при транспортировке по конвейерам случается, что хорошие листы шпона разламываются вдоль волокон на узкие полосы. При лущении и нарезке листов из ленты шпона может быть и так, когда качество шпона высоко, но ширина листа не удовлетворяет стандартам. Для того чтобы получить форматные листы шпона из узких полосок и тем самым повысить коэффициент полезного использования древесины, существуют специальные станки. Для выполнения этой весьма тонкой операции на заводе установлены два ребросклеивающих станка производства японской фирмы Hashimoto. Полосы шпона сращиваются в стык с помощью специальной термонити, которую станок укладывает на шпон и плавит. Застывая, термонить надежно скрепляет полосы друг с другом. Ребросклеивающие станки Hashimoto (рис. 7) считаются сегодня самыми производительными в мире: каждый способен изготовить до 8 м³ форматных листов шпона в час.
Усование
Подготовленный шпон подают на следующую технологическую операцию − усование: две противоположные кромки листа шпона скашивают под углом 45° на глубину 3 см.
Здесь же листы одновременно калибруются по длине и ширине, чтобы обеспечить точное совпадение скошенных кромок шпона при наборке пакета.
Листы шпона со скошенными концами подаются по транспортеру дальше.
На клееналивной машине на шпон сплошной завесой наносится изготовленный по специальной рецептуре фенолоформальдегидный клей и равномерно распределяется по одной стороне каждого листа шпона.
В производстве LVL-бруса используется клей с классом эмиссии Е 1. В качестве поставщика связующего была выбрана компания Hexion − один из крупнейших европейских производителей синтетических смол для деревообрабатывающей промышленности.
Шпон-рубашка подается по отдельному транспортеру, и клей на него наносится только в местах заусовки.
Наборка пакета
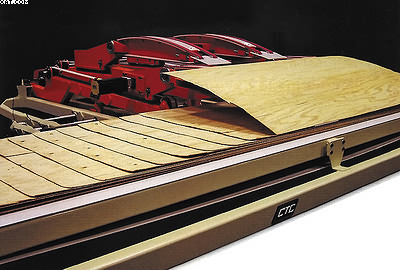
Рис. 8. Станция наборки пакетов производства СТС
Фенолоформальдегидный клей, как и любой другой, имеет ограниченное время открытой выдержки, поэтому листы шпона с нанесенным клеем сразу подаются на станцию наборки пакетов.
Наборка пакетов − пожалуй, наиболее интересное звено в технологии производства LVL-балок (бруса). На заводе «Талион Терра» установлена самая скоростная на сегодня станция наборки пакетов производства компании Corvallis Tool Company (США), имеющая два уровня. Скорость операции составляет 54 листа в минуту, а при необходимости может быть доведена до 81 листа. Сложность состоит в том, что наборка требует высокой точности выполнения, от которой напрямую зависит качество готовой продукции. Главный технолог завода «Талион Терра» Татьяна Токарева поясняет: «Наборка пакета в производстве LVL-бруса происходит в два этапа. Набирается первый пакет, или, как мы его называем, „чешуйка“, состоящая из заданного количества листов шпона. Количество листов в „чешуйке“ определяет толщину будущего изделия. При наборке „чешуйки“ каждый лист шпона сдвигается по отношению к следующему ровно на 150 мм в сторону, противоположную движению основного конвейера линии LVL-бруса. Шпон выкладывается строго по одной линии, которая задается лазером. Когда „чешуйка“ набрана, она меняет направление движения и выкладывается на основной конвейер. Как только первая „чешуйка“ выложена на основной конвейер, уже готова следующая. Вторая „чешуйка“ выкладывается точно в стык с предыдущей, накрывая её „ступеньки“. И так далее. Таким образом получается непрерывный пакет из выкладываемых одна за другой „чешуек“ с предварительно заданным числом слоев шпона».
Отметим, Corvallis Tool Company впервые поставила свое оборудование в Россию. Оно также впервые было изготовлено в метрической системе, на базе аппаратной платформы Simotion и контроллеров Simatic − последних разработок компании Siemens. Проект-менеджер компании СТС Джефри Соуф делится нюансами сделки: «У нас ушел примерно год на то, чтобы спроектировать оборудование в метрической системе, перевести его на новую элементную базу и провести необходимую сертификацию. Я много времени провел в Европе, ведя переговоры с поставщиками, подбирая подходящие комплектующие. В целом стоимость оборудования из-за перехода на европейские комплектующие выросла, думаю, на 15–20%».
В пресс
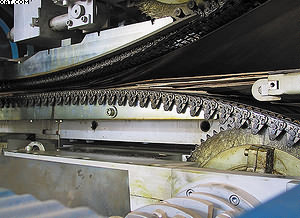
Рис. 9. Подача пакета в пресс непрерывного действия
Dieffenbacher

Рис. 10. Устройство маркировки готовой продукции
производства Claussen All-Mark Inc.
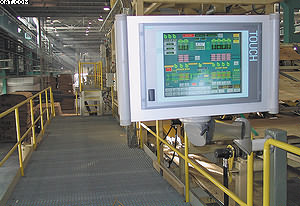
Рис. 11. Система управления линией сортировки сухого
шпона от компании СТС
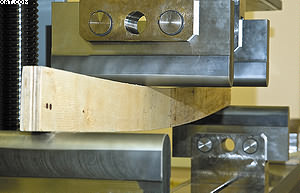
Рис. 12. Лаборатория. Пресс для тестирования LVL
Сформированный таким образом непрерывный пакет из листов шпона шириной 1300 мм подается дальше по конвейеру в горячий пресс. Линию прессования поставила немецкая компания Dieffenbacher (рис. 9). На заводе установлен самый длинный в Европе непрырывный пресс − его длина составляет 60 м. Линия прессования LVL-бруса оснащена американской установкой предварительного нагрева пакета с помощью микроволн. Мощность установки − 500 кВт. Её задача повысить температуру внутри пакета непосредственно перед входом в горячий пресс. Предварительный нагрев позволяет увеличить скорость прессования без риска появления брака в шпоновой плите. Прессование происходит при температуре +185 °С.
После прессования непрерывная плита, двигающаяся дальше по конвейеру, проверяется на наличие непроклеенных мест и вздутий и раскраивается по длине. Систему контроля качества продукции для линии Dieffenbacher поставила компания Electronic Wood Systems GmbH. При обнаружении системой контроля качества дефектных участков диагональная пила удаляет их из шпоновой плиты. Для отвода брака предусмотрена специальная станция. Процент брака, образующегося при непрерывном прессовании, меньше, чем при прессовании на циклических прессах, и обычно не превышает 5%. А показатель разнотолщинности гораздо ниже.
Оборудование, расположенное в цепочке после пресса, предусматривает работу с заготовками максимальной длиной 20,5 м.
После обрезки по длине шпоновые плиты с помощью блока продольных пил торцуются по ширине в размер 1250 мм и раскраиваются на балки. Полученные таким образом LVL-балки, прежде чем попасть на склад готовой продукции, по конвейерам поступают на участок окончательной обработки.
Окончательная обработка
Так называемая окончательная обработка очень важна, так как именно здесь производитель может задавать конкурентные преимущества своей продукции − те свойства, благодаря которым, потребитель отдаст предпочтение именно его товару, а не какому-то другому. На участке окончательной обработки завода «Талион Терра» установлено много интересного оборудования: фрезерный блок для скашивания острых кромок балки, линия маркировки и защиты кромок, линия упаковки.
Скашивание кромок, то есть создание небольшой фаски по всему периметру LVL-балки делает работу с материалом комфортной. Маркировка − обязательный атрибут, присущий высококачественному строительному материалу, − осуществляется на линии производства американской компании Claussen All-Mark Inc. (рис. 10). Печатный оттиск наносится на пласть каждой балки и содержит логотип завода и основную информацию об изделии. Следуя по конвейеру, балки с маркировкой проходят через камеру гидрофобизации кромок. Гидрофобизацию или повышение водостойкости изделия обеспечивает распыление парафиновой эмульсии на торцы каждой LVL-балки. Это важно, так как через незащищенные торцы древесина гораздо интенсивнее впитывает влагу, чем через пласть.
Линия упаковки находится в самом конце производственной цепочки. Здесь балки согласно спецификации заказа укладываются в штабель, который перетягивается шиновальной лентой. Для того чтобы предотвратить попадание влаги при транспортировке или хранении материала на стройплощадке, его пакуют в полиэтиленовую пленку. Учитывая большую длину готового изделия, для упаковки LVL-балок используется специальная пленка, армированная текстильной сеткой. Она не порвется из-за прогиба балок и придаст штабелю дополнительную стабильность. Готовые изделия погрузчик отправляет на склад для отгрузки потребителю.
Лаборатория
Как и любой конструкционный материал, LVL-бруса требует постоянного контроля качества и тестирования. Для этого на заводе организована лаборатория. Оборудование, которым она располагает, позволяет измерять основные физико-механические характеристики готовой продукции: предел прочности при скалывании по клеевому слою, при статическом изгибе вдоль волокон, при растяжении вдоль и поперек волокон, при сжатии поперек и вдоль волокон, а также модуль упругости при статическом изгибе. Кроме того, в лаборатории можно определять плотность материала. Для измерения эмиссии формальдегида из готовой продукции есть газоанализатор производства фирмы Weiss.
Имеется необходимое оборудование и для тестирования топливных гранул: измерения их зольности, теплотворной способности, истираемости и влажности. Лаборатория по тестированию пеллет на заводе − одна из наиболее оснащенных сегодня в России.
Рынок сбыта
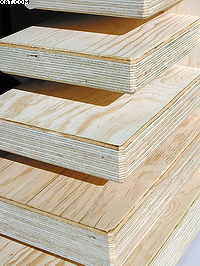
Рис. 13. Ultralam – супердерево из
Торжка
Производственная линия LVL-бруса «Талион Терра» − одна из крупнейших в мире. Вывести завод на проектную мощность (140 тыс. м3 LVL-бруса в. год) планируется за 12 месяцев. При этом Брюс Грэмлинг отмечает: «Мировой финансовый кризис и спад на строительном рынке, безусловно, негативно скажутся на сроках выхода завода на проектную мощность. Но наша линия спроектирована и оснащена так, чтобы обеспечить максимальную гибкость производственной программы. У нас есть все возможности для адекватного реагирования на потребности рынка. Кроме того, как показывает практика, тренд на строительном рынке меняется каждые 5–7 лет и за спадом всегда начинается рост».
Сбыт продукции будет осуществляться через сеть дистрибьюторов. Приоритетными для «Талион Терра» являются российский и европейский рынки. Торговое подразделение Taleon Industries A/S, открытое в Дании, станет эксклюзивным поставщиком продукции завода на севере Европы. LVL-брус производства «Талион Терра» появится на рынке под торговой маркой Ultralam.
Производственная программа предусматривает выпуск трех марок LVL-бруса:
- Ultralam R (Regular) − все слои шпона в изделии имеют одинаковую − продольную ориентацию волокон. Эта марка бруса рекомендуется для использования в строительных конструкциях, где балки будут работать на растяжение и сжатие, то есть там, где основная нагрузка будет прикладываться вдоль балки;
- Ultralam X − 20% слоев шпона в LVL-брусе имеют поперечную ориентацию волокон. Причем они равномерно распределены по толщине бруса, то есть чередуются со слоями шпона со стандартным (продольным) направлением волокон.
Эта марка LVL-бруса по структуре и свойствам напоминает фанеру и рекомендуется для применения в строительных конструкциях, где материал будет воспринимать не только продольную, но и поперечную нагрузки. Кроме этого, Ultralam X имеет улучшенные характеристики по удержанию крепежа; - Ultralam I (Individual) − эта марка будет присваиваться продукции с нестандартными длиной и толщиной. Кроме того, порядок расположения поперечных и продольных слоев шпона в LVL-брусе этой марки может также регламентироваться потребителем.
Максимальная ширина шпоновой плиты, из которой получаются LVL-балки, 1250 мм. Ширина бруса зависит от конструкционных задач, которые решает потребитель. Толщина бруса также зависит от области применения LVL-балок и варьируется от 19 до 106 мм с шагом 3,2 мм. Максимальная длина бруса − 20,5 м.
Материал Ultralam уже успешно прошел сертификацию для российского рынка в ЦНИИСК им. Кучеренко (Москва), получено санитарно-эпидемиологическое заключение. Сертификация для европейского рынка проведена немецким институтом ВАМ (Federal Institute for Materials Research & Testing). Заканчивается сертификация материала для поставки его на североамериканский рынок.
Планы на будущее
Итак, производство LVL-бруса на заводе сегодня ведется, без сомнения, по самой современной технологии в мире. Новейшее оборудование поставлялось из США, Канады, Европы и Японии. Большая часть североамериканского оборудования для проекта в Торжке была впервые изготовлена в метрической системе, и первый раз эти станки оснащены элементной базой Siemens. Монтаж оборудования выполнялся австрийской компанией SGS Industrial Services. Строительными работами управляло российское ООО «Леокаспис».
Успешная реализация столь сложного проекта была во многом достигнута благодаря усилиям инжиниринговой компании Evergreen Engineering (США).
Проект «Талион Терра» весьма амбициозен. Его реализация призвана дать мощный импульс развитию деревянного домостроения в России и способствовать снижению стоимости квадратного метра жилья.
В рамках реализации третьей очереди проекта планируется организовать первое российское производство ориентированно-стружечных плит OSB мощностью 500 тыс. м3 в год. Для этой цели уже приобретена необходимая территория, планируется увеличение арендованной лесосырьевой базы.
Михаил ЯШИН