Фанерные предприятия России
Состояние и перспективы
В России работают примерно 40 фанерных предприятий. В 2021 году было произведено 4,5 млн м3 фанеры и фанерной продукции. Фанера – уникальный древесный клееный материал: легкий, прочный, формоустойчивый, атмосферостойкий и экологичный.
Часть 2. Лущение шпона
Часть 3. Сушка, сортирование и обработка шпона
Часть 4. Склеивание и обработка фанеры
Ни одна древесная плита не может сравниться с фанерой по этим показателям. Волокнистые и стружечные плиты производят из измельченного древесного сырья, то есть с разрушением природной структуры древесины. А фанеру склеивают из сухого лущеного шпона, который сохраняет все свойства древесины как природного полимера. Перекрестное направление волокон в смежных слоях многослойной фанеры позволяет в значительной степени устранить главный недостаток массивной древесины – анизотропию, то есть различие свойств вдоль и поперек волокон. Поэтому фанера ценится в первую очередь как строительный материал, позволяющий создавать надежные несущие и ограждающие конструкции деревянных и прочих (например, металлодеревянных) сооружений. Впрочем, она находит применение и в мебельных конструкциях.
Характеристика продукции
По объему выпуска лидирует фанера марок ФК и ФСФ. Фанера ФК изготавливается на карбамидных (мочевиноформальдегидных) смолах и имеет ограничения по атмосферостойкости (класс D3). Фанера ФСФ производится на фенолоформальдегидных смолах и считается атмосферостойкой (класс D4). Стандартный формат фанерных листов 1,525 × 1,525 м, что объясняется параметрами старых лущильных станков и клеильных прессов. Современные предприятия, оснащенные в основном импортным оборудованием, могут выпускать неквадратную фанеру, более подходящую для строительных целей, например формата 1,22 × 2,44 или 1,5 × 3,0 м. Максимальная толщина фанеры 40 мм.
Кроме необлицованной, многие заводы выпускают ламинированную фанеру, то есть покрытую синтетическими пленками. В строительстве ее часто используют как многоразовую опалубку.
Архангельский фанерный завод производит плиту фанерную трудногорючую атмосферостойкую (ПФА-Т) длиной до 3 м. Она предназначена для изготовления и ремонта внутреннего оборудования пассажирских железнодорожных вагонов всех типов, вагонов метрополитена, применяется в судостроении, а также в качестве строительных материалов (декоративно-отделочных, облицовочных) и для покрытия полов. Трудногорючая плита характеризуется медленным распространением пламени, умеренным образованием дыма, взрывобезопасностью. Эксплуатационный температурный интервал от –50°С до +45°С.
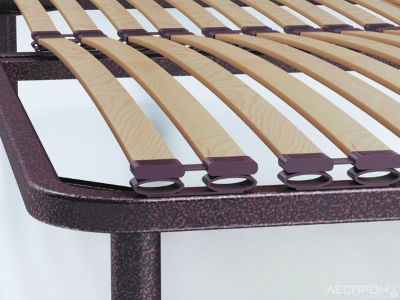
К фанерной продукции следует отнести и побочную продукцию из шпона, так называемые латофлексы – гнутоклееные детали, заменяющие пружины в мягкой мебели (рис. 1). Их толщина 8–12 мм.
Конструкция из латофлекса обеспечивает равномерную нагрузку на основание кровати и предотвращает прогибы, характерные для пружинных конструкций. Латофлесы выпускают несколько заводов, в частности Plyterra в Мордовии, «Парижская коммуна» в Ярославле, «Свеза» в Свердловской области.
Из специальных видов фанерной продукции нужно отметить бакелизированную фанеру, выпускаемую Пермской фанерной компанией. Этот материал используется в основном в судостроении. В отличие от обычной, в бакфанере слои шпона пропитаны бакелитовой (фенольной) смолой, а затем склеены под давлением примерно вдвое выше, чем в случае фанеры ФК и ФСФ. Морской регистр запрещает использовать стружечные и волокнистые плиты для изготовления судовой мебели и других конструкций, для этих целей подходят только бакфанера и фанера ФСФ.
Примерно 20 лет назад российские фанерные предприятия начали осваивать производство принципиально новой продукции из лущеного шпона – балок LVL (laminated veneer lumber). Склеенные из толcтого (примерно 3 мм) шпона, они используются в деревянном домостроении для создания несущих конструкций. Чаще всего изготавливается брус длиной 8–13,5 м, толщиной 21–75 мм и шириной 0,4–1,8 м. Ввиду повышенной прочности LVL-брус служит в основном для изготовления несущих элементов каркаса зданий: коньковых балок кровли, балок межэтажных перекрытий, стропил, а также как элемент силовой опалубки, способный заменить даже металлические конструкции.
LVL-брус выпускают два завода: «ЛВЛ-Югра» и «Талион Терра» (г. Торжок Тверской области). Первый оснащен оборудованием фирмы RAUTE (Финляндия) и производит до 40 тыс. м3 бруса в год с перспективой увеличения до 60 тыс. м3. Завод в Торжке работает на оборудовании Dieffenbacher (ФРГ) и выпускает в год 150 тыс. м3 бруса с возможностью роста до 250 тыс. м3. Продукция обоих предприятий в основном поставляется на экспорт.
На фанерных предприятиях попутно выпускают карандаши (остатки чураков при лущении). Этот вторичный продукт превращается в товарную продукцию после чистовой опиловки торцов. Досушивание карандашей проводится в атмосферных условиях на площадке продавца или покупателя. Обычно диаметр чураков длиной до 1,6 м составляет примерно 70 мм, а длиной 2,5 м – до 100 мм. У карандашей отличный товарный вид, и их используют в строительстве для создания малых форм (детских площадок, беседок и т. п.).
Подготовка сырья к лущению
Согласно действующему ГОСТ 3916.1–96 на фанеру общего назначения (ФК и ФСФ) для наружных слоев можно применять только лиственные породы: березу, ольху, клен, ильм, бук, осину, тополь, липу. Для внутренних слоев, кроме названных, допускаются хвойные породы: сосна, ель, лиственница, пихта и кедр.
В России основным сырьем для фанерного производства служат фанерные березовые кряжи диаметром от 20–22 см. Береза – наиболее подходящая для получения лущеного шпона порода в силу однородности строения и высокой прочности древесины. Большие запасы березы в лесах России обеспечивают определенное конкурентное преимущество российской фанерной продукции на мировом рынке. Для производства LVL-балок применяется в основном сосновый шпон.
Подготовка сырья к лущению включает три операции: гидротермообработку (ГТО), окорку и раскрой зимой. В зимнее время рационально первой операцией делать ГТО, так как это облегчает последующую окорку сырья, но требует устройства больших бассейнов с крышками для сохранения тепла, использования тяжелого кранового оборудования, а очистка бассейнов создает дополнительные экологические проблемы. На большинстве российских предприятий используют именно эту последовательность операций. На заводе «Талион Терра» используется бассейн проходного типа, в котором цепные конвейеры притапливают древесину и обеспечивают ее продвижение в ходе прогрева.
Кряжи обычно распиливаются на чураки круглыми пилами, диаметр которых может достигать 2000 мм. Заточка и обеспечение правильной формы таких пил представляет значительные сложности. Дешевле вариант раскряжевки с помощью цепных пил, используемый например, на некоторых предприятиях в США.
Интересен вариант разделка – окорка и оцилиндровка – проварка чураков, для которого требуется окорочно-оцилиндровочный станок. Его можно сконструировать на базе лущильного станка, если заменить ножевую траверсу и прижимную линейку оцилиндровочным узлом, работающим по принципу токарного станка. Подготовка сырья к лущению в этом случае будет следующая: подающий конвейер для кряжей – раскряжевочный станок – накопительное устройство (поперечный конвейер) – центровочно-загрузочное устройство – окорочно-оцилиндровочный станок с конвейером удаления отходов – линия сортировки чураков по диаметрам – проварочный бассейн.
Преимуществ у такого варианта перед традиционными способами подготовки сырья несколько:
- нет необходимости в тяжелом окорочном станке;
- смесь коры и шпона-рванины получается в измельченном виде и после подсушки готова к использовании в качестве топлива;
- вместо больших бассейнов для проварки фанерных кряжей с тяжелым крановым оборудованием используются малые, с простой загрузкой чураков, их отличают низкие теплопотери и возможность повышения температуры воды и уменьшения времени проварки;
- подача на лущильный станок прогретых оцилиндрованных чураков значительно снижает нагрузку на лущильный нож, продлевает его срок службы и сокращает длительность цикла лущения, то есть повышает производительность станка;
- на лущильном станке не нужно устанавливать специальное центровочное устройство, поскольку чураки правильной геометрической формы.
Общей тенденцией развития производств, работающих с круг¬лыми лесоматериалами, становится применение сканеров для оценки размеров и формы сырья. На основе этих измерений кряжи сортируются и распределяются по карманам. Такая технология уже используется на лесопильном производстве и со временем появится на фанерных заводах.
Текст Владимир Волынский