Фанерные предприятия России
Состояние и перспективы
Часть 4. Склеивание и обработка фанеры
В клеильно-обрезном цехе фанерного предприятия сборка пакетов может выполняться на одном рабочем месте или на пульсирующем конвейере – в зависимости от слойности фанеры. Для сокращения ручного труда используют различные питатели и укладчики шпона. При конвейерной сборке повышается производительность труда, но требуется укрупнение бригады и бóльшая производственная площадь.
Часть 1
Часть 2. Лущение шпона
Часть 3. Сушка, сортирование и обработка шпона
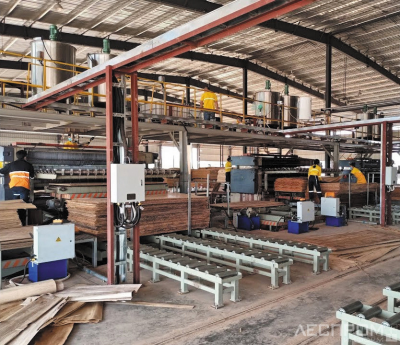
В клеильно-обрезном цехе фанерного предприятия сборка пакетов может выполняться на одном рабочем месте или на пульсирующем конвейере – в зависимости от слойности фанеры. Для сокращения ручного труда используют различные питатели и укладчики шпона. При конвейерной сборке повышается производительность труда, но требуется укрупнение бригады и бóльшая производственная площадь.
Основная идея механизации и автоматизации участка сборки пакетов на основе классических клеенаносящих вальцов – это обеспечение автоматической, без участия наборщика, подачи листов шпона из необходимого количества стоп к месту наборки (рис. 1). При этой концепции линию автоматической сборки можно условно разделить на два основных участка: станцию подачи шпона в вальцы и станцию подачи рубашек и сухих серединок. Необходимое количество подстопных мест определяется слойностью выпускаемой фанеры и применяемой технологией. По этой схеме сборку пакетов осуществляет один оператор, который попеременно получает автоматически необходимые листы шпона и укладывает их в пакет.
Холодная подпрессовка пакетов собранного шпона проводится непосредственно перед горячим прессованием для получения цельных пакетов, удобных для транспортирования и загрузки в горячий пресс. Холодное прессование позволяет исключить взаимное смещение листов, уменьшить повреждение наружных слоев, увеличить скорость транспортировки и загрузки в пресс, отказаться от использования прокладок, повысить производительность горячего пресса за счет повышения его этажности, сделать работу пресса независимой от сборки пакетов. Обычно один холодный пресс может обслуживать не менее двух горячих прессов.
Как показывает практика, цикл запрессовки составляет около 9 мин, что обеспечивает производительность около 10 м3/ч. Сборка стопы занимает примерно 24 мин, поэтому необходимо несколько мест сборки для полной загрузки одного холодного пресса. Время хранения подпрессованого пакета зависит от вида клея и температуры в помещении. Для фенольных клеев (без отвердителя) оно может составлять около 24 часов.
Основным оборудованием фанерного завода выступают горячие многоэтажные прессы. Наиболее удобным теплоносителем является насыщенный пар, при этом температура плит зависит от давления пара. При использовании перегретой воды уменьшаются потери тепла из-за парообразования, сокращается время прогрева, повышается равномерность температурного поля. В целом экономия тепла составляет до 25%.
Используются также высокотемпературные теплоносители – минеральные жидкости с температурой кипения до 300°С при нормальном давлении, например ароматизированый минеральный теплоноситель АМТ-300. Его применение позволяет отказаться от системы паропроводов, использовать электронагрев жидкости и ее циркуляцию без потерь при минимальном избыточном давлении.
Из зарубежных производителей прессов для фанеры следует отметить финскую фирму Raute, итальянскую Italpresse, японскую Yamamoto.
Raute предлагает серию прессового оборудования (Pro, Select, Smart) с системами загрузки-выгрузки. В прессе максимум 36 этажей (рис. 2).
Все прессы с автоматической системой управления, в том числе с контролем толщины готовой продукции. Давление прессования – до 2 МПа, производительность – до 60 тыс. м3 фанеры в год.
Фирма Italpresse выпускает широкий спектр прессового оборудования с плитами пресса размером от 1000 х 1000 до 3000 х 10 000 мм и от 1 до 50 этажей, в том числе прессы с механизмом одновременного смыкания плит (симультантным механизмом).
Многоэтажные прессы выпускает также и японская фирма Yamamoto (рис. 3).
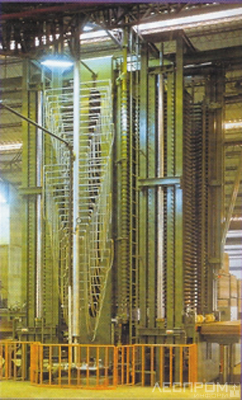
В прессе Yamamoto 45 этажей, усилие прессования 500 т, размер горячих плит пресса 2700 х 3500 х 70 мм, обогрев паром. Главные достоинства этого пресса – патентованные системы автоматического управления и новая система загрузки-выгрузки пакетов.
Такие характерные особенности, как быстрая загрузка пакетов шпона в горячий пресс и быстрое смыкание плит, позволяют сократить до минимума время закрытой выдержки (период от сборки пакета до приложения полного давления), и избежать преждевременного отверждения клея.
Послепрессовая обработка фанеры включает операции охлаждения, обрезки листов, сортирования, починки и (при необходимости) шлифования фанеры.
Охлаждение фанеры используется для снижения температуры и влажности листов, выгруженных из горячего пресса. Из фанеры ФК (на карбамидных клеях) при этом интенсивно выделяется свободный формальдегид. Для ускорения процесса используют веерные или конвейерные охладители. При их длине 6,5 м и скорости подачи 1 м/ мин время охлаждения составляет 6,5 минуты.
Обрезка кромок фанеры необходима для их выравнивания. Допустимые отклонения габаритов составляют 4–5 мм. Обрезку выполняют на круглопильных станках. Наиболее широко применяются 4-пильные агрегаты, составленные из двух 2-пильных станков, расположенных взаимно перпендикулярно.
Опиливание возможно по одному или двум листам с использованием гусеничной подачи при скорости подачи до 30 м/мин либо пачками толщиной до 120 мм. Во втором случае станки оснащаются каретками и обеспечивается более высокая производительность оборудования (скорость подачи 10–12 м/ мин). Следует использовать пилы с напаянными пластинками твердого сплава; для измельчения срезок на одном валу с пилой устанавливается фреза.
За последние годы многие предприятия создали полуавтоматические поточные линии для обработки клееной фанеры. В их состав обычно включают веерный охладитель фанеры, подъемный стол – накопитель листов, два двухпильных обрезных станка, устанавливаемых под углом 90° друг к другу, и транспортер.
Наиболее производительное зарубежное оборудование – это, вероятно, угловая линия обрезки и раскроя фанеры и плит компании Schelling (Австрия). Линия укомплектована автоматической загрузкой плит, пильными агрегатами с подрезными пилами для устранения сколов на нижней стороне, встроенной линией сортировки фанеры.
Фирма Raute (Финляндия) выпускает линии форматной обрезки фанеры в трех вариантах – Pro, Select и Smart. Все они в угловом исполнении с двумя двухпильными станками и различаются уровнем автоматизации на операциях подачи материала и настройки станков.
Почти неизбежной операцией послепрессовой обработки становится переобрез фанеры – опиливание листа до меньшего стандартного размера из-за наличия на нем недопустимого дефекта. Для этого используется однопильный станок типа ЦФ-5 с кареткой. Часто обрезанная полоса фанеры находит спрос как попутная продукция.
Сортирование фанеры в общем случае происходит по породам шпона наружных слоев, форматам, толщине, маркам и сортам. Процесс предусматривает три стадии:
- предварительное сортирование, с выделением экспортной фанеры, общего назначения и направляемой в переобрез;
- сортирование экспортной фанеры;
- сортирование фанеры общего назначения.
Фанера общего назначения для внутреннего рынка подразделяется по внешнему виду на сорта. Каждый лист осматривается с двух сторон и простукивается деревянным молоточком на предмет обнаружения пустот (непроклея). На современных линиях сортирования фанеры для этого используются ультразвуковые приборы. На участке сортирования также выполняется мелкий ремонт листов – заделка выпавших сучков, разошедшихся трещин, слабых углов, пузырей, обзола и т. п. На листе фанеры ставится штамп, указывающий сорт фанеры и номер сортировщика.
Линия сортирования фанеры фирмы «Технолес М» (совместно с Grecon и другими фирмами) предназначена для решения следующих задач:
- приема стоп обрезной фанеры;
- полистной загрузки фанеры;
- автоматического определения пустот и отклонения по толщине листа фанеры;
- визуального определения оператором сортности фанеры;
- ручного разворота листов в плоскости на 90º или 180º (при необходимости);
- загрузки поддонов;
- автоматической маркировки каждого листа;
- автоматической укладки фанеры на пять подстопных мест согласно сортности;
- выгрузки подготовленных к упаковке стоп фанеры на рольганги.
Шлифование фанеры выполняется выборочно, по требованию заказчика. Барабанные шлифовальные станки сегодня почти не используются, так как они требуют частой смены шлифовальной шкурки и не обеспечивают нужного качества обработки. Гораздо совершеннее широколенточные двухсторонние станки, например фирмы Steinemann, отличающиеся более высокими производительностью и точностью обработки.
Текст Владимир Волынский