Фанерные предприятия России
Часть 3. Сушка, сортирование и обработка шпона
Начальная влажность шпона до сушки колеблется в широких пределах и зависит от породы древесины, времени и способа доставки сырья, его хранения, условий подготовки к лущению и режима лущения. Конечная влажность шпона определяется видом используемого клея и варьирует от 7 до 12%. Меньшие значения относятся к фенольным связующим низкой концентрации, так как они сильнее увлажняют шпон в момент нанесения клея.
Часть 1
Часть 2. Лущение шпона
Часть 4. Склеивание и обработка фанеры
На российских заводах используют в основном роликовые сушилки с обогревом паром или топочными газами. Ярославский завод «Пролетарская свобода» выпускает газовые сушилки СРГ-25М с теплогенератором ТСГВ-5.1, работающим на отходах фанерного производства. Сушилка состоит из восьми этажей рабочей шириной 3900 мм, что позволяет загружать на каждый этаж два листа шпона шириной до 1800 мм. Температура газовоздушной смеси на входе до 260°С, производительность сушилки примерно 5 м3/ч. Установленная мощность сушилки около 250 кВт.
На рынке можно видеть предложения китайской фирмы EcoWood по паровым сушилкам рабочей шириной до 5900 мм (рис. 1), то есть для загрузки сразу трех листов шпона на этаж. В них до шести этажей, скорость движения шпона – 15 м/ мин, производительность – до 8 м3/ч.
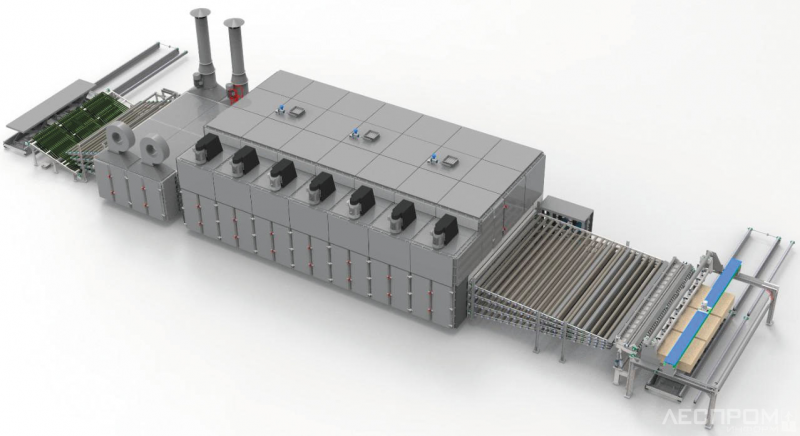
Большим недостатком сушильных цехов старых производств признается большая доля ручного труда, особенно на операциях загрузки шпона в сушилку и сортирования шпона. Восьмиэтажные сушилки СРГ оснащены механизмом распределения шпона по этажам, но подача листов шпона часто выполняется вручную, это тяжело для рабочего. Здесь в системе «человек – машина» организация труда решена в пользу машины (то есть сушилки), поскольку ритм работы задается машиной, а человек вынужден подчиняться. Модернизация производства должна быть направлена на устранения тяжелого ручного труда. Существуют довольно простые механизмы с вакуумными присосками, которые способны полностью заменить человека на этой операции.
Не менее трудоемка ручная сортировка шпона по сортам. При отсутствии механизации одна сортировщица обрабатывает 500–600 листов в час, перенося 11,5 т груза и проходя расстояние до 3 км. Современное предприятие должно переходить на автоматизированную сортировку шпона.
В автоматических сортировках фирмы Raute сухой шпон из сушилки попадает сразу на поперечный конвейер. Оператор визуально оценивает сорт каждого листа и нажимает номер соответствующего кармана. Листы шпона затем с помощью вакуумных присосок поджимаются к верхней перфорированной ленте конвейера и транспортируются до своего места. После формирования стопу высотой до 700 мм выкатывают на параллельный рольганг.
Существуют линии сортирования с автоматической оценкой качества шпона при помощи сканеров и встроенного компьютера. Система улавливает темные места на листе шпона, определяет их количество, размеры, площадь и сравнивает результат с эталонами, сохраненными в ее памяти, на основании чего выносит решение о присвоении того или иного сорта (рис. 2).
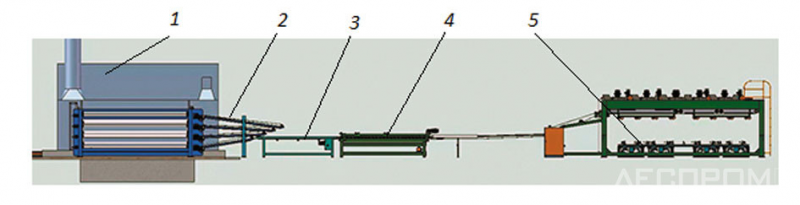
В стопе всегда уложен шпон одной породы древесины и одной толщины. Сортировка ставит целью разделить листы шпона по качеству (сортам) и назначению (для починки шпона и ребросклеивания).
Починка заключается в постановке специальных заплат вместо сучков, что позволяет повысить сорт материала на один разряд. Основной отечественный станок ПШ-2 установлен на многих российских предприятиях. Вырубка сучка и постановка заплатки выполняется на нем автоматически. Сучки вырубаются из специальных полос шпона, для получения которых предназначены делительные станки, например СД-800 (рис. 3) фирмы МАГР (Россия, г. Брянск).
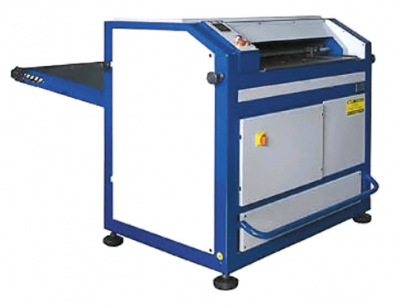
Рабочий на станке ПШ-2 только перемещает лист в нужную позицию и нажимает педаль для срабатывания всей системы. Тем не менее и эта операция утомительная и может быть автоматизирована.
RoboPatching – полностью автоматизированная система починки шпона, по производительности почти в два раза превосходящая станок-полуавтомат. RoboPatching (рис. 4) работает так: система поиска обнаруживает дефект шпона, определяет его координаты относительно заданной точки и передает их промышленному роботу, который подводит дефектное место шпона под штамп починочного станка, работающего в обычном режиме. Производительность системы до 1000 заплаток в час.
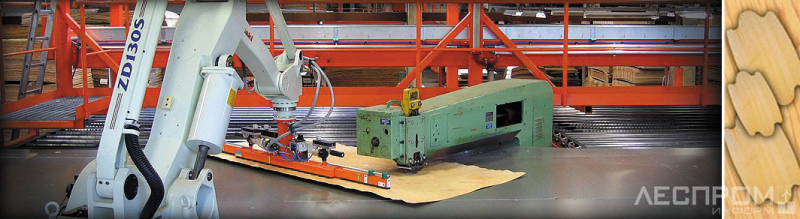
В станке-полуавтомате Patchmaster PM100 используются заплатки сложной формы, которые надежно фиксируются в листе шпона.
Обработка кускового и неформатного шпона заключается в превращении его в полноформатный шпон, например, размером 1600 х 1600 мм. Обычная технология предусматривает использование для этой цели гильотинных ножниц и линии ребросклеивания. На ножницах пачка шпона примерно одной ширины обрубается ножом с двух сторон для получения точной прямолинейной кромки, а на линии выполняется поперечное ребросклеивание (стяжка) шпона термопластичными нитями.
Современное оборудование отличается тем, что в линию ребросклеивания встроены пневматические ножницы, которые обеспечивают получение прямой кромки, что исключает применение гильотинных ножниц. Наряду с немецкими и финскими станками в последние годы в поставках оборудования часто можно видеть японское и тайваньское оборудование. В 2010-х годах в России появилась первая японская линия ребросклейки от компании Hashimoto Denki. На ней проводится последовательно контроль толщины шпона, прирубка кромок, вырубка дефектов, соединение кусков каплями термопластичного клея и упрочнение нитями с одной стороны.
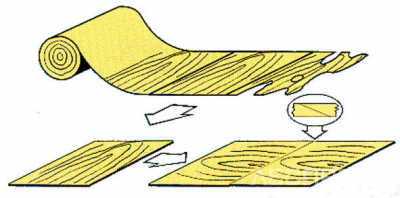
Помимо склеивания по ширине для получения форматного шпона из кусков, на фанерном предприятии часто возникает необходимость сращивания листов шпона по длине. Это особенно актуально при производстве строительной фанеры размером 1220 х 2440 мм из чураков длиной 1,3 м. Укорачивание чурака уменьшает его кривизну и повышает выход шпона. Последующее сращивание коротких кусков шпона по длине открывает возможность для производства большеформатных плит при одновременном повышении полезного выхода шпона из сырья. Для получения достаточной прочности склеивания используют усовое соединение с длиной уса 25–40 мм.
При небольших объемах работ можно использовать отдельные специальные станки – усовочный JVS для формирования скоса по торцам листа шпона и узкоплитный пресс JVPS для склеивания листов шпона. Усовочный станок оснащен двумя пилами для калибровки длины листа и двумя пилами для нарезки уса. Эти станки могут обрабатывать шпон толщиной от 1,5 до 3,2 мм, длина уса составляет 25 мм.
На крупном производстве эти станки объединены в линию. Фирма Raute-Wood выпускает три варианта линий сращивания: с ручным управлением, полуавтоматическую и автоматическую. Автоматическая линия отличается наличием сканирующей камеры, калибровочной пилы для стабилизации ширины листа (размера вдоль волокон), контролем размеров шпона для управления процессом сращивания. В ней достаточно трех прессов на один усовочный станок.
Текст Владимир Волынский
Окончание следует