LIGNA+ – взгляд из «каменного» века
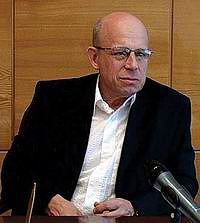
Лесопромышленники Вологодской области в Ганновере на выставке LIGNA+ 2007 своей активностью сумели затмить соседей по Северо-Западному региону. «Видно было, что Вологодская область работает, и нам было, что сказать», – так выразил свое мнение генеральный директор ЗАО «Череповецкий ФМК» Евгений Коротков. И не без оснований, ведь именно череповецкое предприятие сыграло первую скрипку вологодского лесопромышленного оркестра в Германии.
Больше всего в дни выставки вологодская делегация контактировала с компанией «Диффенбахер», с её собственниками была проведена официальная встреча. И это не случайно: Череповецкий фанерно-мебельный комбинат сейчас реализует совместно со знаменитой немецкой фирмой, выпускающей оборудование для деревопереработки, проект по созданию нового завода по производству ДСП. В Германии стороны не ограничились протокольной встречей, а подписали дополнительный контракт в рамках реализуемой программы о сроках поставки оборудования.
Кроме того, представители ЧФМК заключили соглашение с фирмой «Пал» о покупке оборудования сортировки стружки для того же производства. Генеральный директор комбината Евгений Коротков пояснил, что предприятие не закупает у «Диффенбахера» полный комплекс: «Часть оборудования будем брать сами, ведь завод не строится одной фирмой, там может быть оборудование со всего света. Было приятно, что на выставке мы и область выглядели достойно. Было видно, что мы работаем, а не просто декларации делаем, у нас есть большой проект, который действительно реализуется».
Завод, который совместно построят компания «Диффенбахер» и Череповецкий фанерно-мебельный комбинат, будет работать по современной технологии непрерывного прессования. «Мы посмотрели подобный завод в Германии и были, откровенно говоря, в восторге, – продолжает делиться впечатлениями руководитель Череповецкого комбината. – По сравнению с тем, что там увидели, мы находимся в каменном веке. И такое производство мы начинаем строить на комбинате. У меня даже есть опасения, сможем ли мы его хорошо обслуживать – это самые передовые технологии. На „Диффенбахере“ создан специальный сервисный центр, в который в режиме on-line поступает вся информация с линий, там она постоянно анализируется. То есть сбои и неполадки могут быть предупреждены или устранены без промедления. Мы к такой работе не привыкли, это не только дело компетентности и профессионализма, нам нужно менять менталитет».

Действительно, качественно новые технологии требуют и качественно нового мышления. Недостаток средств остается главной преградой для создания новых производств, пока этот барьер не преодолен. Но деньги могут быть потрачены зря, если некому будет управлять современным оборудованием и технологиями. Решая глобальные проблемы плитного подразделения, представители череповецкого комбината основательно позаботились и о своем фанерном производстве. Предприятие купило линию ребросклейки шпона японской фирмы «Хошимото». На выставке фирма-производитель представляла купленное череповецким комбинатом оборудование в действии. Линия вызвала большой интерес у участников «Лигна+». Сейчас линия монтируется на предприятии в Череповце.
Выставка – это во многом яркое шоу, а техника должна доказать свою состоятельность в ежедневной работе, лишенной рекламного пафоса. О том, что такое ребросклейка шпона, и зачем она нужна, нам рассказал главный инженер Череповецкого ФМК Александр Ремезов. При лущении фанерного сырья, то есть при производстве шпона, образуется так называемый неформатный шпон, использование которого ограничено. «Неформат» идет на фанеру низких сортов или на производство клееных деталей.
Линия «Хошимото» склеивает шпон шириной 1600 мм. Для этого, во-первых, точечно наносится клей в месте стыка, во-вторых, листы сшиваются 5 полимерными нитями, за счет этого обеспечивается достаточно высокое качество склеенного листа, а его уже можно использовать для производства фанеры.
Череповецкое предприятие установило уже третью подобную линию. Первая, финская, была приобретена ещё в 1993 году. (Конечно, она не конкурент последним разработкам.) Вторая линия, установленная 3 года назад, тоже фирмы «Хошимото». Последнее приобретение – её аналог, но, конечно, модернизированный. «Эта линия поумней», – коротко охарактеризовал разницу Александр Ремезов.
Нельзя сказать, что линии по ребросклейке стоят на российских предприятиях по производству фанеры повсеместно, но сейчас их стараются ставить все, поскольку повсеместным стал дефицит древесины, который сопровождается ещё и значительным скачком цен на сырье, в особенности в последние полгода. Ребросклейка позволяет использовать весь неформатный кусковый шпон для производства фанеры практически любого качества (нельзя полностью использовать лишь рваные мелкие куски и куски с корой («закоры»)).
А значит, сырье используется по максимуму. То, что отдавали за дешево или вовсе отправляли в отходы, начинает приносить прибыль. Выгода не только в экономии сырья. При работе со склеенным шпоном возрастает до 30% производительность труда при наборе фанеры, то есть листов шпона. Ведь одно дело набирать лист кусочками, другое – шпоном полноценного формата.
Как ни странно, при росте производительности улучшается и качество. И то, и другое – лишь следствие использования полноценного форматного шпона, изготовленного на линии ребросклейки. Главный инженер ЧФМК Александр Ремезов поясняет нюансы современных требований по качеству фанерной продукции: «Сегодня требования по фанере низших сортов ужесточились. Не допускаются так называемые валики, которые обычно образуются при использовании неформатного шпона на серединные слои. Они обычно возникают при нахлесте этих неформатных кусков и достаточно заметны на фанере малой толщины. При использовании склеенных кусков такого уже не случится».
Доводов в пользу использования оборудования по ребросклейке шпона у производителей фанеры достаточно. Есть выбор, есть и приоритеты. «В России популярны станки финских компаний „Рауте“ и „Плайтег“, немецкое оборудование „Купер“, – продолжает профессиональный ликбез Александр Ремезов. – В последние 3 года хорошо продаваемым стало японское оборудование фирмы „Хошимото“. Не остались и мы в стороне – вот уже купили вторую японскую линию. Оборудование для ребросклейки производят итальянцы, бразильцы, американцы, но у нас их техника распространения не получила. Есть ещё тайваньские станки, очень похожие на „Хошимото“, но через год они начинают выходить из строя».
По словам главного инженера предприятия, 3 линии, что теперь будут работать на фанерном производстве, полностью покроют потребности комбината. Кусковой неформатный шпон полностью будет склеиваться, рваные куски и «закоры» пойдут на склейку частично. Конечно, первая линия склейки требует ремонта, но заменить её на новую пока нет возможности – удовольствие это дорогое.
Но нужно подчеркнуть, что в японском оборудовании череповчане уверены, так как убедились в его надежности на примере первой линии «Хошимото», которая работает на комбинате уже 3 года.
Максим РОДИОНОВ
Другие статьи рубрики Тема номера: LIGNA+ 2007
LIGNA+
Душа и дерево едины
«Шоу монстров»
Группа Weinig: укрепляя первенство!
«Щекиноазот»: от возрождения к развитию
Как вологодские инженеры на «Лигну» съездили…
MDF’изация Томской области
Хранители мебельных традиций Северо-Запада
WoodEye завоевывает Европу
Фотографии с выставки LIGNA 2009
Фотографии с выставки LIGNA+ 2007
Фотографии с выставки LIGNA+ 2005
Статья Ligna 2009. Шоу поворотливых слонов
Статья LIGNA+ HANNOVER − 2005