Солома для денег или деньги из соломы
Производство и сжигание гранулированных отходов растениеводства
Рис. 1. Вид линии по гранулированию соломы (с. Заветное, Ростовская область)/strong>
Рис. 2. Вид котельной установки с котлом для сжигания гранул, изготовленных из отходов растениеводства
Рисунки смотрите в PDF-версии журнала
Сохраняющиеся высокие цены на традиционные энергоносители и ужесточающиеся требования к охране окружающей среды обуславливают высокий интерес производителей и потребителей тепловой и электрической энергии, научных организаций к использованию в качестве топлива нетрадиционных и возобновляемых источников энергии, в том числе биомассы. Вступление в силу ряда постановлений Правительства России, определяющих порядок реализации квот на выбросы двуокиси углерода при проведении организационно-технических мероприятий по замене угля и мазута биомассой, обеспечивает финансовый источник для проведения таких мероприятий, что также способствует интенсификации научных исследований и опытно-конструкторских работ по созданию современных котельных установок, работающих на биомассе.
Обычно при упоминании биомассы прежде всего обращается внимание на использование древесной биомассы в качестве топлива, поскольку древесная биомасса − самый древний источник энергии. Однако в исходном состоянии древесная биомасса характеризуется высокой влажностью и относительно низкой теплотой сгорания, и для использования в качестве топлива в котельных установках относительно высокой (более 100 кВт) мощности она должна быть переработана в щепу, а лучше в гранулы (пеллеты). Это позволит относительно просто механизировать и автоматизировать котельные установки, сократить затраты на транспортировку и хранение этого топлива. Из-за высокой влажности древесной биомассы переработка ее в пеллеты является дорогостоящим мероприятием, до 70% затрат на производство таких пеллет приходится на сушку биомассы.
Другой вид биомассы − отходы растениеводства (солома, лузга подсолнечника, риса, проса и т. п.), которые имеют невысокую исходную влажность. В отличие от древесной, эта биомасса, как правило, так и остается отходами, для утилизации которых в любом случае требуются относительно большие затраты. В среднем в 2001−2008 годах в России собирали 38 млн т соломы озимых культур ежегодно. Такую солому используют в животноводстве в тех странах, где оно высоко развито, например в Дании − 36,5% всей собираемой. В РФ около 24 млн т соломы может быть использовано в качестве топлива. Кроме соломы, как топливо можно использовать 1,5−2,0 млн т лузги подсолнечника, 200−300 тыс. т лузги проса, примерно столько же лузги гречихи и других отходов. За исключением лузги подсолнечника использование отходов растениеводства в качестве топлива сопряжено с рядом трудностей, обусловленных их химическим составом.
сухой соломы и древесины
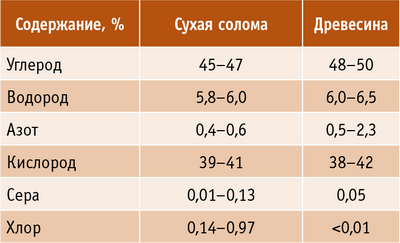
Солома по элементарному составу (табл. 1) и теплоте сгорания (табл. 2) не слишком отличается от древесины, хотя теплота сгорания соломы все же ниже, чем аналогичный параметр сухой древесины. Вместе с тем, с учетом обычной влажности (ниже 20%) солома превосходит по теплоте сгорания древесную щепу, которая в настоящее время начинает широко использоваться в северо-западных и восточных регионах России и давно используется в странах Северной Европы.
В соломе содержатся следующие элементы (% по массе): азот − 0,45−1,13, калий − 0,5−1,7, хлор − 0,11−0,77. Азот увеличивает эмиссию NO2. Содержание серы в соломе различных культур колеблется от 0,10 до 0,77% по массе. Наименьшее содержание серы наблюдается в соломе озимой ржи (~0,16% по массе) и озимой пшеницы (~0,18% по массе), наибольшее − в соломе рапса (~0,56% по массе). В целом содержание серы в соломе можно считать низким
зерновых культур
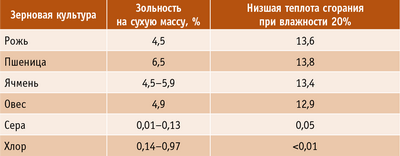
Температура начала деформации золы у сухой соломы − 735−840°C, а у древесины − 1150−1405°C. Зола соломы размягчается при 1035−1150°С, а плавится при 1175−1330°C, а зола древесины размягчается при температуре 1180−1525°C, а плавится при 1225−1650°C.
Высокое содержание хлора в соломе овса, ячменя и рапса обуславливает усиленную коррозию теплообменного оборудования. Причем в «желтой» (свежеубранной) соломе содержится почти в четыре раза больше хлора, чем в «серой» (увядшей). Для вымывания хлоридов из соломы достаточно 5−7 дней.
Самой большой проблемой при сжигании соломы озимой пшеницы, красной канарской травы, зерноотходов, в том числе и в виде гранул, является низкая температура плавления золы, обуславливающая образование золошлаковых агломератов, препятствующих горению и нормальной работе котлов, предназначенных для сжигания древесных гранул.
При сжигании гранул, произведенных из отходов растениеводства, в кипящем слое инертного материала также образуются шлаковые агломераты. Причем установлено: чем выше вероятность образования в кипящем слое таких агломератов, тем выше вероятность образования отложений золы на конвективных поверхностях нагрева котлов и коррозии поверхностей нагрева под этими отложениями.
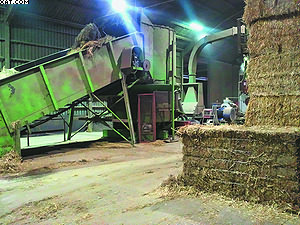
Рис. 2. Вид котельной установки с котлом для
сжигания гранул, изготовленных из отходов
растениеводства
При относительно небольшой мощности котла (400 кВт) и, казалось бы, невысокой зольности топлива (зерноотходы и солома) весь объем топки практически заполнен очаговым остатком (невыгоревшим фиксированным углеродом). Это обуславливает падение КПД котлов до 70%, тогда как при сжигании древесных отходов очагового остатка практически нет и КПД котла типа Ökotherm, работающего на этом топливе, достигает 90−92% [2].
Проблемы при сжигании отходов растениеводства возникают вне зависимости от их вида: натурального (лузга, зерноотходы), сечки или тюков (солома) или гранул. Но в некоторых случаях, например при сжигании в топках теплогенераторов сушильных установок, большая мощность теплогенерирующего оборудования предопределяет использование этих отходов только в виде гранул. Между прочим, по оценкам Тамбовского государственного технического университета всего лишь 2,5 млн т соломенных гранул способны заменить все жидкое топливо, которое ныне используется в нашей стране для сушки зерна и зернопродуктов.
Однако при гранулировании соломы возникают большие проблемы, которые обуславливают чрезвычайно малый объем производства соломенных гранул во всем мире, а не только в России и странах СНГ. В отсутствии же производства гранул нет смысла решать проблемы, связанные с их сжиганием. Несколько лет назад специалистами ТГТУ была поставлена цель доказать потенциальным производителям и потребителям гранул из той же соломы, что производить такие гранулы выгодно и технически возможно.
В 2007 году администрация Ростовской области поддержала предложение ТГТУ о строительстве пилотной линии по производству гранул из соломы в одном из районов области, где в обозримом будущем не планировалась газификация. К таким регионам относятся восточные районы Ростовской области, граничащие с Республикой Калмыкия и Волгоградской областью. Сельское хозяйство там представлено овцеводством и выращиванием зерновых культур. В одном только Заветинском районе Ростовской области, по данным районного управления сельского хозяйства, под озимыми в 2006 году было занято 34 568 га (в коллективных хозяйствах 21 571 га). Причем в последние семь лет отмечается тенденция увеличения в районе площади, занятой озимыми. Урожайность озимых в районе невысокая (из-за плохих климатических условий), но в последние годы выросла более чем в полтора раза. Валовый сбор соломы озимых в 2006 году составил 56 тыс. т, а в 2000−2006 годах − в среднем 46,7 тыс. т в год. В коллективных хозяйствах валовый сбор озимой соломы в 2006 году составил 36 тыс. т, а в среднем за семь лет − 31,1 тыс. т в год. На 6−8 тыс. га озимые убираются с измельчением для поддержания плодородия почвы. Для нужд животноводства в районе используется 15−18 тыс. т соломы, в основном яровых культур. Валовый сбор соломы яровых составил в 2006 году 38 тыс. т. Таким образом, в 2006 году невостребованными оказались около 40 тыс. т соломы озимых. В среднем в 2000−2006 годах ежегодно оставались невостребованными и сжигались на полях около 28 тыс. т соломы озимых. В случае получения положительного результата при реализации проекта планировалось на первом этапе заменить 50?% угля, сжигаемого в муниципальных котельных района, а в дальнейшем увеличить производство соломенных гранул до 12 тыс. т в год, чтобы полностью заменить ими уголь как в муниципальной энергетике, так и в быту. При этом надо иметь в виду, что расчетная стоимость гранул из соломы составляет 1200−2500 руб./т (в зависимости от стоимости соломы, электроэнергии, рабочей силы и т. п.), а стоимость угля − 5500 руб./т (в ценах 2009 года). С учетом того что теплотворная способность угля, применяемого в Заветинском районе, не более чем на 30% выше теплотворной способности соломенных гранул, преимущества использования последних очевидны.
Из-за ограниченности финансовых ресурсов для производства соломенных гранул было выбрано относительно недорогое оборудование отечественного производства. Оно включало стандартный набор, состоящий из дробилки соломенной сечки типа ДКР-3, бункера-накопителя соломенной муки, гранулятора ОГМ-0,8 с дозатором и смесителем, транспортера готовых гранул, колонки охлаждения со столом рассева, нории для транспортирования гранул в бункер готовой продукции.
Планировалось, что солома будет заготавливаться в виде тюков диаметром 145 мм и длиной 140 мм и измельчаться в сечку с помощью измельчителя ИРК-145. Однако оказалось, что использовать указанный измельчитель невозможно, так как сечка получалась длиной до 200 мм, что затрудняло ее загрузку в дробилку и резко снижало производительность установки. В основном эти сложности обуславливались климатическими условиями, в которых выращиваются зерновые в Заветинском районе. С середины апреля до конца октября в районе устанавливается жаркая погода со средней температурой воздуха в летние месяцы (в период уборки) 35−45°С. В этот период стебель зерновых имеет длину 150−250 мм, влажность соломы падает до 4%. В таких условиях очень трудно получить плотные тюки соломы; насыпная плотность соломы в тюках − в среднем 88 кг/м3. При измельчении в ИРК-145 такой тюк расслаивается, более короткие стебли соломы проскакивают через ножи измельчителя практически нетронутыми.
Поэтому был применен измельчитель рулонов соломы принципиально новой конструкции, который позволяет не только измельчать солому в сечку длиной до 50 мм, но и тонко регулировать производительность для возможности совмещения его с дробилкой ДКР-3. Был разработан специальный переход между дробилкой и измельчителем, обеспечивающий перемещение материала во взвешенном состоянии. Таким образом, была решена проблема измельчения соломы при исходной влажности материала не выше 20%.
Сложности возникли также с гранулированием соломы. Из-за низкого содержания лигнина в соломе на первом этапе было трудно регулировать влажность соломенной муки для получения качественных гранул. От обработки соломы паром пришлось отказаться ввиду больших энергозатрат, а обработка соломенной муки водой давала низкий эффект. Решено было получать качественные гранулы за счет увеличения степени сжатия муки в матрице гранулятора. Была применена специальная матрица с двухступенчатой фильерой, гранулятор ОГМ-0,8 был заменен на гранулятор ОГМ-1,5, на главный привод которого был установлен электродвигатель мощностью 110 кВт. В результате были получены очень качественные гранулы с блестящей поверхностью. При влажности соломы 7−20% производительность линии достигала 600−700 кг/ч. При этом было отмечено, что хорошо гранулируется не только свежеубранная солома, но и солома урожая 2-3-летней давности, если в тюках нет гнилой соломы. Линия была введена в эксплуатацию осенью 2009 года.
Произведенные соломенные гранулы будут сжигаться в котлах конструкции ТГТУ, в которых реализуется технология сжигания гранул из соломы, лузги проса, риса и подобных отходов в кипящем слое, который формируют сами гранулы и твердые продукты их горения (частицы коксового остатка и золы). Образующаяся при таком горении гранул зола измельчается тяжелыми гранулами, постоянно поступающими в слой. Мелкие частицы золы уносятся из слоя из-за высоких скоростей газов в слое, которые нужны для поддержания во взвешенном состоянии тяжелых гранул. Это препятствует накоплению соединений калия − основной причине образования золошлаковых агломератов. Кроме того, даже если такие агломераты и образуются, они сразу же разрушаются постоянно движущимися тяжелыми гранулами.
КПД котлов мощностью 200, 300, 500 и 1000 кВт при сжигании гранул, произведенных из отходов растениеводства, − не ниже 85%.
Исследования, проведенные ТГТУ, показали, что при сжигании биогранул (в том числе изготовленных из отходов растениеводства) в кипящем слое, сформированном самими гранулами, частицами их коксового остатка и золой, температура в слое достигает 1000−1100?°С, что достаточно для воспламенения и устойчивого горения коксового остатка; движущиеся частицы постоянно разрушают образующиеся в слое золошлаковые агломераты, поэтому очаговый остаток имеет порошкообразную структуру. В результате при сжигании по предложенному способу гранул из соломы потери от механической неполноты сгорания составляют 7,94%, тогда как при сжигании в обычном гранульном котле Pelling-27 (Чехия) в плотном слое движущихся гранул − 36,44%, при сжигании гранул из лузги проса − 15,76% против 30,12%, гранул из лузги риса − 10,07% против 43,02%, гранул из лузги подсолнечника − 4,96% против 12,46%.
В марте 2010 года делегация в составе ведущих специалистов биоэнергетического центра ТГТУ и руководства фирмы EKO Holz und Pellets (ФРГ) по приглашению итальянской компании − производителя оборудования для гранулирования отходов АПК General Dies s.r.l. посетила в Италии ряд заводов, гранулирующих биомассу из отходов растениеводства, и в том числе самый крупный в южной Европе завод в провинции Лацио, состоящий из двух линий гранулирования производительностью 5 т гранул в час каждая.
Сергей ПЕРЕДЕРИЙ
Использованная литература
1. 1. Ronnbäck M., Johansson M., Claesson F. Combustion test in residential burners of pellets from new ash rich biomass // Proceeding on European Pellets Conferences. Wels, Austria, 2009.
2. Kiesewalter S., Rohricht C. Pelletierung von Stroh und Heu // In Proceeding on European Pellets Conferences. Wels, Austria, 2004. Р. 283−296.