Технологические параметры горячего прессования плит
Редакция продолжает цикл публикаций, рассказывающих о технологических процессах производства древесных плит.
Компоненты древесных плит
Прессы для изготовления древесных плит
Послепрессовая обработка древесных плит
Входной и текущий контроль качества продукции на плитных производствах
Древесные плиты в строительстве
Эти удивительно полезные ДВП
Материалы ДПК: долговечность, прочность, качество
Масса, поступающая в пресс, состоит из твердого вещества, воды и воздуха. Под влиянием тепла и давления в этой трехфазной системе происходят сложные физико-химические процессы. На первой стадии прессования сближаются древесные частицы и вытесняется воздух, начинают действовать силы молекулярного сближения, древесные частицы переплетаются. При дальнейшем росте давления частицы деформируются, площадь их контактов увеличивается. С увеличением температуры древесина становится более пластичной, упрессовка достигает 70-90%. Чтобы добиться равномерной толщины древесных плит, их прессуют с использованием дистанционных прокладок. Толщина плит пресса - 140-180 мм (для сравнения: в прессах для изготовления клееной фанеры она составляет 42-45 мм).
Перечислим основные параметры, характеризующие режим прессования древесных плит.
Влажность прессуемой массы
В производстве ДСП влажность осмоленной стружки для наружных слоев составляет 14-18%, для внутренних - 9-15%. Избыточная влажность ведет к расслоению и разрывам изготавливаемых плит. Чем выше содержание влаги, тем больше времени требуется для ее выпаривания из пакетов в горячем прессе. При формировании и транспортировке ковра его влажность снижается незначительно (на 1%) и при загрузке в пресс составляет 10-14%. Для достижения равновесной (конечной) влажности 8±2% в процессе горячего прессования плит необходимо удалить из них от 2 до 6% влаги, на что требуются время и тепловая энергия.
Температура прессования
Рабочая температура плит современных многоэтажных прессов 150-180 °C, одноэтажных - 180-220 °C, допустимое отклонение от заданной температуры в пределах одной нагревательной плиты ±5 °C. При максимально допустимой температуре 220 °C необходимо использовать для нагрева минеральные или органические высокотемпературные теплоносители и сократить время загрузки пресса и смыкания плит до 45 с. В производстве плит MDF волокнистый ковер часто предварительно прогревают токами высокой частоты, чтобы обеспечить надежное отверждение связующего внутри плиты.
Давление прессования
Оно зависит главным образом от задаваемой плотности плит, а также от влажности и размеров частиц и продолжительности прессования. Задавать давление следует так, чтобы упрессовка пакета до требуемой толщины (посадка на планки) продолжалась не более 30 с. Величина давления прессования в производстве плит: для ДСП и ЦСП - 1,8-2,2 МПа, для MDF и OSB 2,0-2,5 МПа, для твердых ДВП, получаемых мокрым способом, - 4,2-5,5 МПа.
Продолжительность прессования
Время, затрачиваемое на прессование, зависит в основном от температуры плит пресса и вида связующего. В многоэтажных установках с рабочей температурой не выше 180°C удельная продолжительность прессования при использовании карбамидных клеев составляет 0,18-0,22 мин/мм толщины готовой плиты. Соответствующие показатели для фенольных клеев - 0,20-0,22 мин/мм, для изоцианатных - 0,18-0,20 мин/мм. В одноэтажных прессах можно поднимать температуру до 220°C и сокращать удельную продолжительность прессования при использовании карбамидных, меламиновых и изоцианатных клеев до 0,12-0,14 мин/мм, при использовании фенольных клеев - до 0,15-0,18 мин/мм.
Цикл прессования, рассмотренный на примере изготовления трехслойных стружечных плит толщиной 18 мм в многоэтажном прессе, изображен на рис. 1.
Согласно данным, полученным на одном из российских заводов, этот цикл при бесподдонном прессовании складывается из следующих операций:
● загрузка пакетов - 7 с
● смыкание плит пресса - 3 с
● повышение давления - 20 с
● посадка на планки - 60 с
● выдерживание под давлением - 70 с
● снятие давления - 173 с
● выдерживание без давления - 50 с
● размыкание плит пресса - 3 с
● выгрузка пакетов - 7 с
Итого: 393 с.
производства
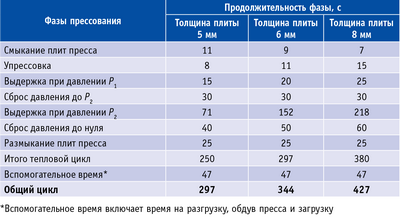
Таблица 2. Технологический режим прессования твердых ДВП
мокрого способа производства толщиной 3,2 мм при ширине ковра
1830 мм
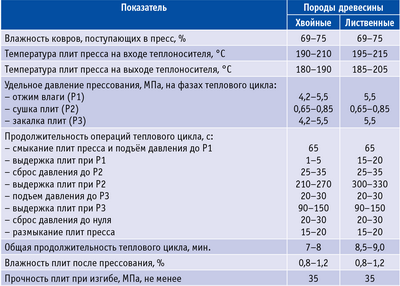
Чтобы избежать преждевременного отверждения связующего, на многоэтажных прессах устанавливают симультанты - механизмы синхронного смыкания рабочих плит. Опасность расслоения плит под воздействием интенсивного парообразования в значительной мере устраняется, если снижать давление плавно, в течение длительного времени. В приведенном выше примере общее время цикла около семи минут, из них на снижение давления и выдержку без него отводится почти четыре минуты.
Цикл прессования тонких (5-8 мм) ДВП сухого способа изготовления отличается тем, что после довольно кратковременной выдержки ковра под давлением Р1 (6-6,5 МПа) давление в течение 30 с понижается до Р2 (1-1,5 МПа). Под этим давлением материал довольно долго выдерживается, затем происходит постепенный сброс давления и медленное разведение рабочих плит (рис. 1).
При мокром способе изготовления ДВП принципиально иной характер циклограммы (рис. 3, табл. 2), так как в горячем прессе волокнистый ковер не только прессуется, но и освобождается от большого количества влаги. В первой фазе (отжим влаги), по мере того как под воздействием давления из волокнистого ковра отделяется свободная влага, он прогревается и уплотняется. Во второй фазе (сушка) изготавливаемый материал выдерживается при пониженном давлении для эффективного удаления связанной влаги, а в заключительной фазе (закалка) при максимальном давлении и высокой температуре он еще уплотняется и его прочность повышается.
На проходных ленточных прессах удается гибко управлять процессом прессования, изменяя давление и температуру на разных участках. Диаграммы на рис. 4 отображают динамику рабочих параметров в процессе изготовления ДСП на установке фирмы Siempelkamp. Стружечный ковtр загружается при довольно низкой температуре плит пресса, что позволяет избежать преждевременного отверждения клея. После полной упрессовки ковра рабочая температура снова снижается и благодаря этому смягчаются условия парообразования в стружечном ковре.
При изготовлении плит MDF на аналогичной установке кривая изменения давления имеет другой вид (рис. 5). При производстве волокнистых плит упрессовка ковра в силу податливости материала происходит быстрее, поэтому на выдержку под максимальным давлением отводится меньше времени. Быстро наращивая давление, можно получить желаемый профиль плотности по толщине плиты - с уплотненными наружными слоями.
Во всех случаях прессование в проходных двухленточных прессах, в отличие от позиционных (тактовых), позволяет получать более качественную продукцию при меньших энергозатратах.
Владимир ВОЛЫНСКИЙ
drevo-inform.ru