Послепрессовая обработка древесных плит
В предлагаемой вниманию читателей публикации рассматриваются некоторые аспекты технологии послепрессовой обработки древесно-плитных материалов.
Компоненты древесных плит
Прессы для изготовления древесных плит
Технологические параметры горячего прессования плит
Входной и текущий контроль качества продукции на плитных производствах
Древесные плиты в строительстве
Эти удивительно полезные ДВП
Материалы ДПК: долговечность, прочность, качество
К операциям послепрессовой обработки относятся: форматная обрезка, кондиционирование (выдержка или охлаждение плит сразу после выхода из пресса), шлифование и сортировка. На некоторых предприятиях сюда добавляют раскрой плит на заготовки требуемых размеров.
Обязательная операция - охлаждение плит, так как их температура перед укладкой в штабеля должна быть не выше 50°C. Для плит на карбамидных смолах укладка и хранение в плотных стопах при температуре более 70°C чревато термодеструкцией отвержденной смолы и снижением прочности при растяжении поперек пласти (до 40%). Обычно применяют конвективное охлаждение в веерных установках (рис. 1).
Работа охладителя сблокирована с работой разгрузочной этажерки пресса. Одновременно в охладителе может находиться 15-18 плит (по числу этажей пресса). За отрезок времени, в течение которого охладитель совершает оборот на 180°, плиты охлаждаются до 50-70°C. После охлаждения плиты укладывают с помощью штабелеукладчика в стопы высотой до 400 мм. В процессе кондиционирования происходит медленное выравнивание влажности и температуры по всему объему плиты и релаксация внутренних напряжений.
Форматная обрезка плит может выполняться сразу после выхода из горячего пресса, после нахождения в охладителе или после хранения на буферном складе. Припуски на обработку обычно составляют 15-30 мм на сторону, а требуемая точность ±2 мм на один метр длины кромки. Форматные станки представляют собой круглопильные агрегаты, расположенные под углом 90° для опиловки последовательно длинной и короткой сторон плиты двумя пилами. Для крупноформатных и проходных прессов необходимы еще делительные пилы для задания длины продукции, пригодной для хранения и транспортировки.
Принципиально иначе выглядит технологическая схема работы участка раскроя плит для прессов непрерывного действия. Представлен пильный агрегат для продольного и поперечного пиления (рис. 2). Для опиловки кромок служат продольные пилы, настроенные на получение заданной ширины плиты, а для получения требуемой длины продукции - диагональная пила, позволяющая делать перпендикулярный рез в нужном месте без остановки непрерывной ленты материала. Отличительная особенность агрегата (рис. 2) состоит в том, что все пильные узлы продублированы. Это позволяет не останавливать пресс при смене пильных дисков. Желательно выполнять опиливание кромок после охлаждения плит. Опиленные кромки чаще всего отправляют в энергетическую установку для сжигания.
Плиты для мебельного производства подвергаются шлифованию и калиброванию для ликвидации разнотолщинности (допуск ±0,2-0,3 мм). Сегодня почти повсеместно используются широколенточные станки. На отечественных предприятиях имеются станки ДКШ-1 с шириной шлифования 1830 мм, оснащенные одним шлифовальным агрегатом, состоящим из верхней и нижней шлифовальных головок. В связи с тем, что за один проход не удается снять припуск, добиться нужной стабильности толщины и высокого качества поверхности, на предприятиях приходится устанавливать друг за другом минимум два агрегата.
Использование в качестве головного оборудования проходных ленточных прессов потребовало увеличения мощности шлифовальных станков. Появились станки, у которых число шлифовальных агрегатов доходит до десяти. Шлифование ведется при скорости подачи 50-90 м/мин. Станки часто выполняются в виде конструкции, состоящей из функциональных блоков (рис. 3): калибровальный блок предназначен для снятия материала грубой шкуркой (зернистость 36-60) и получения плиты постоянной толщины, калибровально-шлифовальный - для обработки шкуркой средней зернистости (60-120); блок финишного шлифования - для выглаживания поверхности шкуркой малой зернистости. Если для шлифования стружечных плит достаточно использовать на последней операции шкурку с зернистостью 100-120, то для шлифования MDF-плит нужна шкурка зернистостью не менее 180, а на некоторых производствах используют шкурку с зернистостью 220-240. Для устранения рисок шлифовальный барабан должен работать с осцилляцией - осевым перемещением. Скорость подачи плит не требует строгого фиксирования. Для того чтобы обеспечить максимально возможную нагрузку на первый калибровальный агрегат, скорость подачи устанавливается автоматически - по показаниям амперметра, фиксирующего силу тока, потребляемого станком. Станки тонкого шлифования, напротив, должны работать с постоянной скоростью подачи, чтобы гарантировать высокое качество поверхности.
Срок службы шлифовальной ленты может быть увеличен за счет использования щеток или сжатого воздуха для очистки ленты.
Опыт работы шлифовальных станков показал, что на операции калибрования необходимо снять 80-85% общего припуска на шлифование. Тогда для чистого шлифования можно использовать шлифовальные ленты на бумажной основе с зернистостью 120/150/180. Расстояние между калибрующим и последующим шлифовальным агрегатом должно быть не менее одного метра - для того чтобы можно было контролировать толщину плиты. Основная нагрузка ложится на первый (калибровальный) агрегат, от качества работы которого зависит качество работы финишных агрегатов, так как припуск, снимаемый последним агрегатом, составляет всего 0,02-0,03 мм. Для получения высокого качества поверхности плит рекомендуется чистовое шлифование выполнять на двух парах агрегатов. Первый чистовой агрегат должен удалить все следы шлифования от грубой шкурки, а второй - обеспечить полирование поверхности.
Для новых прессовых установок принимается 8-часовой максимальный промежуток между окончанием прессования и операцией шлифования, который необходим для полного отверждения связующего и охлаждения плит. Поверхностная температура плит может достигать 50°C. Шлифовальная лента может выдержать температуру до 80°C, при этом стойкость ленты при повышенных температурах примерно вдвое больше, чем при шлифовании полностью охлажденных плит с полностью отвердевшим клеем. Кроме того, так называемое горячее шлифование позволяет снять самый верхний - закаленный слой плиты, что способствует быстрому завершению процесса полного отверждения связующего в плитном материале.
Припуски на шлифование плит зависят главным образом от типа головного оборудования. Старые многоэтажные прессы дают припуск 2,5-3,0 мм, что вынуждает снижать скорость подачи в шлифовальных станках или устанавливать дополнительный калибровальный. Сегодня в Западной Европе старые линии все чаще переводятся на выпуск небольших объемов специальных плит - огнестойких, повышенной влагостойкости, сверхтолстых - для изготовления внутрикомнатных дверей и перегородок и т. п., а плиты для мебели выпускаются на проходных ленточных прессах.
Одноэтажные тактовые прессы вместе с современными формирующими линиями обеспечивают припуск на шлифование 0,8-1,8 мм. На большинстве предприятий с такими прессами установлены 6-головочные шлифовальные агрегаты. На заводах с несколькими прессующими линиями может работать один 8-головочный агрегат с высокой скоростью подачи.
Ленточные прессы позволяют уменьшить припуск на шлифование стружечных плит до 0,4 мм. Стало обычным делом выполнять шлифование в одной линии с проходным прессом. Здесь нужно иметь в виду следующие особенности:
● охлаждение плит способствует высокому качеству шлифования поверхности. Если плита слишком горячая, то клей может оставаться термопластичным. При шлифовании зерна шлифовальной ленты будут вырывать кусочки плиты и вместе с клеем быстро приведут ленту к износу;
● оптимальная температура поверхности плиты 50°C. При этом достигается наивысшее качество поверхности;
● припуск на шлифование не должен отклоняться от припуска, задаваемого прессом, больше чем на 0,1 мм;
● припуск на шлифование не может быть меньше 0,4 мм. В противном случае не удастся полностью снять блестящий закаленный слой плиты, сформированный при контакте со стальной лентой пресса;
● срок службы шлифовальных станков за последнее время сильно вырос. Они могут работать несколько недель без остановки при условии правильного ухода. В центральную систему контроля может быть интегрирован монитор, отражающий информацию о состоянии работы оборудования, в частности, о неисправностях. Фирмы могут поставлять дополнительно системы автоматической смазки станков и контроля за температурой всех быстроходных подшипников;
● совершенствование технологии прессования плит позволило значительно увеличить срок службы шлифовальных лент. На европейских предприятиях - производителях древесных плит - одной лентой с зернистостью 60/100 можно прошлифовать 100-250 тыс. пог. м плитных материалов.
В последние годы разработана и производится шлифовальная лента на особо прочной основе - тяжелой бумаге плотностью 350-400 г/м2. Цена шлифовальных лент на бумажной основе на 30-40% ниже, чем лент на синтетической или комбинированной основе. В условиях высокой влажности воздуха такие ленты должны проходить акклиматизацию, то есть выдерживаться в рабочем климате до равновесной влажности бумаги.
Особенностью некоторых новых шлифовальных станков является то, что шлифовальные барабаны в них устанавливаются под углом 85 и 95° к направлению подачи материала. Верхние и нижние шлифовальные головки могут располагаться точно друг против друга (симметрично) или на некотором расстоянии друг от друга (асимметрично). Последний вариант необходим для шлифования очень тонких плит (например, плит каландрового способа производства), так как это позволяет избежать прямого соприкосновения верхней и нижней шлифовальных лент в момент прохождения межторцовых разрывов между шлифуемыми плитами. Такие станки позволяют проводить тонкое шлифование только одной поверхности плиты.
Еще одна особенность шлифовальных станков - высокая температура в зоне резания. Для ее снижения используют контактные вальцы со спиральными пазами, которые создают дополнительный поток воздуха, увеличивают площадь нагреваемой поверхности и позволяют эффективно отводить тепло от нагретого металла. Для исключения поломки оборудования предназначены защитные системы с температурными датчиками, которые могут автоматически отключить станок, если температура подшипников превысит критическое значение.
Заметным явлением в технологии машиностроения стало использование при изготовлении станин тяжелых станков минерального литья (полимербетона), которое получают из кремнистого известняка с добавкой эпоксидного связующего (до 10%). Новый материал обеспечивают меньшую, чем в случае применявшихся ранее материалов, вибрацию элементов станков и более высокую их термостабильность, он не подвержен коррозии, не боится воздействия агрессивных сред, снижает уровень шума станков. По сроку службы станины из минерального литья сопоставимы с другими литыми конструкциями.
Шлифование плит обычно совмещается с операцией сортирования продукции. Сорт плиты устанавливается оператором при осмотре пластей (нижней - с помощью зеркала) и корректируется автоматическим толщиномером. Здесь же может определяться вес плиты после выхода из пресса для расчета ее плотности. Плотность также определяют и с помощью более современного - радиационного метода, а непрерывное определение распределения плотности по площади плиты - с помощью прибора фирмы GreCon. Ультразвуковой способ помогает легко обнаруживать расслоение плит.
Приведена примерная схема линии шлифования и сортировки плит (рис. 4).
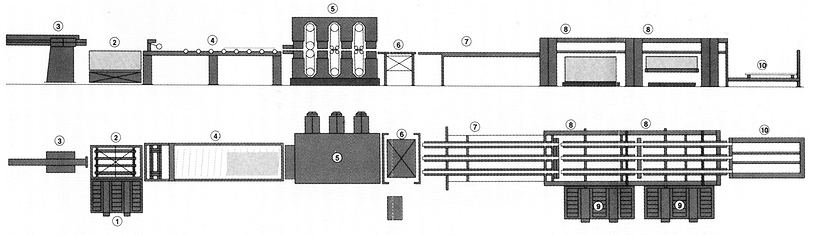
Рис. 4. Линия шлифования и сортирования плит сер. BSM II/6 («Бизон»):
1 – место приема плит, 2 – подъемный стол, 3 – загрузчик линии, 4 – рольганг, 5 – 6-головочный шлифовальный станок,
6 – место осмотра плиты с зеркалом нижнего вида, 7 – ленточный конвейер, 8 – подстопные места отсортированных плит,
9 – тележки, 10 – отбракованные плиты
Основные дефекты плит: недостаточная прочность, образование пузырей и разрывов, расслоение по внутреннему слою, покоробленность, слущивание стружки с поверхности и др.
Маркировка плиты может выполняться автоматически, например, с помощью прибора ML8 фирмы Marconi. Готовые плиты укладывают в стопы штабелеукладчиком, который формирует стопу нужной толщины. На упаковке указывают наименование предприятия, марку, группу, сорт и толщину плиты, номер стандарта. Рекомендованный объем склада готовой продукции - до месячного объема производства.
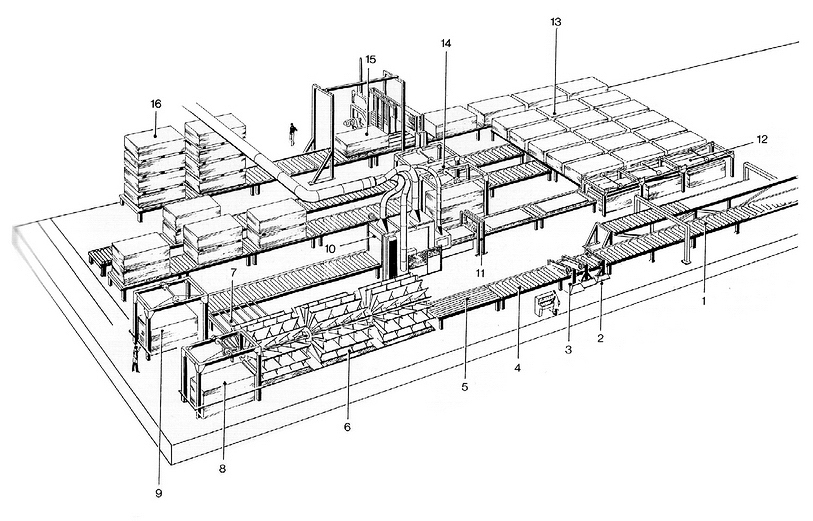
Рис. 5. Вариант организации участка послепрессовой обработки плит:
1 – выходной конвейер проходного пресса, 2 – агрегат опиливания кромок,
3 – агрегат поперечного раскроя бесконечной ленты на плиты заданной длины, 4 – выходной конвейер,
5 – ускоряющий конвейер – отделитель плит, 6 – веерные охладители, 7 – поперечный конвейер к линии шлифования,
8, 9 – буферные зоны на случай остановки шлифовального станка, 10 – шлифовальный станок,
11 – измеритель толщины плит, 12 – сортировочные карманы, 13 – склад плит на роликовых конвейерах,
14, 15 – штабелеукладчики, 16 – склад готовой продукции
Показан пример организации участка послепрессовой обработки плит, выходящих из проходного пресса (рис. 5). Сначала на двухпильном агрегате обрезаются продольные кромки плит и двумя диагональными пилами выполняется поперечное пиление на требуемую длину. Затем на ускоряющем рольганге происходит отделение плит друг от друга, что позволяет им ритмично загружаться в первый веерный охладитель. Для полного и безопасного охлаждения в цехе установлено три таких охладителя. Из последнего охладителя плиты передаются на рольганг перед шлифовальным станком. Здесь имеются буферные площадки для хранения плит в случае остановки шлифовального станка (например, для замены шлифовальной ленты). За шлифовальным станком установлен измеритель толщины плиты. На основании внешнего осмотра и замеров толщины оператор оценивает сорт плиты и направляет ее в соответствующий сортировочный карман.
Владимир ВОЛЫНСКИЙ
Поздравляем!
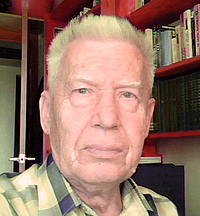
12 апреля отмечает юбилей наш постоянный автор, известный специалист в области деревообработки и просто хороший человек Владимир Волынский! Сердечно поздравляем Владимира Николаевича с днем рождения, желаем ему крепкого здоровья, успехов в работе, добрых отношений в семье и, конечно, дальнейшего плодотворного сотрудничества с нашим журналом!
Редакция
Владимир Николаевич Волынский родился 12 апреля 1938 года в г. Архангельске.
В 1955-1960 годах обучался в Архангельском лесотехническом институте (АЛТИ) по специальности «машины и механизмы лесной промышленности». В 1960-1962 годах работал мастером ремонтно-механических мастерских в леспромхозах Архангельской области. С 1963 до 1973 года трудился в ЦНИИ механической обработки древесины (ЦНИИМОД, г. Архангельск).
В 1970 году по результатам защиты диссертации в Ленинградской государственной лесотехнической академии Владимиру Николаевичу была присвоена ученая степень кандидата технических наук. С 1973 до 2009 года В. В. Волынский - старший преподаватель, доцент, профессор кафедры деревообработки АЛТИ (ныне Северного (Арктического) федерального университета).
Владимир Николаевич - автор ряда научных работ, среди которых: монография «Взаимосвязь и изменчивость физико-механических показателей древесины» (2000), учебно-справочное пособие «Технология клееных материалов» (три издания, 1998-2009), учебное пособие для вузов «Технология стружечных и волокнистых древесных плит» (2004), учебно-справочное пособие «Технология древесных плит и композитных материалов» (2009), справочник «Каталог деревообрабатывающего оборудования» (три издания, 1999-2003), «Краткий лесотехнический словарь (немецко-русский, русско-немецкий)» (2007), «Краткий лесотехнический словарь (англо-русский, русско-английский)» (2007) и др.
В последние годы главным делом Владимира Николаевича Волынского стало развитие Интернет-ресурса drevo-inform.ru, где, в частности, представлена в свободном доступе подготовленная им «Энциклопедия оборудования деревообрабатывающих производств» - систематизированный в структуре EUMABOIS справочник по деревообрабатывающему оборудованию отечественных и зарубежных фирм.