Материалы ДПК: долговечность, прочность, качество
Эти новые материалы на термопластичных связующих, из которых с успехом производят плиты, стеновые панели и другие строительные материалы, а также детали для мебели и пр., появились сравнительно недавно и известны на рынке под названием «древесно-полимерные композиты» (ДПК).
Компоненты древесных плит
Прессы для изготовления древесных плит
Технологические параметры горячего прессования плит
Послепрессовая обработка древесных плит
Входной и текущий контроль качества продукции на плитных производствах
Древесные плиты в строительстве
Эти удивительно полезные ДВП
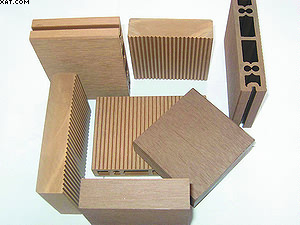
В качестве термопластичных добавок в них используются полиэтилен, полипропилен, сополимеры этилена с пропиленом или винилацетатом, полистирол и сополимеры стирола, поливинилхлориды, полиметилметакрилат и прочие полимеры, получаемые из доступного углеводородного сырья. Древесным наполнителем могут служить древесная мука (дисперсность — 0,01–1 мм), опилки (1–8 мм), молотая кора, растительные сельскохозяйственные отходы, стружка хвойных и лиственных пород (10–20 мм). Исследования показали, что для изготовления ДПК порода древесины особого значения не имеет, гораздо важнее размер и форма древесных частиц. Содержание связующего варьирует в широких пределах — от 10 до 40% массы абсолютно сухой древесины. Получаемый термопластичный материал имеет прочность при изгибе, сопоставимую с прочностью стандартных ДСтП, и при этом обладает такими достоинствами, как экологическая чистота, невысокая плотность, водо-, морозо- и биостойкость, низкая себестоимость и технологичность. Отходы плитного производства в данном случае стопроцентно пригодны для переработки в новую продукцию. Древесно-клеевую смесь можно перерабатывать как методом экструзии с получением профильных погонажных изделий, так и методом плоского прессования с получением не только плит постоянной толщины, но и профильных деталей мебели, стеновых панелей, тарных деталей и т. п. По данным мировой печати, в 2000 году на Западе разработкой и производством подобных древесно-полимерных композитных материалов занималось около 40 фирм.
В Северной Америке годовой объем производства композитов WPC (wood plastic composite) уже в 2005м достиг 700 тыс. т при ежегодном приросте более 10%, а в Западной Европе — только 40–50 тыс. т, но к концу 2010 года ожидается утроение этой цифры.
Номенклатура продукции из композитов весьма разнообразна. В нее входят, например:
- строительные элементы наружного применения — настилы, балюстрады, оконные и дверные профили, сайдинг (доска обшивки), декинг (палубная доска), штакетник, кровля, тротуары, противошумовые барьеры, опалубка для бетонных работ;
- автомобильные детали — внутренние панели, прокладки дверей и крыш, крышки на запасное колесо, короба, полы грузовиков;
- садовые конструкции — парковые скамьи, столы, емкости для мусора, оборудование спортивных и детских площадок;
- детали мебели, поддоны, тара и многое другое.
Как уже отмечалось, композит состоит из измельченной древесины, термопластичного связующего и специальных добавок. В качестве термопластов используют полиэтилен, поливинилхлорид, полистирол и другие полимеры с температурой плавления до 200 °С, в том числе в виде вторичного сырья — промышленных и бытовых отходов. В некоторых композициях используют и вещества природного происхождения — лигнин, казеин, крахмал и т. п.
Доля древесного компонента в составе композита может колебаться от 40 до 95%. Древесный наполнитель представляет собой сухую измельченную древесину, полученную, например, в молотковой дробилке или мельнице, и высушенную до влажности 3–5%.
Чем выше требуемая прочность изделия, тем больше в ней содержание полимерного связующего. Для получения изделий повышенной прочности в композит вводят химические волокна. Если к изделиям предъявляют в основном эстетические требования, то долю древесины в композитной смеси увеличивают.
Третий компонент смеси — специальные добавки (аддитивы) обычно вводятся в небольшом количестве, но могут оказывать решающее влияние на поведение древесно-полимерной массы в процессе переработки и на свойства конечного продукта. Функции добавок могут быть разными: повышение адгезии древесины и полимера; изменение цвета изделия; улучшение эксплуатационных свойств (кислото-, свето-, температуро- и биостойкости); снижение сил трения при прохождении массы через экструдер; повышение тепло и звукоизоляции.
Разработкой рецептур (многие запатентованы) занимаются специальные лаборатории. Например, для производства мебели и интерьерной отделки выпускают материалы с торговой маркой Einwood (Япония), Fasalex (Австрия), TPF (Германия).
Подготовка сырья может проводиться разными способами:
- Предварительное изготовление на собственном или специализированном предприятии полуфабриката в виде гранул или порошка (компаунда), содержащего полимер, наполнитель и добавки.
- Загрузка всех нужных компонентов в экструдер с последующим перемешиванием уже внутри машины.
Материал в виде гранул наиболее удобен в работе. Он имеет постоянную насыпную массу, не слеживается, не образует пробок при продвижении в канале. Гранулы можно получать с помощью экструдеров или специальных машин — грануляторов. На рынке этот полуфабрикат предлагают специализированные компании и крупные производители ДПК.
В агрегате германской фирмы Pallmann для получения гранулированного материала из смеси древесной муки и термопластичного порошка компоненты подаются в машину через гравиметрическую дозирующую установку. После смешивания материал под действием фрикционного тепла и механического давления кратковременно пластифицируется и выдавливается через отверстия в специальной матрице. Пар, образующийся в процессе подсушивания древесины, удаляется с помощью вакуума. Экструдированный материал пневматически подается в гранулятор, где получают гранулы постоянного размера, которые высыпаются в промежуточный бункер. Фирма выпускает установки производительностью от 200 до 2000 кг гранул в час.
Головным оборудованием в технологии ДПК является экструзионный (от экструзия — выдавливание) пресс. Отличительная особенность прессования заключается в том, что нагреванию подвергается формуемый материал, в то время как пресс остается холодным, лишь его загрузочная часть может быть слегка нагрета.
В индустрии полимеров экструзия применяется с 30х годов прошлого века. Наиболее распространенным оборудованием для выполнения этой операции является шнековый экструдер. В загрузочную камеру экструдера загружают исходный материал в виде порошка или гранул. Вращающийся шнек захватывает и сдавливает сыпучую массу, продвигает ее вдоль цилиндрического корпуса в зону нагрева, при этом выделяется дополнительное тепло за счет внутреннего трения частиц друг о друга и с корпусом шнека. Полимерная масса плавится и перемешивается до однородного (гомогенного) состояния. На выходе из экструдера имеется профильное отверстие нужной формы или узкая щель (для получения листов и пленок), через которую смесь выдавливается. Полученный материал затем охлаждается и отверждается.
Экструдеры могут быть одно и двухшнековые. Последние отличаются более сложной конструкцией и обеспечивают более точное дозирование компонентов, адаптацию к различным видам сырья, лучшее перемешивание материала и более высокое качество конечного продукта, чем одношнековые машины. Кроме этого, шнеки могут вращаться как в одном направлении, так и в противоположных, быть цилиндрической или конической формы, иметь конструкцию с взаимным зацеплением или без него.
Процесс получения экструдированного изделия имеет массу тонкостей. Если на выходе из экструдера температура полимерного расплава ниже требуемой по технологическим условиям, он твердеет и выдавливается с образованием раковин и других дефектов. Если температура смеси выше оптимальной, то смесь имеет пониженную вязкость и может просто выливаться через профильное отверстие (фильеру), не приобретая нужной формы. Слишком высокая скорость движения расплава увеличивает силу трения гранул и может привести к неконтролируемому повышению температуры смеси. При слишком быстром охлаждении полученного изделия в нем остаются внутренние напряжения, которые впоследствии приводят к короблению материала и потере прочности.
В отличие от традиционно используемых наполнителей пластмасс (двуокиси кремния, мела, каолина, талька, стеклянных и химических волокон), древесный наполнитель обладает меньшей плотностью и более высокой изменчивостью свойств. Одно из главных требований к древесине — минимальная влажность (не более 2%), потому что пузырьки пара приводят к появлению внутренних и внешних дефектов изделия. Древесина является гигроскопичным материалом, и это диктует одно обязательное условие: высушенный наполнитель должен быть сразу подан в экструдер либо герметично упакован, то есть защищен от влаги, содержащейся в воздухе. Впрочем, современные машины имеют отвод пара, поэтому повышенная влажность древесины для них не является препятствием.
Древесный наполнитель чувствителен к высокой температуре. Из-за термической деструкции происходит потемнение материала и на поверхности изделия иногда появляются бурые пятна. Недостаточно высокой может быть адгезия древесины с термопластами. Силы сцепления разнородных материалов увеличивают за счет дополнительного измельчения древесного наполнителя. При перемещении по каналу экструдера древесные частицы проявляют абразивный эффект — вызывают повышенный по сравнению с другими наполнителями износ рабочих поверхностей экструдера.
За последние годы найдены технические решения, которые позволили преодолеть многие ограничения в использовании древесно-полимерных композитов. В экструдерах предусмотрена специальная конструкция узла загрузки, некоторые машины используют дополнительную сушку древесной массы до смешивания ее с полимером. Оптимальный режим экструдирования достигается путем подбора длины и конфигурации шнеков. Для регулирования скорости продвижения материала шаг резьбы шнека может меняться. Внутренние поверхности корпуса имеют повышенную износостойкость.
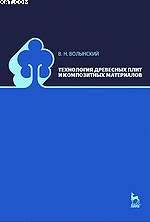
Более подробно о техноло-
гии и оборудовании для
производства материалов
из измельченной древесины
можно узнать в книге
автора: Волынский В. Н.
«Технология древесных
плит и композитных
материалов: учебно-
справочное пособие»
СПб.: лань, 2010. 336 с.,
а также на сайте
www.drevo-inform.ru
В Северной Америке и Европе экструдеры изготавливают десятки предприятий. Наиболее широкое применение нашли двухшнековые конические экструдеры со специальными формующими головками, которые не только обеспечивают сложный профиль изделия, но и определенным образом ориентируют частицы древесины, что повышает прочность продукции.
В производстве ДПК-изделий может применяться метод соэкструзии, при котором выходы двух агрегатов, перерабатывающих различные смеси, объединяют при помощи специальной головки. Таким образом получают, например, провода, покрытые пластмассовой изоляцией, и профильные изделия, покрытые слоем водостойкого полимера. Аналогичным образом можно наносить древесно-полимерную массу на металлические стержни или проволоку, то есть внедрять в изделие армирующие элементы.
Экструдер CWE 5002 финской фирмы Conenor Ltd. имеет два конических ротора диаметром 500 мм с загрузочными патронами диаметром 60 мм. Предусмотрено удаление паров воды из каждого ротора. Начальная влажность материала — до 50%, максимальный размер частиц — до 15 мм, при этом материал дополнительно измельчается в самом экструдере. Производительность — до 400 кг/ч.
Машина позволяет производить методом прямой экструзии без предварительного смешивания и изготовления гранул профили и доски, содержащие до 80% древесных частиц. Возможно и изготовление двухслойных изделий.
После формования требуется дополнительная обработка изделия — калибрование, то есть придание ему точных размеров, охлаждение, нарезка и упаковка. При изготовлении досок настила (деков) на предприятиях США перед окончательным охлаждением изделия обрабатывают специальными металлическими щетками для придания им шероховатости и имитации текстуры древесины.
Владимир ВОЛЫНСКИЙ