Древесиноемкость продукции деревообрабатывающих производств
Деревообработка - одна из финишных стадий лесопромышленного комплекса. Деревообрабатывающая промышленность потребляет не менее половины заготавливаемой деловой древесины для изготовления строительных деталей и изделий. Эффективность деревообработки зависит от количества использованного сырья на единицу конечной продукции, то есть от ее древесиноемкости.
На степень использования любого природного сырья (нефти, древесины, руд и др.) основное влияние оказывают применяемые технологии обработки или переработки.
Обработка и переработка древесного сырья
Обработка - процесс воздействия, в основном механического, на исходное сырье (его полуфабрикаты) без изменения структуры сырья в конечном продукте. Обработкой является, например, огранка алмазов, изготовление изделий из мрамора и гранита, производство деревянных конструкций, изделий и деталей.
Для получения строительной продукции применяют многостадийные технологии. Исходное древесное сырье в виде хлыстов раскряжевывают на бревна определенного размера и качества; бревна как полуфабрикат распиливают на пиломатериалы, которые также в виде полуфабриката обрабатывают резанием для получения следующего полуфабриката - заготовок; детали как конечный продукт или элемент изделий изготавливают фрезерованием, шлифованием, отделкой.
На всех стадиях обработки древесного сырья образуются отходы и потери древесины. Причинами являются как природные факторы (несоответствие формы и размеров сырья или его полуфабриката конечным параметрам продукции, например несоответствие формы бревен сечениям пиломатериалов и заготовок), так и технологические факторы, в частности режимы резания и качество применяемых режущих инструментов. В результате получение деталей и изделий, например, для деревянного домостроения, характеризуется большим расходом сырья, то есть высокой древесиноемкостью этой конечной продукции (табл. 1), которая достигает 80-85% объема исходного древесного сырья, что не может не сказываться на экономике этого сектора деревообработки.
Сокращение расхода древесного сырья на каждой стадии его обработки, то есть оптимизация древесиноемкости конечной продукции, обеспечивается при рациональном использовании сырья и полной переработке неизбежно образующихся отходов как вторичного древесного сырья (ВДС). При этих условиях использование исходного древесного сырья могло бы составлять до 90% объема природного ресурса, то есть объема древесины в растущем дереве.
Переработка - процесс воздействия (температурой, давлением, химическими и другими веществами и способами) на структуру древесного сырья с целью получения продуктов с другой структурой и другими свойствами. Такие процессы позволяют получить древесно-плитные материалы, целлюлозу, бумагу, картон, продукты гидролиза древесины и др. Аналогичные процессы характерны для нефтепереработки и нефтехимии, для металлургии и подобных производств.
Для реального рационального использования древесного сырья необходимо объединение всех стадий его обработки и переработки в одной лесопромышленной структуре, что частично реализовано в Сыктывкарском и Братском лесопромышленных комплексах. В настоящее время отечественное лесопользование представлено, по сути, двумя промышленными структурами с многостадийными технологиями: деревообрабатывающими предприятиями, стремящимися объединить (в одну структуру, компанию, холдинг и т. п.) стадии лесозаготовок, лесопиления и деревообработки с частичной переработкой древесных отходов, и деревоперерабатывающими предприятиями (в основном целлюлозно-бумажными комбинатами), практикующими самообеспечение древесным сырьем и частичную его обработку - с получением пилопродукции, фанеры и другой продукции.
По древесиноемкости конечной продукции деревообработка существенно уступает деревопереработке, и рациональное использование древесного сырья наиболее актуально именно для деревообрабатывающих предприятий, особенно для предприятий с незамкнутым циклом, то есть использующих в качестве исходного сырья пиловочник или пиломатериалы.
Рациональное использование древесного сырья
Организация деревообрабатывающего производства должна базироваться на решении трех основных технических вопросов, определяющих рациональное и экономически эффективное использование древесного сырья: его виде, технологиях обработки, минимизирующих объемы отходов; способах утилизации (переработки) отходов как вторичного древесного сырья.
Вид сырья определяется на основе требований к конечной продукции деревообработки. Приоритет имеет порода древесины; в строительстве, в частности в деревянном домостроении, традиционно используются конструкции, изделия и детали из хвойной древесины; лиственная древесина может использоваться в ограниченных объемах и при определенных условиях.1, 2
Основное влияние на расход сырья, то есть на древесиноемкость конечной продукции, оказывает форма пиломатериалов (обрезанные или необрезанные), размеры пиловочника (его диаметр) и качество, оцениваемое по нормам ограничения пороков древесины.
пиловочника

Таблица 3. Оптимальный выход заготовок из хвойных необрезных
пиломатериалов
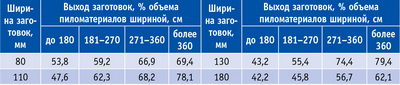
Таблица 4. Выход заготовок строительного назначения из хвойных
необрезных пиломатериалов разной ширины и сортности
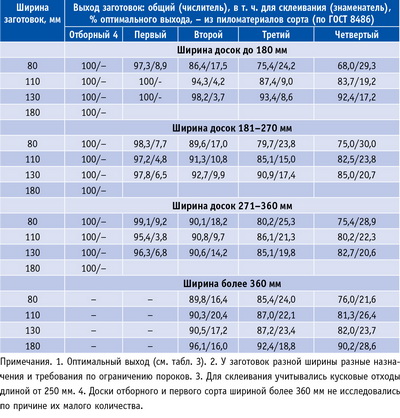
О зависимости выхода заготовок от диаметра хвойного пиловочника можно судить по данным табл. 2, полученным автором в результате исследований. За оптимальный выход принят выход заготовок, длина которых равна длине раскраиваемых пиломатериалов, а толщина заготовок соответствует толщине этих досок. Данные табл. 2 показывают, что увеличение диаметра пиловочника на одну размерную градацию (2 см) повышает выход заготовок на 1-1,5%.
Данные о зависимости выхода заготовок от ширины необрезных пиломатериалов представлены в табл. 3. Также отмечается повышение выхода заготовок при увеличении ширины раскраиваемых пиломатериалов. Эти зависимости целесообразно учитывать при разработке программного обеспечения для компьютерных систем управления раскроем бревен и досок; подобными системами оснащено современное оборудование для раскроя сырья.
У основной массы (не менее 80%) хвойного сырья имеются пороки древесины, в той или иной мере ограничиваемые в изготовляемых деревянных конструкциях или деталях и негативно влияющие на выход заготовок. О влиянии качества (сортности) пиломатериалов на выход заготовок можно судить по данным табл. 4. Следует отметить, что примерное равенство оптимального и фактического выхода заготовок из пиломатериалов отборного и первого сорта привлекательно технологически как исключающее кусковые отходы, но может быть негативным в экономическом плане: стоимость пиломатериалов высших сортов выше пиломатериалов 2-4 сортов и заметнее в себестоимости конечной продукции. Поэтому необходимы детальные технико-экономические расчеты, особенно при использовании пиломатериалов, приобретаемых с учетом их сортового состава.
Когда в качестве исходного сырья используется пиловочник, его сортность может оцениваться по нормам СТО НТО ДП-2-12 «Бревна пиловочные хвойных пород. Технические условия». Сорта пиловочника по этому стандарту (например, по размерам сучков на бревнах) связаны с сортами получаемых пиломатериалов и выходом заготовок для деревянного домостроения3.
Вид сырья, соответствующего по породе древесины, его размерам и качеству параметрам требуемой продукции деревообработки, может быть рационально использован только при тщательной подготовке и соблюдении технологических расчетов и режимов с применением высокопроизводительного и ресурсосберегающего деревообрабатывающего оборудования и качественных режущих инструментов.
Технологии деревообработки характеризуются совокупностью операций по воздействию на исходное сырье и получаемые из него полуфабрикаты с целью изготовления требуемой продукции (деталей, изделий, конструкций) из цельной древесины, обоснованных расчетами и последовательностью выполнения. Критерием эффективности конкретной технологии является прежде всего степень рационального использования исходного древесного сырья, то есть древесиноемкость единицы конечной продукции.
Совокупность последовательных операций составляет технологический процесс изготовления конкретной продукции требуемого качества. Технологический процесс начинается с приемки и хранения исходного сырья и заканчивается реализацией готовой продукции (передачей ее заказчику или покупателю). Технологический процесс - основная часть производственного процесса, включающего также организационные и технические меры и средства обеспечения технологии (здания и сооружения, транспорт и оборудование, инфраструктуру предприятия, персонал и т. д.).
Общие положения и рекомендации по организации деревообрабатывающего производства (на примере деревянного домостроения) по гибким технологиям, по конструкторскому и технологическому обеспечению изложены автором в ряде публикаций (см. «ЛПИ» № 4-6, 2013 год, и № 2-3, 2014 год).
Каждая технологическая операция должна быть обоснована расчетами, нормативными требованиями и регламентирована технологическим режимом - внутренним нормативным документом предприятия. Режим разрабатывается и проверяется на практике технологом, утверждается руководителем предприятия и является основой должностной инструкции (положения) для исполнителей (операторов, станочников, мастеров).
Самый большой объем отходов древесины образуется на операциях раскроя исходного сырья (бревен и досок). Поэтому режим раскроя должен быть рациональным, то есть обеспечивающим максимальный выход полуфабриката для последующей обработки при минимальном объеме отходов.
При раскрое бревен необходимо учитывать:
- требуемую толщину пиломатериалов, определяемую спецификацией получаемых из них заготовок;
- параметры требуемых пиломатериалов - в первую очередь их толщину, вид их обработки (обрезные, необрезные, полуобрезные);
- наличие, размеры и размещение пороков на поверхности бревен;
- нормативные допуски (отклонения) пиломатериалов по толщине;
- допускаемую шероховатость пропиленных сторон досок.
На этой основе определяются оптимальный тип оборудования и вид режущих инструментов и разрабатываются планы раскроя пиловочника. Особого внимания заслуживает поле допуска по толщине пиломатериалов: ГОСТ 24454 «Пиломатериалы хвойных пород. Размеры» устанавливает предельные отклонения (допуски) по толщине пиломатериалов от ±1 мм (толщина досок - до 32 мм), ± 2 мм (толщина от 40 до 100 мм), до ± 3 мм (толщина - более 100 мм). Современное раскройное оборудование позволяет вырабатывать пиломатериалы с минусовыми отклонениями по толщине, что может снижать расход сырья на 3-5%. Применение ленточных пил (вместо дисковых и рамных) на соответствующем оборудовании обеспечивает не только сокращение объемов опилок, но и повышение чистоты (шероховатости) поверхности досок: с 1,25 мм для пиломатериалов отборного - третьего сортов и 1,6 мм для пиломатериалов четвертого сорта до 0,5-0,6 мм, то есть почти на 1 мм уменьшается толщина пиломатериалов. В итоге на этапе производства пиломатериалов сокращение расхода древесного сырья может составить почти 10%. Такая возможность должна учитываться при разработке режимов раскроя пиловочника.
Выход пиломатериалов составляет в среднем 55-60% (при производстве обрезных досок) и 65-70% от объема раскраиваемых бревен при получении необрезных досок. Следовательно, в процессе лесопиления образуется от 30 до 45% отходов древесины, и выбор режимов раскроя бревен, эффективного режущего инструмента и соответствующего лесопильного оборудования имеют определяющее значение для снижения древесиноемкости конечной продукции деревообработки. Планы раскроя должны также учитывать сечение требуемых пиломатериалов (доски, бруса или бруска), это имеет значение для расхода сырья.
На стадии раскроя пиломатериалов необходимо учитывать:
- размеры требуемых заготовок и нормы ограничения пороков древесины в них;
- оптимальные схемы (способы) раскроя пиломатериалов, обеспечивающие максимально возможный выход заготовок;
- спецификацию заготовок - основных (наиболее длинных) и попутных (меньшей длины), и необходимую их комплектность (соотношение числа основных и попутных заготовок);
- возможность последующего использования (для склеивания по длине) кусковых отходов, соответствующих требуемым заготовкам по сечению, но не соответствующих по длине;
- режущий инструмент (обычно - ленточные пилы), использование которого обеспечивает минимальный объем опилок.
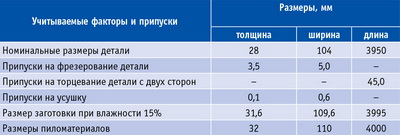
Размеры заготовок должны соответствовать размерам необходимых деталей с учетом припусков на обработку заготовок. Величина припусков зависит от требований к качеству обработки поверхностей деталей, то есть от нормативной шероховатости и влажности древесины. Порядок, условия определения и нормативные величины припусков установлены ГОСТ 7307 «Детали из древесины и древесных материалов. Припуски на механическую обработку». Обычно объем древесины в припусках составляет около 3% объема заготовки. Условный пример порядка определения размеров пиломатериалов для изготовления досок пола (с частичным фрезерованием нелицевой стороны доски) приведен в табл. 5.
Схемы раскроя пиломатериалов определяют на основе оптимального соответствия их вида и качества (сортности) наибольшему выходу требуемых заготовок. Групповой (так называемый батарейный) раскрой применим только для обрезных пиломатериалов, поперечное сечение и сортность которых совпадают с аналогичными параметрами требуемых заготовок. Эта схема осуществляется путем раскроя пачки досок на торцовочных станках и отличается высокой производительностью и довольно небольшим объемом отходов (опилок). По подобной схеме могут раскраиваться высокосортные обрезные доски с получением заготовок обшивок (погонажа), досок пола и других, а также изготавливаться заготовки-детали, не требующие последующей обработки и совпадающие по сечению, длине и нормам ограничения пороков с раскраиваемыми пиломатериалами, например доски чернового пола и другие заготовки-детали вспомогательного назначения.
Оптимальное использование объема сырья обеспечивается при поперечно-продольном раскрое каждой доски, то есть при схеме индивидуального раскроя. Наибольший выход заготовок получается при раскрое необрезных досок с обязательным получением короткомерных кусковых отходов для последующего изготовления из них основных заготовок (склеиванием по длине) или других деталей и изделий.
Заготовки крупного сечения (от 100 х 100 мм) для изготовления брусовых деталей или конструкций могут вырабатываться как на стадии раскроя бревен, так и при склеивании заготовок из досок (ламелей). Этот способ трудоемкий, но у него есть ряд достоинств: клееные брусья характеризуются высокой прочностью, отличаются долговременной формоустойчивостью, стабильной влажностью древесины; при их изготовлении для внутренних слоев могут использоваться пиломатериалы пониженной сортности и склеенные по длине ламели.
На каждом конкретном деревообрабатывающем производстве схемы раскроя пиломатериалов должны быть обеспечены не только технологическим, но и технико-экономическим обоснованием, учитывающим как древесиноемкость конечной продукции, то есть ее себестоимость, так и рыночную ценовую ситуацию, то есть возможную реализацию продукции. Эти аспекты анализируются на этапе организации производства и при его модернизации, а наиболее эффективно реализуются на основе гибких технологических процессов. Все технологические операции деревообработки должны быть регламентированы утвержденными руководителем предприятия режимами.
В настоящей статье рассмотрены технологические операции, имеющие наибольшую значимость для определения древесиноемкости конечной продукции. Другие операции, например сушка пиломатериалов, защитная обработка изделий и конструкций, выбор и подготовка режущих инструментов, несущественно влияют на древесиноемкость продукции (за исключением случаев некачественного их выполнения, приводящего к техническому браку и повышению расхода древесины), но важны для обеспечения требуемого качества конечной продукции.
Необходимо подчеркнуть важность обоснования не только технологических режимов, но и системного контроля их соблюдения, который должен регламентироваться должностными положениями и инструкциями персонала предприятия и быть основным элементом системы качества предприятия.
Использование древесного отходов
Основной объем отходов образуется на стадии раскроя бревен (до 40% объема пиловочника) и пиломатериалов (около 30% их объема); при получении деталей из заготовок с учетом возможной некондиции (отбраковки) отходы составляют 5-10% объема заготовок. В результате объем конечной продукции деревообработки (деталей, изделий, конструкций) не превышает 20-30% объема исходного сырья, то есть пиловочника, и 10-15% объема природного ресурса (растущего дерева). В деревянном домостроении (при создании дома с бревенчатыми и брусчатыми стенами) выход будет в 1,5-2 раза больше, но сути колоссального образования отходов в деревообработке это не меняет и актуальности проблемы древесиноемкости не снижает.
Почти половину объема отходов при раскрое бревен и досок составляют опилки, исключить их образование на этих стадиях - цель исследований и разработки методов безопилочного резания древесины в отечественной и мировой науке, но решения еще не найдены. Поэтому пока в мировом лесопромышленном комплексе активно создаются и применяются разные технологии обработки исходного сырья и переработки отходов деревообработки.
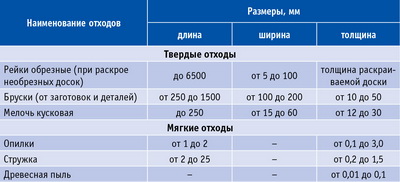
Таблица 7. Объемные параметры ВДС
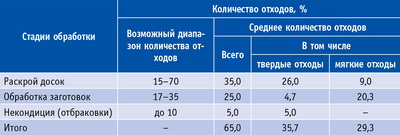
Таблица 8. Коэффициенты перевода насыпной массы мягких
отходов в плотные кубометры
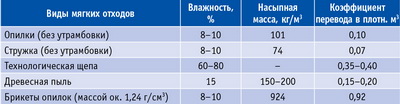
Общие размерные характеристики вторичного древесного сырья представлены в табл. 6, а их объемные параметры при раскрое пиломатериалов и обработке заготовок - в табл. 7. Влажность вторичного древесного сырья имеет большое значение для способов их использования и учета. Учитывают отходы в насыпных (рыхлых) или в плотных кубометрах. Существуют коэффициенты перевода насыпных кубометров в плотные (табл. 8) с учетом влажности вторичного древесного сырья: сухое (до 15% влажности древесины), полусухое (от 15 до 30%) и мокрое (более 30%). При раскрое высушенных необрезных пиломатериалов получают наибольший объем сухих отходов, которые могут быть использованы для дальнейшей обработки или переработки. Твердые (кусковые) отходы составляют до 60% объема вторичного древесного сырья.
Основные направления использования вторичного древесного сырья: обработка твердых отходов и переработка мягких отходов и остатков (некондиции) твердых отходов. Направления использования вторичного древесного сырья определяются на стадии организации или модернизации деревообрабатывающего производства и должны учитывать:
- возможные объемы вторичного древесного сырья и их структуру (твердые и мягкие; сухие и влажные);
- необходимые технические средства для использования вторичного древесного сырья по каждому направлению;
- возможность повышения выхода конечной продукции при обработке твердых отходов (способом склеивания) или снижения себестоимости конечной продукции при изготовлении попутной продукции из отходов, прежде всего твердых;
- потребность производства в тепловой энергии, необходимой для сушки пиломатериалов и отопления зданий предприятия;
- экономическая доступность профильных предприятий - потребителей вторичного древесного сырья, например ЦБК, ТЭЦ и других, для поставки отходов (технологической щепы и т. п.).
Для снижения древесиноемкости продукции деревообработки в настоящее время рекомендуется при наличии на предприятии участка изготовления клееных деталей и конструкций использовать сухие твердые отходы для изготовления клееных деталей, что позволяет сократить расход исходного древесного сырья на единицу конечной продукции на 5-10%. Попутной продукцией при этом варианте использования твердых отходов могут быть мебельные щиты, изделия хозяйственно-бытового назначения. Из 1 м3 твердых отходов можно получить более 0,5 м3 конечной клееной продукции.
Менее предпочтительным, но широко применяемым сейчас вариантом использования вторичного древесного сырья является сжигание всех получаемых отходов древесины для получения тепловой энергии. Во многих случаях, особенно при дефиците или экономической невыгодности использования покупной энергии, этот вариант считается универсальным: сжигание отходов в топке котла решает все проблемы с ними. На ряде предприятий избыток тепловой энергии, получаемой при сжигании вторичного древесного сырья, реализуется муниципальным тепловым сетям. Расчеты и практика показывают, что для сушки 1 м3 пиломатериалов достаточно тепловой энергии, получаемой при сжигании 1 м3 отходов.
Любые варианты использования вторичного древесного сырья требуют тщательных экономических обоснований, так как себестоимость продукции деревообработки состоит из ряда издержек, хотя основной составляющей все-таки является стоимость исходного сырья. Поэтому эффективность деревообработки обеспечивается оптимальным, то есть рациональным, использованием исходного древесного сырья за счет снижения его расхода на единицу конечной продукции и комплексным использованием всего объема исходного сырья, то есть обработкой и переработкой получаемого вторичного древесного сырья, что в итоге определяет себестоимость продукции деревообработки и конкурентоустойчивость деревообрабатывающих предприятий. Оценки нынешнего уровня использования древесного сырья позволяют утверждать, что технически возможное и технологически реализуемое снижение древесиноемкости продукции деревообработки, в частности деревянного домостроения, и полное использование получаемых отходов древесины повышает эффективность производства минимум на 10% и тем самым повышает конкурентоспособность деревянного домостроения на рынке.
Следует также учитывать кору пиловочника как своеобразный вид вторичного древесного сырья. У хвойного пиловочника объем коры составляет: у кедра - 6-10% и 20-25% - у лиственницы. В объем пиловочника кора не включается.
В процессе заготовки и доставки пиловочника часть коры теряется в результате обдира, который считается дефектом (пороком) круглых пиломатериалов; обдир коры открывает древесину для появления поверхностных трещин и биологических повреждений, но в стандартах на круглые лесоматериалы (пиловочник, балансы, фанкряж и др.) обдир коры не нормируется. В середине прошлого века импортеры отечественной древесины стали предъявлять требования по существенному ограничению обдира коры. Выяснилось, что кору они перерабатывают в разнообразную продукцию (плиты, удобрения и т. п.) и получают дополнительные доходы за счет внебалансового (неучитываемого) объема сырья. Это обстоятельство послужило одной из причин внедрения окорки пиловочника на отечественных лесопильных предприятиях и импульсом для научных разработок по эффективной переработке коры не только на композитные материалы типа королита, но и с целью получения химических продуктов.
Наиболее массовым способом использования коры на деревообрабатывающем производстве в настоящее время является включение ее после подсушки в древесные отходы, которые используются в качестве топлива для получения тепловой энергии. Другой, более наукоемкий способ использования коры на основе новых технологий ее переработки для получения ценной продукции может привести к исключению коры из баланса топливных отходов. Но даже сегодняшнее использование ее в качестве топлива позволяет существенно снижать издержки деревообработки и сокращать объемы отвалов гниющего сырья.
У современной деревообрабатывающей отрасли есть существенные резервы повышения эффективности производства и укрепления конкурентоустойчивости продукции как на основе снижения ее древесиноемкости, так и за счет наиболее полного использования древесных отходов.
Виктор КИСЛЫЙ, канд. техн. наук, директор фирмы «МП "ДОМ"»