«Эггер Древпродукт Гагарин»: новый старт!
Родина первого космонавта как перспективный промышленный центр
Будь у каждого деревообрабатывающего предприятия нашей страны собственный основополагающий девиз, гагаринскому заводу «Эггер Древпродукт» подошел бы такой: «Никогда не останавливаться на достигнутом!» Сколько ни приезжали журналисты «ЛесПромИнформа» на завод ГК Egger в Смоленской области, всякий раз он выглядел иначе, прирастал новыми цехами, участками, оборудованием. Не стал исключением и мой весенний визит на производственную площадку.
Впрочем, похоже, за переменами с трудом поспевает даже здешнее руководство...
«Мы накануне пуска нового завода, дел невпроворот! - с воодушевлением рассказывает коммерческий директор ООО «Эггер Древпродукт Гагарин» Евгений Лыюров. - На входе в заводоуправление мы традиционно показываем гостям большеформатное фото завода, сделанное с высоты птичьего полета, так его хоть каждую неделю меняй, настолько быстро этот вид становится неактуальным: казалось бы, еще вчера на картинке сваи виднелись, а теперь там цех плит MDF выстроен, начинаем пусконаладку, а рядом уже готовится площадка для возведения корпуса нового склада готовой продукции».
Несмотря на занятость, Евгений Лыюров нашел время и для детальной экскурсии по производству, и для неформального общения за чашкой кофе. Предлагаю и вам, читатель, совершить заочную экскурсию по заводу вместе с нами. Предоставим слово г-ну Лыюрову.
От биржи сырья до готовой плиты
«Самые первые строения появились здесь к 2008 году, когда предприятие называлось еще Гагаринским фанерным заводом, который был основан российскими бизнесменами, - рассказывает Евгений. - В команде, которая прибыла в г. Гагарин из Республики Коми развивать этот проект, был тогда и я.
Изначально планировалось ввести в эксплуатацию завод по производству ДСтП, а через год-два начать и производство фанеры. Но планы поменялись, и прежде всего потому, что местное сырье не позволяет выпускать фанеру высокого качества. Местность болотистая, леса в основном лиственные, с преобладанием осины. В итоге завод выставили на продажу, было несколько желающих его приобрести, и наконец после своеобразного тендера к 1 июля 2011 года он перешел во владение компании Egger и получил название ООО "Эггер Древпродукт Гагарин".
Масштабное строительство на площадке началось со склада готовой продукции, за ним последовало возведение корпусов для линии ламинирования, участка пропитки, склада бумаги. Вторая очередь завода - так называемый проект Sofia, основным этапом которого является установка ультрасовременного пресса для производства плит MDF. В июне 2015 года введена в эксплуатацию линия по производству напольных покрытий, а уже с августа начались регулярные продажи продукции. Сейчас наращиваем объемы производства, разнообразим коллекции, очень много новых наработок мы переводим из Западной Европы в Россию.
Подвоз сырья на завод и отгрузка продукции осуществляются автомобильным транспортом, скоро появится и своя железнодорожная ветка, уже подготовлена просека. Планировалось ее построить еще в 2008 году, но, введя в эксплуатацию завод, мы поняли, что срочности в строительстве железной дороги нет: автотранспорт вполне справляется с обеспечением текущего объема выпуска. Так что железную дорогу будем использовать больше для доставки сырья, чем для отправки готовой продукции. Расчет показывает, что на расстояниях до 4 тыс. км доставка машинами рентабельнее, чем по железной дороге.
На бирже сырья поддерживается минимум трехмесячный запас сырья (сейчас на площадке не менее 100 тыс. м3 древесины). Такова политика, стратегия компании. Причем биржу заполняем в том числе и с учетом нужд строящегося второго завода.
Сырье доставляется с участков, расположенных не дальше 200 км от завода (Московская, Смоленская обл.). Сейчас в Московской области массово идут санитарные рубки, которые не проводились в течение 50 лет, сырье, заготавливаемое там, хорошее подспорье для нас. Ведь не случайно предприятия, подобные нашему, называют заводами-санитарами: мы используем техсырье, которое даже бумагоделательная промышленность не берет, то есть, по сути, любую древесину (на предприятиях Egger в Германии и вовсе к первичному сырью (щепе) добавляется вторичное - переработанная старая мебель). Производство фактически безотходное, все идет в дело; даже дефектные плиты отправляются в рубилку и снова поступают в работу. "Древесина - слишком ценный материал, чтобы его выбрасывать", - так сказал основатель компании Фритц Эггер. И мы стараемся следовать его завету. Рубительная машина, которой мы сейчас пользуемся, стоит на площадке с момента создания завода, вторая, новая, устанавливается сейчас по соседству. Надо сказать, что при организации в 2008 году фанерного завода его учредители поставили задачу создать предприятие европейского уровня. Не экономили ни на основном, ни на вспомогательном оборудовании, оснащали производство по последнему слову техники, покупали только лучшее. Одним из учредителей был космонавт Алексей Леонов, который хотел обеспечить развитие родине первого человека, полетевшего в космос».
Комплекс подготовки щепы частично расположен под крышей, но самые внушительные его агрегаты - на открытой площадке. Помимо фильтров от немецкой компании Scheuch, здесь заставляют в изумлении задирать голову сушильный барабан и огромный вентилятор...
«Сырая стружка из бункера попадает в сушилку, - продолжает поход по технологической цепочке Евгений Лыюров. - Древесина приходит разной влажности и, по оценкам наших специалистов, иногда мы выпариваем до 20 т воды в час! Сушка выполняется с помощью горячего воздуха, он разогревается в результате сжигания смеси древесной пыли (до 80%) и газа и подается вентилятором, высота которого больше, чем два человеческих роста!
Высушенная стружка направляется в бункер сухой стружки, за которым установлена специальная мельница, где производится древесная пыль. Также древесная пыль поступает и от шлифмашины, обрабатывающей поверхность готовых плит. Далее масса высушенной стружки проходит осмоление (из пульверизатора) и поступает в форм-машину (комплект оборудования этого и следующих участков, включая пресс, изготовлен компанией Dieffenbacher), где перемешивается, и получается масса, которая из форм-машины насыпается на ленту пресса в виде ковра и прессуется. Из пресса выходит так называемая мастер-плита, которую потом режут на части необходимого формата».
Пульт управления и контроль качества
Управление процессом производства осуществляется с единого пульта. Оборудование работает в автоматическом режиме, но за любым автоматом надо присматривать. Операторы следят каждый за своим участком ответственности. Система видеонаблюдения позволяет вывести на экран и укрупнить изображение любого участка, посмотреть, что там происходит. Производство отлажено до мелочей - рецептура, последовательность действий задаются программой и неукоснительно соблюдаются.
- Существующая заводская лаборатория обеспечивает нужды текущего производства, - продолжая экскурсию, Евгений Лыюров открывает дверь в помещение, полное приборов и химической посуды. - Мы делаем здесь все основные анализы: определяем уровень эмиссии формальдегида, проводим тесты на пористость и истирание, гидротермические исследования, аналогично заводам нашей группы по всему миру - как положенные по законам и стандартам исследования, так и специальные, которые выполняются по отдельным запросам и в особых случаях.
- Как часто делаются анализы?
- Пробы плиты с производства берутся регулярно, дважды в день, отбираются образцы из каждой партии, в рамках каждого заказа от одного до нескольких раз, в зависимости от объема (совсем небольшие заказы мы не выполняем; есть норма минимальной партии, выпуск которой для нас рентабелен, удобен для производственников и ритмичной работы оборудования). На новом заводе будет единая большая лаборатория для обслуживания всего производства.
На каждой упаковке нашей продукции обозначены параметры ее содержимого, а также номер партии, дата и время производства, ответственное лицо. Кроме того, стоит маркировка ГОСТ - шлифованную плиту-основу мы делаем по госстандарту; любой наш клиент или дилер может при необходимости проверить образец на соответствие требованиям стандарта, сдав его на анализ в независимую лабораторию. Мы придирчиво относимся к проведению собственных тестов, поскольку отвечаем за качество продукции перед покупателем; так, результаты анализов напольных покрытий хранятся у нас в базе два года (то есть дольше гарантийного срока изделий, на случай рекламаций). Если у клиентов возникают какие-то вопросы по качеству приобретенной продукции, мы всегда готовы дать аргументированный ответ, предоставить детальную информацию по той партии плит, которая поступила потребителям.
Впрочем, поводов для рекламаций немного, ведь все рецептуры отработаны, используемые смолы проверены...
- Какой класс эмиссии формальдегида?
«ЛесПромИнформ» об ООО «Эггер Древпродукт»,
2011 год
C 1 июля группа компаний Egger стала владельцем ООО «Гагаринский фанерный завод» (г. Гагарин, Смоленская обл.). Сделка между прежним владельцем и немецкой группой компаний одобрена Антимонопольным комитетом РФ. «Россия представляет для Egger один из стратегически важных растущих рынков, - прокомментировал сделку руководитель компании в области финансов и управления Томас Ляйссинг. - Этот рынок хорошо развивался даже во время экономического кризиса и имеет большой потенциал».
Мощность Гагаринского ФЗ по выпуску сырой ДСП составляет 500 тыс. м3 в год, на предприятии имеется цех ламинирования производительностью 20 млн м2 в год, а также есть лесозаготовительное хозяйство площадью 80 тыс. га. На заводе работает около 500 человек.
- Стандартный - Е1. Хотя по желанию заказчика мы изготавливаем плиты и с так называемым классом Е0,5, для которых используется другая смола. Говоря об экологичности нашей плиты, следует упомянуть, что до того как компания ИКЕА приобрела завод в Новгороде, мы были одним из ее основных поставщиков, а ИКЕА очень серьезно относится к экологии. Для того чтобы работать на экспорт, мы должны придерживаться европейских и мировых стандартов, в частности, использовать только сертифицированную древесину. Мы дорожим своей репутацией на рынке, за нее отвечает наш отдел качества, кроме того, мы сотрудничаем с подобными службами других заводов группы, а также со сторонними организациями - институтами, лабораториями. Своей приверженностью к ответственному лесопользованию и FSC-сертификации мы вольно или невольно подталкиваем к этому и своих партнеров: заготовителям приходится сертифицировать свои арендные участки, чтобы соответствовать нашим требованиям. Те делянки, которые мы брали в аренду и передали подрядчикам, мы сертифицировали сами. Есть проверенный круг поставщиков сырья, с которыми мы постоянно работаем.
Модная «одежда» для плиты
Оставив за спиной монументальный пресс, следую по технологической цепочке дальше, стараясь не отставать от Евгения Лыюрова.
«Произведенная плита просвечивается сканером-дефектоскопом (он работает в полностью автоматическом режиме): если в ней обнаруживают пустоты, плита выбраковывается, отдельный участок транспортного конвейера опускается и подает ее в дробилку, - рассказывает коммерческий директор завода. - Дробилка разламывает плиту на части, которые поступают на стружечные станки и измельчаются, стружка осмоляется и опять становится сырьем для производства.
Бывает, покупатели, зная наши высокие стандарты качества, спрашивают, нельзя ли плиту второго сорта купить подешевле. Но нам нечего им предложить, ведь второго сорта у нас попросту нет.
Дальше по линии установлен промежуточный веерный охладитель. За ним - автоматический штабелер: набираем пачку высотой четыре метра, весом около 40 тонн, она автоматической тележкой перевозится на промежуточный склад, где остывает. Затем ее шлифуют, режут по форматам (максимальный размер мастер-плиты - 8400 х 2070 мм; в зависимости от того, какие размеры конечного продукта заявлены, ее режут по-разному: если нужна длина 4200 мм, то пополам, если 2100 мм, то на четыре части, и т. д.) и перемещают на другой склад. Все эти операции выполняются автоматически, людей на участке нет. Контролирует все процессы оператор шлифмашины.
Фактически на этом заканчивается основной производственный цикл: плита изготовлена, обрезана по формату, отшлифована, оставлена для остывания. Следующий этап - ламинирование».
К линиям ламинирования мы и направились по специальному мостику, соединяющему корпуса цехов.
«В цехе ламинирования установлены три пресса Wemhoener и параллельно работают три производственные линии, - продолжает рассказ г-н Лыюров. - На самом большом прессе можно ламинировать плиту формата до 3060 х 2070 мм (например, столешницы). Толщина выпускаемых плит - от 6 до 30 мм. Для выпуска плит толщиной 6 мм установлена отдельная каландерная линия на заводе Egger в Шуе, и заказы на тонкую плиту отрабатываются в основном там, на нашем заводе мы чаще всего выпускаем плиты толщиной 16 мм и больше.
Четвертая линия ламинирования (также от компании Wemhoener) стоит особняком - это самая современная модель подобного вида оборудования на сегодняшний день. Максимальное давление пресса - до 70 кг/см3 (для сравнения: на прессах других линий - 40 кг/см3).
На этой линии можно делать "глубокие структуры" и "синхронные поры" - такую отделку поверхности плиты, при которой рельеф полностью совпадает с рисунком дерева. По виду и на ощупь поверхность очень похожа на натуральную древесину, а по классу износостойкости даже значительно ее превосходит: не царапается, не подвержена воздействию влаги и солнечного света, огнеустойчива. Для получения синхронных пор на линии установлен специальный блок позиционирования декоративной бумаги относительно пресс-прокладки».
«Производство так называемого ламината мы открыли в мае прошлого года, - продолжает рассказывать Евгений Лыюров. - Толщина изделий - 8 мм. На каждое изделие специальный струйный принтер наносит информацию, по которой легко отследить, когда и какой сменой, из какой плиты оно сделано. За линией установлен робот-упаковщик, который приводит изделия в тот окончательный вид, в котором вы видите их в магазине. Упаковка - стандартная для продуктов всех предприятий группы Egger, одинаковая в России и за рубежом.
Проект Sofia
В рамках реализации первого этапа амбициозного технологического проекта в Гагарине ввод в эксплуатацию линии по производству MDF мощностью 350 тыс. м3 плит в год запланирован на вторую половину 2016 года. В декабре 2015 года в эксплуатацию введены: новая электроподстанция, окорочная линия, рубительная машина и элементы системы водоподготовки. За ними следует монтаж энергоустановки, рафинера, выпарной установки, сушилки, формовочной линии, линии прессования, участка окончательной обработки продукции, системы аспирации, системы генерирования сжатого воздуха, бункеров сырой стружки, бункеров древесной пыли для сжигания и системы подготовки топлива. Параллельно ведутся работы по установке инженерных систем и противопожарной техники.
Источник информации: Egger
На напольных покрытиях специализируется также завод в немецком г. Висмар, входящий в состав предприятий промышленной группы Egger. И сейчас часть клиентов, которые закупали продукцию там, переходят к нам. Пока это российские компании, но мы начинаем и экспортные поставки, мощности вполне позволяют. Висмарский завод загружен заказами на много месяцев вперед, и там, где возможно, наше предприятие призвано его заменить. Но не во всем - мы выпускаем разные коллекции, ценовые категории тоже различаются. Для российских потребителей мы готовы производить продукцию европейского качества по более низкой цене - ведь для того чтобы даже просто растаможить доставленные из Европы товары, требуются немалые деньги. Такие DIY-сети, как OBI, "Леруа Мерлен", "Касторама", это поняли очень быстро. Работа с OBI стала нашим пробным шаром в сотрудничестве с сетями, далее мы стали расширять сотрудничество с сетевиками и параллельно развивать собственную дилерскую сеть. Как в OBI, так и в сети "Метрика" уже представлены напольные покрытия MegaFloor, наш продукт, предназначенный для сетей DIY. Через дилеров мы продаем также и LFC, так называемый Egger-ламинат. Таким образом, мы используем разные маркетинговые инструменты, предлагая разным потребителям разные марки продукции. Сейчас в ассортименте напольных покрытий изделия, для отделки которых используются 26 декоров и три вида тиснения, и ассортимент постоянно расширяется».
Рядом с цехом расположен склад бумаги - большое помещение, габаритами напоминающее авиационный ангар, заполнено объемными рулонами бумаги разных декоров. «Пропитанная бумага находится здесь на стеллажах и отсюда поступает на линию ламинирования, - поясняет Евгений Лыюров. - Есть ограничения по срокам ее хранения, поэтому стараемся поддерживать такой запас, чтобы бумага здесь надолго не задерживалась».
Не задерживаемся и мы, переходим на «самое чистое производство», как называет его Евгений. Это линия пропитки.
«Чистота - это не только признак культуры производства, но и насущная необходимость, - подчеркивает коммерческий директор предприятия. - Древесная пыль горючая и взрывоопасная, поэтому на заводе мы всегда и везде стараемся поддерживать максимальную чистоту.
Линия пропитки - новейшая модель от компании Vits. Поставщики декоративных бумаг на предприятие - подмосковные заводы "Шаттдекор" (г. Чехов), "Интерпринт" (г. Егорьевск) и другие ведущие производители. Сейчас уже около 30% бумаги эти компании производят в России, и со временем эта доля будет расти - ведь гораздо рентабельнее привезти печатные цилиндры на место использования продукции, локализовать производство там, где дешевле рабочая сила».
Несложно было заметить, что в цехе подготовлено место для установки еще двух аналогичных линий пропитки.
«Мощности существующей линии достаточно для снабжения импрегнатом производства в Гагарине и частично в Шуе, - продолжает рассказ г-н Лыюров. - Когда на предприятии ощущается недостаток бумаги, мы докупаем необходимые объемы на нашем румынском заводе, там сейчас пропиточные мощности сильнее. До установки пропиточной линии на нашем заводе в прошлом году мы полностью зависели от поставок из Румынии и Австрии, а спустя несколько лет - кто знает, возможно, будем сами обеспечивать потребности других предприятий группы».
- Скажите, какие декоры пользуются повышенным спросом, что сейчас модно?
- Помните, как говорил джинн в старом советском фильме о волшебной лампе Аладдина? «Я раб лампы». У нас похожая ситуация: мы должны подстраиваться под вкусы и пожелания мебельщиков. А они могут продать только то, что готов купить конечный потребитель. Признанными законодателями мод в дизайне и декорах мебели, как известно, являются итальянцы. И если раньше новый декор, получивший признание на отраслевой выставке в Милане, мог добираться до российского потребителя пару лет, теперь все происходит гораздо быстрее: весной новинку показали в Милане, а осенью она уже в продаже у российских производителей мебели. Прежде всего это стало возможным благодаря тому, что мебельные компании сотрудничают с такими заводами, как наш. Мы предлагаем европейский сервис и европейские коллекции. У многих производителей в коллекции по 30-40 декоров, не более, а что-то иное - под заказ, что подразумевает изрядные затраты времени на разработку, согласование документов-соглашений, закупку бумаги и т. д., и т. п. На все это может уйти месяц, два, три... Наша складская программа (она единая для всех заводов группы) и постоянное наличие максимального числа декоров позволяют предлагать клиенту самые современные и востребованные декоры и удовлетворить любые запросы потребителя.
Отечественный покупатель мебели довольно инертен, так повелось еще с советских времен: вместо поисков нового покупки продолжаются по принципу «я хочу такой же шкаф, как у соседа». Взять хоть декор «Вишня Оксфорд», он пользуется популярностью, хотя был разработан в 1985 году! В Европе уже никто и не помнит, как он выглядит. Мы склонны ностальгировать: кто в Германии помнит Modern Talking? А у нас они полные залы собирают до сих пор. То же и с мебелью.
- Это плохо?
- Нет, просто это особенность, которую нужно учитывать. Есть разница даже в пристрастиях покупателей из разных регионов. Например, в Дагестане очень популярна мебель темных, насыщенных цветов: «орех эко», «орех горный», «венге», - и чтобы непременно была «золотая» фурнитура. В средней полосе России большим спросом пользуются венге, разные вариации на тему дуба, контрастные сочетания светлой и темной древесины. Мы стараемся удовлетворять все запросы, но также продвигаем современные европейские коллекции. И если раньше мы плотно работали с производителями мебели, то сейчас все больше сотрудничаем с архитекторами и дизайнерами, создающими интерьеры. У нас есть свой декор-менеджмент, есть специальная программа Zoom, с помощью которой наглядно можно показать все возможности использования и комбинирования декоров. Мы часто устраиваем встречи наших декораторов с производителями мебели, архитекторами, дизайнерами, в ходе которых на образцах плит из нашего ассортимента демонстрируем, например, как лучше всего совмещать и сочетать древесные рисунки с однотонными элементами разных цветов и оттенков.
Гагарин и Шуя
- Есть ли специализация у каждого российского предприятия Egger?
- Оба завода работают как на внутренний рынок, так и на экспорт. Завод в Шуе, кроме своей продукции, также предлагает потребителям продукцию европейских заводов группы Egger (кромку, бумажно-слоистые пластики, компактные плиты, легкие плиты eurolight и т. д.). Гагаринский завод предлагает клиентам только собственную продукцию.
Конечно, если ты партнер группы компаний Egger, тебе в равной степени рады на любом предприятии группы. Есть клиенты, которые ориентированы строго на наш завод, и для них мы сами перевозим нужные материалы из Шуи и отгружаем вместе с собственной продукцией. Такое взаимодействие предприятий - работа планового отдела и службы логистики, которая давно и хорошо отлажена. Например, если у нас с заказами поспокойнее, а на западноевропейских заводах завал, они не успевают их выполнять, то они обращаются к нам и просят изготовить для них определенные объемы нужного материала.
Я уже говорил, что здесь мы не делаем тонкую плиту, а при необходимости привозим из Шуи в шлифованном виде и ламинируем для своих покупателей. Кроме всего прочего, мощность шуйского завода ниже: в год на нем производится 280 тыс. м3. Покупателей его продукции больше, но берут они малые объемы. Завод в Гагарине ориентирован на крупных игроков рынка.
На заводе в Шуе оборудование более «возрастное», но у этого есть и свой плюс: возможность изготавливать мелкие партии. На нашем оборудовании - скоростном, мощном - маленькие заказы выполнять невыгодно, и мы размещаем их в Шуе. Хотя желание клиента, как известно, закон, и если клиент захочет, чтобы его заказ был выполнен именно здесь, пусть даже объем заказа будет одна-две пачки, мы выполним его в Гагарине, невзирая на затраты.
В 2014 году компания Holtec получила заказ на поставку линии подачи сырья для завода в Гагарине. Оборудование включало все системы подачи сырья и удаления отходов, а также окорочный станок, силовую и управляющую электрику, а также систему визуализации для всего оборудования. В том числе на заводе Egger был впервые установлен трехроторный окорочный станок модели VarioBarker 2 x 12.000 / 3, производительность которого составляет свыше 100 т АСВ/час, а допустимая длина сырья - до 6 м; угол наклона при подаче сырья можно изменять, адаптируя оборудование к различным условиям окорки. Инжиниринг на весь участок до рубительной машины был предоставлен фирмой Holtec.
Привлекательное лицо компании
- Склад готовой продукции - это лицо компании, - гордо улыбается Евгений, открывая дверь в следующее помещение. - Именно склад был построен первым, когда компания Egger приобрела завод, поскольку основополагающий принцип нашей деятельности - работа со склада. Склад должен быть всегда полон, ведь философия компании в отношении клиента состоит в том, что нужная ему продукция всегда должна быть в наличии. А наша первостепенная задача - поддерживать и регулировать запас на складе. У Egger отлично развитая складская программа, позволяющая гарантировать клиенту наличие любого нужного ему материала в любое время дня и ночи. Заказы мы принимаем по телефону, факсу, электронной почте - и сразу заводим их в систему, данные которой обновляются ежедневно.
Устраивая клиентам экскурсию по заводу, мы первым делом приводим их сюда. Прежде всего для того, чтобы они видели, как правильно должны храниться древесные плиты, чтобы избежать их повреждений, коробления и т. п.
Склад разделен на специальные ячейки. Есть особая маршрутная карта, где отмечено - в каком месте хранится какой декор: водитель погрузчика, получая документы на погрузку машины, знает, из каких ячеек какого ряда сколько пачек чего следует забрать.
Как все это работает? Мы получаем заказ, заносим данные о нем в специальную систему, обсуждаем с отделом планирования сроки, особенно если каких-то материалов нет в необходимом количестве на складе, сообщаем клиенту предполагаемую дату готовности заказа - официальный документ, на который он ориентируется, для того чтобы осуществлять платежи и отправлять машины за готовым продуктом.
Здесь постоянно содержится более 200 номенклатур. Мы еженедельно проверяем статистические данные по отгрузке определенных материалов, декоров - и как только запас остается на неделю-две, пополняем его, включая нужные позиции в заказ на производство. Такой подход дает нам серьезное преимущество перед конкурентами, особенно когда речь идет о таких значимых проектах, как олимпийские объекты в Сочи, или о тендере на строительство большой гостиницы с четко обозначенными сроками. Компания, которая делает мебель для подобного проекта, поставлена в жесткие рамки и не может себе позволить ждать исполнения своего заказа на производстве даже день-два.
- Каковы базовые сроки выполнения заказов?
- Если говорить о складском ассортименте, все просто: сегодня заказ - завтра отгрузка. Если же речь о спецзаказах (особый декор, структура поверхности и т. п.), выполняем в течение недели. На заводе два этапа планирования: во вторник и пятницу, когда производству даются задания на следующие несколько дней. Если человек сделал заказ, допустим, в понедельник, то во вторник он уже проходит планирование и поступает на производство, а в четверг клиент может присылать машину за готовой продукцией. Наши сегодняшние производственные возможности позволяют поддерживать заполненным склад и обеспечивать выполнение особых заказов клиентам. В прошлые, докризисные годы случался «высокий сезон» (например, перед Новым годом), когда спрос был настолько велик, что покупателям приходилось иной раз ждать две-три недели.
- Евгений, может быть, вы припомните самые крупные и важные заказы...
- Я уже упомянул, что олимпийские объекты в Сочи не обошлись без изделий, изготовленных из нашей плиты. Также мы постоянно сотрудничаем с такими крупными компаниями, как «Ангстрем» (г. Воронеж), «Столплит», «Лером» (г. Пенза). Нашу плиту охотно приобретают польские и украинские мебельщики, ведь, невзирая на все политические неурядицы, бизнес остается бизнесом.
- Как ни крути, политика влияет на экономику. Как это сказывается на вашей деятельности?
- Для нас совсем некстати обострение отношений с Турцией: Egger владеет заводом по производству кромочных материалов недалеко от Стамбула. Были обоснованные опасения, что мы не сможем поставлять кромку нашим российским клиентам, и остается только порадоваться, что этот вид продукции не вошел в список запрещенных к ввозу материалов.
- В какие страны экспортируете свою продукцию?
- Наша площадка удачно расположена - недалеко от границы с Польшей. Хороший выход на Запад. Мы успешно работаем с предприятиями стран Балтии. Что касается нового завода, то мы рассматриваем возможности крупных поставок в Китай, США, где востребованы плиты MDF.
За рубеж мы могли бы отправлять вообще всю продукцию, что производим, ни листа не продавая в России. Но мы не хотим этого делать, это несправедливо по отношению к отечественным клиентам. Думаю, на экспорт станем отдавать 20-30% выпускаемой продукции, остальное планируем реализовывать на внутреннем рынке. Мы для того и строим второй завод, чтобы предоставить российским дилерам российскую продукцию, полностью обеспечить деловых партнеров нашей плитной продукцией.
- И все же это вопрос будущего. А в настоящее время в какие российские регионы идет ваша продукция?
- Используя географическое положение завода, мы успешно работаем в Центральной России и в европейской части страны. Но мы также отправляем контейнеры в Екатеринбург и в регионы Сибири. Когда появится своя железнодорожная ветка, станем отправлять продукцию за Уральский хребет вагонами.
Два наших российских завода совокупно отгружают около 100 большегрузных автомашин продукции в сутки. Это очень большие объемы и, «благодаря» особенностям российских законов, изрядные хлопоты. Недавно мы купили осевые весы, чтобы контролировать осевую нагрузку грузовиков (превышение установленных нормативов карается серьезными штрафами по законодательству), и проверяем машины прямо на выезде со склада. Да, весы стоят полмиллиона рублей, но и штрафы весьма внушительные. Кстати, внедрение весов позволило усовершенствовать схему загрузки, нам удалось на 10% снизить транспортные расходы клиентов. Кризис заставляет людей считать каждый рубль, совсем по-другому стали рассуждать бизнесмены - и это правильно.
***
Есть на заводе и склад запчастей и расходных материалов, где хранится их внушительный запас денежным эквивалентом 5 млн евро. Среди вспомогательных участков стоит отметить автомастерскую, где ремонтируют погрузчики, и участок металлообработки с современным станочным парком. Конечно, нельзя обойти вниманием тему энергоснабжения производства.
- Используете ли вы древесные отходы производства для выработки энергии?
- Древесную кору мы частично перерабатываем (измельчаем), но не в полном объеме - излишки пока вывозим на свалку. Возможно, в дальнейшем станем использовать кору в качестве топлива по схеме, действующей на румынском предприятии группы, где имеется энергетическая установка, которая утилизирует все древесные отходы и обеспечивает электричеством весь завод, еще и на продажу городу остается.
Сейчас наши котлы работают на газе, допускаю, что в будущем их сменят котлы на биомассе. Тогда ситуация с энергообеспечением станет совсем другой. На предприятии установлена электрическая подстанция во избежание риска сбоев по причине скачков напряжения от внешних электросетей, которые этим, к сожалению, грешат. Плюс для обеспечения бесперебойности работы мы за свой счет подвели на площадку вторую, резервную высоковольтную линию: если на одной произойдет скачок, за счет второй мы обеспечим безостановочное производство.
Цех ламинирования:
- производство ЛДСП;
- ламинирование плит HDF (КТ4);
- технология создания глубоких структур и синхронных пор на плитах ЛДСП и HDF (КТ4);
- производство плит форматов: 2800 х 2070 мм, 2440 х 1830 мм, 2620 х 2070 мм, 2770 х 1830 мм;
- общая производственная мощность - 34,8 млн м3 в год.
Что дальше?
В строящихся цехах нового завода Egger в Гагарине будет пущено производство плит MDF и HDF, к существующим линиям ламинирования планируется добавить еще две, помимо пятой по счету, которая сейчас находится в стадии монтажа.
«На ней будут производиться только напольные покрытия, а ее мощность позволит четвертую линию перевести на ламинирование ДСП, - поясняет коммерческий директор предприятия. - Сейчас мы чередуем заказы. В ближайшее время мы перейдем при изготовлении изделий на использование исключительно плиты своего производства, тогда как прежде использовали плиту HDF, выпускаемую на предприятии в Висмаре.
C первых шагов в России Egger делает ставку на все самое лучшее: самое современное оборудование, самые передовые разработки. Интересно отметить, что иногда наладчики устанавливаемого оборудования в момент монтажа впервые видели чертежи - такими новыми были модели привезенного оборудования.
Поставка оборудования на новое производство ведется концерном Siempelkamp, сейчас это вообще основной поставщик оборудования для предприятий группы». (С момента визита автора этих строк на предприятие произошли очередные перемены: на заводе завершился монтаж линии по производству плит MDF c прессом ContiRoll Siempelkamp, сейчас на линии идут пусконаладочные работы; введена в эксплуатацию пятая линия ламинирования фирмы Wemhoener (КТ5); установлена шлифовальная машина для плит MDF; началось строительство склада напольных покрытий.
Цех производства напольных покрытий
Установка FuBo 10. Оборудование фирмы Homag:
- одна из двух самых быстрых установок в мире (вторая - на заводе Egger в г. Брилон, Германия);
- рабочая скорость - 360 м/мин., за минуту производится 250 элементов (31 палета, или 3750 м2 в час).
В будущем планируется установка еще одной такой линии (даты пока не определены).
Люди в приоритете
- Оборудование должно быть максимально автоматизировано, а человек должен лишь управлять им, - убежден Евгений Лыюров. - Подобный подход - еще одно отличие нашего предприятия от многих российских, где до сих пор доля ручного труда очень высока, на производстве задействовано много людей.
- Хотя в цехах, по которым мы с вами прошли, людей мы почти не встретили, а оборудование работает в автоматическом режиме, однако 700 человек персонала в штатном расписании «Эггер Древпродукт» все же значатся...
- Но это же общее число. Чтобы подсчитать, сколько человек в три смены трудятся непосредственно на производстве, от этого числа нужно отнять человек 70, работающих в двухэтажном корпусе управления (в штате учтены и такие подразделения, как отделы продаж, планирования, юридический и финансовый, бухгалтерия и пр.), а оставшееся число разделить на три; 200 человек в смену - не так и много для столь масштабного производства.
Мы стараемся, чтобы люди эффективно работали. Невысокая эффективность труда - еще одна проблема российской экономики и, пожалуй, менталитета. Наши австрийские коллеги до сих пор не могут понять, отчего в России так много праздничных и выходных дней в течение года, как можно приходить на работу к 8 часам и до девяти пить чай, травить байки, а только потом приступать к делу. Это настоящий бич: поскольку у нас непрерывный цикл, каждый праздник выбивает производство из колеи, и нужно оперативно решать, кому и куда отгружать готовую плиту, чтобы не сбился отлаженный ритм работы.
В настоящее время на заводе Egger в г. Гагарине работают около 700 человек. Из них примерно 90% - жители Гагарина и Гагаринского района, остальные - из других городов России.
Завод работает круглосуточно и круглогодично, без выходных и праздников, отгружаем продукцию без задержек, он единственный в группе компаний, который работает в подобном режиме. В отличие от западноевропейских стран, где уж не знаю что должно случиться, чтобы сделали отгрузку ночью или в выходной.
Производственные отношения на заводе строятся иначе, чем принято на российских предприятиях. Периодически тройка руководителей завода обходит все цеха и участки, встречается с сотрудниками и в неформальной обстановке обсуждает насущные вопросы (рабочие, и не только). На стенах многих помещений можно увидеть красные ящички с надписью: «Идеи Egger», - и любой рабочий, который видит на своем участке возможности для улучшения рабочего процесса, может записать свою идею, а записку опустить в этот красный ящичек. Идея обсуждается техническими специалистами и, будучи признанной актуальной, реализуется, а рационализатору выплачивается премия. Кроме того, подобные инициативы обнародуются и пропагандируются на предприятии.
Основная часть сотрудников предприятия - местные жители и специалисты, которые, как и я, когда-то переехали в Гагарин, чтобы работать на заводе.
На заводе работают и зарубежные специалисты.
«Мы используем синергию всех 17 предприятий группы, - поясняет г-н Лыюров. - Как правило, вводя в эксплуатацию новое производство, привлекаем работников аналогичных действующих производств, чтобы они не только осуществили пуск знакомого им оборудования, но и показали, как на нем надо работать, обучили тех, кто только начинает осваивать суперсовременную технику. Так, в Гагарине можно услышать немецкую, румынскую речь.
В зависимости от необходимости, от того, как формируется новая рабочая команда, приглашенный специалист остается здесь год, два, а может и больше - помогает осваивать новое оборудование и уезжает, а здесь остаются работать подготовленные им специалисты. Так, первым главным механиком на заводе был австрийский подданный, впоследствии его сменил обученный им житель Гагарина. Подобная смена произошла недавно и в руководстве цеха ламинирования.
Вероятно, похожая история будет и на производстве плит MDF. Год или полтора, в зависимости от указаний владельцев бизнеса, новым предприятием будут командовать приезжие, а за это время мы вырастим местные кадры. Сейчас много зарубежных коллег работает на пусконаладке нового оборудования».
Конечно, причина задействования на предприятии приезжих профессионалов не только в интеграции предприятий группы компаний.
- Что скрывать, - признается коммерческий директор завода, - со специалистами большая проблема: на некоторые должности мы вынуждены искать людей в других регионах и странах, поскольку здесь их просто нет. И это касается не только требующих долгой и серьезной подготовки руководящих кадров, но и, например, сварщиков. Казалось бы, что тут хитрого, обычная рабочая специальность. Ан нет: у нужных нам сварщиков должна быть определенная лицензия, особые допуски, специальные навыки и опыт - таких в России можно по пальцам сосчитать. Это результат неправильного подхода к кадровой проблеме: довольно долго руководству наших предприятий было проще заплатить аккордно какому-то заезжему дяде, нежели вкладывать средства в обучение людей на местах. Результаты такого подхода мы и наблюдаем сегодня: за что ни возьмись, обнаружишь на продукции клеймо "Made in..." Мы вкладывали в чужую экономику - китайскую, европейскую, турецкую - вместо своей, в России до последних лет все меньше своего делалось. Надеюсь, кризис и санкции будут играть очищающую и вразумляющую роль. Нужно учиться обеспечивать себя самим. В том числе и высокопрофессиональными рабочими кадрами, уровень подготовки которых соответствовал бы сложности обслуживаемой техники. Да и деревообрабатывающее оборудование в самой богатой по запасам древесины стране следовало бы делать свое.
Люди - наш приоритет. Когда завод вводили в эксплуатацию, с экономикой в стране дела обстояли неважно. И 80% работоспособных мужчин из Гагарина ездили на заработки в Москву, здесь у них оставались семьи. Мы стали основным работодателем в городе с достойными условиями работы для людей. Многие впервые узнали, что такое оплачиваемый отпуск, социальный пакет и специальные программы (спортивные секции, бассейн, аэробика, ДМС для всех сотрудников). Сотрудникам платим очень неплохие зарплаты, причем работаем исключительно "по-белому", компенсируем затраты на общественный транспорт (человек, заходя в автобус, просто показывает заводской пропуск), регулярно индексируем зарплату с учетом инфляции и т. п.
Многие наши сотрудники говорят, что даже не ощущают кризиса. Да, компания не получает такой прибыли, как раньше, да, мы развиваемся не так быстро, как хотелось бы, но это общероссийские проблемы, и только совместными усилиями их можно решить. Мы все это понимаем и стараемся загрузить работой своих сотрудников. Ведь если нет хороших работников, нет прибыли. Люди должны хотеть работать. А к нам, как вы, может быть, знаете, стоит очередь из желающих устроиться на завод... Этот факт говорит сам за себя.
Ситуация развивается так, что по отдельным специальностям ресурсы города уже иссякли. Мы ведь ищем узких специалистов: электриков, водителей погрузчиков, операторов сложного деревообрабатывающего оборудования. Кого могли взять на работу из гагаринцев, мы уже взяли. Причем отбор довольно жесткий: руководитель каждого подразделения лично набирает себе команду и даже на вакансию помощника слесаря кандидат может пройти пять собеседований. И мы уже вынуждены брать людей из близлежащих областей: Калужской, Московской, Ленинградской. Местных жителей среди наших сотрудников примерно 95%. Но вот простой пример: недавно я искал людей для работы по экспорту, нужен был человек с хорошим английским или немецким языком, а достойные языковые вузы с высоким уровнем преподавания иностранных языков поблизости есть только в Смоленске. Как я ни хотел взять гагаринских ребят, пришлось брать смолян. У них там, кстати, с работой очень плохо, так что они охотно ездят сюда».
Гагарин. Завод и город
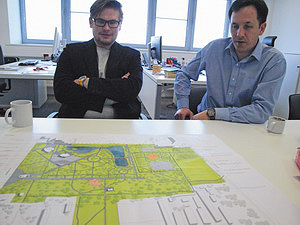
Евгений Лыюров обсуждает планировку парка с
Андреем Поляковым, руководителем проектов в
коммуникационном агентстве АГТ
- А как складываются отношения властей города и руководства завода? Оказываете ли поддержку и помощь друг другу? Участвует ли «Эггер» в жизни города?
- Изначально основной проблемой оказалось не построить завод в чистом поле, а получить все необходимые разрешения, поддержку местных властей, да и населения, наконец!
Чего скрывать, есть определенная антипатия ко всему новому, пришлому в маленьких российских городах. Мы с этим столкнулись. Рассуждали обыватели примерно так: «Приехали какие-то, понастроили, да еще и дымят!» Приходилось объяснять, что дым из трубы - это безвредный пар, что завод на 100% экологичен и приносит городу не вред, а пользу. Мы до сих пор проводим по пятницам бесплатные экскурсии на производство для всех желающих, набираем группы. Многие горожане посетили завод, прошли, как мы с вами, по всем участкам, их сомнения развеялись, и сейчас былого накала отношений нет и в помине.
Вообще, это парадокс: в городе большая проблема с работой, люди ропщут - некуда устроиться, а приходит нормальный работодатель, и его принимают в штыки: «А почему у нас?» Поражает иждивенческая философия некоторых местных жителей: дескать, наш город - город первого космонавта планеты, нам должны! Кто должен, что должен? Никак не возьмут в толк, что никто и никому ничего не должен, всего нужно добиваться собственными силами и старанием. В стране давно капитализм.
Хотя, конечно, на образе Гагарина и всего связанного с ним городские власти могли бы зарабатывать огромные деньги, развивая туристическую индустрию. Но они этого не делают почему-то. Туристы едут со всей страны и из-за рубежа, а в музее Гагарина даже нормального туалета нет, как говорится, удобства во дворе. Обидно. Когда отмечали юбилей первого полета человека в космос, праздновали его не в Гагарине, а в г. Королеве, именно потому, что здесь нет никакой инфраструктуры. Вижу в этом недоработки местного руководства, хотя, вероятно, и недостаток финансирования сказывается тоже.
Знаете, Гагарин ничем не отличается от любого другого маленького провинциального города России, и проблемы здесь те же, что и в других. Прежде всего это ограниченность бюджета. Поэтому мы нормально реагируем на обращения городского руководства за поддержкой - финансовой или материальной (в виде нашей продукции, например, для изготовления мебели для детского сада). Да, мы платим миллионы рублей налогов, но они «уходят» в Смоленск, и небольшая часть их потом возвращается в город, чего совершенно недостаточно для развития. И это при том, что Гагаринский район - донор области, он дотирует другие районы за счет развивающихся здесь крупных промышленных предприятий: нашего завода, крупной агрофирмы «Останкино» и других. Конечно, система налогообложения требует пересмотра, но делать это необходимо на общегосударственном уровне. Не так давно проходила встреча властей города с губернатором Смоленской области, где как раз обсуждался вопрос перераспределения налоговых потоков.
Руководство нашего предприятия решило: мы будем помогать прежде всего образовательным учреждениям - детским садикам, школам. Иногда сумма подобной помощи достигает полумиллиона рублей в месяц. Только за первые месяцы года реализовано 19 социальных проектов с нашим участием. Мы контролируем, как именно используются средства, выделенные на благотворительность, а не просто отдали деньги и забыли. Регулярно направляем проверяющих на объекты, запрашиваем отчеты и фотоотчеты, что позволяет оказывать помощь не только адресно, но и эффективно. Egger помогает ремонтировать дороги в городе (под жестким техническим и финансовым контролем).
Мы продвигаем идеологию, нашедшую отражение в лозунге, который вы можете видеть в наружной городской рекламе и на бортах автобусов: «Работай в Гагарине, оставайся с семьей!» Местное работоспособное население после кризисов 1990-х и «нулевых» привыкло ездить на заработки в Москву - до границы Московской области всего 10 км. И до сих пор процентов шестьдесят местных мужчин ездят в столицу, просто чтобы обеспечивать свои семьи. Но вы же понимаете, какая это при всех московских плюсах жизнь: рано утром в понедельник человек садится в отправляющийся в столицу поезд и возвращается к своим близким только поздно ночью в пятницу. Видит семью только на выходных. Это же не дело! Для меня одним из основных критериев при наборе сотрудников является желание людей работать там, где они родились.
Значимый социальный проект завода Egger в Гагарине - ремонт и реконструкция городского парка, который находится в центральной части города и заброшен с советских времен. В городском бюджете денег на приведение его в порядок, разумеется, не хватает, а детям горожан, в сущности, отдыхать и играть негде. Руководство компании собирается в течение нескольких лет вложить в возрождение парка миллионы рублей (пять - только в течение ближайшего года). Первые объекты для реконструкции - центральная аллея и пруд. Выбраны дизайнеры, подрядчики-строители; сейчас проект, разработанный московской архитектурной студией «Практика», находится в стадии реализации.
Стейки VS гамбургеры
- Какие из действующих на территории страны предприятий вы бы назвали своими конкурентами?
- Говорить о конкуренции «Эггер Древпродукта» с российскими заводами можно довольно условно. Многие из них производят плиты других форматов, например, 2044 х 1830 мм. Мы тоже такой делаем, но основной наш формат 2800 х 2070 мм. На мебельных предприятиях на разные форматы настроены станки, и, как это ни удивительно, зачастую инертность технологов настолько высока, что они просто не хотят перенастраивать оборудование. Вот и выходит, что мы работаем как бы параллельно с другими производителями: каждый на своего клиента.
Ну и к тому же редкий российский завод может обеспечить выпуск плит с таким широким модельным рядом декоров, тиснений, как на нашем. Мы постоянно вкладываемся в обновление - деньгами, материалами, оборудованием, собственными силами. У нас есть служба декор-менеджмента, разрабатывающая свои декоры с полным технологическим обеспечением (какая для производства новинки требуется краска, какой цилиндр, рисунок и пр.). Мы комплексно подходим к делу, чтобы клиент мог сразу получить у нас все, что ему необходимо: мебельную плиту, напольное покрытие и т. д., и т. п. Такова сейчас тенденция в Европе: все сразу от одного поставщика.
Есть еще одна австрийская компания на российском рынке - сильный, агрессивный конкурент, и я только рад, что он постоянно держит нас в тонусе.
Мы за честные отношения с клиентом: если даже курс «прыгнул», после того как оформлен и оплачен заказ, все равно продаем товар по оговоренной цене. Есть же в конце концов этика бизнеса, как было до революции уважаемое купеческое слово: какую цену выставил за товар, за столько и отдай. Да, может быть, мы не получим при этом ожидаемой прибыли, да, снижается маржа, но репутация дороже, и партнер оценит такую добросовестность поставщика, останется с нами. Кроме того, мы всегда продаем за рубли, то есть за валюту страны, где работаем. Кто-то из конкурентов в условиях нестабильности национальной валюты перешел на евро и создал клиенту головную боль - и он никогда не знает, сколько в итоге заплатит за следующую партию сырья, а значит, не понимает, как планировать собственную экономику, как формировать цены на свою продукцию. Egger - семейная компания, и ключевое слово здесь «семейная»: для успеха предприятия отношения, как в семье, должны быть и внутри компании, и с постоянными партнерами. Решения принимаются взвешенно, без суеты и спешки. Первым, кто приехал в Гагарин, когда завод перешел в руки австрийской компании, был Михаэль Эггер; он собрал всех руководителей, чтобы познакомиться, и всех, кто до сих пор работает здесь, знает по именам. В том числе и многих рабочих. Не думаю, что так строятся отношения на многих предприятиях в России, при том что именно у нас многие важные вопросы решаются благодаря не столько формальным, сколько неформальным взаимоотношениям! Сегодня мы идем навстречу насущным надобностям клиента - завтра он отнесется с пониманием к каким-то нашим проблемам. Уверен, в работе с нашей компанией партнеры видят куда больше плюсов, чем минусов, и в подтверждение своих слов отмечу, что в период кризиса много клиентов других компаний перешли к нам потому, что не нашли понимания у своего прежнего поставщика.
Мне дорог любой клиент, иной раз я даже слышу на заводе: «Ты чьи интересы отстаиваешь: наши или клиента?» А я считаю, что занимаю правильную позицию, и отвечаю: «А кто еще за нашего клиента должен его интересы отстаивать?» Клиенту должно быть комфортно работать с поставщиком, он не должен думать ни о каких технических вопросах, связанных с получением товара, за который заплатил деньги. Подобного положения вещей мы добивались постепенно и не всегда легко преодолевали некоторые проблемы...
При этом имейте в виду, Egger никогда не позиционировал свой продукт как массовый, то есть не делал ставку на большие объемы при невысокой цене. Мы не стремимся лепить гамбургеры для фастфуда - мы хотим делать добротные стейки. Мы не демпингуем. Продукция под маркой Egger, вероятно, всегда будет несколько дороже, чем аналогичная у конкурента, но понимающий человек, как и в случае с общепитом, знает, чем обоснована разница в цене, и понимает, почему она оправданна. Возвращаясь к разговору о конкуренции: мы не ставим себе цель отвоевать клиентов у конкурента - мы будем занимать свою нишу, ориентируясь на производство продукции высокого качества и стремясь наиболее полно удовлетворить запросы клиента. А с конкурентами станем соревноваться уже потом, на прилавках магазинов: уровнем качества, коллекциями декоров, разнообразием моделей.
Неизбежный монолог о кризисе
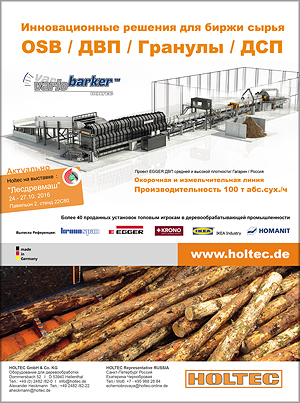
Holtec. Оборудование для лесопильных заводов
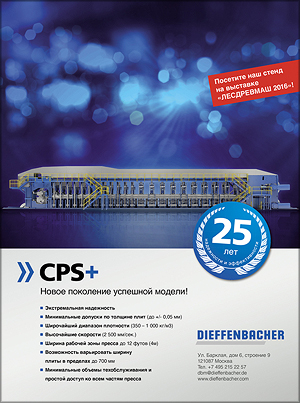
Dieffenbacher. Оборудование для производства
древесных плит
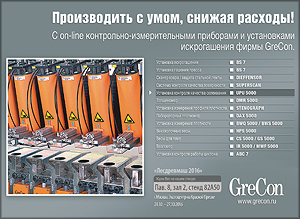
GreCon. Системы искрогашения и измерительные
системы
Есть одна тема, которую в разговоре про бизнес никак нельзя обойти. Во всяком случае не теперь и не в России. Вопрос о кризисе заставил Евгения Лыюрова ненадолго задуматься:
«Кризис... Наш завод, считаю, неплохо преодолевает его. Причем, как ни странно, если бы завод был стопроцентно российским, было бы гораздо трудней: знаю от коллег с других предприятий, что кредиты в банках не взять, а если и дают кредит, то под неподъемные проценты. Помогает и поддержка внутри группы: прежде мы очень много зарабатывали именно в России, сейчас другие рынки выручают: сейчас настоящий бум в Англии, завалены заказами заводы Egger в Австрии и Германии. Наша ГК теперь хорошо зарабатывает там, и руководство компании с пониманием и терпением относится к тому, что год-два российские подразделения не будут приносить серьезный доход. Может быть, мы даже будем брать от группы больше, чем приносить, но я уверен, что все, что взяли, отдадим! Причина такой уверенности очевидна: в России конкуренция все еще очень невысока в сравнении с той же Западной Европой. Открытие каждого завода, подобного нашему, дает толчок развитию мебельных производств, появлению новых игроков на этом рынке. И здесь потенциал еще довольно высок. Это только кажется, что в стране полно мебельных фабрик, - на самом деле, стоило грянуть кризису, и у нас «вымели» весь склад; не потому, что мебельщики делали запас плиты, а потому, что возник ажиотажный спрос на их продукцию: люди старались вложить обесценивающиеся деньги в том числе и в мебель. Вот такое подтверждение моим словам о том, что на качественную плиту здесь долго будет высокий спрос.
Логика развития мебельной промышленности в кризис чем-то схожа с логикой развития автопрома. Владелец авто рассуждает примерно так: «Я не знаю, что будет завтра, поэтому сегодня вложу немножко в ремонт машины и еще пару лет на ней поезжу. Новую покупать не буду, хотя на нее есть деньги, - время непростое, мало ли что». Так и с мебелью: те люди, которые хотели ее купить, уже (один раз) купили и не спешат обновлять обстановку, а большинство просто откладывает покупку на потом. И это понятно: хлеб человеку нужен всегда, а мебель не покупают, когда нет денег на хлеб. Поэтому мебельные предприятия в кризисные времена всегда работают вполсилы - недавно общался с коллегами из Калуги, они рассказывали, что там едва ли не все фабрики работают три дня в неделю...
Кризис и падение курса национальной валюты способствуют выходу производителей на зарубежные рынки, - считает Евгений Лыюров. - Мы можем предложить покупателю лучшие цены в евро, чем конкуренты, - и на ЛДСП, и на напольные покрытия. Это позволяет нам наращивать объемы. С вводом в эксплуатацию нового завода мы нарастим долю сбыта на экспорт: рынки Ирана, Ирака, Афганистана, Турции весьма охотно потребляют плиты MDF. Скоро начнутся поставки этих плит и по регионам России - на рынке появится еще один сильный игрок с известным потребителю именем.
Почему компания семьи Эггер делает ставку на Россию? Вы посмотрите на карту, ведь за Уралом, в Сибири плитных и мебельных производств фактически нет. Кризис помог нам избавиться от китайских конкурентов, а курс рубля избавляет и от европейских - для нас открыт огромный рынок! И тот, кто сейчас вкладывается в развитие, строит, прирастает производственными мощностями, по завершении кризиса стартует быстрее всех и добьется большего. Не случайно наш завод постепенно становится самым большим из 17 предприятий группы Egger.
В России кризис, а Egger вложил 250 млн евро в новый завод. Если австрийские бизнесмены делают такие инвестиции в рынок страны, которая находится в далекой от идеала экономической ситуации, значит, они верят в него, - верно?»
Подготовил Максим ПИРУС
ЛесПромИнформ №1 (123), 2017 г. «Эггер Древпродукт Гагарин» делает ставку на плиты MDF
ЛесПромИнформ №8 (82), 2011 г. Egger приглашает в Гагарин
ЛесПромИнформ №1 (59), 2009 г. Гагаринский фанерный завод. Лидерство, дающее уверенность