Современные методы изготовления алмазных фрез для обработки древесных материалов и пластиков
Появление поликристаллических алмазов позволило производить сравнительно недорогой дереворежущий инструмент. Использование в деревообработке основного технологического оборудования с ЧПУ, оснащенного таким инструментом, в том числе высокоскоростных поточных линий, обеспечивает его высокую производительность, уменьшение трудозатрат и доли ручного труда, возможность выпуска разноплановой продукции и повышение рентабельности производства.
В статье рассмотрены современная технология и необходимое оборудование для производства дереворежущего инструмента.
Технологии изготовления режущего инструмента
Технологии производства насадных и концевых фрез из инструментальных сталей, а также на основе режущих элементов из твердых сплавов (HW) давно и досконально отработаны в мире, в том числе в России, однако постоянно совершенствуются производителями режущего инструмента за счет применения нового обрабатывающего оборудования и расходных материалов.
Что касается режущего инструмента из поликристаллических алмазов (PSD), то технология его изготовления известна в мире всего несколько десятков лет, а в России предприятия, которые производят такие фрезы с нуля, можно сосчитать по пальцам одной руки.
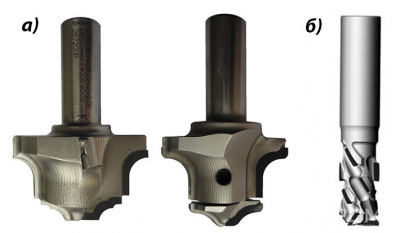
Сегодня существуют минимум две технологии производства режущего инструмента: традиционная и современная. Традиционная технология основана на применении, как правило, не особо точного позиционного, иногда проходного оборудования с традиционными, стандартизированными по ЕСКД методами проектирования (кальками, чертежами и т. п.). Подробно она описана в специальной литературе и учебниках по обработке металлов, а также в ГОСТ 13932–80 «Фрезы дереворежущие насадные цилиндрические сборные. Технические условия (с изменениями №1, 2, 3, 4, 5)», ГОСТ 8994–80 «Фрезы дереворежущие концевые цилиндрические. Технические условия», ГОСТ Р 52419–2005 «Фрезы насадные, оснащенные твердым сплавом, для обработки древесных материалов и пластиков. Технические условия», ГОСТ Р 52589–2006 «Фрезы концевые, оснащенные твердым сплавом, для высокоскоростной обработки древесных материалов и пластиков. Технические условия и требования безопасности» и ряде других, в настоящее время катастрофически устаревших по рекомендуемым материалам, сплавам, допустимым допускам и посадкам, дисбалансу, а также биению.
В качестве примера можно привести рекомендуемые этапы проектирования фрезы: анализ профиля и уточнение конструктивной схемы фрезы; выбор материала режущей части; выбор основных параметров фрезы; профилирование зубьев, расчет конструктивных параметров; вычерчивание фрезы и назначение технических требований.
Рекомендуемые этапы изготовления фрез:
- Подготовка заготовки фрезы: заготовка материала для фрезы; термическая обработка заготовки; обработка внутреннего отверстия; обточка боковых поверхностей.
- Фасонная обточка заготовки – поверхности вращения.
- Фрезерование зубьев: разметка зубьев; сверление отверстия впадин; фрезерование зубьев.
- Фасонная обработка зубьев фрезы – формирование затылков зубьев.
- Термическая обработка фрезы: закалка; отпуск.
- Отделка фрезы: чистовое шлифование внутреннего отверстия; чистовое шлифование боковых опорных плоскостей; клеймение, нанесение штампа изготовителя.
- Заточка: заточка зубьев; балансировка.
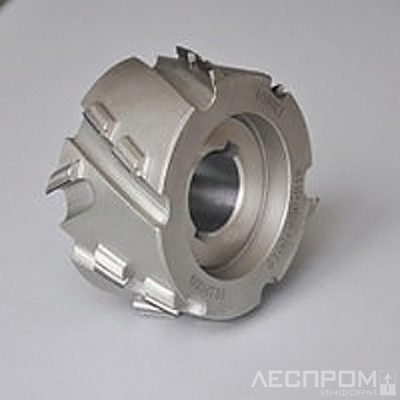
У традиционной технологии много недостатков, в частности, длительные сроки изготовления инструмента, значительные трудозатраты, необходимость большого штата проектировщиков, ИТР и рабочих. Кроме этого, точность изготовления инструмента по этой технологии невысока, а установка такого инструмента на современное оборудование с частотой вращения шпинделей 18000–36000 1/мин может привести к печальным последствиям как для заготовок и оборудования, так и для персонала.
Современная технология производства алмазного режущего инструмента строится на иных принципах, чем традиционная, в частности, на цифровом объемном проектировании и применении оборудования 3D–6D с ЧПУ. Это позволяет при проектировании видеть инструмент со всех сторон, исключить дефекты конструкции, а также быстро начать выпуск продукции на основе электронных чертежей, адаптированных к оборудованию. Кроме того, по традиционной технологии на оборудовании можно одновременно изготавливать как концевой, так и насадной режущий инструмент, а также наладить выпуск не только серийного, но и штучного инструмента – фрез (рис. 1, 2).
К сожалению, ни ГОСТов, ни доступной популярной отечественной литературы по этой технологии нет. Отсутствуют и рекомендуемые параметры и технологические режимы изготовления фрез, поскольку это, как правило, коммерческая тайна производителя инструмента.
Технология и оборудование для изготовления алмазных фрез
Изготовление фрез можно разбить на следующие этапы:
- цифровое проектирование инструмента на основе ТУ заказчика;
- нарезка заготовок из металлопроката (инструментальной и конструкционной стали);
- токарная 3D-обработка заготовок (для серийного производства);
- фрезерная 6D-обработка заготовок (для мелкосерийного и серийного производства);
- галтовка готовых корпусов;
- закалка заготовок;
- напайка алмазных пластин на корпус фрезы;
- пескоструйная обработка заготовок;
- электроэрозионная заточка и профилирование режущих элементов фрезы;
- оптический контроль соответствия параметров фрезы чертежу;
- динамическая балансировка инструмента;
- нанесение покрытия на корпус фрезы;
- печать логотипа фирмы и маркировки на корпусе фрезы;
- упаковка инструмента и отправка на склад.
Такая технология позволяет выпускать прецизионный (особо высокоточный) режущий инструмент для современного высокопроизводительного (позиционного и проходного типа) оборудования, рассчитанного на долгосрочную качественную работу.
Рассмотрим современную технологию производства алмазных фрез подробнее.
Отдел проектирования и производственный участок должны быть укомплектованы квалифицированными инженерами-конструкторами, ИТР и операторами-станочниками и оснащены проводной или беспроводной системой приема и передачи данных (интернетом, Wi Fi и т. д.).
Программы для проектирования адаптируются под все технологическое оборудование с ЧПУ. После изготовления чертежа на производственный участок выдается цифровой наряд-заказ (с прикрепленным чертежом), на основании которого начинается собственно производство режущего инструмента.
На заготовительном участке подбирается металлопрокат и раскраивается, например, на ленточно-пильном станке, на черновые заготовки (рис. 3).

В зависимости от ТУ, условий эксплуатации инструмента стальные заготовки изготавливаются из инструментальной или нержавеющей стали (рис. 4).
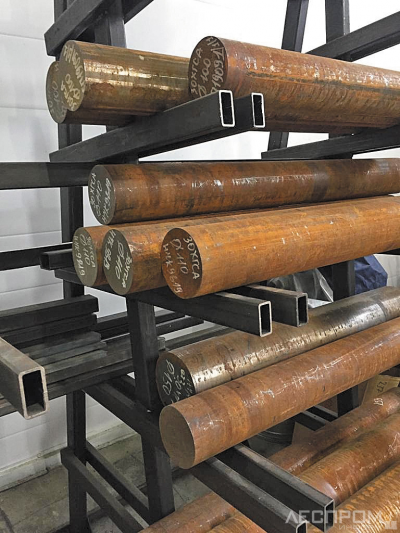
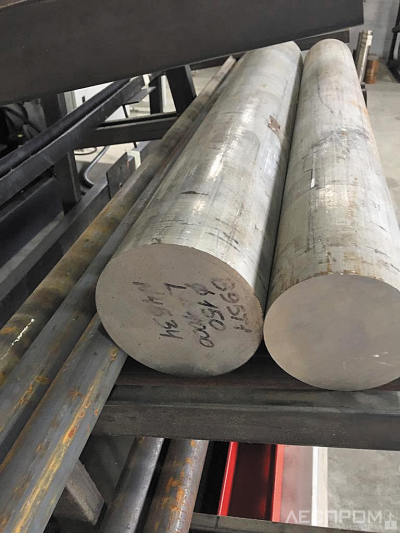
Далее мерные заготовки направляются на участок токарной обработки, оснащенный токарными 3D-станками с ЧПУ (рис. 5), на которых выполняется полная токарная обработка заготовки фрезы. После инструментального контроля всех размеров заготовки поступают на участок фрезерной обработки корпуса фрез.
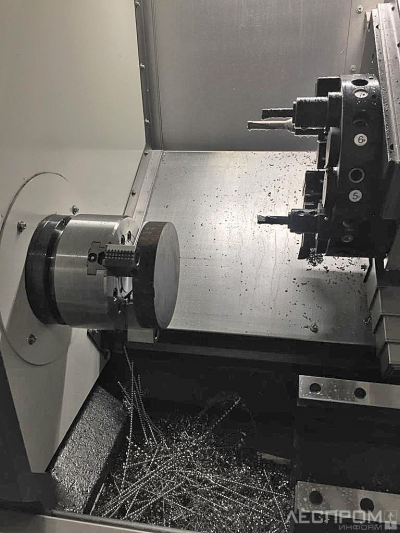
Фрезерный участок может быть оснащен современными фрезерными станками (3D–6D) с ЧПУ, которые позволяют обрабатывать наружную поверхность корпуса фрезы и дорабатывать посадочные отверстия, например, выполнять шпоночные пазы (рис. 6). На фрезерных станках 6D можно без использования токарного станка полностью изготовить корпус не только насадной, но и концевой фрезы, однако для серийного (поточного) производства их производительности недостаточно.
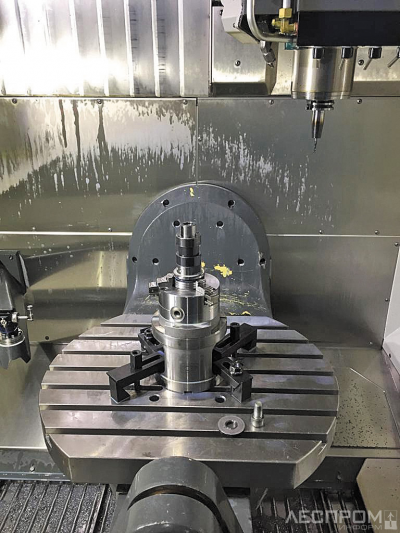
В результате вышеперечисленных операций получаются заготовки корпусов фрез (рис. 7), которые при необходимости направляются на галтовку (удаление заусенцев, мелких дефектов и т. п.).
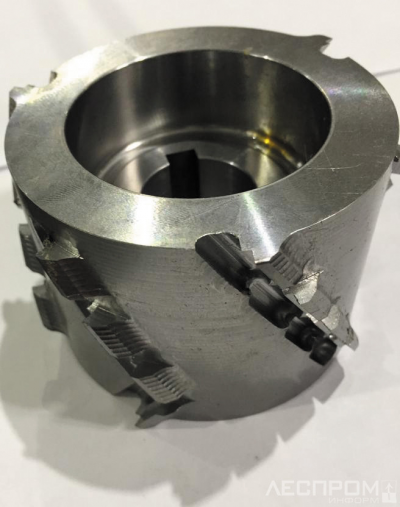
После галтовки заготовки пос- тупают на участок закалки, где сталь корпуса фрезы приобретает требуемую технологическую твер- дость.
На участке пайки с ТВЧ, как вручную, так и на полуавтоматическом оборудовании на корпуса фрез напаиваются алмазные пластины (рис. 8). Затем заготовки проходят пескоструйную обработку (рис. 9).
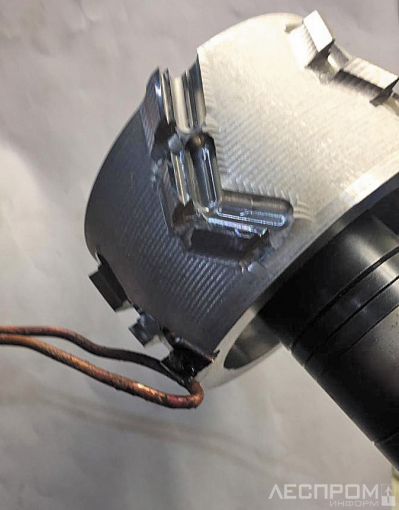
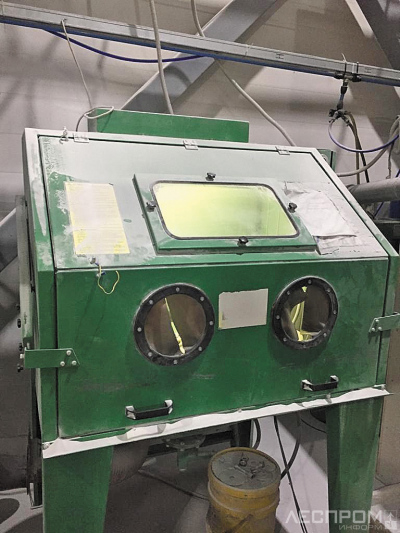
Далее выполняется электроэррозионная заточка и профилирование режущих элементов фрез (рис. 10) и проводится оптический контроль соответствия параметров фрез чертежу.
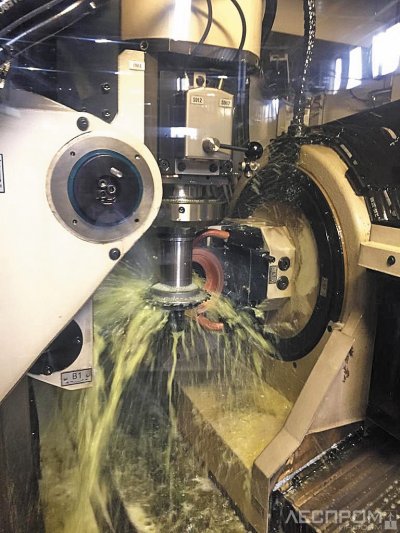
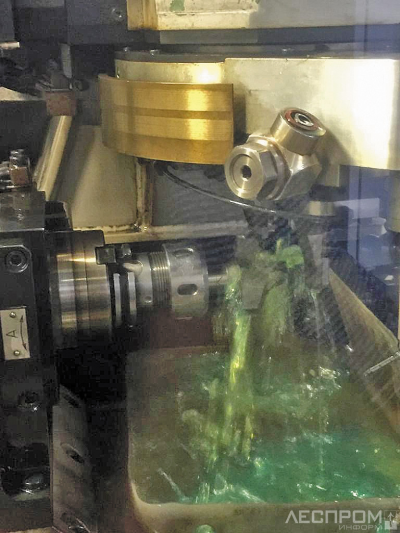
После всех этих операций фрезы массой более 200 г подлежат обязательной или выборочной динамической балансировке на специальном станке (рис. 11).

На готовые фрезы иногда наносится покрытие и методом шелкографии или лазерной гравировки на корпусе отпечатывается логотип фирмы и маркировка. Упакованный инструмент отправляется на склад.
Это лишь примерный перечень технологических этапов, который может быть изменен в зависимости от применяемого оборудования, расходных материалов и квалификации работников.
Текст Владимир Падерин