О сушке ламелей из древесины дуба
Деревообработчики хорошо знают о существенных различиях в работе с хвойными и лиственными породами. Сегодня в России много предприятий, заготавливающих и перерабатывающих большие объемы хвойной древесины. И очень мало компаний занимаются твердолиственными породами. Такое распределение обусловлено не только ресурсами доступного для заготовки леса, но и спецификой применения древесины.

В отличие от хвойных пиломатериалов, которые широко используются как конструкционные, пиломатериалы из твердолиственных пород чаще применяются в производстве мебели, окон и дверей, паркета. Одной из самых ценных пород для их изготовления считается дуб.
На протяжении веков древесину дуба высоко ценили плотники, без нее не обходились в кораблестроении, кроме того, ее экспортировали. К сожалению, за последние 50 лет состояние дубовых насаждений в России значительно ухудшилось. В центральной части страны заготовка дуба ведется в основном в Теллермановском лесном массиве и Шиповом лесу (Воронежская область). Дубом также активно занимаются на Северном Кавказе, преимущественно в Адыгее.
Для распиловки заготовленной древесины чаще всего используют ленточно-пильные станки. Во-первых, они, в отличие от круглопильных систем, обеспечивают небольшую толщину пропила, что позволяет повысить полезный процент выхода пиломатериала. Во-вторых, дают возможность работать с бревнами большого диаметра, а дубовые нередко больше 40–50 см. Получаемые при распиловке материалы часто необрезные. При пилении теряется немало материала – сегодня трудно найти высококачественный пиловочник, много внутренних пороков древесины, так что полезный выход от одного бревна нередко меньше 35%. После сушки изготовление конечных изделий из полученных таким образом пиломатериалов представляется довольно сложной задачей.
Дубовая древесина имеет кольцесосудистую структуру, основными путями транспортировки влаги внутри служат сердцевинные лучи, объем которых может достигать 28–32% объема ствола. Древесина дуба подвержена растрескиванию и цветовому окрашиванию. Сегодня для получения качественной продукции из дуба при производстве столярных изделий и паркета все чаще применяют специальные тонкорезные ленточно-пильные станки, позволяющие получать ламели толщиной от 4 мм. Такое использование пиломатериалов экономически обосновано ввиду высокой рыночной стоимости дубовой древесины. При производстве паркета такие ламели используют в качестве лицевых панелей.
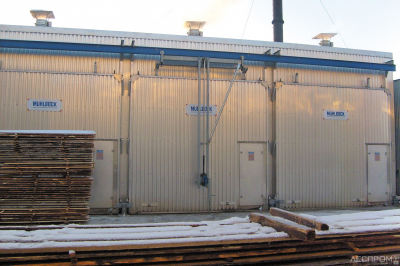
Сушка дубовых ламелей сильно отличается от сушки толстых пиломатериалов не только продолжительностью, но и режимами. Для пиломатериалов больших сечений традиционно используют низкотемпературную сушку. Высокая температура в начале процесса может вызвать образование внутренних трещин, которые обнаружатся только при последующей механической обработке. Большое значение имеет и скорость циркуляции сушильного агента. Дубовая древесина очень плотная. Влага в ходе сушки подтягивается к поверхности медленно, при попытке интенсифицировать этот процесс в конвективных сушильных камерах с принудительной циркуляцией, чаще всего используемых для промышленной сушки пиломатериалов из дуба, возникает риск пересушивания поверхности и образования так называемой корки. Именно поэтому мощность удаления влаги в камерах для сушки толстых пиломатериалов твердолиственных пород часто не больше 2 л/ч, тогда как для работы, например, с хвойными породами она достигает 6,0–7,5 л/ч. Так как цикл сушки дуба очень продолжительный, для экономии электроэнергии камеры оснащают системой частотного регулирования скорости вращения вентиляторов.
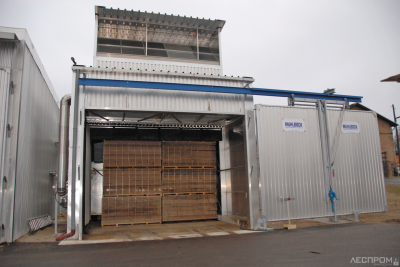
Для сушки ламелей проектируются специализированные сушильные камеры небольшого полезного объема загрузки, но с очень высоким показателем мощности удаления влаги – до 18 л/ч. На рис. 2 и 3 представлены две сушильные камеры. Слева камера, спроектированная для сушки материалов больших сечений, в ней установлены четыре вентилятора с диаметром крыльчатки 800 мм, мощность калориферов всего 300 кВт. При этом полезный объем загрузки доской толщиной 32 мм составляет 35 м3. Время сушки до 8% влажности в такой камере зависит от начальной влажности пиломатериалов и составляет от 26 до 36 суток. Камера справа предназначена для сушки ламелей. Цикл сушки ламелей толщиной 5,5 мм всего около 48 ч. При этом мощность удаления влаги 12 л/ч, а объем загрузки нетто 7 м3 древесины.
Есть отличие и в конструкции приточно-вытяжной системы. В камере для сушки ламелей циркулирует намного больший объем воздуха и скорость циркуляции значительно выше, поскольку, несмотря на высокую плотность древесины дуба, ламели отдают влагу значительно интенсивнее. Помимо этого, используется иная схема циркуляции, предусматривающая возможность одноразового использования воздуха с помощью специального клапана, смонтированного над фальшпотолком.

За счет интенсивного удаления влаги с поверхности ламелей значительно сокращается цикл сушки и минимизируется склонность дубовой древесины к растрескиванию. Расстояние, которое должна преодолеть влага при движении из центра ламели к поверхности, сравнительно небольшое, а пропускная способность сердцевинных лучей и сосудов позволяет своевременно удалить ее в процессе сушки, поэтому эффект пересушивания поверхности наблюдается редко. При эффективной работе системы управления регулируются степень открытия воздушных заслонок и скорость воздушного потока и таким образом искусственно снижается риск образования трещин. Для обеспечения равномерного распределения воздуха и направления его в штабель в таких камерах используют пакеты с перекрытым пространством под межпакетный брус (рис. 4).
Однако остается нерешенной проблема легкого окрашивания древесины дуба. В связи с этим большое внимание уделяется прокладкам, незаменимым при формировании сушильных пакетов. Многие предприятия эмпирически нашли разные интересные решения. Все они позволяют минимизировать площадь соприкосновения прокладок с поверхностью дубовых ламелей. Выбор материала прокладок для сушки ламелей вызывает множество споров, однако по экспериментальным данным, риск образования пятен определяется площадью соприкосновения с поверхностью, а не материалом. Чаще всего применяются прокладки из дерева и алюминия разной формы и толщиной не более 10–12 мм.
При использовании металлических прокладок возможно образование черных пятен, вызванное загрязнением и нерегулярной чисткой металла.
Если сушильный штабель довольно высокий, на ламелях нижнего пакета вследствие большого давления тоже могут появиться пятна. Целесообразно уменьшать высоту штабеля до оптимальной для каждого материала. Найденный оптимальный вариант можно зафиксировать распоркой на погрузочной тележке, если она используется.
Основной недостаток показанных на рисунке прокладок – необходимость укладки вручную. Но есть интересные решения по автоматизации, уже реализованные на нескольких европейских паркетных производствах. При автоматическом формировании штабеля используют специальную металлическую решетку, которая подается роботом при послойной укладке. При высокой производственной нагрузке, больших объемах переработки такая система позволяет значительно сократить время формирования пакетов и исключить человеческий фактор. Основным преимуществом алюминиевой сетки является простота укладки, равномерное распределение веса по площади слоя и минимальное соприкосновение ламелей с металлическими частями.
Еще одна особенность древесины дуба – агрессивный химический состав конденсата, выделяющегося в процессе сушки. Если в случае хвойных пород конденсат состоит в основном из кислот, смоляных веществ и полисахаридов наподобие арабиногалактановых соединений, содержащихся в лиственнице, дуб выделяет дубильные вещества, представляющие собой многоатомные фенолы. С одной стороны, дубильные вещества обеспечивают защиту древесины от влаги и гниения, с другой – это сложности для производственников, поскольку конденсат вызывает сильную коррозию ограждений сушильной камеры, которая в результате приобретает нетоварный вид, а срок ее эксплуатации сокращается. И тут камеры, изготовленные специально для сушки ламелей, также демонстрируют преимущества за счет интенсивного воздухообмена, когда почти вся влага из древесины быстро удаляется с теплым воздухом через приточно-вытяжные каналы.
Для деревообработчиков плюсы использования специального оборудования для сушки ламелей очевидны. Это и небольшие финансовые вложения в загрузку камер, объем которых редко превышает нетто 10 м3 древесины, и интенсивный воздухообмен, предотвращающий образование метиковых и внутренних трещин, и возможность оперативного наращивания объема производства путем автоматизации пакетоформирующей зоны.
В работе с дубовыми ламелями много технических тонкостей, но сегодня современные решения ведущих европейских производителей оборудования позволяют относительно быстро получать качественно высушенный материал при относительно низких финансовых рисках.
Текст Михаил Шестак, Mühlböck-Vanicek