Раскрой плит − дело тонкое! Часть 4
Проблемы раскроя плит и выбор оборудования для раскроя плит
Часть 4
В предыдущих номерах журнала («ЛесПромИнформ» № 1−3, 2009 г.) мы рассказывали об особенностях различного типа оборудования, которое используется на мебельных производствах для раскроя плит. О том, когда такое оборудование стало широко применяться в мировой практике, а также о том, какие основные типы станков существуют, на какие особенности их конструкции следует обращать внимание при выборе станков для мебельного предприятия, − эта публикация.
После окончания Второй мировой войны Европа начала восстанавливать свое разрушенное хозяйство. Обустройство нового жилья, строившегося повсеместно бурными темпами, требовало огромного количества мебели, которое, конечно же, не могли изготовить существовавшие тогда мелкие столярные мастерские, производившие изделия из массива древесины практически вручную.
Это послужило социальным заказом для организации изготовления мебели в промышленных масштабах и создания новой отрасли − мебельной промышленности.
но оказалось, что для изготовления мебели в громадных объемах не хватает высококачественной древесины. Тогда вспомнили о новом в то время материале − древесно-стружечной плите (ДСП), первый завод по производству которой был запущен в Германии в 1942 году.
Её использование заставило в корне изменить конструкцию изделий корпусной мебели, технологию их производства и потребовало создания принципиально нового специального оборудования. Многие из найденных тогда технических решений применяются до сих пор.
Понятно, что при раскрое полноформатных древесно-стружечных плит ручные пилы, ручной механизированный инструмент, станки круглопильные с кареткой или вертикальные станки не могут обеспечить производительности, достаточной для крупного производства, и применяются в основном на небольших предприятиях или как оборудование, дополняющее станки с высокой производительностью.
Станки для раскроя плит портального типа
Сначала для раскроя плит применялись специализированные многопильные станки. На мебельных предприятиях СССР использовался станок для форматной обрезки пачек фанеры мод. ЦТ3Ф, разработанный ещё в 1954 году и выпускавшийся практически без изменений до конца 1980‑х. У станка имелся рабочий стол, перемещавшийся в продольном направлении, и расположенный поперек него портал, на котором были установлены три пильных суппорта: два для продольного пиления и один для поперечного. При работе станка (рис. 1а) пакет плит, уложенный на стол, обрезался двумя пилами с двух сторон, после чего суппорты автоматически сближались, и при втором ходе стола пакет раскраивался на три полосы. При следующем рабочем ходе стола третий суппорт производил обрезку этих полос по длине и их поперечный раскрой на пачки заготовок заданного размера. Недостаток такого оборудования заключался в том, что на нем невозможно было осуществлять смешанный раскрой плит на заготовки, а это существенно снижало полезный выход материала.
Более совершенная конструкция была у аналогичного станка мод. S50 немецкой фирмы Schwabedissen («Швабедиссен»), стол которого состоял из двух частей, которые могли смещаться относительно друг друга (рис. 1б). При этом после продольного раскроя пакета плит на три полосы две из них оставались на одной из этих половин, а третья − на другой. Взаимное смещение частей стола позволяло за один ход поперечной пилы производить раскрой полос со смещенными резами и выполнять более экономичный смешанный раскрой.
Ещё одна конструкция станка портального типа мод. Teutoburger, в котором раскрой производился всего одной пилой, также была разработана немецкой фирмой Schwabedissen. В этом станке стол оставался неподвижным, а продольное перемещение относительно него совершал портал, на котором был установлен пильный суппорт, перемещавшийся вдоль балки портала − поперек стола. Причем пила могла поворачиваться вокруг вертикальной оси. Это давало возможность производить не только продольные и поперечные резы, но и резы под любым углом. Стол станка также состоял из двух частей (половин), что обеспечивало выполнение смешанного раскроя.
Основной недостаток всех станков подобного типа − длительное и сложное формирование пакетов раскраиваемых плит на столах. Эта операция плохо поддается механизации, занимает много времени и существенно снижает производительность станков.
Многопильные станки с перемещением плиты
Поэтому в начале 1960‑х годов были разработаны многопильные станки для раскроя плит не в пакетах, а по одной. Раскрой осуществлялся так: плиты надвигались на неподвижно расположенные пилы. Наиболее известна конструкция таких станков, впервые предложенная немецкой фирмой Anthon, ставшая прототипом отечественного станка мод. ЦТМФ и созданной на его основе линии раскроя плит мод. МРП (рис. 2, а). ЦТМФ был оснащен автоматическим питателем для поштучной подачи плит из стопы в поперечном направлении, пильным суппортом для продольного раскроя плиты на полосы и десятью (!) пильными суппортами для поперечного раскроя плит на заготовки заданного размера. Причем положение поперечных суппортов настраивалось заранее, и они включались в работу группами, в зависимости от предусмотренного картой раскроя положения резов относительно каждой полосы плиты. Из-за этого считалось, что станок имеет программное управление.
Другая, совершенно оригинальная схема многопильного станка для раскроя плит по смешанной схеме была предложена немецкой фирмой Torwegge («Торвегге»). Обрезка плит по ширине в продольном направлении производилась сразу четырьмя пилами, после чего одна полоса направлялась на поперечный раскрой сразу несколькими пилами вправо, а две другие − влево (рис. 2, б). Полученные детали поступали на рольганги и укладывались в стопы. Из-за сложности конструкции станка эта схема распространения не получила.
Общие недостатки всех многопильных станков для раскроя плит − высокий уровень шума и большое количество инструмента, участвующего в работе. Но главное − невозможность получения заготовок с высокой точностью размеров. Поэтому такие станки применялись для раскроя необлицованных плит, а полученные заготовки снабжались припусками от 7 до 15 мм на сторону, которые удалялись при форматной обрезке после облицовывания пластей.
Станки с прижимной балкой
В 1957 году австрийской фирмой Schelling («Шеллинг») был создан станок для горизонтального раскроя плит с движущимся пильным суппортом, а в следующем году итальянская компания Giben («Джибен») сообщила о получении патента на станок для раскроя плит, оснащенный прижимной балкой, ставший прототипом всех остальных станков этого типа. В 1970 году немецкая фирма Holzma («Хольцма») усовершенствовала такой станок и получила патент на механизм подачи пакета плит с системой ЧПУ.
Именно эта конструкция до сего дня является основной в подавляющем большинстве станков, производимых во всем мире. Причем в середине 1970‑х такие станки были разработаны и в СССР (мод. ЦРЛ20 и ЦРЛ40), а на их основе − линия раскроя облицованных плит мод. МРП1, оснащенная системой автоматической сортировки по размерам и укладки раскроенных пачек деталей в стопы.
в соответствии с принятой в нашей стране классификацией это оборудование называют станками для раскроя плит с прижимной балкой.
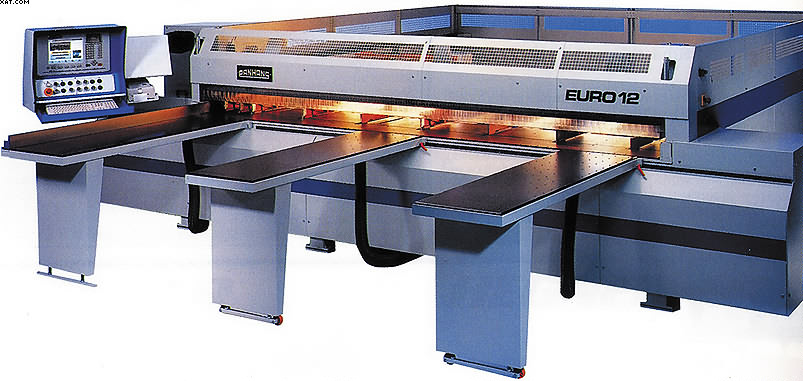
Рис. 3. Станок для раскроя плит с прижимной балкой
По технологической схеме все известные сегодня станки такого типа практически одинаковы и отличаются только конструктивным исполнением (рис. 3).
Они включают в себя сварную станину, стол, пильный суппорт, перемещаемый по длинным горизонтальным направляющим, привод перемещения суппорта, прижимную балку с механизмом вертикального перемещения, упорную линейку, упор для прижима к ней раскраиваемого пакета с механизмом его перемещения и программируемый толкатель, обеспечивающий продвижение раскраиваемого пакета плит или отрезанных от него полос на расстояние, задаваемое системой ЧПУ в зависимости от карты раскроя.
Суппорт станка для раскроя плит с прижимной балкой (рис. 4) имеет основной пильный шпиндель с самостоятельным приводом от электродвигателя (посредством клиноременной передачи) и дополнительный подрезной пильный агрегат с отдельным электродвигателем или приводимый во вращение от основного также посредством клиноременной передачи. Рабочий ход и возврат (обратное перемещение) всего суппорта по направляющим осуществляются специальным механизмом подачи с помощью втулочно-роликовой цепи или троса. Регулирование скорости подачи производится посредством механического вариатора или за счет изменения скорости вращения электродвигателя. Шпиндели основного и подрезного пильных агрегатов имеют возможность вертикального перемещения по отдельным направляющим, установленным на суппорте. Шпиндель основного − для настройки на толщину раскраиваемого пакета плит и опускания пилы при возврате суппорта в исходное положение; подрезного − для регулирования глубины пропила при подрезке прилегающей к столу пласти нижней детали в пакете или для отключения подрезки без снятия подрезной пилы. В более дорогих моделях станков регулирование высоты положения пил производится от отдельных механических приводов; в более простых и дешевых − вручную, ступенчато, с использованием заранее настроенных упоров. Обе пилы закрыты приемниками, подсоединяемыми к системе пневмоудаления отходов посредством длинного гибкого шланга.
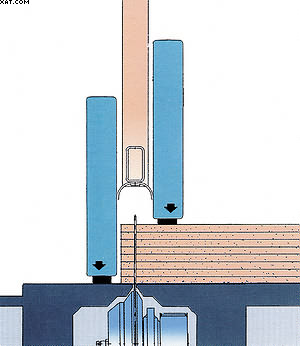
Рис. 5. Сечение прижимной балки, составленной из двух
независимых частей
Направляющие для перемещения суппорта обычно круглые, в виде двух скалок, одна из которых несет основную нагрузку от суппорта, а вторая, поддерживающая, обеспечивает прямолинейность его перемещения строго в одной плоскости. Некоторые изготовители станков используют для перемещения пильного суппорта плоские сварные направляющие. Они имеют некоторое преимущество перед круглыми, поскольку в них трение скольжения заменено трением качения, что снижает износ. Однако такие направляющие дороже и ощутимо увеличивают цену всего станка.
Прижимная балка станка (рис. 5) имеет снизу прорезь, в которую при пилении входят зубья пилы, выступающие над пластью верхней детали раскраиваемого пакета. Образующиеся при пилении опилки отсасываются через патрубок, подсоединяемый к системе пневмоудаления отходов. Для прочного удержания пакета балка снабжается уравнивающим механизмом, исключающим её перекос.
Стол у станков простых моделей для раскроя выполняется в виде стальной плиты с прорезью для прохода основной и подрезной пил. У более дорогих, зона вдоль этой щели снабжается своего рода козырьком, который автоматически опускается после выполнения при раскрое первого и последнего реза. В результате в столе образуется довольно широкая щель, в которую падают отходы, удаляемые затем из-под стола ленточным транспортером и перемещаемые по нему в дробилку для измельчения.
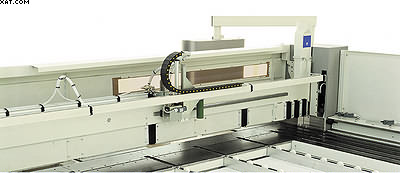
Рис. 6. Прижимная балка, стол с прорезью для прохода пилы и упорная
линейка
В станке любой модели для раскроя для обеспечения точности особое значение имеет конструкция упорной линейки (рис. 6). Если раскраиваемый пакет закрепляется ненадежно, сдвигается или гнется под воздействием усилия упора, прижимающего пакет к линейке, о качестве раскроя говорить просто не приходится. Если станок оснащен линейкой, изготовленной из алюминия, вероятность брака при раскрое весьма высока.
При работе станка пакет раскраиваемых деталей помещается на его столе под прижимной балкой. Включается перемещение выравнивающего упора, придвигающего кромку раскраиваемого пакета вплотную к продольной упорной линейке. После этого прижимная балка опускается, прижимая пакет к столу, и суппорт совершает рабочий ход, осуществляя пиление. Затем основная и подрезная пилы опускаются ниже поверхности стола, после чего суппорт на повышенной скорости возвращается в исходное положение.
Станки более дорогих моделей снабжены устройством, автоматически определяющим ширину раскраиваемого пакета и после совершения суппортом холостого хода останавливающим его в положении, наиболее приближенном к краю пакета, чтобы при проведении следующего реза длина рабочего хода была наименьшей. Одновременно с завершением холостого хода суппорта прижимная балка поднимается, и пакет освобождается.
В качестве опции практически все подобные станки для раскроя плит могут оснащаться устройством для раскроя пакета плит или деталей, имеющих неплоские, профильные в сечении кромки. К ним обычно относятся плиты и детали, кромки которых облицованы методом пост- или софтформинга. Как правило, при отсутствии такого устройства в зоне выхода основной пилы на них образуются вырывы и сколы. Принцип работы любого устройства, предупреждающего образование сколов, состоит в том, что в конце рабочего хода пильного суппорта станка подрезная пила, вращающаяся в попутном направлении, поднимается, пропиливая все кромки деталей в пакете. В результате зубья основной пилы при окончании реза выходят в пропиленный ею паз и не отрывают облицовку.
Первый рез пакета на станке называют отбеливающим. Он проводится для того, чтобы выровнять все кромки плит и создать базу для последующих резов. При выполнении резов пакет всегда продвигается вдоль упорной линейки.
Величина пути перемещения пакета обеспечивается по-разному. Так, наиболее простые (и дешевые) станки оснащаются удлиненными линейками с набором установленных на них упоров, заранее настроенных на заданные размеры. Эти упоры могут последовательно откидываться вручную или выводиться по заданной программе в рабочее положение с помощью пневмоцилиндров.
Важной характеристикой любого станка для раскроя плит является наименьшая ширина детали, остающейся в пакете при проведении последнего реза. Проблема состоит в том, что при выполнении некоторых операций по карте раскроя приходится в последнюю очередь выпиливать детали шириной меньше толщины пакета, в результате чего возникает опасность, что весь его остаток сдвинется или рассыплется. Лучшие станки обеспечивают выпиливание деталей с этим размером не более 40 мм.
станки для раскроя, получившие сегодня наиболее широкое распространение, оснащаются устройством для перемещения раскраиваемого пакета на необходимое расстояние между резами, захватывающим пакет клещевыми зажимами (рис. 7). Для того чтобы обеспечить строгую параллельность перемещения, все подобные устройства снабжены выравнивающими механизмами, включающими две зубчато-реечные пары, шестерни которых соединены между собой длинным поперечным валом. В некоторых станках зажимные клещи этих устройств выполнены таким образом, что могут зажимать и продвигать детали или плиты, имеющие свесы облицовки, не повреждая их. Задание величины последовательных ходов этого устройства производится системой числового программного управления.
Конструкция всех известных станков обеспечивает возможность их загрузки вручную спереди с использованием гладких столов, столов с воздушной подушкой или сзади при помощи подъемного стола, применяемого для автоматической загрузки пакета плит из стопы (рис. 8).
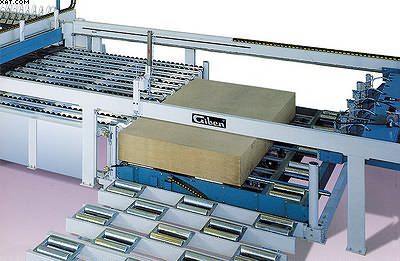
Рис. 8. Загрузчик плит с подъемным столом на задней стороне станка
для раскроя
Загрузка станка вручную трудоемка и отнимает много времени. В результате его сменная производительность не превышает 5−6 м³. Увеличению производительности примерно на 50% способствует использование предлагаемого некоторыми изготовителями загрузчика плит с подъемным столом, выдающего их на передние загрузочные столы станка.
Производительность станка для раскроя вопреки обычным уверениям изготовителей на практике определяется не максимальной толщиной раскраиваемого пакета, а количеством используемых потребителем карт раскроя. Так, при производстве мебели по индивидуальным заказам или при большой номенклатуре продукции может оказаться, что пакет максимальной толщины просто не может быть набран из-за отсутствия потребности именно в этих конкретных деталях. Тогда предприятие вместо раскроя пакета толщиной 80−100 мм бывает вынуждено раскраивать пакет из двух плит или даже всего одну плиту. Это снижает фактическую производительность участка раскроя и приводит к тому, что затраты на уже купленный дорогой станок оказываются неэффективными. Предприятие могло бы обойтись другим, более дешевым оборудованием, рассчитанным на меньшую толщину раскраиваемого пакета. Как показывает опыт, такая ситуация встречается, к сожалению, довольно часто, и многие предприятия, не учтя её вовремя, вынуждены приобретать дополнительное оборудование.
Одной из опций, предлагаемых изготовителями станков для раскроя плит, является регулируемый упор, устанавливаемый на столе станка и обеспечивающий пиление под углом к кромке заготовки. Некоторые производители снабжают станки дополнительными упорами, дающими возможность выпиливать с их помощью непрямоугольные (косоугольные) детали с точными размерами без предварительной разметки заготовок.
Стоимость базовых моделей станков определяется не только наибольшей толщиной раскраиваемого пакета (обычно 60, 80 и 100 мм, у некоторых моделей, изготавливаемых по спецзаказу, − 350 мм и более), но и величиной наибольшего хода суппорта, определяющей максимальную ширину раскраиваемого пакета (обычно она соответствует определенному ряду, одинаковому практически у всех изготовителей: 3200, 3800, 4200 мм и более). При выборе рабочей ширины не стоит перестраховываться, так как даже без учета подстопных мест минимальная площадь, занимаемая станком, составляет приблизительно 6 х 6 м. увеличение рабочей ширины только на 500 мм отнимает не менее 3−4 м² площади цеха.
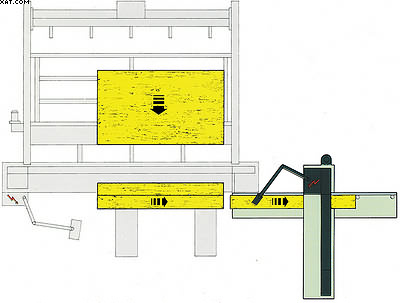
Рис. 9.Линия раскроя на базе двух станков с прижимной балкой, с ручной
передачей полос между станками
У некоторых изготовителей оборудования имеются и станки с рабочей шириной 1300 мм, чаще всего применяемые для раскроя полос с облицовкой из пластика, с кромками, облицованными методом постформинга. По сравнению со станками с шириной, например, 4200 мм они почти вдвое дешевле. Такое оборудование можно использовать для раскроя на детали полос, выпиленных на первом станке с большей рабочей шириной, передавая их между загрузочными столами станков вручную. В результате с минимальными затратами может быть получена полуавтоматическая линия, имеющая большую производительность, чем два отдельных станка, каждый из которых работает только по своей карте раскроя (рис. 9).
Станки для раскроя плит с прижимной балкой в последние полтора десятилетия полностью вытеснили применявшиеся в конце 1980‑х годов многопильные станки. Они производят меньше шума, не требуют высоких затрат на режущий инструмент, проще в настройке и обслуживании, обеспечивают высокую точность выпиленных деталей, достаточную для их использования без последующей форматной обрезки и т. д.
Эти станки или линии, построенные на их базе, − основа современного мебельного производства, и без них не может обойтись ни одно предприятие. Но, чтобы не совершать ошибок при выборе оборудования, нужно сначала хорошо изучить не только все их возможности, но и конкретные потребности того производства, на котором они будут использоваться.
Сергей НИКИТИН, компания «МедиаТехнологии»,
по заказу журнала «ЛесПромИнформ»
Статьи из цикла «Раскрой плит — дело тонкое!»:
Раскрой плит – дело тонкое! Проблемы раскроя плит и выбор оборудования для раскроя плит. Часть 1
Раскрой плит – дело тонкое! Проблемы раскроя плит и выбор оборудования для раскроя плит. Часть 2
Раскрой плит – дело тонкое! Проблемы раскроя плит и выбор оборудования для раскроя плит. Часть 3