Новая разработка компании Siempelkamp
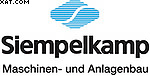
Технология производства изоляционных древесно-волокнистых плит
Изоляционные древесно-волокнистые плиты (ИДВП) — один из первых материалов, который был разработан именно для изоляционных целей. Технология их производства берет свое начало от папье-маше. На технологию по папье-маше англичанину Клэю (Clay) был выдан патент в 1772 году.
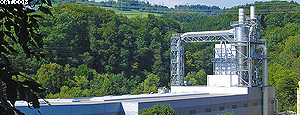
В Европе первые изоляционные древесно-волокнистые плиты были выпущены в 1932 году в Германии на заводе, который работает до сих пор. Но в 1937 году у изоляционных древесных плит появились конкуренты в виде таких материалов, как минеральные волокна и стекловолокна, а немного позднее и различных продуктов из пенопласта. Минеральное волокно не горит, а синтетические пенопласты обладают низкой теплопроводностью. Поэтому уже тогда можно было предположить, что доля ИДВП на рынке сбыта уменьшится.
Но этого не произошло. Данный материал не был вытеснен с рынка по разным причинам. Если вы помните, некоторое время назад в обществе долго дебатировалось предположение врачей, что применение минерального волокна в строительстве может приводить к раковым заболеваниям. В результате состав волокна был изменен, что позволило сделать продукт биологически разлагаемым. Дебаты сыграли важную роль ещё и потому, что они помогли сохранить изоляционные древесно-волокнистые плиты как материал.
ИДВП характеризуется целым рядом технических преимуществ. Древесина как материал обладает высокой удельной тепловой мощностью, которая примерно в 2,5 раза больше, чем у минеральных материалов или стекла. Это означает, что в теплое время года стены дома, для изоляции которых использованы изоляционные древесно-волокнистые плиты, могут поглощать в течение всего дня большое количество тепла, не пропуская его в помещения, а ночью это тепло выделяется наружу. В результате комнатная температура в доме, изолированном плитами ДВП, значительно ниже, чем температура в домах, которые изолированы плитами из минерального волокна, что позволяет экономить на затратах на энергию для кондиционеров. Кроме того, древесина может поглощать влагу из воздуха или выделять её, почти не изменяя при этом свои изоляционные свойства. Это свойство материала позволяет использовать ИДВП в концепциях стен, которые являются диффузионнооткрытыми. В результате отпадает, например, необходимость в паронепроницаемом слое, минимизируется проблема с накапливанием конденсата в стенах, и помещение может «дышать».
Все это служит объяснением, почему растет количество потребителей изоляционной ДВП, несмотря на то что по сравнению с другими изоляционными материалами ИДВП занимает, например, на рынке Германии менее 5% от общего объема (24 млн м в год). Таким образом, потребители голосуют за полноценный, экологически чистый и возобновляемый продукт.
Цель новой разработки Siempelkamp
Так называемый мокрый способ изготовления ИДВП — технология вчерашнего дня, у которой имеются значительные недостатки:
- плиты можно выпускать толщиной только примерно до 25 мм;
- плотность нельзя снизить ниже примерно 150 кг/м ;
- содержание влажности в плитезаготовке составляет 120−170 %. Процесс сушки (примерно 2,5 часа) крайне энергоинтенсивный.
Поэтому несколько лет назад компания Siempelkamp приняла решение создать новую технологию для производства изоляционной ДВП, которая исключает все вышеуказанные изъяны. Перед разработчиками была поставлена цель добиться следующих параметров:
- толщина плиты — от 10 до 240 мм;
- плотность — от 80 до 200 кг/м ;
- разряд материала — «экологически чистый» (потребление энергии на 30−40 % ниже, чем при производстве плит по мокрому методу, в составе нет вредных химикатов).
Описание технологии
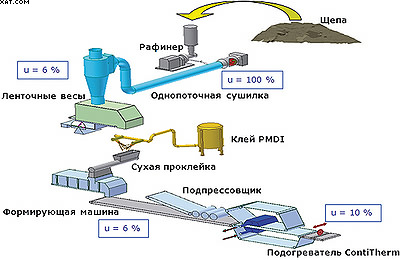
Технология Siempelkamp для производства изоляционных ДВП сухим
методом
Технологический процесс делится на следующие участки:
- приготовление волокна, сушка;
- подмешивание клея (смола);
- настил (формирование ковра);
- уплотнение;
- нагрев и отвердение;
- конечная обработка (разрез, раскрой, штабелеукладка).
Волокна получаются при обработке щепы паром в рафинере. Но в отличие от технологии изготовления MDF для достижения оптимальных свойств материала в производстве ИДВП лучше использовать относительно крупные волокна, поэтому в качестве сырья предпочитаются хвойные породы древесины.
Известная по стандартной технологии изготовления MDF проклейка до сушки волокна не могла быть применена в новой разработке по причине использования нового клея, который очень быстро затвердевает. Поэтому специалисты Siempelkamp создали новую систему, которую мы называем «сухой трубой сушилки» («сухая Blow-Line»). Речь идет о башне, на дно которой волокна подаются пневматическим способом после сушки в традиционной «мокрой трубе сушилки» («мокрой Blow-Line»). Вверху башни находится ряд форсунок, которые распрыскивают клей PMDI (Polymeres Diphenylmethan-diisocyanat) в поток падающих вниз волокон. На дне башни волокна улавливаются ситом и транспортируются механическим способом к формирующей машине.
Процесс настила осуществляется на обычных конвенциональных формирующих машинах MDF. За ним следуют подпрессовка и обрезка кромок. После уплотнения ковра до необходимой толщины нужно с помощью подогревателя ContiTherm® передать в ковер тепло, чтобы вызвать реакцию отвердения смолы.
При этом смесь из пара и воздуха вдувается в ковер при точно установленной точке росы. Как только эта смесь соприкасается с холодными волокнами, пар моментально конденсируется и отдает им свое тепло, в результате чего температура волокон поднимается до точки росы. При непрерывной подаче смеси пара и воздуха конденсаторная завеса движется по материалу и нагревает его за очень короткое время. Время выдержки в этом процессе составляет всего 10−30 секунд в зависимости от толщины и плотности ковра.
Нагрев ковра с помощью пара повышает содержание влаги в волокнах примерно на 3,5 %. В этой связи очевидно ещё одно преимущество клея PMDI: смола не содержит воду. Волокна, высушенные приблизительно до 7 %, сразу же (вместе с увлажнением в подогревателе ContiTherm® ) получают необходимую влажность — влажность плит. Поэтому дополнительной сушки не требуется. Из подогревателя ContiTherm® выходит уже готовый материал, который можно раскраивать на нужные форматы.
Свойства
Огнестойкость минеральных материалов выше, чем у органических. ИДВП не исключение. В соответствии с европейскими стандартами EN 13501−1 изоляционные ДВП относятся к классу E.
При изготовлении новой плиты, у которой плотность ниже приблизительно 130 кг/м , в массу необходимо добавлять противопожарное средство (например, полифосфат), которое подается в трубу сушилки за рафинером.
При производстве ИДВП, которые будут применяться для устройства кровель, необходимо (как и в технологии изготовления плит MDF) использовать парафиновую эмульсию для того, чтобы уменьшить способность плит к поглощению влаги. Эмульсию можно добавлять сразу в рафинер или в трубу сушилки непосредственно после рафинера.
Применение
Новые изоляционные ДВП, которые изготавливают по сухому методу, характеризуются меньшей плотностью и большей толщиной по сравнению с конвенциональными изоляционными плитами, производимыми по мокрому способу.
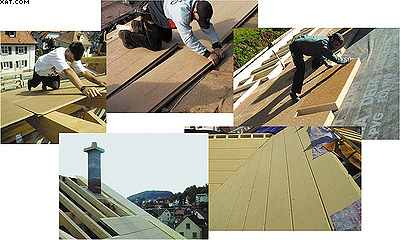
Рис. 1
Сферой, в которой ИДВП находят широкое применение в Европе, является изоляция крыш со стропильной конструкцией (рис. 1). С течением времени с целью экономии энергии требования к изоляции зданий ужесточаются, что приводит к выпуску изоляционного материала, толщина которого зачастую больше, чем высота стропил. Поэтому изоляционный материал укладывается либо под стропила (в этом случае уменьшается пространство помещения), либо на стропила (в этом случае степень уплотнения плиты должна быть достаточно высокой, чтобы выдержать нагрузку от кровельной конструкции, включая вес, например, черепицы). Изоляционные плиты, уложенные на стропила, исключают образование холодных зон, так как в этом случае вся крыша обшита сплошным слоем материала, стыки плит соединены при помощи шпунтов и гребня. При этом важным показателем является прочность плит на сжатие, так как он дает информацию о том, какой предельный вес кровельного покрытия (черепицы) они способны выдержать. Новая изоляционная древесно-волокнистая плита отлично подходит для изоляции кровельных конструкций, потому что прочность на сжатие у ИДВП с такой плотностью выше, чем у плит, изготовленных по конвенциональному мокрому способу.
Для кровельных конструкций особое значение имеет высокая термическая мощность изоляционных ДВП, так как солнечное излучение оказывает наиболее сильное воздействие именно на крыши. В помещениях, расположенных под крышей, для устройства изоляции которой применялись ИДВП, наблюдается более низкая температура по сравнению с теми помещениями, которые находятся под крышей, изолированной минеральным материалом. А это увеличивает комфортность и экономит энергию для кондиционеров.
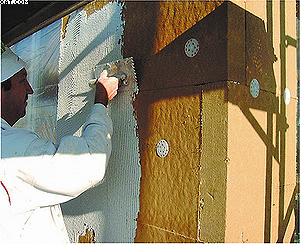
Рис. 2
Ещё одной областью применения ИДВП является устройство изоляции стен зданий (рис. 2). Типичным примером может служить специальная изоляционная соединительная система. Сегодня любая европейская фирмаизготовитель предлагает систему для так называемой термостены на базе ИДВП. Внешняя сторона этой системы состоит из диффузионнооткрытой минеральной или органической штукатурки, укрепленной матами из стекловолокна.
Кроме того, изоляционные ДВП используются и в качестве материала для стандартной изоляции внутренних и наружных стен с деревянной рамой. Плиты ИДВП обладают более высокими, чем у плит из минерального волокна, звукоизоляционными характеристиками.
В такой области применения новых плит, как устройство полов, большим достоинством этого материала является снижение ударного шума при хождении людей по полу. ИДВП укладываются под бесшовное напольное покрытие или в качестве заранее приготовленных напольных элементов, например, на гипсоволокнистой плите для сухого строительства.
Издержки производства
Издержки производства изоляционных ДВП по сухому методу Siempelkamp меньше, чем издержки производства плит, изготовленных по конвенциональному мокрому способу. Это достигается не в последнюю очередь за счет значительного снижения затрат для сушки. Да, конечно, по сравнению с некоторыми изоляционными материалами, такими как минеральное волокно и пенополистирол, издержки производства ИДВП выше — в зависимости от области применения. Но, прежде чем делать выводы, нужно в каждом конкретном случае рассматривать ту строительную конструкцию, в которой предполагается использовать ИДВП, в целом. Так, например, при применении для устройства подвесного потолка древесно¬волокнистой плиты, которая служит в качестве водоотводного слоя под кровельным покрытием, отпадает необходимость в дорогостоящей конструкции из тканевой пленки.
Разработка нового метода
Технология для производства ИДВП была разработана между 2002 и 2004 годом в научно-исследовательском и экспериментальном центре компании Siempelkamp с использованием прототипов сухой трубы сушилки («сухой Blow-Line») и подогревателя ContiTherm® .
Промышленное применение
Первая промышленная установка была продана в 2004 году немецкому производителю изоляционных ДВП, фирме Gutex, основанной в 1932 году и расположенной в регионе Шварцвальд на юге Германии. Интересно, что Gutex вообще первое предприятие в Европе по выпуску ИДВП. Ширина плит, изготавливаемых здесь, составляет до 2,6 м. Производительность завода — 460 тыс. м в год (для плит с минимальной плотностью). На рис. 3 показан предварительно уплотненный ковер, который поступает в ContiTherm® , где происходит нагрев, калибровка и отвердение смолы. После этого бесконечная плита разрезается с помощью диагональной пилы на плитызаготовки, раскраивается на окончательный размер и укладывается в штабели на линии конечной обработки.
Строительство нового завода началось в середине 2005 года, в эксплуатацию он был введен в феврале 2006. В июне того же года линия перешла на трехсменный режим работы. В настоящее время установка работает при полной загруженности 7 дней в неделю в 4 смены. Спрос на новый продукт не снижается.
Дальнейшие разработки: гибкие плиты
Для тех областей применения, где изоляционный материал укладывается между существующими строительными элементами, например между стропилами, требуется продукт, который может компенсировать стандартные строительные допуски. То есть нужна гибкая плита, которую можно закрепить между стропилами. Поэтому специалисты Siempelkamp продолжили свои разработки и усовершенствовали технологию изготовления ИДВП по сухому методу для того, чтобы можно было выпускать такой материал.
Гибкие изоляционные древесно-волокнистные плиты производятся с применением так называемых двухкомпонентных волокон. Речь идет о расплавленных пластмассовых волокнах с тугоплавким ядром и низкоплавкой оболочкой. В процессе производства оболочка нагревается до точки плавления и представляет собой «клейковину», с помощью которой двухкомпонентные волокна соединяются между собой и с древесными волокнами. Другой клей (например, PMDI) больше не требуется.
Таким образом компания Siempelkamp углубила разработку сухого метода так, чтобы на одной и той же установке можно было выпускать как твердые, так и гибкие плиты. На пилотной линии в научно-исследовательском и экспериментальном центре Siempelkamp эта технология уже успешно верифицирована (рис. 4)!
Для организации процесса изготовления гибкой плиты требуется немного дополнительного оборудования. Двухкомпонентные волокна доставляются в виде тюков, которые развязываются с помощью специальных машин. Для интенсивного перемешивания двухкомпонентных волокон с деревянными волокнами используется специальная смесительная система, с помощью которой достигается гомогенная смесь. Последующая технологическая цепочка схожа с цепочкой производства твердых плит на базе клея PMDI, то есть из волоконной смеси механическим способом формируется ковер, который уплотняется до конечных размеров в подогревателе ContiTherm® и подогревается с помощью смеси из пара и воздуха до температуры плавления.
Затем плита, ещё в момент калибровки, охлаждается с тем, чтобы зафиксировать состояние уплотнения. Гибкие плиты характеризуются плотностью в диапазоне между 40 и 70 кг/м и имеют толщину в диапазоне между 40 до 240 мм. Они применяются в основном для устройства изоляции между стропилами крыш и для изоляции стен между стойками конструкции, состоящей из деревянных каркасов. В зависимости от плотности и толщины этих плит можно достичь суточной производительности в 1350 м и выше.
О компании Siempelkamp
Группа Siempelkamp — это машиностроительное предприятие, выпускающее высокоразвитое технологическое оборудование и состоящее из трех главных подразделений: машиностроение, литейная техника и ядерная техника. Siempelkamp является лидером на международном рынке по поставке линий прессования и комплектных установок для промышленности по выпуску древесных материалов. Кроме этого, группа Siempelkamp известна как поставщик крупногабаритных заготовок ручного литья весом до 300 т, а также как поставщик контейнеров CASTOR® для ядерной техники.
Оборот группы в 2008 году составил 502 млн евро. С учетом представительств и дочерних предприятий во всем мире в ней занято 2745 сотрудников.