У зеркала два лица
У производителей поддонов в 2009 году были непростые времена: кризис отрицательно сказался на спросе на продукцию. Многим участникам рынка пришлось пересмотреть свое отношение к способам производства поддонов, вопросам эффективности работы, уделить внимание снижению себестоимости продукции. О том, какие шаги для оптимизации производства следует предпринимать в этот нелегкий период, нашему корреспонденту Ольге Мамаевой рассказал заместитель директора ТД «Пневмо-Электро» Владимир Мороз.
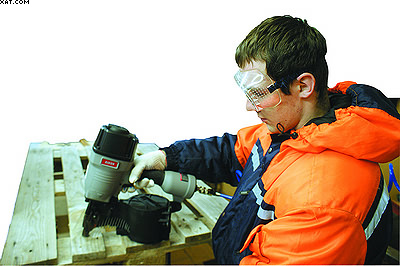
Конечно, в такой работе надо брать на вооружение опыт тех, кто давно и прочно обосновался на рынке. Стратегия развития крупных европейских предприятий, выпускающих поддоны, предполагает использование автоматизированных (а в идеале роботизированных) линий по их производству. При этом важно учитывать и культуру европейских производителей, и жесткие требования, предъявляемые ими к качеству заготовки и крепежа. Наконец, немаловажным фактором является и стоимость рабочей силы. Бесспорно, российским производителям поддонов нужно стремиться к этому уровню. Но, зная действительность, мы можем сказать, что отечественному производителю до этого пока далеко. Всякому, кто желает завоевать твердые позиции на рынке, изначально следует исходить из того, что поддон в России — товар дешевый. Европоддон, изготавливаемый на автоматизированных линиях, — продукт хоть и качественный, но дорогой (в России цены на европоддоны в два раза выше, чем на обычные). Поэтому надо обеспечить выполнение сразу нескольких обязательных условий. Во-первых, придерживаться жестких требований к качеству материала, из которого делаются поддоны, то есть добиться от отечественных поставщиков древесины того, чего сегодня они не могут обеспечить в 80 случаях из 100. Во-вторых, найти источник поставок сырья неподалеку от места производства. Наконец, надо решить такую проблему, как отсутствие качественных расходных материалов, ведь качество крепежа очень сильно сказывается на производительности. Конечно, в России есть несколько крупных изготовителей поддонов, эксплуатирующих полностью автоматизированные линии, но и они, столкнувшись с проблемами, вызванными кризисом, вынуждены искать такие решения, которые бы позволили сохранить производство и его объемы.
Кризис подтолкнул тех, кто раньше занимался первичной обработкой древесины — заготовкой, распиловкой, продажей доски, к поиску новых решений для своего бизнеса. Сегодня предприятия начинают выпускать поддоны из остатков ликвидных досок, древесины второго сорта. Одновременно в условиях кризиса многие предприятия, которые раньше осуществляли перевозку грузов только на европоддонах, уже перешли на использование в грузообороте обычных поддонов.
Практически во всех случаях стало экономически невыгодно производить поддоны собственными силами. И использование полностью автоматизированного оборудования оказалось не совсем приемлемым решением для большинства предприятий России, поскольку его стоимость и стоимость его обслуживания намного превышают возможности средних и малых предприятий, которые в 2008–2009 годах стали основными поставщиками поддонов на рынок.
В начале 2010 года наблюдается оживление спроса на дешевые поддоны, причем конкуренция в этой области очень сильная. Спрос на европоддоны в России в 2009 году сильно упал, равно как и цена на продукцию. У многих производителей возникла сложная ситуация со сбытом (особенно прошлой зимой) — рынок был перенасыщен. Произошло так называемое перезатаривание поддонных производств. Готовая продукция не находила своего потребителя. Многие заводы стали останавливаться, следовательно, спрос на поддоны падал. В результате объемы накопленных на складах поддонов даже сейчас намного превышают покупательский спрос.
Кризис показал, что нужно делать дешевые поддоны. При этом требования к их качеству никто не отменяет, но себестоимость поддонов должна быть как можно ниже. Снижение себестоимости можно обеспечить за счет использования дешевых материалов либо увеличения количества производимых поддонов. И здесь нужно применять эффективное оборудование. Например, пневматический гвоздезабивной инструмент помогает существенно увеличить производительность при уменьшении затрат на производство. На предприятии, где изготавливали 10 тыс. поддонов в месяц, при использовании пневмоинструмента без увеличения числа работников можно добиться повышения производительности на 70%. Это подтверждено практикой! Соответственно, мощность производства составляет уже 17 тыс. поддонов в месяц. Пневматические инструменты увеличивают скорость совершения тех или иных операций в 4–10 раз по сравнению с теми предприятиями, где применяется ручной труд. Можно выделить следующие плюсы приобретения и использования пневмоинструментов:
- невысокая цена на расходные материалы (например, гвозди);
- простота настройки и обслуживания;
- увеличение скорости рабочего процесса (в сравнении с ручным трудом);
- снижение себестоимости продукции за счет увеличения количества изготавливаемых поддонов и снижения косвенных издержек (уменьшения платы за изготовление единицы изделия);
- возможность организации выпуска многоразовых поддонов, сертифицированных европоддонов, дешевых одноразовых поддонов;
- «утапливание» шляпки гвоздя без использования дополнительных приспособлений;
- отсутствие необходимости перестраивать инструмент для выпуска других видов поддонов или деревянной тары (ящиков, коробов);
- возможность использования дешевой древесины с большими допусками точности изготовления заготовок.
Учитывая названные выше факторы, можно сделать вывод, что в ближайшее десятилетие альтернативой пневмоинструментам, используемым для изготовления поддонов (и не только), может быть лишь… ручной молоток.
Но для тех, кто активно ищет пути оптимизации производства даже в такое трудное время, как сейчас, и стремится укрепить свои позиции на рынке производства деревянных поддонов, выбор очевиден.
Ольга МАМАЕВА