Выходной контроль качества плитной продукции
Контроль качества продукции заключается в оценке соответствия определенных характеристик плит установленным нормативам. Действующие в Российской Федерации стандартные методы испытания плит разработаны до 1990 года и во многом уже не отвечают современному уровню развития отрасли. В этой публикации приводятся не только отечественные методы испытаний, но и методы, предусмотренные в европейских стандартах (EN).
Компоненты древесных плит
Прессы для изготовления древесных плит
Технологические параметры горячего прессования плит
Послепрессовая обработка древесных плит
Входной и текущий контроль качества продукции на плитных производствах
Древесные плиты в строительстве
Эти удивительно полезные ДВП
Материалы ДПК: долговечность, прочность, качество
древесных плит
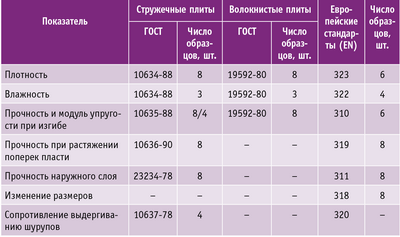
Сегодня в РФ действуют система государственных стандартов на методы испытаний стружечных плит и ГОСТ 19592-80 на методы испытаний волокнистых плит. Европейские стандарты едины для всех видов плит, включая MDF и OSB. Для испытаний из контролируемой партии продукции отбирается определенное стандартом количество плит, из которых выпиливаются образцы. Объем испытуемого материала обычно составляет от 0,1 до 0,5% от числа листов в партии. Выборку стараются делать по возможности минимальной, так как плиты, из которых взяты образцы, обычно исключаются из поставки. Перечень контролируемых показателей и минимально допустимое количество образцов (n) приведены в табл. 1.
Все испытания следует проводить с образцами, выдержанными в лабораторных условиях, то есть при температуре воздуха 20°С и относительной влажности воздуха 65%, до состояния, при котором массу образца можно считать стабильной. Проведение испытаний возможно как в собственной лаборатории предприятия, так и в сторонней организации.
Плотность изделий
Плотность изделий, которая в плитном производстве измеряется в килограммах на кубический метр, определяют по образцам размером 100 х 100 мм с точностью не ниже 0,1%. Расчеты ведут по формуле:
где m - масса образца, г; l, b, h - размеры образца, мм.
В лабораторных условиях при отработке технологии также исследуют профиль плотности по толщине плиты с помощью специальных приборов - денсиметров, или путем измерения сопротивления сверлению в наружных и внутреннем слоях плиты.
Влажность плиты
Влажность плиты должна соответствовать равновесной влажности, определяемой влажностью и температурой окружающего воздуха. Для плит класса interior, то есть используемых внутри помещений, климатические условия эксплуатации соответствуют условиям жилых и иных закрытых помещений с влажностью от 40 до 60% и температурой около 200 0C. Этим условиям соответствует равновесная влажность древесины 6-9%. Уровень влажности определяют путем полного высушивания образцов размером 50 х 50 мм в сушильном шкафу при температуре 103 0C до достижения полностью стабильной массы (для ориентировочных опытов можно использовать образцы и меньших размеров). Влажность рассчитывают по формуле:
где m1 - масса образца до высушивания, г;
m2 - масса образца после высушивания, г.
Прочность плит при изгибе
Ее проверяют по схеме, показанной на рис. 1, и рассчитывают как отношение изгибающего момента (М) к моменту сопротивления поперечного сечения образца (W) в момент приложения максимальной (разрушающей) нагрузки. Для образца прямоугольного сечения прочность вычисляется по формуле
где Рmax - разрушающая нагрузка, Н; l - расстояние между опорами, мм; b - ширина образца (50 мм); h - толщина (высота) образца, равная толщине продукции, мм.
Испытание образца до разрушения надо проводить в течение примерно одной минуты. Расстояние между опорами должно составлять 20h согласно требованиям европейского стандарта -и 10...15 h - в соответствии с отечественным стандартом для ДСП (h - толщина образца, мм). Такое существенное расхождение требований в цифрах затрудняет сравнение показателей плит, испытанных по разным методикам.
Поэтому целесообразно проводить испытания в соответствии с EN 310, так как эта методика позволяет получать наиболее объективную характеристику прочности плит при изгибе.
На результаты испытаний влияет объем образца (т. н. масштабный фактор), поэтому в нормативах для тонких плит указаны более высокие значения прочности.
Модуль упругости при изгибе
Его необходимо знать для оценки поведения плит под изгибающей нагрузкой, так как прогиб детали прямо пропорционален нагрузке и обратно пропорционален модулю упругости при изгибе. В европейском стандарте модуль упругости при изгибе так же обязателен, как и предел прочности при изгибе. Оба показателя могут определяться на одних и тех же образцах, по одной схеме испытания, так как Е-модуль можно определить без разрушения материала. Статический модуль упругости рассчитывают по формуле
где l - расстояние между опорами, мм (не менее 20h); b - ширина образца (50 мм); h - толщина образца (равна толщине готового изделия), мм; ΔР - приращение нагрузки, Н, соответствующее приращению прогиба по середине длины Δf, мм. Прогиб можно измерять прямым способом, с помощью индикатора часового типа по диаграмме «нагрузка - прогиб», или косвенным - по времени роста нагрузки при постоянной скорости деформирования.
Прочность при растяжении поперек пласти
Показатель прочности при растяжении поперек пласти плиты служит для оценки качества склеивания среднего слоя стружечных плит и характеризует минимальную прочность продукции. На образец для испытаний (рис. 2) размером 50 х 50 мм наклеиваются накладки из древесины твердых пород, фанеры или металла, с помощью которых он растягивается перпендикулярно пласти и разрушается по среднему слою. Предел прочности рассчитывается как отношение разрушающей нагрузки к площади образца. Методики испытания по ГОСТу и EN почти не различаются.
Прочность наружного слоя
Этот показатель имеет значение при использовании плит в мебельной промышленности. По отделочному слою, как правило, определяют значения разбухания и усушки, отличные от величин, характерных для самой плиты. Разбухание и усушка этого слоя порождают дополнительные напряжения между облицовкой и плитой, которые при существенных изменениях климата могут достигать больших значений, что может привести к отслоению облицовки от плиты. Прочность наружного слоя зависит главным образом от степени его уплотнения, расхода связующего и схемы прессования.
При определении прочности на отрыв наружного слоя (рис. 3) по ГОСТу 23234-78 в образце размером 50 х 50 мм делают кольцевую выточку шириной 2 мм и внутренним диаметром 25-30 мм и приклеивают цилиндрическую испытательную головку такого же диаметра. Согласно ЕN 311, диаметр головки d составляет 35,68 мм (площадь - 1000 мм2).
При одноосном растяжении измеряют усилие отрыва головки Pmax от поверхности. Предел прочности рассчитывают как отношение разрушающей нагрузки к площади склеивания:
Нижняя граница показателя составляет примерно 1 Н/мм2. Установлено также, что на результаты испытания оказывает влияние тип клея. Клеи, проникающие в структуру плиты, обеспечивают ей высокую прочность.
Разбухание плит по толщине и водопоглощение
Стружечные плиты в разной степени разбухают по пласти и по толщине. Плиты плоского прессования по толщине разбухают примерно в 50 раз больше, чем по ширине или длине.
У экструзионных плит это соотношение противоположное. Такая анизотропия связана с ориентированностью стружки в плите, поэтому для плит плоского прессования измеряют только разбухание по толщине. Согласно ГОСТу 10634-78, у образцов размером 100 х 100 или 25 х 25 мм измеряют толщину и массу с точностью до 0,1%. Образцы погружают в сосуд с водой при температуре 20 0C (большие образцы располагают вертикально) так, чтобы они не соприкасались друг с другом и были полностью покрыты водой. Период выдержки в воде: 2 ч - для малых и 24 ч - для больших образцов. После выдержки образцы осушают фильтровальной бумагой, вторично взвешивают и измеряют их толщину. Водопоглощение рассчитывается по формуле
а набухание по толщине - по формуле
где m1 - масса образца до погружения в воду, г; m2 - масса образца после вымачивания, г; t1 - толщина образца до погружения в воду, мм; t2 - толщина образца после вымачивания, мм.
Согласно европейскому стандарту, у образцов должны быть размеры 50 х 50 мм.
Изменение размеров плит при изменении влажности воздуха
Этот показатель имеет значение для плит, используемых в деталях мебели. В период эксплуатации изделий возможны сезонные и иные колебания относительной влажности воздуха, которые вызывают разбухание и усушку деталей.
Стандарт предусматривает такую процедуру испытаний:
Образцы размером 300 х 50 мм выдерживают в лабораторных условиях, то есть при температуре воздуха 20 0C и относительной влажности 65% не менее 48 ч и измеряют толщину индикатором часового типа и длину образца с точностью не менее 0,01 мм в специальном приспособлении (рис. 4).
Образцы помещают в камеру с повышенной влажностью воздуха (85%) и через 48 ч снова измеряют их толщину и длину. Затем образцы помещают на 48 ч в камеру с пониженной влажностью воздуха (35%), после чего снова измеряют их толщину и длину. Рассчитывают следующие показатели изменчивости размеров образцов:
- разбухание по толщине
- разбухание по длине
- усушка по толщине
- усушка по длине
Здесь h1 и l1 - начальные размеры образцов, мм; h2 и l2 - размеры образцов после выдерживания их в условиях повышенной влажности воздуха, мм; h3 и l3 - размеры образцов после выдерживания их в условиях пониженной влажности воздуха, мм.
Сопротивление выдергиванию шурупов
Согласно ГОСТу 10637-78, образцы должны иметь форму квадрата со стороной 50 мм. Шуруп 4 х 40 завинчивают в предварительно просверленное отверстие диаметром 2 мм в кромку образца на длину нарезки шурупа и в пласть образца - на толщину плиты. Образец помещают в приспособление (рис. 5) и испытывают на растяжение с такой скоростью, чтобы общее время испытания составило около одной минуты.
Удельное сопротивление выдергиванию шурупов, H/мм, рассчитывают по формуле:
где Pmax - максимальная нагрузка, Н; l - глубина завинчивания шурупа, мм.
Методика этих испытаний по EN 320 аналогична отечественной методике. При толщине плит менее 15 мм показатель рассчитывается по такой же формуле. При толщине плиты более 15 мм за сопротивление выдергиванию принимается усилие выдергивания (WS = Pmax, Н).
Содержание свободного формальдегида
Этот показатель определяет токсичность клееной продукции и во многом ее конкурентоспособность на рынке древесных плит. Существует несколько способов определения содержания свободного формальдегида. В ГОСТе 27678-88 и EN 120 содержится описание перфораторного способа для образцов размером 25 х 25 мм, используемых и для фанерной продукции. Процедура испытаний занимает 4-6 ч.
В стандарте EN 717 регламентированы еще три способа определения этого показателя: камерный, газоаналитический и колбовый (рис. 6).
При камерном способе образцы плит обдуваются воздухом при 2300С и относительной влажности 45%, скорость циркуляции 0,1-0,3 м/с. Регистрируется количество газа, адсорбируемого в воде с учетом объема воздуха в камере. Испытания продолжаются 28 дней.
При газоаналитическом способе образец размером 400 х 50 мм в течение четырех часов обдувается горячим (600С) воздухом. Формальдегид попадает в абсорбирующую жидкость, а затем в газоанализатор. Масса выделенного формальдегида рассчитывается как среднее значение за последние три часа и выражается в мг/(м2/ч), то есть с учетом площади образца и продолжительности обдува.
При колбовом методе образец плиты размером 25 х 25 мм, который находится в закрытом сосуде с 50 мл воды, помещается в печь, где поддерживается температура 400С. Содержание свободного формальдегида рассчитывается исходя из разности показателей химического состава раствора, находящегося в колбе, и дистиллированной воды.
Покоробленность плит
Для испытаний (ГОСТ 24053-80) берут образцы размером 1200 х 650 мм и толщиной, равной толщине плиты. Для контроля покоробленности используют прибор с двойной базой: Б1 = 610 мм и Б2 = 200 мм (рис. 7). Прибор представляет собой жесткую балку с тремя опорами для каждой базы и индикатором часового типа. Образец ставят на стенд (рис. 8) и прибор поочередно прикладывают к образцу по измерительным осям Х-Х и Y-Y, совмещая шток индикатора с точкой пересечения осей. Отклонения показаний индикатора от нулевого значения показывают стрелу прогиба. Измерения производят на обеих пластях образца, а за величину покоробленности принимают сумму величин отклонений по обеим измерительным осям.
Контроль качества облагороженных ДСП
которых проверяемая партия принимается
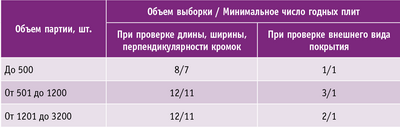
Количество облицованных плит, отбираемых для проверки качества, зависит от объема партии, отгружаемой заказчику. Объемы выборки и минимальное число годных плит, при которых проверяемая партия принимается, регламентирует ГОСТ Р 52078-2003 (табл. 2).
Соответствие плит требованиям ГОСТа оценивают на основе внешнего осмотра поверхности с расстояния приблизительно 300-500 мм, под углом 30-60º, без использования увеличительных приборов и при освещенности 1000-5000 люкс. Осмотр следует выполнять при рассеянном естественном или искусственном освещении. Матовость и блеск покрытий также оценивают визуально, сопоставляя с характеристиками образца-эталона.
Размеры вмятин (углублений) на поверхности плиты определяют при помощи стрелочного индикатора, закрепленного в металлической П-образной скобе с цилиндрическими опорными поверхностями с радиусом 5±1 мм (расстояние между опорами 60-100 мм). Перед замерами шкалу индикатора тарируют: чтобы определить нулевое положение, скобу с индикатором ставят на поверочную линейку или на поверочную плиту. Ход штока в обе стороны от опорной плоскости должен быть не менее 2 мм.
Гидротермическая стойкость поверхностей
Испытуемый образец (квадрат со стороной 75 либо 100 мм) помещают на колбу с кипящей водой и в течение одного часа подвергают воздействию горячего пара. Затем образец промокают фильтровальной бумагой и осматривают сразу после испытания при комнатной температуре, отмечая следующие изменения на поверхности: трещины (в том числе выявляемые при помощи лупы), вздутия, расслоение, потерю блеска и/или цвета (видимые невооруженным глазом). Если внешний вид покрытия не изменился и образец не расслоился или если расслоение отсутствует, а обнаруженные изменения внешнего вида исчезают в течение 24 ч, то результаты испытаний считаются положительными.
Устойчивость поверхностей к повышенной температуре воздуха
Для испытаний берут образцы, имеющие форму квадрата со стороной 250 мм. Их острые кромки зачищают абразивной шкуркой так, чтобы удалить сколы покрытия. Образцы помещают в термошкаф при температуре 70±5°С на 24 ч, затем выдерживают 24 ч при температуре воздуха 20±5°С. Декоративную поверхность после испытания осматривают невооруженным глазом с расстояния 250 мм под углом 20-30°. Выдержавшими испытание считаются образцы без трещин на покрытиях. В результате вся партия плит считается качественной.
Владимир ВОЛЫНСКИЙ