«Харовсклеспром» – кардинальное обновление
Этому старейшему лесопромышленному предприятию Вологодчины в 2014 году исполняется 95 лет - Харовский лесопромышленный комбинат был построен в 1919 году на берегу реки Кубены, вблизи железнодорожной магистрали Москва - Архангельск.
С 2002 года ООО «Харовсклеспром» входит в состав Группы компаний «Вологодские лесопромышленники». Сегодня ООО «Харовсклеспром» - крупнейшее предприятие города Харовска и одно из крупнейших лесопромышленных предприятий Вологодской области.
О том, как происходит техническое «перерождение» ООО «Харовсклеспром», рассказывает технический директор комбината Сергей Цема.
Новая котельная Agro на «Харовсклеспроме»
Сергей Цема, технический директор
ООО «Харовсклеспром»
Сушильные камеры Katres
Линия сортировки сухих пиломатериалов
Подразделения компании располагаются на площади 27,78 га. ООО «Харовсклеспром» выпускает широкий ассортимент пиломатериалов из сосны и ели, а также технологическую щепу. Продукция реализуется в различные регионы России и в страны ближнего и дальнего зарубежья. В компании трудятся около 400 человек. Успешная деятельность комбината обеспечивается благодаря реализации организационной и инвестиционной политики, проводимой холдинговой компанией «Вологодские лесопромышленники».
Начиная с 2006 года на предприятии ведется поэтапная модернизация с заменой устаревшего оборудования на современное и освоением прогрессивных технологий лесопиления и деревообработки. Причем процесс обновления идет, что называется, «без отрыва от производства» - к осени 2014 года на существующей производственной площадке, по сути, будет построено абсолютно новое производство, при этом завод продолжает работать без остановки, постепенно наращивая мощности.
За ООО «Харовсклеспром» на договорной основе в качестве основных поставщиков сырья закреплены ООО «Ломоватка-Лес», ЗАО «Вожега-лес» и ООО «Верховажьелес», благодаря чему комбинат находится в более выгодных условиях по сравнению со многими деревообрабатывающими предприятиями Северо-Западного региона России.
Некоторые данные об основных этапах модернизации комбината приведены в таблице. К 2015 году планируется увеличение объема распиловки до 400-450 тыс. м3 в год по сырью, и ежегодный объем выпуска готовой продукции составит 200-225 тыс. м3 пиломатериалов и около 110-125 тыс. м3 щепы.
Коротко расскажу о структуре нашего предприятия: в состав лесопильного производства входит участок сушки пиломатериалов, а в составе деревообрабатывающего производства - линия сухой сортировки пиломатериалов, транспортный цех, биржа сырья, биржа готовой продукции, участок выработки тепла ТЭС; бесперебойную работу основных производственных единиц обеспечивают вспомогательные подразделения: электроцех и ремонтно-механический цех. Теплоэлектростанция комбината снабжает тепловой энергией предприятие и один из микрорайонов г. Харовска. Сегодня в штате 370 человек, а до очередного этапа масштабной реконструкции, который длится уже полтора года, численность персонала была 440 человек. В связи с вводом высокотехнологичного оборудования нового поколения с максимальной автоматизацией планируется дальнейшее сокращение обслуживающего персонала.
История предприятия «Харовсклеспром»
В сентябре 2014 года предприятию исполнится 95 лет! На основанном спустя два года после Октябрьской революции заводе был начат выпуск шпал для Северной железной дороги.
Во время Великой Отечественной войны предприятие было перепрофилировано на выпуск продукции для военных нужд, а в послевоенные годы оно было преобразовано в «Харовский лесопильно-деревообрабатывающий комбинат». Комбинат был ориентирован на выпуск дверей, окон и другой продукции для типовых домов, которая была очень востребована в условиях строительного бума 1960-80-х годов. В течение 1960-70-х годов отслужившие свое лесопильные рамы были заменены на более современные, предприятие стабильно развивалось вплоть до развала СССР. В начале 90-х предприятие акционировалось и было преобразовано в ОАО «Лесдок». С 2002 г. предприятие вошло в состав ЗАО ГК «Вологодские лесопромышленники» и было преобразовано в ООО «Харовсклеспром». К тому моменту на «Харовском ЛДК» работало около полутора тысяч человек, а к 2008 году осталось 800.
Доля ручного низкоквалифицированного труда была крайне высока, что в современных условиях отрицательно влияло на рентабельность. На комбинате эксплуатировались лесопильные рамы и фрезерно-брусующие станки отечественного производства. Работали два лесопильных цеха. В одном действовали два потока лесопильных рам: один поток был оснащен рамами 2Р75-1 и 2Р75-2, а второй - рамой 2Р50 и многопильным станком Ц8Д8 (это оборудование эксплуатировалось в цехе до марта 2012 года). До июня 2012 года функционировал лесопильный поток на базе Hew Saw R200SE.
Вскоре после вхождения предприятия в состав холдинга «Вологодские лесопромышленники» началась постепенная реконструкция производства: сушильные мощности были увеличены: в 2006 году сначала было поставлено пять камер Secea (Италия) - три с разовым объемом загрузки 180 м3 и две по 130 м3, а в 2007 году к ним добавлены еще три камеры объемом 130 м3 каждая. Также в феврале 2006 года была запущена в работу линия лесопиления на базе Hew Saw R200SE (б/у, 2002 года выпуска) и поставлена шведская линия сортировки сырых пиломатериалов на 15 карманов (б/у, 1979 года выпуска) - линия была скомплектована из оборудования разных производителей. В тот же период была запущена б/у линия сортировки бревен на 22 кармана (1979 года выпуска) с окорочным станком Valon Kone VK-450 (1997 года выпуска).
К 2011 году на предприятии перерабатывалось до 205 тыс. м3 древесного сырья: на линии Hew Saw R200SE - около 140 тыс. м3, а на линии со старыми лесопильными рамами - 60-65 тыс. м3. Завод стал работать с прибылью.
Однако у линии Hew Saw R200SE был недостаток - невысокий процент выхода продукции из-за ограничения по распилу бревен - от 13 до 23 см в вершине. Из любого бревна можно было получить только две центральных и две боковых доски. Общий процентный выход пиломатериалов составлял 44-45%. По этой причине все бревна с диаметром более 23 см приходилось распиливать на старых рамах 2Р75 - довольно примитивном оборудовании, требовавшем большой численности персонала. Кроме того, качество продукции было невысоким, что ограничивало рынки сбыта: если на внутреннем рынке еще получалось найти покупателей, то клиенты из Европы от низкокачественных пиломатериалов отказывались. Мы же в первую очередь старались ориентироваться на европейские рынки сбыта и поэтому, чтобы соответствовать их требованиям, в 2011 году было принято решение провести масштабную реконструкцию комбината.
Рассматривалось очень много предложений, в итоге в качестве поставщика оборудования была выбрана шведская компания Soderhamn Eriksson AB. Выбор был сделан, исходя из соотношения «цена/качество», а также из-за возможности оборудования обеспечить высокий процент выхода продукции. Шведы предложили интересное решение с линией кромкообрезки, дающее возможность получить 50-51% готовой продукции. Мы выбрали линию, которая при загрузке в две смены способна перерабатывать 350 тыс. м3 сырья в год. А с введением третьей смены можно будет увеличить производительность до 400-420 тыс. м3, что мы и планируем сделать. То есть фактически мы собираемся увеличить объем переработки леса в два раза!
Söderhamn Eriksson стал не просто поставщиком лесопильной линии, а генеральным подрядчиком, который подобрал и налаживает для нас всю технологическую цепочку, отвечая за инжиниринг и координацию, разработку проекта электронного обеспечения, шеф-монтаж оборудования, ввод в эксплуатацию, обучение персонала.
Лесопильная линия производства компании Soderhamn Eriksson представляет собой комплект лесопильного оборудования, состоящий из нескольких функциональных участков, объединенных единой автоматической системой управления. Обработка сырья полностью автоматизирована, начиная с загрузки бревен на стол подачи бревен и заканчивая выгрузкой готового пакета сырых пиломатериалов из цеха, а также удаления отходов производства в бункеры-накопители. Перемещение материалов между участками переработки полностью автоматизировано и осуществляется при помощи системы продольных и поперечных цепных и роликовых транспортеров.
Система управления позволяет одному оператору из кабины управления контролировать весь технологический процесс производства пиломатериалов на участках, работающих в автоматическом режиме.
Поясню - в чем особенность линии Soderhamn Eriksson, которая нас так «подкупила»:
Шведская компания предложила оригинальную технологию: бревно подается на линию, проходит через сканирующее устройство, которое оценивает его параметры и выдает команды, в соответствии с которыми бревно поворачивается специальными вальцами по оси таким образом и устанавливается под таким углом, чтобы обеспечить оптимальный раскрой, далее бревно распиливается на центральные и боковые пиломатериалы. Необрезные боковые доски поступают на линию кромкообрезки, где они обрабатываются и оптимизируются по ширине. Таким образом, обеспечивается максимально возможный выход пиломатериалов. Все полученные от раскроя бревна доски поступают на линию сортировки.
Подача пиловочника и окорка
Производственный процесс делится на несколько этапов и начинается с подачи пиловочника и окорки. Бревна подаются перевалочной машиной Liebherr 924 на поперечный цепной транспортер, состоящий из двух секций длиной 12 м и 6 м, выполняющий роль накопителя и разобщителя. Затем бревна посредством устройства поштучной выдачи пошагового действия выдаются на продольный цепной транспортер и далее на продольный цепной транспортер с рамкой сканера, где установлен 1-D-сканер модели Millscan (Швеция), который определяет, где у бревна вершина, а где комель. Линия подачи пиловочника также оснащена оптимизатором зазора, представляющим собой электронное устройство с лазерными датчиками, которое обеспечивает постоянный разрыв между бревнами при их подаче на продольный цепной транспортер.
После определения сканером положения вершины с помощью разворотного устройства револьверного типа бревно разворачивается вершиной по ходу движения и падает на продольный цепной транспортер. Затем бревна поступают на окорочно-оцилиндровочную линию Cambio 600. На линии можно обрабатывать бревна диаметром от 12 до 60 см. А линия лесопиления рассчитана на распиловку бревен диаметром от 12 до 43 см в вершине или на обработку сортиментов диаметром до 50 см в комле. Бревна диаметром свыше 43 см составляют не более 1,5% от общего объема сырья за весь год, и поэтому нам проще отсортировать толстомеры и продать их.
Окорочно-оцилиндровочная линия представляет собой комбинацию подающих, удерживающих устройств, оцилиндровочного и окорочного роторов и устройства выгрузки. Процесс окорки начинается с подачи бревен на центрирующий входной транспортер. Потом бревна проходят через устройство подачи и оцилиндровочный узел, где выполняется оцилиндровка комлевой части, и далее, через устройство подачи, на окорочный станок Cambio 600 и устройства выгрузки.
Cambio 600 - двухдисковый окорочный станок; один барабан - оцилиндровочный, оснащен пятью оцилиндровочными ножами, которые выставляются с необходимым шагом обработки бревен диаметром от 20 до 48 см. Значение диаметра выставляется вручную перед началом работы линии. Срок службы ножей, которые установлены на барабане, полгода. С июля прошлого года мы ни разу их не снимали, не затачивали, они до сих пор находятся в хорошем состоянии, возможно потому, что мы используем этот барабан для обработки бревен диаметром от 26 и выше.
Техническое решение оцилиндровочного узла станка Cambio 600 - эксклюзив от Soderhamn Eriksson. Настройка оцилиндровочного ротора на диаметр может выполняться с шагом через 1 мм и не требуются дополнительные оцилиндровочные кольца.
Частота вращения окорочного ротора может изменяться частотным преобразователем, а усилие прижима короснимателей в окорочном роторе задается при помощи пневматических подушек, в которые закачивается воздух с давлением от 1,5 до 3 бар - в зависимости от диаметра бревна, скорости подачи и сезона (зима или лето). Изменением частоты вращения окорочного ротора также можно добиться более мягкой или жесткой работы короснимателей.
Окорочный ротор производства Soderhamn Eriksson интересно сравнить с подобным оборудованием Valon Kone. Если ротор Valon Kone вращается по часовой стрелке, то у Söderhamn Eriksson - против, если у ротора Valon Kone ножи установлены на выходе из окорочного станка, то у Soderhamn Eriksson - на входе в окорочный ротор. При окаривании сосны и ели у оборудования Valon Kone приходится менять инструмент, у ротора Soderhamn Eriksson нет такой необходимости. Работа в тестовом режиме показала, что станок прекрасно справляется со своей задачей, но есть небольшие проблемы с окоркой бревен малого диаметра (13-16 см). При пусконаладочных работах и в процессе дальнейшей эксплуатации выявились проблемы «загрызания» вершины бревна и вследствие этого периодические поломки бревен. На диаметрах 17 см и выше данной проблемы не наблюдалось. Вызванный нами для настройки станка специалист компании Soderhamn Eriksson провел плановое обслуживание, гарантийный ремонт и настройку станка, после чего качество окорки бревен значительно улучшилось, однако проблема периодически возникала вновь. Чтобы разобраться с причинами появляющейся проблемы, мы еще раз пригласили специалистов компании Soderhamn Eriksson для совместной наладки оборудования и выработки решения о правильной и грамотной эксплуатации окорочного узла станка. На сегодняшний день мы получили доскональную, более проработанную инструкцию по настройке станка, и я могу сказать, что теперь качество окорки на нашем станке превосходит все ожидания - содержание коры в щепе составляет менее 0,1%! Хочу отметить, что данное оборудование - это техника экстра-класса, требующая очень бережного и грамотного обращения и настройки всех параметров станка. Замечание к шведской компании только одно - более оперативно реагировать на наши запросы. Хотя отмечу, что компания Soderhamn Eriksson никогда не отказывала в помощи при решении проблем, надеюсь, так же будет и в дальнейшем.
Удаление коры из-под окорочно-оцилиндровочной линии предусмотрено с помощью скребкового транспортера и ленточного транспортера с металлодетектором. Измельчение коры выполняется в молотковой дробилке. На зимний период она демонтируется. Кора и мусор от бревен из-под двухсекционного поперечного цепного транспортера убираются скребковым транспортером.
После окорки и оцилиндровки бревна перемещаются на круглопильную лесопильную линию посредством продольного цепного транспортера, винтового питателя, устройства поштучной выдачи бревен и продольного цепного транспортера.
Круглопильная лесопильная линия
Цех лесопиления
Подача окоренных бревен на линию лесопиления
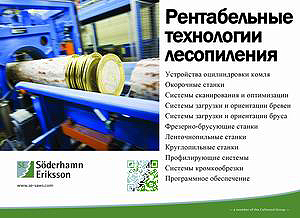
Söderhamn Eriksson. Оборудование для лесопильных
производств
Окоренное бревно проходит через 3D-сканер MillScan, приобретенный по рекомендации компании Soderhamn Eriksson. Этот сканер просматривает все бревно, фиксируя через каждый сантиметр изображение и отражая его на экране монитора. Полученные данные от сканера поступают в компьютер с программой оптимизации и раскроя бревен МРМ, позволяющей рассчитать оптимальный угол поворота бревна при загрузке в лесопильную линию и индивидуальную схему раскроя каждого бревна с основной целью - оптимизацией раскроя боковой доски.
Программа оптимизации содержит множество вариантов. После того, как визуализация бревна сделана, согласно заданному центральному поставу ПК выбирает программу получения оптимального количества боковых досок. Допустим, из бревна необходимо получить четыре боковые доски; исходя из полученных параметров бревна, ПО компьютера указывает, какой именно толщины получатся боковые доски: 16, 19, 22 или даже 32 мм. Бревна у нас отсортированы с шагом через сантиметр, иногда за счет этого можно объединить два постава, например, 20-й и 21-й.
Схема раскроя бревна в нашем случае следующая: центральный постав фиксированный - он задается поставом пил, установленном на многопильном станке Eurosaw FDP. При начале пиления оператор указывает в программе MPM центральный постав (например, 50х150 - 3-х log - три центральные доски), а также желаемую толщину боковых досок (например, 22 мм с каждой стороны). Но оператор обязан указать все другие варианты, которые могут получаться при обработке бревен (например, толщиной 16 и 19 мм). Программа оптимизации МРМ обрабатывает информацию от 3D-сканера и, учитывая параметры центральных пиломатериалов, которые необходимо получить в данный момент, оптимизирует раскрой каждого бревна таким образом, чтобы получить центральные пиломатериалы и максимальное количество боковых досок с максимальной толщиной. При этом с одного бревна можно получить до восьми боковых досок разной толщины. Оптимизация сводится к тому, что из бревна меньшего диаметра мы получим более тонкие боковые доски, а из бревна большего диаметра - более толстые боковые доски.
На всех станках линии и подающих устройствах стоят сервоклапаны, и в процессе пиления под каждое бревно происходит позиционирование пильных узлов. Исключение составляет многопильный станок Eurosaw FDP, постав которого для центральных и боковых пиломатериалов установлен жестко на валу.
Бревна поступают на самый первый узел - кантователь, где каждое бревно устанавливается в позицию самого оптимального раскроя бревна для получения максимального выхода готовой продукции. Два ошипованных вальца кантователя имеют привод от гидромотора. Наклон роликов производится посредством гидравлических линейных позиционеров. Кантование бревна производится путем наклона одного ролика по отношению к другому. Вальцы имеют три фиксированных положения угла наклона в зависимости от диаметра и длины бревна для обеспечения оптимального кантования. После цикла кантования вальцы возвращаются в исходное вертикальное положение.
Первый фрезерно-брусующий станок (ФБС) выполняет фрезерование двух горбылей в соответствии с программой оптимизации раскроя МPM. Допустим, после сканирования бревна, программа определила, что из бревна можно получить одну боковую доску толщиной 22 мм, а вторую боковую доску толщиной 19 мм. Программа управления процессом пиления (программа МРМ) дает команду первому фрезерно-брусующему станку установить фрезерные головки таким образом, чтобы профрезеровать бревно в соответствии с заданными размерами и получить двухкантный брус. На установленном сразу за первым фрезерно-брусующим станком круглопильном станке модели CS 900 от двухкантного бруса с каждой стороны отделяется одна-две необрезные доски, которые после выхода из станка отсоединяются на отделителе боковых досок и направляются на линию обрезки. То есть на лесопильной линии получается боковой необрезной пиломатериал.
На станке CS 900 используются круглые пилы диаметром 900 мм с толщиной полотна пилы 3,2 мм и шириной пропила 4,5 мм. Кроме того, в конструкции станка применен принцип «плавающих» пил - для каждой пилы установлена специальная направляющая, куда подается водо-воздушная смесь. Это наиболее проблемный и сложный узел оборудования, требующий очень тонкой и правильной настройки. Также на этом станке дополнительно установлены верхние пилы диаметром 400 мм и шириной пропила 5,2 мм, которые могут быть задействованы при высоте пропила 380 мм и более. Этот станок весьма требователен к правильным и точным настройкам и к качеству подготовки инструмента.
Из одного бревна после оптимизации распила мы должны получать от двух до восьми боковых досок, сейчас по факту мы получаем от двух до шести.
С первого прохода (первый фрезерно-брусующий станок и круглопильный станок CS 900) мы должны получать 2+2 боковые доски, но по факту получаем 1+1. Шведская компания вовремя не предоставила необходимое приспособление для применения функции «2+2 боковые доски». Это приспособление поступило только в конце января 2014 года, но должно использоваться со специальным инструментом, которого у нас пока нет. Поэтому мы сейчас заказываем необходимый инструмент и 2+2 боковые доски будем получать не ранее апреля этого года. А пока 2+2 боковые доски мы получаем со второго прохода и затем обрабатываем эти доски на линии кромкообрезки.
Как с первого, так и со второго прохода мы можем получать нечетное количество боковых досок.
Эффективное криволинейное пиление
Полученный двухкантный брус укладывается на пласть кантователем бруса и перемещается по ходу линии роликовым транспортером. Перед загрузкой во второй фрезерно-брусующий станок выполняется центрирование и боковое смещение двухкантного бруса на транспортере загрузки. Хочу обратить внимание вот на что - на нашем предприятии предусмотрено выполнение криволинейного пиления при кривизне бревна 1 см на 1 м длины бревна (или когда у 6-метрового бревна высота стрелы прогиба - 60 см) - это соответствует радиусу 60 мм на любой длине бревна. То есть, если взять 6-метровое бревно с кривизной до 6 см, то возможно эффективное криволинейное пиление: начиная со второго фрезерно-брусующего станка и далее будет происходить процесс пиления по кривой. Загрузочное устройство направляет двухкантный брус по радиусу стрелы прогиба (высчитанной программой оптимизации МРМ после получения данных с 3D-сканера) во второй фрезерно-брусующий станок. Кривизна полученной доски визуально почти не видна - получается доска с небольшой «лыжей». На линии можно распиливать бревна и с большей кривизной, только мы не сможем получить максимальный эффект. Мы провели эксперимент - отключили функцию криволинейного пиления, и сразу же выход сырых пиломатериалов снизился на 1,5%. Поэтому функцию криволинейного пиления мы не отключаем.
Единственное условие: нужно обязательно оставлять зазор между бревнами (межторцовый разрыв) от 1,5 до 2 м. Это необходимо, чтобы все механизмы каждого станка успели перестроиться для распиловки конкретного бревна на основании программы оптимизации раскроя. В следствие этого количество бревен в минуту получается меньше, однако по рекомендации шведских партнеров мы оптимизируем распил, начиная с диаметра 16 см, а мелкие бревна (диаметром 12-15 см) пускаем по линии на максимальной скорости с разрывом между бревнами 0,5 м. Оператор с пульта управления может задавать значения необходимого разрыва. Постав задается оператором, разрыв между бревнами устанавливается программой для каждого диаметра бревна с учетом скорости подачи. Оператор может уменьшить разрыв для увеличения производительности до определенного программой предела, или увеличить разрыв, если посчитает необходимым. Линия может работать как в автоматическом режиме, минимизируя так называемый человеческий фактор, так и в ручном режиме.
Все управление лесопильной линией выполняется посредством PLC контроллера. Результаты работы линии лесопиления могут быть распечатаны на бумаге или переданы в систему управления заводом в виде отчетов с компьютера, находящегося в кабине управления.
Окончательный раскрой бруса на пиломатериал
Полученный после второго фрезерно-брусующего станка четырехкантный брус перемещается по роликовому транспортеру к устройству загрузки круглопильного станка, оснащенного системой смены инструмента и устройством смазки пил.
EuroSaw FDP - это многопильный станок с жестким поставом, мы его собираем на специальных пинолях - втулках, на которых собирается постав пил, у станка два вала - верхний и нижний. На валы насаживаются втулки с собранными поставами (с пилами необходимого диаметра). Причем вращаются валы в разные стороны: нижний - навстречу движению бруса (встречное пиление), а верхний - по ходу движения бруса (попутное пиление). За счет этого достигается эффект безопасного пиления, то есть брус одновременно ускоряется и притормаживается. Кроме того, по высоте бруса пиление происходит в таком соотношении: 45% - нижний вал и 55% - верхний. Скорость обработки бревен - от 40 до 90 м/мин., мы даже пробовали пилить бревна диаметром 13-14 см на скорости 100 м/мин., и у нас получилось. При высоте пропила до 105 мм на этом станке можно работать одним валом (нижним). Мы используем эту функцию при распиловке бревен диаметром 13-14 см.
На EuroSaw FDP установлена система смены инструмента, которая позволяет выполнить эту операцию за несколько минут. Эта система представляет собой специальную конструкцию консольного типа, установленную на станок, к которой подвешена штанга с валами, имитирующими пильные валы на многопильном станке. Причем на штанге с обеих сторон (друг напротив друга) установлены как нижний, так и верхний валы. При замене инструмента оператор открывает станок, откручивает стопорную гайку и вручную подводит штангу по направляющей к пильным валам (на одном конце валов штанги установлены собранные поставы на специальных втулках) свободными концами валов. Затем вручную снимает втулку с пилами с верхнего и нижнего валов (на свободные концы валов приспособления), разворачивает штангу на 180 градусов и надевает новые втулки с поставами пил. Отводит штангу со снятыми втулками, закручивает стопорные гайки и закрывает станок. Для того, чтобы установить пильные валы в рабочее положение, имеется специальный пульт дистанционного управления, с помощью которого верхний и нижний валы опускаются/поднимаются. Кроме того, у валов есть функция горизонтального перемещения (до 4 мм) - для точной установки верхних и нижних пил относительно друг друга. После окончательной настройки станок готов к работе.
На этом станке можно выпускать до пяти центральных досок и до четырех боковых (2+2). Шведская компания предоставила нам все чертежи всех видов режущего инструмента. Мы заказываем инструмент таких производителей, как LSAB, Swedex и др.
После многопильного станка в линии установлен отделитель боковых досок, который выполняет отделение боковых досок от центральных пиломатериалов. Полученные готовые центральные пиломатериалы перемещаются по ленточному транспортеру к сбрасывателю, после чего центральные пиломатериалы поступают на транспортер поперечный цепной линии сортировки сырых пиломатериалов. Боковые доски после отделителя поступают вниз на поперечный цепной транспортер, далее по ленточному транспортеру подаются на линию кромкообрезки.
Линия кромкообрезки Catech 1000
На нашей линии кроме распиловочной группы станков установлена линия кромкообрезки, в состав которой входят сканер с двумя лазерными головками IVD 3D, центрирующий транспортер, обрезной станок Catech SE 520, рейкоотделитель, ленточный транспортер для досок и сбрасыватель пиломатериалов на поперечный цепной транспортер линии сортировки сырых пиломатериалов.
Все необрезные боковые доски обрабатываются на линии Catech 1000. Работой линии кромкообрезки управляет со специального кресла с пультом управления оператор из операторской комнаты.
Все боковые доски поступают на поперечный цепной транспортер и далее попадают на наклонный транспортер-элеватор. Затем они поштучно подаются на поперечный цепной транспортер, где оператор может визуально оценить доску на предмет брака (гниль, синева, горбыль). Если у оператора есть сомнения в качестве доски, он может развернуть ее на 180 градусов и посмотреть ее другую сторону. Если оператор убедится в плохом качестве доски, он может отправить ее вниз на вибрационный транспортер, который подаст ее в рубительную машину. Далее доски попадают в загрузочный транспортер, где выполняется их двухстороннее сканирование (как ширины, так и глубины обзола) и генерирование оптимальной схемы раскроя, а затем доски обрезаются на обрезном станке. Оптимизация раскроя боковой доски осуществляется при помощи программного обеспечения Catech 6000.
Catech - это шведская компания. Раньше они были самостоятельной структурой, а на сегодняшний день их выкупила компания Söderhamn Eriksson AB. Они специализируются на производстве высокоскоростных линий обрезки. Наша линия позволяет работать со скоростью до 420 м/мин., т. е. ее пропускная способность составляет около 60 досок длиной 6 м в минуту.
Коротко о том, как работает программа оптимизации раскроя боковой доски. Программа максимально приближена к потребностям клиента. Мы можем ввести в нее любые параметры продукции, которые хотим получить, естественно, мы используем только те размеры, которые соответствуют установленным стандартам. Допустим, пришел заказ на 5-метровую доску толщиной 22 мм. В программе есть возможность задать приоритет, а сканер, получив фактические значения доски, отправляет полученные параметры в систему управления, и ПК, в соответствии с программой раскроя, выдает команды обрезному станку на обрезку в определенный размер. В программе также есть алгоритм выбора приоритетных параметров, к примеру, в случае, если невозможно получить приоритетный продукт № 1, выбирается следующий по востребованности - продукт № 2 или № 3, и так далее. После обрезки готовые доски поступают на ленточный транспортер, далее - на сбрасыватель пиломатериалов, а затем на поперечный цепной транспортер линии сортировки сырых пиломатериалов.
Эта линия может работать полностью в автоматическом режиме - задача оператора проконтролировать наличие бракованной доски и нахождение перед загрузочным транспортером только одной доски.
По линии кромкообрезки Catech 1000 пока возникают вопросы: не всегда правильно сканируются и обрезаются доски. Центрирующий транспортер, ролики, которые должны доску центровать, сначала плохо работали. Тут вся проблема как раз в центровке: как загрузочный транспортер отцентрует доску, так дальше доска и поступит в сканер и обрезной станок. Соответственно, какие параметры сканер снимет с доски, так доска и будет обрезана на обрезном станке. У станка Catech SE520 есть интересная функция - на нем можно выполнять диагональную обрезку досок путем смещения пил в процессе пиления. Эта функция установлена специально для продольного сканирования - такой сканер установлен у нас.
В операторской сосредоточен центр управления всей линией - главный сервер лесопильной линии, сервер линии кромкообрезки, компьютер с программой раскроя и управления линией лесопиления (программа МРМ принимает и обрабатывает данные со сканера 3D MillScan), компьютер с программой раскроя боковой доски, сервер видеоконтроля за работой линии. В процессе пиления оператор участвует мало. Его задача - включить линию, запустить станки, убедиться, что все функционирует исправно, и если все хорошо, то он запускает процесс пиления и просто наблюдает на видеомониторах за разными участками. Ко всем важным узлам подключены видеокамеры, и оператор должен контролировать процесс.
Вообще, вся техника сложная, «умная», пока ее налаживали, часто происходили сбои, но сейчас уже реже. Компания Soderhamn Eriksson в помощи не отказывает, специалисты-наладчики приезжают, но оперативности в реагировании на проблемы нет. Хотя линия сейчас на гарантии. Гарантийные случаи уже были - особенно с окорочным станком было много проблем. Повторюсь, от шведской компании хотелось бы более оперативного реагирования на наши проблемы.
Для быстрого сервиса есть возможность дистанционного контроля: мы подключили основной сервер лесопильной линии к сети интернет через систему удаленного доступа с присвоением специального IP-адреса. Таким образом, у шведских специалистов есть прямой доступ к серверам линии лесопиления. Поставщики могут зайти в любое время в программу и выполнить корректировку, если это необходимо. Производитель программного обеспечения - компания Milltech (Швеция). Эта программа работает так: каждый механизм при подаче определенного сигнала перемещается на то или иное расстояние, вращается с определенной скоростью или выполняет какую-то определенную функцию. Но данные для выполнения операций предоставляет программа MPM, в которой рассчитывается оптимальная схема раскроя и оптимизируются боковые доски по толщине. Кроме того, в программе Milltech есть возможность калибровки каждого узла линии, а также тонкой настройки любого механизма или станка лесопильной линии.
Еще об одной особенности лесопильной линии стоит упомянуть - все узлы, на которых выполняется пиление бревен, бруса или досок круглыми дисковыми пилами, оснащены системой водо-воздушного охлаждения. Специальные перемешивающие установки есть на круглопильном станке модели CS 900, многопильном станке EuroSaw FDP, обрезном станке Catech SE 520. Подготовка воды для этих узлов выполняется системой химической подготовки воды, на которой техническая вода очищается до качества питьевой воды - это требование шведской компании.
Также на всей лесопильной линии установлена централизованная система смазки всех цепных транспортеров, включая наружные (установленные на улице), поставщик - шведская компания Lubtech (в рамках контракта с Soderhamn Eriksson AB).
При запуске линии происходило довольно много сбоев: неправильно выставлялись размеры, застревали бревна, плохо отделялись боковые доски от центральных и т. п. Спустя какое-то время мы выяснили, что неправильно работали некоторые датчики, их пришлось поменять, с ошибками действовали операторы при возникновении внештатной ситуации, некорректно работали импульсные шифраторы (энкодеры). Поясню: каждому бревну программой присваивается свой номер. Допустим, по какой-то причине на каком-то станке обработка бревна останавливается, и бревно убирают. Далее линию включают снова, но и обработка следующего бревна также останавливается. Почему? Ведь все исправно. Просто система управления не получила информацию, что бревно, к примеру, № 1, уже удалено, и считает, что следующее бревно - это все тот же № 1, и все механизмы выстроены под параметры именно этого бревна. Мы не сразу разобрались, как нужно обнулять информацию об удаленном бревне, выяснилось, что с пульта оператора это буквально за минуту делается.
Этой тонкости нас поначалу шведские поставщики не обучили, да и некоторые датчики тоже неправильно работали, но сейчас устранены почти все замечания. Линия работает довольно хорошо.
Линия сортировки сырых пиломатериалов
Линия сортировки сырых пиломатериалов Almab (Швеция) принимает и обрабатывает пиломатериалы - как центральные, так и боковые, которые вышли с линии Soderhamn Eriksson. Центральные доски выходят пачкой: на лесопильной линии мы можем получать до пяти центральных и восьми боковых досок, всего - до 13 досок. Если на линию запущены бревна малого диаметра (12-17 см), ее пропускная способность составит до 12 бревен в минуту, если же это будут бревна большого диаметра (26-40 см), примерно семь бревен в минуту. Для примера: из бревна диаметром 30 см мы получаем четыре центральные доски и шесть боковых. При производительности 7 бревен в минуту получаем 28 центральных досок и 42 боковые доски. Все эти доски поступают на поперечный транспортер линии сортировки сырых пиломатериалов.
Итак, центральные и боковые обрезные пиломатериалы перемещаются по поперечному цепному транспортеру, далее поштучно по наклонному транспортеру на рольганг, где выравниваются торцы пиломатериалов. После этого пиломатериалы транспортируются по поперечному цепному транспортеру и выдаются на устройство поштучной выдачи. Далее доски поступают поштучно на цепной транспортер с упорами, который направляет их в сканер обзола Limab (Швеция). Сканер определяет наличие обзола на доске, замеряет геометрические размеры (ширина, толщина и длина) и выдает команду триммеру (мультиторцовочной пиле, 21 пила) для обрезки обзола. На этой линии качество пиломатериалов не определяется. Все доски сортируются по сечению. Кусковые отходы падают вниз на ленточный транспортер и далее попадают на транспортер отходов. Также сканер выдает команды на направление досок в определенный карман.
После триммера доски поступают на сортировочный транспортер, который состоит из 40 сортировочных карманов, предназначенных для накопления пиломатериалов. Карманы этой линии заполняются пиломатериалами одного сечения, длина не важна. То есть все доски с сечением, допустим, 16х100 падают в один из карманов. Программа считает количество досок, которое необходимо для формирования сушильного пакета. Допустим, если требуется собрать 500 досок, карман отключится, как только это количество будет набрано в нем, и встанет в очередь на выгрузку. Скорость линии сортировки, работа которой синхронизирована с работой лесопильной линии, - до 100 м/мин.
После того, как в сортировочном кармане будет накоплено заданное количество досок, их выгружают на поперечный цепной транспортер. Далее пачка пиломатериалов перемещается на следующие поперечные цепные транспортеры, после чего пачка разбирается с поштучной выдачей досок на два наклонных транспортера. Слой пиломатериалов перемещается по транспортеру к устройству поштучной подачи. При движении пиломатериала по транспортеру и двум последующим рольгангам выполняется ориентирование торцов пиломатериалов по заданным размерам пакета.
Пакет пиломатериалов формируется на штабелеформирующей машине, оснащенной девятью кассетами прокладок. Прокладки в цех загружаются по поперечному транспортеру. Готовый сушильный пакет пиломатериалов по поперечному цепному транспортеру удаляется из цеха и далее перемещается погрузчиком на склад сырых пиломатериалов. Сушильные камеры в течение дня загружаются сушильными пакетами: отдельно - пакетами с центральными пиломатериалами, отдельно - с боковыми. В одну камеру укладываются сушильные пакеты с досками одинаковой толщины, длина и ширина досок не имеют существенного значения.
В проекте модернизации «Харовсклеспрома» участвовало много компаний. Генеральный поставщик всего лесопильного комплекса - Soderhamn Eriksson AB, а линию входа с линии подачи пиловочника поставляла шведская компания Hedlunds (Gosta Hedlund AB). В составе этой линии поперечные цепные транспортеры подачи бревен на устройство поштучной подачи, продольный цепной транспортер с системой оптимизации зазора, продольный цепной транспортер со сканером (вершина/комель), разворотное устройство револьверного типа, приемный транспортер со сбрасывателем материалов после окорочного станка, винтовой питатель, устройство поштучной выдачи бревен, продольный цепной транспортер для приема бревен. А также ленточный транспортер для коры с металлодетектором, скребковый цепной транспортер для подачи коры в бункер и молотковая дробилка для коры.
Уборку отходов от лесопильной линии обеспечивает техника компании Bruks (Германия), включая транспортеры и двухножевую барабанную рубительную машину. Очень надежная техника - поставили и работает, вопросов никаких. Основное требование по уходу - очень много точек смазки. Если ухаживать, вообще проблем нет никаких. Правда, я считаю, что не совсем правильно подобрана рубительная машина - щепа на ней получается низкого качества. Также Bruks поставил нам вибротранспортеры двух видов: один, облегченной конструкции, с линии Catech 1000 принимает отбракованные оператором доски, а второй, установленный под обрезным станком и рейкоотделителем, направляет обрезки прямо в рубительную машину. В этот же транспортер попадают обрезки досок, которые образуются после триммера Almab, и возврат крупной фракции щепы на дорубку. Установка сортировки щепы также производства Bruks. После сортировки кондиционная щепа направляется в один бункер, опилки и отсев щепы - в другой. Это оборудование очень надежное - с момента запуска не было ни одного простоя, связанного с техническими проблемами оборудования Bruks.
Раньше мы отгружали в год 40-50 тыс. м3 щепы, 90% объема которой шло на финские ЦБК - у нас прямой контракт с Metsaliitto. В России мы работаем с ОАО «Волга», но с ними контракт только по еловой щепе. С началом модернизации объемы производства щепы существенно выросли: в среднем в щепу у нас сейчас перерабатывается 28-30% от объема распиловки, а раньше было 23-25% от объема распиловки. А с увеличением производительности до 350-400 тыс. м3 в год по сырью щепы мы будем вырабатывать примерно 100-115 тыс. м3. И на весь этот объем у нас уже есть спрос.
Что касается погрузочной техники, мы используем в основном машины компании Liebherr, еще в 2005 году были куплены два погрузчика, которые очень хорошо себя зарекомендовали. Сегодня у нас работают два фронтальных погрузчика - Liebherr L 544 (2005 года выпуска) и L 566 (2011 года выпуска). Оба погрузчика могут работать как с лесным захватом, так и с ковшом. Ковш у погрузчика L566 - довольно большой, на 11 м3. Эта машина осуществляет уборку бункеров щепы и опилок, перемещает щепу на склад, выгружает опилки на площадку старой котельной. Также у нас задействованы колесные погрузчики экскаваторного типа Liebherr 924 (2011 года выпуска) и Liebherr 934 - также с лесным захватом. Эти погрузчики могут перемещать пиловочник пачками. Кроме того, в 2012 году была куплена перегрузочная машина Fuchs модели 350 на аутригерах. Нам очень нравится работать с Liebherr - у них очень хороший сервис. У Fuchs с сервисом хуже. А машина сама по себе хорошая, у нее очень большая стрела - длиной 16 м, с ее помощью можно складывать штабели высотой 10 м и далеко работать с одной точки. У Fuchs 350 подъемная кабина, оператор может подниматься довольно высоко, что очень удобно при разгрузке леса из полувагонов. Еще мы используем вилочные погрузчики Daewoo Doosan. Они тоже неплохо себя зарекомендовали. В декабре к нам придут еще два погрузчика грузоподъемностью 13 т и 9 т.
Под планируемый годовой объем 400 тыс. м3 по сырью мы вложились в покупку новой линии сортировки бревен Hekotek на 40 карманов с 3D-сканером (производитель - «Автоматика-Вектор», Россия) и металлодетектором. Она уже получена, но пока еще не смонтирована, так как для ее установки требуется площадь, которая пока что занята старой котельной. Полный вывод старой котельной из эксплуатации запланирован на конец февраля, и затем она будет демонтирована. После чего начнется подготовка площадки под устройство фундаментов для новой линии. Мы планируем в сентябре-октябре текущего года установить и запустить в работу новую линию сортировки бревен Hekotek.
Пока же мы работаем на старой линии 1979 года выпуска с 22 карманами, которая была куплена в ходе реконструкции в 2005 году. Она хоть и старенькая, но пока справляется с текущим объемом, документации по ней почти никакой не осталось. В составе линии 2D-сканер производства компании «Автоматика-Вектор», который мы установили самостоятельно.
Все это оборудование было приобретено и установлено в ходе первого этапа модернизации предприятия. Второй этап уже вовсю идет - в работу запущена новая котельная производства Agro Forst & Energietechnik GmbH (Австрия), также в 2014 году намечено ввести в строй новые сушильные камеры Valutec (Финляндия) и линию сухой сортировки пиломатериалов Almab с системой определения качества пиломатериалов FinScan.
Модернизация сушильного комплекса
Производительность сушильного комплекса на сегодня составляет 10-12 тыс. м3 пиломатериалов в месяц, это 20-25 тыс. м3 в месяц по распиленному сырью. И это сегодня - потолок.
В связи с приобретением новых сортировочной и лесопильной линий и увеличением объема выпуска продукции более чем в два раза остро встал вопрос о наращивании сушильных мощностей. До модернизации сушка пиломатериалов в основном проводилась в итальянских камерах Secea периодического действия, выполненных из алюминия. Качество сушки и производительность камер существенно снижались в зимний период, так как конструктивно эти камеры не совсем пригодны для работы в северных условиях. Мощностей камер Katres, докупленных ранее под увеличенные объемы, также не хватало.
Выбор был сделан в пользу полуавтоматических сушильных туннелей непрерывного действия Valutec из нержавеющей стали. Основные причины:
- срок непрерывной работы туннеля - 345 дней в год, в то время как камера периодического действия работает максимум 290 дней в году, все остальное время занимают необходимые операции загрузки/разгрузки и техническое обслуживание - это не самое выгодное решение с точки зрения себестоимости сушки 1 м3 пиломатериала, особенно если учитывать наши большие объемы;
- туннели удобны с точки зрения внутренней логистики производственной площадки предприятия;
- в туннеле есть возможность сушки пиломатериалов со смежными величинами сечения, что для нас особенно важно. Если мы выйдем на объем 350-400 тыс. м3 в год на входе, то объем готовой продукции составит 180-200 тыс. м3, из них около 50-70 тыс. м3 в год - боковой доски, а остальное - центральные доски. Поэтому для начала мы приобретаем два сушильных туннеля именно для боковой доски.
Боковая доска требует особого внимания - ее надо аккуратно сушить. При неправильной сушке боковой доски проявляются дефекты - коробление и растрескивание. И продолжительность работы тоннеля нам тоже подходит из-за особенностей работы с боковой доской. После оптимизации из каждого бревна мы получаем боковые доски разной толщины, а технические характеристики камер Valutec позволяют одновременно загружать в них пиломатериал с разной толщиной - от 16 мм до 32 мм! Но есть тонкости: в одну камеру допускается загружать доски не более двух сечений - например, 16 и 19 мм или 19 и 22 мм. Но, например, загрузка досок сечением 16 и 22 мм не допускается. Кроме того, на каждой тележке может сушиться доска только одного сечения, а на соседних тележках могут быть загружены доски другого сечения. Суть такая: допустим, мы в программе задали сушку до 18% влажности. Значит, доска потолще высушится до 18%, потоньше - до 16%. И поэтому главное - попасть в «коридор» от 16 до 20%. В принципе, есть возможность сушить доску и до 14% влажности.
Условия для нас получаются идеальные: боковая доска потоком пойдет через камеры непрерывного действия, потому что постоянно поступает пиломатериал разной толщины, а центральные доски будут сушиться партиями, сформированными из досок одинаковой толщины.
Две камеры Valutec будут полностью задействованы для сушки боковой доски, а центральную доску будем сушить в периодических камерах и третьем туннеле Valutec, который планируем покупать.
Сначала были заказаны камеры с двигателями мощностью 15 кВт, но позже поставщиком было принято решение укомплектовать два туннеля, предназначенных для сушки боковых досок, более мощными двигателями - на 22 кВт. Сушка боковых досок требует большой мощности, так как горячий воздух прогоняется через 50-100 просветов между пиломатериалами в сушильном пакете, а не через 20, как при сушке центральной доски. Также, учитывая то, что средняя длина пиломатериалов 5,8-6 м, действительно лучше брать оборудование с двигателями с запасом мощности. Для большей надежности Valutec решил изменить параметры заказа и увеличил мощность двигателей на 25-30% по сравнению с планировавшейся, то есть с запасом сверх требуемой производительности, причем без доплаты, за что им отдельное спасибо. В соответствии с контрактом у нас уже начался монтаж двух первых туннелей, третий будет поставлен на «Харовсклеспром» в течение 2014 года.
Специалисты компании из «КАМИ-Древ» установили на одной из наших камер Secea новую систему управления сушильным процессом. Это сделано в связи с тем, что у одной из камер Secea вышел из строя контроллер управления, и с августа 2013 года камера не работала. Специалистов по Secea в России и за рубежом уже не осталось. Поэтому мы обратились к нашим давним партнерам, и они отлично справились с поставленной задачей. Камера запущена в работу и успешно функционирует.
Новая котельная Agro
Оборудование в котельной Agro
Андис Лусис (представитель компании Agro Forst &
Energietechnik GmbH в России) проводит обучение
персонала котельной
Новая котельная, оборудованная компанией Agro
Паровая котельная с котлами ДКВр 10-13 Бийского завода на «Харовсклеспроме» работает с 1958 года - это самое старое из «унаследованного» от советских времен оборудования. Она всегда работала на экологически чистом топливе - на биомассе. Но ее время уже ушло, четыре котла, каждый из которых должен выдавать по 7 МВт, сообща выдают всего 10 МВт. Кроме того, мы не можем позволить себе «роскошь» - из 26 га нашей территории занимать 10 га котельной. К тому же прошлой осенью в работе оборудования котельной начались сбои, а мы несем ответственность за отопление не только предприятия, но и микрорайона г. Харовска. Помимо этого, в концепцию организации максимально автоматизированного производства котельная с обслуживающим персоналом 65 человек никак не вписывается.
Мы серьезно подошли к выбору производителя оборудования для котельной, в первую очередь смотрели на качество и степень автоматизации, да и стоимость играла не последнюю роль. Мы остановили свой выбор на оборудовании водогрейной котельной от компании Agro Forst & Energietechnik, так как они показали нам свои котельные в работе: провезли по предприятиям Латвии, Германии, Австрии, на которых это оборудование эксплуатируется. Особенно нас впечатлило, что котельную, отапливающую небольшой городок в Альпах, по численности такой же, как Харовск, - 10 тыс. жителей, обслуживает (и то, по сути, дистанционно) всего один человек, хотя у него есть два помощника - на всякий случай. Он и начальник, и оператор, и погрузчиком управляет. В котельной все автоматизировано, везде стоят датчики и подключена система автоматизированного учета и передачи данных через интернет с оповещением оператора СМС-сообщением о возникших проблемах или внештатных ситуациях. Оператор в любое время может проверить дистанционно какой-либо параметр оборудования и посмотреть, все ли там в порядке: какая температура держится, как функционирует котел. Последние сомнения отпали после того, как мы увидели, на каком топливе может работать это оборудование. Котел «всеяден»: кора, ветки, можно даже бревно затолкать в топку - все сгорит. Они даже говорят не «котельная на коре», а «котельная на биомассе». Мы убедились воочию, что это оборудование может работать, по сути, и на одной коре! Это было решающим фактором в выборе котельной установки.
Пуск котельной Agro был намечен на сентябрь 2013 года, но были свои сложности: проектировщики немножко подвели - запоздали с проектом, а без проекта невозможно начинать монтажные работы: гидравлическую обвязку котельных установок, коммуникации, электромонтаж и т. д. Все монтажные работы были выполнены к концу октября - началу ноября 2013 года. Котельная была готова к пусконаладочным работам с участием представителей компании Agro уже в середине ноября 2013 года и с их приездом эти работы и начались. Уже в начале декабря оба котла были пущены в работу. Но в начале декабря к котельной установке были подключены только сушильные камеры предприятия. Вывести котлы на максимальную мощность не было возможности по причине отсутствия потребителей с нагрузкой не менее 10 МВт. Окончательно все коммуникации для подключения микрорайона Харовска к нашей котельной, а также коммуникации отопительной системы отопления предприятия были готовы к пуску в конце декабря 2013 года. С 20 января 2014 года новая котельная работает на полную мощность, обеспечивая тепловой энергией как наше предприятие (отопление и сушильные камеры), так и городской микрорайон. Все получилось удачно - котельная превосходно справляется со своими задачами.
Общая мощность котельной - 20 МВт (два котла по 10 МВт). Что еще хочется отметить - в котлах Agro процесс горения оптимизирован, что обеспечивает существенную экономию затрат на электропотребление. При работе котла на максимальной мощности энергопотребление одной котельной установки составляет всего около 180 кВт.
В штате котельной четыре оператора, один слесарь, который обслуживает системы (смазка, проверка и ревизия насосов, гидравлических систем и т. п.) и электрик. Работа оборудования не требует большого вмешательства человека: оператор сидит за компьютером и контролирует процесс горения и выработки тепловой энергии. Управление котельной входит в зону ответственности непосредственно главного энергетика.
Каждая котельная установка состоит из следующих элементов: бункер с системой подвижного пола, гидравлический толкатель в камеру сгорания, камера сгорания, вертикальный трехступенчатый котел, воздухонагреватель (для первичного воздуха), мультициклон (для очистки дымовых газов), дымосос, система первичной подачи воздуха, система вторичной подачи воздуха и система управления с визуализацией процесса.
Гидравлические толкатели с помощью двух гидравлических цилиндров подают топливо в камеру сгорания. Толкатель запрессовывает топливо в прочный металлический топливопровод, в начале которого установлены специальные ножи, срезающие излишки топлива (в том числе - любые кусковые отходы). В результате негабаритные материалы автоматически обрезаются. Так что подготавливать топливо заранее не требуется, что очень удобно.
Монтаж котельной был выполнен очень быстро, поскольку многие части от производителя были привезены, по сути, в собранном виде: и подвижный пол, и транспортеры, и гидростанция. Транспортер-толкатель вообще был доставлен в сборе, и его краном опустили в заранее подготовленное место и забетонировали.
Котел устроен следующим образом: топка, подвижная колосниковая решетка в виде «горки» - два слоя подвижных колосников двигаются при помощи гидравлических цилиндров, а также золоудалитель. Вся зола удаляется автоматически, через специальный шлюз, который периодически открывается, и толкатель подает золу на цепной транспортер, который направляет ее в передвижной бункер, расположенный за пределами котельной (на улице, под навесом). По мере заполнения бункер транспортируют на свалку, где зола ссыпается.
Дымовые газы под воздействием вентилятора от дымососа поступают непосредственно в вертикальный трехступенчатый котел. В котле циркулирует вода, а дымовые газы двигаются по ступеням (каналам) - по одной, двум или всем трем ступеням, что определяется программой управления. Котел оборудован специальным механизмом, который открывает или закрывает каналы для движения дымовых газов. За счет высокой температуры дымовых газов (в камере сгорания она достигает 1000ºС) вода нагревается до температуры 100, максимум 110ºС. Выбор в пользу водогрейной котельной был не в последнюю очередь обусловлен тем, что подобные котельные установки не требуется регистрировать в органах Ростехнадзора.
Максимальное давление в котле - 6 бар, рабочий режим - 4 бар. Отработанные дымовые газы поступают в воздухонагреватель, где происходит подогрев первичного воздуха, который подается в камеру сгорания и выполняет две функции: поддержание горения топлива и подсушка топлива. После вентилятора первичного воздуха установлено специальное разделительное устройство («штаны»), которое автоматически делит поток первичного воздуха надвое: одна часть уходит в зону горения, вторая - в зону сушки топлива. Дальше установлен мультициклон - система очистки дымовых газов. Здесь собирается вся зола, присутствующая в летучем состоянии в дымовых газах. Затем зола собирается в конус, из которого при помощи дозатора и шнека непрерывно направляется обратно в камеру сгорания, в зону работы системы золоудаления. Зола падает на дно камеры сгорания и периодически удаляется гидравлическим толкателем. Дымовые газы выбрасываются в дымовую трубу. В этих котлах установлена простая, но очень эффективная система очистки дымовых газов. Благодаря ей выбросы нашей котельной в три раза меньше разрешенных российским законодательством.
Дальше нагретая вода через два насоса (основной и резервный) попадает в распределительные узлы. Для нормальной работы сушильных камер необходима температура воды не менее 90-95 ºС, и поэтому задача котельной - нагревать воду до 100-105 ºС. Это тем более важно, что мы намерены приобрести камеры Valutec, которые будут потреблять довольно много энергии и для нормальной работы которых также требуется, чтобы температура воды на входе непосредственно в сушилку была 100 ºС.
У котельной есть двойная система защиты от возгорания в топливопроводе при работе камеры сгорания, куда непрерывно поступает топливо. На входе в камеру сгорания в двух местах установлены температурные датчики и система подачи воды. При обнаружении зоны с температурой, превышающей допустимую, система начинает подачу воды в эту зону для предотвращения возгорания. Мы спрашивали у специалистов компании Agro, были ли в их практике возгорания в котельной, и они ответили, что ни разу не было, но они обеспечивают перестраховку таких рисков. И это правильно. Ведь каждый потребитель использует разное топливо. Например, мы используем кору, и, вероятно, сложностей не будет. А некоторые потребители используют сухие опилки или стружку, и может, опасность возгорания существует.
Хочется отметить удобство работы с наладчиками Agro, их готовность помогать и консультировать нас даже по вопросам, выходящим за рамки контракта. Их сервис также предусматривает возможность проведения онлайн-консультаций для операторов котельной.
Подводя итоги первого этапа сотрудничества с Agro Forst & Energietechnik GmbH, можно сказать, что мы получили и качественный европейский продукт, и хороший сервис. Надеемся, что так будет и в дальнейшем.
Сортировка сухих пиломатериалов
В рамках программы модернизации мы решили приобрести также новую линию сортировки сухих пиломатериалов на 55 карманов. Старая линия Hamar 1986 года выпуска на 30 карманов была куплена еще в 2008 году в Швеции. Сейчас на ней при работе в три смены можно обработать не более 12 тыс. м3 сухих пиломатериалов. И карманы у нее прямого падения, то есть доски летят вниз и зачастую ломаются, особенно - центральные. Необходимость ее поменять давно назрела.
Рассматривая поставщиков такого оборудования, мы выбирали между Hekotek и Almab и остановились на последнем. Техника Almab, в принципе, уже неплохо зарекомендовала себя на сырой сортировке. Кроме того, у Almab есть очень интересная разработка - устройство позиционирования доски. Другие компании не смогли нам предложить подобное. На линии установлено специальное устройство, которое может сдвинуть или отодвинуть доску на 300 мм. Смысл такой: на линии установлен сканер для определения качества сухого пиломатериала FinScan BoardMaster FS-120 HDL и две системы EndSpy для сканирования обоих торцов пиломатериала. То есть выполняется оценка качества пиломатериала со всех его шести сторон. Анализируются размеры пиломатериала (длина, толщина, ширина), деформация, обзол и трещины, сучки и проростки, синева и гниль, смоляные кармашки, остатки коры. Если в результате сканирования выявляется дефект, допустим, у края доски, требуется отпилить всего 100 мм, и можно получить готовую доску. Но триммер установлен жестко, он не двигается и торцовку выполняет той пилой, которая расположена ближе остальных к дефектному месту. И вот это специальное позиционирующее устройство может сместить доску так, чтобы добиться максимальной оптимизации. В результате мы получим длинную доску и увеличим объем готовой продукции.
Эта линия рассчитана на переработку в год 225 тыс. м3 сухих пиломатериалов при работе в две смены со скоростью обработки до 120 досок в минуту. Она может работать полностью в автоматическом режиме. Обслуживать ее будут всего 6 человек, включая мастера. Мы подсчитали, что скорость обработки на этой линии будет 95-100 досок в минуту. Чтобы обработать текущий объем, хватит и такой скорости. Теоретически, организовав работу в три смены, можно и еще увеличить объем обработки. Монтаж линии мы начали с середины октября 2013 года и в апреле 2014-го планируем запустить ее. Плюс еще месяца два-три на пусконаладку, на отладку работы сканнера FinnScan.
Эти сканеры очень популярны в России, за 25 лет продаж в нашей стране они доказали свою эффективность, по статистике от производителя на российский рынок было поставлено около 350 сканеров. Как показывает практика, после недели, которая необходима для подключения этого оборудования, наладка его работы может занять еще месяц-два, так как FinnScan может оценивать пиломатериалы в широком диапазоне параметров. Хорошо настроенный FinnScan работает отлично, а его индивидуальная, тонкая настройка способствует значительному повышению полезного выхода продукции. После пуска сканера мы будем отслеживать параметры его работы и смотреть, что и на каких скоростях будет получаться. Опытные партии мы переберем вручную и сравним полученную информацию с данными, полученными от FinnScan. Как только результаты начнут полностью совпадать, наладка будет считаться завершенной.
На месте старой, пока еще работающей линии сортировки сухих пиломатериалов, в освободившемся цехе площадью около 2500 м2 мы, возможно, разместим оборудование под новое направление - производство клееных деревянных конструкций, но это пока вопрос будущего. В любом случае, уже сейчас мы развиваемся, модернизируемся, оптимизируем выход продукции, уменьшаем затраты - делаем все для стабильной и качественной работы в сегменте лесопиления.
Работы предстоит еще очень много. Так как, модернизируя производство и запуская новое оборудование, мы увеличиваем объемы переработки леса, потребуются большие площади для хранения пиловочного сырья. Поэтому предстоит фактически с нуля обустроить площади для новой биржи сырья. Мы планируем завершить эту работу в конце 2014-го - начале 2015 года. Кроме того, с увеличением объема распиловки увеличатся и объемы хранения и складирования готовой продукции - значит, потребуется увеличение площадей биржи готовой продукции с возможностью хранения до 10 тыс. м3 готовой продукции и осуществления отгрузки в две, а при необходимости - и в три смены. Причем будут расти объемы отгрузки как автомобильным, так и железнодорожным транспортом (контейнерные перевозки).
Я уверен: наша компания способна реализовать все задуманное и стать одним из лидеров лесопиления Вологодской области и одним из ведущих лесопильных предприятий России.
Подготовила Светлана ЯРОВАЯ
Фото - Андрей Забелин
Компания Soderhamn Eriksson выражает благодарность за плодотворное сотрудничество при реализации проекта и высокий профессионализм всей команде «Харовсклеспрома», а особенно Андрею Коноплеву, Сергею Окатову и Сергею Цеме.
Информация о приоритетном инвестиционном проекте ООО «Харовсклеспром» «Реконструкция производства»