Одноступенчатое производство древесной пыли
Превратите отходы своего производства в энергию
Еще в 2011 г. группа компаний Dieffenbacher вывела на рынок измельчитель нового поколения - ClassiSizer. В последующие годы эта машина, в основу рабочего принципа которой положена технология ударного воздействия, была по достоинству оценена многочисленными клиентами.
Применяемый в целом ряде областей измельчитель ClassiSizer успешно справляется с самыми разными задачами. Он уже давно используется для подготовки сырья из древесины и прочего биогенного материала (например, соломы и т. п.), а также применяется в различных отраслях производства, связанных с переработкой отходов.
Конструкция и принцип работы измельчителя ClassiSizer
При измельчении древесины размер загружаемого материала может сильно варьироваться: от мельчайших пылевых частиц до кускового материала с длиной кромки до 400 мм. Для ClassiSizer такой широкий диапазон размеров подаваемого материала не проблема - напротив, при работе с таким сырьем достоинства машины становятся очевидными. Так, ClassiSizer применяется для производства различных материалов: стружки среднего слоя из древесины вторичного использования; стружки из сырой щепы, предназначенной для пеллетирования; древесной муки - основы древесно-полимерных композитов; летучей древесной пыли, используемой в качестве сырья для выработки тепла и энергии.
Остановимся на производстве древесной пыли. Частичное замещение первичных энергоносителей летучей древесной пылью дает предприятию существенную экономию и вызывает большой интерес у наших клиентов.
Прежде всего рассмотрим более подробно общую конструкцию и принцип работы ClassiSizer.
Центральный элемент машины - так называемая ударная камера, в которую предназначенный для измельчения материал подается сверху через загрузочный люк. В нижней части ударной камеры горизонтально установлен быстро вращающийся ротор, оснащенный износоустойчивыми ударными элементами. Сама ударная камера имеет форму многоугольника. На боковых стенках могут устанавливаться разные, индивидуально подобранные в зависимости от производственной задачи плоские сегменты решетчатых сит, обеспечивающих равномерную разгрузку измельченного в ударной камере материала. От конструкции и вида перфорации этих сит главным образом зависит размер частиц получаемой фракции.
Измельчение происходит за счет взаимодействия подаваемых частиц материала с ротором, ситами, а также отдельных частиц друг другом. Основная работа осуществляется ротором, вращающим частицы в ударной камере с высокой кинетической энергией. Из-за большого расстояния между диаметром вращения ротора и ситами исключается энергоемкое трение и (или) размол подаваемого материала, которые положены в основу принципа измельчения в других машинах. Получаемый в ударной камере материал, измельченный до желаемого размера, собирается в разгрузочных емкостях, расположенных по обеим сторонам машины, выводится с помощью двух разгрузочных шнеков и может, механическим или пневматическим способом, транспортироваться дальше.
Режим работы ротора и конфигурация просеивающих сегментов имеют множество вариантов и легко могут быть приспособлены к задачам заказчика. В сочетании с предельно стабильной и прочной конструкцией машины это открывает широкий спектр возможностей для ее применения.
Эффективная технология измельчения древесины
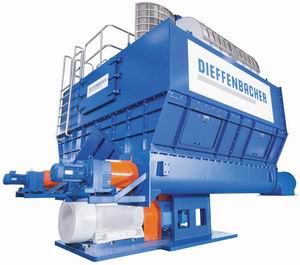
Измельчитель древесины ClassiSizer
Один из конкретных примеров эксплуатации ClassiSizer - производство летучей пыли, которая затем сжигается как топливо. Сырьем в данном случае служат отходы производства плит (ДСП, MDF или OSB). Полученная из отходов древесная пыль является дешевым и, кроме того, СО2-нейтральным топливом. Это экономически выгодная и экологически безвредная альтернатива природному газу и различным видам жидкого топлива.
Приведем для примера простой расчет. Средняя теплотворная способность 1 м3 природного газа составляет около 10 кВт·ч, теплотворная способность 1 кг абс. сухой древесной пыли - около 4,4 кВт·ч. Следовательно, 1 т древесной пыли позволяет заменить около 440 м3 газа. Если принять во внимание, что средняя цена газа для крупных европейских потребителей 0,33 евро за 1 м3, а средний эксплуатационный период энергоустановок - 7,5 тыс. ч в год, то получается, что при производстве 1 т абс. сухой древесной пыли в час будет сэкономлено 3,3 млн м3 природного газа (в денежном эквиваленте - более 1 млн евро).
Современные энергоустановки наряду с колосниковой решеткой оснащены, как правило, одной или несколькими пылевыми горелками для точного регулирования технологического тепла. Эти горелки зачастую являются гранульными и могут работать с относительно крупными частицами, размером до нескольких миллиметров. При этом энергоустановки и горелки сконструированы таким образом, что частицы полностью сгорают в пламени, за счет чего достигается максимально полное использование тепловой энергии, получаемой от сгорания древесного гранулята, а остаточная зольность, являющаяся следствием неполного сгорания топлива, сводится к абсолютному минимуму.
На старых заводах часто встречаются газовые горелки. И если там планируется замена газа на пыль, то требования к максимальному размеру частиц значительно строже. Для достижения максимальной эффективности сжигания летучей пыли ее частички должны быть меньше 1 мм, причем по возможности на 100%.
Фирма В. MAIER Zerkleinerungs-technik GMBH («Б. МАЙЕР Техника измельчения ГМБХ»), отвечающая внутри группы компаний Dieffenbacher за участок подготовки материала, предлагает решение, соответствующее самым высоким требованиям. ClassiSizer, благодаря особой конструкции ударной камеры и сит, позволяет экономичное одноступенчатое производство древесной пыли с размером частиц меньше 1 мм. В качестве сырья могут использоваться самые разные производственные отходы: опил (OSB), мелкая фракция, обрезки окантовок, шлифовальная пыль, а также плиточный бой. Кроме того, исходным материалом также могут служить пеллеты, брикеты, сухая и предварительно очищенная щепа из древесины вторичного использования.
Ведущие предприятия деревоперерабатывающей промышленности в Западной и Восточной Европе, а также по всему миру уже установили и успешно эксплуатируют такие установки. Используя ClassiSizer для производства древесной пыли, наши клиенты получают дополнительную выгоду за счет существенной экономии затрат на газ, значительно сокращают эксплуатационные расходы, повышая тем самым общую рентабельность предприятия.
Благодаря ClassiSizer предприятие, помимо экономически эффективного использования собственных отходов, получает еще одно важное преимущество: организовав собственное производство древесной пыли, оно обретает независимость от первичных топливно-энергетических ресурсов. Кроме того, переход на «зеленую» энергию сокращает «углеродный след» продукции, снижает затраты на утилизацию отходов производства.
Новые перспективы
Принцип ударного воздействия ClassiSizer может использоваться не только в деревообрабатывающей и пеллетной промышленности - сферах, которые традиционно являются профильными для группы компаний Dieffenbacher. Открываются новые области применения машины, прежде не входившие в основной фокус группы. Например, сегодня множество машин ClassiSizer эксплуатируется в биогазовых установках для подготовки различных органических субстратов - сырья для производства биогаза. В области переработки материалов вторичного использования ClassiSizer с успехом применяется для производства топливозаменителей из отходов с высокой теплотворной способностью, для измельчения отработанного электрического и электронного оборудования, легких строительных материалов, таких как гипсокартон или минеральное волокно, для подготовки композитных материалов.
ClassiSizer, как и все наше оборудование, непрерывно совершенствуется. В тесном сотрудничестве с клиентами постоянно осваиваются новые области применения измельчителя. При необходимости станок и его периферия приспосабливаются к индивидуальным задачам заказчика. Работа над совершенствованием машины поддерживается многочисленными испытаниями, которые проводятся в собственном современном технологическом центре Dieffenbacher в городе Эппинген (Германия).