Способы облицовывания кромок мебельных деталей
Настоящая статья посвящена нюансам работы с клеями-расплавами, способам нанесения клея и методам облицовывания кромок мебельных заготовок на стандартных станках, а также с помощью лазера и горячего воздуха - технологиям, которые в последнее время используются на мебельных предприятиях.
От качества облицовывания кромок мебельных деталей во многом зависит качество всего изделия. Кромки современной мебели могут облицовываться рулонными материалами толщиной от 0,2 до 3 мм (бумагой, пропитанной меламиновыми смолами, ПВХ и АБС) и полосовыми материалами толщиной до 25 мм (шпоном или рейкой из массивной древесины). Для приклеивания кромочного материала используются клеи-расплавы на основе EVA (этиленвинилацетата), APAO (аморфного полиальфаолефина), PUR (полиуретана), PA (полиамида).
Клеевые материалы для кромкооблицовывания
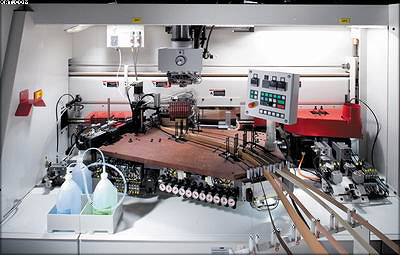
Клеевой узел и зона подачи кромки станка IMA Novimat
Выбор клея определяется его физико-химическими характеристиками, а также типом оборудования для облицовывания и кромкооблицовочного материала. Характеристики клея должны обеспечивать необходимые эксплуатационные показатели изготовленного с его использованием изделия. Наиболее широко применяются в мебельном производстве EVA-клеи. По мнению руководителя направления Durable Assembling в России и СНГ компании H. B. Fuller Александра Балашова, «основные достоинства EVA-клеев - доступность по цене и простота применения при высокой производительности оборудования и сохранении качества конечной продукции. Рецептура клеев на основе EVA в основном остается неизменной на протяжении последнего десятилетия. В нее вносят изменения только тогда, когда на рынке нет того или иного компонента клеевого состава». Говоря об основе клея, г-н Балашов отмечает: «Если раньше мебельные предприятия использовали составы на основе полиамида (ПА-составы), которые придавали клеевому соединению большую теплостойкость, то теперь подобные клеи востребованы мало и постепенно уходят с рынка. Причин малого спроса на них несколько. Цена за 1 кг такого клея крайне высока. У клеев на основе полиамида очень короткое открытое время, так как диапазон температуры между точкой размягчения и рабочей температурой весьма мал. И, как это ни парадоксально, для клеев с высокой теплостойкостью у ПА-составов не совсем хорошие показатели стабильности в расплавленном состоянии: они меняют свои характеристики при длительном воздействии повышенной температуры».
Кроме основного полимера, в состав клеев могут входить различные наполнители, модификаторы, стабилизаторы и т. д. Помимо наполненных и ненаполненных клеев-расплавов, производители могут предлагать материалы с разной долей наполнителя в клеевом составе. По количеству наполнителя в составе материалы бывают малонаполненные (плотность 1,05-1,1 г/м3), средненаполненные (плотность 1,2-1,4 г/м3) и наполненные (плотность >1,4 г/м3). Эту классификацию можно назвать «внутренней», так как подобных ГОСТов и терминов в нашей стране до сих пор нет. Быстро определить при приемке партии клея, наполненный он или нет, можно двумя способами. Первый - визуальный, по цвету: ненаполненный клей будет прозрачным, малонаполненный - полупрозрачным, а наполненный - молочно-белым. Второй способ - по плотности: плотность ненаполненного клея меньше плотности воды (<1 г/см3). Поэтому, если опустить небольшое количество ненаполненного клея в стакан воды, такой клей всплывет. Чтобы узнать степень наполненности клея, проводят лабораторные тестирования с целью определения плотности продукта.
От плотности клея зависит его расход. Наполненные составы стоят дешевле ненаполненных, чем и привлекают потребителя. Однако сэкономить не получится: чем выше плотность клея, тем больше его расход. И, следовательно, больше себестоимость продукции в расчете на один погонный метр изделия, для облицовывания которого использован клей.
На заметку производителю мебели
Качество приклеивания кромки во многом зависит от правильного подбора клеевого материала, материала мебельной кромки, условий и способа клеенанесения, параметров работы кромкооблицовочного оборудования и его настройки.
Для получения клеевого соединения с требуемыми характеристиками производители клеев рекомендуют обращать внимание на рабочую температуру клея-расплава, температуру склеиваемых детали и кромки, воздуха в рабочем помещении, а также на усилие прижима. Продакт-менеджер компании Kiilto Oy Антон Родионов отмечает, что в технических характеристиках производители указывают вязкость клея и точку размягчения. Эти параметры необходимы при настройке станка и корректировке режима работы на нем. Например, у клея-расплава «Кестомелт С213» вязкость при 200°С - 90 000 мПа•с и точка размягчения - 100°С; у «Кестомелт С185» вязкость при 180°С - 68 000 мПа•с, при 200°С - 42 000 мПа•с, а точка размягчения 100°С. Если эти параметры не соблюдать, приклеить кромку к детали не получится.
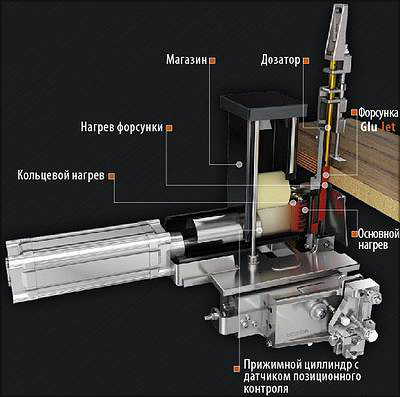
Расход клеевых материалов (КМ) также определяется качеством облицовываемой панели (для заполнения рыхлого среза древесной плиты требуется больше клея); скоростью подачи на станке (при высокой скорости на облицовываемую поверхность состава наносится меньше), способом нанесения (при вальцовом расход больше, чем при нанесении форсунками).
«Для приклеивания толстой кромки к рыхлой ДСП мебельщики в основном используют наполненные клеи-расплавы, - делится опытом руководитель отдела активных продаж компании «Эрготек» Евгений Малышевский. - Затраты на клей в этом случае минимальные. У наполненного клеевого состава высокая плотность за счет введенных в него добавок. Однако при одинаковой массе наполненного и ненаполненного клея-расплава объемы будут отличаться (у наполненного он будет меньше, что обуславливает его увеличенный расход на один квадратный метр). Ненаполненные клеи-расплавы применяются, когда необходимо приклеить прозрачную и цветную (например, черную) кромку, тонкую кромку при низкой температуре, а также облицевать кромку детали из плиты HDF».
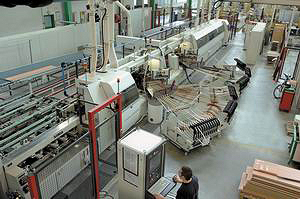
Станок для облицовывания кромок IMA Combima с
несколькими клеевыми узлами и магазинами для кромки
на 72 рулона
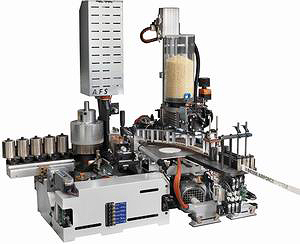
Узел нанесения кромочного материала на станках Biesse.
Внутри одного узла установлены две системы. На станке
можно облицевать кромки как с применением клеев-
расплавов и традиционных кромочных материалов, так
и горячего воздуха (система AFS) и кромочных
материалов типа Laser Edge
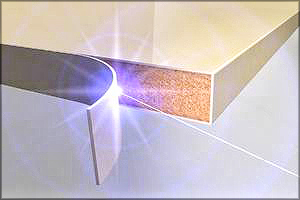
При работе с EVA-расплавами, в том числе с клеями homakoll 663, homakoll 635, homakoll 612, которые выпускает компания «Группа "ХОМА"», важно периодически контролировать температуру клея на роликах. Если она ниже рекомендуемой для применения, это приведет к сокращению времени схватывания клея и в конечном результате к некачественному склеиванию. При температуре клея на роликах выше рекомендуемой клей может разлагаться с изменением цвета, вязкости и ухудшением клеящих свойств. Склеивание холодных или влажных поверхностей может привести к дефектам склеивания в связи с сокращением периода схватывания клея. Для каждого производства следует проводить пробные испытания клеевых материалов с учетом условий склеивания и типов соединяемых материалов. В случае применения клеев-расплавов на основе PUR расход уменьшается почти в два раза, по сравнению с клеем-расплавом на основе EVA.
Рабочая температура является одним из важных параметров приклеивания кромки к заготовке. Ее превышение в течение длительного времени отрицательно сказывается на характеристиках клея и может привести к его деструкции, а следовательно непригодности для использования. Если рабочая температура клея ниже той, какую рекомендуют производители, уменьшается адгезия, а вязкость клея повышается. На качество облицовывания оказывает влияние и температура склеиваемых поверхностей - плиты и кромочного материала (рекомендуемая температура должна быть не ниже 18°С).
Если детали или кромку, поступившие на участок кромкооблицовки с холодного склада, предварительно не выдержать в цехе, то расплавленный клей при нанесении на склеиваемые поверхности быстро остывает, что не позволяет гарантировать должного качества приклеивания материала к поверхности. А это уже считается дефектом. Кроме того, важно правильно установить скорость подачи клея с учетом его открытого времени. Если используется клей с коротким открытым временем, то необходима высокая скорость подачи заготовки. Невысокая скорость подачи устанавливается при работе с клеем, у которого длинное открытое время. При небольшой скорости клей с коротким открытым временем до момента прижатия кромки успевает сильно охладиться, в результате чего снижается его адгезия. В технической характеристике, прилагаемой к клею, производитель указывает рекомендуемое усилие прижима, от которого также зависит, будут ли обеспечены требуемые параметры смачивания и адгезии.
По словам специалиста компании «Сфинкс» (официального дистрибьютора компании Henkel) Алексея Савченко, «при работе с тонкими, "капризными" пленками ПВХ и АБС используют низкотемпературные клеи-расплавы. Для решения подобных задач компанией Henkel разработаны специальные продукты: "Техномелт КС 224/2" и "Техномелт КС 250". Клеи на основе полиолефина (например, "Техномелт КС 300") обладают повышенной морозостойкостью и теплостойкостью (до 120°С), а также адгезией при наклеивании кромки на MDF. Указанные достоинства становятся еще более явными с учетом более низкой цены по сравнению с полиуретановыми клеями-расплавами, для применения которых также требуется специализированное оборудование». В дополнение к клеевым материалам серии «Техномелт» компания Henkel предлагает разные сервисные продукты, а именно очистители от клеев-расплавов. Жидкий очиститель «Техномелт Cleaner M-O-C» распыляют на остывшие части оборудования и остатки клея, что позволяет значительно облегчить удаление этих остатков. Гранулированный очиститель «Техномелт PUR Cleaner 4» предназначен для очистки клеевых ванн, клеепроводящих шлангов и каналов, а также клеенаносящих элементов (форсунок, роликов и т. д.) от клея-расплава. Очиститель окрашен для удобства в синий цвет, расплавляется непосредственно в оборудовании и в дальнейшем остатки очистителя удаляются вместе с нагаром. Рекомендуется регулярно проводить очистку для уменьшения риска простоев оборудования и снижения трудоемкости производства.
Оборудование для приклеивания кромки
установленного на российских предприятиях
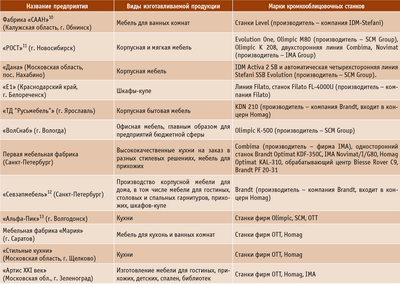
Современная мебель - это множество деталей, для приклеивания кромки на которые на предприятии может использоваться весь арсенал кромкооблицовочного оборудования, начиная с ручных кромкооблицовочных машинок и заканчивая высокопроизводительными линиями и обрабатывающими центрами. За годы работы представители нашего журнала побывали на множестве разных деревообрабатывающих предприятий, в том числе и мебельных, расположенных в Московской области, Краснодарском крае, в Ярославле, Вологде, Санкт-Петербурге и т. д. Рассказывая читателям о подобных производствах, мы особое внимание обращали на то, какое оборудование (марки, производитель) на них установлено и как оно подбиралось (что учитывалось, что повлияло на выбор), ведь от его уровня и возможностей, от правильной настройки и эксплуатации зависит качество продукта, который поступает в мебельные магазины. На российском рынке представлено оборудование иностранных компаний Felder, Casadei, Griggio, SCM Group, Paolini, Homag, IMA, Cehisa, Filato, Holz-Her, Italmac, Vitap, Altesa, OTT, Egurko, Olimpic, Biesse, Hebrock, Viritex, Adamik, Sietro, а компания Vita Group, помимо европейских брендов, предлагает станки отечественного завода «Станковита», который входит в ее состав.
Как правило, конструкция и принцип работы всех «кромочников» схожи, а станки могут отличаться числом тех или иных узлов. Производственниками в соответствии с задачами каждого предприятия выбирается станок, который может быть оснащен дополнительными узлами и устройствами. В табл. 1 представлены некоторые марки кромкооблицовочных станков, которые эксплуатируются на российских мебельных предприятиях.
Выбирая «кромочник» , специалисты советуют обращать внимание на его производительность, толщину обрабатываемого материала, тип кромки, а также на то, будет ли в процессе использоваться кромка с уже нанесенным клеем, или станок наносит клей сам.
Рассмотрим нюансы методов нанесения клея на кромку детали на примерах работы оборудования нескольких производителей: IMA, Biesse, OTT, Holz-Her, Felder, Altesa и «Станковита».
основе EVA для прямого кромкооблицовывания и рекомендуемые
условия работы с ними
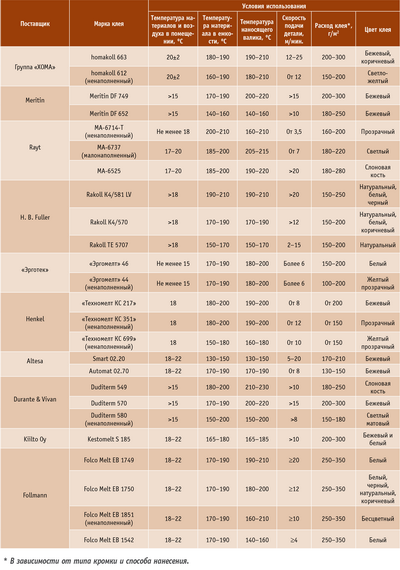
На всех станках фирмы IMA пользователь может работать как с клеем EVA, так и с клеем PUR. При работе с клеем EVA на проходных станках гранулят нагревается в клеевой ванне электрическими нагревательными элементами (ТЭНами) до рабочей температуры (120-200°С) и при помощи вращающегося клеенаносящего вальца клей переносится на торец проходящей мимо ролика заготовки. Скорость вращения ролика и подачи заготовки синхронизирована таким образом, чтобы клей не размазывался, а равномерно наносился на край детали. В зависимости от типа станка используется клеенаносящий валец необходимого диаметра (для станка Advantage - 30 мм, для Novimat - 60 мм). Ведущий специалист компании «ИМА-рус» Сергей Панферов подчеркивает, что использование клеевого вальца с большим диаметром позволяет стабильно наносить на кромку (торец) детали необходимый объем клея при значительной длине и ширине заготовок и обеспечивать при этом минимальную толщину клеевого шва.
Клеевой валец постоянно вращается, отдавая клей на торец заготовки и забирая новый клей из клеевой ванны. Деталь, двигаясь по конвейеру, соприкасается с копиром клеевой ванны, при этом сам валец детали не касается. Задача оператора - настроить станок так, чтобы при минимальной толщине клеевого слоя на заготовку перенеслось столько клея, сколько требуется для надежной фиксации кромочного материала. Объем клея на вальце регулируется эксцентриковыми заслонками, в зависимости от типа материала и размера заготовок бывает необходимо увеличить или уменьшить толщину клеевого шва (рыхлые материалы впитывают клея больше, плотные - меньше). На станках IMA работа оператора упрощается: клеевая ванна оснащена специальным копиром, перемещением которого задается расстояние между заготовкой и клеенаносящим вальцом.
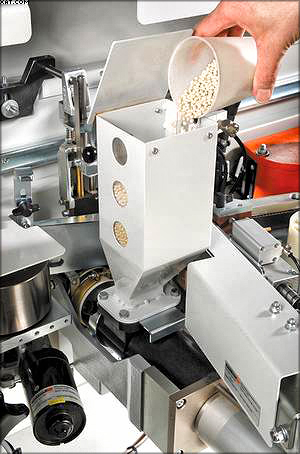
Клеевая станция Glu-Jet, которая устанавливается на
кромкооблицовочное оборудование Holz-Her
На всех марках станков IMA время готовности клеевой станции EVA-клея примерно одинаковое: 15-20 мин. с момента включения. Разные модели клеевых станций IMA схожи по конструктиву и невелики по объему (0,7-0,8 л). Если уровень клея в ванне снижается, автоматически по команде датчика из зоны предварительного расплава или из бункера с гранулятом добавляется какое-то количество клея. При работе с EVA- или PUR-клеем для замены клеевых ванн требуется 1-2 мин., а для нагрева установленной на станок ванны - 10-15 мин. Решить эту проблему помогают специальные столы, поддерживающие сменные клеевые ванночки в подогретом состоянии, что дает возможность приступить к работе сразу после установки новой ванны.
На станках, производимых компанией Biesse, при прямом кромкооблицовывании клей наносится на панель при помощи клеевого ролика, а в случае использования PUR-клея может быть применена система с форсунками компании Nordson. По словам менеджера компании Biesse в России Василия Амалицкого, «при использовании клеевого ролика регулировка количества подаваемого на панель клея выполняется вручную за счет изменения ширины зазора между специальной пластиной и клеевым роликом. Если для нанесения PUR-клеев используется система с форсунками, то регулировка количества клея происходит автоматически. Время, затрачиваемое на разогрев клеевого материала, зависит от многих факторов, таких как количество клея, температура на предприятии и тип клея, но составляет от 5 до 15 минут. При наличии запасной клеевой ванны и клеевого ролика переход с клея одной основы на другую (или с клеевого материала одного цвета на другой) осуществляется за пять минут».
В кромкооблицовочных станках Holz-Her устанавливаются специальные системы клеенанесения. «Кромочники» Holz-Her комплектуются магазином для гранулированного клея-расплава или картриджами. В клеевой системе 1905/1906 под высоким давлением клей-расплав через форсунки наносится на кромку детали, что позволяет снизить расход клеевого материала по сравнению с вальцовым нанесением. Клеевой шов получается тонким и прочным. В клеевой системе не образуются нагары, так как количество расплавляемого в ней клея определяется его расходом. Клеенанесение с помощью картриджной системы ускоряет процесс смены магазина с клеем. Например, при замене клеевого материала одной основы другой (например, PUR вместо EVA) или клея одного цвета на клеевого материала другого цвета. Время разогрева системы клеенанесения всего 3,5 мин., что обеспечивает высокую производительность станка. Нагрев клея-расплава и металлического сопла в системе Glu-Jet кромкооблицовочных станков Holz-Her занимает 3 мин. (что позволяет снизить потребление электроэнергии на этой стадии процесса до 2 кВт). Затем горячий клей поступает на дозирующее устройство и через щелевое сопло наносится на кромку мебельной плиты.
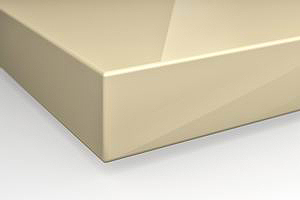
Древесная плита, кромки которой облицованы
материалом Raukantex Laser Edge (Rehau)
При работе на станках завода «Станковита» минимальный расход клея обеспечивается глубиной рифления клеенаносящего ролика, регулировка подачи клеевого материала осуществляется перемещением скребка, удаляющего излишки клея с клеенаносящего ролика. На разогрев клеевого расплава до рабочей температуры уходит 20 мин. Замена клея возможна только при полной очистке бачка механическим способом, что предполагает демонтаж клеевого узла и его частичную разборку. Такая процедура может длиться до четырех часов.
При оценке качества изделия в первую очередь обращают внимание на его внешний вид. Стык кромочного материала и ЛДСП должен быть малозаметен и не ощущаться на ощупь. Щели на стыке недопустимы, так как нахождение изделия во влажной среде приведет к проникновению влаги внутрь ЛДСП и ее разбуханию, кроме того, в составе связующего, используемого для производства ЛДСП, есть свободные фенол и формальдегид, которые могут попасть в воздух через щели. Особое внимание должно уделяться качеству приклеивания кромочного материала, особенно в зимнее время, при работе в плохо отапливаемом цехе или при обработке плит ЛДСП, хранящихся в неотапливаемом помещении. Следствием работы в таких условиях может стать отслаивание кромочного материала спустя какое-то время после приклеивания кромки.
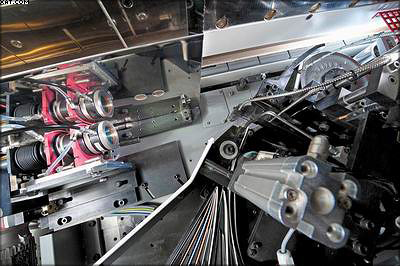
Узел нанесения кромочного материала с помощью лазера на станке IMA
Novimat
Директор по развитию компании «Интервесп» Сергей Жданов рассказывает, что для приклеивания прямой кромки к мебельным деталям компания «Интервесп» предлагает станки Altesa серии Advantage, а также оборудование SCM Group и Italmac. Выбор той или иной модели зависит от объемов производства и вида выпускаемой продукции. Помимо односторонних станков, на предприятиях, где серийная мебель изготавливается в больших объемах, целесообразно устанавливать двухсторонние «кромочники», например, производства SCM Group. При выборе станка для приклеивания прямой кромки важно учитывать несколько параметров: число выполняемых на нем операций, скорость подачи, тип крепления узлов (на станине либо в подвешенном состоянии), возможность подачи очищающей жидкости перед полировкой, тип подающего механизма кромки, а также скорость и удобство перенастройки станка при необходимости использования разных типов кромки. Скорость перенастройки на станках Advantage модели Euro выше, чем на оборудовании стандартной модели Advantage. Ориентировочное время перехода на станках модели Euro с кромки толщиной 0,4 мм на кромку толщиной 2,0 мм и наоборот - 1-3 мин., а на станках стандартной серии - 3-5 мин. Кроме того, скорость перенастройки станка зависит от квалификации оператора.
При кромкооблицовывании следует обращать внимание в первую очередь на тип прижима (механический или пневматический) и число прикатных роликов (от двух до пяти). Сергей Жданов рассказывает: «Клей-расплав на всех популярных станках, предлагаемых нашей компанией, наносится рифленым роликом вальцовым способом. Узел клеенанесения состоит из клеевой ванны и приводного вала, по которому клей поднимается из клеевой ванны и наносится на деталь. На станках Altesa расход клея регулируется специальной шторкой при помощи поворотной рукоятки, которая дает возможность настроить станок на минимальную подачу, что позволяет добиться почти невидимого клеевого шва».
Нанесение клея в станках Felder осуществляется на заготовку (торец древесной плиты). Расход клея контролируется с помощью регулировочного винта, вращение которого по часовой стрелке или против нее влияет на подачу клея. «Наши станки оснащены объемной клеевой ванной с несколькими ТЭНами для разогрева клея, что позволяет сократить время разогрева клея до восьми минут, - поясняет ведущий менеджер компании Felder в Москве Константин Шумилов. - У ванны толстое тефлоновое покрытие (как у сковороды Tefal) - чтобы клей не пригорал, быстрее разогревался и можно было удалять старый клей». Сокращение времени на разогрев позволяет сократить и время ожидания после включения станка. Продолжительность замены клея-расплава зависит в первую очередь от особенностей производства. Перед использованием нового расплава обязательны очистка и обслуживание ванны. За смену может быть использовано несколько клеевых ванн. По мнению г-на Шумилова, при бесклеевой технологии качество облицовывания выше, чем при кромкооблицовывании по традиционной технологии. Однако сегодня бесклеевая технология не востребована, так как кромочный материал и оборудование очень дороги.
По мнению специалистов австрийской фирмы OTT, получить незаметный клеевой шов можно не только с применением бесклеевого метода. Результатов, сопоставимых по качеству облицовывания кромок заготовок, можно достичь, если довести до совершенства традиционную систему подготовки и нанесения клея. В кромкооблицовочных станках OTT применяется запатентованная клеевая система CombiMelt, главными особенностями которой являются модульная конструкция и автоматическое дозирование клея.
Для всех выпускаемых сегодня форм клея - гранулы, патроны, блоки - разработаны быстросъемные накопители, в которых происходит предварительное плавление клея. Клеевая головка и валец также съемные, что существенно облегчает доступ ко всем поверхностям для их обслуживания и очистки. Потребитель может выбирать разные виды клея и с помощью системы управления быстро находить оптимальный режим их использования: температуры, дозирование, скорости вращения. Оператор с пульта может вносить корректировки в зависимости от температуры в цехе, партии клея, свойств облицовываемых материалов. В отличие от станков других марок, здесь не требуется вручную, с помощью ключа или отвертки, регулировать количество наносимого на деталь клея - управление дозированием осуществляется путем нажатия виртуальных кнопок на сенсорном экране.
«Наиболее высокого качества можно достичь при применении полиуретановых клеев, для работы с которыми не требуется устанавливать дополнительные опции на кромкооблицовочные станки OTT», - подчеркивает Олег Новиков, генеральный директор официального дистрибьютора ОТТ в России компании Novimex.
Иногда для модернизации производства с целью повышения его производительности и качества выпускаемой продукции достаточно заменить узел клеенанесения. Этот вопрос могут решить компании, занимающиеся изготовлением клеевых систем. Хорошее оборудование прослужит много лет при своевременном обслуживании. Как отмечает генеральный директор компании «Робатех Рус» Елена Вранцева, «при работе с термоклеем может образовываться нагар на внутренних деталях системы клеенанесения. Производители подобных систем рекомендуют проводить их периодическую профилактику. У своих заказчиков мы ежегодно выполняем очистку систем клеенанесения, а если на систему приходится повышенная нагрузка (двух-трехсменная), то очистку выполняем не реже двух раз в год. Такое обслуживание помогает продлить срок службы оборудования на десятки лет. Самое старое оборудование, которое работает сегодня и обслуживается нашей компанией на территории России, выпущено в 1992 году».
Для интеграции клеевых систем в оборудование для облицовывания кромок необходимо подобрать компоненты в соответствии с задачами производства. Успех интеграции напрямую зависит не только от характеристик клеевой системы, но и от квалификации специалистов, занимающихся интеграцией. Станок можно довольно легко дооснастить типовыми системами. Монтаж и настройка занимают один-два дня.
Довольно часто при переходе предприятия с одной группы клеев на другую приходиться решать задачи по модернизации производства.
Используемые при кромкооблицовывании EVA и PUR - клеи с разной основой. В отличие от EVA-клеев, плавление PUR-клеев осуществляется в герметичных баках. До недавнего времени считалось, что для каждого типа клея необходимо использовать определенный тип оборудования. С 2010 года в ассортименте компании Robatech появились универсальные клеевые системы, позволяющие работать как с PUR-, так и с EVA-клеем.
На производстве стремятся к снижению затрат на расходные материалы, в том числе и клей. «Снижения расхода клея можно добиться, только пересмотрев технологический процесс производства изделия, - утверждает г-жа Вранцева. - Расход клея задает технолог производства, который проводит тесты, исследования, рассчитывает, сколько клея нужно для склеивания конкретных изделий и какой именно способ клеенанесения надо использовать: например, щелевой вместо вальцового. Щелевая головка позволяет добиться значительной экономии клея и повысить качество клеевого слоя».
Бесклеевое кромкооблицовывание
Несмотря на то что использование клея для приклеивания мебельной кромки остается востребованным, в последние несколько лет появилась возможность облицовывать кромки мебельной детали с применением лазера, плазмы и горячего воздуха.
В Германии, где была разработана эта технология, многие мебельные предприятия используют для кромкооблицовки лазерные станки. Как заявляют производители мебели, клеевой шов получается невидимым, прочным и герметичным, что важно при эксплуатации мебели для ванных комнат и кухонь. Использование двухслойной лазерной кромки исключает из процесса кромкооблицовки операцию нанесения клея. Клей содержится в одном из слоев кромки. Помимо расходных материалов экономится энергия. Потребляемая мощность лазера значительно ниже потребляемой мощности клеенаносящего агрегата (например, в рабочем режиме 3 вместо 13 кВт).
Как происходит склеивание, подробно рассмотрим на примере работы оборудования компании IMA. В станках этого производителя используется лазерная система на базе фокусирующих линз с проецированием лазерного луча в зону приклеивания кромочного материала к заготовке, что позволяет работать с панелями толщиной более 50 мм на высокой скорости подачи (более 30 м/мин.) с гарантированным качеством. В зависимости от высоты используемого кромочного материала и скорости подачи подбирается лазер необходимой мощности, как правило от 3 до 12 кВт. Для кромкооблицовки используется кромочный материал с праймером. Технология кромкооблицовки состоит из четырех этапов. На первом этапе на внутренней стороне кромки активируется праймер с помощью лазерной установки. Затем его кинестетическая энергия преобразуется в тепловую, функциональный слой кромочного материала плавится, и он приваривается к кромке детали. Возникает плотное сцепление кромочной системы и плиты, создающее монолитный внешний вид мебельных деталей и полную защиту материала, из которого они сделаны, от влаги. По словам ведущего специалиста компании «ИМА-рус» Сергея Панферова, «наиболее важное условие для обеспечения положительного результата - это стабильная работа всех агрегатов, начиная от фуговального и заканчивая плоскими циклями. При нанесении лазерной кромки нет клеевого шва, который компенсирует неточности работы всех агрегатов, поэтому IMA особое внимание уделяет конструкции агрегатов и их весу. Следует отметить, что для получения идеального результата при изготовлении мебельных фасадов недостаточно использовать только технологию Laser Edging, так как радиус кромки необходимо обработать сдвоенной профильной циклей и отполировать. Это особенно актуально для панелей High Gloss, в которых не должно быть видно разницы цвета на границе пласти и кромки детали».
.jpg)
Как правило, Laser Edging используют для топовой линейки продукции, будь то кухни или мебель для ванных комнат. В условиях сокращения партийности изделий и повышения гибкости производства технология Laser Edging будет набирать популярность. Далеко не каждое мебельное предприятие располагает собственным цехом покраски, обученным персоналом и складом лакокрасочных материалов, что делает более востребованной технологию «нулевого шва», которая не требует дополнительных площадей для организации самого процесса и места для хранения расходных материалов и выдержки готовой продукции. «Компания IMA первой вышла с лазерной технологией на рынки России и стран СНГ. Станки, которые используются для Laser Edging, успешно работают в Минске, Баку и Калининграде. Технология Laser Edging занимает 10-15% в общем объеме операций кромкооблицовки на мебельном предприятии», - рассказал г-н Панферов.
При приклеивании кромки на лазерных «кромочниках» сокращается время на подготовку оборудования к работе (не требуется разогревать клей) и техническое обслуживание (очистку или замену клеевого бачка), не затрачивается время на подбор расходных материалов (клея и кромки).
Другие способы приклеивания кромок к деталям основаны на использовании плазмы и горячего воздуха. На выставке ZOW в феврале 2011 года компания IMA впервые представила кромкооблицовочные устройства, в которых применялся плазменный нагрев вместо лазерного. Клеевой слой разогревался по всей ширине полосы плазмой, вытекающей из форсунок, которые могут быть расположены в один (четыре форсунки) или в два ряда (восемь форсунок). Но для этой технологии есть ограничения по типу кромочного материала и толщине обрабатываемых заготовок, а также по скорости подачи (до 25 м/мин.).
Компанией Biesse разработаны два узла для технологии так называемой бесклеевой кромкооблицовки: Air Force System STEP 1 и Air Force System STEP 2 (AFS). AFS STEP 2 может обеспечить кромкооблицовку на скорости до 25 м/мин. Такая система устанавливается на станки моделей Stream A и Stream B. Есть и упрощенная версия AFS Step 1, которая работает на скорости до 18 м/мин. и может быть установлена на станки класса Akron. Таким образом, бесшовная кромкооблицовка доступна для применения на предприятиях разного уровня при неизменно высоком качестве финальной продукции. Как рассказывает менеджер представительства компании Biesse в Москве Василий Амалицкий, «по сравнению с другими бесклеевыми способами, AFS обеспечивает наименьшие текущие затраты при высоком качестве облицованных кромок и особо высокой влагостойкости соединения. Узел AFS - это система, которая использует горячий воздух для расплавления функционального слоя кромкооблицовочного материала. До появления этой системы предприятия, которые хотели добиться отсутствия клеевого шва на панели после кромкооблицовки, были вынуждены тратить огромные деньги на закупку и использование лазерной системы, что не всегда было оправданно экономически. Безусловно, система, в которой используется горячий воздух, более проста в эксплуатации и обслуживании, а также более безопасна, за счет чего при работе по этой технологии достигается снижение расходов предприятия».
Качество и влагостойкость соединения обеспечиваются за счет равномерного прилегания кромки к панели и использования влагостойких материалов. Процесс кромкооблицовывания заключается в следующем: предварительно нанесенный на кромкооблицовочный материал функциональный влагостойкий слой плавится при помощи AFS. Затем благодаря воздействию прижимной системы расплавленный функциональный слой проникает в структуру древесной плиты и кромочный материал приклеивается к детали. На станках с системой AFS не требуется следить за какими-либо определенными параметрами процесса приклеивания кромки - все операции полностью контролируются ЧПУ. Включение и выключение узлов выполняется автоматически, в соответствии с выбранной программой. Можно предусмотреть также и автоматическую настройку всех обрабатывающих кромку узлов с помощью ЧПУ. В таком случае для перенастройки станка оператору не нужно вручную настраивать узлы. Большим плюсом является отсутствие необходимости настраивать станок на определенное количество подаваемого клея (функциональный слой уже нанесен на кромкооблицовочный материал). Это позволяет оператору работать, не заботясь о дополнительной настройке станка в процессе приклеивания кромки, как этого требует стандартная клеевая система. Станки с системой Air Force сегодня работают в Краснодарском крае и Московской области.
В кромкооблицовочное оборудование, выпускаемое российским заводом «Станковита» (в том числе в станки «Бурлак 6.3 LE»), может быть встроена система HASY (Hot Air System for Laser Edge), принцип работы которой основан на воздействии горячего воздуха, поступающего под давлением по термоизолированному каналу через сопло непосредственно к месту приклеивания кромочного материала Laser Edge. Горячий воздух под давлением по термоизолированному каналу поступает в сопло. Весь узел защищен, чтобы обеспечить безопасность оператора. Система устройства сопла позволяет регулировать ее высоту для достижения идеального рабочего положения в каждой конкретной ситуации.
Екатерина МАТЮШЕНКОВА
Комментарий специалиста
Рассказать о развитии технологий бесклеевого кромкооблицовывания мы попросили руководителя направления «Мебельные комплектующие» компании Rehau по Восточной Европе Владимира Минакова.
- Скажите, пожалуйста, насколько востребованы в нашей стране кромочные материалы Laser Edge?
- Кромочные материалы для бесклеевого применения пока слабо представлены на российском рынке. В отличие от Европы, у нас станки бесклеевой технологии используют всего около десятка компаний. Однако есть предпосылки к тому, что в будущем число мебельных предприятий, на которых будет применяться эта технология, может увеличиться. Об этом говорят и растущий интерес со стороны ведущих производителей мебели, и тот факт, что отраслевые «законодатели мод» (например, МФ «Мария» или «Томские мебельные фасады») уже полным ходом осваивают бесклеевые методы. Поэтому сегодня тенденция к внедрению этой технологии сохраняется, хотя и несколько замедлилась в связи с резко изменившейся экономической ситуацией.
- В условиях снижения затрат на расходные материалы, в том числе на мебельную кромку, в какой мере ваша продукция доступна российским мебельным предприятиям?
- Компания Rehau предлагает довольно широкий ассортимент кромочных материалов: есть продукты как премиум-класса, так и базовые продукты европейского производства.
Что касается материалов для бесклеевых методов, то здесь текущие изменения рынка носят двоякий характер. С одной стороны, оптимизируя затраты на мебельные комплектующие, производители неизбежно начинают пересматривать сметы и пересогласовывать некоторые закупки. С другой стороны, многие серьезные компании рассматривают кризис как период для реализации новых возможностей, прежде всего для привлечения внимания клиентов к мебели из другого сегмента рынка. Например, те, кто раньше специализировался на недорогой мебели, запускают линейки мебели премиум-класса, рассчитанные на покупателей дорогой и элитной мебели. Ведь ни для кого не секрет, что сегмент high end мебельного рынка просел не так сильно, как mid и low. Все хотят чем-то выделиться, получить дополнительные конкурентные преимущества. Мебельщики, готовые инвестировать в свой бизнес, могут вложить средства в бесклеевую технологию и на изломе кризисной волны выйти в лидеры в этом нишевом сегменте.
- Для приклеивания мебельной кромки к детали широко используются клеи-расплавы (на основе EVA, PUR, APAO). Как вы считаете, сможет ли бесклеевая технология вытеснить клеи-расплавы? Как скоро мебельщики будут готовы перепрофилировать свои производства? Оправданы ли затраты на лазерные кромочные материалы и лазерные станки?
- Полностью вытеснить технологию, которую использовали на протяжении 50 лет, бесклеевой метод не сможет, но свою долю на рынке, бесспорно, займет. Аналогию можно провести с меламиновой пленкой - все знают, что термопластичный кромочный материал лучше меламина, однако это не мешает последнему пользоваться устойчивой популярностью.
В Германии, где были разработаны бесклеевая технология и кромочные материалы, большое число фабрик уже инвестировали в разные станки, на которых можно наносить кромку без использования клея (при помощи лазера, горячего воздуха, инфракрасных лучей или плазмы). Некоторые производители приобрели новое оборудование, другие просто дооснастили существующие линии кромкооблицовывания. Идти путем зарубежных коллег или нет, российские мебельщики должны решать сами. Однако совершенно очевидно, что метод бесклеевой кромкооблицовки - это следующий шаг в развитии отрасли, и те компании, которые уже делают его, на данный момент смотрятся выигрышнее конкурентов.
Важно, что затраты на станки бесклеевой технологии и соответствующие кромочные материалы оправдываются качеством готовой мебели. Детали, облицованные этим способом, отличаются высокой устойчивостью к воздействию влаги и пара, соединение кромки не загрязняется и не выцветает, за счет чего конечное изделие дольше сохраняет первозданный вид и радует глаз владельца.