История фанеры. Часть 2
От послевоенных лет до нашего времени
Эпохой фанеры называли первые послевоенные годы в США. С окончанием военных действий в 1945 году экономика этой страны постепенно становилась на мирные рельсы. 1950–1960-е годы стали для производителей фанеры в Канаде и США периодом процветания. Недорогого сырья было в избытке, а средний диаметр сосны Дугласа, из которой в основном производилась фанера, превышал 73,66 см. Фанерные заводы росли как грибы.
С начала 1960-х и до начала 1980-х годов в США было построено около 70 фанерных заводов. Производители оборудования просто не успевали за растущей потребностью в лущильных станках, прессах, сушилках. Одна только компания CОЕ поставила около 125 лущильных станков и 175 сушилок для удовлетворения потребностей отрасли.
Производители фанеры старались убедить строителей, инженеров и архитекторов использовать фанеру вместо пиломатериалов. Этот материал рекламировался в журналах. Были распространены пособия по использованию фанеры в строительстве. Для привлечения потенциальных потребителей разрабатывались разные виды фанеры. Громадными тиражами издавались книги с подробными планами кухонных шкафов, книжных полок, кроватей, садовой мебели и прочих изделий из этого материала. Фанера пропагандировалась как идеальный материал для строительства парусных судов, прогулочных катеров и лодок.
Лущение шпона на заводе по производству фанеры 1950-е годы (США)
Под давлением производителей государственные регулирующие органы и строительные инспекции США и Канады включили фанеру в нормативные строительные документы. Казалось, ничто не угрожает стремительному росту объемов производства фанеры из года в год. Первый тревожный звонок для производителей прозвучал в начале 1960-х. Ситуация с лесными ресурсами в США стала меняться к худшему. Интенсивные лесозаготовки привели к тому, что с 1962 года объемы заготовок сырья большого диаметра стали неуклонно сокращаться, росла его стоимость. Только с 1962 по 1982 год фанерный кряж подорожал почти в пять раз.
Заголовок статьи в американском журнале о достоинствах и недостатках фанеры и OSB, изображавший фанеру и плиту OSB в виде спортсменов, сошедшихся в боксерском поединке, 2005 год
Но самый ощутимый удар по фанерной промышленности нанесло появление на рынке плит OSB. Они были запатентованы в 1965 году, а в 1970-е годы началось их промышленное производство. Сначала фанера и плиты OSB конкурировали за долю рынка. Противостояние было жестким, как на боксерском ринге.
В 1980-е годы плиты OSB стали использоваться для устройства стен и крыш. Производители фанеры старалась изо всех сил отбиваться, и фанера все еще применялась для устройства полов, но конкурировать с плитами OSB, которые были дешевле, оказалось сложно. Тем не менее в ряде случаев фанера отвоевывала утраченные позиции. Так, после того как в 1992 году ураган Эндрю пронесся над Южной Флоридой, оставив более 250 тыс. человек без крова и причинив штату почти $30 млрд ущерба, Совет комиссаров округа Майами-Дейд запретил использование плит OSB в качестве материала для обшивки крыши.
В 2000 году объем производства плит OSB незначительно превысил объем производства фанеры. В настоящее время доля плит OSB в общем объеме выпуска плитных материалов в США достигла 75%.
Несмотря на то что плиты OSB доминируют на рынке строительных материалов, многие подрядчики и строители остались верными фанере. Возможно, потому, что она все еще воспринимается как более высококачественный материал. Кроме того, у фанеры текстура натуральной древесины и она как нельзя лучше подходит для индивидуального домостроения.
Конкуренция плит OSB подстегнула производителей фанеры во всем мире к поиску новых технологий, клеев, сфер применения фанеры, разработке нового оборудования и автоматизации технологического процесса. Если в целом технологический процесс производства фанеры остался неизменным, то в плане оборудования для ее производства в конце 1970-х годов был достигнут очевидный прогресс. Фирма СОЕ, ведущий на то время производитель оборудования в США и мире, разработала лущильные станки, в которых поддерживающие ролики были приводными (бесшпиндельный лущильный станок J.F. McCarroll, США, запатентованный еще в 1934 году, был чрезвычайно сложным, одних только поддерживающих роликов с цепным приводом в нем было пять). Позже вместо прижимной линейки с нажимной гранью в станках этой фирмы стал использоваться приводной обжимной рифленый ролик. Такое техническое решение позволило лущить довольно мягкую древесину, не опасаясь провертышей, так как усилие вращения передавалось на чурак не только шпинделями станка, но и обжимным и поддерживающими роликами. Также специалисты СОЕ сконструировали компьютеризированное Х–У центровочно-загрузочное устройство, систему гидравлического привода суппорта.
Фанера с тисненым резиновым покрытием и фанера со звукоизолирующим и виброгасящим слоем
Середину 1970-х годов можно считать началом компьютерной эры в производстве фанеры. Фирма СОЕ разработала свой первый компьютеризированный лущильный станок в 1978 году. Использование достижений научно-технического прогресса позволило повысить полезный выход и производительность лущильных станков более чем на 35%. Несколько позже к гонке технических достижений в области оборудования для производства присоединились финская Raute, японские Uroko, Meinan и другие.
Новый качественный рывок в разработке лущильных станков произошел в 1980-е годы, когда японские фирмы Uroko и Meinan запатентовали и стали производить станки для бесшпиндельного лущения. Конструкция этого оборудования позволила сократить диаметр карандаша до 35 мм и за счет этого повысить полезный выход шпона. Кроме лущильных станков, было значительно усовершенствовано и другое технологическое оборудование. На смену клеевым вальцам пришли сложные высокопроизводительные линии сборки пакетов с нанесением клея методом налива или распыления.
Росла и этажность горячих прессов. Появились 30-, 40- и даже 50-этажные прессы. Дальнейшее увеличение числа этажей ограничивалось необходимостью строить высокие производственные корпуса и делать глубокие приямки. Японская фирма Taihei пошла по иному пути и выпускает уникальные горизонтальные 200-этажные фанерные прессы.
Горизонтальный 200-этажный фанерный пресс фирмы Taihei (Япония)
В последнее время на европейских и американских фанерных заводах наметилась тенденция к снижению производственных издержек за счет автоматизации и роботизации производства. Роботы заменяют человека там, где это еще совсем недавно казалось невозможным – на участках сортировки и починки шпона и фанеры. Мало того, разрабатываются и успешно реализуются проекты фанерных заводов, на которых участие человека вообще сведено к нулю. Межоперационная логистика вместо вилочных погрузчиков осуществляется специальной конвейерной системой. Лидером здесь является испанская Biele.
В создании клеев для фанеры прогресс оказался не таким очевидным, как в техническом перевооружении. В конце 1970-х годов казалось, что с развитием химии полимеров водорастворимые карбамидо- и фенолоформальдегидные клеи рано или поздно будут вытеснены более совершенными клеями, например на основе изоцианатов. Однако этого не произошло. По соотношению «цена – качество» карбамидо- и фенолоформальдегидные клеи остаются вне конкуренции. Дело в том, что карбамид, фенол и формальдегид – самые дешевые из массово производимых химических реагентов.
Сейчас все чаще для приготовления клеевых составов (КС) используются смолы, фенолы и другие компоненты природного происхождения. Работы в этой области проводились и ранее, но дальше экспериментальных разработок и опытного применения дело не шло, и только сейчас смолы производятся в промышленных масштабах. Использование природных фенолов позволяет заменить нефтяные фенолы возобновляемыми реагентами. Фирма UPM (Финляндия) освоила синтез лигноформальдегидных смол BioBond на основе природного лигнина, получаемого в качестве побочного продукта при варке целлюлозы.
Во многих странах в последнее время проводятся исследования по созданию водостойких клеев на основе природных компонентов. И если раньше этим занимались в развивающихся странах, испытывающих дефицит химического сырья (Вьетнаме, Индии, Пакистане и др.), то сейчас и в США работают над созданием водостойких клеев на основе соевой муки. Происходит своеобразный возврат к технологиям начала прошлого века, что вызвано не столько соображениями экологии, сколько ростом цен на фенол и формалин.
«Стул мечты» Tadao Ando, выклеенный из шпона (Япония)
Для повышения конкурентоспособности фанеры продолжаются разработки ее специальных видов для разных сфер применения, превосходящие другие плитные материалы на основе древесины, такие как плиты OSB и ДСтП. По самым скромным подсчетам, разработано более 200 видов фанеры. Большинство их было запатентовано еще в первой половине XX века.
Фанера с самого начала прошлого века успешно применяется в автомобилестроении. Если и был период, когда по ряду причин фанера несколько сдала свои позиции в этой отрасли, то в последнее время, благодаря достижениям в технологии производства, она вновь стала востребованным материалом.
Фирма Metsa (Финляндия) производит большой ассортимент фанеры для автомобилестроения разных форматов, толщины и с разными характеристиками. Для автобусов финны разработали специальную огнестойкую фанеру Sonex со звукоизолирующим слоем из резины толщиной 2–3 мм. Помимо высокой прочности, легкости, огнестойкости и долговечности, эта фанера отличается прекрасными звукоизолирующими и виброгасящими показателями, что позволяет значительно снизить уровень шума в пассажирском салоне и кабине водителя без использования дополнительной звукоизолирующей обработки кузова.
Для изготовления полов трейлеров та же фирма выпускает высокопрочную ламинированную фанеру формата до 6000×2200 мм и толщиной от 15 до 27 мм, а также фанеру с тисненым резиновым покрытием.
Голландская фирма XXTrail изготавливает с использованием ламинированной фанеры небольшие трейлеры для перевозки лошадей. В названии модели, например, Jade Plywood, фигурирует материал, из которого они изготовлены: Plywood (фанера).
Трейлер производства XXTrail Jade Plywood для перевозки лошадей, 2011 года выпуска (Нидерланды)
Для автомобилестроения выпускается фанера, комбинированная с листами стеклопластика, металлизированная алюминием и сталью, покрытая листовыми пластиками ПВХ, ПНД, ПВД, HPL самых разных цветов и текстур.
Если до 1940-х годов использованию фанеры в изготовлении мебели не было альтернативы, то с началом промышленного производства ДСтП в 1950-е годы фанера постепенно стала сдавать позиции в производстве массовой, недорогой мебели. Однако она по-прежнему остается любимым материалом дизайнеров мебели, которые создают из нее настоящие шедевры.
Эксклюзивная авторская мебель из фанеры изготавливается в единичных экземплярах и стоит довольно дорого.
Фанера как нельзя лучше подходит для изготовления детской мебели, здесь ДСтП ей не конкурент. Только из фанеры можно изготовить легкую, прочную, экологически безопасную и одновременно красивую мебель.
Очень интересную детскую мебель из этого материала производит в России семейная компания Playply, основанная в 2013 году дизайнером Андреем Анисимовым и архитектором Марией Анисимовой-Карасик.
Детская мебель Playply (Россия), серия детской мебели Allison Holden (США)
Мебель Playply совмещает в себе минимализм и многофункциональность: ребенок может с комфортом отдыхать, хранить вещи, придумывать и разыгрывать истории приключений, не ограничивая свою потребность в движении. Оригинальные решения для детской комнаты раскрывают игровой потенциал пространства. Наравне с комфортом и безопасностью ребенка уделяется большое внимание внешнему виду мебели. Выверенные дизайнерские решения позволяют развивать у ребенка чувство прекрасного.
Американский дизайнер Эллисон Холден разработала серию детской мебели, предназначенной для стимулирования творческих способностей ребенка и игры. Серия включает плательный шкаф, стул и стол на колесах и неразъемный стол. Все части мебели изготовлены из березовой фанеры и могут быть легко собраны без инструментов.
Фанера нашла и не совсем обычное применение. Британский дизайнер Питер Рольф больше 10 лет работает с этим материалом. Начинал Питер с создания традиционной мебели для жилых помещений и офисов, шкатулок, потом решил попробовать совместить мебель со скульптурой. Современные технологии обработки материала, оборудование позволяют, что называется, разгуляться творческой мысли. На сайте дизайнера можно увидеть не только скульптурную мебель, но и интересные столы, стулья, комоды, шкатулки и прочие вещи. Это настоящий эксклюзив.
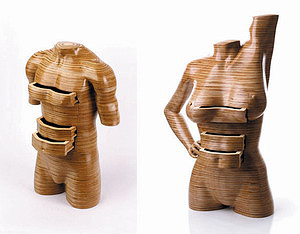
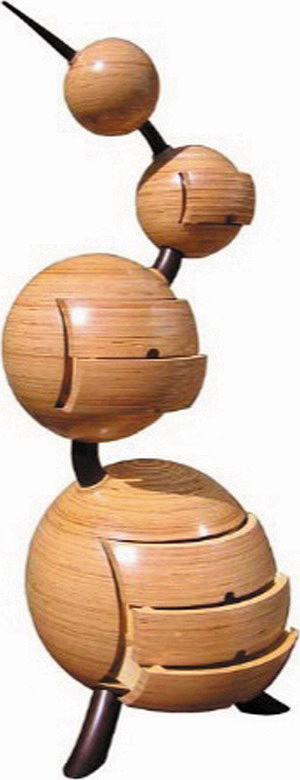
Итальянская студия дизайна MammaFotogramma разработала и запатентовала инновационный пластичный материал Woodskin (пер. с англ. – древесная кожа) с трехслойной конструкцией. Внутренний слой из специальной гибкой ткани оклеен фанерными треугольниками со скошенными гранями. Конструкция обладает удивительной гибкостью, что позволяет делать из Woodskin предметы и объекты интерьера довольно сложной формы. Причем эту форму можно постоянно менять, а форма и размеры треугольников Woodskin могут быть любыми. В конце 1950-х – начале 1960 годов произошел настоящий бум использования фанеры – этого легкого, простого в обработке, не требующего сложных инструментов, прощающего ошибки начинающим мастерам материала – для изготовления самых разнообразных поделок в том числе в домашних условиях.
Использование Woodskin в оформлении магазина одежды в Милане
С созданием оборудования для лазерной резки появилась возможность изготавливать из фанеры необычные по функциональному назначению предметы мебели. Дизайнеры, словно соревнуясь, проектируют мебель, детали которой вырезаны лучом лазера из листа фанеры.
Появилось множество фирм, разрабатывающих оригинальные чертежи изделий для изготовления их деталей на станках с ЧПУ. Можно за небольшую плату загрузить с сайта разработчика понравившуюся модель, сделать заказ онлайн, и фирма, специализирующаяся на лазерной резке фанеры, выполнит нужные заготовки.
Образец чертежа стула из фанеры для изготовления методом лазерной резки
В малотоннажном судостроении пик использования фанеры пришелся на начало 1960-х годов. По стоимости простейшие фанерные лодки были доступны для американского среднего класса. Школьные учителя и каменщики, бухгалтеры и таксисты могли себе позволить купить лодку длиной 8,5 м, оснащенную мотором и всем необходимым, всего за $6995. Оборотистые предприниматели начали в больших объемах производить из фанеры прогулочные катера, яхты, рыбацкие лодки.
Нередко в погоне за прибылью нарушались элементарные технологические требования защиты фанеры от действия воды. Поэтому большинство построенных в те времена судов не продержались на воде и десяти лет, почти все они сгнили и развалились. На смену фанере в малотоннажном судостроении пришел стеклопластик. Однако не все лодки, построенные в те годы, постигла печальная участь. Уцелевшие стали объектом мечтаний коллекционеров, стоимость хорошо отреставрированных экземпляров доходит до семизначных сумм. В 1960-е годы лодки из фанеры выпускались не только на заводах. Производители этого материала, стремясь стимулировать спрос на свою продукцию, финансировали выпуск громадными тиражами печатных пособий с подробными чертежами для начинающих судостроителей. Выпускались и наборы деталей, так называемые кит-комплекты из фанеры для строительства лодок и даже гоночных скутеров. Интересно, что подобные издания пользуются спросом и в наши дни. Книга Л. Глена была переиздана несколько раз, в том числе выпущена на DVD. Казалось бы, стеклопластик и алюминий полностью вытеснят фанеру из судостроения, особенно там, где требуются высокая прочность и надежность, например в создании океанских яхт. Конечно, фанера успешно используется для производства мебели или декоративных панелей судов, но изготовить из нее корпус яхты, способный противостоять буйным силам природы... Оказывается, это возможно.
Обложка книги Л. Глена «Строительство лодок из фанеры», переизданной в 1989 году
Французская фирма RM Yachts производит великолепные океанские яхты из фанеры. Им присвоен рейтинг А ЕС (CE Class A), и предназначены они для плавания в любых условиях и во всех водах.
Владелец фирмы Марк Ломбард утверждает, что фанера – идеальный материал для изготовления яхт, поскольку может впитывать эпоксидную смолу. Сочетание фанеры и эпоксидной смолы позволяет создать очень прочный и долговечный корпус. Яхты изготавливаются только вручную. Естественно, их стоимость выше, чем сделанных из стеклопластика. Но RM Yachts, безусловно, эксклюзивный бренд, поэтому лодки действительно стоят этих денег.
Фанера в судостроении используется в качестве звукоизолирующего и утепляющего материала. У выпускаемой итальянской фирмой Bellotti под торговой маркой Lariphon фанеры лицевые слои из высокопрочной древесины породы окуме, а между ними резиновая прослойка. Ассортимент Bellotti насчитывает около 40 видов фанеры для судостроения: палубная фанера, фанера с наружными слоями из ценных пород древесины для отделки кают и изготовления судовой мебели, звуко- и теплоизолирующая фанера.
Отреставрированная лодка из фанеры производства компании Chris Craft 1956 года выпуска (США)
Яхта производства RM Yachts (Франция)
Корпус яхты из фанеры в процессе строительства на стапеле
С появлением плит OSB многие решили, что фанера в строительстве себя исчерпала. Однако оказалось, что плиты OSB пригодны в основном для производства утилитарных строительных конструкций и только фанера в силу своих прочностных характеристик и возможности принимать, по сути, любую форму по-прежнему остается материалом, вдохновляющим архитекторов на создание шедевров деревянного зодчества, многие из которых были отмечены престижными наградами и премиями в архитектуре.
Павильон Endesa, сделанный почти целиком из фанеры, был частью экспозиции Smart City Expo 2012 в Барселоне (Испания). Павильон разработан Институтом передовой архитектуры Каталонии как энергосберегающее здание, на крыше которого установлены солнечные батареи. Новаторство форм здания и выбранный для его постройки материал привлекали к павильону внимание посетителей выставки и прессы.
Павильон Endesa из фанеры на Smart City Expo 2012 в Барселоне (Испания)
Классическим примером дизайнерского подхода к использованию фанеры в домостроении стал трехэтажный дом XS house, спроектированный и построенный в Бостоне (США) архитекторами компании UNI. Он считается одним из самых необычных домов в мире, иногда его называют «дом из фанерных ящиков».
Внешний вид и интерьер «дома из фанерных ящиков», Бостон (США)
Интерьеры квартиры и мебельного магазина, ставшие победителями престижных архитектурных выставок
При первом взгляде на это сооружение кажется, что архитектор просто поставил друг на друга три большие фанерные коробки размером 4,88×6,70 м, причем довольно небрежно. На самом деле это продуманная конструкция: три этажа дома, три прямоугольные комнаты как бы нанизаны на ось и соединены внутренней лестницей. Свет проникает сквозь потолочные окна в углах коробок, вот для чего архитектор сдвинул их «винтом». Треугольные окна в потолке не только обеспечивают освещение, но и позволяют обозревать небеса в разное время суток. Интерьер помещений тоже отделан фанерой и лаконичен, как и экстерьер. Впрочем, это кажущаяся простота. В отделке дома также использованы мрамор и дуб.
Фанеру в дизайне интерьера квартиры для своей семьи использовал архитектор Джейсон Гибни. Минимализм дизайнерского решения был высоко оценен на международной выставке Houses Awards в 2011 году. Совсем недавно полностью изготовленный из фанеры интерьер павильона офисной мебели Herman Miller в Сингапурском мебельном магазине Xtra завоевал титул лучшего мирового интерьера года на престижной выставке Inside festival 2017.
Шпунтованная фанера и ее сборка
Трудно перечислить все виды фанеры для строительства, выпускаемой в мире. Так, для наружной отделки зданий в США производят сайдинг из фанеры, которую облицовывают мраморной крошкой и разными пластиками, изготавливают шипованную фанеру для соединения «паз – гребень». Для устройства «теплого пола» выпускают фанеру с фрезерованными под нагревательные элементы пазами, а также фанеру с впрессованными в нее пленочными нагревательными элементами. И так далее...
Рассматривая перспективы производства и использования фанеры в мире, можно отметить, что по спросу на нее североамериканский регион по-прежнему занимает доминирующее положение на рынке, что объясняется высоким потреблением в строительном секторе. За Северной Америкой следует Европа. Однако самый высокий рост спроса демонстрирует Азиатско-Тихоокеанский регион. В Китае, Индии и Японии наблюдаются высокие темпы жилищного строительства, что в значительной степени стимулирует спрос на фанеру.
Страны, богатые лесными ресурсами (Индия, Бразилия и страны Юго-Восточной Азии), в ближайшем будущем могут стать ключевыми поставщиками фанеры на мировой рынок. Леса Индии с их разнообразием лиственных, хвойных, тропических и вечнозеленых пород могут стать важным ресурсом для деревообрабатывающей промышленности. Кроме того, ожидается, что в ближайшее время в результате повышения доходов населения Индии растущий спрос на фанеру сделает эту страну серьезным потребителем этого материала.
Повышение строительной активности во всем мире и растущее применение фанеры в дизайне интерьера, особенно в дорогостоящих жилых помещениях, наряду с развитием мебельной промышленности, как ожидается, будут стимулировать и активность на мировом рынке фанеры в течение нескольких лет. По разным оценкам, этот рынок должен вырасти в среднем на 9,3% в следующем десятилетии.
Итак, фанера останется востребованным материалом XXI века: прочным, надежным, красивым и, что немаловажно, материалом, сырье, для производства которого при разумном использовании будет у человечества всегда.
Александр ФИЛИППОВИЧ