Эффективный пресс для гранулирования древесины
Каким он должен быть?
Повышение энергоэффективности производства всегда было одной из важнейших задач по достижению конкурентной себестоимости продукции. В наше время оно стало основным показателем современного подхода к сохранению природы и условий для жизни планеты.
Особенно это актуально при производстве «зеленых» возобновляемых источников энергии, в том числе древесных топливных гранул – пеллет. Способ повышения энергоэффективности был обнаружен при анализе параметров эксплуатации пеллетных прессов различной конструкции, при этом выявлена возможность повышения их производительности.
Известно, что с увеличением мощности привода в итоге достигается предельная нагрузка, которую пресс может выдержать без разрушения. Именно такая ситуация сложилась на рынке прессов примерно с 2010 года, когда произошел скачок мощности прессов для древесины (с круглой матрицей сходной мощности) с 315 (320) до 355 кВт. С тех пор следующий шаг – пак и не сделан. В настоящее время производятся испытания и даже начата промышленная эксплуатация таких мощных прессов, но для комбикорма.
Возникает вопрос: есть ли способ повышения производительности пресса при ограниченной сегодня мощности привода и прочности станка? Идею для поиска ответа подсказало исследование энергетики гранулирования и опыт эксплуатации разных прессов.
Энергетика гранулирования
В 2009 году группа ученых из Дании и США под руководством Нильса Нильсена и при участии компании Andritz Feed & Biofuel провели серию исследований процесса гранулирования древесины. Целью было изучение влияния на энергетику гранулирования различных факторов, в том числе температуры. Для этого процесс был разделен на компоненты сжатия, течения и трения, и для каждого были проведены эксперименты и рассчитана затраченная энергия.
Часть опилок (больше 50%) в сжатом виде распределяется по поверхности матрицы между пресс-каналами. Чтобы войти в пресс-каналы, материал должен стать текучим.
Сжатие опилок и проталкивание их в пресс-каналах представляют собой работу сил трения, а компонент течения – работу вязкого трения.
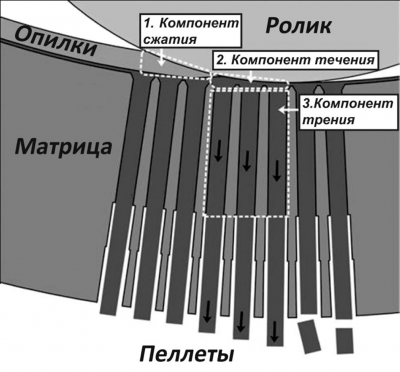
Изучение гранулирования древесины сосны и бука
Первый эксперимент – прессование отдельных порций древесины с приведением результатов к 0,25 г (рис. 2 и 3). В двух компонентах (сжатия и течения) исследователи выявили энергетический минимум процесса при Т = 105°С. То же получилось и для энергии трения при прессовании единичной порции 0,25 г сосновой древесины.
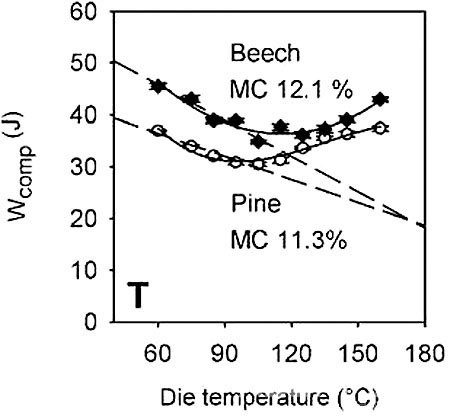
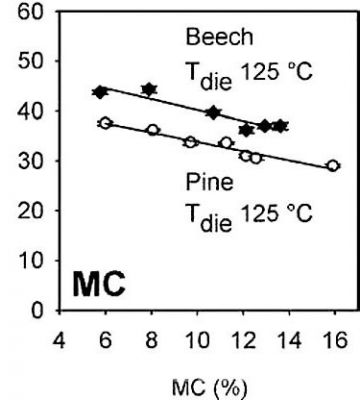
Второй эксперимент – прессование последовательно порций древесины по 0,25 г (рис. 4). Каждая порция (слой) увеличивала длину пеллеты на 3,5 мм.

Было показано, что при длине пеллеты (в реальных условиях это длина прессующего канала) от 25 до 60 мм энергия течения вместе с энергией трения растут экспоненциально.
Ограниченность этого эксперимента связана с изучением процесса только при температуре 125°С.
Дополнительные выводы и следствия
- Для формирования пеллеты требуемой плотности и прочности необходимо создать нужную силу трения в прессующем канале, что обеспечивается длиной прессующего канала; силу трения можно оценить как положительный фактор. Энергия трения выше при низкой температуре, поэтому требуется меньшая длина прессующего канала. Для стабильного качества пеллет сила трения должна быть стабильной, однако при увеличении длины прессующего канала условия трения могут изменяться нелинейно (например, сушка материала в канале может привести к изменению коэффициента трения, возможно увеличение давления на стенку канала).
- В эксперименте не учитывалась энергия нагрева матрицы (нагрев производился ТЭНами для контроля температуры). Оценочно для поддержания рабочей температуры матрицы требуется дополнительная энергия из расчета 0,032 кВт·ч на 1°С на 1 т пеллет, что дает дополнительно 2,88 кВт·ч/т при Т = 105°С и 3,52 кВт·ч/т для Т = 125°С (при температуре окружающей среды 15°С). Кроме того, энергия расходуется на нагрев пресса и окружающего пространства, но оценка не проводилась.
- 3Общие энергетические затраты в установившемся режиме прессования были определены для хвои при Т = 125 °С из расчета 45 Дж на 0,25 г, или 50 кВт·ч/т (без учета нагрева матрицы). С учетом нагрева матрицы 53,5 кВт·ч/т.
- Для расчета мощности привода пресса следует принять стандартную нагрузку мотора 60%, что даст установленную мощность 89 кВт/т в условиях эксперимента (Т = 125°С).
- Процесс протекает при высоком давлении, 210–450 МПа, что значительно повышает текучесть компонентов древесины. Фактор давления не отражен в классических исследованиях плавления и текучести компонентов древесины. Результаты этих исследований не могут использоваться напрямую для изучения прессования, температурные показатели в них, очевидно, выше, чем на практике.
Исследование выявило вполне определенную физику гранулирования древесины, а идеальными можно назвать условия, при которых достигаются минимальные удельные энергозатраты (кВт/т). Какое это имеет практическое значение?
Энергетическая эффективность прессов-грануляторов
Прессы различаются конструктивно, по типу матрицы и привода, мощности двигателя, сервисным возможностям. Рассмотрим особенности двух прессов (табл. 1).


Рабочая температура прессов сильно отличается. Размеры матрицы и количество роликов тоже разные. Для определения искомого влияния на энергетику можно оценить скорость движения роликов по матрице. Рассчитаем ширину рабочего фронта, равную произведению ширины рабочей дорожки матрицы и количества роликов, и коэффициент равнозначной линейной скорости прессования.
Результаты сравнительного анализа высоко- и низкотемпературного прессов:
1. При одинаковых мощности и производительности скорость движения роликов по матрице в низкотемпературном прессе могла бы быть на 33% (в 1,5 раза) ниже.
Поскольку она действительно ниже, гранулирование смещается в более энергоэффективную область с пониженной температурой, а потребная удельная мощность гранулирования снижается. Такой результат объясняется свойствами сил трения.
Вся или почти вся выполненная приводом пресса работа расходуется на преодоление сил трения, которые по определению преобразуются в нагрев станка, инструмента, изделий и в конечном счете окружающей среды. А величина силы трения зависит от давления тел друг на друга и относительной скорости движения.
Пресс с более узким рабочим фронтом и меньшим диаметром матрицы должен обеспечивать более высокую скорость процесса при одинаковой производительности. При этом температура процесса повышается, а КПД падает. И наоборот.
Сбалансированная конструкция пресса обеспечивает оптимальный энергетический баланс, с минимальной удельной мощностью прессования и максимальным КПД, что обеспечивает заметный рост производительности.
2. Повышенная температура не только не полезна для технологического процесса, но и вредна, прямым доказательством чего служит оснащение высокотемпературных прессов системой охлаждения роликов.
3. Оценить разницу производительности самым простым способом можно путем сравнения рабочей температуры. Например, снижение температуры процесса на 15°С, что составляет около 15% (от базовой 15°С), должно привести к пропорциональному росту производительности при одинаковой мощности с учетом процента нагрузки мотора. Это предположение подтверждается статистикой: низкотемпературные прессы с двигателем 355 кВт обеспечивают среднюю практическую производительность на сосне 4,5 т/ч, что соответствует 36 тыс. т в год при 8000 рабочих часов и удельной установленной мощности 355 кВт/4,5 т = 79 кВт/т.
Для сравнения: декларируемая годовая производительность высокотемпературного пресса составляет 30–32,5 тыс. т, что предполагает среднюю практическую производительность 4 т/ч и меньше. Такое же значение получено и при анализе эксперимента, а именно: 355 кВт/89 кВт/т = 3,99 т (в час).
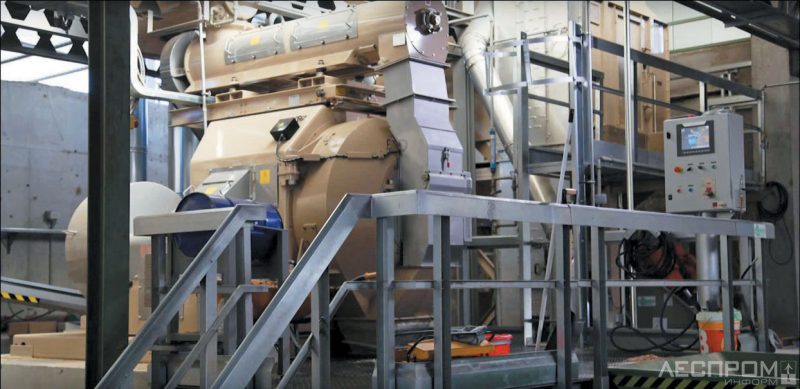
Особенности эксплуатации низкотемпературных прессов
- Не требуется система охлаждения роликов.
- Подача пара эффективнее из-за бóльшей температурной разницы. По результатам эксплуатации трех роликовых прессов с добавкой пара, прибавка производительности достигала 20% на сосне. Рабочий процесс при этом становился эластичнее и не требовал точной подгонки параметров матрицы (прессующей длины канала).
- Использование трех роликов вместо двух не является более затратным вариантом, так как их износ зависит от количества произведенной продукции на каждый ролик. А низкие скорость и температура способствуют меньшему износу металла и расходу смазки для роликов.
- У трехроликовых прессов минимизировано смещение роликов во всех направлениях вследствие рабочих нагрузок. У двух- роликовых прессов – только в плоскости, проходящей через оси роликов, в перпендикулярной плоскости возможны смещения от сгибающих/вращающих моментов. Это может вызвать вибрацию.
Текст
Виктор Анисимов, Wood&Pellet Project