Фанерное производство: на пути совершенствования производственного процесса
На VII Международной конференции представителей фанерных предприятий России и стран СНГ, которая прошла в феврале этого года в Санкт-Петербурге, в конференц-зале гостиницы «Москва», обсуждался широкий круг вопросов, имеющих большое значение для фанерной отрасли.
Например, рассмотрению нюансов использования новых смол и клеев было уделено большое внимание в первой части конференции. Обсуждались также вопросы лесной биоэнергетики, а вторая часть конференции в основном была посвящена проблемам модернизации оборудования и технологических процессов.
Отрасли нужны квалифицированные кадры
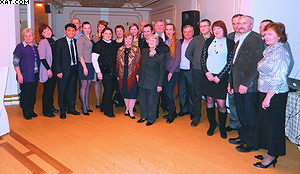
Слово «модернизация» на конференции часто звучало не только в связи с оборудованием и технологическими процессами. В начале конференции ее участники много говорили о необходимости модернизации профессионального образования. Почетный президент Санкт-Петербургского государственного лесотехнического университета (СПбГЛТУ), д-р техн. наук, проф. Владимир Онегин в своем докладе очертил круг хорошо известных проблем. Он отметил, что в результате развала системы советского лесного образования, имевшего крепкую научную базу, произошли глубокие системные изменения. Почти полностью было уничтожено среднее профессиональное образование: в стране из 50 техникумов в области деревообработки остались всего 16. Произошел отток высококвалифицированных молодых педагогов и научных сотрудников из системы образования в коммерческие структуры или за рубеж. Резко снизилось качество образовательных услуг, и, соответственно, снизился уровень подготовки молодых специалистов.
Говорившие об этом докладчики отмечали сложную ситуацию с кадрами для производств, в том числе фанерных. Не менее сложной остается ситуация в отраслевой науке. Бизнес все еще не испытывает потребности в научных разработках и не проявляет инициативу для сотрудничества. Нет в среде предпринимателей и активности в подготовке кадров для своих производств. На конференции отмечалось, что проблема с кадрами, которая последнее время буквально душит лесную отрасль, актуальна почти во всех отраслях. Сегодня повсеместно появляются новые технологии, новое оборудование, но очень мало специалистов, которые могут их грамотно использовать и развивать, поэтому особое значение приобретает система повышения квалификации. За рубежом эта система хорошо отлажена. Например, в Германии срок переподготовки кадров - три, максимум - четыре года. В этом процессе участвуют и государство, и предприятия, и многие люди вкладывают деньги в повышение собственной квалификации. Российские специалисты и бизнесмены еще не готовы к такому мышлению, хотя интерес к этой форме обучения есть. В год на ФПК Лесотехнической академии обучается больше тысячи человек, а за пять лет там прошли переподготовку представители 30 фанерных предприятий.
Российские инновации в производстве клеев
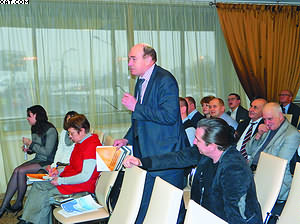
На конференции состоялась презентация книги «Синтетические смолы в деревообработке» (авторы - В. П. Кондратьев, В. И. Кондращенко, В. Е. Шредер). По мнению тех, кто уже успел с ней ознакомиться, эта книга должна быть на каждом производстве. В ней собрана исчерпывающая информация по клеям и смолам, описаны новые безопасные технологии производства карбамидоформальдегидных и диановых смол и клеев на их основе для изготовления экологически безопасных древесных материалов. Безусловный интерес специалистов вызовет и раздел, посвященный синтетическим смолам, а также технологическим решениям, направленным на повышение качества фанеры и древесных плит. В книге приведены примеры новых экологически безопасных технологий производства клеев. Доклад одного из авторов, главного инженера проекта «Смолы» ОАО «Пигмент» Владимира Шредера о современных синтетических клеях для древесных материалов был заслушан участниками мероприятия с большим вниманием.
Доклад затрагивал важные для фанерной промышленности вопросы экологии и энергосберегающих технологий. Решать задачу энергосбережения при склеивании фанеры можно путем интенсификации режимов, за счет уменьшения времени и снижения температуры склеивания при увеличении производительности процесса. Экологические задачи решаются за счет снижения токсичности компонентов смол и фанерной продукции. Владимир Шредер рассказал об инновационных работах, выполненных ОАО «Пигмент» совместно с ООО «ЦНИИФ», цель которых - создание новых видов клеевых композиций и разработка на этой базе режимов склеивания шпона. На предприятии была введена в эксплуатацию установка для производства концентрированного низкометанольного формалина, качество которого определяет технические и экологические показатели синтетических смол.
Владимир Шредер отметил, что «в настоящее время на рынке, помимо хорошо известной отечественной фенолоформальдегидной смолы марок СФЖ-3014, 3066, 3096 и ряда других российских смол, появились смолы компаний с иностранным капиталом. Все эти материалы производятся на современных реакторах большого объема (40 м3), с использованием современных компьютерных программ, позволяющих обеспечивать получение заданных параметров. Однако эти смолы не совсем удовлетворяют деревообработчиков по одной простой причине: они выпускаются массово и не учитывают потребности деревообрабатывающих предприятий, так как технология производства на этих реакторах исключает возможность введения какого-либо индивидуального параметра». В ОАО «Пигмент» производство смолы организовано на высококонцентрированном формалине собственного изготовления в новых 25-кубовых реакторах, не имеющих аналогов в России, с применением полностью автоматизированной системы управления технологическим процессом. При этом обеспечивается возможность учета меняющихся требований потребителя.
Еще одна совместная инновационная разработка ОАО «Пигмент» и ОАО «ЦНИИФ» - отвердитель ЛП-2 для фенольных смол, который позволяет снизить расход клея на один кубический метр фанеры на 10%, расход смолы - до 90 кг на кубический метр и уменьшить время прессования фанеры на 10-15%. Для производства фанеры на основе карбамидоформальдегидных смол разработан комплексный отвердитель ЛП-3. Его использование позволяет обеспечить высокое качество холодной подпрессовки за счет нивелирования зависимости клейкости смолы от степени ее старения.
Производительность и энергоэффективность
К сожалению, формат журнальной публикации не позволяет осветить подробно каждое выступление по перспективным смолам, выпускаемым предприятиями химической промышленности для фанерных предприятий, но можно отметить, что во всех докладах содержалась информация о способах повышения производительности за счет инновационных решений.
Много интересных сообщений на конференции было посвящено модернизации оборудования и современным станкам. Глава представительства фирмы Raute (Финляндия) Александр Кирпичников подробно рассказал о модернизации линий лущения и современных методах клеенанесения. За последние несколько лет эта компания провела модернизацию линий лущения в разных российских компаниях. На одних предприятиях такие линии были модернизированы полностью, на других - проведена замена отдельных блоков. Во всех случаях реализация мероприятий по обновлению и совершенствованию оборудования позволила повысить и производительность станков, и коэффициент использования сырья.
Так или иначе, доклады касались почти всех этапов производства фанеры. Глава представительства фирмы Steinemann, руководитель филиала фирмы «ГреКон» в России и странах СНГ Алексей Васичев сообщил о новом станке NOVA-H для шлифования фанеры. Шлифование - наиболее важная завершающая стадия производства продукции, и станок должен обеспечивать отличное качество обработки и высокую экономическую эффективность. Г-н Васичев также рассказал о контрольно-измерительных приборах и установках фирмы «ГреКон». Высокое качество конечной продукции может быть обеспечено только при постоянном контроле параметров производственного оборудования. Одна из существующих проблем - это невидимые отклонения от заданных параметров, которые распознаются только на стадии раскроя плиты или уже на том предприятии, где выполняется дальнейшая обработка плит. Алексей Васичев подчеркнул, что установки фирмы «ГреКон» позволяют не только распознавать воздушные включения, такие как пузыри, расслоения, места непроклея, но и оптимизировать технологический процесс в целом.
Наряду с докладами по современному оборудованию для деревообработки прозвучали доклады об использовании древесных отходов в целях энерго- и теплообеспечения основных производств компаний. Сегодня каждое предприятие стремится оптимизировать технологические и химические процессы в производстве фанеры, модернизировать оборудование и комплексно подходить к вопросам энергосбережения, потому что все это вместе позволяет снижать себестоимость продукции. Д-р техн. наук, проф. СПбГЛТУ Анатолий Смоляков выступил с интересным и обстоятельным докладом, посвященным использованию технологии газогенерации в переработке древесных отходов. Он отметил, что создатели современных газогенераторов сталкиваются с серьезными трудностями. В советские времена генераторы работали на заранее заготовленной древесной - обязательно березовой - чурке, влажность и размеры которой должны были соответствовать специальному ГОСТу. Сегодня древесные отходы характеризуются очень высокой влажностью, причем слои в одной массе различаются по влажности. Еще одна сложность - фракционный состав отходов, размер которых колеблется в пределах от одного-двух миллиметров до нескольких десятков сантиметров. Все это оказывает сильное влияние на генераторный процесс: тем не менее удалось создать новый газогенератор, который может эффективно газифицировать очень влажные древесные отходы разного фракционного состава.
О наиболее интересных вопросах, рассмотренных на конференции, мы расскажем подробно в ближайших номерах журнала.
Галина МАЛИКОВА
Вадим Ким, заместитель председателя совета директоров ЗАО «Технопарк ЛТА»
Профессор А. Смоляков в своем докладе, посвященном газификации древесных отходов в газогенераторах с получением генераторного газа и его использованием в качестве энергоносителя для выработки тепла или электроэнергии, очень подробно рассказал о проблеме недостаточной эффективности утилизации отходов. Мир живет в условиях постепенно сокращающихся запасов традиционных энергоносителей и неуклонно растущих цен на различные виды энергии. И газогенерация как один из путей решения проблемы вызывает у мирового сообщества все больший интерес. Неудивительно, что доклад проф. Смолякова был прослушан как российскими, так и зарубежными участниками конференции с особым вниманием. Финская компания «HT-инжиниринг» предложила компании «Технопарк ЛТА» предоставить все необходимые условия, вплоть до высокотехнологичного научного оборудования, для проведения теоретических и прикладных исследовательских работ по газогенераторной тематике.
«HT-инжиниринг» потратила на разработку эффективного газогенератора два года и более 4 млн евро. Опытный экземпляр изготовлен, на нем можно получать генераторный газ, аппарат проработал в тестовом режиме 100 часов. Запустить ее в серийное производство не позволяют ряд недоработок и нестабильность работы энергетической установки. В результате газогенератор законсервирован, проект остановлен, и решить проблему своими силами финские коллеги не в состоянии. Они обратились к нам с просьбой помочь разобраться с их установкой, провести ряд испытаний и найти решение, которое обеспечит получение требуемых параметров для действующей установки.
Я выступил на конференции с сообщением о работах по созданию газогенераторной установки небольшой мощности, которую можно было бы запустить в массовое производство для предприятий мелкого и среднего бизнеса, занимающихся деревообработкой. Вопрос использования таких установок актуален и для фанерных производств, на которых накапливается огромное количество древесных отходов.