«Элеон». Пусть в наших домах живут мир и счастье
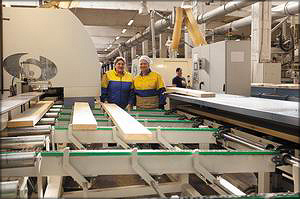
Это небольшое подмосковное предприятие в статистических отчетах, характеризующих общий объем промышленного производства в г. Электросталь, конечно же, не может составить конкуренцию крупным производителям высококачественной стали, топлива для атомных электростанций и станков и оборудования для тяжелой промышленности. Но зато продукция ООО «Элеон» весьма интересна и металлургам, и машиностроителям, и ядерщикам, и представителям многих других профессий, живущим в Москве, Московской области и других регионах России. Деревянные дома из клееного бруса, которые изготавливают в « Элеоне», пользуются у потребителей спросом.
Компания «Элеон» была создана на базе деревообрабатывающего комбината, с 1946 года входившего в состав треста «Главмособлстрой». До перестройки ДОК, в машинном парке которого были две лесопильные рамы РД-75 и другое отечественное оборудование, занимался лесопилением, сушкой пиломатериалов, изготовлением столярных изделий, в частности окон и дверей. как для жилищного строительства, так и для объектов промышленного и социально-культурного назначения. Но с наступлением кризисных 1990-х годов объемы строительства в стране резко сократились и продукция ДОКа оказалась невостребованной. В 1991 году было зарегистрировано ООО «ЭЛИС», которое в дальнейшем было реорганизовано в ООО «Элеон». Вплоть до начала 2000-х годов предприятие выживало, как могло. Приходилось браться за выполнение любых заказов, например изготавливать тарные ящики, и сокращать число работников... И тогда руководство компании приняло решение освоить производство нового, перспективного продукта - клееного бруса, для чего требовалось кардинальное обновление производственных мощностей. Были привлечены инвестиции частных и юридических лиц, и в 2001 году на предприятие поставили первый комплект оборудования производства компании Weinig. Рассказывает генеральный директор завода «Элеон» Валерий Новиков: «Конечно, пришлось нам тогда непросто, ведь дело для нас было новое. Мы изготавливали шестиметровый стеновой непрофилированный брус (станков для профилирования не было) сечением 140х200 и 160х200 мм. В тот период у нас еще не было станков для зарезания чашек, поэтому мы поставляли свой брус предприятиям, у которых имелись такие центры и профилирующие четырехсторонние станки. Постепенно стали появляться заказы для домостроения. Примерно до 2006 года мы выпускали оконный и стеновой клееный брус, в том числе балку. А затем приступили к очередному этапу модернизации станочного парка. Были приобретены линии сращивания итальянского производства, два четырехсторонних станка Winner BL 6-23, а также итальянский профилирующий четырехсторонний строгальный станок Basic 400 (производитель - C. M. Macchine s.r.l.). Освоив новое оборудование, мы стали выпускать детали домов, готовые для монтажа. Тогда мы изготавливали от 380 до 420 м3 в месяц и сформировали собственное строительное подразделение, которое занималось монтажом домов. Для того чтобы добиться большего, нам необходимо было решить несколько задач: отладить организацию производственных процессов, соединить разрозненные станки в поточную линию, сократить до минимума объем ручного труда на некоторых операциях и рационально использовать имевшиеся трудовые ресурсы, продолжить модернизацию машинного парка.
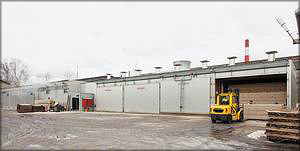
Сушильные камеры EISENMANN
Масштабное обновление производственных мощностей началось в 2009 году и велось без остановок основного производства до конца 2011 года. Оценив имевшееся на тот момент на рынке оборудование по принципу "цена - качество", мы остановили свой выбор на технике итальянской компании Spanevello. Работая на комплексной линии этого итальянского машиностроителя, мы приобрели хороший опыт производства клееного бруса, поняли особенности этого оборудования, освоили работу с рекомендованным нам инструментом и программным обеспечением и оптимизировали ПО в соответствии с нашими условиями».
Кроме комплексной технологической линии Spanevello в период полной модернизации парка оборудования и инфраструктуры завода были закуплены и введены в эксплуатацию гидравлический пресс производства российской компании «Бакаут», деревообрабатывающие программные центры Hundegger К2 производства немецкой компании Hundegger Maschinenbau GmbH, австрийские станки AUER для изготовления домокомплектов, сушильные комплексы производства компаний Secea (Италия) и Eisenmann (Германия), построена новая водогрейная котельная, работающая без присутствия операторов, автономно, на природном газе. Мощность котельной - 12,2 МВт (два котла GKS Dynaterm-3200 и один котел GKS Dynaterm-5000 производства компании Wolf GmbH, Германия). Для полного удаления стружки от станков, надежной очистки отработанного воздуха и обратной подачи его в цех (что позволяет поддерживать стабильную температуру в цехе и экономить на отоплении цеха в зимний период) была приобретена и установлена система аспирации российского производителя - фирмы «Консар».
Профиль современного предприятия
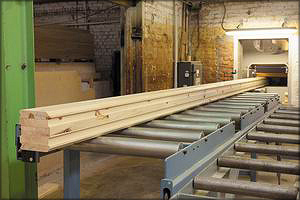
Выход профилированного бруса из строгального станка
Universal-700
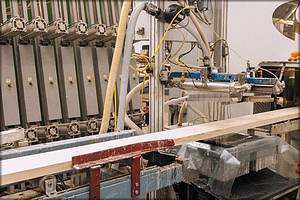
Установка раздельного нанесения клея компании Akzo
Nobel

Новая водогрейная газовая котельная
Итак, сегодня ООО «Элеон» - современное высокоавтоматизированное предприятие с мощной машинной базой и большими потенциальными возможностями. Производственные площади завода составляют более 34 000 м2.
Выпускаемая продукция - от клееного бруса до готового домокомплекта и бруса для фахверкового строительства. Объем производства - около 9500 м3 клееного бруса и домокомплектов в год.
Максимальная длина клееного бруса, предназначенного для производства домокомплекта, - до 14 000 мм. Сечение: по высоте бруса - от 140 до 360 мм, по ширине - от 120 до 360 мм с шагом 40 мм. На клееный брус разработаны технические условия с учетом пожеланий потребителей и в соответствии с действующими ГОСТами и СНиПами РФ. Предприятие не только производит брус и домокомплекты для сторонних домостроительных компаний по их проектам, но и своими силами проектирует и собирает дома из комплектов собственного производства. В основе бизнес-концепции компании ориентация на частных клиентов, домостроительные компании, девелоперов поселков и компаний, специализирующихся на продвижении клееного бруса на российском рынке.
Высокопроизводительный машинный парк, солидная инженерно-конструкторская и технологическая база, современное программное обеспечение cadwork, квалифицированные кадры - все это позволяет создавать проекты со сложными архитектурными формами и узлами и обеспечивает предприятию спрос на его продукцию и услуги. С «Элеоном» охотно сотрудничают как частные лица, так и организации, недостатка в клиентах нет. Сейчас завод осуществляет застройку трех коттеджных поселков в Помосковье: «Онтарио» (50 км по Минскому шоссе, недалеко от Нарвских прудов), «Брусландия» (Истринский район) и «Зеленый парк» (по Ярославскому шоссе, между Сергиевым Посадом и Александровом). Кроме производства клееного бруса и строительства домов предприятие оказывает заказчикам услуги по сушке пиломатериалов (ель, сосна, лиственница), а также строганию и торцовке в размер.
Сырье, клей, инструмент
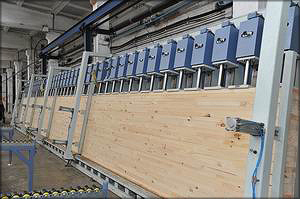
Гидравлические пресса компании Spanevello
Для производства клееного бруса на «Элеоне» используют в основном еловые и сосновые пиломатериалы, которые на подмосковное предприятие доставляют автомобильным и железнодорожным транспортом из северных районов России, преимущественно из печорской тайги.
«Мы гордимся тем, что сырье для нашей продукции заготавливается в экологически чистых лесах Печоры, - говорит генеральный директор компании «Элеон». - Достоинства северной древесины очевидны: это северный лес, выращенный в здоровой среде, в районах, где нет вредных выбросов промышленности. Он мало подвержен заражению гнилостными бактериями, обладает высокими прочностными характеристиками, выдерживает большие нагрузки на изгиб, растяжение и излом. Прирост годовых колец в стволе дерева, произрастающего в северных районах, менее 1 мм, именно поэтому древесину северных лесов отличают повышенная плотность и прочность, она прямоствольная, хорошо обрабатывается. Из такого леса производятся наши материалы и строятся деревянные дома на века».
Кроме того, «Элеон» закупает пиломатериалы в Архангельской, Вологодской, Кировской, Костромской и Ивановской областях. Месячная потребность предприятия в сырье составляет от 1,2 до 1,5 тыс. м3.
Большую роль в технологическом процессе изготовления клееного бруса играет клеевой состав. Именно от качества клея зависят такие важные характеристики клееного бруса, как прочность, долговечность, экологичность, эстетичность и др. На «Элеоне» для производства бруса используется меламиновая клеевая система ведущего мирового производителя - компании AkzoNobel.
В основном на технологической линии эксплуатируется итальянский режущий инструмент, рекомендованный компанией Spanevello и поставленный в комплекте с оборудованием. Кроме того, используются фрезы со сменными пластинками и инструмент из твердосплавной стали производства российской компании «ЭЛСИ» (г. Муром), а также шведские фрезы для зарезки микрошипов, закупаемые через компанию «Альянс Форест» (Санкт-Петербург). Через эту же компанию фрезы с отработанными твердосплавными пластинами отправляются в Швецию на реставрацию.
На предприятии есть участок для заточки инструмента, полностью отвечающий требованиям современного производства: он укомплектован так, что ему позавидует иной специализированный сервисный центр. Здесь установлены различные виды оборудования: для заточки ножей, пил из твердых сплавов и различных фрез, в том числе фрез для зарезки микрошипов (станок Holytek G-400S производства Тайваня), станок для заточки профильных фрез (производитель - компания Weinig) и другого инструмента.
Производство бруса и домокомплектов
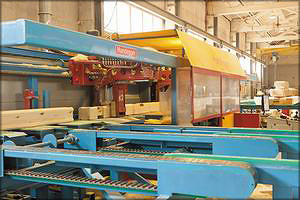
Обрабатывающий програмный центр Hundegger К-2
Первое звено технологической цепочки производства клееного бруса - сортировка исходного сырья на сортировочной площадке, на которую доставляются пиломатериалы естественной влажности. Сырье, выгруженное из железнодорожных вагонов и кузовов автомобилей десятитонным портальным краном, вручную сортируется и укладывается в штабели перед тем как отправляется в сушильные камеры.
ООО «Элеон» располагает девятью современными сушильными комплексами, среди которых немецкие Eisenmann и итальянские Secea (объем разовой загрузки всех камер составляет 720 м3, в т. ч. итальянских камер - 480 м3, немецких - 240 м3). Подготовленные пакеты пиломатериалов загружают в камеры и подвергают сушке в специальных технологических режимах - пиломатериалы проходят 14 фаз сушки. За соблюдение точных режимов сушки, контроль температуры и влажности отвечает электроника. Режим мягкой сушки позволяет избежать деформации пиломатериалов и их растрескивания, достичь оптимального показателя влажности пиломатериалов на выходе: 10-12%. Особая конструкция камер обеспечивает равномерность сушки по штабелю. С помощью датчиков в камере ведется непрерывный мониторинг показателей температуры воздуха, равновесной влажности и влажности древесины, при необходимости показатели корректируются в соответствии с режимом текущей фазы сушки. Качеству сушки уделяется особое внимание, ведь от влажности ламелей, из которых склеивается брус, зависят самые важные характеристики бруса. Высушенные доски поступают в цех для акклиматизации (кондиционирования) в течение как минимум суток, а затем - на линию, в переработку. Здесь автоматические влагомеры еще раз проверяют влажность каждой доски. Те доски, влажность которых не соответствует необходимым параметрам, изымаются из дальнейшего процесса на доработку, а нормальный (кондиционный) пиломатериал проходит черновую строжку (калибровку) для того, чтобы выровнять геометрические параметры доски. После этого доски поштучно поступают на маркировочный стол. Опытные маркировщики выявляют дефекты, такие как гнилые выпадающие сучки, сквозные трещины, обзол и другие, отмечают их специальными люминесцентными мелками. Затем на линии оптимизации автоматический станок с лазерным считывающим устройством в соответствии с маркировочными отметками вырезает все отмеченные участки досок с дефектами. После удаления дефектов качественные отрезки (заготовки) сращиваются по длине на микрошип и получается единая доска-ламель.
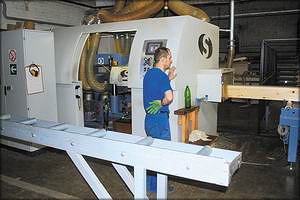
Шести-шпиндельный четырех-сторонний стогальный
станок Universal-700 для профилирования бруса
«Главная задача на этом этапе - выявить наиболее качественные зоны доски. И здесь еще раз стоит отметить достоинства северной древесины, - говорит г-н Новиков. - Участки такой доски без дефектов достигают в длину 1,2 м и более. Именно такие длинные доски идут на изготовление лицевых ламелей, у которых небольшое количество мест сращивания».
Доски меньшей длины используются при изготовлении ламелей для внутренних слоев бруса. Сортировка на линии выполняется автоматически. Пневмотолкатели сбрасывают с рабочего стола станка короткие доски в одну сторону - на линию пакетного сращивания, а длинные - в другую сторону, откуда они по транспортеру поступают на линию бесконечного сращивания.
Для сращивания заготовок по длине на микрошип в единую ламель на предприятии используется сертифицированный однокомпонентный клей повышенной влагостойкости класса D4 концерна AkzoNobel. После выдержки сращенные ламели проходят чистовую строжку, а после нанесения на них дождевым способом клея укладываются под гидравлический пресс на соответствующую технологии выдержку под давлением. Подготовленные ламели укладываются одна на другую, и каждый слой проклеивается. При этом используется сертифицированный двухкомпонентный меламиновый клей того же концерна AkzoNobel. Этот известный производитель клеевых составов гарантируют надежную склейку и экологическую безопасность клеевого соединения и изделия в целом.
«Готовый брус необходимо обработать на строительной площадке водоотталкивающими, огнестойкими, противогрибковыми пропитками, - говорит руководитель предприятия. - Впрочем, плотная древесина хвойных пород и без такой обработки хорошо противостоит воздействию атмосферной влаги, солнечных лучей и ветров».
После склеивания в прессе брус-заготовка проходит финишную строжку (профилирование), а затем, после проверки качества поступает в цех изготовления деталей домокомплектов согласно проекту. На производстве установлены две линии зарезки: австрийская AUER - для зарезки чашек и получения технологических отверстий в стеновом брусе, и немецкая Hundegger К2 с универсальной фрезой, с помощью которой можно выполнять разные фигурные срезы при изготовлении домокомплектов.
«Мы фрезеруем чашки соединения на такую глубину, чтобы обеспечить один оборот утеплителя на внутричашечном шипе, - делится секретами технологии главный технолог ООО «Элеон» Николай Москалев. - Тем самым мы добиваемся непродуваемости углового соединения или переруба. Мы много общались со строителями, следили за тем, как ведут себя соединения в элементах домокомплектов при эксплуатации домов и считаем, что не ошиблись, когда выбрали такую технологию зарезки чашек, о которой я сейчас рассказал. Мы хотим, чтобы нашим заказчикам было тепло и комфортно в их домах».
«Очень важно, чтобы пазы каждого бруса были сделаны с абсолютной точностью. Иначе не избежать механических напряжений в стене, а это грозит резким ухудшением всех характеристик строения. Точность линейных размеров готового изделия такова, что дом собирается как детская игрушка-конструктор», - подчеркивает главный инженер ООО «Элеон» Александр Устимов.
Готовые детали проходят окончательный осмотр, маркируются, каждый домокомплект упаковывается. В соответствии с проектом или заказом элементы будущего дома комплектуются, загружаются в автомобили и отправляются заказчику или на строительную площадку, где будет выполняться монтаж здания.
Конкурентные преимущества
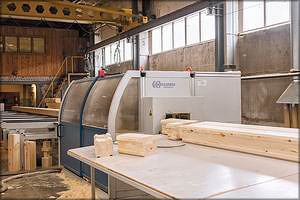
Автоматизированный станок AUER Big LOG для зарезки
деталей дома
«Элеон» - предприятие высокой производственной культуры, оснащенное автоматизированным современным оборудованием, укомплектованное квалифицированными кадрами. Все этапы производственного процесса находятся под строгим контролем. Особое внимание уделяется обеспечению высокого качества продукции. Несмотря на то что сейчас в РФ отменена обязательная сертификация клееного стенового бруса, на «Элеоне» периодически, раз в три года, проводится сертификация бруса специалистами Московского государственного университета леса (МГУЛ). Рассказывает главный технолог завода: «Специалисты компании AkzoNobel ежемесячно отбирают образцы клееной продукции, которую испытывают в независимой лаборатории на расслоение клеевого шва, а результаты тестов присылают нам. Кроме того, периодические испытания нашего бруса выполняют в МГУЛ. Есть у нас и так называемый экологический паспорт».
Еще одним конкурентным преимуществом завода «Элеон» является безусловная надежность выполнения заказов в оговоренные в заказе сроки. Стандартный срок изготовления домокомплекта объемом около 100 м3 - 45 дней, но чаще всего предприятие выполняет заказ за месяц. Такую оперативность обеспечивают имеющиеся всегда на складах переходящие запасы готовой продукции (250-300 м3 бруса разного сечения) и пиломатериалов (от 760 до 1100 м3 ежемесячно).
Такой подход к организации производства и высокое качество уже давно оценили партнеры и клиенты завода «Элеон», среди которых как частные застройщики, так и известные архитектурные и строительные компании.
В 2013 году «Элеон» не испытывал недостатка в заказах и план всегда был сформирован на два, а то и на три месяца вперед. Даже зимой 2014 года, когда в отрасли был спад, портфель заказов был полон. «На сегодня в этом портфеле заказов на три-четыре месяца вперед», - говорит г-н Новиков.
Кадры
Любое современное деревообрабатывающее предприятие, даже высокоавтоматизированное, нуждается в достаточном для успешного функционирования штате квалифицированных работников. Сейчас в ООО «Элеон» трудится почти 130 человек. У многих производственников стаж работы в лесопромышленной отрасли от 20 до 40 лет: например, генеральный директор и главный технолог уже более 30 лет трудятся на этом предприятии. Средняя заработная плата сотрудников - 30 700 руб. в месяц. Руководство предприятия говорит о планах ее повышения. На заводе созданы хорошие условия для отдыха (оборудованы комнаты для отдыха и питания, сделан ремонт в раздевалках и душевых кабинах).
Сотрудники компании регулярно повышают квалификацию, внимательно следят за новинками техники и новыми технологиями, берут на вооружение эффективные методы организации труда. «Элеон» постоянно участвует во всех проводимых в России специализированных выставках по деревянному домостроению. На предприятии постоянно проводится аттестация рабочих мест, проверка знаний инструкций по технике безопасности.
Перспективы развития
Несмотря на достигнутый уровень производства есть еще над чем работать, считают в руководстве компании. «В первую очередь надо автоматизировать процесс загрузки ламелей на пакетную линию сращивания, - говорит Валерий Новиков. - Сейчас на конвейере подачи заготовок мы вынуждены держать три-четыре человека. Еще один технологический этап, нуждающийся в модернизации, - это загрузка прессов. Прессы у нас вертикальные, и укладывать ламели в них для формирования стопы приходится вручную. Да и разгрузку бруса из пресса тоже хорошо бы автоматизировать».
Будет продолжена модернизация машинного парка - планируется покупка нового автоматизированного комплекса для зарезки чашек и профилирования бруса. Будут пересмотрены некоторые технологические потоки с целью оптимизации процесса производства: так, станок для профилирования будет установлен в буфере перед зарезкой деталей домокомплекта, что позволит более оперативно и качественно, чем сейчас, изготавливать домокомплекты.
На «Элеоне» уверены: деревянное домостроение в нашей стране будет развиваться, а спрос на дома из клееного бруса будет расти. Причем, если по какой-то причине, например, в период экономического кризиса, спрос на стеновой брус упадет, предприятие готово быстро отреагировать на изменившиеся условия на рынке и предложить потребителям брус для фахверковой технологии строительства, производство которого здесь уже освоено.
В ближайшей перспективе планируется сделать еще один важный организационный шаг - укрупнить производство и диверсифицировать деятельность предприятия: предполагается покупка земли и строительство на ней поселков из собственных материалов с последующей продажей домов и земельных участков.
Ольга РЯБИНИНА,
Александр РЕЧИЦКИЙ