Как «обманывает» харвестер
Один из важнейших показателей лесозаготовительных машин - объем выработки, то есть количество древесины, заготовленное за определенный период. На этих данных базируются планирование и стабильность работы многих предприятий лесопромышленного комплекса. Поэтому лесозаготовители очень серьезно относятся к методам определения выработки и предназначенным для этого устройствам. Но зачастую даже самые совершенные приборы выдают неточные данные. Как и почему - попробуем разобраться.
Свой первый сортиментный харвестер я увидел в 1991 году, проезжая по дороге Хабаровск - Владивосток на практику в пос. Сукпай. В лесхозе за забором торчала стрела странной машины с остекленной кабиной и гроздью фар.
«Вот кому-то повезло», - подумалось мне тогда. Новые финские машины только стали поступать на Дальний Восток. Естественно, интерес к ним был огромный, но было их всего четыре единицы на весь край, и еще были четыре машины совместного производства - финские манипуляторы и агрегаты фирмы Valmet на базе наших колесных Т-150К Харьковского тракторного завода. Собирались такие машины на предприятии «Ленлес» с 1990 по 1992 год, и было их собрано около 100 единиц. Так что вероятность того, что я смогу поработать на новенькой машине, которую я увидел проездом на практику, была крайне мала.
Какие же из агрегатных машин массовых выпусков работали на лесозаготовках в Советском Союзе тогда, в 80-х и начале 90-х годов прошлого века?
Валочно-пакетирующая машина ЛП-19 (выпускалась Йошкар-Олинским заводом лесного машиностроения на базе тяжелого экскаватора ЭО-4121, поставленного на ходовую часть трелевочного трактора ТТ-4) с захватно-срезающим устройством с цепной низкооборотной пилой, цепь которой весила столько, что я, без пяти минут выпускник техникума, с трудом мог отнести ее в заточку. Была еще ЛП-17 на базе ТДТ-55 (гусеничного трелевочного трактора; выпускался Онежским тракторным заводом), но для лесов Дальнего Востока эта ВПМ была «слабой» и к нам не поставлялась. ЛП-19 была переделкой экскаватора в ВПМ, а у ЛП-17 были две кабины, и оператору во время работы приходилось постоянно переходить из кабины в кабину.
Появилась тогда и валочно-трелевочная машина ЛП-49 (тоже на базе ТТ-4). Стрела с плавающей валочной головкой с захватом, который перекладывал сваленный хлыст в клещевой захват. Машина была сконструирована так, что могла брать лес только справа по ходу (слева оператору ничего не было видно), а масса установки (12 т при весе базового трактора те же 12 т) и рейсовой нагрузке (до 24 м3) разрушала тракторную ходовую часть очень быстро.
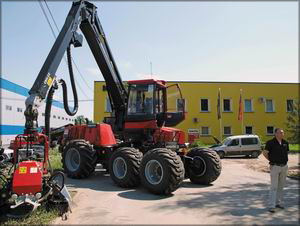
Бесчокерные трелевочные тракторы были двух видов: ЛП-18 и ТБ-1, которые выпускались на базе ТТ-4 и ТДТ-55 соответственно, со стрелами и тросовыми петлями. Кроме этих машин пачковым захватом оснащали трактор К-700, и в Сибири он собирал пачки из-под ЛП-19. Сучкорезная машина ЛП-33 на базе опять же ТТ-4 неплохо очищала от сучьев тяжелые хлысты, но требовала большеразмерных площадок для складирования. Хорошо, что у меня в бригаде был бульдозер D6D компании Caterpillar. Иначе бригада мучилась бы с организацией складов. Березу и прочий лиственный лес сучкорубы не любили, и им приходилось обрезать сучья вручную - безредукторной мотопилой «Тайга 2ЭМ». Грузили хлысты на лесовозы челюстными погрузчиками перекидного типа на базе ТТ-4. На мой взгляд, эти машины уже тогда плохо отвечали нуждам отрасли. Почему?
Как по причине устаревшей конструкции базовых тракторов, так и из-за попыток приспособить имеющиеся машины к выполнению определенных операций без учета их прочностных и весовых характеристик. Например, установка башни от экскаватора на шасси ТТ-4 при производстве ЛП-19 потребовала удлинения рамы трактора и введения в конструкцию дополнительного балансирного катка. Машина получилась тяжелой, вязла в болотистом грунте, и на пнях у нее отламывались оси катков. Даже ее транспортировка в лес на трейлерах представляла проблему из-за большей, чем у трейлера, ширины базы: она просто свисала с его боков. Перегон машины своим ходом был долог и утомителен: ее максимальная скорость (5 км/ч) - меньше, чем маршевая скорость пехоты... Перегоняя ЛП-19 своим ходом от пос. Березовый на БАМе до делянки, мои товарищи засыпали за рычагами, просыпаясь от того, что машина начинала бороздить башней склон сопки.
Тем не менее эти машины мне нравились. Кто хоть раз пробовал валить лес вручную, меня поймет. Летом вальщик мокнет под дождем, зимой под снегом, зарабатывая себе радикулит. Редукторные пилы типа «Урала» своей тряской вызывают виброболезнь, все вальщики просили меня привезти из города часы-«луковицу», обычные ручные часы при валке жили недолго. Комфортная работа в теплой, прочной, закрытой кабине перевешивала все недостатки конструкции. Вот такими были советские лесные машины в 1980-е, а возможность поработать на импортной технике была крайне мала.
И все-таки мне повезло. Заканчивая Хабаровский политехнический институт по трехгодичной программе подготовки инженеров лесозаготовительного комплекса, имеющих за спиной техникум, я попал в группу молодых специалистов, которых наше тогдашнее ТПО «Дальлеспром» в 1992 году направило на обучение в Финляндию, в лесную школу «Валтимо».
В течение 20 дней обучения в этой школе я понял разницу между конструкциями лесных машин, имевшихся тогда в Советском Союзе, и конструкцией скандинавских харвестеров и форвардеров. Она была огромной. И не столько в плане удобства работы оператора (хотя и это тоже немаловажно, кондиционер в закрытой кабине - не роскошь, а средство выжить в жару), сколько в плане эффективности применения зарубежной техники при заготовке. Используя всего две скандинавских машины, лесозаготовительный участок мог давать готовую продукцию в виде бревен, рассортированных и уложенных в штабеля. По сравнению с машинами, которые эксплуатировались тогда в СССР, эта техника позволяла поднять производительность труда на заготовке до 600% на человека. Операторы в кабине были полностью защищены от опасности, возникающей при падении деревьев и их частей, то есть основная причина получения травм на лесозаготовках полностью исключалась.
Для учета заготовленного леса на зарубежных харвестерах уже тогда, в начале 1990-х, имелся очень важный инструмент - бортовой компьютер, который вел учет срубленных деревьев, давал сведения о числе и кубатуре спиленных бревен. Причем номенклатура длины и диаметра тогдашних компьютерных систем вполне обеспечивала необходимый ассортимент бревен той длины и диаметра, которые запрашивали наши лесопилки.
Компьютеры, которыми оснащены теперь современные модели харвестеров, кроме выполнения вышеперечисленных операций, позволяют оптимизировать распил дерева на части по ценности покупаемых бревен. Скандинавы разделяют дерево по ценности на четыре части: зона без сучков (самая ценная древесина), зона сухих сучьев (древесина подешевле), зона живых сучков (древесина еще меньшей ценности), балансы (совсем дешевая древесина). Введение в программу раскряжевки харвестера прейскуранта бревен в зависимости от длины и диаметра в породе позволяет харвестеру ориентироваться на выработку самых дорогих сортиментов. То есть машина не просто работает, а зарабатывает ее владельцу деньги с максимальной эффективностью, в зависимости от качества леса на делянке, длины и толщины деревьев. Программы харвестеров и форвардеров сейчас также ведут учет рабочего времени машины по операторам и сменам, позиционируют машину на местности с передачей данных через модемы в центральный офис, учитывают расход топлива и т. д. Но нас в первую очередь интересуют возможности программного обеспечения бортовых компьютеров харвестеров, которые позволяют вести учет заготовленного сырья. Принцип, который используется для измерения леса, действителен для всех типов харвестеров всех производителей и остается неизменным с 90-х годов прошлого века, несмотря на то, что меняются операционные системы, рабочие программы.
Опытные операторы лесных машин, специалисты и руководители лесозаготовительных компаний давно заметили, что показатели объема заготовленной древесины, которые фиксируются бортовыми ПК харвестеров, не соответствуют замеренным вручную - они зачастую выше обмеренных объемов заготовленного сырья. Почему же так происходит? Попробуем разобраться.
Как харвестер измеряет бревно? Он это делает во время протяжки с помощью системы датчиков, установленных на харвестерных головках/агрегатах. Первый важный датчик - датчик длины. До начала 2000-х годов эти датчики были фотоимпульсными, теперь просто импульсные, более надежные. При протягивании бревна в агрегате вперед или назад вращается зубчатое колесо привода датчика длины, который посылает импульсы на блок управления головкой, а оттуда данные передаются в процессор ПК (см. рис. 1).
Перед пуском машин в работу систему датчиков всегда настраивают, делают их калибровку. При калибровке длины оператор как бы «объясняет» системе измерения, какое количество импульсов от датчика приходится на метр отмеренной длины сортимента. Для этого оператор, отпилив несколько сортиментов, выходит из кабины и рулеткой замеряет длину нескольких отпиленных бревен. Потом вводит эти данные в рабочую программу харвестера в разделе калибровок, и программа сама пересчитает поправки на длину. Измерительная система любого харвестера измеряет сортименты с точностью до сантиметра, потому что расстояние между зубцами колеса привода у харвестерных головок всех производителей - 1 см.
Второй важный датчик - так называемый угловой потенциометр (на харвестерную головку ставится не менее двух, чтобы обеспечивать точность измерений). Этот датчик измеряет диаметр бревна крест-накрест прямо в процессе протягивания. Датчики диаметра теперь чаще всего устанавливают в верхних ножах головок (см. рис. 2).
Измерение диаметра происходит так: ножи агрегата закрываются на минимум примерно 40 мм и открываются на максимум около 700 мм. От привода ножа харвестерной головки поворачивается ось внутри датчика, и он посылает импульс тока в модуль головки, а информация о величине этого импульса поступает в программу раскряжевки ПК машины. Датчик выдает ток в диапазоне от 0 до 5 В. Калибровкой датчиков оператор распределяет эти 5 В на диапазон значений диаметра деревьев, перекрывая диаметр каждого дерева, захватываемого агрегатом. Оператор должен постоянно проверять эту калибровку, так как точность измерения диаметра равна 1 мм и ошибки измерения каждого диаметра существенно влияют на результат обмера бревен. Далее показания двух датчиков диаметра складываются и делятся пополам, что обеспечивает высокую точность измерений, а программа бортового ПК вычисляет объем сортимента.
При протяжке бревна компьютер через каждый сантиметр длины фиксирует данные о диаметре, формируя в памяти цифровое изображение этого участка бревна в виде своеобразного блина (секции). Далее «блины» собираются в дециметровые участки (секции), объем которых прибавляется к общей кубатуре бревна. Причем набор в таком отрезке ведется от большого диаметра к малому. Если диаметр следующего измеренного «блина» больше, чем предыдущего, в зачет принимается предыдущий диаметр (см. рис. 3), что позволяет парировать наличие шишек на стволе и утолщений в месте роста сучьев.
Измерив объем каждого 10-сантиметрового отрезка бревна (последний отрезок может быть короче 10 см), получаем полный объем бревна. Каждому бревну программой раскряжевки присваивается свой файл, для учета и контроля. Машинное измерение бревна ведется по формуле Губера (или секционными отрезками). Более точного способа измерения конусной некруглой фигуры обычного дерева пока не придумали. Этот метод позволяет определить почти истинный объем бревна в коре.
У файла, присваиваемого бревну, есть номер и расширение stm. «Прочитать» его можно с помощью либо специальной программы калибровочной вилки - у разных производителей этих приборов есть свои программы, например, у шведской компании «Хаглоф» такая программа называется «Скалман» с номером версии, - либо рабочей программы управления лесозаготовительными комплексами. Есть еще офисные программы для управления и анализа работы сортиментных комплексов, и обычно программа для чтения файлов, присвоенных бревнам, есть и там. Файл каждого бревна невелик по объему (примерно 200-400 Кб) и сохраняется вместе с информацией о делянке очень долго - для проверок заготовленных объемов леса, если таковые потребуются. В случае возникновения какой-либо спорной ситуации можно проверить точность измерений, выбрав из штабеля несколько бревен - промерить их снова электронной вилкой и найти в списке файлов ПК харвестера данные, соответствующие замеренным. Чтобы избежать такой ситуации, подрядчики на лесозаготовке в Скандинавии требуют от операторов часто проверять калибровки, история проведения калибровок записывается, также сохраняются данные о введенных поправках. С помощью такой системы работы подрядчики удерживают точность измерений в пределах 2% погрешности. Хотя нормативы, действующие в Скандинавских странах, допускают погрешность до 4%. Расширения файлов и способы передачи данных заложены в стандарте, называемом StanForD. И все производители харвестерных агрегатов в Скандинавских странах придерживаются этого стандарта на измерение леса и передачу данных.
До появления бортовых компьютеров на лесных машинах в разных странах использовались разные способы измерения древесины, и в программах ПК харвестеров есть возможность учесть эти особенности при измерении кубатуры бревен.
Выбор формул и способов измерения объема лесоматериала предусмотрен при настройке измерительной системы харвестера, так же как вычет из кубатуры бревна объема коры. Какие способы можно использовать? Те, которые заложены в программу раскряжевки харвестера производителями систем измерения, наиболее распространенные. Информацию о них можно найти в руководствах оператора харвестеров. Коротко перечислю основные: немецкий HKS, когда верхний диаметр бревна умножают на длину бревна (рис. 4а); с помощью измерения и суммирования объемов дециметровых отрезков бревен (рис. 4б); серединный диаметр сортимента умножают на длину сортимента (рис. 4в).
И вот теперь возникает вопрос: а есть ли в России стандарт на приемку леса с помощью измерительных систем харвестерных головок? Какими инструментами в России пользуются для приемки леса до сих пор? Линейка, рулетка, шест? И еще, если возникает необходимость разбирательства по делу о недопоставках древесины, что будет предъявлено в суде в качестве доказательства правоты одной из сторон? Естественно, то, что прописано в договоре: акт приемки-передачи лесоматериалов, обмер которых выполнен согласно ГОСТу.
Вот что говорится в аналитической записке «Соблюдение государственных интересов Российской федерации при поставке круглого леса на экспорт», опубликованной в Бюллетене Счетной палаты Российской Федерации за 2001 год за номером 5(41). Цитирую п. 5 «Стандарты учета круглых лесоматериалов»: «Основополагающими стандартами, определяющими и устанавливающими нормы и правила учета древесины, являются: ГОСТ 2292-88, ГОСТ 2708-75, таблица № 4 в ГОСТ 2708-75, ОСТ 13-303-92. Указанные стандарты допускают отклонения и погрешности измерения при определении объемов круглых лесоматериалов 5%.
Для получения показателей объемов лесоматериалов при групповом учете основными являются ОСТ 13-43-79, ГОСТ 3243-88.
Для определения объема отдельных деревьев, а также запасов древесины на установленной площади - лесосеке, делянке или выделе с целью определения всего запаса или среднего объема дерева - хлыста применяются таблицы «Определение объемов хлыстов и сортиментов», 1985 г., Н. П. Анучин; ОСТ 13-75-88. «Хлысты древесные. Методы измерения объема».
Следует отметить, что все вышеперечисленные стандарты по учету леса, как растущего на корню, так и в хлыстах и сортиментах, введены в действие в соответствии с требованиями Федерального закона «О стандартизации» от 10.06.93 г. № 5154-1, являются обязательными для всех пользователей леса как внутри страны, так и при поставке древесины на экспорт».
Поштучный пересчет бревен при помощи сортиментных таблиц обеспечивает точность в пределах 5%. Но при настройке системы измерения харвестеров российские операторы не могут приспособить ее к нашим условиям: сведения, содержащиеся в отечественных сортиментных таблицах, в память бортовых ПК харвестеров не внесены.
Однако измерение объемов заготовленной древесины выполняется - из показателя, который выдает ПК харвестера, вычитается какой-то объем, взятый из «таблиц Потолочного» при помощи «справочника Пальцева». Ведь никаких нормативных актов на этот счет нет, пересчитывать вручную каждую балансину - дорого и долго. Тем более что все знают, что компьютер харвестера врет... Вот и вводится минусующая поправка, а учет заготовленного леса начинается при его отгрузке в лесовозы.
Еще одним фактором, влияющим на точность измерения, является вычет объема коры из объема всего заготовленного леса. Российским ГОСТом для определения параметров толщины коры в районе лесозаготовок регламентирована выборка в 500 бревен. А вот скандинавские лесозаготовители при начале разработки делянки сверяются с картами, на которых обозначены параметры толщины коры по породам. Кто эти данные собирал? Скорее всего, лесные институты по заказу лесопромышленников и государства.
Такие данные в России я видел только у двух работающих в нашей стране компаний: финской «Стора Энсо» (в Тихвине) и ОАО «Монди» (в Сыктывкаре). Остальные заготовители, видимо, используют таблицы и справочник, упомянутые выше, то есть тычут пальцем в небо. А на деле объем заготовленного лесоматериала зависит от того, как на предприятии договариваются при расчете с рабочими.
Так как же поступить, если мы хотим знать точное количество и объем заготовленных сортиментов? Можно нанять человека для измерения. Можно подсчитать самому, как это делал я, работая мастером: прыгать по штабелям с линейкой и мелом. Ну а зачем тогда нам компьютер в харвестере? А если мы должны заготавливать сортименты одной породы разной длины и форвардер должен складывать весь пиловочник не в один штабель, а, допустим, в десять, рассортировывая бревна еще и по длине? Прощай, производительность труда форвардера (и, соответственно, харвестера). Давайте к этому добавим еще, что заготавливаемых пород - четыре, а балансы разной длины; что пересчет по таблицам хорош для измерения объемов пиловочника и очень проблематичен при ручном измерении балансов и подходит для измерения бревен с фиксированной длиной через один метр (как указано в таблицах), рассортированных по разным штабелям вершинами в одну сторону... А еще есть дрова, которые тоже нужны, и учитывать их приходиться. Один десятник с таким учетом не справится. Да и десятников на двух операторов уже нужен десяток. Словом, желание связываться с такими машинными системами учета, да и с самими машинами весьма низкое...
Альтернатива - геометрический обмер штабелей, вывод коэффициента полнодревесности, работа только ручная, и с большой погрешностью.
Конечно, можно как в Скандинавских странах - проверять объемы заготовленного леса при поставке его на заводы. Но тогда потребуется установка сканеров и весов на всех лесопильных и целлюлозно-бумажных комбинатах. Это можно было бы сделать, но опять мы упремся в существующие правила. ГОСТами использование таких приборов не предусмотрено, а значит, деньги, потраченные на их установку, будут считаться израсходованными впустую.
На самом деле там, где есть сканеры, они экономят деньги и время на приемку леса. Но, случись конфликт с поставщиком, суд обратится к норме, и комбинат вынужден будет вернуться к старой системе приемки. Комбинаты пока спасает их почти монопольное положение с покупкой балансов.
Еще одна проблема при учете леса с использованием ПК харвестера - сезонность заготовки и вывозки леса. Если заготовленные штабели вовремя не удастся вывезти, как оплатить работу операторов харвестера и форвардера? На что опереться при закрытии нарядов и выплате заработной платы? Естественно, на вышеприведенную практику занижения действительных объемов леса.
Как с «обманами» харвестеров справляются скандинавы? Как я уже говорил, с помощью компьютера системы измерения и правил приемки леса на заводах и комбинатах. В любой спорной ситуации можно проверить всю цепочку поставки от начала до конца с помощью сохраненных файлов при таксации леса электронными вилками, при рубке леса харвестером, при трелевке леса форвардером с помощью весового контроля, по трекам маршрута лесовоза. Также можно посмотреть в рабочей программе харвестера историю калибровок и введения поправок, что для операторов в Скандинавских странах является обязательным условием при работе на машине. И все эти меры предназначены для того, чтобы максимально повысить точность измерений и уменьшить влияние человеческого фактора при измерениях.
Но не следует считать меня безоглядным критиком существующей в ЛПК РФ технологии измерения. Просто хочется нормальной работы, без ошибок и проблем. И принятием в России одного лишь нормативного документа, регламентирующего правила приемки леса с помощью компьютерных систем измерения, не обойтись.
Почему я так считаю?
Потому что пользование лесами должно быть комплексным. Харвестер с форвардером - в первую очередь инструменты для выборочных рубок, и только потом - для сплошных. И если мы хотим перейти (или вернуться) к разумному рациональному использованию лесов, то и начинать необходимо с самого начала - с таксации лесов.
Надо, чтобы пробные площадки закладывались с засечкой широты и долготы в центре измеряемой площади (здравствуйте, ГЛОНАСС и GPS!), а высоту дерева замеряли лазерным дальномером (поверенным согласно нашим ГОСТам). Если таких приборов в данный момент нет, значит, их надо создать, проверить и ввести в действие. Работы для наших институтов - поле непаханое! Актуально и внедрение геоинформационных систем, в которые данные таксации встраиваются очень легко. Что это даст? Это даст высокое качество проведения таксации, исключит практику простого переписывания данных предыдущих измерений. И тогда владелец леса или арендатор будет точно знать, сколько и какого леса в конкретном квартале, выделе, на делянке. Проверить данные о наличии леса или его отсутствии в том или ином месте можно будет с большой степенью достоверности - подняв файлы замеров с привязками к местности. И отчитываться за срубленную древесину будет гораздо проще: вот карта делянки, вот количество срубленного леса, данные из компьютера харвестера с историей калибровок. Будет обеспечен анализ качества срубленного леса и данные о реальном выходе деловой, балансовой древесины, а также треки системы позиционирования на местности, чтоб не вылезти за границы делянки. И еще много-много всего хорошего и полезного...
Операторы лесных машин, наконец, смогут реализовать все возможности техники: не только «свалил-распилил», они в полном смысле слова станут лесными инженерами, для которых можно и нужно создавать отечественный стандарт на измерение леса. А можно воспользоваться и зарубежным опытом.
Деревообработчики, зная реальное количество лесных запасов в России (которое всегда можно проверить) и получая от таксаторов и заготовителей объективные сведения о количестве растущих лесов и их породном составе, смогут планировать выпуск нужной людям продукции, покупая необходимые станки и оборудование.
Государственные надзорные органы смогут легко проверять данные заготовок леса и контролировать процессы перемещения сортиментов - эти данные станут «прозрачными»: сколько леса в стране есть, сколько выделено, сколько переработано и продано.
«Ну хорошо, а тебе-то зачем это все?» - можете спросить вы. Да мне всего-то и нужно, чтоб харвестер не «обманывал»... Учить операторов легче будет.
Владислав КОЛЕСНИКОВ, инструктор компании Komatsu Forest