Перевооружение плитного рынка
Производители ДСП воюют с кризисом,
а не с товарами-заменителями
Специалисты помнят: когда в 2011 году создавалось впечатление, что рынок плит вышел из кризиса, тут же наступил новый. Сейчас похожая ситуация. Мебельный рынок уже столкнулся со снижением продаж, но производители ДСП держатся: закупают передовое оборудование, осваивают новые технологии.
Древесно-стружечные плиты - материал, который производится в нашей стране с советских времен. Области использования ДСП: судостроение, вагоностроение, строительство (облицовка вертикальных и горизонтальных поверхностей, подложка под напольные покрытия, опалубка, перегородки), а также производство готовых изделий строительного назначения (стеновых панелей, межкомнатных и входных дверей, фальшполов). Но все-таки основное назначение ДСП - изготовление мебели: от 75 до 95% всего объема выпускаемых плит используется именно в этой отрасли.
Динамика производства
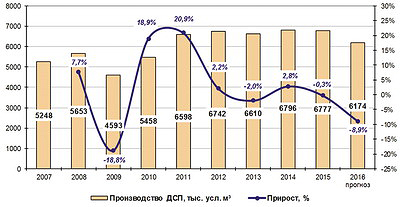
Рис. 1. Общая динамика производства ДСП в России в 2007–2015 годы и
прогноз на 2016 год, м3
ДСП используют для изготовления почти всех видов мебели, включая кресла и столы; для корпусной и встроенной мебели - ламинированные плиты, для каркасов мягкой мебели могут подойти плиты без облицовки. Мебель из ДСП бывает дорогой и дешевой, но наибольший объем приходится на сегмент экономкласса. На дешевизну конечного продукта влияет низкая стоимость самой плиты, а также эффективность раскроя, благодаря чему отходы составляют менее 5%. Предприятия производят ДСП разных размеров: толщина варьирует от 6 до 75 мм, максимальная ширина плиты составляет 1,8 м, а длина достигает 3,6 м (при непрерывном способе производства плита может быть нарезана в размер согласно требованиям заказчика).
Выпуск ДСП в России довольно стабильный даже в условиях регулярно возникающих кризисов. Спад производства в 2009 году составил около 19%, после чего два года подряд наблюдался рост, в результате чего докризисный объем производства был перекрыт на 17%. Возможно, выпуск ДСП продолжил бы расти, но в 2013-2014 годах рост экономики застопорился, реальные доходы населения постепенно стали снижаться и наметились проблемы в разных потребительских сегментах, включая мебельный рынок. В 2015 году все эти факторы усугубились под влиянием экономических санкций, наложенных мировым сообществом, а также ответных мер, принятых российским правительством в области торговых отношений с рядом западных стран.
В этих условиях отечественные плитные предприятия несколько лет производили почти один и тот же объем ДСП: с 2011 по 2015 год выпускалось 6,6-6,8 млн м3 плит ежегодно (см. рис. 1). Специалисты ожидают, что в 2016 году выпуск все же пойдет на спад под давлением неблагоприятных экономических факторов, снижение может составить 8-10% по сравнению с предыдущими годами.
Производители ДСП в России
Большая часть производственных линий, до сих пор благополучно работающих в стране, была введена в эксплуатацию в 60-е годы прошлого века. Технология производства ДСП довольно проста. Различают два основных способа: периодический и непрерывный. В основе технологии всех старых производств периодический способ прессования стружки, который предполагает использование одноэтажных или многоэтажных прессов - оборудование российского производства СП-25, а также зарубежных линий Bison-Werke (Германия), Rauma-Repola и Raute Wood (Финляндия) и других, менее известных. На современных предприятиях используются установки непрерывного прессования; наиболее известные производители подобного оборудования - немецкие компании Siempelkamp и Dieffenbaсher. Непрерывная технология позволяет получать плиту высокого качества: с равномерным распределением стружки, низким уровнем содержания формальдегида и оптимальной плотностью слоев. Почти на всех новых заводах, введенных в эксплуатацию в России за последние десять лет, а также на модернизированных производствах основным оборудованием являются прессы именно этих компаний.
Предприятие «Карелия ДСП» (входит в состав Segezha Group АФК «Система») освоило технологию непрерывного производства одним из первых в России: первая ламинированная плита, изготовленная на оборудовании фирмы Dieffenbacher, была выпущена в марте 2002 года. На Сыктывкарском фанерном заводе цех по производству ДСП был открыт в 1976 году и изначально работал, как и многие в то время, на хорошем финском оборудовании Rauma Repola и Raute Wood. Первая немецкая линия появилась на заводе в 2002 году, и вплоть до настоящего времени здесь приобреталось и другое зарубежное оборудование. Заводы компаний «Кроностар» и «Кроношпан» заработали в России в 2003 и 2004 годах соответственно, на них плитные материалы производятся также на основе технологий Dieffenbacher. В 2004 году провели модернизацию производства компании «Шатура-Плиты» и ОАО «Юг» (Краснодар). В 2006 году на оборудовании Siempelkamp приступило к производству ДСП новгородское ООО «Флайдерер», которое позже было приобретено компанией IKEA. Теперь этот завод именуется Pfleiderer IKEA, его начальная мощность составляла 320 тыс. м3 в год, но потом была доведена до 550 тыс. м3. Австрийская компания Egger владеет двумя заводами в России: производство в г. Шуя (Ивановская область) было пущено еще в 2006 году, а в 2011 году концерн переоборудовал мощности бывшего гагаринского фанерного завода (Смоленская область). Теперь совокупная мощность холдинга - более 850 тыс. м3 ДСП в год. ЗАО «Череповецкий ФМК» обновил мощности в 2007 году.
Что касается новых предприятий, то завод «Югра-Плит» начал работу недавно - в 2010 году (мощность 265 тыс. м3), но уже в 2013 году провел модернизацию и нарастил мощности. Широкомасштабную модернизацию предприняла и компания «Увадрев-Холдинг»: в январе 2015 года с пресса непрерывного действия типа Contiroll (Siempelkamp) сошла первая плита ДСП, а общая мощность завода выросла до 315 тыс. м3.
К этому «клубу» современных производителей ДСП вскоре присоединится компания «Томлесдрев» («Томский завод ДСП»), где уже на стадии пуска находится производство мощностью 350 тыс. м3 (пресс Dieffenbacher). В ближайшее время ожидается долгожданный ввод в эксплуатацию предприятия-гиганта «Кроношпан» под Уфой (плановые мощности предполагают производство до 1 млн м3 плит), который уже почти построен. Весной 2016 года пуск был отложен из-за сложностей с инфраструктурой, а до этого регулярные проблемы возникали с общественными организациями, которые до сих пор протестуют против пуска этого предприятия. С подобными протестами сталкиваются многие проекты деревообрабатывающих производств. В частности, экологические активисты в свое время выступали против проекта завода «Эггер» в Шуе, дело доходило до разбирательств в природоохранной прокуратуре и суде. Российских общественников пугает масштаб новых предприятий и вероятность того, что в погоне за прибылью иностранные концерны принесут в жертву экологию тех регионов, в которых строятся новые заводы.
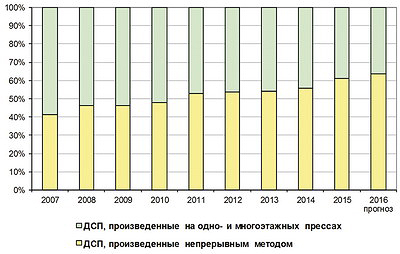
Рис. 2. Рост доли ДСП, производимых непрерывным способом, в 2005–2015
годах и прогноз на 2016 год, %
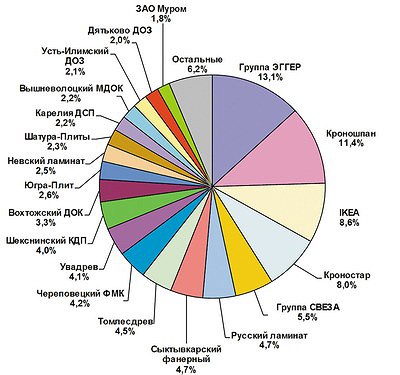
Рис. 3. Распределение выпуска древесных плит по ведущим заводам ДСП в
2015 году, %
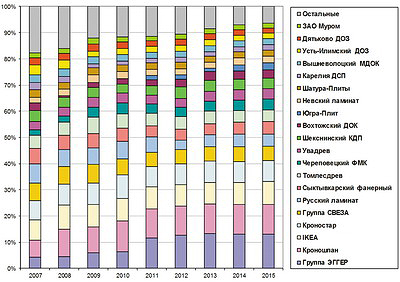
Рис. 4. Динамика долей производства плит ДСП по производителям, 2008–
2015 годы и прогноз на 2016 год, %
Но именно со строительством подобных заводов мощностью от 200 до 700 тыс. м3 плит в год связаны перспективы развития отечественного производства древесных плит. Для оптимального соотношения «цена/качество» мощности нового завода должны быть 350-500 тыс. м3 в год. Благодаря тому, что подобные предприятия регулярно появляются, доля ДСП, произведенных непрерывным способом, с каждым годом растет. И если в 2007 году в структуре общего производства высококачественные плиты составляли около 40%, то в 2015 году - уже более 60% (см. рис. 2). В 2016 году, несмотря на общий спад, доля ДСП, изготовленных на непрерывных прессах, скорее всего, продолжит расти, так как крупным современным заводам легче удержаться на плаву в сложных условиях.
Стоит добавить, что в советское время древесно-стружечные плиты ламинировали редко, чаще их просто шлифовали, красили, лакировали либо облицовывали натуральным шпоном. Сейчас же большая часть производимых плит ламинируется прямо на производстве, а при непрерывном способе производства прессование и ламинирование выполняются одновременно. И чем больше появляется новых производств, тем быстрее растет доля ламинированных ДСП. На хорошо оборудованных заводах доля ламинированной плиты доходит до 100%, так как вся она отправляется производителям мебели, ведь использовать ДСП высокого качества в строительстве невыгодно.
По объемам производства ДСП в России лидирует группа Egger, которая, как сказано выше, располагает двумя заводами: в Ивановской и Смоленской областях. «Эггер» вышел на первое место по объемам в 2011 году, а в 2015 году на долю этой группы приходилось более 13% всего выпуска. На втором месте находилась компания «Кроношпан», ее доля 11%. После ввода в строй второго завода в Башкортостане «Кроношпан» с большой долей вероятности обгонит своего конкурента, и случится это если не в 2016-м, то в 2017 году. Заводы Pfleiderer IKEA и «Кроностар» по итогам 2015 года находятся на третьем и четвертом месте соответственно. Помимо «Эггер», в России есть еще два холдинга, каждый из которых объединяет два ДСП-производства: группа «СВЕЗА» и группа «Русский ламинат». По объему производства они по итогам 2015 года находятся на пятом и шестом месте соответственно. Сведения о долях этих и остальных заводов в общем объеме выпуска плитных материалов по итогам 2015 года отражены на рис. 3, а динамика долей производства плит ДСП по производителям - на рис. 4.
Импорт и экспорт
производителей ДСП в России (по состоянию на июнь 2016 года)
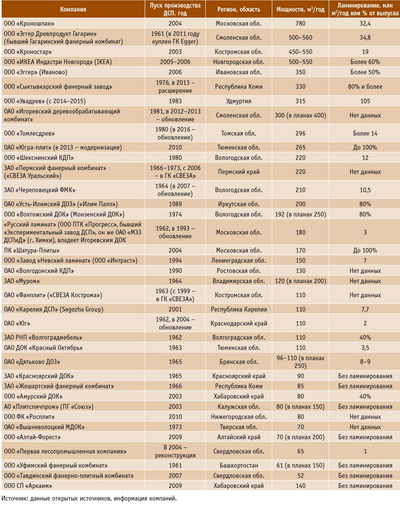
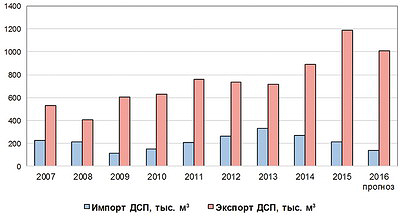
Рис. 5. Динамика импорта и экспорта ДСП в 2007–2015 годы и прогноз на
2016 год, тыс. м3
Экономические санкции ряда западных стран и контрмеры России почти никак не повлияли на отечественный рынок ДСП - импорт этого материала давно уже не столь значителен (в последние годы составлял около 300 тыс. м3), поэтому никакого импортозамещения не произошло, хотя поставки из-за рубежа в 2014-2015 годы действительно сократились. В том числе и потому, что в конце 2014 года Роспотребнадзор ввел запрет на ввоз древесно-стружечных плит компании «Кроно-Украина». Официальная причина запрета - выявленное превышение уровня формальдегида. Но украинских плит на российском рынке и до запрета было не так уж много, примерно в два раза меньше, чем белорусских.
Импорт ДСП играл более-менее значимую роль на отечественном рынке до 2005 года. До этого импортная продукция выигрывала у российской по трем причинам: большой диапазон толщины плит (от 8 до 38 мм), более широкая декоративная гамма, разнообразие фактур, рисунков и цветов, соответствие требованиям по токсичности. Теперь же плиты высокого качества, соответствующие международным нормам, на российском рынке предлагают отечественные и иностранные производители, работающие на территории России. Технические характеристики отечественных ДСП также вышли на более высокий уровень. Российские плиты стали более влагостойкими, некоторые заводы предлагают ДСП с огнеупорными характеристиками, экологические параметры плит соответствуют международному стандарту Е1. Крупным предприятиям удалось даже снизить содержание формальдегида до половины Е1 (не более 4,0 мг/100 г).
Сейчас импортируются преимущественно ламинированные плиты (или с покрытием ПВХ) марок Kronospan, Pfleiderer, Kronopol, FAB SRL, IKEA, Egger, Duropal и некоторых других европейских компаний, а также в небольшом объеме дешевая китайская ДСП.
А вот что касается экспорта, то российским производителям есть куда расти. В 2015 году из России было экспортировано 1185,1 тыс. м3 древесно-стружечных плит. После мирового финансового кризиса 2008-2009 годов экспорт ДСП из России стремится к росту. В 2016 году объем экспорта составит 900-1000 тыс. м3 (уровень 2014 года), но дальнейшего роста, наверное, не будет, так как ожидается спад производства. Правда, эксперты считают, что с 2017 года объемы экспорта снова начнут расти.
Инвестиционная привлекательность производства ДСП
производству ДСП в 2011–2015 годы, тыс. руб.
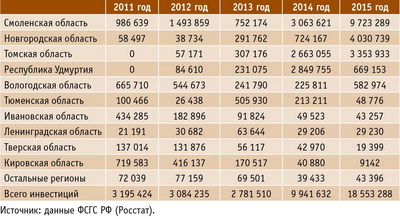
С учетом сказанного выше понятно, что проекты строительства новых предприятий по выпуску ДСП по-прежнему являются инвестиционно-привлекательными. Заводы, построенные в прошлом веке и оснащенные периодическими прессами производства 1960-1980-х годов небольшой мощности постепенно вытесняются с рынка. Для внутреннего рынка необходимо расширение ассортимента ДСП за счет производства влагостойких плит и плит для строительства, массовое освоение выпуска малотоксичных плит класса Е0,5, отвечающих новым требованиям по содержанию формальдегида, для чего необходимо применение в производстве плитной продукции меламиносодержащих карбамидных смол.
Стоимость строительства нового завода с нуля - 3-6 млрд руб. Сроки окупаемости составляют пять-шесть лет, а в условиях кризиса и больше, при продолжительности строительства два-три года (как показывает российская практика). Зачастую выгоднее переоснастить старый завод новым оборудованием, что, собственно, и делают многие отечественные предприятия. Статистика инвестиций в производство ДСП за последние пять лет свидетельствует: в лидерах Смоленская область (здесь модернизируются завод «Эггер» и Игоревский комбинат), Новгородская область (завод «Флайдерер ИКЕА»), Томская область (установлено новое оборудование на ООО «Томлесдрев»), Республика Удмуртия (модернизация на заводе «Увадрев»), Вологодская, Тюменская области и другие регионы.
Сравнение рынка ДСП с рынком плит MDF
Анализируя рынок плит MDF и HDF*, мы отмечали, что эти материалы составляют основную конкуренцию ДСП; давайте сейчас посмотрим, удается ли волокнистым плитам средней и высокой плотности вытеснять древесно-стружечные плиты с рынка. Плиты MDF больше, чем ДСП, подходят для производства изделий, используемых при повышенной влажности: мебели для ванной комнаты и кухни, влагостойких стеновых панелей. Из грубой ДСП невозможно изготавливать мебельные фасады со сложной внешней обработкой (филенками, сложными узорами, закругленными углами, гнутыми деталями), подобные изделия тоже лучше производить из плит MDF ввиду однородной структуры этого материала.
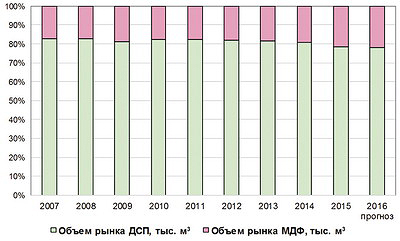
Рис. 6. Соотношение продаж ДСП и плит MDF на российском рынке в 2007–
2015 годах и прогноз на 2016 год, %
Анализ количественных параметров обоих сегментов показывает, что, хотя рынок плит MDF и HDF активно растет, а выпуск ДСП демонстрирует умеренный рост, а в последние годы и вовсе почти стоит на месте, «подвинуть» древесно-стружечные плиты с занятых на рынке позиций не так-то просто. Только в 2015 году заметны некоторые подвижки (см. рис. 6), да и то лишь благодаря активизации некоторых новых производителей, в частности компании «Кастамону» (Татарстан), которая старается загрузить свои мощности, чтобы занять солидную долю рынка, пользуясь кризисной ситуацией. Но если учесть, что в мебельной промышленности используются далеко не все производимые плиты MDF, а большая часть идет на изготовление дверей, напольных покрытий и для нужд строительства, то, похоже, производителям ДСП пока бояться нечего. В лучшем случае лишь около 3-5% заготовок для недорогой мебели могут производиться из плит MDF и HDF, для выпуска остальных по-прежнему будет использоваться ДСП. По прочности и устойчивости к механическим ударам и нагрузкам плиты HDF ощутимо проигрывают древесно-стружечным плитам, не говоря уже о преимуществе последних при сравнении цен на эти материалы.
Вера НИКОЛЬСКАЯ,
директор по исследованиям агентства ABARUS Market Research