Деревообрабатывающее оборудование. Классификация Eumabois. Часть 16
Оборудование для отделки древесины жидкими лакокрасочными материалами
Отделкой называют процесс создания защитно-декоративного покрытия на поверхности древесины, либо процесс обработки поверхности термомеханическим или иным способом, в результате чего она приобретает новые, улучшенные свойства. Защитно-декоративное покрытие может быть сформировано с помощью пленочных материалов, наклеиваемых на поверхность детали, или твердеющих жидких материалов (краски, лаки, эмали, грунтовки, шпатлевки и т. п.). В настоящей публикации речь пойдет об оборудовании для подготовки поверхности к отделке, для нанесения жидких лакокрасочных материалов (ЛКМ) и их отверждения.
Часть 2. Лесопильное оборудование
Часть 3. Оборудование для сушки пиломатериалов
Часть 4. Торцовочные пильные станки для вторичной деревообработки
Часть 5. Круглопильные станки: прирезные и форматные
Часть 6. Станки ленточнопильные столярные
Часть 7. Станки продольно-фрезерные
Часть 8. Станки фрезерные и фрезерно-копировальные
Часть 9. Шипорезные станки
Часть 10. Станки для обработки и облицовывания кромок
Часть 11. Станки для выборки отверстий и пазов
Часть 12. Станки токарные
Часть 13. Станки шлифовальные
Часть 14. Оборудование для сращивания на зубчатый шип
Часть 15. Оборудование для склеивания массивной древесины
Часть 17. Оборудование для облицовывания древесины пленочными материалами
Часть 18. Оборудование для производства окон и дверей
Часть 19. Специализированное оборудование для производства стульев
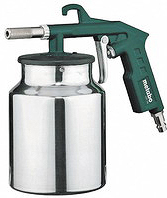
Рис. 1. Пескоструйный пистолет SSP 166 (производитель – компания Metabowerke GmbH,
Германия)
Подготовка поверхности к отделке заключается в ее очистке от загрязнений и шлифовании. В строительстве при ремонте деревянных и иных зданий для очистки поверхностей применяют пескоструйные аппараты. Распыляемые ими мелкие песчаные частицы, попадая на отделываемую поверхность, очищают ее от загрязнений. На рис. 1 приведено изображение малого пескоструйного пистолета SSP 166, который предназначен для обработки небольших площадей. Песок, распыляемый из его форсунки под рабочим давлением 7 бар, удаляет ржавчину и остатки краски. Вес аппарата - 0,7 кг.
В комплект более крупной пескоструйной установки I-30 (производитель - ГК «Воздух», Москва) входят: бункер для абразива, шланг воздушный, сито, рукав абразивный, инжекторный пистолет, абразивноструйное сопло из легированной стали и компрессор производительностью 1 м3/мин. с рабочим давлением 6 бар. Производительность установки - до 3 м2/ч.
В столярно-мебельном производстве для очистки поверхности от пыли и других загрязнений, для снятия свесов, остатков клея или ЛКМ после их отверждения, а также для структурирования поверхности широко используют щеточные станки.
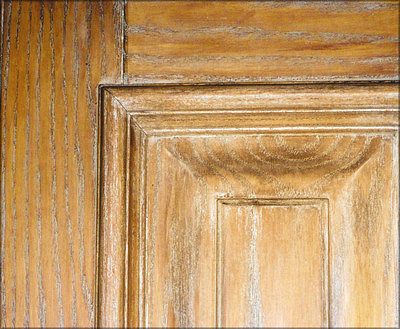
Рис. 2. Деревянные детали после искусственного старения

Рис. 3. Машинка для искусственного старения древесины Festool Rustofix GmbH (Германия)
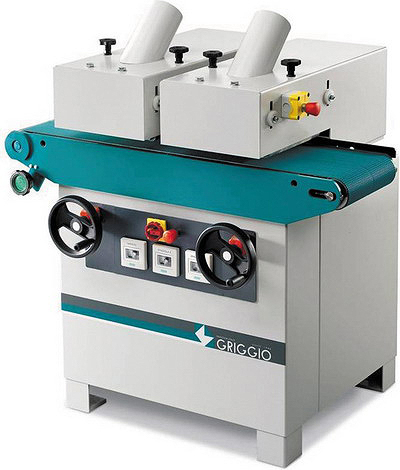
Рис. 4. Станок для искусственного старения древесины с двумя щеточными валами R300/2 (производитель – компания Griggio, Италия)
Термин «структурирование поверхности» означает изменение структуры древесины в результате механического или иного воздействия на нее. При обработке абразивными материалами мягкая ранняя древесина годового слоя удаляется в большей степени, чем поздняя древесина, в результате чего поверхность приобретает объемный характер (рис. 2), часто напоминающий структуру старой древесины, а сам процесс иногда называют процессом искусственного старения древесины.
Сегодня на рынке представлено большое разнообразие щеточных станков универсального назначения. Сменные щетки позволяют использовать один и тот же станок как для грубых работ вроде удаления старой краски, «старения» древесины, так и для тонких работ, например, шлифования поверхности под отделку.
Машинка Festool (рис. 3) предназначена для домашних мастерских и малых производств. С помощью быстросменных щеток ее можно использовать для выполнения трех операций: структурирования, промежуточного шлифования и выглаживания поверхности. Вес машинки - 7,5 кг.
Для искусственного старения древесины в промышленных масштабах можно использовать специальные станки с одним или двумя валами (рис. 4). Станок оснащен двумя валами со щетками диаметром 200 мм, работающими от двух моторов мощностью 4 л. с. Щетки поднимаются с помощью маховичков, оснащенных механическим визуализатором. Скорость подачи материала - 3-20 м/мин. Станок предназначен для работы с заготовками, высота и ширина которых не превышает 300 мм.
Щеточные валы для деревообрабатывающего оборудования выпускает фирма «Осборн-Рус» (Санкт-Петербург, Россия). В ассортименте продукции этой компании валы с металлической проволокой разной длины и жесткости, а также валы с нейлоновым ворсом.
Щеточные очистные станки конструктивно близки к станкам для старения древесины. Например, станки от фирмы Paul Ernst Maschinenfabrik GmbH (Германия) находят применение для очистки заготовок после мембранных прессов (3D вакуум-пресс). Они оснащаются разными щеточными вальцами, которые устанавливаются относительно направления подачи под углами 0,15 и 300. Щетки можно устанавливать по высоте и менять посредством быстросменного приспособления в течение пяти минут.
В конструкцию высокоэффективного варианта станка для крупного производства входят четыре щеточных вальца, которые используются для закругления острых кромок пленки в нижней пласти заготовок и очищают их от остатков клея-расплава. Станки автоматически настраиваются на предварительно выбранную толщину заготовок, поэтому на них могут обрабатываться заготовки разной толщины, поступающие от нескольких мембранных прессов.
Серия пылеудаляющих станков KDC создана для очистки и выглаживания поверхности заготовок перед нанесением на них лаковых покрытий. Наличие функции реверсного вращения обоих роликов дает возможность очищать как длинные, так и короткие заготовки, пылеулавливающий колпак обеспечивает удаление пыли. Скорость варьируется при помощи инвертера.
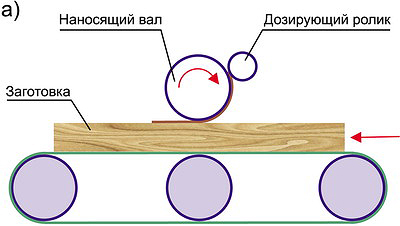
а) с одним наносящим вальцом
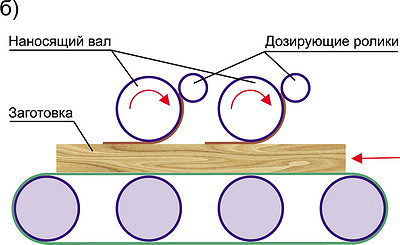
Рис. 7. Схемы вальцовых наносящих станков:
а) с одним наносящим вальцом,
б) с двумя наносящими вальцами
Нанесение лакокрасочных материалов может выполняться разными методами. Широко распространенным является вальцовый метод (рис. 7). Одновальцовые станки используются для нанесения на поверхность красителей и верхних слоев лака. Благодаря наличию индивидуальных двигателей каждого ролика можно отдельно регулировать скорость дозирующего и наносящего роликов, что позволяет равномерно распределять цвет по поверхности заготовки и убирать следы от наносящего ролика. На двухвальцовых станках можно использовать все типы лаков и наносить на поверхность деталей больше ЛКМ, чем на одновальцовых, без угрозы образования следов от вальцов.
Для нанесения ЛКМ обычно используют обрезиненные вальцы. Материал подается насосом в пространство между наносящим и дозирующим вальцами и торцевыми уплотнительными щечками. Вальцы могут вращаться во встречном или попутном направлениях. В случае встречного вращения на дозирующем вальце устанавливают ракели (скрепки), которые очищают валец от ЛКМ. На станке имеется также механизм тонкой настройки щели между дозирующим и наносящим вальцами в интервале 0-5 мм, что позволяет в некоторой степени регулировать расход материала.
Достоинства вальцового нанесения отделочных материалов: широкий диапазон вязкости ЛКМ, высокая скорость подачи (до 25 м/мин.), возможность нанесения очень тонких слоев лаковых покрытий. Недостатки метода: довольно быстрый износ резины на наносящем вальце, невозможность отделки рельефных поверхностей и нанесения толстых слоев ЛКМ.
Для нанесения низковязких материалов, например, водных растворов красителей, наносящий валец покрывают поролоном. При крашении заготовки отделочный слой на древесине не образуется, происходит лишь изменение ее цвета на глубину пропитки (до 0,5 мм при поверхностном крашении).
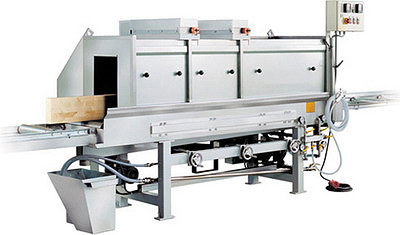
Рис. 8. Щеточно-распылительный станок Impregmat Evo (производитель – Schiele Maschinenbau GmbH, Германия)
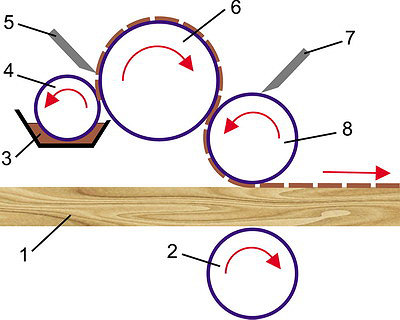
Рис. 9. Схема печатного станка: 1 – деталь, 2 – подающий валик,
3 – ванная с печатной пастой, 4 – питающий валец;
5, 7 – очистные ракели, 6 – текстурный цилиндр, 8 – печатный цилиндр
Для кругового нанесения водорастворимых красителей можно использовать щеточно-распылительный станок - например, такой, как Impregmat Evo (рис. 8).
Заготовки подаются на этот станок без разрывов. Уникальная распылительная система выполняет 4-стороннее нанесение отделочного материала на заготовку. Затем щетки встречного вращения втирают материал в древесину, а излишки удаляются настолько тщательно, что заготовка выходит из станка без капель жидкости. Максимальные размеры поперечного сечения заготовок - 300 х 300 (300 х 500) мм, минимальная длина - 1 м, скорость подачи - 10-60 м/мин. Излишки ЛКМ фильтруются и снова используются.
Вальцовый принцип нанесения применяется и в печатных машинах, которые предназначены для нанесения рисунка на поверхность древесины, плиты, бумаги и других материалов путем оттиска с печатной формы. В качестве печатной формы наиболее распространены печатные цилиндры, на которые нанесен фотохимическим способом или методом гравирования тот или иной рисунок, обычно - текстура древесины ценных пород.
В подобных станках (рис. 9) имеется печатный цилиндр, облицованный эластичным полиуретаном. Краска из ванночки валиком наносится на текстурный цилиндр, остатки краски счищаются ракелем. Рисунок с текстурного цилиндра переносится на печатный цилиндр, а с него - на отделываемую поверхность. Чтобы сохранить четкость рисунка, поверхность печатного цилиндра очищают ракелем или промывают специальным устройством.
Декоративно-печатные машины Druma-S выпускает фирма Robert Buerkle (Германия). Диаметр печатного гравированного цилиндра в машинах серии Druma варьируется в пределах 270-440 мм, скорость подачи - до 50 м/мин., ширина машины - от 400 до 3600 мм.
В состав линии двухцветной печати на базе подобных станков входят 16 единиц оборудования. Рисунок на панелях, которые используются при производстве офисной мебели, стеновых панелей, в дизайне интерьера, формируется с помощью вальцовых покрасочных станков, затем поверх рисунка наносится специальное покрытие. Далее поверхность панелей сушится и готовые изделия упаковываются.
Распыление - наиболее распространенный способ нанесения лакокрасочных материалов. Он позволяет отделывать поверхности любой сложности. Различают пневматическое распыление и безвоздушное.
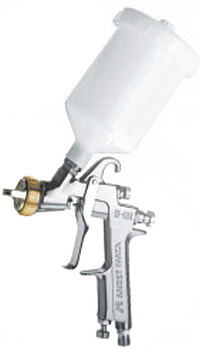
Рис. 10. Пистолет-распылитель
Для пневматического распыления используется пистолет-распылитель, в камеру смешивания которого по шлангам одновременно поступают жидкий лакокрасочный материал и сжатый воздух. При истечении воздуха из форсунки образуется воздушный факел с мелкими частицами ЛКМ, которые оседают на поверхности изделия. При безвоздушном распылении ЛКМ подается под высоким давлением в распылительное устройство, а при выходе из форсунки дробится на мелкие частицы за счет перепада давлений. При использовании этого способа потери материала меньше, чем при воздушном распылении.
Процесс распыления всегда выполняется в специальных распылительных кабинах (покрасочных камерах), где имеются устройства для очистки выходящего воздуха, сбора остатков ЛКМ.
Наряду с позиционным оборудованием на многих предприятиях сегодня эксплуатируются установки проходного типа с автоматическим распылением лакокрасочных материалов, которые особенно эффективны при отделке дверных полотен, профильных деталей мебели, элементов декора, стеновых панелей, багета.
Основным направлением совершенствования пневматического окрасочного оборудования является повышение коэффициента переноса окрасочных материалов, от которого зависят не только экономичность подобного метода окраски, но и экологичность этого процесса.
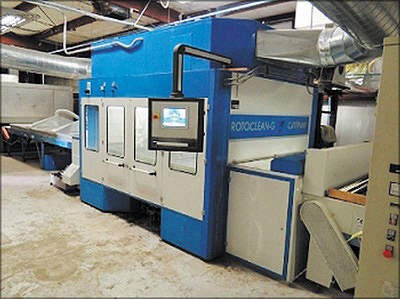
Рис. 11. Покрасочная камера Rotoclean G8 с каруселью пневматических форсунок (поставщик – компания «КАМИ- Станкоагрегат», Росссия)
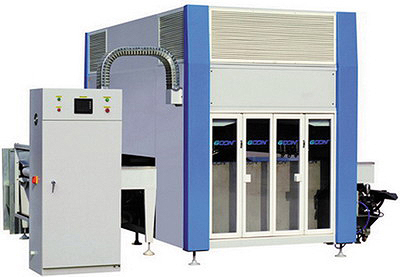
Рис. 12. Автоматическая покрасочная камера SP1300 (поставщик – «КАМИ- Станкоагрегат», Россия)
Производители предлагают пистолеты-распылители двух видов – для воздушного (рис. 10) и безвоздушного распыления. Конструкция воздушных распылителей может предусматривать принудительную подачу ЛКМ и верхний или нижний бачок. Кроме того, воздушные распылители различаются также по рабочему давлению: пистолеты с низким давлением (для создания промежуточного слоя лака или краски на поверхности детали) и со средним давлением (для создания наружного слоя). Пистолет безвоздушного распыления не требует подключения к компрессору. Он подсоединен к насосу высокого давления (до 200 атм), который погружен в емкость с лакокрасочным материалом.
Для промышленного производства выпускается широкая гамма покрасочных камер с распылителями разных конструкций. Изображение одной из современных покрасочных камер представлено на рис. 11.
Камера предназначена для нанесения в проходном режиме морилок, грунтов и финишных лаков методом распыления на пласть и кромки элементов мебели, плоские и рельефные панели на крупных мебельных производствах с многосменным режимом работы.
Производители и поставщики предлагают полностью автоматические камеры; например, у камеры SP1300 (рис. 12) имеются два независимых контура подачи лака для моментального перехода с одного материала на другой (например, с грунта на финишный лак). В систему встроена рейка с фотоэлементами, которая на входе станка считывает размеры и положение детали, передает данные в ЧПУ, которое управляет пистолетами, что позволяет избежать перерасхода ЛКМ.
Проходной станок предназначен для автоматической покраски распылением изделий погонажного типа (багета, плинтуса, наличника, рейки, составных элементов полов и т. д.) в проходном режиме. Деталь подается в зону покраски ленточным конвейером и окрашивается распылительными пистолетами. Пистолеты автоматически включаются в момент входа детали в зону покраски и отключаются после ее прохождения. В конструкцию станка входят система сбора неиспользованного ЛКМ для его повторного использования и система вытяжки, которая оснащена фильтрами для очистки воздуха.
Сущность электростатического распыления заключается в том, что аэрозольные частицы лака (краски) получают электрический заряд и осаждаются на изделии, у которого противоположный заряд. Одно из достоинств этого метода - минимальные потери лакокрасочного материала ввиду отсутствия т. н. тумана при распылении ЛКМ.
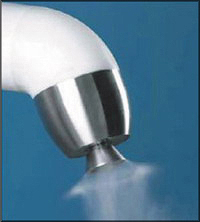
Рис. 13. Вид окрасочного факела центробежного электростатического распылителя
Чаще всего используют безвоздушное центробежное или гидравлическое распыление лакокрасочного материала. В отличие от пневматического, центробежный способ распыления предполагает формирование многочисленных микроструек ЛКМ на внешней кромке вращающегося с большой угловой скоростью (десятки тысяч оборотов в минуту) распылительного элемента - диска или колокола. Эти микроструи образуются за счет пленочного стекания материала по поверхности распылительного элемента под действием центробежных сил. Распад микроструй на мелкие фрагменты вблизи кромки распылительного элемента приводит к образованию «мягкого» низкоскоростного окрасочного факела (рис. 13).
Для управления формой этого факела и скоростью движущихся в нем частиц можно использовать относительно спокойные потоки воздуха, формируемые воздушными соплами, расположенными вокруг распылительного элемента. Некоторые модели таких сопел оснащены тангенциальными каналами, образующими осесимметричный вихрь вдоль оси турбины; направление вращения в этом вихре противоположно направлению вращения распылительного колокола. Сформированный таким образам воздушный поток снижает окружную скорость частиц краски, сходящих с кромок вращающегося колокола, уменьшая при этом тенденцию расширения факела за счет центробежного эффекта. Благодаря этим особенностям центробежный способ распыления позволяет исключить описанные выше негативные факторы, связанные с использованием интенсивных воздушных потоков и сохранять высокое качество распыления ЛКМ.
Подача электрического потенциала на распылительный элемент позволяет создать необходимые условия для реализации эффективного электростатического нанесения ЛКМ. В пространстве между распылительным элементом и заземленной поверхностью окрашиваемой детали возникает электростатическое поле. Электрический заряд, приобретенный частицами краски, способствует дальнейшему дроблению этих частиц на мелкие фрагменты, а также равномерности их распределения в пространстве.
Достоинства высокоскоростных центробежных распылителей реализованы в продукции компании ITW Ransburg (Германия). В ассортименте центробежных распылителей Ransburg представлены дисковые устройства, модели с распылительным колоколом для установки на линейные манипуляторы, а также модели серии RMA-303, специально разработанные для монтажа на «руку» окрасочного робота.
Для облицовки кромок изделий типа дверных полотен используют специальные автоматические линии, распыляющие ЛКМ на вертикальные поверхности.
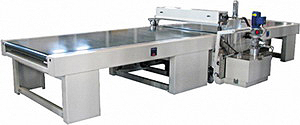
Рис. 14. Лаконаливная машина (производитель –
компания Superfici, Италия)
Жидкие лакокрасочные материалы можно наносить на обрабатываемую поверхность методами налива, облива и окунания. Лакокрасочный материал подается на изделие из наливочной головки. Материал, не попавший на изделие, стекает в отстойный бак и возвращается в лаконаливную головку. Деталь перемещается с помощью ленточных конвейеров. Расстояние от головки до поверхности детали должно быть по возможности минимальным. Толщина покрытия зависит главным образом от скорости подачи детали (до 140 м/мин.). Станки подобного типа широко применялись для нанесения полиэфирных лаков на щитовые заготовки мебели.
На рис. 14 показана одноголовочная лаконаливная машина производства фирмы Superfici (Италия).
Лаконаливная машина, работающая с одной скоростью, доступна в исполнении с одной или двумя убираемыми завесами. Узлы лаконаливной машины установлены на тележках и могут быть извлечены для очистки и сокращения времени смены лакокрасочных материалов.
Недостатками станков этого типа является невозможность нанесения лака на детали сложной формы (например, с фрезерованным рисунком), а также непостоянство вязкости ЛКМ - в процессе работы активно испаряется летучий растворитель, который периодически необходимо добавлять в систему.
Методом струйного облива на детали обычно наносят морилки, а также всевозможные защитные пропитки при изготовлении наружных окон и дверей из массива древесины. Методом облива можно отделывать подвешенные или стоячие элементы, как отдельные детали, так и целые изделия в сборе.
Суть метода заключается в нанесении избыточного объема лакокрасочного материала, большая часть которого под действием гравитации стекает в специальную емкость. Разумеется, ЛКМ, попавший в эту емкость, собирается и, пройдя через фильтры, вновь подается к обливным форсункам, благодаря чему вынужденные потери не превышают 10% изначального объема ЛКМ. Для лучшего растекания материала по изделию и получения покрытия равномерной толщины в установках струйного облива имеется зона выдержки изделия в парах растворителя той краски, которой обливается изделие. В этой атмосфере краска сохнет очень медленно и успевает равномерно растечься по всем элементам изделия, в том числе затечь в места, куда краска при обливе сразу попасть не может.
Из-за своей простоты метод облива может применяться как в ручном, так и в автоматическом режиме. В советские времена были созданы и успешно эксплуатировались автоматические и полуавтоматические линии, например, полуавтоматическая линия окраски столярно-мебельных изделий ДЛ38М. Скорость конвейера линии составляла 0,4-1,8 м/мин.
Струйный облив осуществляется путем подачи краски через сопла неподвижного контура, охватывающего деталь, или через систему сопел на качающейся трубе (осцикаторе), расположенной под конвейером с деталями. Необходимая концентрация паров в паровом туннеле создается главным образом за счет испарения растворителей с поверхностей окрашенных деталей.
К недостаткам метода следует отнести повышенный расход растворителя, неравномерность и невысокие декоративные качества покрытия, невозможность окрашивания изделий с внутренними полостями (карманами), большая производственная площадь, занимаемая линией отделки.
Способ окунания применяют для отделки небольших брусковых деталей, например, круглых ножек столов и стульев, других деталей решетчатой мебели. Отделываемая деталь должна быть простой обтекаемой формы, без уступов и гнезд. Достоинства метода: не требуется сложное оборудование и квалифицированный персонал, возможна полная механизация процесса, обеспечиваются полная отделка всех поверхностей деталей, малые потери ЛКМ, высокое качество покрытий за одну операцию.
Недостатки метода окунания: можно отделывать только детали обтекаемой формы, невозможно обеспечить равномерность толщины покрытия, необходимы ванны большого объема для лакокрасочного материала, интенсивно испаряется растворитель и повышается вязкость ЛКМ.
Лакокрасочные материалы для окраски окунанием должны содержать большой процент пленкообразующих веществ, обладать хорошей текучестью и высокой жизнеспособностью. Качество покрытий зависит от скорости погружения и выгрузки деталей из ванны, вязкости и температуры ЛКМ. Вязкость отделочных материалов должна быть в пределах 300-400 с по ВЗ-4. При простоте установок окунания и возможности механизации окраски метод окунания не получил широкого распространения вследствие невозможности обеспечить равномерность толщины покрытия, образования потеков на нижних кромках деталей, большого зеркала испарения растворителя (и связанным с этим высоким риском пожароопасности процесса отделки). Метод окунания используется на отдельных предприятиях для отделки брусковых или погонажных деталей на оборудовании, изготовленном собственными силами.
Экструзию (выдавливание) используют для нанесения ЛКМ на детали постоянного сечения. Деталь проходит через закрытую камеру, наполненную лакокрасочным материалом, сквозь шайбы (фильеры), которые обжимают деталь, полностью повторяя ее форму, и не дают лаку вытекать из камеры. Детали должны подаваться торец в торец, без остановки.
В 70-80-х годах прошлого века для нанесения покрытий методом экструзии применяли нитроцеллюлозные лаки НЦ-218, НЦ-223, предварительно выпарив из них разбавитель и доводя таким образом их вязкость до 350 с по ВЗ-4. Количество наносимого лака регулируют жесткостью фильеры и степенью обжатия деталей. Достоинства метода: экономичность (потери не превышают 7%); высокая производительность; метод хорошо поддается механизации и автоматизации.
С развитием высокоточных станков с числовым программным управлением стало возможным применение метода экструзии не только для отделки погонажа с круглым и шестигранным сечением, но и четырехгранной и даже фасонной форм. Для глубокой пропитки погонажных изделий из массива древесины можно использовать метод вакуумной экструзии, суть которого сводится к тому, чтобы заставить лакокрасочный материал проникнуть как можно более глубоко в тело древесины. Внутри герметичной покрасочной камеры создается значительное разряжение (в некоторых станках предусмотрена функция «пульсирующего разрежения»), и изделие, которое находится внутри камеры и окружено ЛКМ, подвергается воздействию этого разряжения. Воздух, находящийся в поверхностных порах древесины, вытягивается, а сами поры сжимаются. Затем давление возрастает до атмосферного, и поры, расширяясь, заполняются окружающим их лакокрасочным материалом. Благодаря этой технологии появилась возможность пропитывать древесину на глубину от нескольких миллиметров до нескольких сантиметров.
Подобные станки на рынке оборудования представляет, например, фирма Schiele. В установке возможно использование разных лакокрасочных материалов с расходом от 10 до 200 г/м2 при скорости подачи до 300 м/мин. Потери материала здесь минимальны, не более 1%.
В составе производственной линии Master Coat имеется облицовочная камера Vacumat, на ее входе и выходе расположены сменные матрицы, профиль которых повторяет профиль изделия (с зазором в несколько миллиметров). При входе заготовки в камеру в последней создается разряжение, которое способствует нанесению отделочного материала на все поверхности заготовки. Излишний отделочный материал попадает в систему рециркуляции.
Отверждение (сушка) лакокрасочных покрытий может выполняться следующими методами: конвективным нагревом (обдувом горячим воздухом), терморадиационным нагревом инфракрасными (ИК) лучами, ультрафиолетовой (УФ) сушкой покрытий (фотополимеризацией), радиационно-химическим отверждением (с помощью обработки ускоренными электронами). Поэтому в отделочных цехах предприятий устанавливают конвективные сушильные камеры, камеры терморадиационной сушки покрытий, камеры фотохимического отверждения.
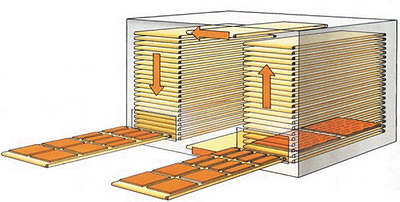
Рис. 15. Вертикальная конвективная сушильная установка Contivert ETC (производитель – компания Superfici / SCM, Италия)
Метод конвективной сушки состоит в нагревании деталей в специальных сушильных установках воздухом или продуктами сгорания газообразного или жидкого топлива. Окрашенным деталям тепло передается в результате конвективного теплообмена. Температура сушки колеблется от 50 до 200°С в зависимости от вида покрытий и материала просушиваемых деталей. Период высыхания составляет от нескольких минут до нескольких часов.
Вертикальный сушильный туннель с конвейером и лотками Contivert производства компании Superfici (рис. 15) может создавать контролируемый поток воздуха при минимальном расходе энергии, еще одно его достоинство - небольшая площадь. Лотки располагаются один над другим и перемещаются по вертикали и горизонтали, причем между лотками создается постоянный воздушный поток с заданными параметрами (скорость движения воздуха, температура), соответствующими параметрам цикла сушки определенного лакокрасочного материала. Высота лотка - 90-180 мм, длина - от 3,5 до 6,5 м (в зависимости от модели сушилки).
Терморадиационная сушка ведется с использованием ИК-лучей, генерируемых нагревателями темного излучения при температуре их металлической поверхности около 400°С. Излучение проникает на некоторую глубину в лакокрасочные покрытия и в первую очередь нагревает деталь, интенсифицируя процесс удаления растворителя из лакокрасочных материалов. Образование твердой пленки начинается изнутри слоя покрытия, что создает благоприятные условия сушки. Период высыхания лакокрасочного покрытия при терморадиационной сушке в 10-12 раз меньше, чем в конвекционных печах с нагретым воздухом.
Сушилка предназначена для сушки лакокрасочных материалов на заготовках любого типа - погонажа, щитовых деталей, дверных полотен, фасадов, столешниц и прочих плоских и рельефных заготовок, а также заготовок объемного типа.
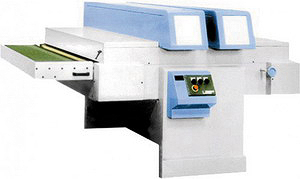
Рис. 16. Туннель УФ-сушки UVGZ (поставщик – компания «КАМИ-Станкоагрегат», Россия)
Ультрафиолетовую сушку можно использовать только для обработки материалов ультрафиолетового отверждения, т. е. содержащих специальные добавки - фотосенсибилизаторы. Плюсы использования подобных ЛКМ: короткое время сушки, высокий процент сухого остатка, широкая цветовая гамма и высокое качество получаемой поверхности.
Туннели УФ-сушки (рис. 16) предназначены для фотополимеризации грунтов и лаков, нанесенных на погонаж, щитовые детали, дверные полотна, фасады, столешницы и прочие плоские и рельефные заготовки. В этом туннеле ультрафиолетовая лампа находится в центре полусферы с высокой отражательной способностью. Подобное оборудование может встраиваться в автоматические покрасочные линии.
Сушка потоком электронов (радиационно-химическая) рекомендуется для изделий, покрываемых лаками и эмалями на основе полиэфиров, акриловых, эпоксидных и полиуретановых смол. Процесс полимеризации происходит в течение секунды или долей секунды. При сушке потоком электронов допустимы высокие скорости конвейера. Метод, однако, не получил широкого распространения в промышленности.
Известен также способ предварительного аккумулирования тепла. Он заключается в нагревании отделываемой поверхности перед нанесением на нее лакокрасочного материала. В этом случае процесс высыхания покрытия начинается снизу слоя, что значительно ускоряет процесс сушки и обеспечивает высокое качество покрытия. Для реализации этого метода предназначены специальные камеры разогрева.
Модуль применяется с целью достичь заданной температуры поверхности перед нанесением лакокрасочных материалов, что улучшает растекаемость и повышает качество нанесения ЛКМ. Под кожухами располагаются инфракрасные лампы, эффективно передающие тепло на лакируемую поверхность. Для достижения требуемой температуры в модуле могут быть установлены три, шесть или девять ламп (в соответствии со скоростью подачи линии).
Владимир ВОЛЫНСКИЙ